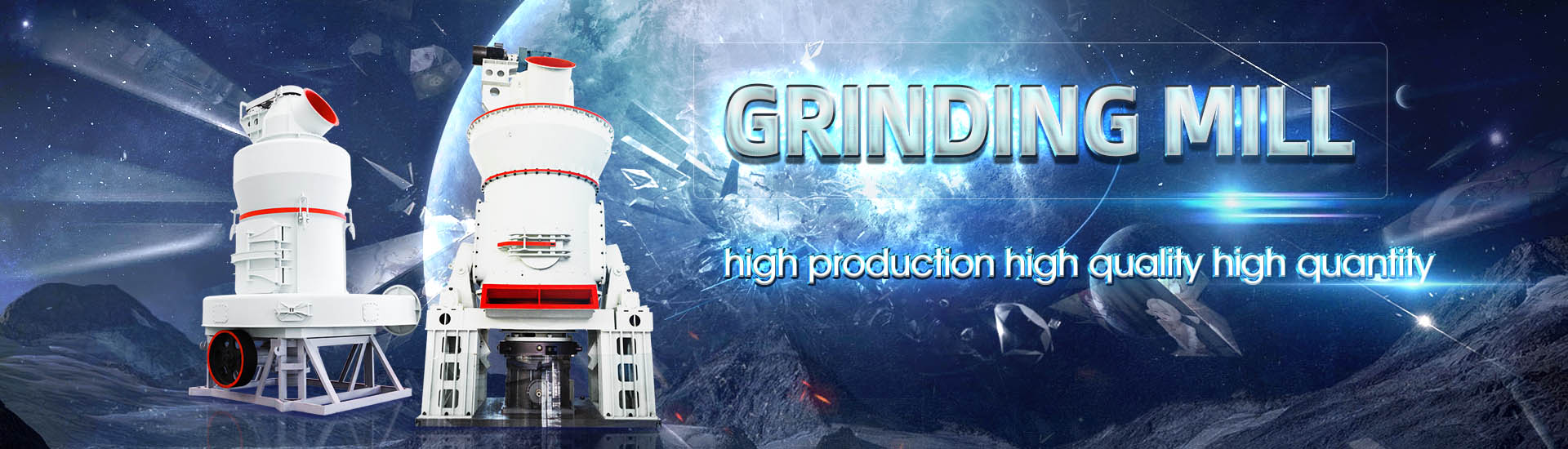
PXB series highenergy swing ore grinding mill

Helping to reduce mining industry carbon emissions: A step
2022年3月30日 High Pressure Grinding Rolls (HPGR) circuits have the potential to reduce the Mining Industry’s CO 2 emissions by up to 345 megatonnes/year, or 435% when compared 2019年4月12日 高压辊磨机能量利用率高,目前已在水泥行业、金属矿山、冶金球团等领域广泛应用。 结合当前研究成果及工业现场数据,本文对比了高压辊磨机在金属矿山和球团预处理行业中的工艺流程,以及辊面比压力、辊面线速度、 高压辊磨机在金属矿选矿与球团预处理领域的工艺和 2019年9月5日 Stirred mills Energy efficiency fine grinding technology Metso stirred mills are the optimal choice for fine wet grinding Ideal for grinding finer products, stirred mills are known for Metso comminution solutions Grinding2023年1月1日 Scaling up HPGRtower mill comminution circuit should consider size reduction ratio This paper presents the commercial implementation of a novel comminution circuit with Evaluating the performance of an industrialscale high
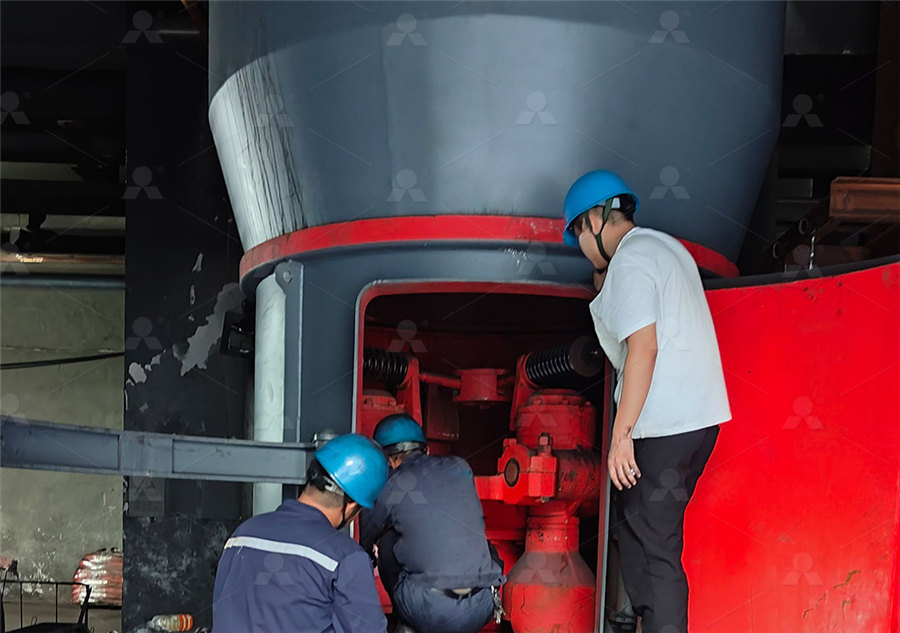
Energy conservation and consumption reduction in grinding
2023年11月1日 In response to the high consumptions of energy and media during grinding operations, An ingenious technique incorporating ceramic media and a new type of stirring mill 2024年10月15日 Vertical stirred mill is a fine grinding equipment that covers advantages of low rotation speed, high reliability and long life cycle Since it is operated with wet grinding method, the mill requires no cooling system due to Vertical Stirred Mill Mineral Processing 2022年8月24日 HPGRs (high pressure grinding rolls) have been developed within the last decades for energy efficient processing of a wide variety of ores Special interest has been Quantification of HPGR energy efficiency effects on 2018年2月20日 technology provide modern, sophisticated, flexible and energy efficient grinding solution for fine and ultra fine grinding Outotec HIGmills™ offer the uniqueOutotec HIGmills; A Fine Grinding Technology
.jpg)
THE REVOLUTION IN ULTRAFINE GRINDING RETSCH
