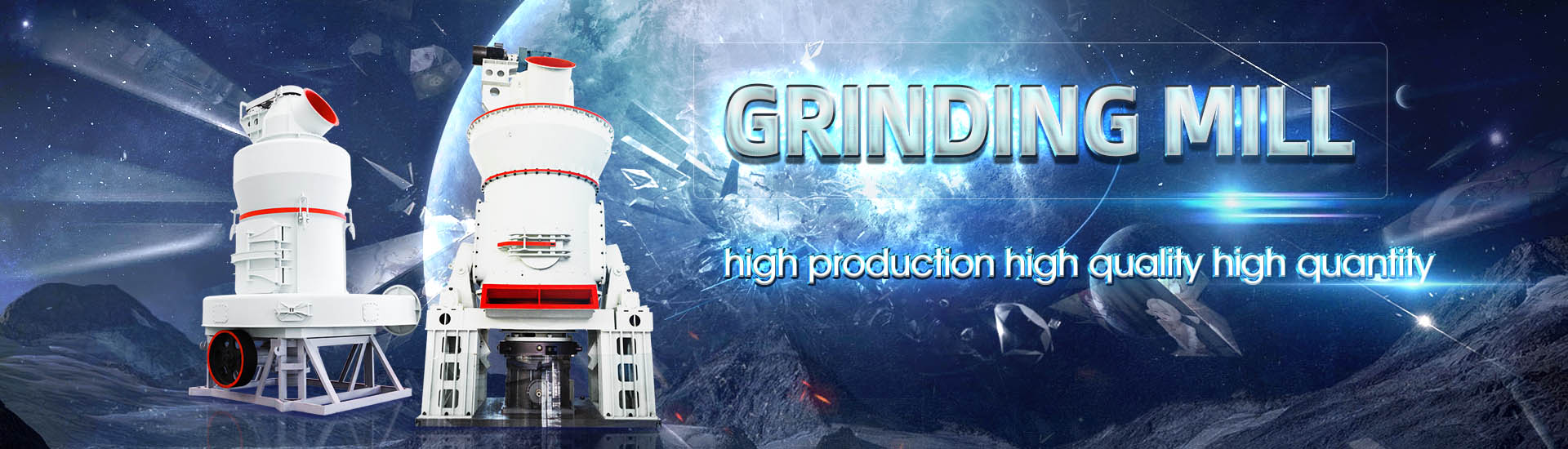
What is the working oil pressure of the grinding production line
.jpg)
In Grinding, Coolant Application Matters SME
2008年3月1日 Pressure controls the velocity of the fluid; the flow rate and temperature control the rate of heat transfer into the fluid The direction of the flow allows the fluid to remove the airbarrier that travels with the wheel Many researchers have studied the role of grinding fluids in 2016年9月4日 research on fluid application systems to determine how much flow is needed, what pressures are required and how the fluid should be injected into the grinding contact Optimisation of Fluid Application in Grinding Liverpool John common solution to grind raw materials and cement Roller presses are used mainly in combination with a ball mill for cement grinding applications and as finished product grinding BALL MILLS Ball mill optimisation Holzinger Consulting2020年1月1日 The importance of high pressure in the lubrication gap can be led back to the increase of the evaporation temperature of the metalworking grinding fluid and that the Interactions of grinding tool and supplied fluid
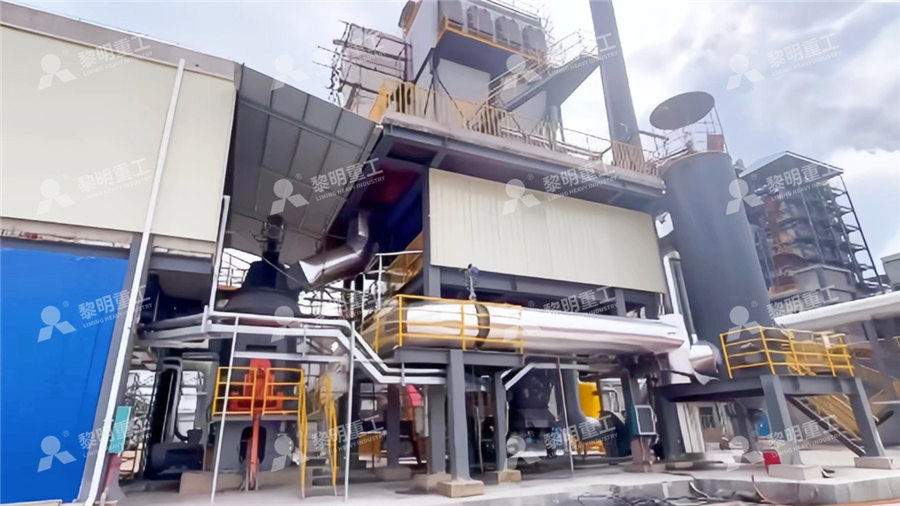
The use of cooling lubricant for grinding
2022年10月27日 The grinding fluid must be routed through the appropriate coolant line to provide the required pressure and precision UNITED GRINDING machines work with three 2014年8月18日 When working with tube and material drawing shops, the lubricant governs the entire operation Combine speed, (activating the lubricant) precise tool geometry, (allowing the lube to penetrate protect) and compatible A Guide to Metalworking Fluids Production MachiningThe fluid pressure force increases with the cutting speed as a function of the cooling lubricant volume flow and can exceed the grinding normal force according to the amount The outcome is a total normal force that increases with the Grinding Process SpringerLink2023年7月1日 However, synthetic oil is recommended for roughing processes, and hydrocrackedbased oil is recommended for finishing processes The addition of some Cooling and lubrication techniques in grinding: A stateoftheart
.jpg)
Fluid Flow and Pressure in the Grinding WheelWorkpiece Interface
