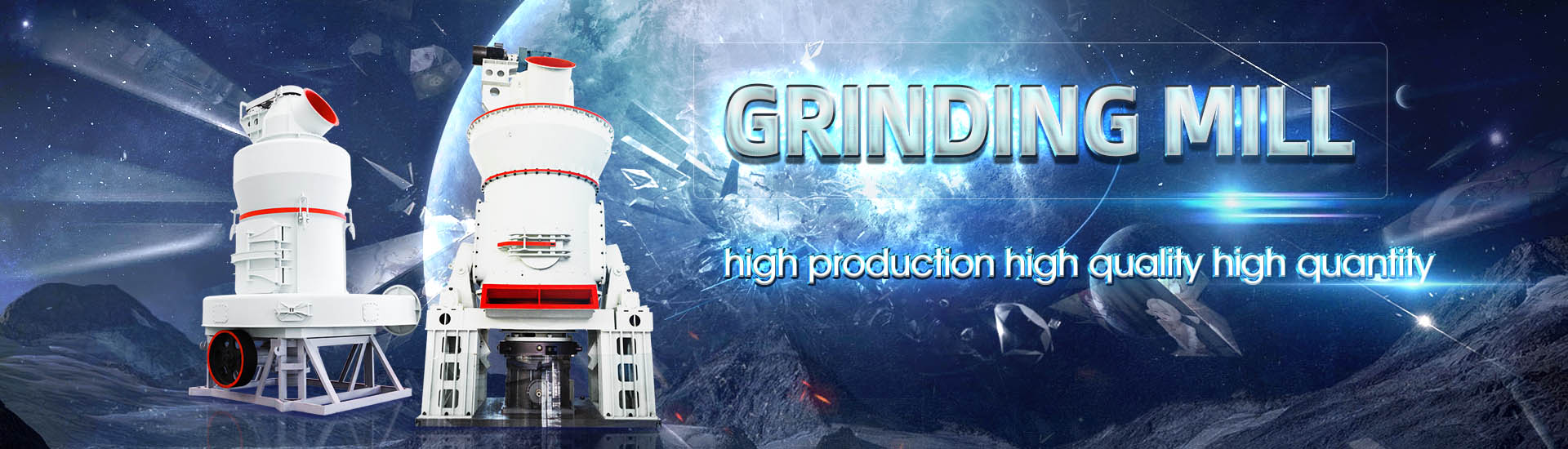
Are slag micro powder die castings durable
.jpg)
Structure and Properties of Slags Used in the Continuous
The primary tasks of a mould slag in specialised casting are identical to those in conventional casting, namely: (i) The liquid slag pool must seal off the steel and prevent oxidation (ii) The powder bed must provide thermal insulation to prevent the steel from freezing (iii) The liquid The structure is principally defined by (i) the degree of polymerisation of the slag (ii) cation effects and (iii) the physical state of the slag (liquid, glass or crystalline phase and granules or powder Structure and Properties of Slags Used in the Continuous Casting 2016年11月29日 For increased casting speeds ie up to 8 m/min, slag infiltration and in particular the control of mould heat transfer via crystallisation of the slag film becomes even more important It(PDF) Understanding mould powders for high 2021年5月24日 Based on these findings, promising mold slag compositions are designed and characterized in the laboratory using a furnace crystallization test, mineralogical investigations, and the single/double hot thermocouple New Mold Slag Compositions for the
.jpg)
Thermochemical Evaluation of Cast Iron Slags Generated
2023年1月9日 It is accepted that slag is a part of the cast iron process by most foundries, and it is given little attention as long as it is manageable However, some slag compositions have a 2016年11月29日 Comparing to mould powders for conventional slab casting, mould powder for thin slab casting have lower slag viscosity and increased basicity and solidification temperature For increased casting speeds, ie Understanding mould powders for highspeed 2021年3月18日 rinefree mold powder compositions for casting two types of peritectic steel were used In contrast to the results of Wang et al[11,12] promising results, including uniform New Mold Slag Compositions for the Continuous 2018年3月1日 The main requirements for mould powder for thin slab casting (casting speeds up to 6 m/min) are proper powder melting, undisturbed slag infiltration followed by adequate Understanding mould powders for highspeed casting