RETSCH is the leading manufacturer of laboratory mills for homogenization of solid samples and has developed a High Energy Ball Mill which fulfills all these requirements With a unique The High Energy Ball Mill Emax, the most powerful in the RETSCH portfolio, achieves the highest energy input with speeds up to 2000 rpm, resulting in an acceleration of 76 g This, combined with its unique function principle and High Energy Ball Mills Milling RETSCH2022年1月1日 A pilotscale grinding technology of ceramic medium stirred mill was proposed in this study Based on the specific productivity and grinding efficiency, the appropriate grinding parameters were ascertained as follows: material ball ratio of 07, ceramic ball medium size ratio (10 mm: 15 mm: 20 mm = 3:2:5), stirring speed of 110 rpm, grinding concentration of 50%, Highefficiency and energyconservation grinding technology using 2023年10月17日 3 Ultrafine Powder Grinding Mill Ultrafine powder mill (threering / fourring mediumspeed micropowder mill) feed particle size ≤25 mm, production capacity 0545 t/h, production fineness 1503500 mesh,it is a high How to choose a suitable ore powder grinding
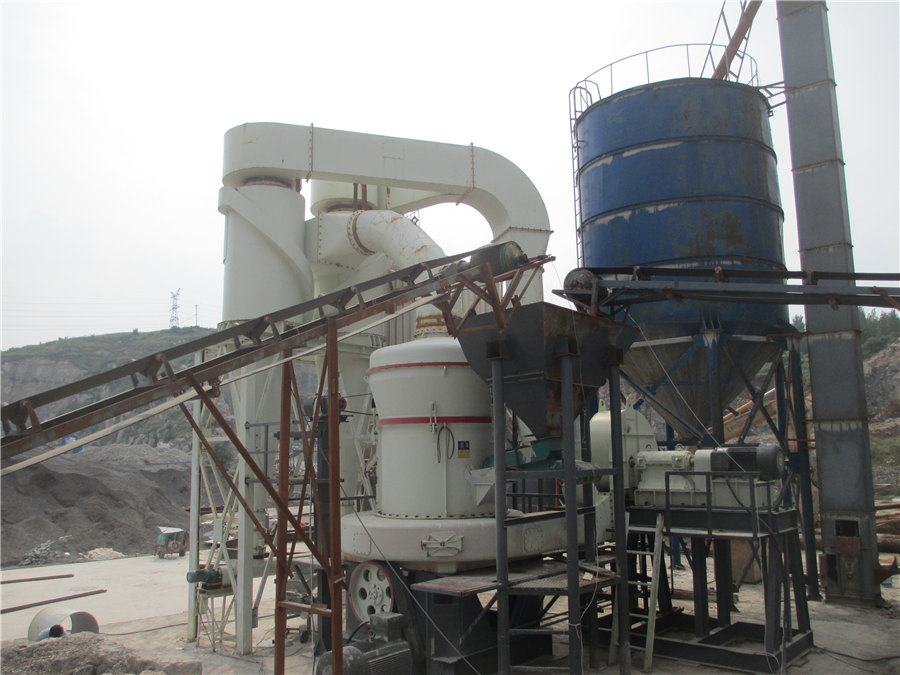
Outotec Higmill – EnergyEfficient HighIntensity Grinding
GrindForce’s vaned rotors enable a significant improvement in grinding efficiency to the target grind size 1000 100 Specific Grinding Energy (kWh/t) Specific Grinding Energy 10 100 Particle size (µm) 1000 GrindForce rotor Flat discs Specific Grinding Energy (kWh/t) versus the particle size (P80, µm) showing consistent reduction in 2023年10月10日 Types of Grinding Mills Grinding mills play a crucial role in the mining process, as they are responsible for reducing large chunks of ore into smaller particles that can be further processed There are various types of grinding mills available, each designed to meet specific requirements based on the material being ground and the desired