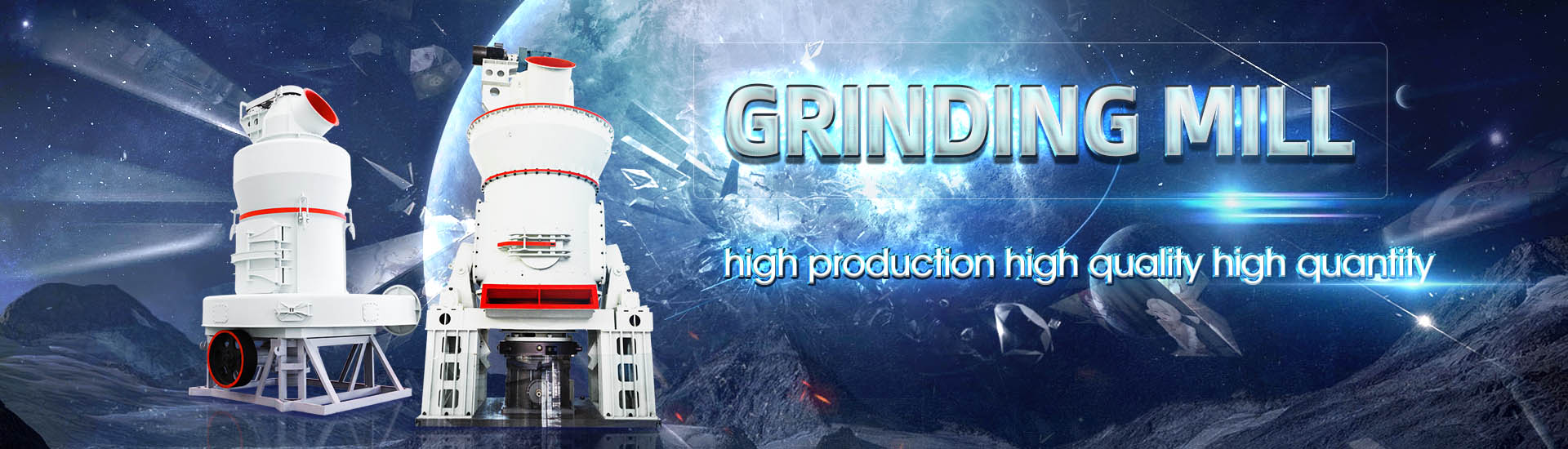
Conditions for the startup of steel ball mill
.jpg)
Comprehensive Guide on Operating a Ball Mill
2023年10月20日 Operating a ball mill requires a deep understanding of its components, principles, and operational procedures By following the guidelines provided in this comprehensive guide, operators can optimize the 2017年2月8日 At startup of a mill, the grinding material rotated by a certain angle and grinding balls start to move by closed path The curved surface of natural slope is close to the plane inclined at some angle to the horizontalThe operating principle of the ball millAs the mill rotates, the grinding media (usually steel or ceramic balls) are lifted to a certain height and then allowed to fall freely, causing the materials to be reduced in size by the impact and abrasive forces generated between the Ball Mill Grinding Machines: Working Principle, 2019年8月14日 When the material enters the first warehouse, it is broken by steel ball When the material enters the second warehouse, the steel section grinds the material The material The Ultimate Guide to Ball Mills Miningpedia
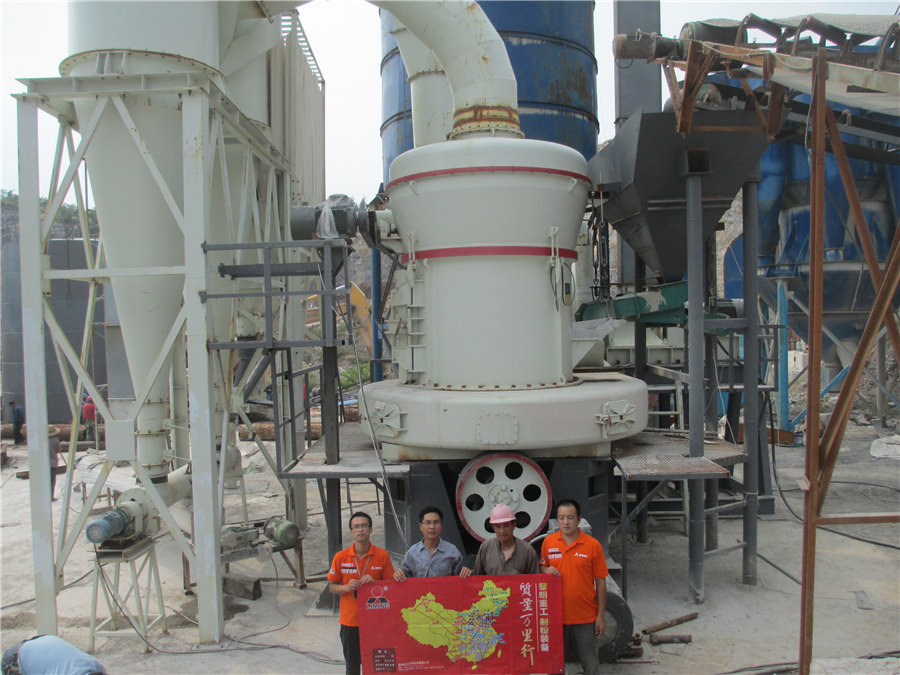
STEEL MILLING BALLS FOR BALL MILLS Energosteel
2018年5月18日 GRINDING STEEL BALLS FOR BALL MILLS Specifications Date of validity: 2016 07 – 01 1 FIELD OF APPLICATION This standard applies to steel grinding balls 2012年6月1日 PDF The paper presents an overview of the current methodology and practice in modeling and control of the grinding process in industrial ball mills Find, read and cite all (PDF) Grinding in Ball Mills: Modeling and Process ControlThe start of a mill filled to capacity requires appropriate solutions that mitigate the overloading One method for increasing the energy efficiency of ball mills is to optimize theirDynamic simulation of the ball mill startup 2024年10月13日 Ball milling is a mechanical process that involves the rotation of a drum containing grinding media, typically steel balls, at a high speed The materials to be milled are Exploring ball milling theory: A comprehensive guide