.jpg)
How to Manipulate Slag Behaviour in the Mould SpringerLink
2017年6月7日 The following processes are examined: (1) Thermal insulation of the powder bed and vertical heat transfer (2) Melting rate of the mould powder (3) Formation of a slag pool (4) To reduce the occurrence of stickers and longitudinal cracks during continuous casting (CC) of peritectic steel, herein, the use of a mold slag with high basicity and adequate lubrication is proposOptimization of Mold Slag for Continuous If you`re looking for the best provider of LowPressure Die Casting Services, you can count on Inox Casting We have more than 20 years of experience in unique RD prototype designing, lowpressure die casting moulding, cold chamber Low Pressure Die Casting Services Expert Inox 2023年8月11日 Diecast zinc alloy: 6769g/cm 3; 2) Melting point: Pure zinc: 419°C; Zinc alloy: 387390°C; Die casting temperature: 390410°C; 3) The most commonly used diecast zinc alloy is ZAMAK 3 II Models of DieCast Zinc Zinc Alloy Die Casting Basics You Should Know
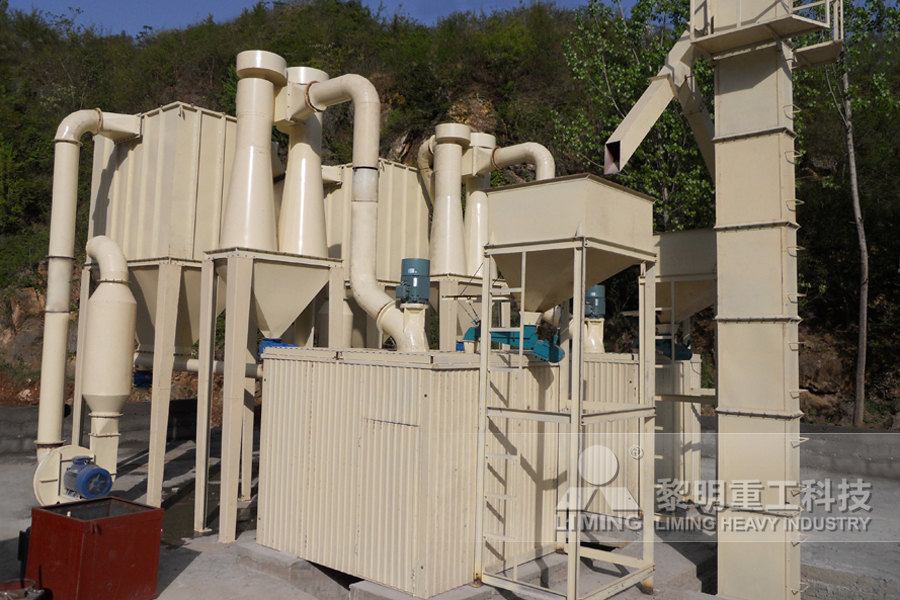
Understanding Porosity in Casting: Causes,
A leading die casting factory in China Since 2010, we've been delivering precision and innovation in aluminum, zinc, and magnesium die casting Our stateoftheart facilities and expert team ensure tailored solutions for your 2016年11月29日 The development and application of mould powder for highspeed continuous casting of steel is described For thin slab casting, the main requirements are proper powder melting, undisturbed slag (PDF) Understanding mould powders for highspeed casting2021年12月10日 This die casting finishing class entails applying an alloydependent surface coating to limited areas of casting It has maximum value in microinches and is suitable for relatively small parts such as gaskets and Oring seals Powder coating surface defect Die casting surface finish defects are quite a number and often caused by several Die Casting Surface Finish: The Definitive FAQ Guide2022年3月9日 The microstructure of slag film solidified on the inner wall of