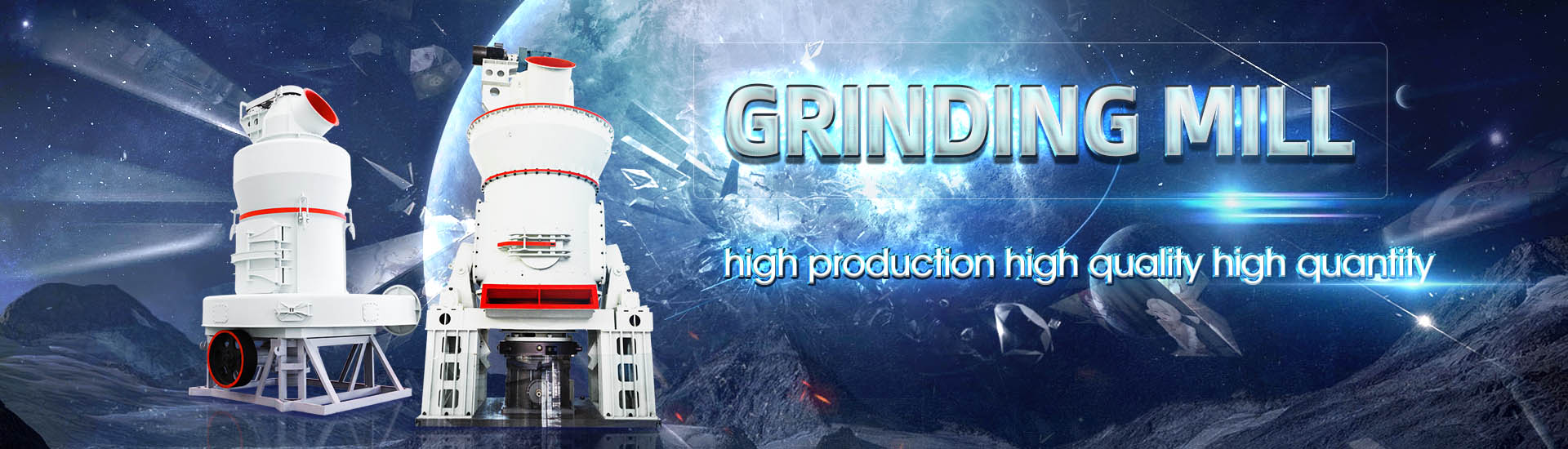
Mine electromagnetic high fine vertical mill
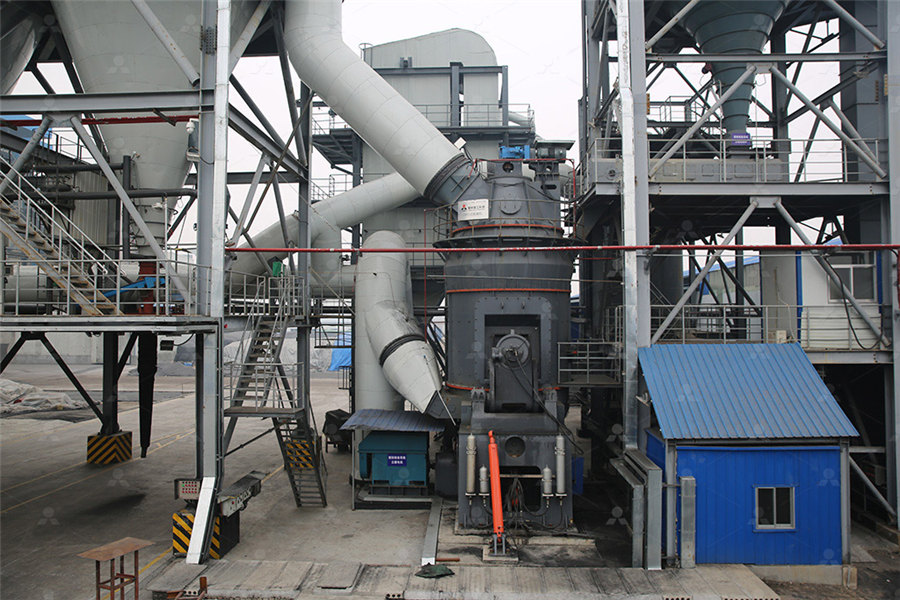
HIGmill high intensity grinding mill Metso
The Metso HIGmill™ is an advanced, energyefficient fine and ultrafine grinding solution that utilizes proven technology With the tall, narrow, vertical body arrangement, grinding media is evenly distributed and mineral particles remain Vertimill® is an energy efficient grinding machine They tend to grind more efficiently than, for example, ball mills with feeds as coarse as 6 mm to products finer than 20 microns This provides up to a 40% higher energy efficiency Vertimill® Metso2023年9月21日 STM Minerals introduced the VPMTM (Vertical Power Mill), which is a further development of the industry leading VRMTM technology The VPMTM has a wider grinding RECENT DEVELOPMENTS IN COARSE GRINDING USING 2016年1月1日 One of the advantages of the electromagnetic mill is the the ability to enhance many of technological processes by grinding in the area in which the ferromagnetic rods Construction of the electromagnetic mill with the grinding
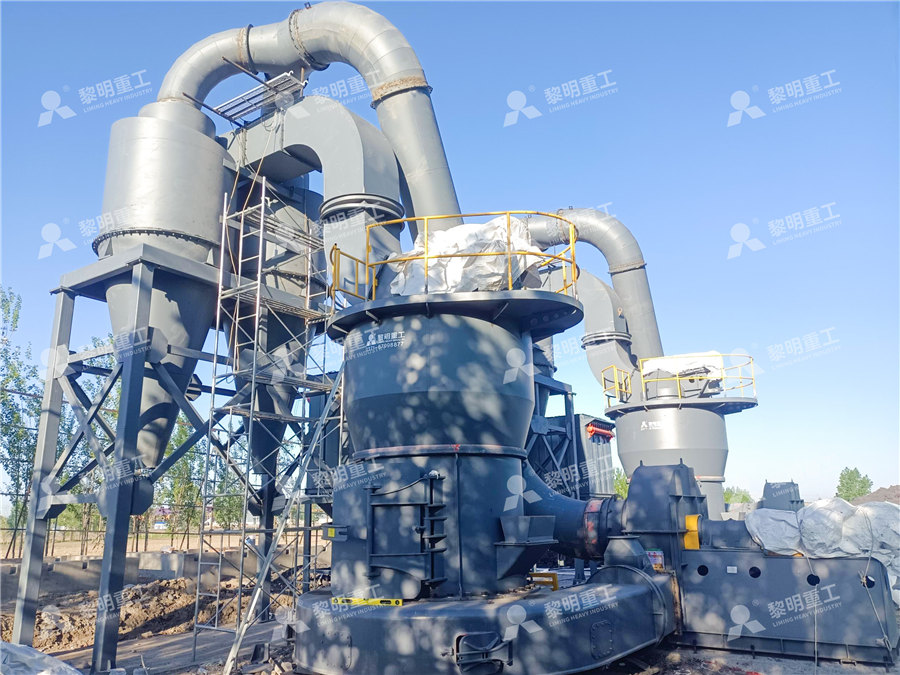
Stirred media mills in the mining industry: Material
2020年6月1日 Stirred media mills are used by the mining industry for ultrafine grinding to enhance liberation, and to decrease particle sizes of industrial minerals to tailor functional 2024年9月16日 A proven vertical agitated media mill for energy efficient fine grinding n The vertical stirred agitated mill was originally invented in Japan in the 1950s The horizontal ball EIRICH TowerMill Vertical agitated media mill2012年7月1日 ABSTRACT This article evaluates the effects of operating parameters on fine particle grinding process with a vertically stirred media mill The effects are investigated The liberation effect of magnetite fine ground by vertical stirred mill Vertical stirring mill is a kind of fine grinding and ultrafine grinding equipment with high efficiency and low energy consumptionIt is widely used in concentrate regrinding and the second and Research progress on grinding mechanism of vertical stirring mill
.jpg)
EnergyEfficient Advanced Ultrafine Grinding of