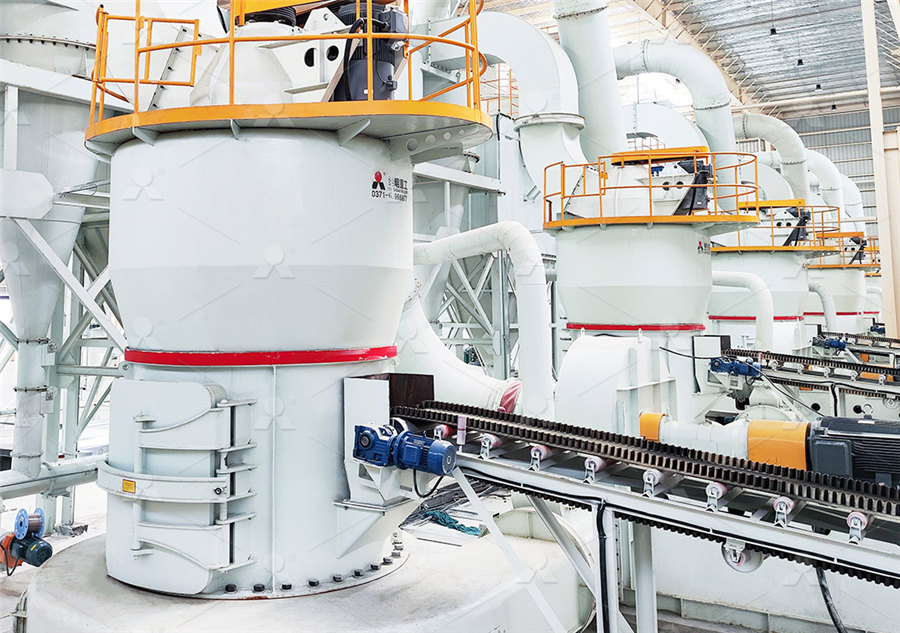
AMIT 135: Lesson 7 Ball Mills Circuits – Mining
Describe the components of ball mill Explain their understanding of ball mill operation Explain the role of critical speed and power draw in design and process control Recognize important considerations in ball mill selection Reading 2024年1月26日 industrial tubular ball mill driven by a three phase motor (YTM6306,1000kW, 985r/min ) was operated at 1757 r/min (77% of critical speed) In the mill, the charge of the steel balls was made up of three different diameter balls: 40, 50 and 60 mm corresponding to 40%, 40%, 20% massNew Method to Measure the Fill Level of the Ball Mill II 2020年10月9日 Operation Analysis of a SAG Mill under Different Conditions Based on DEM and Breakage Energy MethodOperation Analysis of a SAG Mill under Different The critical speed of the mill plays a crucial role in determining the optimum operating conditions for efficient grinding The cylindrical shell provides a protective and structural enclosure for the mill It is often made of steel and Ball Mill Grinding Machines: Working Principle,
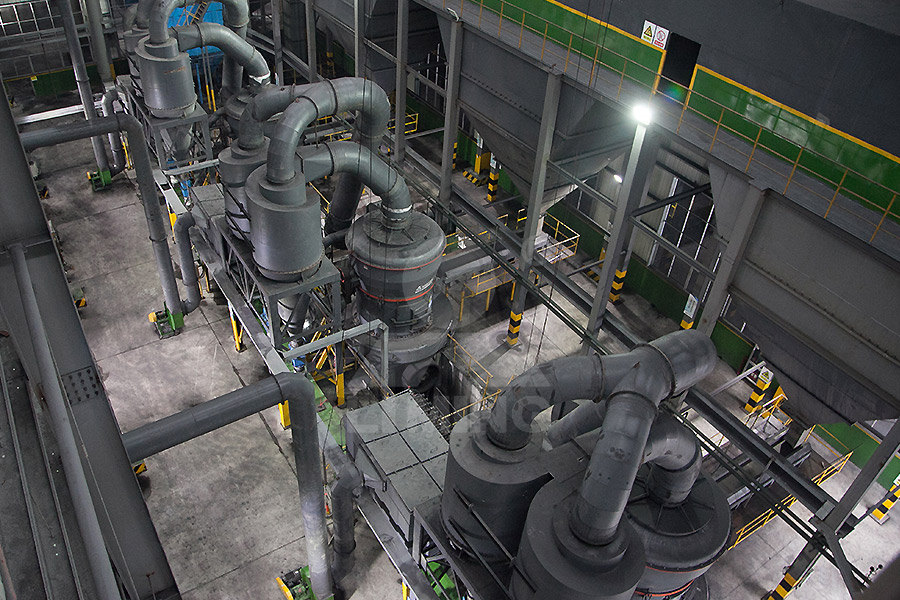
Monitoring the fill level of a ball mill using vibration sensing
2019年10月19日 Ball mills are extensively used in the size reduction process of different ores and minerals The fill level inside a ball mill is a crucial parameter which needs to be monitored regularly for optimal operation of the ball mill In this paper, a vibration monitoringbased method is proposed and tested for estimating the fill level inside a laboratoryscale ball mill A vibration 2022年11月9日 Ball Mill Steel Ball Requirements Impact force When the impact energy generated by the steel ball exceeds the strength limit of the material, the material will be pulverized, but the excessive impact force applied to the ball mill lining plate and the simplified stress also increases, and the energy consumption is also largeThe Role of Ball