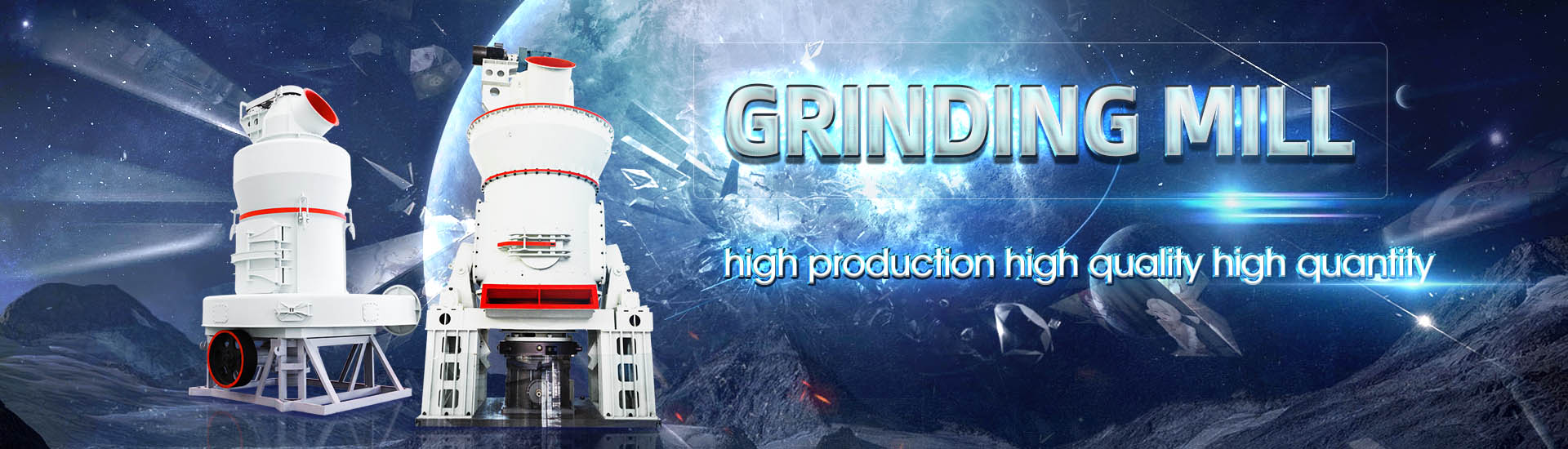
What should I do if the grinding roller jack of the ore grinding mill cannot be lifted down
.jpg)
Operating and Troubleshooting a Grinding Circuit
2015年8月7日 If you make a change in the ore in the fine ore bin, that change will be reflected through the entire grinding process and beyond into the rest of the concentration system The first thing that an operator will have to learn is to be able to tell when the rod mill is, or isn’t, 1970年1月1日 The grinding roller device of Raymond mill need to be replaced after used for more than 600 hours When the grinding roller is replaced, the rolling bearings must be Raymond mill maintenance guideline2019年10月8日 The recommended procedures for conventional grinders are: mount the wheel on its own sleeve, rough true it in the machine, remove the wheel and sleeve assembly from Roll grinding procedures, wheels, belts, setup, end relief, tips2015年4月9日 The grinding mills are categorized in three groups, namely (i) tumbling mills,(ii) roller mills, and (iii) very fine grinding mills which include (a) high speed pulverizing or hammer Grinding Mills and Their Types IspatGuru
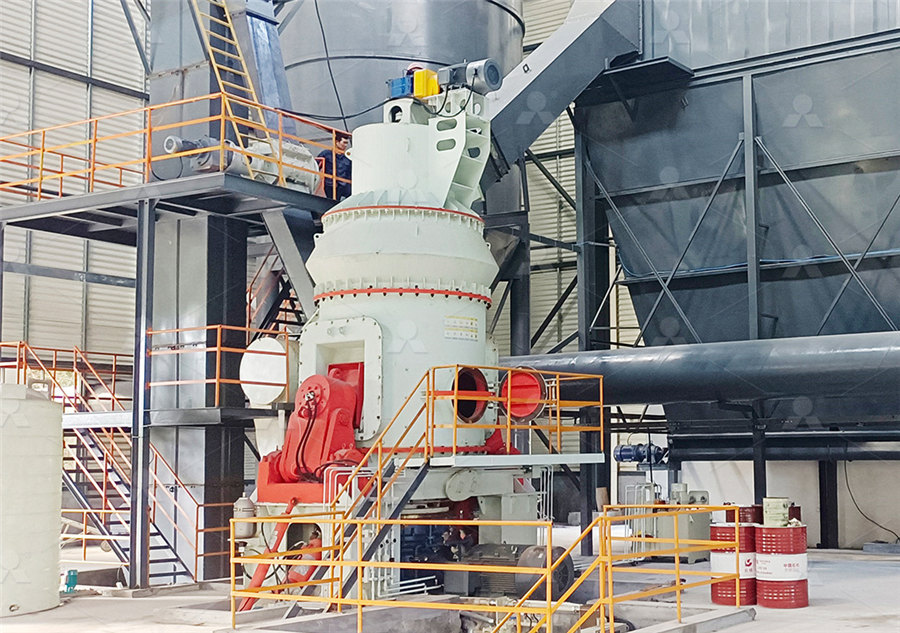
AMIT 135: Lesson 7 Ball Mills Circuits – Mining Mill Operator
As the mill starts, grinding action and throughput increases However, after reaching a critical speed, the mill charge clings to the inside perimeter of the mill Under this conditions, the There are a number of factors that can affect the grinding performance of ores in ball mills These include the milling conditions, the size and shape of the balls, and the type of ore being Factors affecting ores grinding performance in ball mills2024年5月17日 There are two primary methods: This method utilises load cells positioned beneath the mill to directly measure the weight of the material inside It offers the most A guide to SAG Mill management2023年7月20日 Ore grinding is a process to further reduce and disperse the ore particle size In the mineral processing industry, ore grinding is the particle size preparation before the Ore Grinding SpringerLink
.png)
Roller Mill SpringerLink
2023年7月4日 Roller mill is a type of grinding equipment for crushing materials by pressure between two or more rolling surfaces or between rolling grinding bodies (balls, manganese ore fine grinding, and other fields Horizontal Cylinder Roller Mill As for the horizontal cylinder roller, its roller surface and roller have a horizontal layout2019年10月8日 Universal roll drives should be used to insure uninterrupted rotation TIR (total indicated runout) should be checked by dial indicator and