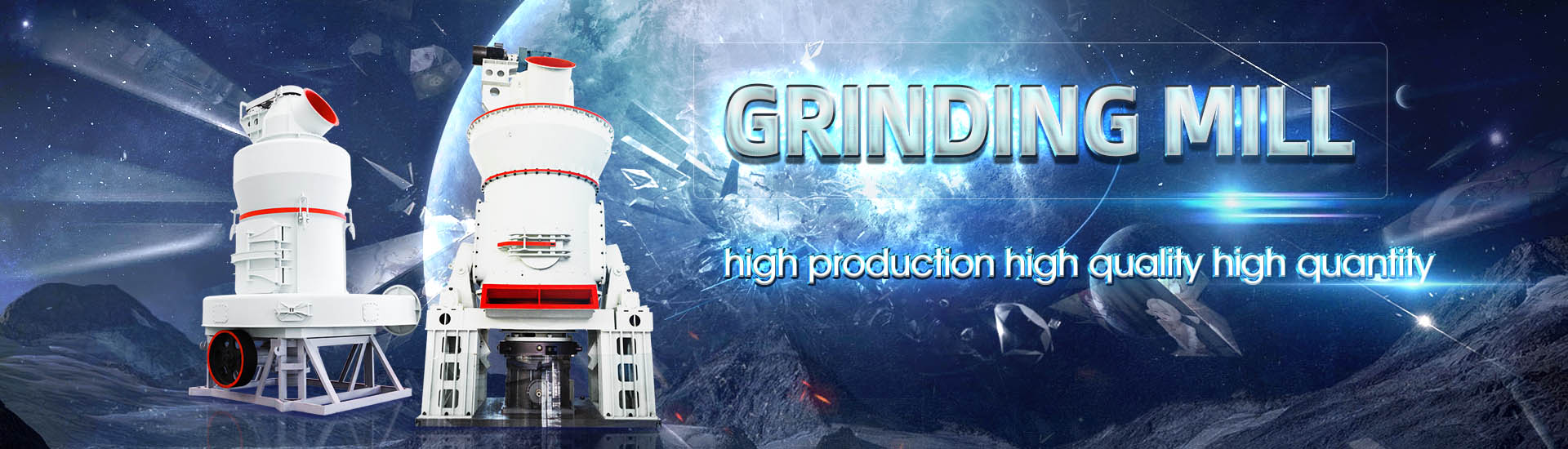
Equipment for producing granite clinker
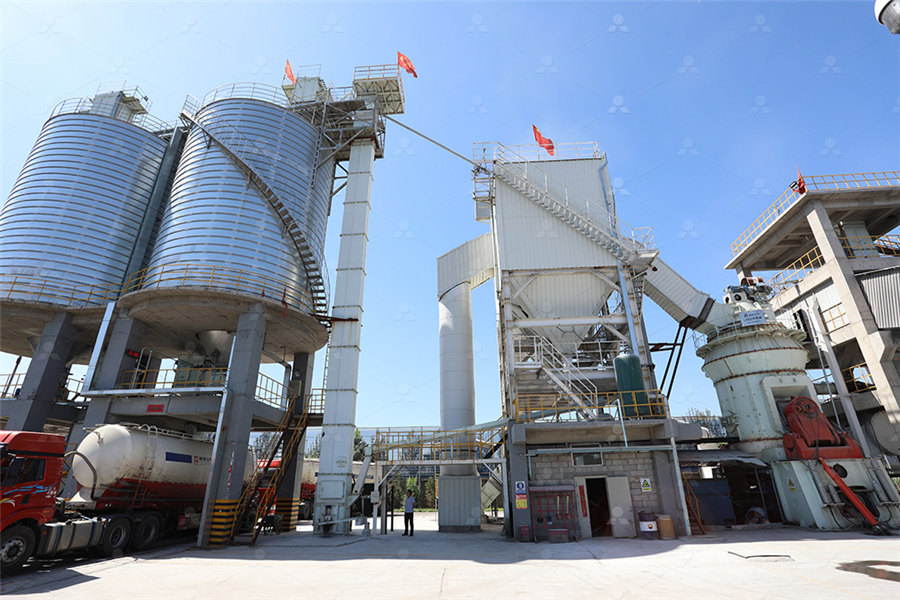
Clinker Production Clinker Manufacturing Cement
Cement kiln is the main equipment for clinker sintering From structure, it can be divided into rotary cement kiln and shaft kiln, while, from the working principle, it can be divided into the dry method and wet method kilnClinker is produced by pyroprocessing in large kilns These kiln systems evaporate the free water in the meal, calcine the carbonate constituents (calcination), and form cement minerals Clinker Production an overview ScienceDirect TopicsAGICO Cement provides cement equipment of clinker production, including rotary kiln, preheater, and precalciner, start cement plant now!Clinker Production Clinker Plant Cement Plant 2023年10月19日 Use of HighEfficiency Equipment: Invest in modern, energyefficient grinding equipment, such as vertical roller mills (VRM), which can significantly reduce energy consumption Waste Heat Recovery: Implement Clinker Grinding Techniques in Cement Manufacturing
.jpg)
Clinkerization Cement Plant Optimization
The process of clinkerization signifies conversion of raw meal into clinker minerals mainly consisting of C4AF (Aluminoferite), C3A (Aluminite), C2S (Belite) and C3S (Alite) phases along with small percentage of free lime CaO, MgO, Alkalies, Design, implementation and modernisation of clinker storage installations, customised as per requirement, achieve maximum customer benefit Adapted to the customer`s specific Clinker Storage Systems AumundIn this part of the project, the indirect mechanosynthesis process was carried out for the laboratory preparation of clinker from a premix (limestone/kaolinite) to obtain clinker production at a temperature of 900 °CCement and Clinker Production by Indirect Taranto’s GBFS, separate slag and clinker grinding is a more efficient process than intergrinding It also proved to be the more flexible and economical method because the mills can be SEPARATE OR INTERGRINDING? Loesche
.jpg)
Important Machines Required for ClinkerProduction Medium
2022年9月5日 The three main clinker production machines are as follows: This one is also known as the suspension preheater and it is one of the most crucial pieces of equipment in the A clinker sample from the cooler discharge will be at least 45 minutes old by the time the analysis is started in the laboratory and laboratory analysis can take 30 – 90 minutes to complete Clinker alkali content Clinker alkali concentration can Everything