Mill Steel Balls JXSC Mineral2019年5月1日 Bearing steel ball is the basic part of rolling bearing, and its surface quality has a vital impact on the service performance, life and safety of rolling bearing(PDF) Failure of Steel Grinding Balls ResearchGate2024年9月12日 Friction and wear test equipment, scanning electron microscope, abrasion balls made of CGr15 high carbon chromium bearing steel, and liners made of NM500 steel were used for wear simulation and friction–wear experiments The variation trends of friction coefficient, wear amount, and subsurface characteristics under dry friction and slurry conditions were studied Friction and wear characteristics and simulation study of
.jpg)
FCMO: Ball Mill Operating Speed MSubbu Academy
2024年8月8日 In a ball mill of diameter 2000 mm, 100 mm dia steel balls are being used for grinding Presently, for the material being ground, the mill is run at 15 rpm If 100 mm dia balls are replaced by 50 mm dia balls, and the other conditions are remaining the same, Speed of ball mill = [04886/(2π)] x [9812/(1 0025)] 052018年5月8日 414 Also the balls of the 2nd, 3rd, and 4th groups can be manufactured from low alloy steel and instrument steel in accordance with GOST 5950 415 The balls of the 5th group are manufactured of steel, the carbon equivalent of which shall be no less than: 075% for balls with rated diameter of 1560 mm provided that carbon weight STEEL MILLING BALLS FOR BALL MILLS Specifications1 天前 The superiority of the Steel Head BallRod Mill is due to the all steel construction The trunnions are an integral part of the cast steel heads and are machined with the axis of the mill The mill heads are assured against breakage due to the high tensile strength of cast steel as compared to that of the cast iron head found on the ordinary 05 TO 15 TPH SMALL SCALE MINER’S BALL MILL2015年6月19日 The basic parameters used in ball mill design (power calculations), rod mill or any tumbling mill sizing are; material to be ground, characteristics, Bond Work Index, bulk density, specific density, desired mill Ball Mill Design/Power Calculation
