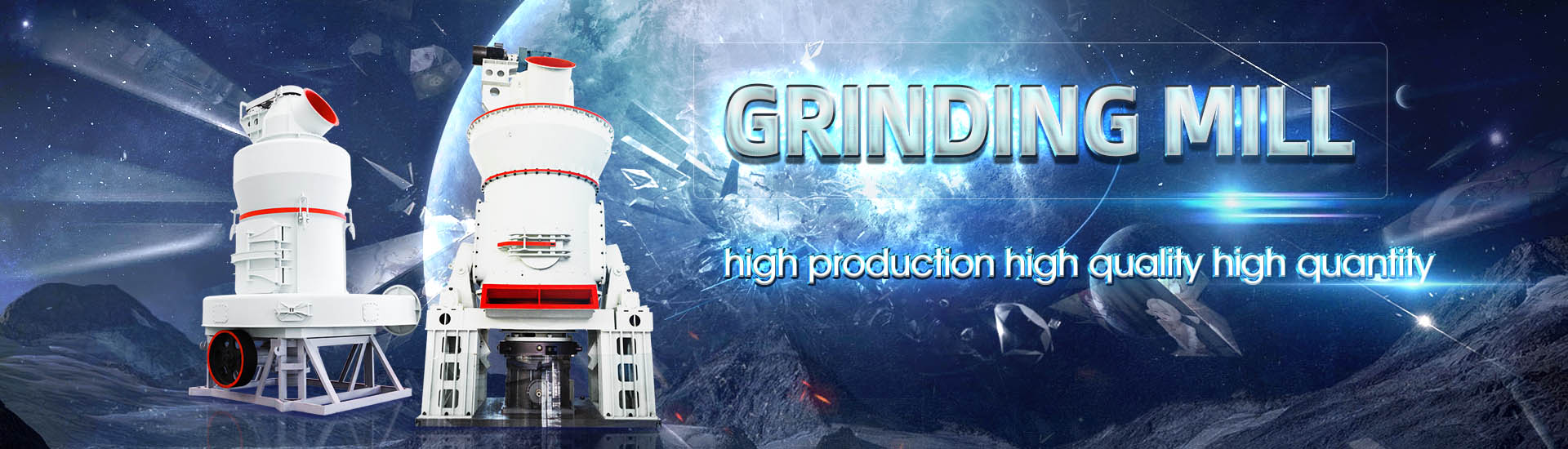
Raw material vertical mill
.jpg)
OK™ Raw and Cement Mill
Our bestinclass OK™ Mill is a globally successful vertical roller mill solution for grinding raw material, cement and slag Its cuttingedge design features consistently deliver the highest quality products with the greatest efficiency It Our bestinclass OK™ Mill is a globally successful vertical roller mill solution for grinding raw material, cement and slag Its cuttingedge design features consistently deliver the highest quality products with the greatest efficiencyVertical roller mills FLSmidth Cement2022年10月3日 Raw materials grinding process is a first step of cement production which is has an important role in the first grinding step Vertical Raw Mill is a main equipment that is used in grinding or (PDF) ANALISA KINERJA ALAT VERTICAL RAW MILL PABRIK II PT Vertical raw mill is one kind of raw mill, generally used to grind bulk, granular, and powder raw materials into required cement raw meal in the cement manufacturing plantVertical raw mill is an ideal grinding mill that crushing, drying, grinding, Vertical raw mill Cement Plant
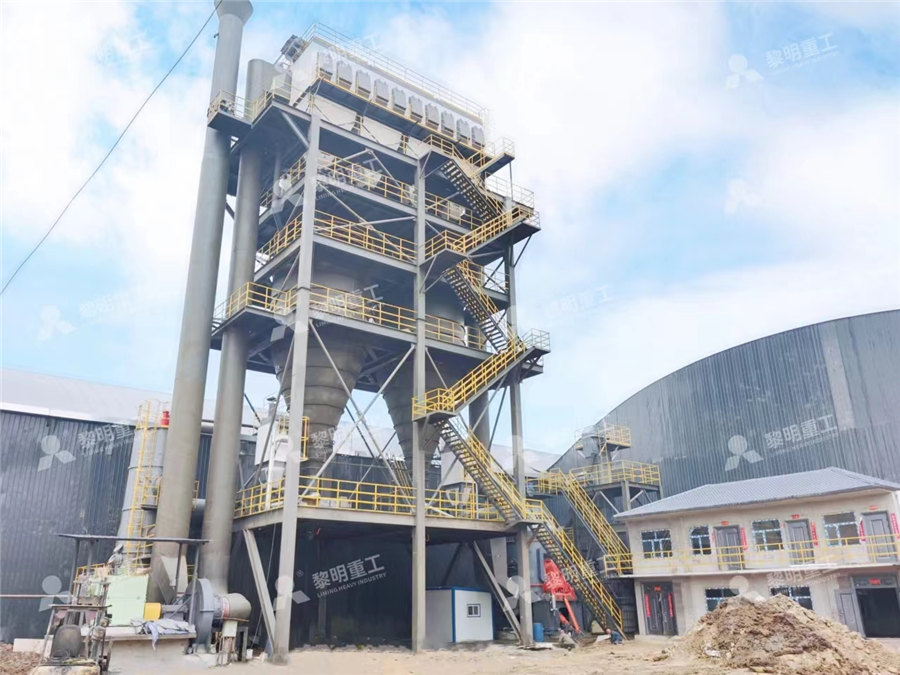
Vertical roller mill for raw Application p rocess materials
Vertical roller mill for raw materials Application p rocess Raw material process Background Grinding raw materials needs lots of energy Tube mills had been used for grinding, but the energy efficiency level was lower Therefore, the introduction of highly efficientThe vertical roller mill (VRM) is a type of grinding machine for raw material processing and cement grinding in the cement manufacturing processIn recent years, the VRM cement mill has been equipped in more and more cement plants around the world because of its features like high energy efficiency, low pollutant generation, small floor area, etc The VRM cement mill has a Vertical Roller Mill Operation in Cement PlantLow investment: the vertical raw mill set crushing, drying, grinding, grading transportation in one, simple system, compact layout, less space, Stable quality of raw mix: because the material stays in the raw mill for a short time, it is easy to detect and Raw mill Cement PlantDry Grinding: Open circuit Ball mill, closed circuit Ball mill, vertical roller mill, Roll Press or Roll press in circuit with ball mill However, it would be seen that the most significant process and types used for raw material grinding operations in modern cement industry are: Process: Dry Closed circuit drygrinding Type of mill: Ball and Raw Material DryingGrinding Cement Plant Optimization