you need to know about Kiln System The impact of coating layers on the clinker production process within a rotary kiln burning both coal and Refuse Derived Oxygen lance is the key piece of equipment for iron and steel smeltingClinker formation process in a modern plant rotary kiln2023年12月17日 Like ordinary clinker, this type of paving stone is more like a brick, but with increased strength properties This is achieved largely through the use of special grades of clay The very same production of clinker paving stones is focused not on compaction processes by means of vibration and pressing machines, but on firing technologiesPaving stone production: equipment, technology Industry 2024
.jpg)
How Cement is Made Portland Cement Association
While each cement plant may differ in layout, equipment, and appearance, the general process of manufacturing portland cement is the same: crushed limestone and sand are mixed with ground clay, shale, iron ore, fly ash and alternative raw materialsGrate Cooler Grate Cooler 1 Introduction Clinker Cooling is an Important phase in clinker production; Clinker Cooler is exposed to extremely difficult operatingconditions with a highly abrasive and hot material; The Cooling Rate of clinker at elevated temp has direct impact on cement strength(fig1)Grate Cooler INFINITY FOR CEMENT EQUIPMENT2022年9月21日 Cement and Clinker Production by Indirect Mechanosynthesis Process September 2022; Construction Materials 2(4) Compression tests were carried out with 300 kN equipment (Syntech, 3R,Cement and Clinker Production by Indirect Mechanosynthesis Protection of equipment and personnel at all times; Consistently good clinker quality; Smooth and stable operation; Maximum thermal efficiency; Maximum production rate; 1 INTRODUCTION The different kiln systems can be distinguished by the moisture content of the raw material, which is fed to the kiln systemKiln Control and Operation INFINITY FOR CEMENT EQUIPMENT
.jpg)
Granite processing grinding mill machines
2 Jul 2022; Granite grinding machines Granite grinding machines are composed by a number of ancillary equipment, mining equipment, and then blasting process, clinker blasting process through the granite, granite clinker fragments, rock hammer, falling ball, and the lower crusher, gyratory crushermachines and other equipment, crude materials sent by conveyor to the Table 351 shows typical data for production and specific fuel consumption of different kiln systems (Alsop and others, 2001) Figure 351 View of the Ålborg Portland cement plant in