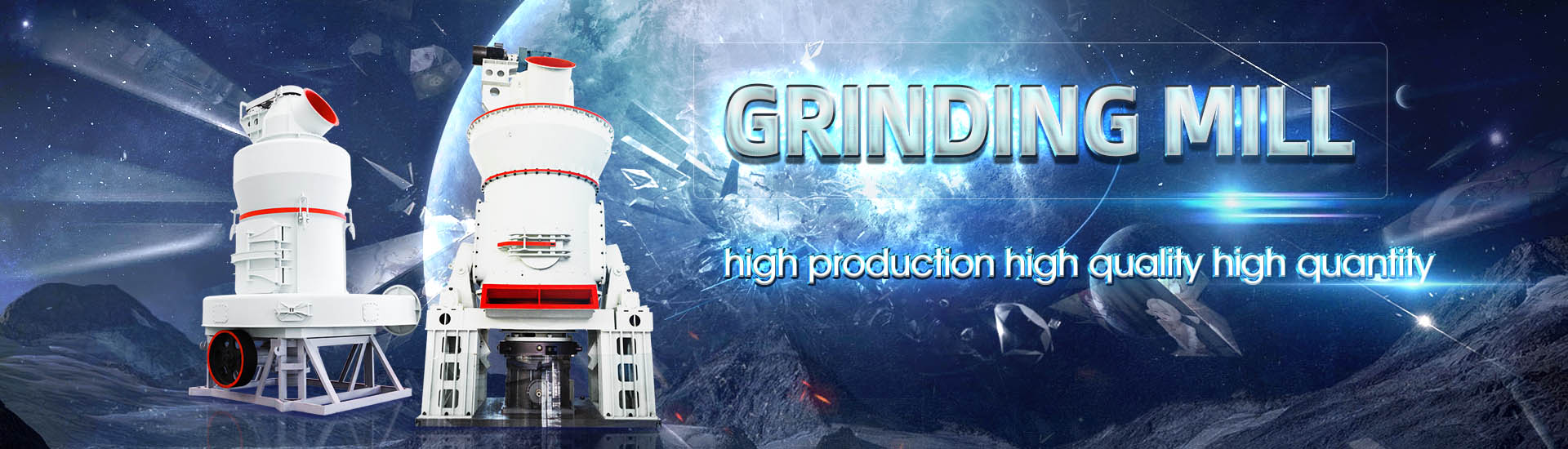
Alumina ash, overhaul slag, aluminum electrolyte grinding system, welding rod powder
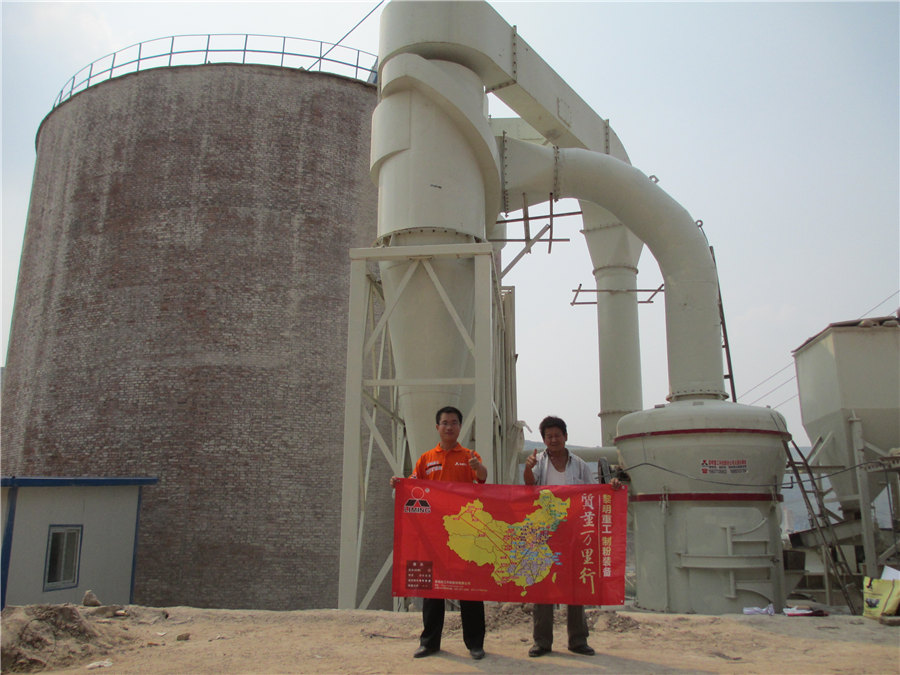
Efficient lithium recovery from electrolytic aluminum slag via an
2024年2月1日 The electrolytic aluminum industry generates a large amount lithium (Li)containing electrolytic aluminum slag (EAS) annually, and this can result in severe 2023年4月25日 This article analyzes and summarizes the composition and hazards of the overhaul slag and the current development status of domestic and international electrolytic Research Progress of Electrolytic Aluminum Overhaul Slag Disposal2023年5月20日 Effect of reaction conditions on the firststage aluminum salt leaching process was investigated in detail Under the optimal leaching conditions, the leaching rates of F, Na, Regeneration of raw materials for aluminum electrolysis from 2024年7月24日 The lithium was selectively recovered and enriched from spent aluminum electrolyte slag by using calcium salt roasting transformation followed by HBL121solvent Cleaner Process for the Selective Extraction of Lithium from Spent
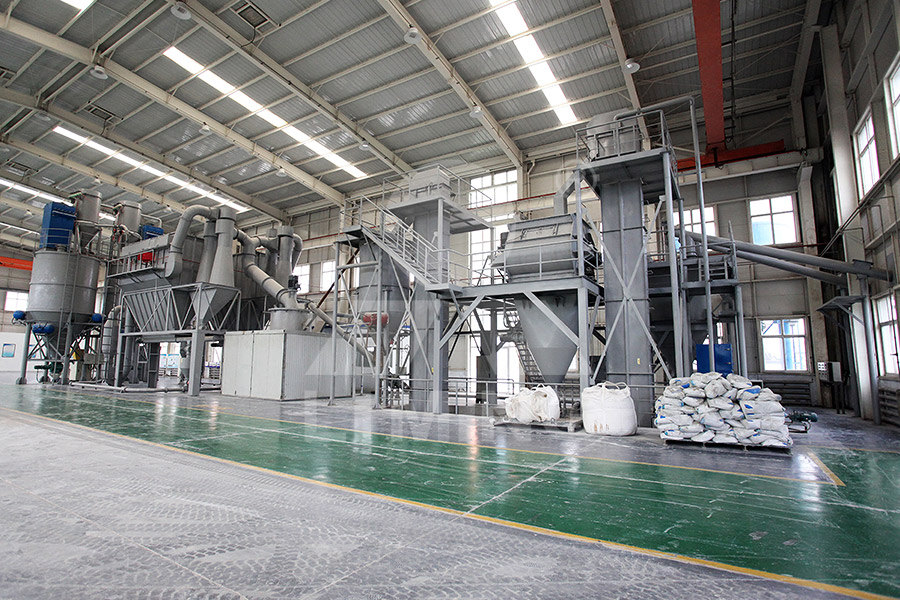
Recycling and Utilization of the Electrolytic Aluminium Ash and Slag
Aluminium ash and slag are produced from molten slag cooling in the electrolytic aluminium production process,the recycling and utilization of the electrolytic aluminium ash and slag is 2019年2月1日 Aluminum ash is an industrial waste residue produced during alumina electrolysis and aluminum processing and casting In the experiment, alumina powder with a purity of Preparation of Alumina from Aluminum Ash by Sintering with 2023年8月1日 Synthesis and characterization of MgF 2 –CoF 2 binary fluorides Influence of the treatment atmosphere and temperature on the structure and surface propertiesDissolution behavior of overhaul slag from aluminum reduction 2020年1月2日 TL;DR: In this paper, a harmless treatment method of aluminum electrolysis overhaul slag is proposed, where materials are weighted according to a weight ratio, and the Fluorineretaining agent for overhaul slag of aluminum electrolytic
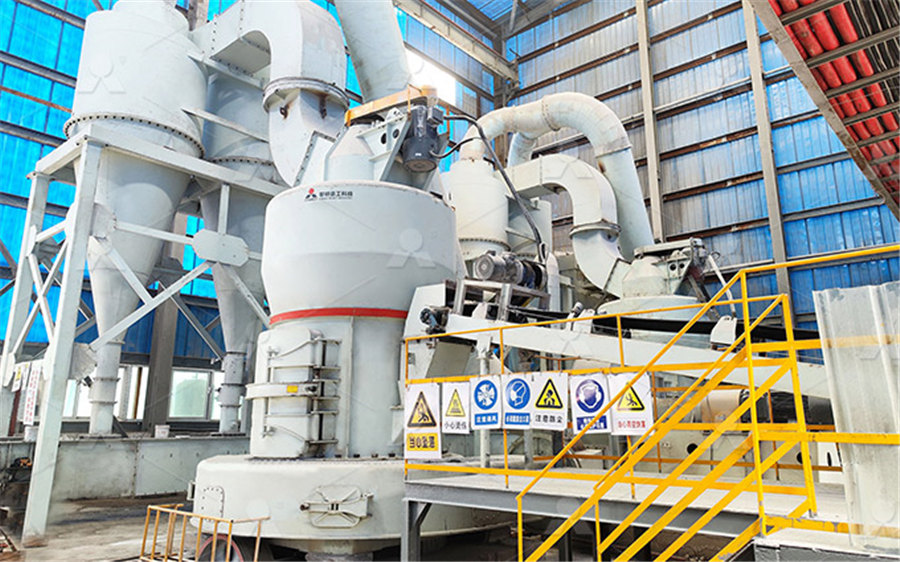
Progress in Aluminum Electrolysis Control and Future Direction for