recentering should be within 002" on the journals before proceeding with Roll grinding procedures, wheels, belts, setup, end 2020年8月12日 Altun et al [15] explored the influence of the parameter settings of a vertical roller mill on grinding performance and demonstrated the influence of grinding pressure values on the size and mass An investigation of performance characteristics and 2013年8月3日 In Grinding, selecting (calculate) the correct or optimum ball size that allows for the best and optimum/ideal or target grind size to be achieved by your ball mill is an important thing for a Mineral Processing Engineer AKA Metallurgist to do Often, the ball used in ball mills is oversize “just in case” Well, this safety factor can cost you much in recovery and/or mill liner Calculate and Select Ball Mill Ball Size for Optimum Grinding
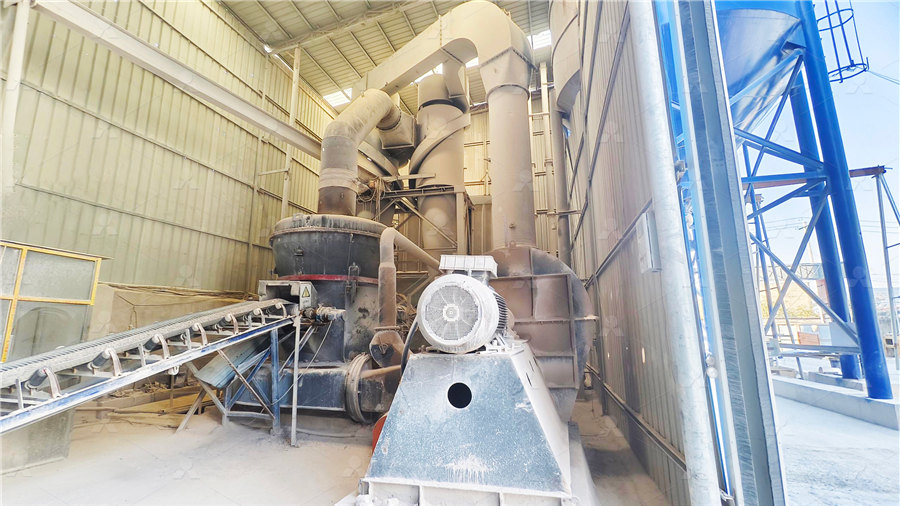
Ore Grinding SpringerLink
2023年7月20日 Therefore, the rod mill is mostly used for coarse grinding of the previous period of ball mill, or grinding of brittle materials and materials against overcrushing, such as tungsten and tin ore before gravity separation; and (3) autogenous mill – it refers to the materials which themselves are collided and ground mutually to be crushed when the grinding mill rotates, and Request PDF On Mar 15, 2015, Mathis Reichert and others published Research of iron ore grinding in a verticalrollermill Find, read and cite all the research you need on ResearchGateResearch of iron ore grinding in a verticalrollermill2022年11月28日 Grinding is a type of finishing process in mechanical processing, with less machining and high precision It is widely used in the machinery manufacturing industry The heattreated and quenched carbon tool steel and carburized and quenched steel parts often have a large number of regularly arranged grinding cracks on the surface that is basically What is Grinding Process How It Works Different Types of Grinding2010年10月18日 The purpose of conditioning is to produce, or restore, a wheel geometry and/or topography appropriate to the grinding task Conditioning involves three different subprocesses: profiling, sharpening and cleaning, where profiling and sharpening come under the general term of dressing [1, 3] With profiling, the required geometrical and runout accuracy of the grinding Dressing of Grinding Wheels SpringerLink
.jpg)
Raymond Roller Mill PartsUltimate Guide Fote Machinery
