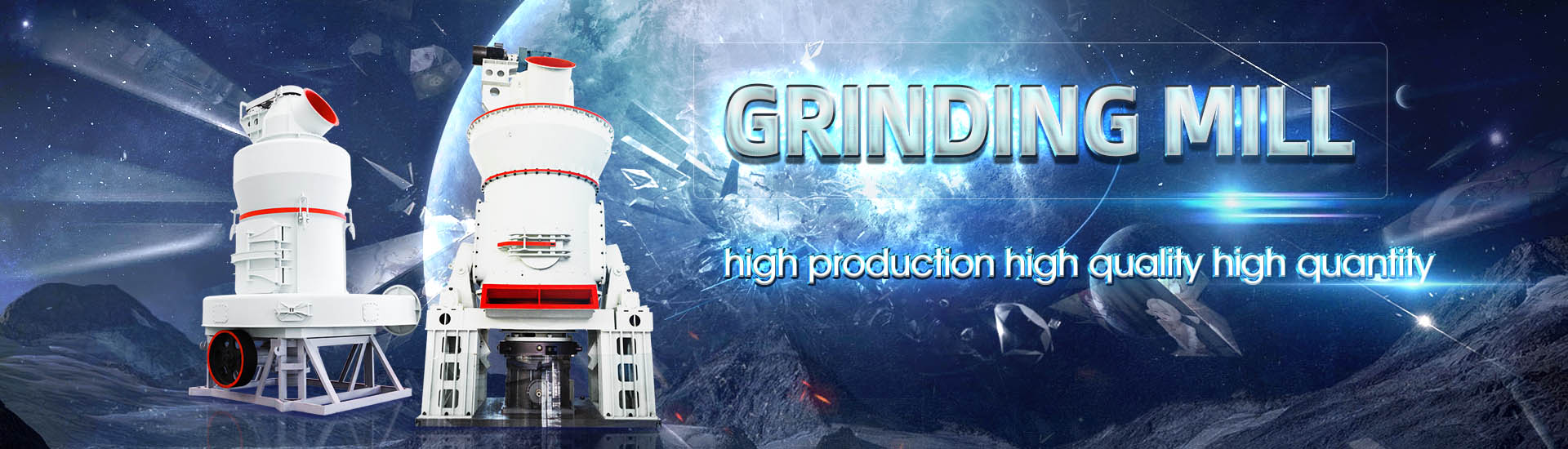
Standard for limestone for flue gas desulfurization
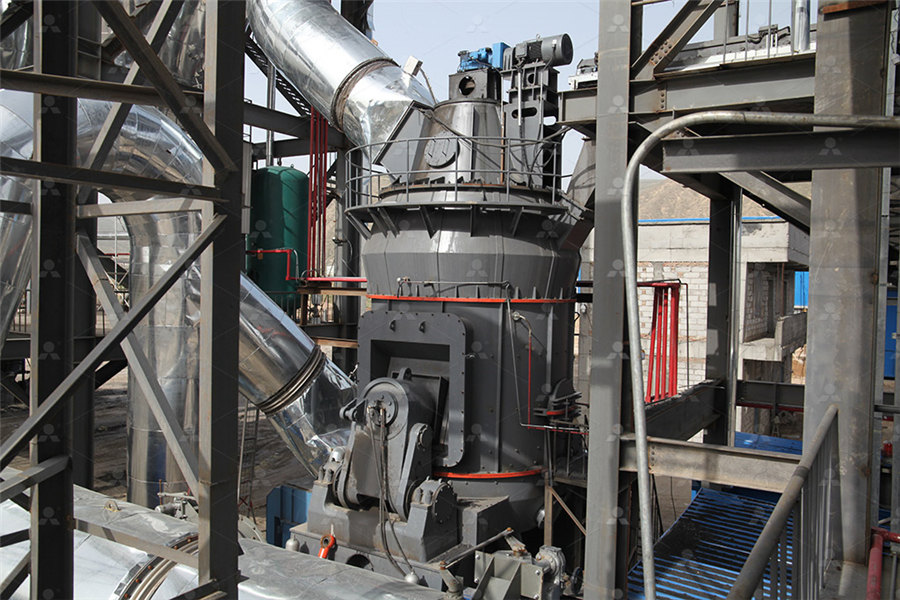
Analysis of limestone for flue gas desulfurization in a
2024年5月22日 standard calibration curve has been developed on the ARL OPTIM’X for the five elements (Ca, Si, Mg, Al, Fe) in limestone as a pressed powder The resulting calibrations for lime, magnesia, iron oxide and silica are illustrated in Figures 1, 2, 3 and 42024年5月22日 The Thermo ScientificTM ARLTM QUANT’X EnergyDispersive Xray Fluorescence (EDXRF) Spectrometer is used to control the quality of limestone used for flue Analysis of limestone for flue gas desulfurization in a 2020年3月28日 Wet scrubbers are used in utilities, paper mills, and chemical plants to remove sulfur dioxide (SO 2) and other pollutants from gas streams Undesirable pollutants are Lime / Limestone Wet Scrubbing System for Flue Gas 2017年7月1日 The most common system for flue gas desulfurization (FGD) is the wet scrubbing process in which, the contact between the flue gases to be treated and an alkaline sorbent Enhancing the recovery of gypsum in limestonebased wet flue gas
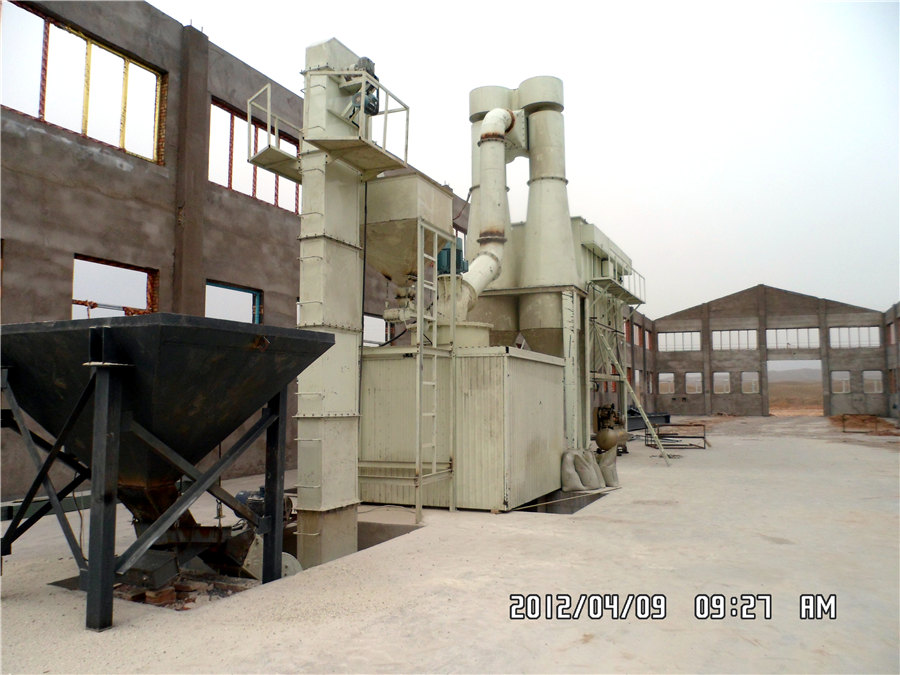
Dissolution rate of limestone for wet flue gas desulfurization
2009年9月15日 Limestonebased wet flue gas desulfurization (WFGD) technology has been considered as the most effective method for the control of SO 2 from coal fired boilers In this 2023年11月13日 FGD system limits the escape of SO x from flue gas by spraying the wet limestone, which reacts with the SO x in the flue gas producing calcium sulphate dihydrate [CaSO 4 2H 2 O]Characterization of flue gas desulphurized (FGD) 2020年11月11日 Wet flue gas desulfurization was simulated to improve gypsum production using lowgrade limestone Highgrade limestone with 94 wt% CaCO 3 content is used for Modeling of the wet flue gas desulfurization system to Adding 1030 mmol/L acetic acid, degree of desulphurization was increased to 95% and the limestone utilization was enhanced to 935%, comparison with fine limestone, the New LimestoneGypsum Flue Gas Desulfuization Technology
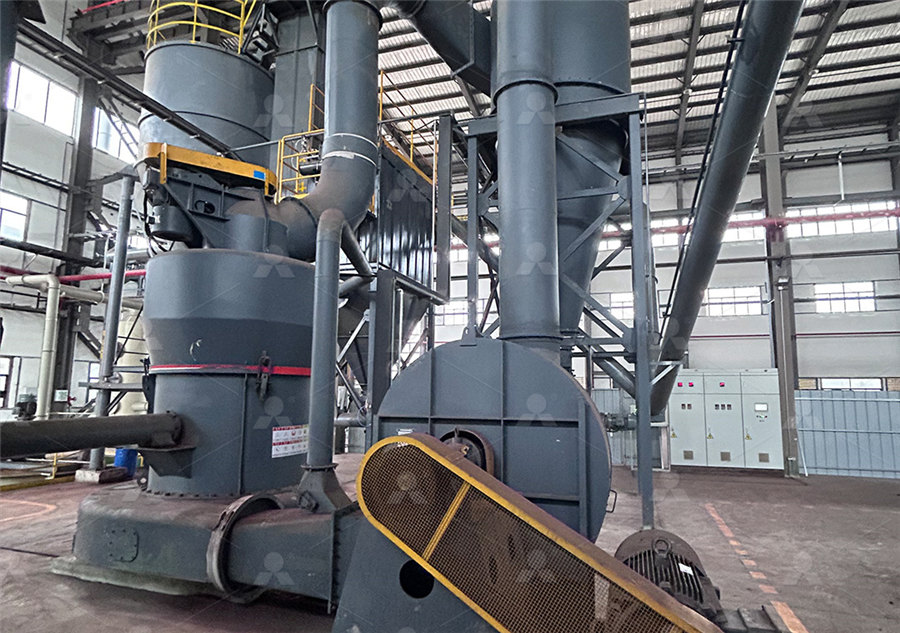
Model of the Wet Limestone Flue Gas Desulfurization