mold in continuous casting of low carbon steel has been examined experimentally and analyzed theoretically A puzzle for the crystallization sequence has been solved by this work, which is useful to guide the modification of slag microstructure in efficient casting of advanced steels The experiments The Microstructure Formation in Slag Solidification at
.jpg)
Die Casting: Process, Types, Materials, Advantages and
Die casting is a metal casting process that involves feeding molten nonferrous alloys into dies under high pressure and at high speed to rapidly create molded products The main materials used in die casting are alloys of aluminum, magnesium and zinc powder coating, wet plating, and many more Types of Die Casting The aim of all die 2022年7月25日 Applications Differences Between Injection Molding and Die Casting Die casting is ideal for fabricating medium and smallsized parts with intricate details It is used to cast industrial and commercial products like faucets, automobiles, hard wares, sinks, gears, etc Provided the metal parts are not too large, die casting is your ideal choiceDie Casting vs Injection Molding: A Detailed Comparison2021年4月21日 The die casting process today has been well researched and systematically quantiied in terms of thermodynamics, heat transfer and luid low parameters This technology has been transferred to the die casting industry, where its use has made a signiicant improvement in the design of die casting dies, the die steel used in die construction,Design and Develoopment Sourcebook: Product Design 2023年12月28日 1 What are the most common surface finishing for aluminum die castings? The most prevalent surface coating options for aluminum die castings include anodizing, powder coating, chromate conversion coating, and electrophoretic painting Each method offers unique benefits, addressing aesthetic, protective, and functional requirements 25 Common Surface Finishing Options For Aluminum Die Castings
.jpg)
Slag inclusions Foundry Gate