2016年10月24日 In this paper, the development of aluminum electrolysis control systems is reviewed, followed by a discussion of the progress made since 2000, which mainly consists of 2022年10月9日 Where, γ c refers to the yield of flotation concentrate (%); A c (%) and A f (%) are the ash content of flotation concentrate and feed material, respectively 3 Results and discussion 31 Characterization of raw carbon Recovery of carbon and cryolite from spent carbon 2022年1月10日 Selective comminution and grinding mechanisms of spent carbon anode from aluminum electrolysis using ball and rod mills January 2022 Physicochemical Problems of Mineral Processing 58(3):Selective comminution and grinding mechanisms of 2022年12月12日 Based on the research on bulk solid waste contact molding technology by our team [49], the comprehensive performance of pressed bricks with different ratios of aluminum ash and calcium carbide slag was investigated, the ratios of aluminum ash and calcium carbide slag are 9:1 ∼ 1:9 and pure aluminum ash and calcium carbide slag, the pressing pressure is 300 Comprehensive performance study of aluminum ash and calcium
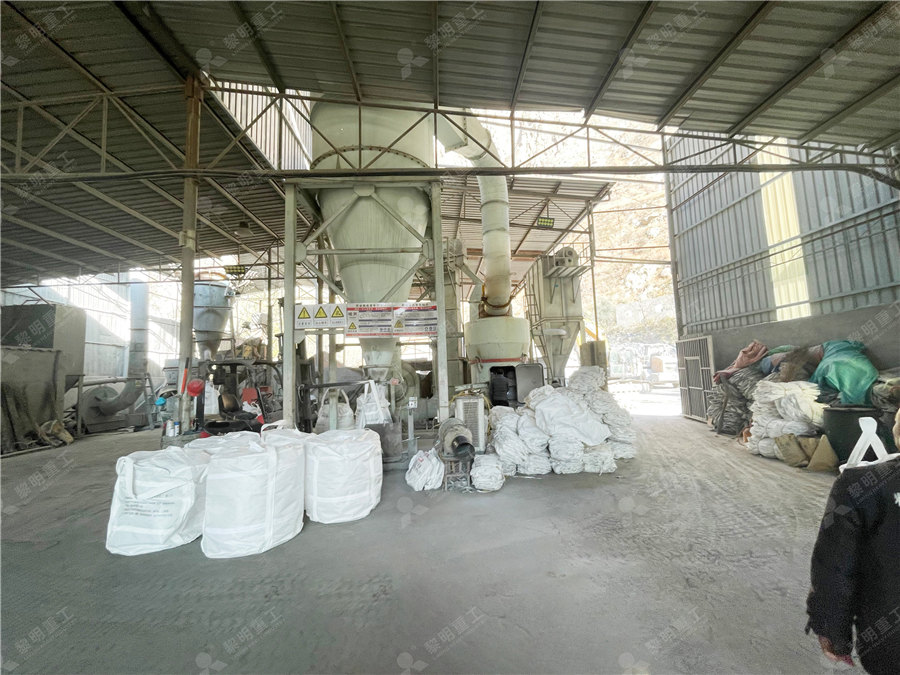
Aluminum extraction technologies from high aluminum fly ash De Gruyter
Coal fly ash (CFA), an industrial byproduct of hightemperature combustion of coal in coalfired power plants, is one of the most complex and largest amounts of industrial solid wastes generated in China It is widely recognized that CFA should be considered as a potential alumina resource to substitute bauxite In this review, the features of highalumina fly ash and aluminum recovery 2019年8月1日 Highalumina fly ash microbeads and steel slag were used as main raw materials to synthesize feldspar porous ceramics via hightemperature solid phase sintering by adding pulverized coal as a pore Preparation of anorthitebased porous ceramics using highalumina 2022年1月3日 Ferrotitanium slag was used as a sintering aid to prepare highperformance alumina (Al2O3) ceramics by pressureless sintering at different temperatures The bulk density, apparent porosity, bending strength, and hardness of the 99 wt% Al2O3 ceramics after sintering at 1420 °C were 391 g/cm3, 016%, 38937 (± 761) MPa, and 1564 (± 016) GPa On the Fundamental Research on the Densification of Alumina 2022年10月10日 One of the main electrolytic aluminum production costs is the consumption of carbon anodes, and carbon anode slag is a common hazardous waste in the aluminum industryRecovery of carbon and cryolite from spent carbon anode slag of
.jpg)
What Is Slag in Welding? Understanding the Basics