outputUnderstanding the SAG Mill in Copper Ore Mining Process2018年2月20日 The relative ‘efficiency’ of horizontal grinding mills compared to other comminution equipment is often debated, and efforts to improve the energy efficiency of these mills is an ongoing area of attention for process engineers The discharge arrangement design affects the material transport characteristics within a horizontal grinding millAchievement of High Energy Efficiency in Grinding Mills 2023年7月20日 According to the ore discharging method, the grinding mill is divided into overflow type, grating type, and peripheral discharging type rod mill – its efficiency is relatively high with the feeding particle size less than 30 mm and the product particle size around 3 mm, and the produced product particle size is uniform with less Ore Grinding SpringerLink
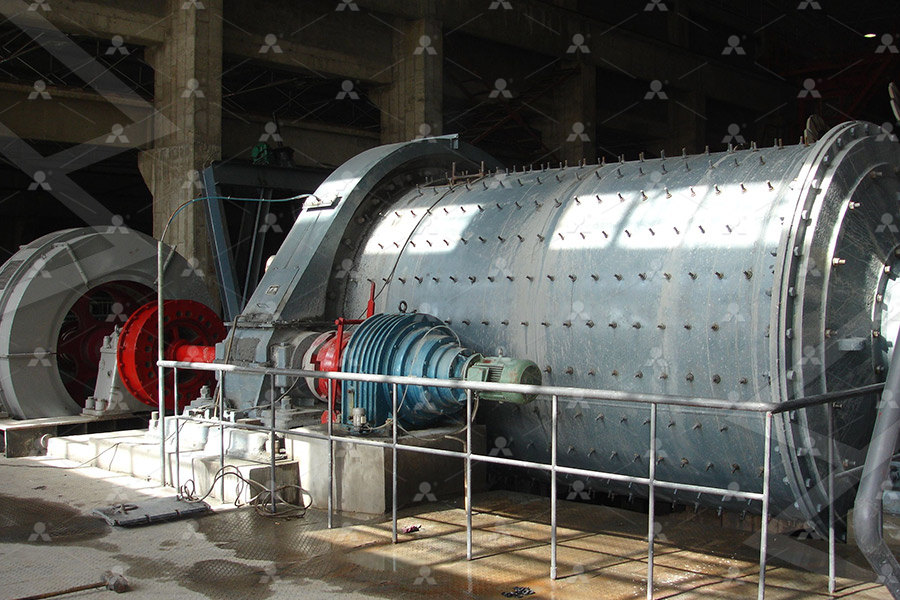
Highefficiency and energyconservation grinding technology using
2022年1月1日 A pilotscale grinding technology of ceramic medium stirred mill was proposed in this study Based on the specific productivity and grinding efficiency, the appropriate grinding parameters were ascertained as follows: material ball ratio of 07, ceramic ball medium size ratio (10 mm: 15 mm: 20 mm = 3:2:5), stirring speed of 110 rpm, grinding concentration of 50%, 2016年10月5日 In this chapter an introduction of widely applied energyefficient grinding technologies in cement grinding and description of the operating principles of the related equipments and comparisons over each other in terms of grinding efficiency, specific energy consumption, production capacity and cement quality are given A case study performed on a EnergyEfficient Technologies in Cement Grinding2012年6月1日 The paper presents an overview of the current methodology and practice in modeling and control of the grinding process in industrial ball mills Basic kinetic and energy models of the grinding (PDF) Grinding in Ball Mills: Modeling and Process Control2019年4月16日 Vertical roller mills (VRM) have been used extensively for comminuting both cement raw materials and minerals like limestone, clinker, phosphate, manganese, magnesite, feldspar and titanium(PDF) LEARNING FROM OTHER INDUSTRIES;