2005年3月21日 It was found that the flow rate through the contact zone between the wheel and the workpiece is a function of fluid pressure in the grinding zone, delivery flow rate, fluid 2021年7月6日 This study has investigated an existing production line of an angle grinder manufacturing and used an LM approach to improve the production process to ensure the Balancing of the Production Line Process in the Manufacturing of 2021年8月27日 Before understanding the working we must go through the principle of working of electrochemical grinding The working principle of electrochemical grinding is When a metal surface is acted upon with an Electrochemical Grinding: Definition, Parts or 2023年7月19日 With these sorts of shaper machines, the hydraulic system provides the reciprocating action of the ram The hydraulic shaper utilises highpressure oil This is provided through a system which is understood by the Shaping Machine: Learn the working principle,
.jpg)
What is Centerless Grinding? The complete guide to
2021年10月19日 Today we are going to answer a simple question about a simple machining process; What is Centerless Grinding? Centerless grinding is a process that has been a part of manufacturing for nearly 100 yearsIt helps This is based on production rate, die friction, and quality In this particular case, corn and grain and grain byproducts pelleted on a 5/32” x 13/4” operated at friction of 210°F and the mill operated 6070% mill load, at rates of 822 ton; the quality was 510% fines Die selection is a function of quality and production rateThe Pelleting Process CPMThe residual oil content in meal, the residual hexane content in meal and in oil and the oil and meal moisture are the main quality parameters targeted after solvent extraction and meal treatment In the solvent extraction section, utilities like steam consumption and electricity are typically ≤ 150 kg/t and ≤ 5 kwh/t, respectively, with hexane consumption of 046 kg/tOverview of the soybean process in the crushing industry• Check the grinding wheel before mounting it Make sure it is properly maintained and in good working order • Follow the manufacturer’s instructions for mounting grinding wheels • Keep face of the wheel evenly dressed • Ensure that the wheel guard covers at Chapter 5: Surface Grinder – Manufacturing Processes 45
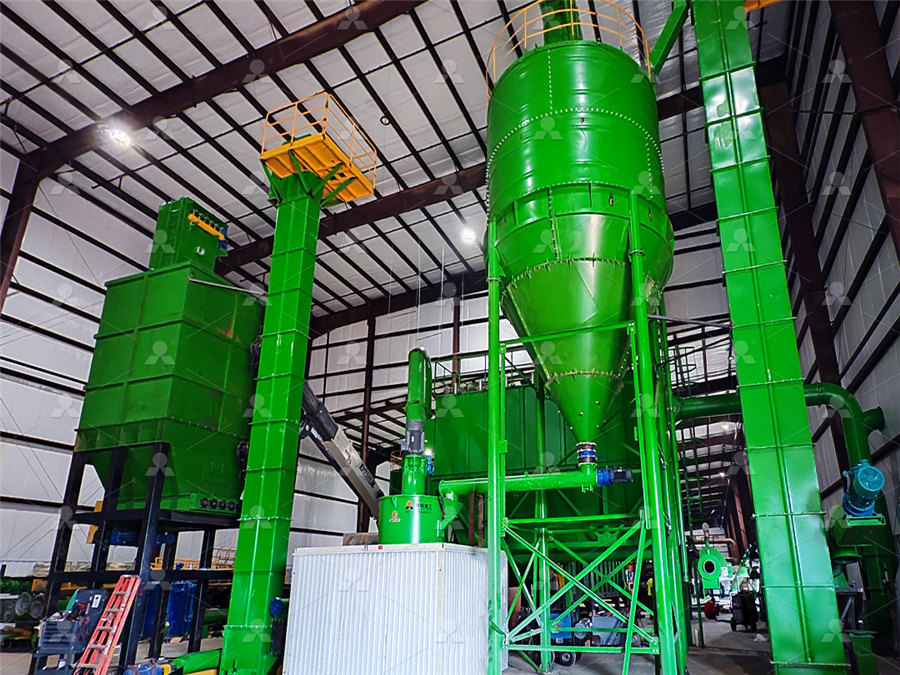
GENERAL ASPECTS OF ROLL COOLING FOR HOT COLD