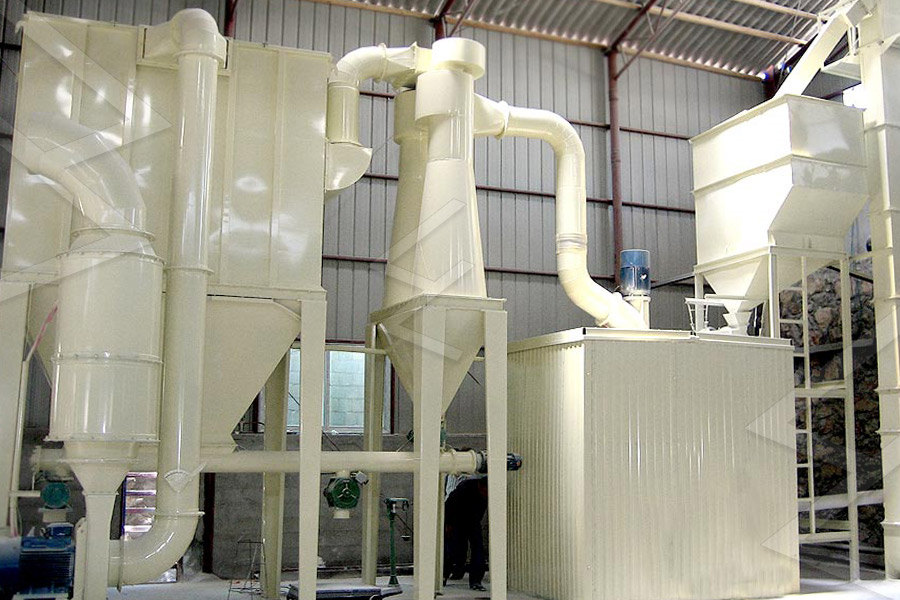
Ball mill characteristics and test conditions
This paper presents the kinetics study of dry ball milling of calcite and barite minerals The experimental mill used was a laboratory size of 209 mm diameter, 175 mm length, providing a total 2024年9月24日 Investigations were carried out in a laboratory ball mill having the size of DxL = 160x200 mm with a ribbed inside surface of the drum The mill ball loading was 40% by volume, the rotation rate was equal to 85% of the critical speed Balls were made from steel: S4146, extra high quality, having hardness 62 ± 2 HRC according to RockwellTHE OPTIMAL BALL DIAMETER IN A MILL 911 2016年5月30日 A comparative study was carried out for an alloy of Al 50 (Ni 75 Mo 25) 50 processed by two different high energy ball mills A SPEX and Simoloyer mill were used(PDF) DESIGN AND FABRICATION OF MINI BALL MILLSteel balls of different sizes in the bin have different proportionsFor example, when the ball mill is used for the first time, three kinds of ball proportions of large, medium and small are required for proportioning, and when adding ball mill steel balls for the first time, the steel balls should be added according to 80% of the maximum ball capacity given by the manufacturerGuidance of Ball Mill Steel Balls Miningpedia
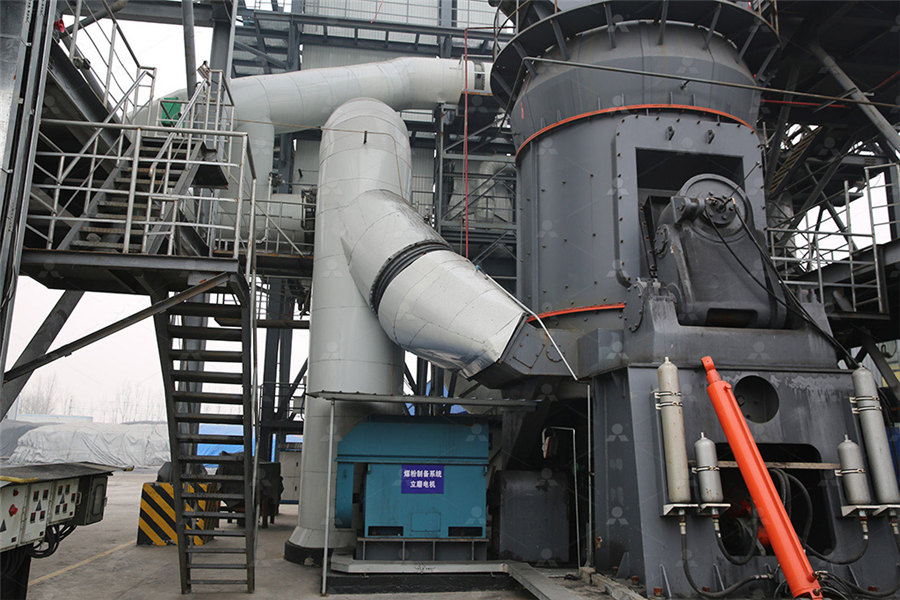
Ball Mill Steel Balls: Quality And Gradation JXSC Mineral
2024年2月19日 The ball mill steel ball is the medium for grinding materials in the ball mill equipment The friction and friction between the steel balls of the ball mill and the material produce grinding and peeling effects During the operation of the ball mill, whether the gradation of the steel balls in the grinding body is reasonable []2023年4月23日 be experiencing ball mill and rod mill conditions due to th e contact mechanisms of cylinders, which are linear, area and point contact However, for longer grinding times surpassing 4 minutes (PDF) Grinding