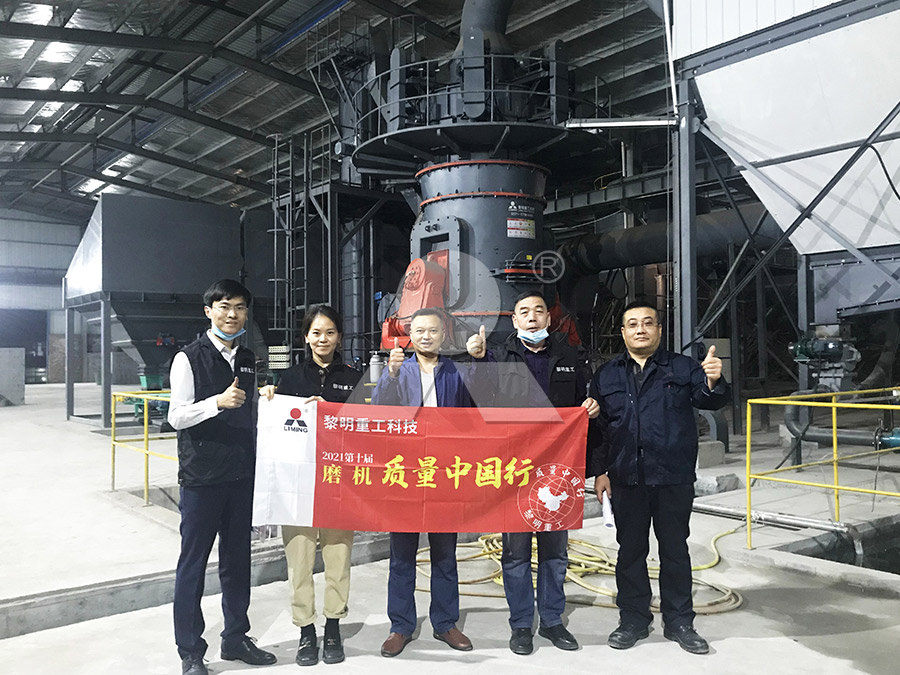
Vertical Roller Mill for Cement Raw Material SINOMALY
Vertical Roller SINOMALY produces cement raw material grinding mills in various specifications These machines are suitable for grinding mill production lines with an output of 2500t/d, 3200t/d, 4000t/d, 5000t/d, 6000t/d and 8000t/d The vertical grinding mill is utilized for the grinding of raw materials, mixed cement, and slag powderThe power consumption of raw material vertical mill system is 97Kwh/t lower than ball mill, that is to say: in one year, a 5000TPD cement plant can save energy in clinker grinding system: 97kWh/t * 5000t/d * 300d=14,550,000 kWh, that means the cement plant clinker grinding system can save 14,550,000 kWh electricity one yearVertical Raw Mill CHAENGIn addition, the raw material grinding process will be supported by a QMR² 48/24 For the 4,000 tons per day kiln line Shiva Cement Ltd contracted a quadropol® vertical roller mill for grinding pet coke with a QMK² 32/16 The same mill size QMK² 32/16 is running in Indonesia for years now, grinding and drying lignitequadropol® Vertical Roller Mill myPolysiusServiceThe cement raw material mixtures are ground, dried, and classified in the Pfeiffer vertical roller mill For drying the material, hot gases are directed into the mill Product fineness can be adjusted within a wide range (0063 to 02 mm)Raw mills for all requirements Gebr Pfeiffer
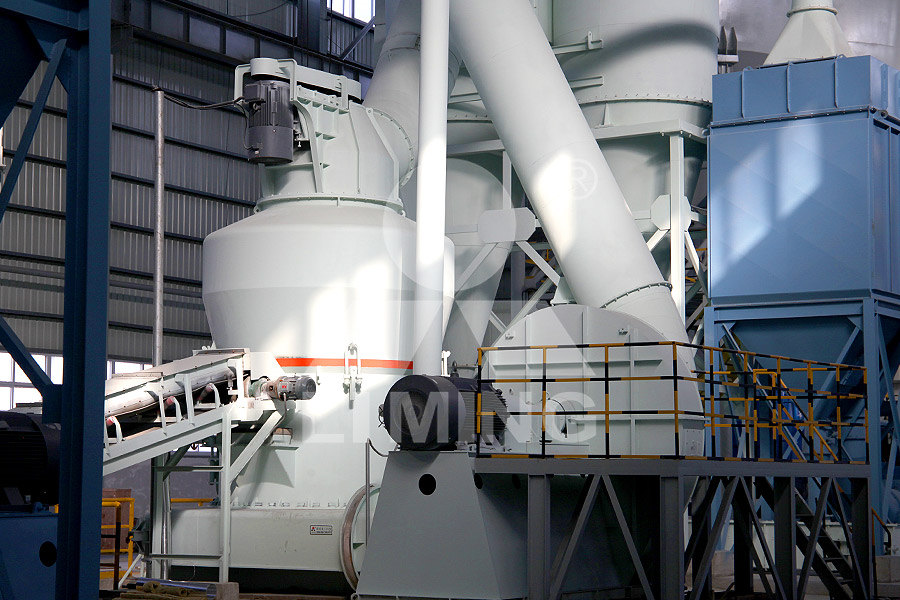
OK RAW AND CEMENT MILL
OK™ Raw Mill QUALITY AND PROFITIMPROVING FEATURES Vertical Roller Mills (VRMs) have been the standard option for raw materials grinding in the cement industry for several decades FLSmidth Cement has supplied the global cement industry with leading VRM designs for all applications since they were first brought to marketRoller; Roller pada Vertical Raw Mill berfungsi sebagai media penggilingan material ke meja Roller Vertical Raw Mill berjumlah empat buah dengan diameter 2,5 mANALISA KINERJA ALAT VERTICAL RAW MILL PABRIK II PTPROCESS TRAINING for operators of Vertical RAW Mills Heating of mill and grinding