2023年7月10日 Both horizontal stirred mills (IsaMill) as well as vertical media mills (tower mills and stirred media mills) are gaining popularity in the mining and mineral industries for ultrafine grinding The particle size distribution is a 2024年9月16日 the mill grinding chamber, in which the vertical agitator screw is located, together with a charge of grinding media and grinding material in slurry form Highgrowth markets in copper, ironore, gold, leadzinc ores, mineral sands and rareearth metals drive increasing demand for fine grinding to maximize recoveryEIRICH TowerMill Vertical agitated media mill2024年3月1日 The study area of this paper is the Jiangjun Gobi No 1 Openpit Coal Mine field, which is located in the southeast of the Junggar Basin, Xinjiang Uygur Autonomous Region, ChinaGeological exploration of coal mine burnt rock and 2012年7月1日 A magnetite middling was used to compare the liberation effect of the magnetite fine ground by a vertical stirred mill and a ball mill The magnetite middling contained a high content of magnetite intergrowth with the particle size mainly distributed in the range of 40–150 μmThe new generated −38 μm products were concentrated by magnetic separationThe liberation effect of magnetite fine ground by vertical stirred mill
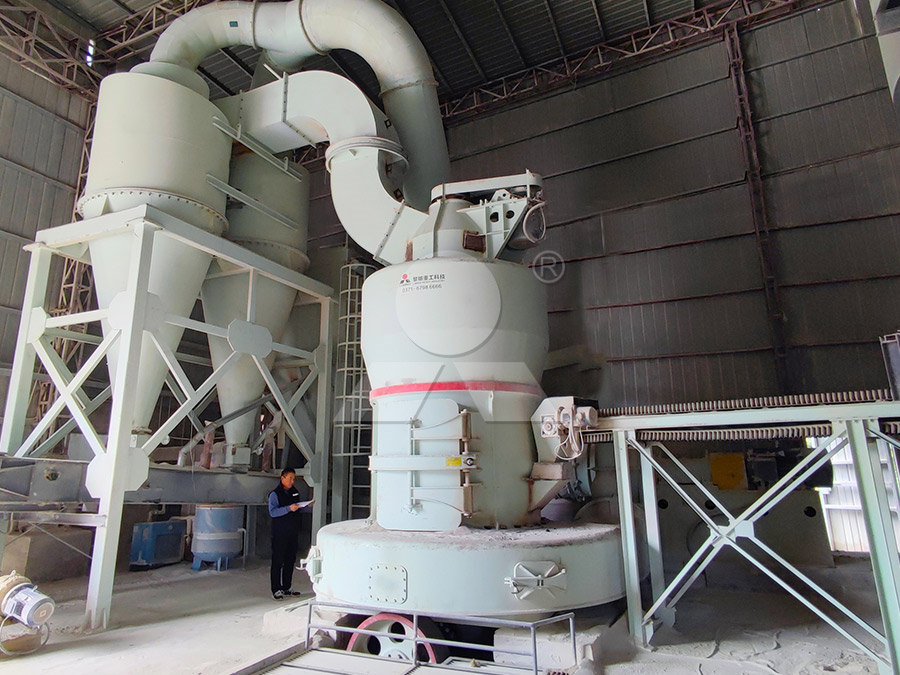
Magnetic separation Metso
Metso High Gradient Magnetic Separators (HGMS) are designed to recover weakly magnetic material from nonmagnetic matter and can be used for many applications including the processing of iron ores, rare earths and other weakly magnetic minerals, which are not normally treatable by ordinary magnetic separators Explore High Gradient Magnetic 6 天之前 HLM series vertical mill is a largescale, highyield, and energysaving grinding product developed by FTM Machinery using advanced grinding and external circulation technology, combined with years of milling production experience coal vertical mills, slag vertical mills, and ultrafine vertical mills 1 Cement vertical mill Raw materials Energysaving and Efficient Vertical Roller Mill Fote MachineryCLUM series ultrafine vertical roller millwas produced by Shanghai Clirik Machinery Co, Ltd Relying on 12 years of experience in the production of ultrafine powder and based on German and Taiwan ultrafine vertical mill technologies The top technical team members were joined this project Besides, highquality wearresistant parts are used to develop milling equipment which Ultra fine vertical roller millUltra Fine Millultramill 1 Introduction