2023年6月23日 At this point, we’ve covered everything a beginner needs to know about slag formation during welding We hope that this article answers all the questions you had floating around your head about what slag is, why it’s useful in welding, and how you should go about slag removal from your weld area2007年6月7日 Modern smelter potlines often undergo process excursions, which are attributed to “solubility problems” of the alumina used Assigning the problem to a specific property is, however, a challenge, compounded by the fact that the alumina has usually undergone secondary treatments through a dry scrubbing system prior to arrival at the cell With a better Crust and alumina powder dissolution in aluminum smelting electrolytes 2007年5月1日 However, the percentage of the cumulative dissolved alumina mass does not show a gradual increasing trend In general, the alumina dissolution curves of the simulation results are consistent with (PDF) Crust and Alumina Powder Dissolution in Aluminum Smelting 2024年6月29日 In the aluminum electrolyte system, excessive lithium content will decrease the initial crystallization temperature of electrolytes and worsen the dissolution performance of alumina (Heng 2019; Xu 2017; Zhang et al 2011); in addition, potassium can penetrate the inside of the carbon cathode of the electrolytic tank, resulting in serious damage to carbon block Stepwise extraction of lithium and potassium and recovery of
.jpg)
Efficient extraction and recovery of lithium from waste aluminum
2023年10月1日 Cryolitealumina (Na 3 AlF 6Al 2 O 3) molten salt electrolysis is the only modern method for the industrial production of metallic aluminum (Ishak et al, 2017)Under the influence of direct current, Al 2 O 3 dissolved in the molten salt is reduced to monolithic aluminum at the cathode (Haraldsson and Johansson, 2020)As the blood of the electrolytic cell, the electrolyte Pyrometallurgical options for recycling spent lithiumion batteries: A comprehensive review Brian Makuza, Dawei Yu, in Journal of Power Sources, 2021 3221 Smelting slag system design Slag system design is vital for a successful smelting operation [34]The most commonly used slag system is CaO–SiO 2 –Al 2 O 3, in which SiO 2, along with CaO, is chosen as a slag former, Slag System an overview ScienceDirect Topics2023年3月12日 Aluminum has a variety of uses in the building, transportation, electric power, packaging, national security, and hightech industries due to its unique chemical and physical properties []Cryolitealumina