This oil plateout is very important in obtaining proper lubrication and hence proper strip surfacequality If the rolls run too cold, insufficient oil plateout may occur and strip surface suffers Like for hot rolling, oil can be applied to the roll gap soby called direct applicationure oil is sprayed into the P roll gap just before the bite2019年6月25日 The article presents results of research concerning computational fluid dynamics (CFD) of water oil emulsion in grinding zone during sharpening of hob cutter face surface The numerical simulations made possible to determine the influence of different angular nozzle settings and nominal emulsion flow rate on the quantity of emulsion directly reaching the area Numerical analysis of coolant flow in the grinding zone2024年10月17日 At its core, oil and gas production is a series of processes aimed at extracting, refining, and distributing crude oil and natural gas from subsurface reservoirs to consumers worldwide These processes, broadly categorized into upstream, midstream, and downstream stages, involve a range of activities from exploration and drilling to refining and marketing of What is Oil and Gas Production: Stages, Methods ImpactIndepth, practical, comprehensive grinding education for hardcore grinders working in production grinding Overview: The Book of Grinding is the most indepth, comprehensive, practical resource in existence for engineers, machine operators and salespeople working in production grinding It has been created in The Grinding Doc’s popular, graphicsfocused style of describing complex The Book of Grinding
.jpg)
Machining 101: What is Grinding? Modern Machine
2021年7月3日 Made in the USA Season 2 Episode 6: Why, and How, Hardinge is Reshoring Machine Tool Production In this episode of Made in the USA, several executives and senior staff at Hardinge give their firstperson June 2022; ARCHIVE Proceedings of the Institution of Mechanical Engineers Part C Journal of Mechanical Engineering Science 19891996 (vols 203210) 236(2):1107(PDF) A comprehensive review on the grinding process: 2002©John Wiley Sons, Inc M P Groover, “Fundamentals of Modern Manufacturing 2/e” Material removal by action of hard, abrasive particles usually in the form of a bonded wheel • Generally used as finishing operations after part geometry has been established by conventional machining • Grinding is most important abrasive processLesson 6 GRINDING AND OTHER ABRASIVE PROCESSES KSUThe workpiece is moved past the grinding wheel either manually or by power feed The grinding wheel is composed of abrasive grains held together in a binder These abrasive grains act as cutting tools, removing tiny chips of material from the What is Grinding? – Working Principles, Applications Use of
.jpg)
Centerless Grinding:What is and How it Works?