plant For drying the wet raw material it is necessary that prior to the mill start up the grinding plant isheated for some timeOtherwise the cold PROCESS TRAINING for operators of Vertical RAW MillsUBE Vertical mill will meet these needs UBE Vertical Mill Video Strong Points Energy Saving (Less than 30% compared to Ball Mill) Possible to carry out simultaneously with grinding, drying and classifying; Raw materials are supplied onto the table through the chute and spead to the outer table by the centrifugal force STEP2UBE Vertical Mill UBE Machinery Corporation, Ltd
.jpg)
Vertical roller mills FLSmidth Cement
For raw materials and cement clinker, the vertical roller mill is an excellent grinding solution because of the relatively lower cost of installation, ease of operation and maintenance, energy efficiency and product quality Further, our vertical roller mill solution for cement grinding has an ability to dry, grind and separate within a single Application of Vertical Roller Mill in Cement Industry Vertical roller mill (VRM) technology has become an integral part of the cement industry, offering several advantages over traditional grinding mills Today, this type of grinding machine is becoming more and more popular in both the raw material grinding process and the cement grinding Application of Vertical Roller Mill in Cement ProductionAGICO Cement Vertical Mill AGICO Cement Ball Mill Cement Vertical Mill Grinding System Cement vertical mill, also called roller mill, is another raw mill commonly used in cement pared with the cement ball mill, it has a great difference in structure, grinding principle, process layout, automatic control, and energy consumption, which play an important role in the Raw Mill – Raw Mill In Cement Plant AGICO Cement Raw MillWith the incensement of moisture of the raw material, the powder consumption will decrease obviously The vertical mill saves 30%40% of energy consumption compared to the ball mill Vertical mill has less noise than ball mill, about 2025dB Besides, vertical mill adopt enclosed system, and works under negative pressure, no dust, clean Vertical Cement Mill
.jpg)
Proses Raw Mill (Penggilingan Raw Material) 123dok