molten salt electrolysis is mainly applied in modern industrial aluminum production [2,3]As the aluminum production process continues, a large amount of Recovery of Carbon and Cryolite from Spent Carbon Anode Slag2024年1月1日 Semantic Scholar extracted view of "Efficient lithium recovery from electrolytic aluminum slag via an environmentally friendly process: Leaching behavior and Green and efficient separation of fluorine from spent aluminum electrolyte by aluminum sulfate solution: Leaching behavior and mechanism Lingqi Meng Tianxiang Hao +5 Efficient lithium recovery from electrolytic aluminum slag via an
.jpg)
A Review of Secondary Aluminum Production and Its Byproducts
2021年7月30日 Sintering Aluminum dross and coal fly ash were used to prepare mullitebased ceramics through sintering and acid leaching methods At a sintering temperature of 1500 C, high mullite2019年6月25日 As a type of industrial solid waste with huge emission and heap stock, highaluminum pulverized coal ash has a significant negative impact on resources and the environment At the same time, as a secondary resource, its aluminum content can reach 50%, which is close to that of mediumgrade bauxite; thus, it can be used as a substitute for bauxite Extraction of alumina from highalumina coal ash using an 2023年4月1日 Comparing with other materials, the aluminum industry is energy intensive with a notable difference between primary and secondary production (174–186 MJ/kg and 10–20 MJ/kg, respectively) (Abdulkadir et al, 2015)The reason by which secondary aluminum production consumes much less energy is because its raw material is aluminum scrap and primary Synthesis strategies of alumina from aluminum saline slags2018年10月1日 After the delivery of alumina to the aluminum industry, alumina is reduced to aluminum metal through an electrolytic process (Gil, 2005) In 2010, a total of about 56 million tons of aluminum metal was globally produced (approximately 18 million tons of scraps were recycled), compared to about 28 million tons in 1990 (more than 8 million tons of scraps were Hazardous aluminum dross characterization and recycling
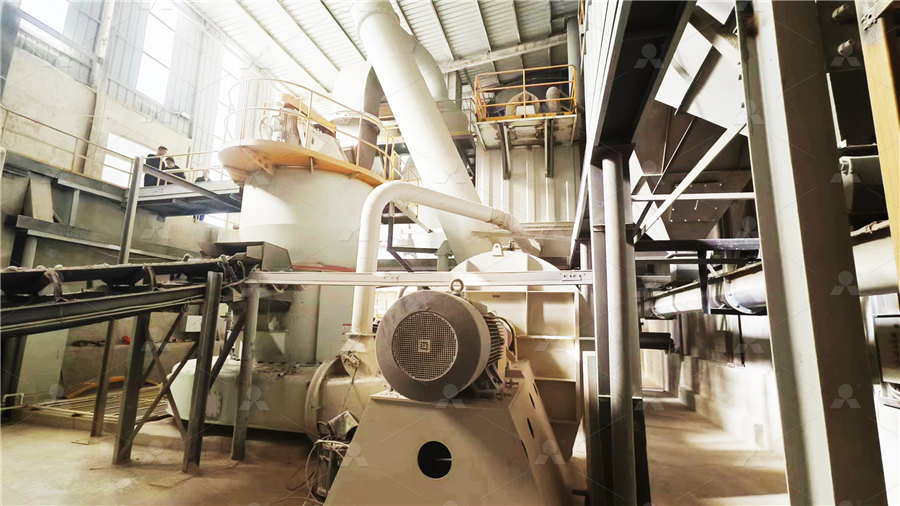
Multifunctional crust breaker for automatic alumina feeding system