Denmark showing the preheater tower and rotary kiln for production of mineralized clinker (Photo courtesy Duncan Herfort, Ålborg Portland) Table 351Everything you need to know about Fluxes and Mineralizers inClinker, made from magnesiarich feed must be very rapidly cooled once it has been burned, to guard against production of unsound clinker Plants faced with this problem usually locate the burning zone very close to the discharge end EVERYTHING YOU NEED TO KNOW ABOUT THE The diagram in Fig 2216 shows material tempera tures and undergrate pressures for a typical combina tion clinker cooler, producing about 1700 mt/24 h of clinker from 1360 Pipe and duct connections, as well as measuring and Clinker cooling INFINITY FOR CEMENT EQUIPMENT
.jpg)
Clinker Grate Cooler for Cement Plant
Processing capacity: 8004000t/d; Applications: Cement, silicate products, new building materials, refractory materials, glass ceramics and other production industries; Applicable materials: limestone, cement clinker, bauxite, activated Previous Post Next Post Contents1 10 secrets of clinker11 First Rule12 Second rule13 Third rule14 Fourth rule15 Fifth rule16 Sixth Rule17 Seventh rule18 Eighth rule19 Ninth rule110 Tenth rule 10 secrets of clinker First Rule Reducing raw mix rejects lowers burning temperature and grinding energy This is particularly the case with siliceous rejects This action 10 secrets of clinker INFINITY FOR CEMENT EQUIPMENT2021年12月28日 Currently, the production of one ton of ordinary Portland cement (OPC) releases considerable amounts of CO2 into the atmosphere As the need and demand for this material grows exponentially, it Alternative Clinker Technologies for Reducing Carbon Emissions 4 Kinetics of Clinker Burning Practical Considerations Assessment of Raw Meal Burnability 5 Thermodynamics of Clinker Formation During clinker production, heat is both absorbed (endothermic heat changes) and produced (exothermic heat changes) TempFormation of Clinker INFINITY FOR CEMENT EQUIPMENT
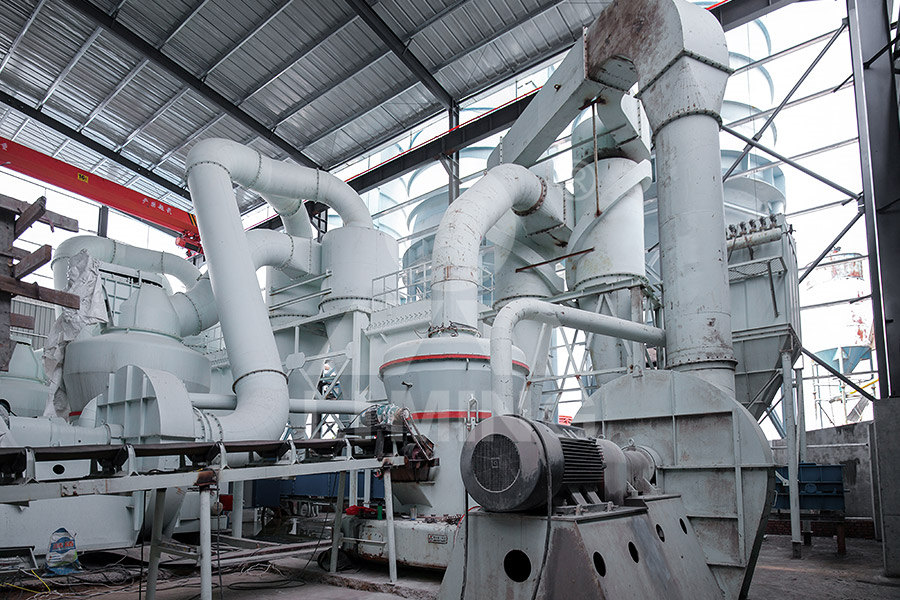
CLINKER COOLING COOLER SYSTEMS INFINITY FOR CEMENT EQUIPMENT
The one shown (Fig 3) is producing 4000 t/d clinker, and the cooler consists of 10 tubes, each 24 x 29 m Only for kilns with less than about 1000 t/d capacity it is economical to leave out the support below The equipment required is very simple: Just a gutter around the coolers, AGICO Cement provides cement equipment of clinker production, including rotary kiln, preheater, and precalciner, start cement plant now! Skip to content +86 