2018年7月10日 97 Description of defects: Slag inclusions Fig 44: Slag inclusions in the top part of a grey iron casting, in some cases still there, in others already removed by shot blasting Scale: 10 mm = 8 mm Fig 45: Slag inclusions and gas defects under the surface of a grey iron casting Inclusions caused by turbulence Scale: 10 mm = 008 mm2023年9月22日 Originalarbeit TABLE 1 Chemical composition of the used mould powdersin wt% Powder F Na2O MgO Al2O3 SiO2 CaO MnO C CaO/SiO2 A 82 80 20 34 309 386 00 60 125 B 81 68 12 47 318 381 10 Slag Rim Formation of two Mould Powders used for 2022年7月19日 Macro shrinkages look like jagged lines or marks and are visible to the eyes On the other hand, the micro holes look angular and can be seen with microscopes Warping A slag inclusion firmly attaches to the casting, 17 Types of Casting Defects: Understanding 2023年5月1日 Due to its high hardenability, strength, toughness, and softening resistance, AISI H13 steel is frequently used as a hotworking die steel in hot forging, extrusion, die casting, and other industries [1, 2]It is crucial to develop hot working die steels with excellent performance because they must function for an extended period of time in harsh conditions (high Cleanliness improvement and microstructure refinement of H13 die
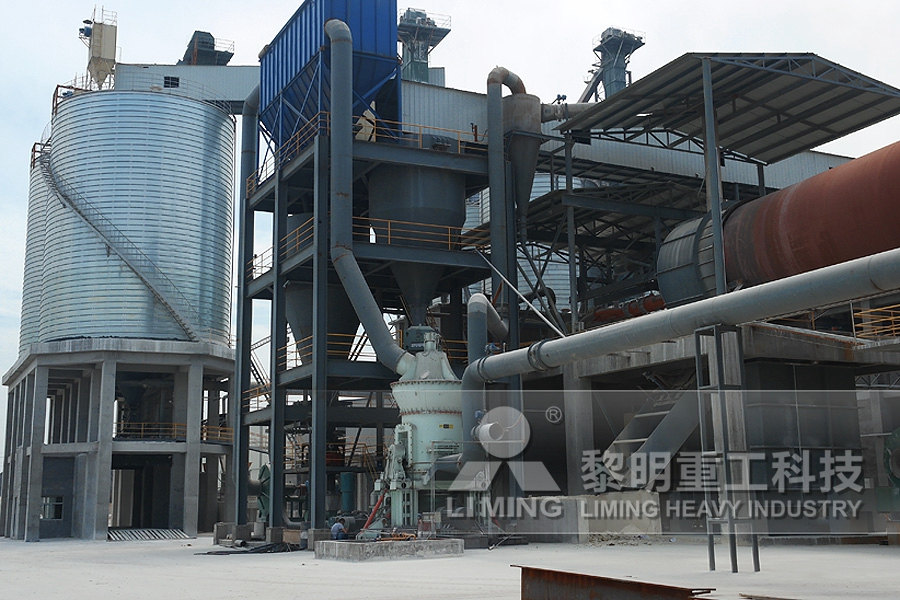
Die Casting Powder Metal
2023年9月27日 Constructed from durable materials like steel or aluminum, this mold is meticulously designed to withstand the elevated temperatures and pressures integral to the diecasting process Initiating the mold design process entails crafting a ComputerAided Design (CAD) model of the required moldThe primary tasks of a mould slag in specialised casting are identical to those in conventional casting, namely: (i) The liquid slag pool must seal off the steel and prevent oxidation (ii) The powder bed must provide thermal insulation to prevent the steel from freezing (iii) The liquid slag film must provide lubrication to the shellStructure and Properties of Slags Used in the Continuous Casting Prediction of Slag Inclusion Casting Defect in Gravity Die Castings using ADSTEFAN Casting simulation software Slag inclusions casting defect are nonmetallic impurities that can form during