The vertical roller mill (VRM) is heavy mechanical equipment that used in the cement materials industry to process cement, slag, and coal cinder (Pani Mohanta, Citation 2015)The equipment always needs to work in the environment of heavy load, high temperature, high pressure, high corrosiveness, electromagnetic radiation interference, and multifield Full article: Reliability assessment of the vertical roller mill
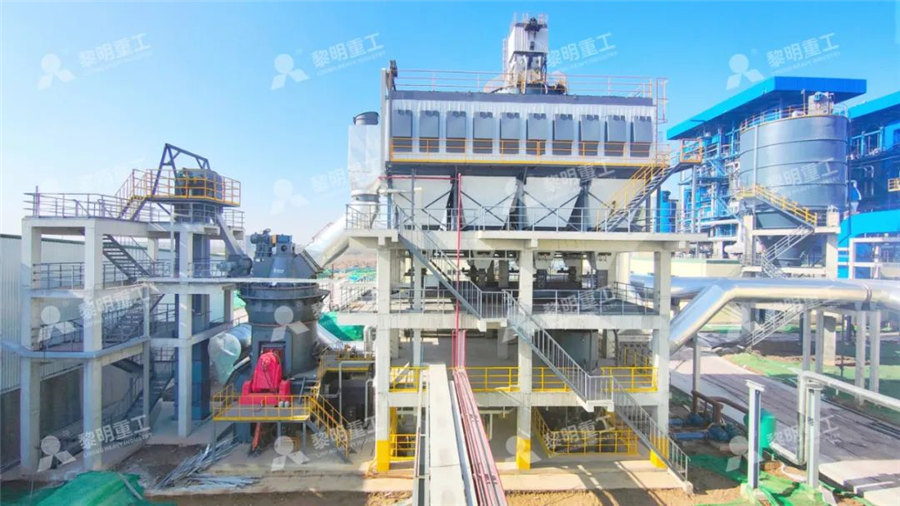
Vertical Grinding Mill: How it Works, Application And
The electromagnetic vibration feeder feeds uniformly, is easy to adjust, small in size, lightweight, easy to maintain and saves power The significant parts of a vertical grinding mill is made from highquality castings and rigorous processes ensure high durability An opentype dust collector is used to filter out excess air from the mill 2022年2月28日 Using an electromagnetic mill, a comparison between these two grinding environments has shown; while wet grinding requires around 16 kW of energy, the dry condition needs 3 kW for the same condition highspeed stirred mills, in which the rotational speed of the stirrer tip is usually higher than 15 m/s, are able to produce 5 μm or even Grinding SpringerLink2014年10月20日 The basis for this lies in its high energy density (310 times higher than other HEM), the ability of continuous operation, high number of operating parameters (circumferential velocity, ball Regrind of metallic ores with vertical mills: An overview of 2022年1月1日 The existing technological process of Aoshan concentrator in Nanshan mining company of Masteel is as follows: closed circuit crushing, high pressure roller mill superfine crushing, wet screening, magnetic separation, coarse particle discarding tailings, coarse concentrate stage grinding, stage magnetic separation, and fine screening regrindingHighefficiency and energyconservation grinding technology using
G[R.jpg)
Ultra Fine Mill,Ultra Fine Grinder,Ultra Grinding
HGM125 ultra fine grinding mill, ultra fine powder grinder is a kind of representative machine, and it is the new type industrial ultra fine grinding equipment specializing in producing fine and superfine powder of non 2024年4月1日 Figure 37 Size analysis for a repeat experiment performed in a vertical mill shown as a function of grinding time for a single 595 +420μm feed size 71 Figure 38 