2001年5月19日 A detailed process model of the wet limestone flue gas desulfurization system has been presented This model can be used to calculate indispensable parameters for 2006年7月18日 Effect of adjusted mesoscale drag model on flue gas desulfurization in powderparticle spouted beds Frontiers of Chemical Science and Engineering 2022, 16 (6) , 909920 PilotPlant Technical Assessment of Wet Flue Gas Desulfurization 2020年3月28日 2) and limestone (CaCO 3) Rosemount Analytical pH equipment is used to control the feed rate of these chemicals PROCESS After fly ash removal, the flue gas (seen in Figure 1) is bubbled through the scrubber, and the slurry is added from aboveThe lime or limestone reacts with the SO 2 in the flue gas to create insoluble calcium sulfite (CaSO Lime / Limestone Wet Scrubbing System for Flue Gas 2023年8月3日 The slurry jet technique is widely used for flue gas desulfurization, whereas the increase in its absorption efficiency is required to meet the increasingly strict exhaust emission standards In this work, we developed a Venturitype slurry jet nozzle to improve the efficiency of flue gas desulfurization As anticipated, the absorption efficiency of SO2 can be enhanced by A Venturitype slurry jet nozzle for efficient flue gas desulfurization
.jpg)
Modeling of the wet flue gas desulfurization system to
2020年11月11日 Wet flue gas desulfurization was simulated to improve gypsum production using lowgrade limestone Highgrade limestone with 94 wt% CaCO3 content is used for producing gypsum with 93 wt% purity, but owing to the resource depletion of highgrade limestone, lowgrade limestone should be replaced as an alternative However, lowgrade 2015年7月27日 3 Flue Gas Desulfurization Technologies Flue gas desulfurization is an efficient method for the reduction of the sulfur dioxide emissions Citation 2 Many processes are available in the market, such as (a) wet scrubbers, (b) spray dry scrubbers, (c) sorbent injection, (d) regenerable processes, and (e) combined SO 2 /NO X removal processes The different flue Review of Design, Operating, and Financial Considerations in Flue Gas 2015年9月1日 EPACICA Fact Sheet Flue Gas Desulfurization1 Name of Technology: Flue Gas Desulfurization (FGD) Wet, limestone systems are limited to