s AGICO Cement supplies cement equipment for clinker plant, such as cement rotary kiln, preheater in cement plant, rotary kiln dryer, clinker cooler, etc Clinker Production Clinker Plant Cement Plant EquipmentGlobal cement production has reached 39 billion tons However, the clinkerization process, which is the basis of cement production, is responsible for an approximate annual global CO2 emission of 2 billion tons As part of CEMBUREAU’s 5C strategy, the European cement industry aims to achieve carbon neutrality throughout the cementconcrete value chain by 2050 This article is Cement and Clinker Production by Indirect Mechanosynthesis 2015年1月1日 About 33% of the total energy is wasted from the rotary kiln chimney apart from the heat loss through the wall of rotary kiln in a clinker production process (Ustaoglu et al, 2017)(PDF) Exergetic assessment of a rotary kiln for clinker production
.jpg)
Quantitative Optimization of Cement Rotary Kiln for Heat
designed to consume ≤750Kcal/Kg of clinker but the observed consumption averages between 756 Kcal/Kg 766Kcal/Kg The derived mathematical model provides solution from the objective function which gives heat consumption at 73978 Kcal/Kg of clinker Keywords: Heat Energy, Energy Consumption, Clinker, Kiln, Optimization I INTRODUCTION2020年10月1日 This research focused the role to study the effects and ways to control the chemical composition of clinker for better cement production Cement is a substance produced by grinding a mixture of a clay and limestone and Effects and Control of Chemical Composition of Figure 381 Grate clinker coolers At the discharge end of the kiln, the clinker is red hot and contains around 10 million Btu per short ton thermal energy The clinker is also to some extent still reacting chemically toward creation of Everything you need to know about Clinker CoolersRole in cement production Efficiency benefits Word count: 1000; Cooler Types (grate cooler, planetary cooler, etc) Impact on clinker quality and energy efficiency Word count: 1000; Section 4: Kiln Operation and Optimization Kiln StartUp and ShutDown Procedures Detailed processes and safety measures Word count: 1500; Operational Comprehensive Guide to Cement Kilns: Processes, Types,
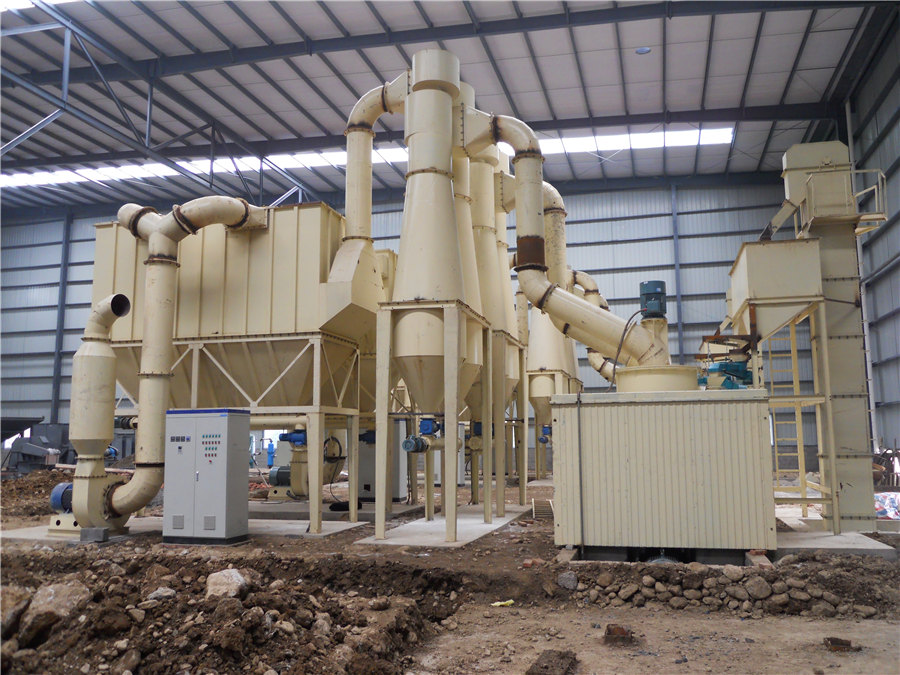
Cement Clinker Manufacturing Process with Reactions