2023年2月15日 Disassemble and Installation of important parts of Raymond roller mill Removal steps of the grinding roller of Raymond mill 1 Remove the protective cover on the left side of the Raymond mill body, the Vbelt and the double pulley on the fast roller shaft 2 Remove the gear box and the large and small gears on the right side of the fuselage2023年8月2日 The milling process has evolved over time, employing various techniques to produce flour with different particle sizes and applications This paper discusses the advancements in the wheat flour The Latest Innovations in Wheat Flour Milling: A Review2018年11月21日 A grinding wheel is a precision tool with thousands of cutting points on its surface abrasive grains that are held in place by a bond matrix (hence these are known as bonded abrasives) and separated by pores Which Grinding Wheel Should I Choose? Norton Typical advantages of grinding cement raw materials using a roller mill are as follows: • Reduced energy consumption; • Simplified processing system, with drying, grinding and classification processes combined in one machine; • Simplified and rapid control of product parameters such as fineness and chemical composition; and •Grinding Mill an overview ScienceDirect Topics
.jpg)
Revolution of Grinding Mill (Roller Body), Design,
2019年6月3日 Common parts of a Roller Body 1 Break roll feed box 2 Feed inlet 3 Middle wall 4 Impulse transmitter 5 Feed gate segment 6 Feeding device 7 Break feed roll2016年9月1日 Altun et al [15] explored the influence of the parameter settings of a vertical roller mill on grinding performance and demonstrated the influence of grinding pressure values on the size and mass Operational parameters affecting the vertical roller mill 2015年10月23日 In this chapter an introduction of widely applied energyefficient grinding technologies in cement grinding and description of the operating principles of the related equipments and comparisons over each other in terms of grinding efficiency, specific energy consumption, production capacity and cement quality are given A case study performed on a EnergyEfficient Technologies in Cement Grinding IntechOpen2016年10月12日 An increase in the diameter of a mill gives greater economy in two ways : In the first place, the balls do more effective work in a large than in a small mill, because, falling from a greater height, they shatter the pieces of ore with greater force ; in the second place, the ratio of the deadweight of the mill to the weight of the ball charge decreases as the diameter increases Closed Circuit Grinding VS Open Circuit Grinding
.jpg)
Roller mills: Precisely reducing particle size with greater efficiency