Vertical mill geometry (left) and RockyDEM simulation of the vertical millPREDICTING THE PRODUCT PARTICLE SIZE 2019年4月16日 Vertical roller mills (VRM) have been used extensively for comminuting both cement raw materials and minerals like limestone, clinker, phosphate, manganese, magnesite, feldspar and titanium(PDF) LEARNING FROM OTHER INDUSTRIES; WHY THE VRM 2023年9月21日 Pilot test work was carried out by Mazzinghy et al (2015) on a batch ball mill and pilot scale vertical mill to assess the energy efficiency factor The results shows that the scaling factor of 135 was required to adjust the ball mill energyspecific breakage rates to match the breakage rates in a vertical mill The vertical millRECENT DEVELOPMENTS IN COARSE GRINDING USING
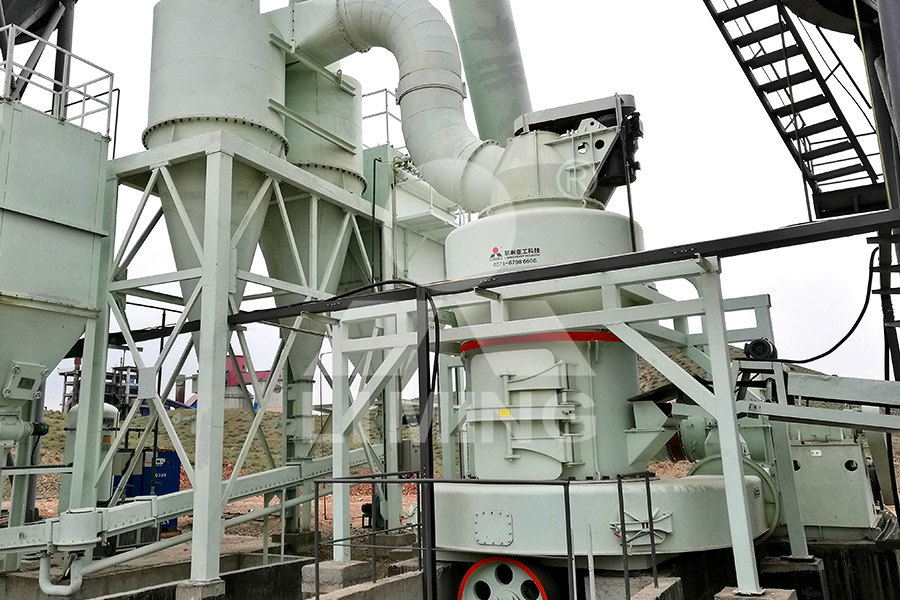
Energy Savings and Improved Recovery with Small
2018年2月20日 power saving from 10% to 44% In vertical stirred mills, the power saving increases from 20% to 60% More potential savings have been identified For the same operating conditions, how a vertical stirred mill is performing compared to ball milling? In regrind application, a vertical stirred mill with small media (512 mm Millpebs) will2023年7月10日 The present literature review explores the energyefficient ultrafine grinding of particles using stirred mills The review provides an overview of the different techniques for size reduction and the impact of energy requirements on the choice of stirred mills It also discusses the factors, including the design, operating parameters, and feed material properties, EnergyEfficient Advanced Ultrafine Grinding of Particles Since the Magnetic Mill Liner (MML) was invented and patented in 1989, more than 600 mills have been retrofitted with the MML worldwide nickel and gold mines as well as other nonferrous mines Magnetic Mill Liners sort out fine ball chips to increase effective charge volume and enhance grinding efficiency found in old ball mills Magnetic Mill Liner reduces cost AT MineralsVertical mills such as the FLS Tower Mill or the VXPmill and ball mills are commonly used for fine grinding in industries like mining, cement, and chemical processing These mills reduce material into finer particles, making them ideal for applications where fine to ultrafine grinding is required , such as in regrinding of ore in mining or Vertical mills for fine grinding – FLS FLSmidth
