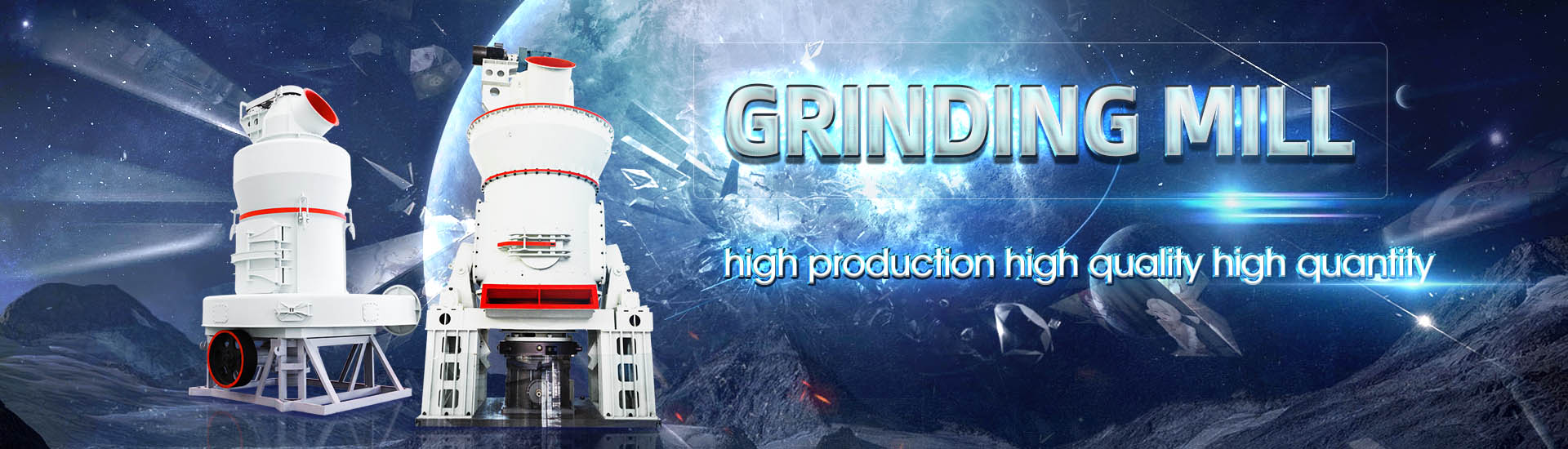
Iron finishing powder process
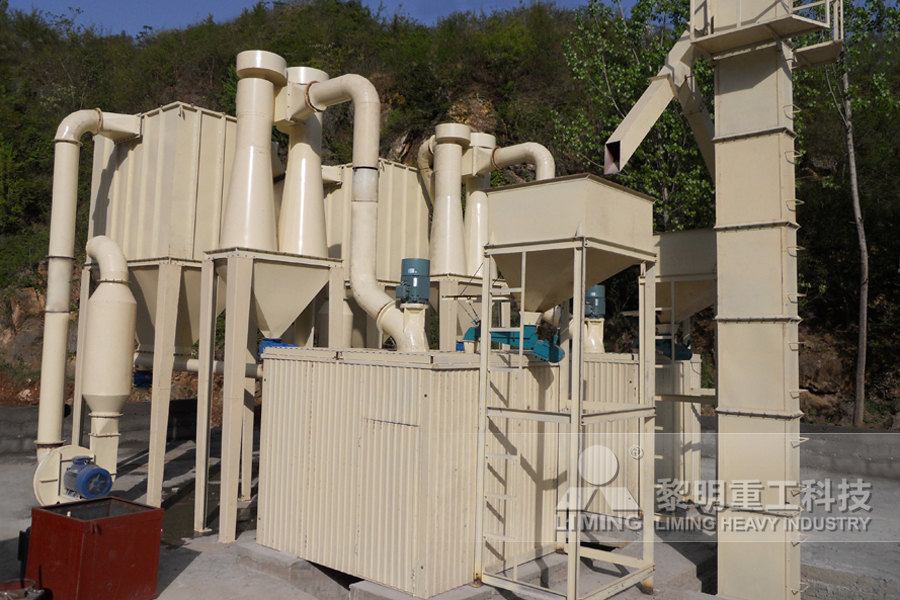
What Is Powder Coating? Types, Process Benefits
2021年9月3日 Powder Coating Process The powder coating process requires three basic steps, regardless of the type of powder used: preparation, or pretreatment, application, and curing Here is an overview of each step 2022年12月27日 Powder coating finishes improve your part's durability and aesthetic Here are insights on the process, tips, pros, cons, and uses of powder coatingPowder Coating Finish: Everything You Need to KnowPowder coating is a dry finishing process that involves the application of fine, electrostatically charged powder particles to a substrate's surface This application method ensures an even and consistent coating, free from drips, Powder Coating Process Explained – A Detailed 2021年9月21日 Powder coating provides a durable, lasting alternative to liquid paint Its application process requires careful pretreatment and an electrostatic charge to adhere the pigmented coating onto the surface With powder A Complete Guide to Powder Coating: How Does It
.jpg)
The Powder Coating Process Products Finishing
2011年9月29日 Powder coating is a dry finishing process used to apply a dry coating material The coating material is made up of finely ground particles of resin and pigment for color, along with other additives for specific functions 11 Define surface finishing 12 Describe the main processes used for Surface Finishing and their basic principles 13 Describe the purposes for which these finishes are applied to substrates INTRODUCTION Powder Coatings Materials FinishingRaw iron powder grades can be sent to finishing processes such as milling, classifying, mixing and coating according to further uses Iron, Furnace in the form of liquid iron [also known as Iron Manufacturing process related to the specified manufacture(s)Powder coating is a dry coating process used as a metal finish mostly on industrial equipment Powder coating is applied as dry powder through an electrostatic process, then cured with heat It is well known for providing high Everything you should know about powder coating
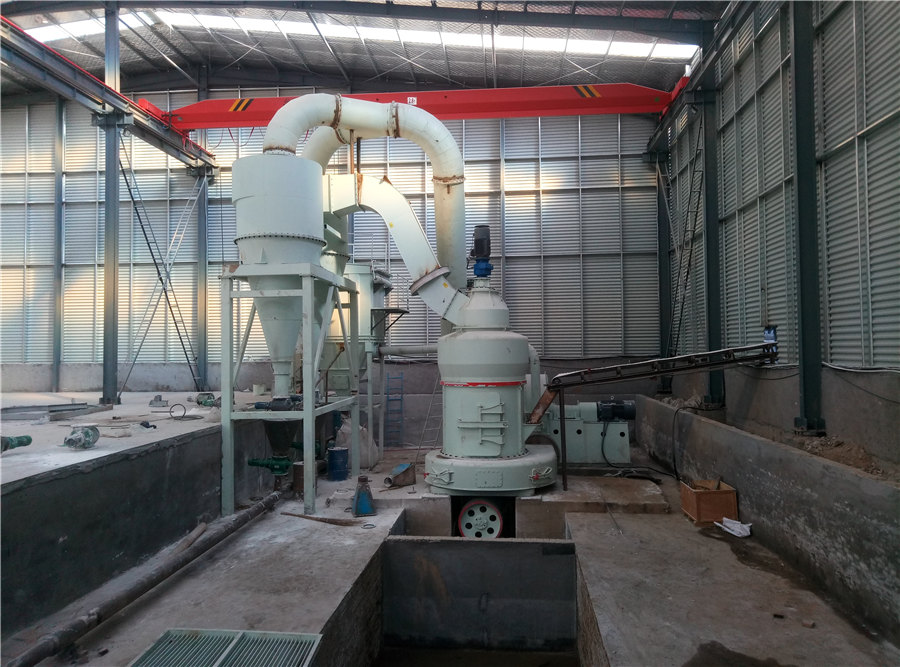
Exploring the World of Metal Surface Finishing: Types,