roller mill tests of your material in the manufacturer’s test facility with various roll corrugation styles and under conditions that duplicate your operating environment Figure 1 Particle size distributions: Roller mill versus other grinding methods Other grinding methods Roller mill Overs Target particle size Fines Figure 22020年8月10日 Grinding, a process that concentrates a high amount of friction energy on a small area, is usually the last machining step to produce the desired surface finish or the final dimensions of a component Grinding can also lead to thermal damage and potential crack formation on a ground part Overheating, specifically in the peripheral zones of the ground Grinding Burn What Can I do? UNITED GRINDING2021年1月29日 Vertical roller mills, VRMs, are widely used for grinding raw materials in factories engaged in the extraction and processing of minerals Any machine used for grinding or crushing consumes around Increase productivity of vertical roller mill using seven QC tools2013年5月4日 How to choose the best grain mill to grind your own flour at home, because really, every home and kitchen should be experiencing the benefits of grinding your own flour And to do that, you need to make sure you're choosing the best flour mill for your houseWhy You Should Grind Your Own Flour Choosing a Mill
.jpg)
(PDF) Effects of High Pressure ORE Grinding on the
2014年1月20日 In this process, a highpressure grinding roller (HPGR) and a stirred mill were employed as primary comminution techniques and a nanobubble flotation column as a key separation process2017年2月20日 Autogenous grinding should, therefore, be considered and tested when a new plant shall be designed As a grinding mill is built to last for decades, it is more important to watch the operation costs than the price of the mill installation The CRRK series of wet grinding pebble mills are tabulated below Selecting Wet or Dry Grinding MillGrinding Mill Design Ball Mill Manufacturer 911Metallurgist2017年1月17日 Grinding mills are infamous for their extremely low energy efficiency It is generally accepted that the energy required to produce new mineral surfaces is less than 1% of the electricity consumed Breaking down energy consumption in industrial Google's service, offered free of charge, instantly translates words, phrases, and web pages between English and over 100 other languagesGoogle Translate
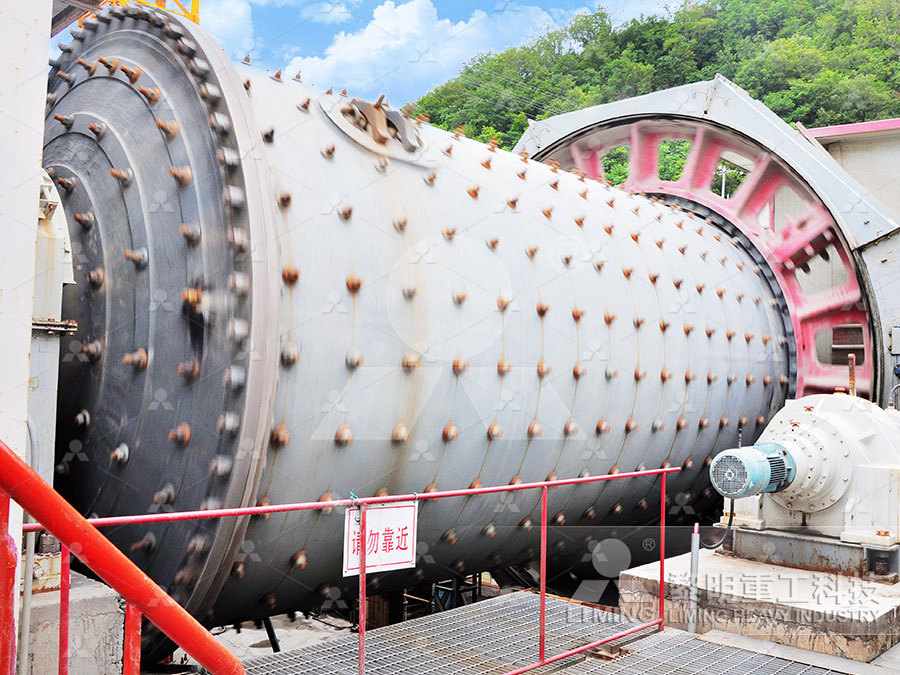
Ball Mill Success: A StepbyStep Guide to Choosing the Right Grinding