appr oximately 90% Lime is easier to manage onsite and has control The process forms a dry waste product which is collected with a standard particulate matter (PM)Air Pollution Control Technology Fact Sheet US EPAFluegas desulfurization (FGD) which is collected with a standard PM collection device such as a baghouse or ESP The process also removes almost all the HCl contained in the flue gas The calcium carbonate in the limestone reacts with the SO 2 and oxygen from the air to produce gypsum, which precipitates from the solution The HCl is FlueGas Desulphurization an overview ScienceDirect Topics
.jpg)
A comprehensive review of flue gas desulphurized gypsum:
2023年8月22日 Flue gas desulfurization (FGD) gypsum is a byproduct of the combustion of coal, used for electricity generation (MoEFCC), India, introduced new standards for emission limits for coal power stations (Table 1) As of now, only 8 % of power plants in India have been installed with FGD units Flue Gas Desulphurization: Limestone 2001年5月19日 A detailed process model of the wet limestone flue gas desulfurization system has been presented This model can be used to calculate indispensable parameters for estimating costs and next to minimize capital and operating costs The process model describes most important stage of SO2 removal running in an absorber and a holding tank It includes Model of the Wet Limestone Flue Gas Desulfurization 2001年5月19日 A detailed process model of the wet limestone flue gas desulfurization system has been presented This model can be used to calculate indispensable parameters for estimating costs and next to minimize capital and operating costs The process model describes most important stage of SO2 removal running in an absorber and a holding tank It includes Model of the Wet Limestone Flue Gas Desulfurization 2024年3月20日 Desulfurization wastewater is industrial wastewater with a high salt content, high metal ions, and high hardness produced by flue gas desulfurization of the limestonegypsum method in coalfired power plants This paper summarizes the source of desulfurization wastewater, water quality characteristics, water quality impacts, and other factors, combined Current Status of Zero Liquid Discharge Technology for Desulfurization