A centerless grinding process uses abrasive cuts to remove material from a workpiece’s outside diameter Centerless grinding is different from traditional grinding because it does not require that the workpiece be mounted or fixed The material can be removed quickly, producing a smooth and precise finish2024年3月11日 Grinding, a critical precision machining process for difficulttocut alloys, has undergone continual technological advancements to improve machining efficiency However, the sustainability of this process is gaining heightened attention due to significant challenges associated with the substantial specific grinding energy and the extensive heat generated Towards Sustainable Grinding of DifficulttoCut Alloys—A 2022年3月16日 Abstract HPGR has been found to be efficient size reduction equipment compared to conventional size reduction equipments due to its potential processing benefits in terms of energy savings, improved exposure or liberation and particle weakening The objective of the current work is to study the optimization of different process parameters during grinding Potential of HighPressure Grinding Roll (HPGR) for Size During a machining process with a trackbound cutting edge engagement, the cutting edge of the grain penetrates the workpiece upon a flat path and, after a phase of elastic deformation, triggers plastic flow of the workpiece material (Fig 3)Due to the shape of the cutting edge, the angle between the cutting edge contour and the workpiece surface is very small at the beginning of Grinding Process SpringerLink
.jpg)
Determining a Feasible Working Condition for Hydrostatic Spindle
The oil viscosity η is determined by equation as [1]: 2 2 0 h s S nD ph η= (5) where S h speed parameter; n – spindle rotation speed (Rad/s); p s – pump pressure (MPa) The oil recess pressure r pin accordance with the ability of manufacturing technology is in a range of 15 MN/m2 For hydrostatic bearing, the ratio of oil chamber and The addition of a grinding aid spreads the feed particles farther apart, thus exposing more surface area to the grinding media, resulting in increased production The grinding aid adheres to the individual particles, thereby restoring the particles to a balanced state, thus reducing agglomeration, ball coating and pack setEverything you need to know about clinker/cement Grindingaba Grinding The aba company was founded in 1898 under the name "Messwerkzeugfabrik Alig Baumgärtel Aschaffenburg", hence the initials aba Today, the aba Grinding Technologies is exclusively focused on the What is the Lapping and Define the Process?optimising the process, the grinding tools will have a significant impact on lower production costs as well as maintenance costs Ball mills and grinding tools Cement ball mills are typically twochamber mills (Figure 2), where the first chamber has larger media with lifting liners installed, providing the coarse grindingBALL MILLS Ball mill optimisation Holzinger Consulting
.jpg)
Application of optimized lubricooling technique in throughfeed