2024年11月5日 Powder coating is another standard finishing process in which a dry powder is applied and finished with a heatcured process that gives a good aesthetic appearance and strong adhesion of the coating All the processes are designed to serve different purposes; therefore, manufacturers are able to select the right method for the particular functional needs and 2023年10月8日 Iron alloys powder refers to powder metallurgy forms of iron mixed with alloying elements like nickel, chromium, manganese, and carbon Iron powder metallurgy allows the manufacture of parts and components with controlled density, porosity, strength, magnetic and other properties by compacting and sintering ironbased powder mixesIron Alloys Powder: A Complete Guide Additive Manufacturing We use iron phosphate to offer moderate corrosion protection It also serves as a primer for additional coatings Zinc Phosphating: The zinc phosphating process provides a thicker coating than iron phosphating This results in a better Phosphating Explained: How It Works and Why It Matters2024年7月18日 In simple terms, phosphating involves placing a metal — usually iron, zinc, or aluminum — in an acidified solution of phosphate ions Milt Stevenson Jr Typical phosphoric acid baths also contain metal ions (zinc or manganese), an oxidant such as nitrites and/or chlorates, and accelerators such as nickelfluorides, too, if the bath is applied to aluminumPhosphating: The Process and its Applications
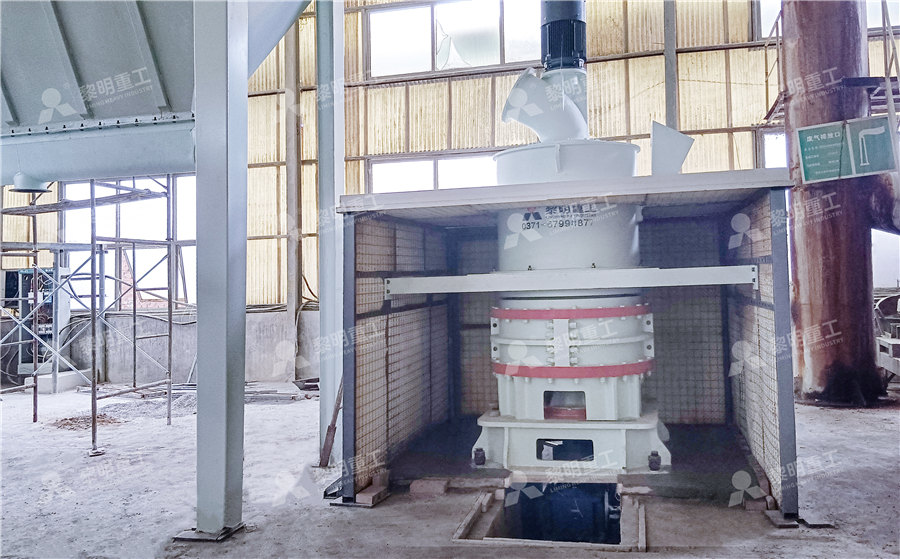
Powder Metallurgy: A Comprehensive Guide for Beginners
2023年9月5日 It is the most challenging and significant factor in injection molding and constitutes the longest step in the process 26 The Origin of Powder Injection Molding Powder injection molding is a new process that combines powder metallurgy technology with plastic injection moldingThe quality of iron powder varies based on the production method Common methods include atomization, reduction, and electrolysis, with electrolysis yielding the purest form of iron powder Titanium Of the variety of metals available for the powder metallurgy process, titanium is Powder Metallurgy: What Is It? Processes, Parts, Metals UsedPowder coating is a dry finishing process that involves the application of fine, electrostatically charged powder particles to a substrate's surface Conversion Coating: For enhanced corrosion resistance, consider applying a conversion coating