.jpg)
Research of iron ore grinding in a verticalrollermill
2015年3月15日 Compression breakage, which dominates in the high pressure grinding roll (HPGR) and vertical roller mill (VRM), is said to be energyefficient (Altun et al, 2015;Genç and Benzer, 2016; Reichert 2019年11月15日 Semantic Scholar extracted view of "Breaking down energy consumption in industrial grinding mills" by J Bouchard et al The link between operational practices and specific energy consumption in metal ore milling plants – Ontario experiences high pressure grinding roll and tumbling mill circuits S Morrell Engineering 2009; 48Breaking down energy consumption in industrial grinding mills2021年4月29日 The ball mill is a rotating cylindrical vessel with grinding media inside, which is responsible for breaking the ore particles Grinding media play an important role in the comminution of mineral A Comparative Study of Energy Efficiency in Tumbling Mills 2024年1月2日 energy input to the mill and is equal to the product of specific power, P/H, and grind time, t A description of a continuous tumbling mill requires not only a description of the breakage kinetics,Population balance model approach to ball mill

Population balance model approach to ball mill optimization in iron ore
2014年1月1日 An analysis of the kinetics of dolomite grinding in a dry ball mill reveals that the following approximations apply for the parameters of the batch grinding model: the size discretized selection 2009年6月1日 At product sizes finer than 80% passing 75 μm, the efficiency of ball mill grinding rapidly decreasesThe practical limit to ball mill product fineness is considered to be 40–45 μm (Gao and Weller, 1994)Although