.jpg)
STANDARD TECHNICAL SPECIFICATION FOR RETROFIT
2020年4月7日 31 General description of wet limestone FGD system 50 311 Flue gas system 50 312 Absorber system 50 313 Limestone unloading, crushing storage system 51 314 Limestone grinding, slurry preparation and storage System 51nitrate/nitrite measured as total nitrogen in the flue gas desulfurization (FGD) wastewater discharged from power plants1 These discharge standards were based on the performance of chemical precipitation and biological treatment2 Several recent pilotscale evaluations of these technologies for FGD wastewater treatment, however, haveFlue Gas Desulfurization Wastewater Composition and 2024年8月5日 This blog post is the second in a threepart series that discusses flue gas desulfurization (FGD) The first post provides overviews of sulfur dioxide pollution (SO 2) and emissions regulations, the FGD industry, and global FGD market trendsThis second post provides highlevel overviews of wet, semidry, and dry FGD technologies with respect to SO 2 Flue Gas Desulfurization: Technology Overview Long 2020年11月24日 Solidliquid dissolution is a central step in many industrial applications such as pharmaceutical, process engineering, and pollution control Accurate mathematical models are proposed to improve reactor design and process operations Analytical methods are significantly beneficial in the case of iterative methods used within experimental investigations In the Modeling of Limestone Dissolution for Flue Gas Desulfurization
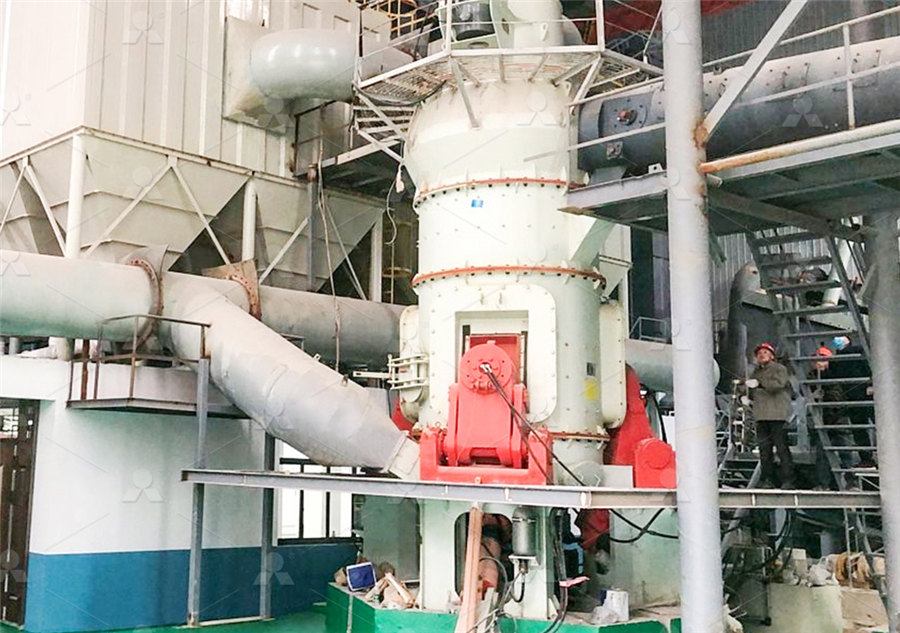
Flue Gas Desulfurization Technologies for CoalFired Power
Particularly notable are the programs on flue gas desulfurization (FGD) technologies that have been ongoing in a number of coun tries for several years Seeking to improve the effective The control of sulfur dioxide emissions from thermal power plants is examined in light of the recent advances made in developing commercial processes for this 2001年5月19日 Warych et al [43, 44] established a model of the thermal power plant flue gas desulfurization process based on the thin film theory, which simulated the SO 2 absorption process and limestone Model of the Wet Limestone Flue Gas Desulfurization2024年1月10日 