Proses Raw Mill (Penggilingan Raw Material) Proses Raw Mill (Penggilingan Raw Material) BaruBaru Ini Dicari Tidak ada hasil yang ditemukan Group CCR tuban 12 mengendalikan dan mengkoordinasikan kegiatan pengoperasian Roller Vertical mill Tuban 12 secara terpusat dari central control room, agar peralatan beroperasi dengan lancar, In addition, the raw material grinding process will be supported by a QMR² 48/24 For the 4,000 tons per day kiln line Shiva Cement Ltd contracted a quadropol® vertical roller mill for grinding pet coke with a QMK² 32/16 The same mill size QMK² 32/16 is running in Indonesia for years now, grinding and drying lignitequadropol® thyssenkrupp Polysius Grinding TechnologiesMPS vertical mill from Pfeiffer is the ideal allrounder Grinding of coal, petcoke, clay, limestone and remote control of grinding pressure and classifier rotor speed ensure a fully automatic operation of the MPS mill even with varying Coal mill, gypsum mill, clay mill, etc Pfeiffer MPS millsWide product range: For meeting various requirements from different clients, our cement mill range from cement ball mill, vertical cement mill, Raymond mill, coal mill in cement plant, etc Strong production ability : AGICO CEMENT has a Cement Mill Cement Ball Mill Vertical Cement Mill
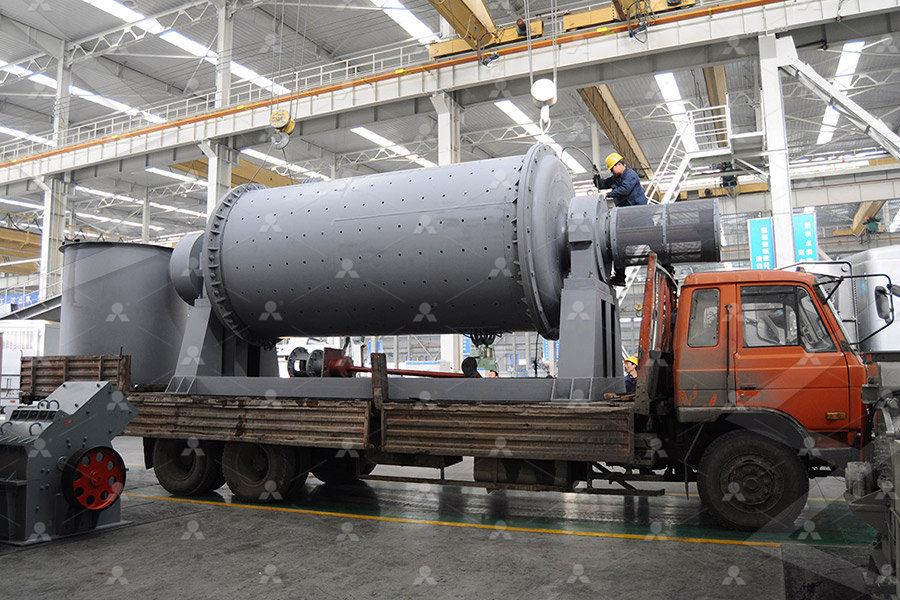
Optimizing Raw Mills Performance ; the Materials
2019年6月22日 Optimizing Raw Mill through Raw Materials Selection and Optimizing Chemical and Physical Properties: In authors experience at one of the plants using vertical raw mill; vertical planetary gear reducer At the same time, raw material is dried by hot gas induced through the louver ring installed at outer side of the table Construction This Machine is a vertical type roller mill which performs drying grinding classification and pneumatic transportation simultaneously Material is fed at aVERTICAL ROLLER MILLS AMCL2016年9月1日 Vertical roller mill (VRM) is a largescale grinding equipment, which is used to grind raw materials from block/granule into powder Due to harsh production environment and inconsistent raw Operational parameters affecting the vertical roller mill Vertical raw mill is important equipment widely used in the cement raw meal (cement raw materials) grinding section of the cement production process in cement plantBecause the vertical raw mill is the use of roller grinding principle to crush materials, its vertical raw mill operation is more efficient and energysaving, product output is more stable, so in cement industry, electric Vertical Raw Mill ball mills supplier