.jpg)
Vertical roller mills: The new leader in grinding technology
2019年10月11日 Mining companies today face a completely new battery of challenges to recover minerals Historically the reefs were rich and large profits were made with ordinary recovery circuits but today mines are dealing with complicated ores that require fine grinding to allow a 92% – 98% recovery rate just to stay in the game Read more about gold miningThe coal vertical mill, also referred to as the vertical roller coal mill, is an advanced equipment developed by our company It combines modern technology with our extensive experience in powder manufacturing This coal pulverizer HighEfficiency Vertical Coal Mill Enhancing 2024年10月15日 Vertical stirred mills are a fine grinding equipment that covers advantages of low rotation speed, high reliability and long life cycle The significant advantages that the vertical stirred mills have over the ball mills are Vertical Stirred Mill Mineral Processing A Complete Vertical Mill Mining Solution We would like to introduce our newest metal matrix composite wear parts, something that we truly believe is a gamechanger with respect to vertical mill mining activities today In short, these wear parts are a fivestep solution that meets the rigorous demands of mining companies operating these daysVertical Mill Mining Magotteaux
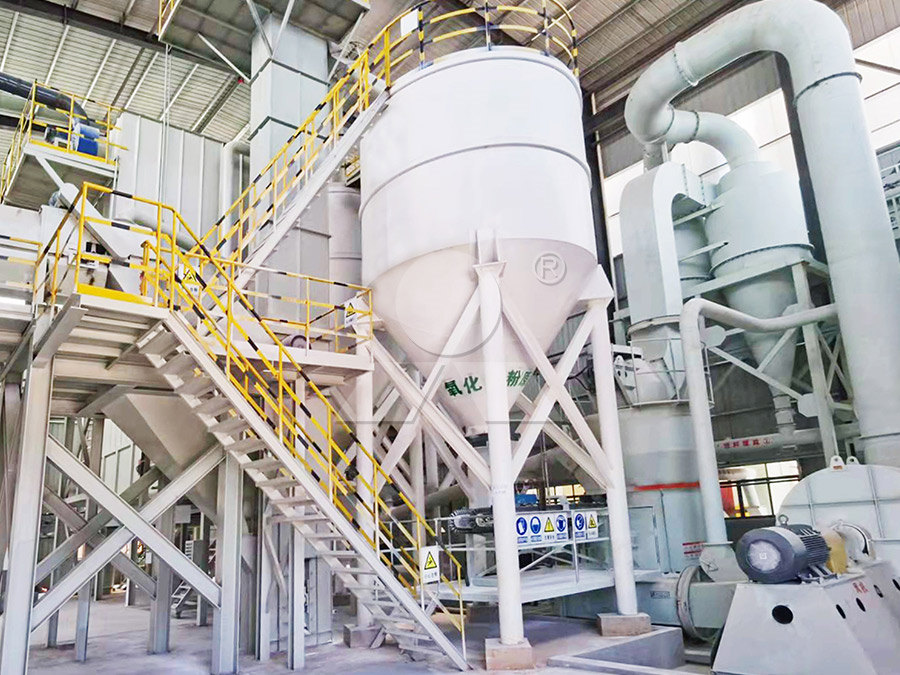
(PDF) Design of an electromagnetic mill Its ResearchGate
2016年1月1日 The construction of the magnetic conductors of the electromagnetic mill inductors used in [3][4][5][6][7][8] [9] [10][11], in our opinion, is far from optimal in terms of their massdimensional VertiSense™ is a digital solution for Vertimill ® stirred milling technology It is a novel system designed to enhance the grinding process in Vertimill ® that enables the wear monitoring of screw liners in real time and maximize operational efficiency through intuitive software and analytics Key benefits: Easy to install, maintain and use; Optimizes efficiency by ensuring wear parts are Vertimill® MetsoProduct advantage of talc powder ultrafine vertical roller mill 1 High quality powder size The fineness of the finished product is D97 545 microns Narrow particle size distribution, can produce 2 micron content of 20%70% products, greatly improving the added value of finished