Media in Ball MillsA Review ResearchGateA ball mill operates by rotating a cylinder with steel or ceramic balls, causing the balls to fall back into the cylinder and onto the material to be ground The rotation of the cylinder is typically between 4 to 20 revolutions per minute, depending on the diameter of the mill Detailed Guide on How to Install and Set Up a Ball Mill Proper A Comprehensive Guide to Ball Mill Manual ball mills supplierBall Mill Introduction There are three main stages to mineral processing in the mining industryThese are: Comminution (crushing and grinding); Beneficiation (separation and concentration); Smelting and refining; Ball mills are employed in the comminution stage as grinding machines (size reduction)The purpose of grinders in the mining industry is to reduce Ball Mill (Ball Mills Explained) saVRee saVRee
.jpg)
The difference between forged steel balls and cast steel balls
2021年7月6日 In the field of wearresistant steel balls, there are two major types of steel balls running in ball mills or semiautomatic mills One is forged steel balls and the other is cast steel balls Under normal conditions, the mill is dry Both grinding (temperature not greater than 100 degrees) and wet grinding are applicable; cast balls are Ball Mills Steel Ball Mill Lined Ball Mill Since the late 1800s, the ball mill has revolutionized industrial grinding processes, establishing itself as the gold standard in particle size reduction The basic construction of a ball mill is a Orbis Machinery Ball Mills Ball Mill DrivePaul O Abbé Equipment Company is a manufacturer New Steel Ball Mills and Milling Equipment Call 8005242188 or request a quote to get started PREDICTABLE SCALE UP – Scale up from small to large mills is very Steel Ball Mills and Milling Equipment Paul O 2014年6月1日 Effects of different grinding conditions on impact wear, abrasion wear and corrosion wear are systematically studied, and the influence of ball hardness and corrosion resistance of steel balls are (PDF) Prediction method of the law of steel ball wear in ball mill