.jpg)
Cement Industry Loesche
The roller grinding mill technology, patented in 1928 and continuously developed since then, has become synonymous with Loesche‘s pioneering engineering knowhow CEMENT BLAST FURNACE SLAG CEMENT RAW MATERIAL2021年7月27日 Raw materials grinding process is a first step of cement production which is has an important role in the first grinding step Vertical Raw Mill is a main equipment that is used in grinding or Evaluasi Kinerja alat Vertical Raw Mill Melalui Perhitungan Neraca Vertical raw mills are widely used in the cement industry due to their high efficiency, low energy consumption, and compact design The Role of Vertical Raw Mills in Cement Production: 1 Grinding Limestone: The primary function of a vertical raw mill is to grind limestone, the main raw material in cement production, into a fine powderThe vertical raw mill: A key component in cement productionVertical Raw Mill: A vertical raw mill is mainly used in cement plants for raw material grinding Simple process flow, providing for drying, grinding and classifying all in one equipment; Minimum floor space requirement, compact layout and low investment in civil works; High grinding efficiency, low energy consumption and low wear on metal partsVertical Roller Mills LNV TECHNOLOGY
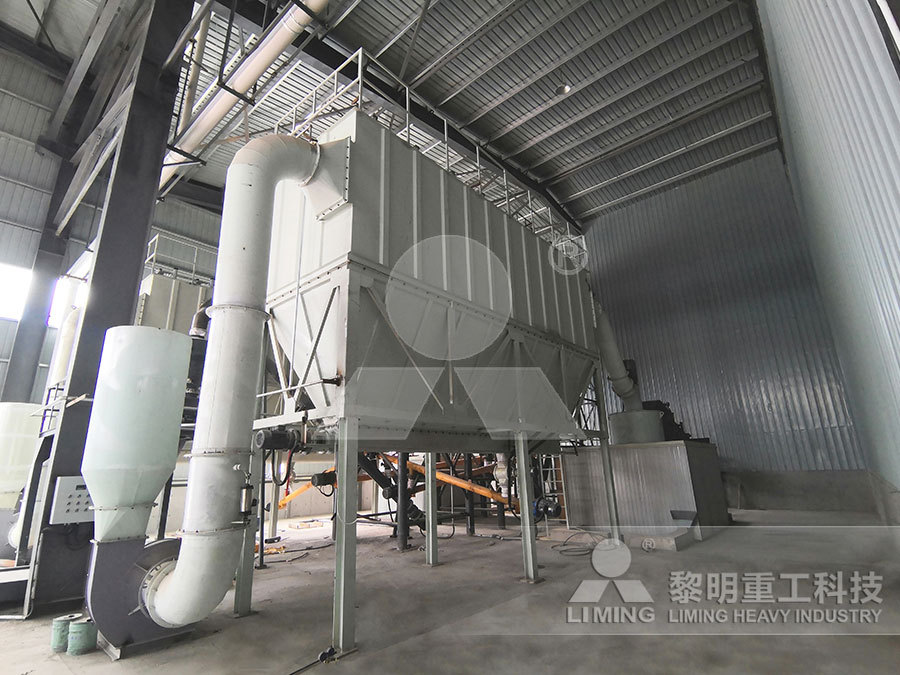
PROCESS OPTIMISATION FOR LOESCHE GRINDING PLANTS
vertical roller grinding mills for grinding: • Coal • Cement raw material • Clinker / granulated slag • Industrial minerals, and • Ores The core elements of these plants are the Loesche vertical a vertical roller mill (VRM) • Surpasses the classic methods if the controlled2017年9月11日 PDF In this study, an extensive sampling study was carried out at vertical roller mill Recent decades have proven the great effectiveness of a vertical roller mill for grinding raw materials(PDF) Performance Evaluation of Vertical Roller Mill 2015年1月1日 Vertical cement mill (vertical mill) is a machine that plays an important role in the raw meal production process of the newtype dry cement, and it is a set breakage, drying, grinding, transport in one []Raw material grinding process is a vital and energy consumption link in the cement productionModeling Based on the Extreme Learning Machine for Raw Cement Mill Part Three: Raw