the melting and pouring of metal They typically arise from the reaction of molten metal with oxides formed due to more contact time with air during Prediction of Slag Inclusion Casting Defect in Gravity Die Castings 2017年12月11日 Two different mould powders are used for casting peritectic steel grades at the voestalpine Stahl Linz GmbH slab casting machine Powder A forms significantly larger slag rims than Powder B Slag Rim Formation of two Mould Powders used for Casting
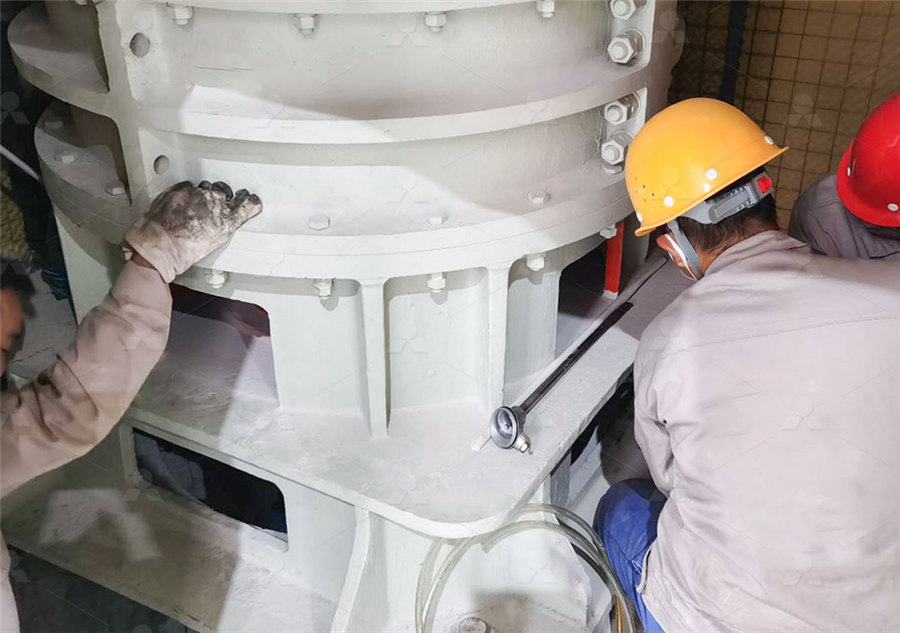
(PDF) Mould Powder Requirements for Highspeed Casting
2008年2月1日 The temperature range across the mold powder slag in the interfacial gap between the continuous casting mold and strand leads through different transformation behavior into crystalline phases2024年11月25日 The calculation formula for the selection of diecasting machine: Diecasting machine clamping force (t) = 14 * casting projected area * ratio of the projected area of the die castingthe orthographic projected area of the die casting * modulus (CM2)How To Calculate Pressure Die Casting Tonnage Becu2021年3月18日 ing of lowcarbon steel, the Ffree mold slag exhibited a similar melting performance, absorption ability for alumina, and slag pool thickness to the Fcontaining mold slag The surfaces of the slabs were of good quality[27] During the development of mold slags for casting highAl steels, it was found that these slags show an increasedNew Mold Slag Compositions for the Continuous t is the powder consumption (with units of kg (powder) tonne −1 (steel)) and f* is the fraction of powder forming slag2) Powder consumption, Q s, with units of kg slag m −2 (of mould) is a measure of the lubrication supplied to the shell and is calculated via Eq (1) where R*=2(w+t)/wt, ie the ratio of (mould surface area/volume) w=width andStructure and Properties of Slags Used in the Continuous
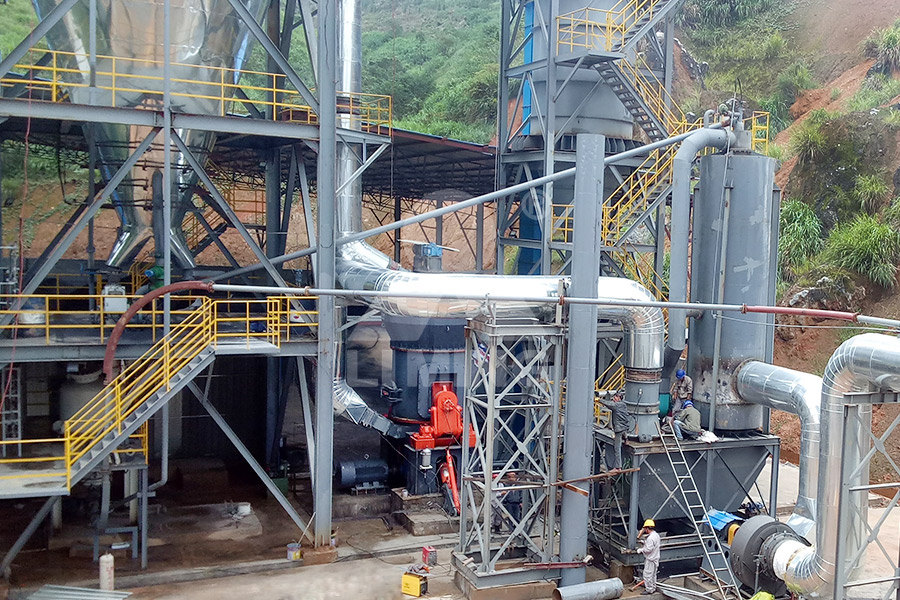
How to Manipulate Slag Behaviour in the Mould SpringerLink