ball mills can still be found in the regrind circuits in a number of mineral processing plants, their energy consumption is high, and size reduction efficiency is parison of energy efficiency between ball mills and stirred mills 2024年8月20日 The majority of steel production is supported by iron ore sourced from high grade hematite energy efficient stirred mills Steel grinding media usage significantly increases the operating Reducing Grinding Energy and Cost Magnetite Iron It can be shown, using Bond’s equation (Equation 54), that 19% extra energy must be consumed in grinding one screen size finer on a 2 screen series A strategy to reduce grinding energy consumption in low grade high tonnage flotation plants is to employ a coarse primary grind and regrind the rougher flotation concentrate, which represents a Grinding Mill an overview ScienceDirect Topics
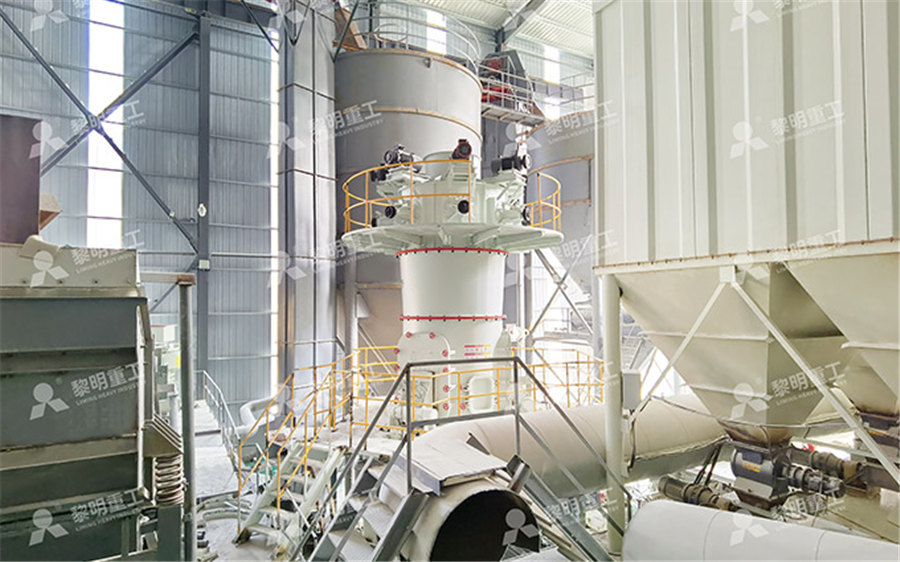
Ball mill, Ball grinding mill All industrial manufacturers
Ball mill is suitable to grind various mineral and other materials, which is widely used in various industries such as benefication, construction materials, chemical industry, etc, it has two ore grinding A crushing plant delivered ore to a wet grinding mill for further size reduction The size of crushed ore (F 80) was 40 mm and the SG 28 t/m 3 The work index of the ore was determined as 122 kWh/t A wet ball mill 1 m × 1 m was chosen to grind the ore down to 200 micronsGrinding Mill an overview ScienceDirect Topics2023年7月10日 The present literature review explores the energyefficient ultrafine grinding of particles using stirred mills The review provides an overview of the different techniques for size reduction and the impact of energy EnergyEfficient Advanced Ultrafine Grinding of 2022年12月15日 It can be concluded that the HPGRStirred mill combination was a more energyefficient grinding circuit than the HPGRBall mill combination for PGE bearing chromite oreSize reduction performance evaluation of