2021年6月4日 The objective of this research is to evaluate the metallographic properties to obtain cast iron with nodular spherical graphite ISO 40012 by “In mold” modification using the vibratory methodThe main components in the aluminum slag are metallic aluminum, alumina, aluminum nitride, fluoride salts, chloride salts, as well as the elements such as iron, silicon, magnesium, and calcium The secondary aluminum dross is generated by separation of metallic aluminum from aluminum slag and is toxic and harmful, which pollutes the environmentTechnical Report International Aluminium2024年7月24日 Spent aluminum electrolyte slag is a byproduct produced during the electrolysis of aluminum and contains elements such as F, Al, Na, and Li It is a toxic and harmful substance with a stable and complex structure As a Cleaner Process for the Selective Extraction of Lithium DOI: 101016/jegyr202304036 Corpus ID: ; Dissolution behavior of overhaul slag from aluminum reduction cell in a cryolitebased molten salt system @article{Yang2023DissolutionBO, title={Dissolution behavior of overhaul slag from aluminum reduction cell in a cryolitebased molten salt system}, author={Jianping Yang and X Lu and Dissolution behavior of overhaul slag from aluminum reduction
.jpg)
Clean Process for Selective Recovery of Lithium Carbonate from
2023年9月1日 Lithium (Li)bearing aluminum electrolyte slag is an inevitable byproduct of the aluminum industry, and improper disposal or stacking it may lead to potential environmental hazards This study employed hydrometallurgical processes to selectively leach lithium from Licontaining aluminum electrolyte slag, using sodium carbonate solution as the leaching agent 2015年1月1日 The cogasification of biomass together with fossil fuels, like coal, intends to reduce the related CO 2 emissions, because of a CO 2 neutral life cycle of biomass [1]Due to their extensive gas purification, gasification based processes have shown additional environmental advantages compared to combustion ones, ie nearly no emissions of sulfur Ash melting behavior and slag infiltration into alumina refractory 2022年1月26日 The density and surface tension of the proposed molten salt system of different components Na3AlF6AlF3CaF2BAD were measured by Archimedes and separation methods at 940–980°C The dissolution rate of black aluminum dross (BAD) and aluminum oxide in the electrolyte after denitrification was compared The aluminum alloy was prepared from BAD raw Basic Physical Properties of Aluminum Alloys and Their Electrolyte 2020年5月4日 A model of flotation was developed and applied to alumina in the aluminum electrolysis cell The conditions of flotation for alumina on the cryolitic bath surface were determined for disc and sphere geometries The contact angle between alumina and cryolitic bath, which had not been found in the literature, was measured and it was found to be around 30 Flotation of Alumina on the Surface of the Electrolyte in an Aluminum