2017年6月7日 It is important that the free carbon content of the casting powder should be at a level where it allows the required, powder consumption to be attained, ie Q slag MR ≥ Q slag MR req Fig 48 Powder consumption, Q slag s req as a function of R* , the ratio of (surface area/volume) of the mould, diamond billets; = blooms; Δ = slabs; = thin 2020年6月10日 Highpurity Al 2 O 3 refractory is suitable for high MnO containing slag M Wu, J Li, A Kharicha, A Ludwig, “Multiphase modelling of the microsegregation in Ingot casting”, 1st International Conference on Ingot Casting, Rolling and Forging, 2012 “A process for developing continuous casting mouldpowder for steel industries Refractory for Casting SpringerLink2023年9月11日 The downside of plaster molds is that they can only be used for casting lowmeltingpoint metals like aluminum alloy 3 Ceramic Mold Casting Ceramic mold casting is accomplished in much the same way as sand and plaster mold casting but uses a ceramic slurry to form the mold instead of sand or plaster Most often, metallic patterns are used Unlike Metal Casting Process: Guide to Types of Casting, Methods 1 天前 Gas porosities appear in the body of the die casting parts, round or oval, with smooth surface and bright white or bright yellow color The machined surface can be identified by visual inspection after machining, and the nonmachined surface 13 Die Casting Defects and How to Avoid Them
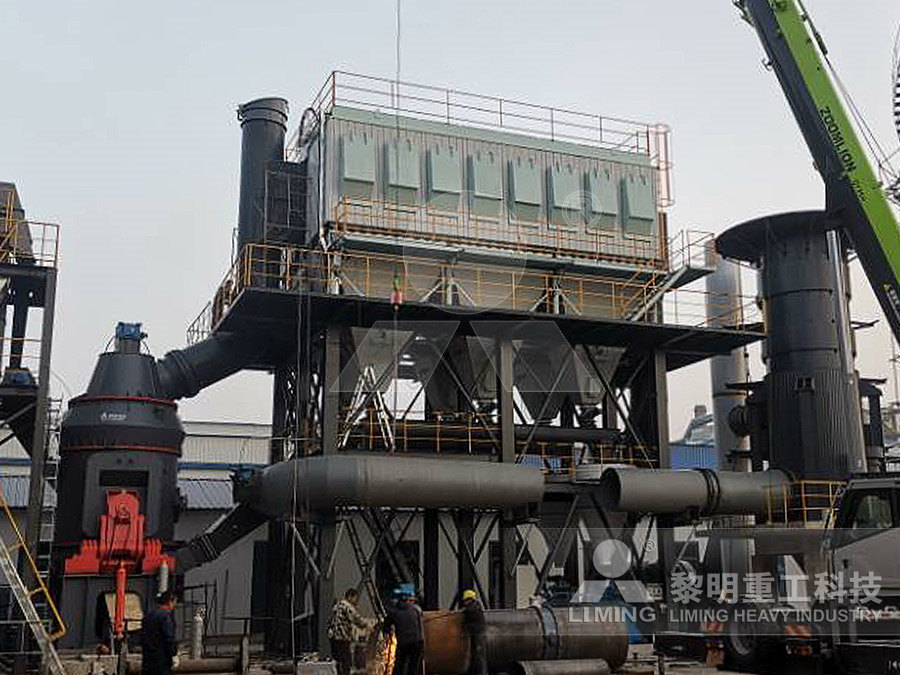
The Microstructure Formation in Slag Solidification at
2022年4月2日 The microstructure of slag film solidified on the inner wall of mold in continuous casting of low carbon steel has been examined experimentally and analyzed theoretically2021年7月13日 A transient threedimensional mathematical model is developed to study the slag entrapment in a continuouscasting mold The unsteady turbulent flow is computed using the large eddy simulation (LES) The subgrid scale structure is modeled by Smagorinsky–Lilly model The movements of discrete bubbles, as well as three continuous phases (airslagsteel) are Evaluation of Slag Entrapment in Continuous Casting Mold2021年4月25日 Generally, diecasting is only intended for large batch production because it is costly and complicated, and only largescale production can absorb the