The powdery or granular mixture quickly solidifies into spherical nodules of clinker Cooling and storing The mixture inside the slightly inclined kiln is rapidly cooled from 2000°C to 100°C200°C Thus, the final product, clinker, is produced, and then stored, ready for the production of cement2020年10月15日 This research focused the role to study the effects and ways to control the chemical composition of clinker for better cement production Cement is a substance produced by grinding a mixture of a Effects and Control of Chemical Composition of Clinker for There are many instances where cooler operating problems can lead a perfectly stable kiln into a severely upset condition with possible damage to the equipment With the introduction of largesized rotary kilns having production capacities in excess of 1500 tons per day, traveling grate cooler; have become a problem in some plantsEVERYTHING YOU NEED TO KNOW ABOUT OPERATION AND CONTROL OF CLINKER 2012年11月8日 Finish grinding of clinker and other cement ingredients reduces 25 mm clinker balls to particle sizes optimally ranging from 3 to 30 microns The European Cement Research Academy (ECRA) estimates that up to 70% of the power consumed in cement production is for material size reduction Increasing the efficiency of particle size reduction couldBreakthrough in Clinker Grinding Massachusetts Institute of
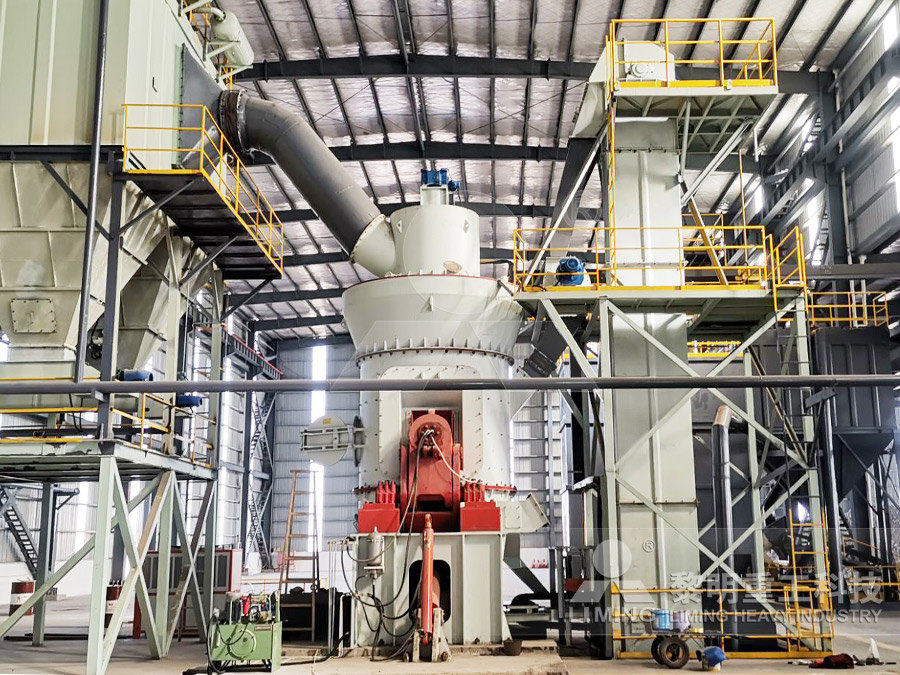
Cement Rotary Kilns Efficient Equipment for Clinker Production
Capacity:100012000t/h Product Specifications:Φ32×50 – Φ62×96 Material: limestone, clay, slag, fly ash Application fields: cement rotary kilns are used for cement production, lime production, metallurgical industry, petrochemical and waste treatment, etcindustry: Calcination and cement clinker burning Calcination of raw material CaCO 3 => CaO + CO 2 Process emissions of raw material: = 054 t CO 2 /t clinker Endotherm reaction at 950 °C ca 1700 MJ/t clinker ≈ 50% of energy Cement clinker burning at 1450 °C formation of hydraulic properties of clinker Thermal energy requirement:Process characteristics of clinker and cement production SINTEF2022年3月1日 Quantification of crystalline phases and the degree of amorphism of the raw materials used in the production of clinker Mineralogical composition GRFA GRFB ISCD CODE Quartz (SiO 2 ) 177 1062 Influence of the Content of Alkalis (Na2O and K2O), 2024年5月13日 In order to increase the utilization rate of stainless steel slag, reduce storage needs, and mitigate environmental impacts, this study replaces a portion of limestone with varying amounts of stainless steel slag in the Experimental Study on Calcination of Portland Cement
.jpg)
Cement Making Process: Equipment Manufacturing