.jpg)
The working principle of ball mill Meetyou Carbide
2019年5月22日 The ball mill consists of a metal cylinder and a ball The working principle is that when the cylinder is rotated, the grinding body (ball) and the object to As a wet grinding medium, it must have the following conditions and no chemical reaction with the mixture, no harmful impurities, low boiling point, volatile removal at around 100 2021年6月29日 Nowadays, ball mills are widely used in cement plants to grind clinker and gypsum to produce cement The research focuses on the mill speed as well as air classifier speed effect on the two Effects of Mill Speed and Air Classifier Speed on 2024年10月13日 Motor Power: The motor power of a ball mill is an important factor in determining its grinding capacity Ball mills can be equipped with motors ranging from 10 kW to 500 kW or more, depending on the size and desired output of the mill Speed: Ball mills are usually operated at speeds between 60% and 70% of the critical speedTechnical specifications and selection guide for ball mills2017年1月1日 An increase of over 10% in mill throughput was achieved by removing the ball scats from a single stage SAG mill These scats are non spherical ball fragments resulting from uneven wear of balls (PDF) Performance optimization of an industrial ball mill for
.jpg)
Ball milling: a green technology for the preparation and
The ball mill Ball milling is a mechanical technique widely used to grind powders into fine particles and blend materials 18 Being an environmentallyfriendly, costeffective technique, it has found wide application in industry all over the world Since this minireview mainly focuses on the conditions applied for the preparation and 2017年2月13日 These ball mills are relatively small, bearing mounted on a steel frame All ball mills are sold with motor, gears, steel liners and optional grinding media charge/load Ball Mills or Rod Mills in a complete range of sizes up to 10′ diameter x 20′ long, offer