such as iron phosphate or zinc phosphatePowder Coating Process Explained – A Detailed Breakdown2008年3月7日 for Metal Finishing since 1989 7 tank hot phosphating process Q We use lot of sheet metal components in an industrial product with a powder coated finish The basic pretreatment used before powder coating is 7 / 8 tank Hot process for cleaning applying a thin phosphate coat7 tank hot phosphating process
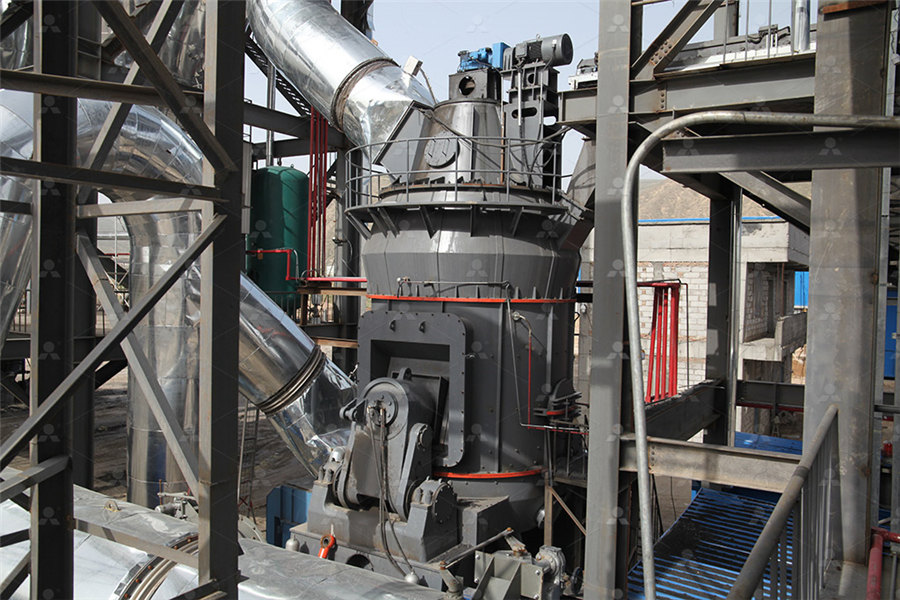
How the Powder Metal Sintering Process Enhances Part Strength
2024年11月4日 Competitive markets need every advantage they can get when it comes to product performance and cost efficiency That’s in large part why so many manufacturing processes exist – to provide options for finding a path toward faster, better, stronger components Powder metallurgy (PM) is a metalforming process that sinters compacted metal powders just 2023年9月19日 Iron Phosphate Iron phosphate part Iron phosphate may be applied to the surface in an immersion or spray application Parts must first be cleaned to remove surface oils, grease, and shop dirt This may be accomplished in a separate cleaning step or in a combination of cleaning and phosphate in a single process tank or stationPhosphate Coatings: Some Basic Points FinishingandCoatingThe powder metallurgy process, also known as pressandsinter consists of mixing elemental or alloy powders, compacting the mixture in impregnation, machining, vibratory finishing, plating, shotpeening or heat treatment Most Conventional Powder Metallurgy Process MPIF2016年4月22日 Iron phosphate provides increased corrosion resistance Most powders provide a saltspray rating of 250 hours on clean metal, but what happens when the protective powder coating is scratched or worn? Phosphate Using Iron Phosphate To Get A Better Powder Coated
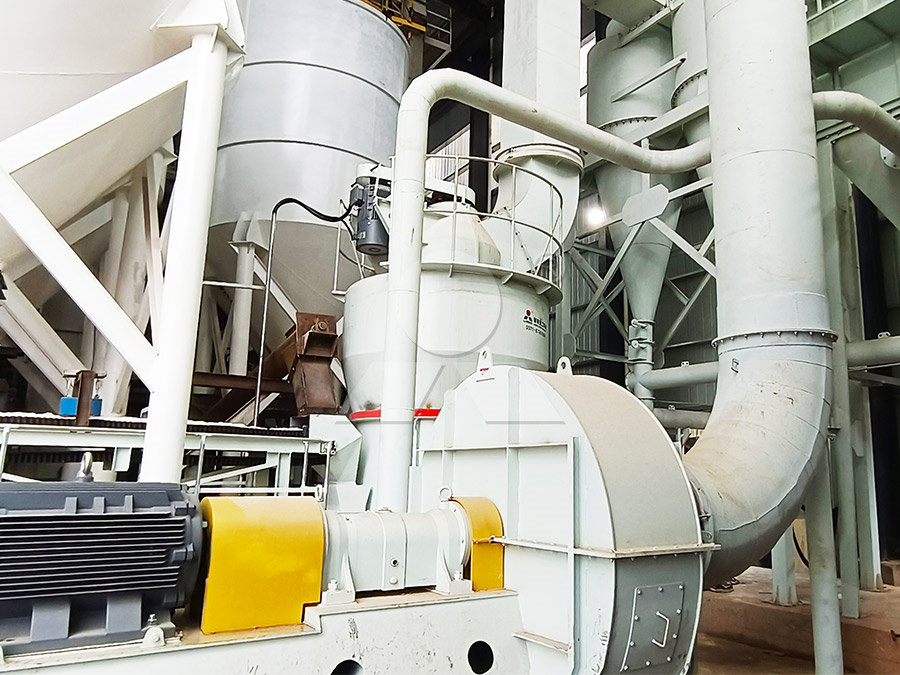
Modeling of material removal in magnetic abrasive finishing process
2020年7月1日 Modeling of material removal in magnetic abrasive finishing process with spherical magnetic abrasive powder Author links open overlay panel Yuewu Gao, Yugang Zhao, Guixiang Zhang, Fengshi Yin, Haiyun Zhang Development of Spherical IronBased Composite Powder with Carried Alumina Abrasive Grains by Plasma Spray Adv Mater Res The process of manufacturing of shaped components or semifinished products such as bar and sheet from metal