Mill Process of Raw Mill The proportioned raw material is feed first to a grinding mill In the mill, particles ground in to very fine sizes In the grinding unit, drying, grinding and mixing takes place simultaneously Hot gas from clinker burning unit is passed into the grinding unit to assist the drying and grinding processCement Manufacturing Process INFINITY FOR CEMENT EQUIPMENT
.jpg)
Vertical Roller Mill in Cement Manufacturing Plant
2023年7月4日 3 Raw material grinding: The crushed raw materials are ground into a fine powder, called raw meal, using grinding equipment like ball mills or vertical roller mills 4 Pyroprocessing: The raw meal is heated in a rotary kiln at high temperatures (around 1450°C) to form clinker, a semifinished product consisting of small, nodular lumps 5For the preparation of cement raw material, cement, and granulated blastfurnace slag with small to medium output rates, the MVR mill with conventional drive is the right choice This mill type is by the way the core piece of our modular ready2grind systemMVR vertical roller mill with planetary gearbox Gebr PfeifferThe document discusses optimization and operation of vertical roller mills (VRMs) Key points include: 1) Continuously monitor and adjust process parameters to find the optimum operating conditions of highest capacity and lowest power consumption 2) Relevant process parameters to monitor include product rate, fineness, classifier speed, grinding force, power consumption, air Optimization of Vertical Raw Mill Operation PDF2022年1月23日 This work concentrates on the energy consumption and grinding energy efficiency of a laboratory vertical roller mill (VRM) under various operating parameters For design of experiments (DOE), the response surface method (RSM) was employed with the VRM experiments to systematically investigate the influence of operating parameters on the energy Analysis and Optimization of Grinding Performance of Vertical
.jpg)
Everything you need to know about cement Materials Preparation and Raw
The Horomill used as a raw mill is claimed to combine the effectiveness of the vertical roller mill and the roller press with a very low pressure drop in the circuit It is also expected to offer some advantage in handling raw materials containing a higher percentage of quartz in comparison to vertical roller mills (Buzzi, 1997)