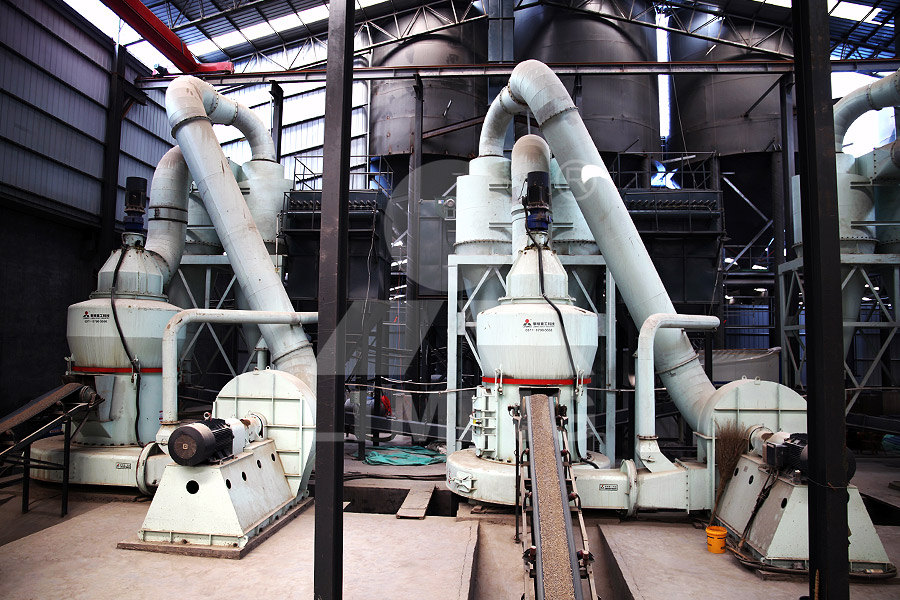
Grinding Modeling and Energy Efficiency in Ore/Raw
2022年8月31日 Grinding plays an important role in mining, construction, metallurgy, chemical, coal and other basic industries In terms of beneficiation, grinding is the most energy consuming operation So, reasonable grinding conditions according to the properties of ores is the key to obtain good grinding results and reduce energy consumption and resource 2009年5月1日 In this study, the particle size distribution, fractal dimension, specific energy consumption, and grinding kinetics of chalcopyrite ore under high voltage pulse discharge were systematically Predicting the overall specific energy requirement of crushing, high Our main products include ultrafine vertical roller mill, ultrafine grinding mill, stone powder production equipment, Welcome to consult +17 [ protected]SBM Ultrafine Powder Technology Industrial Grinding Mill, 2023年12月12日 Even though semiautogenous grinding mills and ball mills are normally used in grinding processes, the industry is driven to decrease cost by increasing efficiencies and decreasing energy consumption(PDF) Control of ball mill operation depending on ball load and ore
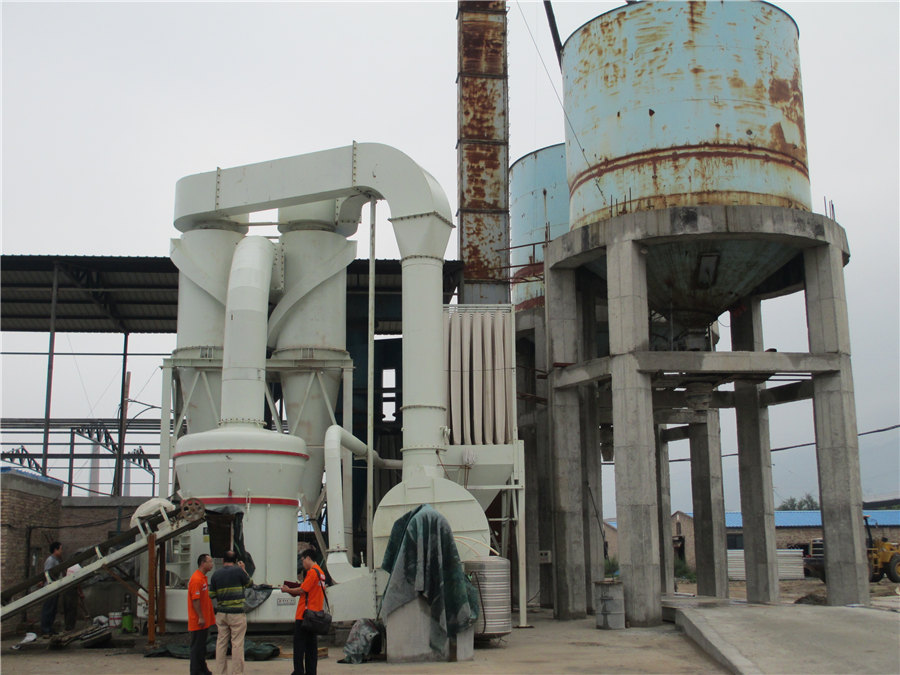
Optimization of stirred mill parameters for fine grinding of
2020年7月23日 The depletion of highgrade ores has forced the utilization of lowgrade ores The small liberation sizes in the lowgrade ores require fine grinding which is an energy intensive operation2019年3月27日 Grinding is one of the most energydemanding processes of copper mines Declining ore grades and harder rocks will further intensify this demandStudying the integration of solar energy into the operation The High Energy Ball Mill Emax combines highfrequency impact, intensive friction, and controlled circular jar movements to a unique and highly effective size reduction mechanism The grinding jars have an