powder is called as Powder metallurgy The technique of powder metallurgy combines unique technical features with cost effectiveness and generally used to produce sintered hard metals known as ‘carbides’ or ‘tungsten carbides’Introduction To Powder Metallurgy Principles of Powder Metallurgy ProcessShot blasting produces a uniform surface finish by removing residual surface burrs or debris from the casting process Sand Blasting Process Painting and Powder Coating Castings can be finished according to customer specification, with wet painting and Finishing Processes for Sand Castings Iron foundryFig1 finishing process of cylindrical work piece in magnetic field Novateur Publication’s International Journal of Innovation in Engineering, Research and Technology particles are prepared by sintering of ferromagnetic powder (iron) and abrasive powder at a very high pressure and manufacturing process employed determines surface finish MAGNETIC ABRASIVE FINISHING Zenodo
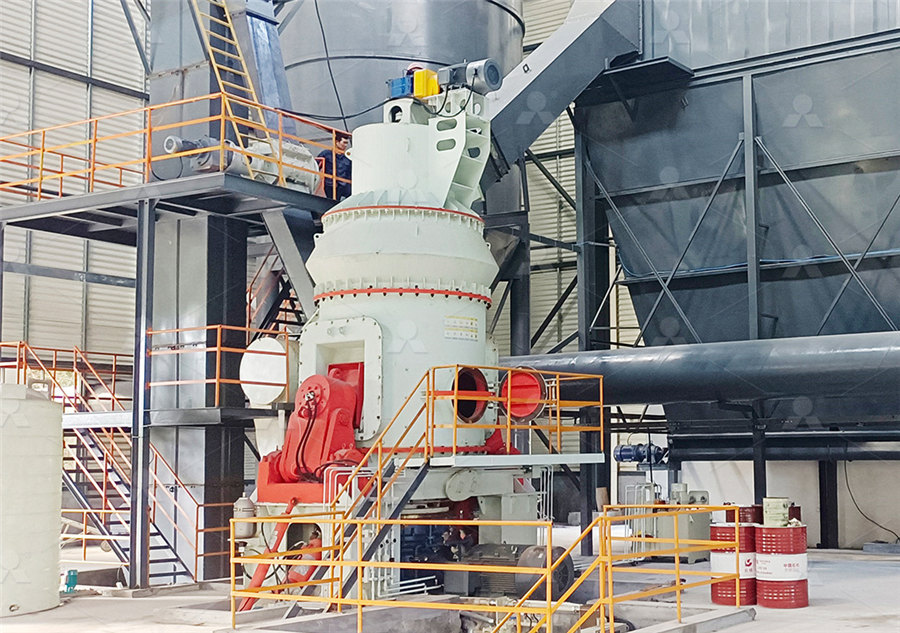
Iron Ore Processing: From Extraction to Manufacturing
2024年4月26日 The final stage in iron ore processing is ironmaking, where the iron ore is transformed into molten iron through a process called reduction The most common method of ironmaking is the blast furnace route In a blast furnace, iron ore, coke (carbon), and fluxes (limestone or dolomite) are loaded into the furnace from the topCleaning: Iron phosphate coating also provides a cleaning process for the surface before powder coating, which ensures the best possible adhesion for the coating Overall, iron phosphate coating is an effective pretreatment process that can improve the adhesion and corrosion resistance of powder coating on metal surfaces, making it a costeffective and environmentally friendly optionIron Phosphate Commercial Finishing CorporationSetting Up the Powder Coating Gun: Adjust the powder coating gun’s settings for optimal performanceChange the air pressure, flow rate, and spray pattern to suit the specific powder and item being coated Applying Powder Evenly: Hold the gun at a consistent distance from the surface, moving in smooth, linear motionsEnsure each pass overlaps slightly with the 9 Key Steps To Powder Coating Process Zemetal2024年6月24日 The process involves applying a dry powder that’s then cured under heat to form a Skip to content Call us : 9722999911 Opening hours : Monday – Friday 8:00 AM – 4:00 PM CALL TODAY: 9722999911 Opening hours : Monday – Friday 8:00 Powder coating is a finishing process where a dry, powder form of paint is Powder Coating Process: StepbyStep for Beginners