costs to make it costeffective It is not a practical choice for smallscale production Specific Weight Requirements The diecasting process has certain weight specifications that must be What Are the Pros and Cons of DieCasting? SEI CASTINGS2024年3月15日 The two main types of pressure die casting are low (LPDC) and highpressure (HPDC) die casting LPDC requires the metal to be injected into the mold at low pressures, between around 2–15 psi, and takes a more controlled and gentle approach which takes longer because the inert gas pressure gently forces the alloy upwards into the moldAll About Pressure Die Casting Xometry
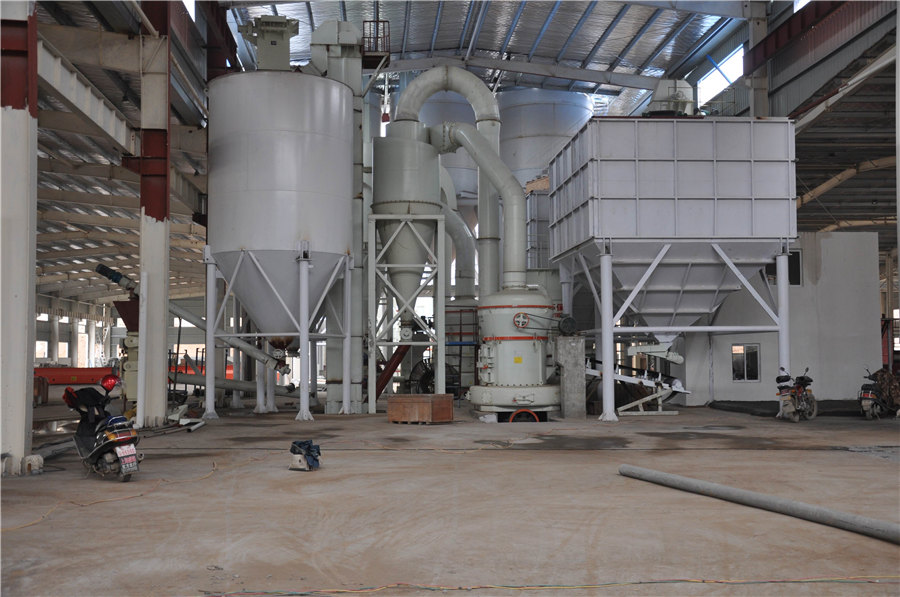
Low Pressure Die Casting Services Expert Inox
If you`re looking for the best provider of LowPressure Die Casting Services, you can count on Inox Casting We have more than 20 years of experience in unique RD prototype designing, lowpressure die casting moulding, cold chamber 2023年8月11日 Diecast zinc alloy: 6769g/cm 3; 2) Melting point: Pure zinc: 419°C; Zinc alloy: 387390°C; Die casting temperature: 390410°C; 3) The most commonly used diecast zinc alloy is ZAMAK 3 II Models of DieCast Zinc Zinc Alloy Die Casting Basics You Should KnowA leading die casting factory in China Since 2010, we've been delivering precision and innovation in aluminum, zinc, and magnesium die casting Our stateoftheart facilities and expert team ensure tailored solutions for your Understanding Porosity in Casting: Causes, 2016年11月29日 The development and application of mould powder for highspeed continuous casting of steel is described For thin slab casting, the main requirements are proper powder melting, undisturbed slag (PDF) Understanding mould powders for highspeed casting
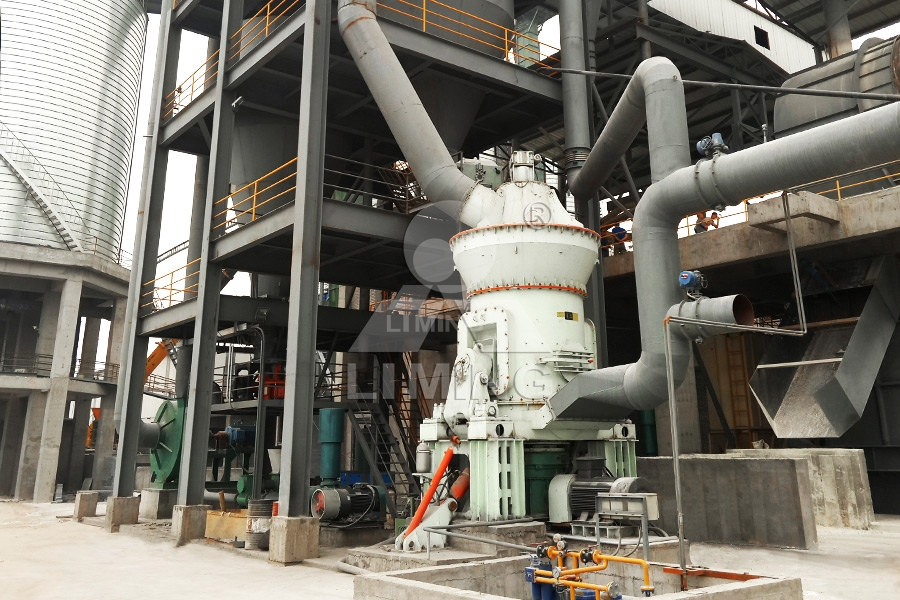
Die Casting Surface Finish: The Definitive FAQ Guide