It offers a smaller physical size and lower initial cost than wet desulfurization systems, making it a practical option for upgrading existing plants to meet stricter flue gas cleaning standards 16Modeling based on machine learning to investigate flue gas 2022年8月15日 Oxygenenriched combustion is the most promising CO 2 emission reduction technology for coal burning However, the sharp increase in CO 2 and SO 2 concentrations in flue gas after oxygenenriched combustion poses a new challenge to the subsequent wet flue gas desulfurization (WFGD) system In this study, limestonebased dualloop WFGD technology Limestonebased dualloop wet flue gas desulfurization
46.jpg)
Flue Gas Desulfurization: The State of the Art Taylor
2023年8月26日 The cocurrent contact of slurry and flue gas allows for a higher flue gas velocity and results in a reduced pressure drop Additionally, combining the cocurrent absorber tower and reaction tank can reduce space requirements In this design, limestone slurry is sprayed above the grid and is contacted by the flue gas Simultaneous forced oxi2020年12月14日 EKATO Agitators for Flue Gas Desulfurization Highly efficient performance, robust and reliable design Worldwide over 12,000 EKATO agitators prove their reliability every day in more than 1,500 flue gas desulfurization plants As theworld market leader EKATO set benchmark in nowadays stateoftheart FGD agitator systemsEKATO Agitators for Flue Gas Desulfurization EKATO 2020年11月13日 Seawater flue gas desulfurization (SWFGD) is considered to be a viable solution for coastal and naval applications; however, this process has several drawbacks, including its corrosive absorbent (PDF) Advanced and Intensified Seawater Flue 2019年3月13日 Exhaust flue gas enters the WFGD system from the entrance, which is located at the lower part of the tower The exhaust gas comes into mass transfer and chemical reactions in countercurrent mode with the limestone Modeling and optimization of wet flue gas
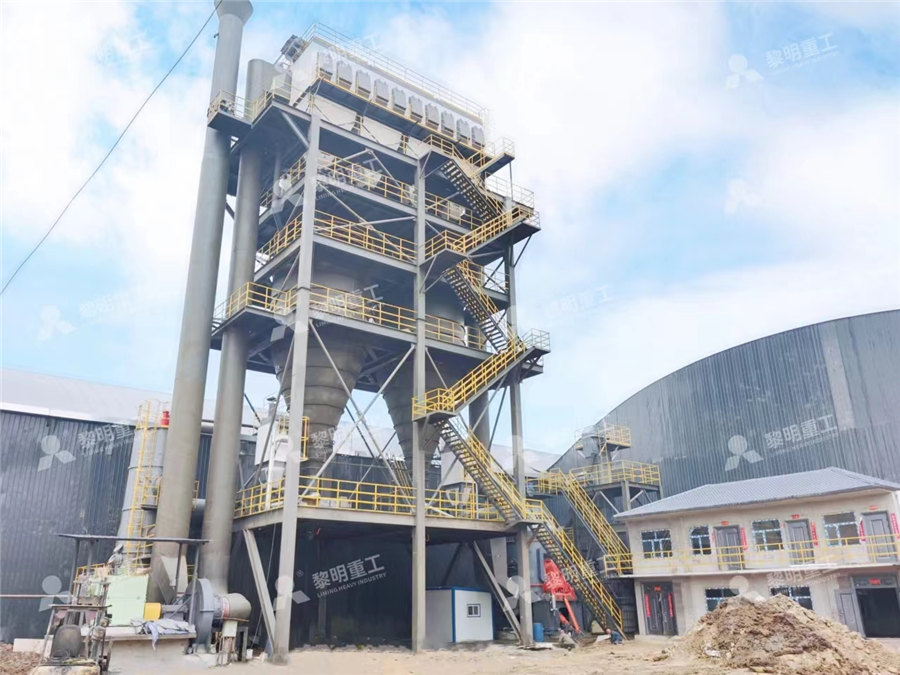
11 Flue Gas Desulfurization Air Quality and