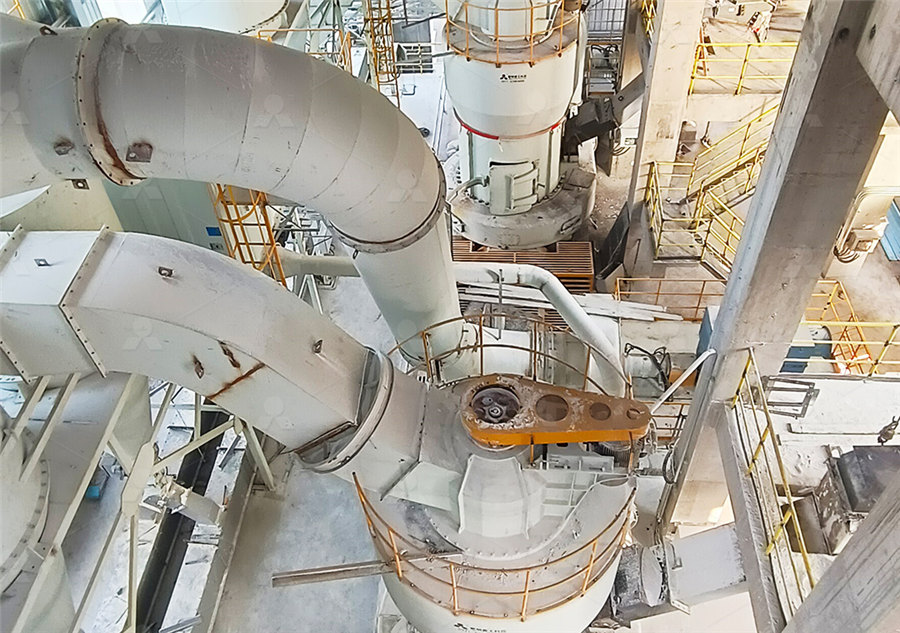
How to Prep Aluminum for Powder Coating Reliance Finishing
Powder coating is a highly effective method for enhancing the durability and aesthetic appeal of aluminum surfaces As the leading provider of quality powder coating services in Grand Rapids and across West Michigan, Reliance Finishing ensures your aluminum components receive topquality treatmentIn a compact that contains only iron powder particles, the solid state sintering process would generate some shrinkage of the compact as the sintering necks grow However, a common practice with ferrous PM materials is to make an Sintering in the Powder Metallurgy Process2020年9月3日 Powder coating is a finishing process that is used to add colour to objects (usually metal), and strengthen them beyond the capabilities of conventional paint It’s a freeflowing, dry powder based on polymer resin, and How Does Powder Coating Work? Prestige Wrought the proceSS – FroM iron to cip CIP is produced by thermal decomposition of iron pentacarbonyl (Fe(Co) 5), which is previously distilled to high purity Carbonyl Iron Powder Finishing Fe(co) 5 Synthesis Fe(co) evaporation distillation Fe(co) decomposition Cr Mo Fe ni FeParticle GrowthCarbonyl Iron Powder
.jpg)
Understanding the Powdered Metallurgy Process
Powder metallurgy is a process that creates precise and accurate parts by applying a range of pressures to press powdered metals and alloys into a hard tooling Here are the four fundamental processes in this technique: Powder Preparation All metals and alloys can be reduced to a powder, regardless of the method utilizedTo support this, we continue to invest in finishing equipment and facility expansion, including: New hybrid finishing for singlepass primer powder and topcoat; Multiple conveyorized powder systems with laser oxide removal; Multiple batch systems: wash, liquid coat, powder coat, sandblasting; Salt spray testing and ISO 9001 quality managementIndustrial Finishing Services Standard Iron2024年6月17日 The ACS5 Powder Coating Guidelines provide instruction on powder coating over galvanized