Cement manufacturing equipment needs to withstand the heat and the abrasive material from which cement is made Making cement involves combining raw materials including limestone, clay, and shale, which are milled into a very fine How is clinker shipped? Introduction Cement production is a vital element of the construction industry, and cement clinker is the main constituent of cement Cement clinker is produced by heating a mixture of limestone, clay, and other raw materials in a kiln The resulting product is ground into fine powder, which is then used to produce cementHow is clinker shipped? INFINITY FOR CEMENT EQUIPMENTClinker production is the most energyintensive stage in cement production, accounting for over 90% of total industry energy use Clinker is produced by pyroprocessing in kilns These kiln systems evaporate the free water in the meal in preheater cyclone, calcite the carbonate constituents (calcination) in calciner, and form Portland cement minerals (clinkerization) in Cement Manufacturing Process INFINITY FOR CEMENT EQUIPMENTF = mass dry feed per mass of clinker (tons/ton) or (kg/kg) G = slurry rate (m3/s) g = slurry rate (gpm) M = percent moisture 306 Clinker Production per Slurry Tank Unit Note: This formula applies only to the cylindrical portion of the slurry tankEVERY SINGLE EQUATION IN CEMENT INDUSTRY
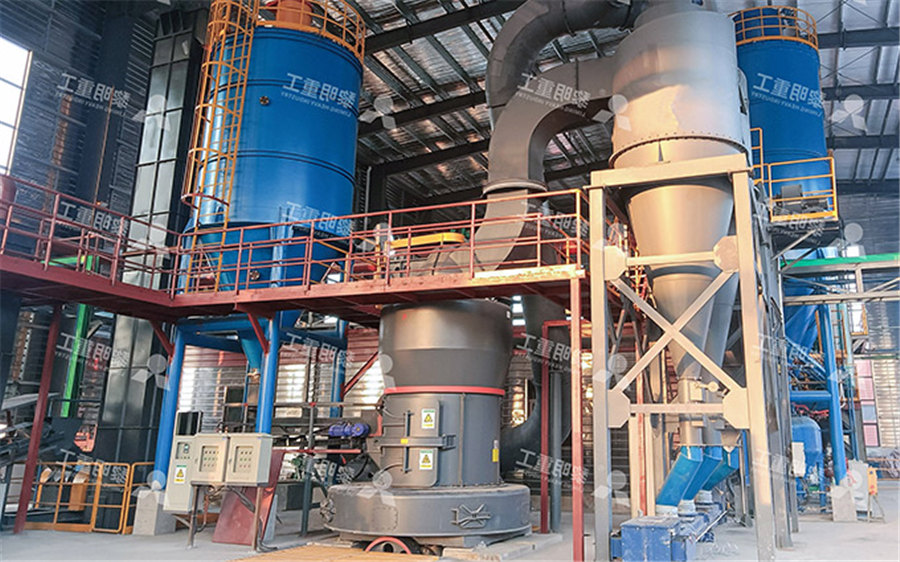
Clinkerization Cement Plant Optimization
Production rate, tpd Run tine factor in % Clinker free lime (CaO f) Moreover, it serves as a safety equipment for all critical equipments in upstream gas circuit like, ESP, Bag house etc Oxygen content of 15 25% is considered good at preheater outletFigure 833 Poorly burned (underburned) clinker in wateretched polished section at 100X, showing strong nonuniformity Belite is found almost totally in nests, many tightly packed and with central voids, indicating coarse quartz and very high porosityEverything you need to know about Microscopical Quality Control Cement production is a complex process consisting of many technological steps Depending on the choice of cement production technology — dry, wet or combined — the selection of equipment for cement production depends Regardless of the type, the technology of cement production will necessarily include such a stage as clinker burningClinker kiln — Equipment for the production of cement2023年10月23日 Cement production requires significant energy, and entails high costs and CO2 emissions This is because the clinker requires very fine grindingA study of different grinding aids for lowenergy cement clinker production