.jpg)
New opportunities for aluminum electrolysis with metal
2004年1月1日 A new electrolyte based on the KFAlF 3Al 2O 3 system was investigated for lowtemperature aluminum electrolysis Analysis indicated that the solubility of alumina was about 45 wt% at 700°C2023年5月22日 The dissolution performance of black aluminum dross (BAD) in cryolite electrolyte is key to its recovery by molten salt electrolysis The stable operation of the electrolyzer depends mainly on the rapid dissolution of BAD in Na3AlF6AlF3Al2O3 electrolyte system In this paper, the dissolution performance and behavior of BAD and its main components in the Dissolution characteristics of black aluminum dross in NaAluminium ash and slag are produced from molten slag cooling in the electrolytic aluminium production process,the recycling and utilization of the electrolytic aluminium ash and slag is attracting more and more attention at home and abroad for their valuable components such as 10%30% aluminium and 30% Al2O3The recovery utilization and technology of advantages Recycling and Utilization of the Electrolytic Aluminium Ash and Slag2023年12月1日 RECENT DEVELOPMENTS ON METALS AND ENERGY EXTRACTION FROM WASTE STREAMS Comprehensive Extraction of Silica and Alumina from Coal Fly Ash via Reduced and Oxidized RoastingLow (PDF) RECENT DEVELOPMENTS ON METALS AND
.jpg)
(PDF) Study on Harmless and Resources Recovery
2012年12月31日 3, 4 SCC contains many valuable inorganic compounds, such as alumina, cryolite, uoride, and aluminum silicate, and some carbon blocks also contain small amounts of cyanide 5,6 According to 2023年11月9日 The process of extracting aluminum with sulfuric acid from highalumina fly ash activated by roasting with Na2CO3 and NaOH as raw materials ware studied The results revealed that the aluminum in fly ash activated by sodium carbonate reached 932% under the optimum conditions (30% H2SO4, 90°C, 120 min, and liquidtosolid ratio was 5:1) Kinetics of aluminum extraction from roasting activated fly ash by 2019年11月28日 The obtained alumina is suitable for aluminum production according to the studied characteristics XRD patterns of alumina obtained at 800 °C, 900 °C, 1000 °C MicroXRD spectral analysis Obtaining Alumina from Kaolin Clay via Aluminum Chloride2015年5月1日 The Reynolds numbers for alumina sedimentation were in the range of (788 × 107)(756 × 103) that indicated the Stockesian regime The values were significantly lower than those calculated in Ref [39] for both agglomerated and nonagglomerated alumina particles settling, which were in the range of 34–25458 for the size range from 40 μm (non Analysis and modeling of alumina dissolution based on heat and
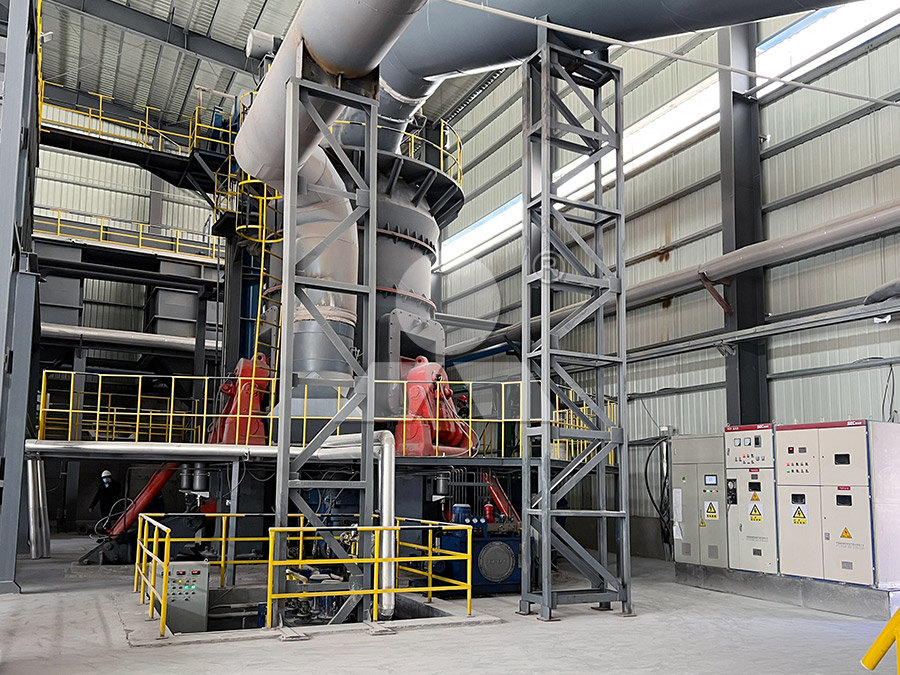
Enhancing Alumina Production Efficiency with Wet Grinding and
Here’s the deal: When we talk about alumina finishing, we mean making the alumina powder fine enough so it works better, whether that’s in making aluminum or as an ingredient in other products Dispersion technology steps in by breaking down the particles in the alumina slurry— that’s a mix of alumina and water— to the nano level2024年2月1日 Overhaul slag, as one of the main hazardous solid wastes generated in the electrolytic aluminum, has high research value [12]The electrolytic cell lining is eroded by continuous chemical corrosion of hightemperature molten metal and salt, resulting in expansion and peeling off, leading to low production efficiency and degradation of performance [13]A novel approach for extracting lithium from overhaul slag by low 2023年1月30日 The present article is focused on extraction alumina from high alumina fly ash using an improved hydrochemical method with highefficiency alkali circulation and mild reaction conditions The alumina leaching behavior and corresponding reaction mechanism of the process were systematically investigated The results revealed that the alumina extraction efficiency A HighEfficiency Alkali Circulation Process for Alumina Extraction 2024年4月17日 Recycling plays an important role in today's world due to its considerable contributions to mitigating energy concerns and environmental challenges One of them is dross recycling from aluminum (Al) cast houses Unlike other recyclable materials, dross has an abundance of components, including rare earth elements, heavy metals, ferrous, and recycled Aluminum dross: aluminum metal recovery and emerging
.jpg)
Recovery of carbon and cryolite from spent carbon anode slag of
carbon anode slag, grinding flotation, carbon, cryolite, selectivity index 1 Introduction Cryolitealumina molten salt electrolysis has been the most commonly used process for