products and application areas 2Talc Powder Ultrafine Vertical Roller Mill Shanghai Clirik Mine Mill2023年10月10日 The Vertical Shaft Impactor Mill, also known as the VSI Mill, is a unique type of grinding mill that operates on a completely different principle compared to other types of mills This type of mill uses highspeed rotors with wearresistant tips to crush and grind materials into smaller particlesUnderstanding the SAG Mill in Copper Ore Mining Process
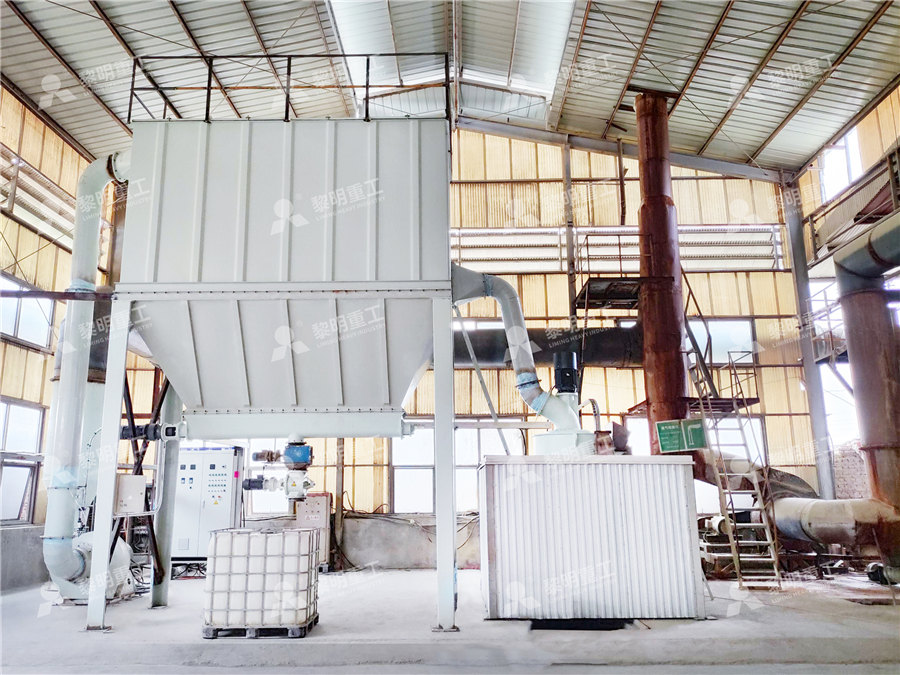
(PDF) Performance Comparison of the Vertical and
2023年2月23日 Varied types/geometries of stirred mills have been produced by different manufacturers, and the comparison task has been accomplished for some of the technologies, ie, Tower mill vs IsaMill2020年8月12日 This study shows the performance of a currently running vertical roller coal mill (VRM) in an existing coalfired power plant In a power plant, the coal mill is the critical equipment, whose An investigation of performance characteristics and 2024年9月16日 the mill grinding chamber, in which the vertical agitator screw is located, together with a charge of grinding media and grinding material in slurry form Highgrowth markets in copper, ironore, gold, leadzinc ores, mineral sands and rareearth metals drive increasing demand for fine grinding to maximize recoveryEIRICH TowerMill Vertical agitated media mill2024年3月1日 The study area of this paper is the Jiangjun Gobi No 1 Openpit Coal Mine field, which is located in the southeast of the Junggar Basin, Xinjiang Uygur Autonomous Region, ChinaGeological exploration of coal mine burnt rock and
.jpg)
The liberation effect of magnetite fine ground by vertical stirred mill
2012年7月1日 A magnetite middling was used to compare the liberation effect of the magnetite fine ground by a vertical stirred mill and a ball mill The magnetite middling contained a high content of magnetite intergrowth with the particle size mainly distributed in the range of 40–150 μmThe new generated −38 μm products were concentrated by magnetic separationMetso High Gradient Magnetic Separators (HGMS) are designed to recover weakly magnetic material from nonmagnetic matter and can be used for many applications including the processing of iron ores, rare earths and other weakly magnetic minerals, which are not normally treatable by ordinary magnetic separators