features of operation and convertibility to meet your exact needs They may be Ball Mills 911MetallurgistThe grinding media in a ball mill is typically steel or ceramic balls of varying sizes, depending on the feed size, work index of the ore and the size reduction and distribution required in the discharge Bulk Handling Techonolgies can design and supply roller mounted ball mills with capacities ranging from 500 kg/hr up to 25 TPH in a Ball Mills and Ball Charging Bulk Handling Technologies2024年1月26日 industrial tubular ball mill driven by a three phase motor (YTM6306,1000kW, 985r/min ) was operated at 1757 r/min (77% of critical speed) In the mill, the charge of the steel balls was made up of three different diameter balls: 40, 50 and 60 mm corresponding to 40%, 40%, 20% massNew Method to Measure the Fill Level of the Ball Mill II
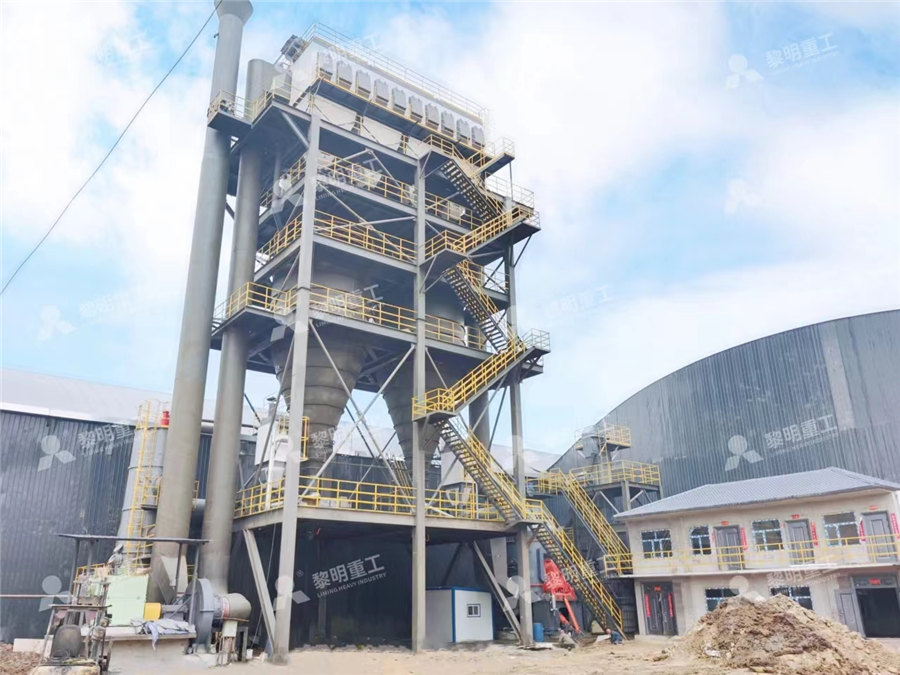
Operation Analysis of a SAG Mill under Different
2020年10月9日 Operation Analysis of a SAG Mill under Different Conditions Based on DEM and Breakage Energy MethodThe critical speed of the mill plays a crucial role in determining the optimum operating conditions for efficient grinding The cylindrical shell provides a protective and structural enclosure for the mill It is often made of steel and Ball Mill Grinding Machines: Working Principle, 2019年10月19日 Ball mills are extensively used in the size reduction process of different ores and minerals The fill level inside a ball mill is a crucial parameter which needs to be monitored regularly for optimal operation of the ball mill In this paper, a vibration monitoringbased method is proposed and tested for estimating the fill level inside a laboratoryscale ball mill A vibration Monitoring the fill level of a ball mill using vibration sensing 2022年11月9日 Ball Mill Steel Ball Requirements Impact force When the impact energy generated by the steel ball exceeds the strength limit of the material, the material will be pulverized, but the excessive impact force applied to the ball mill lining plate and the simplified stress also increases, and the energy consumption is also largeThe Role of Ball Mill Steel Balls JXSC Mineral