steel, creating a hybrid solution that marries the protective benefits of galvanizing with the aesthetic freedom of powder coatings Enhanced Corrosion Resistance Powder coating on galvanized steel offers a powerful duallayer defense against corrosionGalvanizing vs Powder Coating: A Comparative Analysis1 WHAT IS POWDER COATING Powder coating is an advanced method of applying a decorative and protective finish to a wide range of materials and products that are used by both industries and consumers The powder used for the process is a mixture of finely ground particles of pigment and resin, which is sprayed onto a surface to be coatedPRETREATMENT FOR POWDER COATING
.jpg)
Phosphating Process Products Finishing
2008年2月1日 We are in the process of setting up a pretreatment plant, and would like to know which phosphating process will be best, considering quality, investment, and maintenance for: 1) room temperature dicationic process, 2) tricationic 2009年4月27日 We are doing a WBC grade cast iron parts Hot Zinc phosphating (7 tank Process) and then powder coating60% of the surface is covered with powder coating and remaining as phosphating finish Our customer doesn't want to apply rust preventive oil on the phosphated surface but requires to have good shelf life against rust before assemblyIt is Iron Phosphate Coating Process QA'sSponge iron provides the base feedstock for all ironbased, selflubricating bearings and still accounts for around 30% of iron powder usage in PM structural parts Solid state reduction is also used for the production of refractory metal Powder production technologies Powder 2023年2月22日 Powder Metallurgy Process: Not Without Limitations PM is economical and widely used, but it has its limitations The powder metallurgy process cannot produce parts beyond 220 kilograms due to the fluidity of Powder Metallurgy Process: Steps, Applications
.jpg)
A Guide to Steel Finishing Options
2023年1月6日 It is a prerequisite for other metal finishing techniques, such as powder coating or electroplating, and it is a valuable step in improving a product An acid bath in either nitric or citric acid dissolves free iron from steel’s 12 STEP FINISHING PROCESS Nothing matches the look of a wellmade, wrought iron iron door The weight, the detail of the artisanal wrought iron, the stately effect it lends to any building comes