Explore High Gradient Magnetic Magnetic separation Metso6 天之前 HLM series vertical mill is a largescale, highyield, and energysaving grinding product developed by FTM Machinery using advanced grinding and external circulation technology, combined with years of milling production experience coal vertical mills, slag vertical mills, and ultrafine vertical mills 1 Cement vertical mill Raw materials Energysaving and Efficient Vertical Roller Mill Fote MachineryCLUM series ultrafine vertical roller millwas produced by Shanghai Clirik Machinery Co, Ltd Relying on 12 years of experience in the production of ultrafine powder and based on German and Taiwan ultrafine vertical mill technologies The top technical team members were joined this project Besides, highquality wearresistant parts are used to develop milling equipment which Ultra fine vertical roller millUltra Fine Millultramill
.jpg)
Full article: Reliability assessment of the vertical roller mill
1 Introduction The vertical roller mill (VRM) is heavy mechanical equipment that used in the cement materials industry to process cement, slag, and coal cinder (Pani Mohanta, Citation 2015)The equipment always needs to work in the environment of heavy load, high temperature, high pressure, high corrosiveness, electromagnetic radiation interference, and multifield The electromagnetic vibration feeder feeds uniformly, is easy to adjust, small in size, lightweight, easy to maintain and saves power The significant parts of a vertical grinding mill is made from highquality castings and rigorous processes ensure high durability An opentype dust collector is used to filter out excess air from the mill Vertical Grinding Mill: How it Works, Application And 2022年2月28日 Using an electromagnetic mill, a comparison between these two grinding environments has shown; while wet grinding requires around 16 kW of energy, the dry condition needs 3 kW for the same condition highspeed stirred mills, in which the rotational speed of the stirrer tip is usually higher than 15 m/s, are able to produce 5 μm or even Grinding SpringerLink2014年10月20日 The basis for this lies in its high energy density (310 times higher than other HEM), the ability of continuous operation, high number of operating parameters (circumferential velocity, ball Regrind of metallic ores with vertical mills: An overview of