2024年8月8日 In mining, a copper processing plant struggled with inefficient ore grinding using standard steel balls, leading to poor mineral recovery rates After analyzing their milling conditions, they opted for highdensity steel balls, which provided the needed impact strength to break down the copper ore more efficiently2016年1月1日 To operate the HPGR Polycom grinding mill, the pressure required is applied hydraulically through four cylinders to the roll that is designed to move laterally The second roll is immovable The crushing pressure applied is generally of the order of 200 MPa, but for hard ores, higher pressures are requiredRoll Crushers ScienceDirectIntroduction This article concerns itself with vertical grinding mills used for coal pulverization only (coal pulverizers), although vertical grinding mills can and are used for other purposes The 3D model in the saVRee database represents a vertical grinding bowl millOther grinding mill types include the ball tube mill, hammer mill, ball and race mill, and , roll and ring millVertical Grinding Mill (Coal Pulverizer) Explained saVReeA crushing plant delivered ore to a wet grinding mill for further size reduction The size of crushed ore (F 80) was 40 mm and the SG 28 t/m 3 The work index of the ore was determined as 122 kWh/t A wet ball mill 1 m × 1 m was chosen to grind the ore down to 200 micronsGrinding Mill an overview ScienceDirect Topics
.jpg)
EnergyEfficient Advanced Ultrafine Grinding of Particles Using
2023年7月10日 The present literature review explores the energyefficient ultrafine grinding of particles using stirred mills The review provides an overview of the different techniques for size reduction and the impact of energy requirements on the choice of stirred mills It also discusses the factors, including the design, operating parameters, and feed material properties, Speed also plays a role in ore grinding; too high of a speed can cause damage to the mill gears and other components, while too low of a speed can cause excessive wear on these same components It is important to find a balance between these two variables in order to achieve optimal grinding performanceFactors affecting ores grinding performance in ball mills2019年4月16日 Conference: Applying a Successful Technology from the Cement Industry: Advantages of Grinding Ore in a VerticalRollerMill; At: Antalya, Türkey(PDF) LEARNING FROM OTHER INDUSTRIES; WHY THE 2019年10月11日 Consequently, efficiency in energy used can be as much as 40% – 45% less than a wet ball mill circuit – noticed with all power going into the comminution of the ore Smarter process control ensures consistent grinding Vertical roller mills: The new leader in grinding
.jpg)
Understanding the SAG Mill in Copper Ore Mining