oval shape and are mounted on two discs respectively which move the jars on a circular course without changing their orientationEmax High Energy Ball Mill RETSCHThe High Energy Ball Mill Emax, the most powerful in the RETSCH portfolio, achieves the highest energy input with speeds up to 2000 rpm, resulting in an acceleration of 76 g This, combined with its unique function principle and High Energy Ball Mills Milling RETSCH
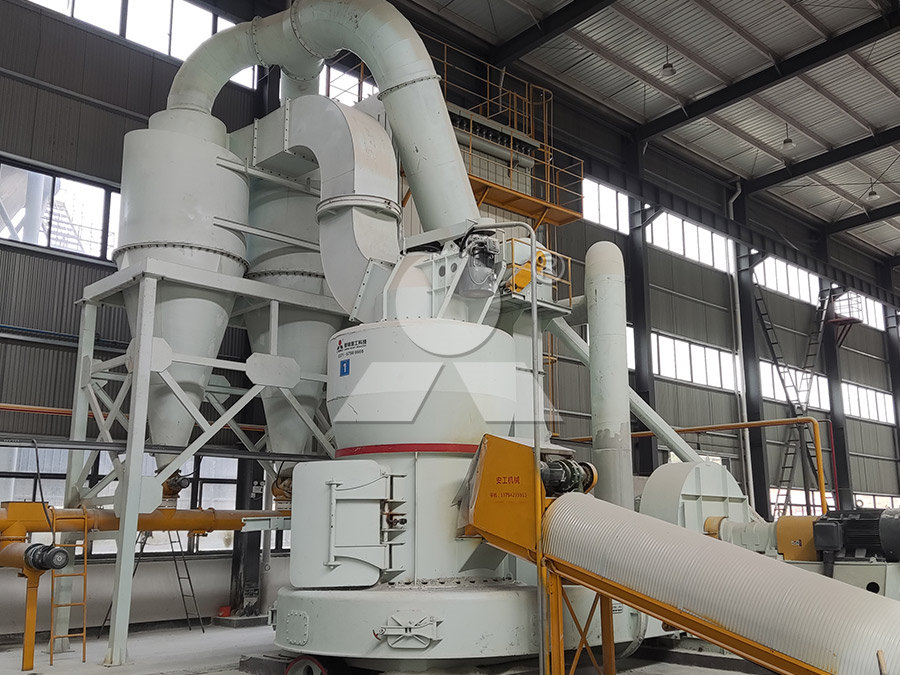
Highefficiency and energyconservation grinding technology using
2022年1月1日 A pilotscale grinding technology of ceramic medium stirred mill was proposed in this study Based on the specific productivity and grinding efficiency, the appropriate grinding parameters were ascertained as follows: material ball ratio of 07, ceramic ball medium size ratio (10 mm: 15 mm: 20 mm = 3:2:5), stirring speed of 110 rpm, grinding concentration of 50%, 2023年10月17日 3 Ultrafine Powder Grinding Mill Ultrafine powder mill (threering / fourring mediumspeed micropowder mill) feed particle size ≤25 mm, production capacity 0545 t/h, production fineness 1503500 mesh,it is a high How to choose a suitable ore powder grinding GrindForce’s vaned rotors enable a significant improvement in grinding efficiency to the target grind size 1000 100 Specific Grinding Energy (kWh/t) Specific Grinding Energy 10 100 Particle size (µm) 1000 GrindForce rotor Flat discs Specific Grinding Energy (kWh/t) versus the particle size (P80, µm) showing consistent reduction in Outotec Higmill – EnergyEfficient HighIntensity Grinding2023年10月10日 Types of Grinding Mills Grinding mills play a crucial role in the mining process, as they are responsible for reducing large chunks of ore into smaller particles that can be further processed There are various types of grinding mills available, each designed to meet specific requirements based on the material being ground and the desired outputUnderstanding the SAG Mill in Copper Ore Mining Process