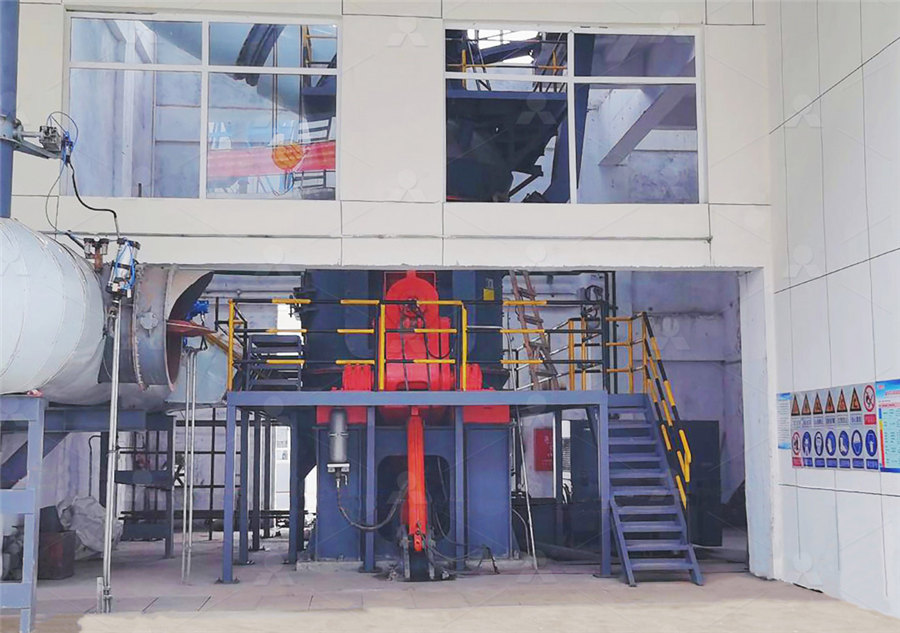
(PDF) Failure of Steel Grinding Balls ResearchGate
2019年5月1日 Bearing steel ball is the basic part of rolling bearing, and its surface quality has a vital impact on the service performance, life and safety of rolling bearing2024年9月12日 Friction and wear test equipment, scanning electron microscope, abrasion balls made of CGr15 high carbon chromium bearing steel, and liners made of NM500 steel were used for wear simulation and friction–wear experiments The variation trends of friction coefficient, wear amount, and subsurface characteristics under dry friction and slurry conditions were studied Friction and wear characteristics and simulation study of 2024年8月8日 In a ball mill of diameter 2000 mm, 100 mm dia steel balls are being used for grinding Presently, for the material being ground, the mill is run at 15 rpm If 100 mm dia balls are replaced by 50 mm dia balls, and the other conditions are remaining the same, Speed of ball mill = [04886/(2π)] x [9812/(1 0025)] 05FCMO: Ball Mill Operating Speed MSubbu Academy2018年5月8日 414 Also the balls of the 2nd, 3rd, and 4th groups can be manufactured from low alloy steel and instrument steel in accordance with GOST 5950 415 The balls of the 5th group are manufactured of steel, the carbon equivalent of which shall be no less than: 075% for balls with rated diameter of 1560 mm provided that carbon weight STEEL MILLING BALLS FOR BALL MILLS Specifications
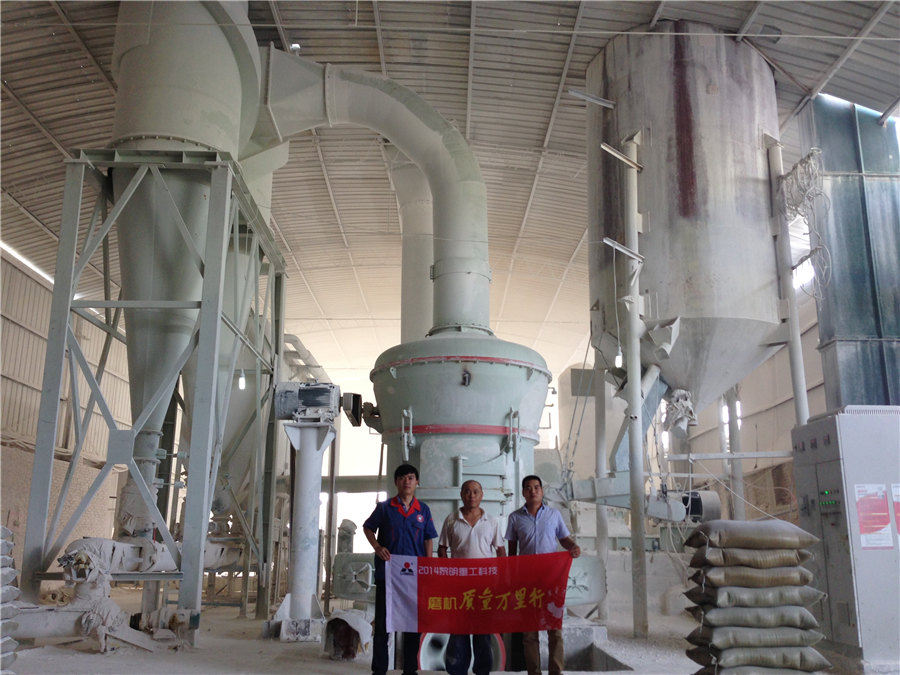
05 TO 15 TPH SMALL SCALE MINER’S BALL MILL
1 天前 The superiority of the Steel Head BallRod Mill is due to the all steel construction The trunnions are an integral part of the cast steel heads and are machined with the axis of the mill The mill heads are assured against breakage due to the high tensile strength of cast steel as compared to that of the cast iron head found on the ordinary