The Autogenous Mill, also known as AG Mill, is a type of grinding mill used in the mining industry This machine uses ore and rock itself as grinding media to perform its job Unlike other types of mills that use steel balls or rods for in combination with a ball mill for cement grinding applications and as finished product grinding units, as well as raw ingredient grinding equipment in mineral applications This paper will focus on the ball mill grinding process, its tools and optimisation possibilities (see Figure 1) The ball mill comminution process has a high electricalBALL MILLS Ball mill optimisation Holzinger Consulting2022年1月23日 This work concentrates on the energy consumption and grinding energy efficiency of a laboratory vertical roller mill (VRM) under various operating parametersAnalysis and Optimization of Grinding Performance of Vertical Roller 2017年4月1日 Vertical roller mills (VRM) have found applications mostly in cement grinding operations where they were used in raw meal and finish grinding stages and in power plants for coal grinding The mill combines crushing, grinding, classification and if necessary drying operations in one unit and enables to decrease number of equipment in grinding circuitsOperational parameters affecting the vertical roller mill
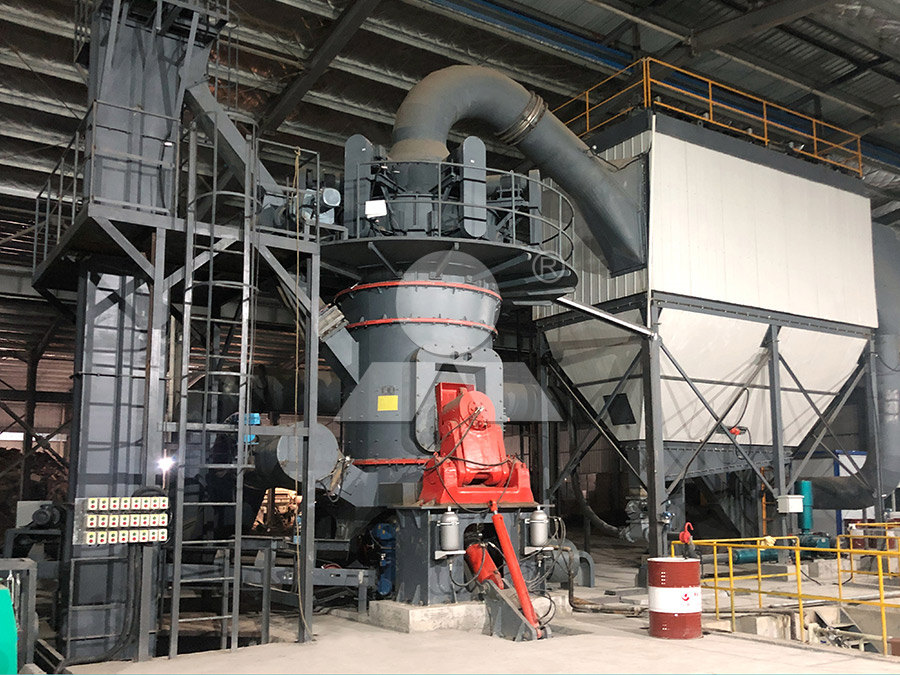
Numerical Investigation of Vertical Roller Mill Operation Using
2023年12月4日 The simulation results showed that the rolling point is moved near the outer diameter of the grinding table as the mill speed increased This behavior matches the previous experimental analysis carried out in a labscale VRM The grinding force increased when the mill speed or gap between the roller and table was reduced2023年4月23日 grinding media in a grinding mill with about 2630 wt% chrome by Chen et al [37] using a phosphate ore in a modified ball laboratory ball mill whose electrochemical potential could be controlled(PDF) Grinding Media in Ball MillsA Review ResearchGate2023年6月6日 Conventional grinding is manual, less precise, and simpler, making it more costeffective for specific applications The choice depends on precision needs, volume, complexity, and resources available Do I need any special training to operate a CNC grinding machine? Yes, CNC grinding machines require operators to have specific knowledge and C Grinding 101: Everything You Need to Know ATMachining2021年5月5日 The following application of Grinding Machine are: The Grinding Machine is used in various industries for grinding The first and foremost industry where this machine is used in Manufacturing Industry The Grinding Machine is used for finishing the cylindrical and flat surfaces In other words, we can say it is used for grinding various materialsGrinding Machine: Definition, Parts, Working Principle, Operation