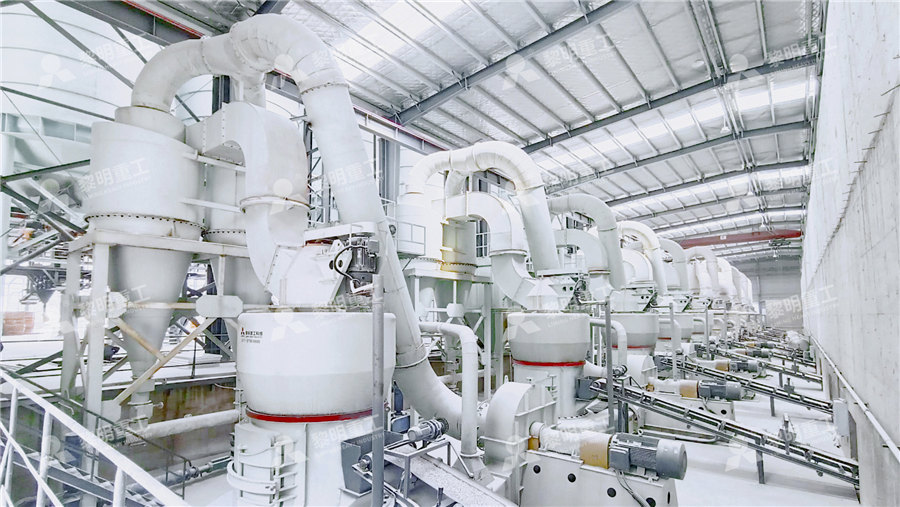
Achievement of High Energy Efficiency in Grinding Mills
2018年2月20日 The relative ‘efficiency’ of horizontal grinding mills compared to other comminution equipment is often debated, and efforts to improve the energy efficiency of these mills is an ongoing area of attention for process engineers The discharge arrangement design affects the material transport characteristics within a horizontal grinding mill2023年7月20日 According to the ore discharging method, the grinding mill is divided into overflow type, grating type, and peripheral discharging type rod mill – its efficiency is relatively high with the feeding particle size less than 30 mm and the product particle size around 3 mm, and the produced product particle size is uniform with less Ore Grinding SpringerLink2022年1月1日 A pilotscale grinding technology of ceramic medium stirred mill was proposed in this study Based on the specific productivity and grinding efficiency, the appropriate grinding parameters were ascertained as follows: material ball ratio of 07, ceramic ball medium size ratio (10 mm: 15 mm: 20 mm = 3:2:5), stirring speed of 110 rpm, grinding concentration of 50%, Highefficiency and energyconservation grinding technology using 2016年10月5日 In this chapter an introduction of widely applied energyefficient grinding technologies in cement grinding and description of the operating principles of the related equipments and comparisons over each other in terms of grinding efficiency, specific energy consumption, production capacity and cement quality are given A case study performed on a EnergyEfficient Technologies in Cement Grinding
.jpg)
(PDF) Grinding in Ball Mills: Modeling and Process Control
2012年6月1日 The paper presents an overview of the current methodology and practice in modeling and control of the grinding process in industrial ball mills Basic kinetic and energy models of the grinding