Suggested Citation:"11 Flue Gas Desulfurization"National Research Council 1975 Air Quality and Stationary Source Emission ControlWashington, DC: The National Academies Press doi: 1017226/108402017年7月1日 The most common system for flue gas desulfurization (FGD) is the wet scrubbing process in which, the contact between the flue gases to be treated and an alkaline sorbent such limestone is realized with the correspondent production of gypsum The first test referred to the use of standard limestone normally used in a wet FGD system The Enhancing the recovery of gypsum in limestonebased wet flue gas Sulfur dioxide (SO/sub 2/) was one of these pollutants These ambient air quality standards have had perhaps their biggest impact on the power utilities In an effort to meet the air quality standards set forth by the EPA, utilities using high sulfur fuels have been forced to install flue gas desulfurization (FGD) systemsWet limestone grinding for flue gas desulfurization OSTIGOV2012年2月1日 Reactivity of various calcium carbonate samples for flue gas desulfurization was tested Two groups of CaCO 3 samples were considered; natural limestone containing calcite phase dominantly and Use of Carbonate Rocks for Flue Gas Desulfurization
.jpg)
Dissolution Reactivity and Kinetics of LowGrade Limestone for Wet Flue
2020年7月22日 DOI: 101021/acsiecr0c01896 Corpus ID: ; Dissolution Reactivity and Kinetics of LowGrade Limestone for Wet Flue Gas Desulfurization @article{Gu2020DissolutionRA, title={Dissolution Reactivity and Kinetics of LowGrade Limestone for Wet Flue Gas Desulfurization}, author={Shuaiwei Gu and Zhizhong Yang and Zhen Chen 2020年2月26日 This research was carried out on the limestone forced oxidation (LSFO) flue gas desulphurization (FGD) system installed at 2*660 MW supercritical coal fired power plantArtificial IntelligenceBased Emission Reduction Strategy for Limestone 2019年3月1日 Together, as publishers that will always put purpose above profit, we have defined a set of industry standards that underpin highquality, ethical scholarly communications [13] Zhou A and Qian N Y 2011 Study on Optimization of limestonegypsum wet flue gas desulfurization system Science Technology Information 14 1033910340 Google Progress of Desulfurization and Denitration Technology of Flue Gas 2017年5月16日 Flue gas flow rate (max) 3310 m /hr Flue Gas Temperature 280 C Patricia Córdoba presented a general review of the Flue Gas Desulphurization (FGD) technologies used to abate sulphur emissions from coalfired power plants, and exposes the major physicchemical processes occurring during wet limestone FGD( Patricia Córdoba, 2014)Analytical Investigation and Design of Flue Gas