2022年2月2日 Throughfeed centerless grinding is a highproductivity machining process widely used for mass production of cylindrical parts and rotationally symmetrical parts in automotive and bearing industries Grinding process is strictly related to large amount of heat generated in the cutting zone, ie, the interface between the workpiece and the abrasive tool This process 2023年2月25日 The angle of repose is an intrinsic characteristic of a given material; it depends principally on: particle size, rotational speed of the kiln (Fig 2), and surface condition of the kiln wallMore specifically, this angle characterizes the flow properties of “solid particles” in the kiln; it is often assumed to be constant but may vary along the length of the kiln, in correlation with Rotary kiln process: An overview of physical mechanisms, models In centerless grinding, the workpiece is held between two grinding wheels, rotating in the same direction at different speedsOne grinding wheel is on a fixed axis and rotates so that the force applied to the workpiece is directed downward This wheel usually performs the grinding action by having a higher linear speed than the workpiece at the point of contactCenterless Grinding an overview ScienceDirect Topics2016年6月3日 This device offers a significant power savings on wet fine grinding applications when compared to conventional tumbling mills This paper describes the laboratory application of this mill wet grinding hydrated alumina to products of 50 percent passing 2 to 6 microns The basic grinding action in the Tower Mill is abrasionTower Mill Operating Work Index 911Metallurgist
.jpg)
Understanding Grinding Fluid Canadian Metalworking
2011年10月25日 The arc of contact in grinding is the portion of the circumference of the grinding wheel that is in contact with the workpiece According to Foster, the longer the arc of contact, the more critical wetting becomes “The correct velocity also is very important A lot of people will flood the grinding area, but this is actually not beneficial2018年12月1日 working oil e xtraction and especially with the h elp of cold press co ld sque ezing or c old pressing Cold press is preferred due to its wide usage areas, simple use, lack of manpower,(PDF) Cold press in oil extraction A review ResearchGate2018年1月1日 In times of unstable market development due to the energy system transformation and legislative measures concerning the reduction of CO 2 emissions, the manufacturing industry is increasingly aware of the ecological and economical importance of the factor energy A considerable share of industrial energy and resource consumption can be attributed to Energy efficiency of stateoftheart grinding processesmachining, which is about 1/20th of that of general grinding wheels 2 General grinding is line contact processing Honing is surface contact processing 3 It acts as a lubrication as a sliding surface and an oil reservoir of a rotating part Trend of honing processing!What is honing? 株式会社サクラ・アイ・ディー
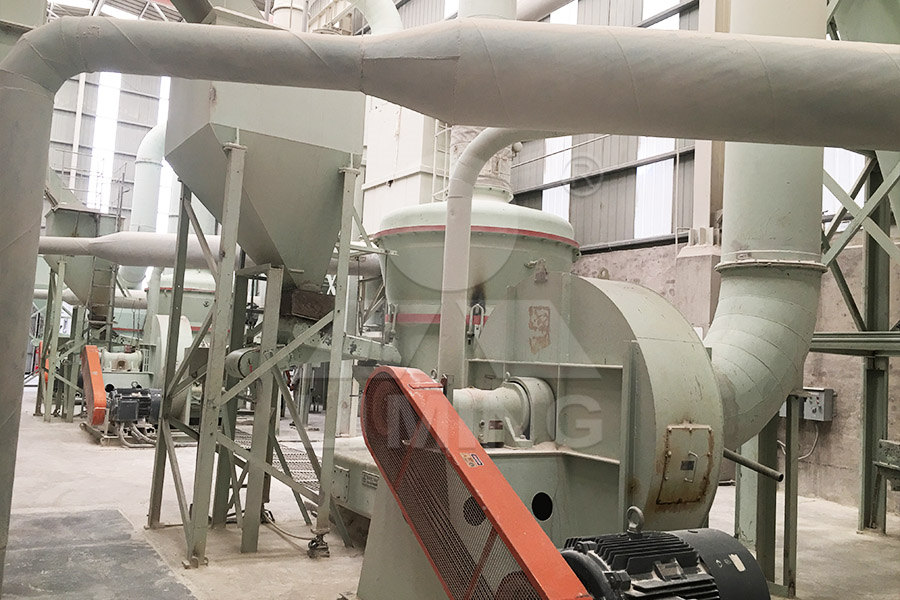
The Science Of HighPressure Coolant Production Machining