2021年12月10日 This die casting finishing class entails applying an alloydependent surface coating to limited areas of casting It has maximum value in microinches and is suitable for relatively small parts such as gaskets and Oring seals Powder coating surface defect Die casting surface finish defects are quite a number and often caused by several 2022年3月9日 The microstructure of slag film solidified on the inner wall of mold in continuous casting of low carbon steel has been examined experimentally and analyzed theoretically A puzzle for the crystallization sequence has been solved by this work, which is useful to guide the modification of slag microstructure in efficient casting of advanced steels The experiments The Microstructure Formation in Slag Solidification at Die casting is a metal casting process that involves feeding molten nonferrous alloys into dies under high pressure and at high speed to rapidly create molded products The main materials used in die casting are alloys of aluminum, magnesium and zinc powder coating, wet plating, and many more Types of Die Casting The aim of all die Die Casting: Process, Types, Materials, Advantages and 2022年7月25日 Applications Differences Between Injection Molding and Die Casting Die casting is ideal for fabricating medium and smallsized parts with intricate details It is used to cast industrial and commercial products like faucets, automobiles, hard wares, sinks, gears, etc Provided the metal parts are not too large, die casting is your ideal choiceDie Casting vs Injection Molding: A Detailed Comparison
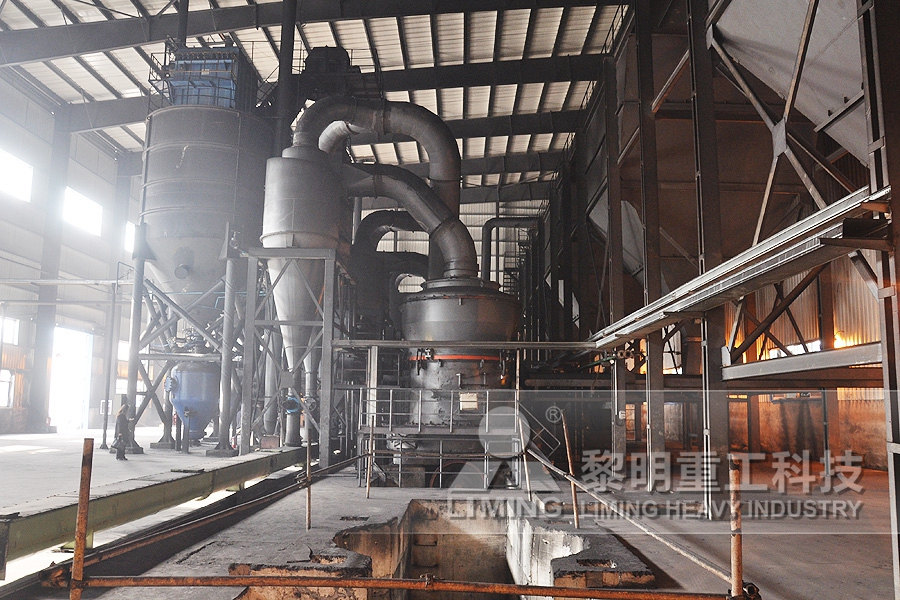
Design and Develoopment Sourcebook: Product Design
2021年4月21日 The die casting process today has been well researched and systematically quantiied in terms of thermodynamics, heat transfer and luid low parameters This technology has been transferred to the die casting industry, where its use has made a signiicant improvement in the design of die casting dies, the die steel used in die construction,2023年12月28日 1 What are the most common surface finishing for aluminum die castings? The most prevalent surface coating options for aluminum die castings include anodizing, powder coating, chromate conversion coating, and electrophoretic painting Each method offers unique benefits, addressing aesthetic, protective, and functional requirements 25 Common Surface Finishing Options For Aluminum Die Castings