.jpg)
Lime / Limestone Wet Scrubbing System for Flue Gas
2020年3月28日 2) and limestone (CaCO 3) Rosemount Analytical pH equipment is used to control the feed rate of these chemicals PROCESS After fly ash removal, the flue gas (seen in Figure 1) is bubbled through the scrubber, and the slurry is added from aboveThe lime or limestone reacts with the SO 2 in the flue gas to create insoluble calcium sulfite (CaSO 2023年8月3日 The slurry jet technique is widely used for flue gas desulfurization, whereas the increase in its absorption efficiency is required to meet the increasingly strict exhaust emission standards In this work, we developed a Venturitype slurry jet nozzle to improve the efficiency of flue gas desulfurization As anticipated, the absorption efficiency of SO2 can be enhanced by A Venturitype slurry jet nozzle for efficient flue gas desulfurization 2020年11月11日 Wet flue gas desulfurization was simulated to improve gypsum production using lowgrade limestone Highgrade limestone with 94 wt% CaCO3 content is used for producing gypsum with 93 wt% purity, but owing to the resource depletion of highgrade limestone, lowgrade limestone should be replaced as an alternative However, lowgrade Modeling of the wet flue gas desulfurization system to 2015年7月27日 3 Flue Gas Desulfurization Technologies Flue gas desulfurization is an efficient method for the reduction of the sulfur dioxide emissions Citation 2 Many processes are available in the market, such as (a) wet scrubbers, (b) spray dry scrubbers, (c) sorbent injection, (d) regenerable processes, and (e) combined SO 2 /NO X removal processes The different flue Review of Design, Operating, and Financial Considerations in Flue Gas
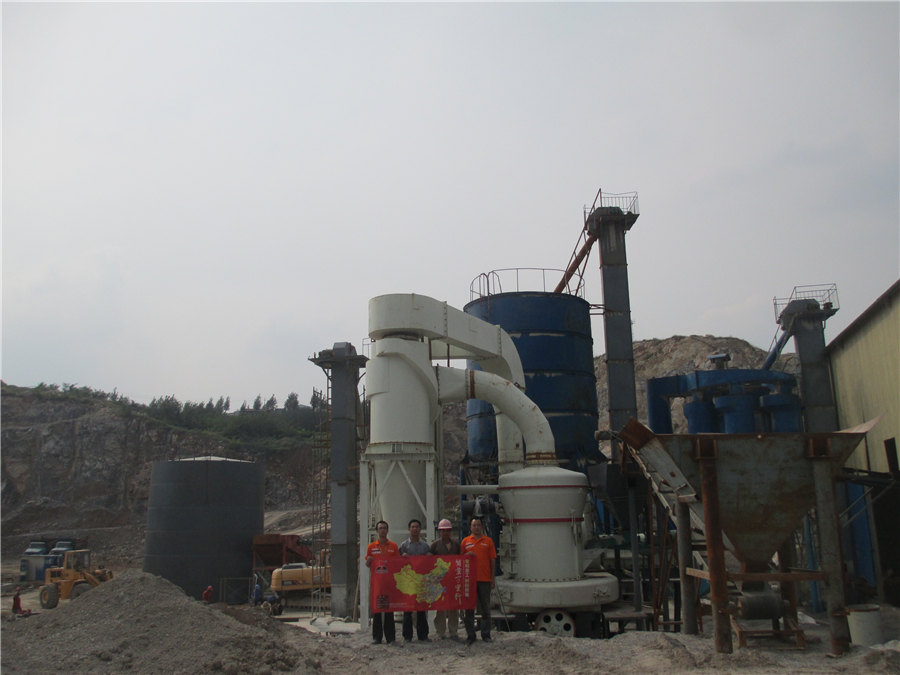
Air Pollution Control Technology Fact Sheet US EPA