2004年6月25日 Unfortunately, most of the manufacturers that buy high pressure don’t really know how to get the most benefit out of it There is even some confusion about what pressure qualifies as “high pressure” When I refer to high pressure, I mean at least 1,000 psi2015年3月21日 Fig 2 Typical schematic diagram of straight grate system The gratekiln system depicted in Fig 1 consists of a traveling grate for drying and preheating the pellets to about 1040 deg C, a rotary kiln for uniformly heating Understanding Pellets and Pellet Plant Operations2024年4月3日 In precision grinding, plentiful and effective coolant is missioncritical As abrasive compounds in grinding wheels remove material, temperature rises quickly Oilbased and watermiscible coolants each help to ensure a Oil Water: Which Coolant is Best for Precision CNC 2021年1月1日 India is the world's second largest producer of cement and produces more than 8 per cent of global capacity Due to the rapidly growing demand in various sectors such as defense, housing, commercial and industrial construction, government initiative such as smart cities PMAY, cement production in India is expected to touch 550–600 million tones per Review on vertical roller mill in cement industry its performance

What is Grinding? Definition, Working Principle, Types, Applications
2024年2月24日 Grinding is a type of abrasive machining process which uses a grinding wheel or abrasive belt as a cutting tool Grinding is basically a finishing process used for producing close dimensional accuracies and desired smooth surface finishIt is commonly used to remove the material from a workpiece, to produce a smooth finish on the surface of the workpieceGrinding is the common collective name for machining processes that utilize hard, abrasive particles as the cutting medium The grinding process of shaping materials is probably the oldest in existence, dating from the time prehistoric humans found that they could sharpen their tools by rubbing them against gritty rocksGrinding Processes SpringerLink2010年1月1日 Depending on contact conditions, three principle classes of process kinematics can be distinguished: area, line and point contact Area and line contact kinematics are used for high and medium volume production in optics manufacturing, where cup and pellet wheels are applied for the generation of flat and spherical geometriesUltraprecision grinding ScienceDirectPortland clinker is the main constituent of most cements In Portland cement, a little calcium sulfate (typically 310%) is added in order to retard the hydration of tricalcium aluminateThe calcium sulfate may consist of natural gypsum, anhydrite, or synthetic wastes such as fluegas desulfurization gypsum In addition, up to 5% calcium carbonate and up to 1% of other Cement mill Wikipedia
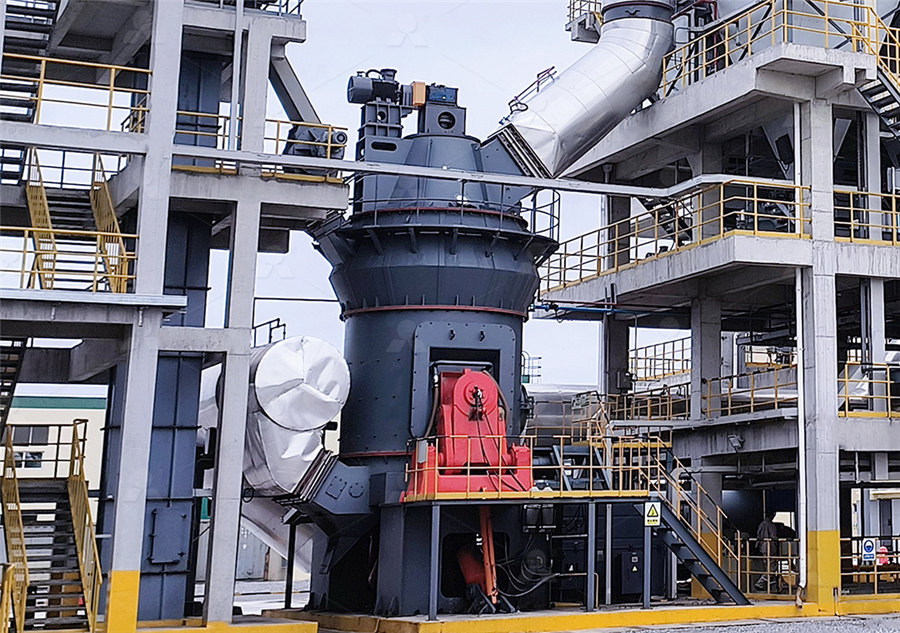
Separation in The Oil Gas Industry, Their Classification and Working
C IP or MP Separator (Intermediate or Medium Pressure): This type of Separator is placed downstream to Production Separator which typically operated at low Pressure than the production separator D LP Separator (Low Separator): These are used where separation is to be achieved at low operating pressure within the Separation Process 3 Based on the Orientation of the 2019年9月7日 Equation () means that the grinding torque \( M{L} \) is proportional to the pressing force \( F{n} \)As mentioned above, the grinding subsystem and the pressing subsystem are actuated separately it allows to design two controllers for the two subsystems respectively, one is for the grinding subsystem to keep the \( \upomega{r} \) to be a constant, Controlling Strategy of Rail Grinding Mechanism for the Constant