together to create the most enviable door and 12 Step Finishing Process Forever Custom Iron DoorsPowder Coating pretreatment: iron phosphate vs zinc phosphate Q I have a big problem I run a powder coating and a pretreatment facility The process is the CRS (Cold Roll Steel) sheets are first dipped into an 8process pretreatment stage One of the stage is on the phosphating where I obtain an Iron Phosphate instead of our usual zinc Best metal pretreatment before powder coating? Onestep vs iron Powder metallurgy usually refers to powder compression molding The powder metallurgy process involves several stages, such as powder preparation, mixing, pressing, sintering, etc, each contributing to the final production of highquality parts and components Powder production Powder production is a crucial step in the powder metallurgy processWhat is Powder Metallurgy Process, Materials, and Applications
.jpg)
Understanding How the Powder Coating Process Works
2023年12月11日 Powder coating is a process where manufacturers apply dry powder on a product’s surface and then cure or bake it to adhere the particles to the material The powder is electrostatically charged, allowing it to stick to the surface evenly, and the result is a hard, durable, and attractive finish that lasts much longer than conventional paint2024年9月7日 Powder Coating Powder coating is a finishing process in which a powder material is sprayed onto a surface and then cured under heat to form a hard coating This method is renowned for its highquality, durable finish, offering Ultimate Guide to Metal Finishing TechniquesThe Powder Metallurgy Process Powder Metallurgy comprises a family of production technologies, Powder production Virtually all iron powders for PM structural part production are manufactured using either the sponge iron process or water atomisation The application of finishing processes to the sintered partThe Powder Metallurgy Process2021年12月15日 The finishing accuracy and efficiency of magnetic abrasive finishing (MAF) are mainly depending on magnetic abrasive powders (MAPs) A new kind of core–shell structured carbonyl iron powders (CIMAPs) with a hard Fe/Al intermetallic shell for magnetic abrasive finishing is successfully synthesized by insitu alloyhardening the surface of spherical Achieving insitu alloyhardening coreshell structured carbonyl iron