2015年9月1日 EPACICA Fact Sheet Flue Gas Desulfurization1 Name of Technology: Flue Gas Desulfurization (FGD) Wet, limestone systems are limited to appr oximately 90% Lime is easier to manage onsite and has control The process forms a dry waste product which is collected with a standard particulate matter (PM)Fluegas desulfurization (FGD) which is collected with a standard PM collection device such as a baghouse or ESP The process also removes almost all the HCl contained in the flue gas The calcium carbonate in the limestone reacts with the SO 2 and oxygen from the air to produce gypsum, which precipitates from the solution The HCl is FlueGas Desulphurization an overview ScienceDirect Topics2023年8月22日 Flue gas desulfurization (FGD) gypsum is a byproduct of the combustion of coal, used for electricity generation (MoEFCC), India, introduced new standards for emission limits for coal power stations (Table 1) As of now, only 8 % of power plants in India have been installed with FGD units Flue Gas Desulphurization: Limestone A comprehensive review of flue gas desulphurized gypsum: 2001年5月19日 A detailed process model of the wet limestone flue gas desulfurization system has been presented This model can be used to calculate indispensable parameters for estimating costs and next to minimize capital and operating costs The process model describes most important stage of SO2 removal running in an absorber and a holding tank It includes Model of the Wet Limestone Flue Gas Desulfurization
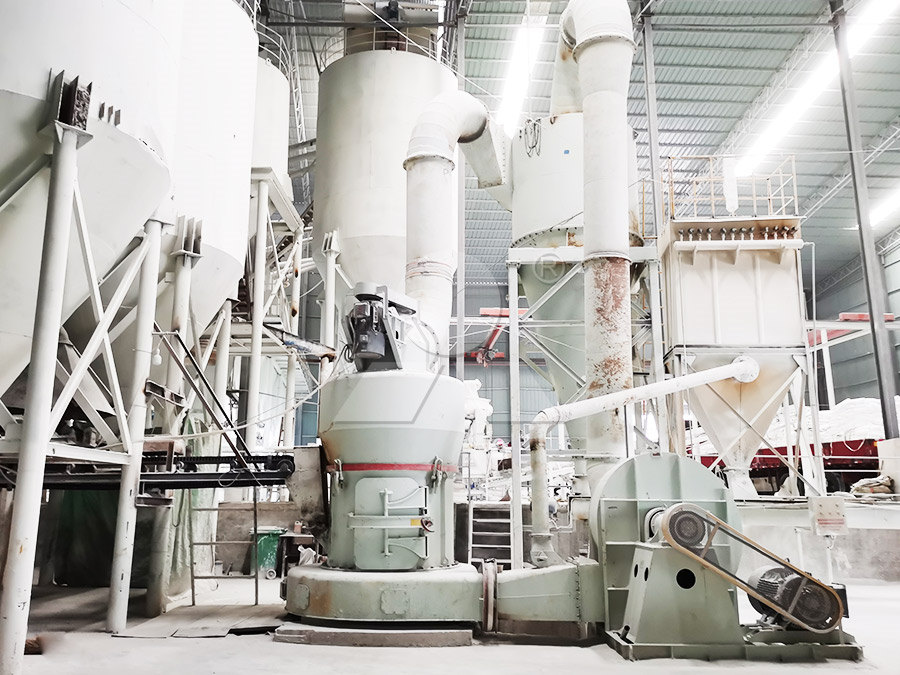
Model of the Wet Limestone Flue Gas Desulfurization
2001年5月19日 A detailed process model of the wet limestone flue gas desulfurization system has been presented This model can be used to calculate indispensable parameters for estimating costs and next to minimize capital and operating costs The process model describes most important stage of SO2 removal running in an absorber and a holding tank It includes 2024年3月20日 Desulfurization wastewater is industrial wastewater with a high salt content, high metal ions, and high hardness produced by flue gas desulfurization of the limestonegypsum method in coalfired power plants This paper summarizes the source of desulfurization wastewater, water quality characteristics, water quality impacts, and other factors, combined Current Status of Zero Liquid Discharge Technology for Desulfurization