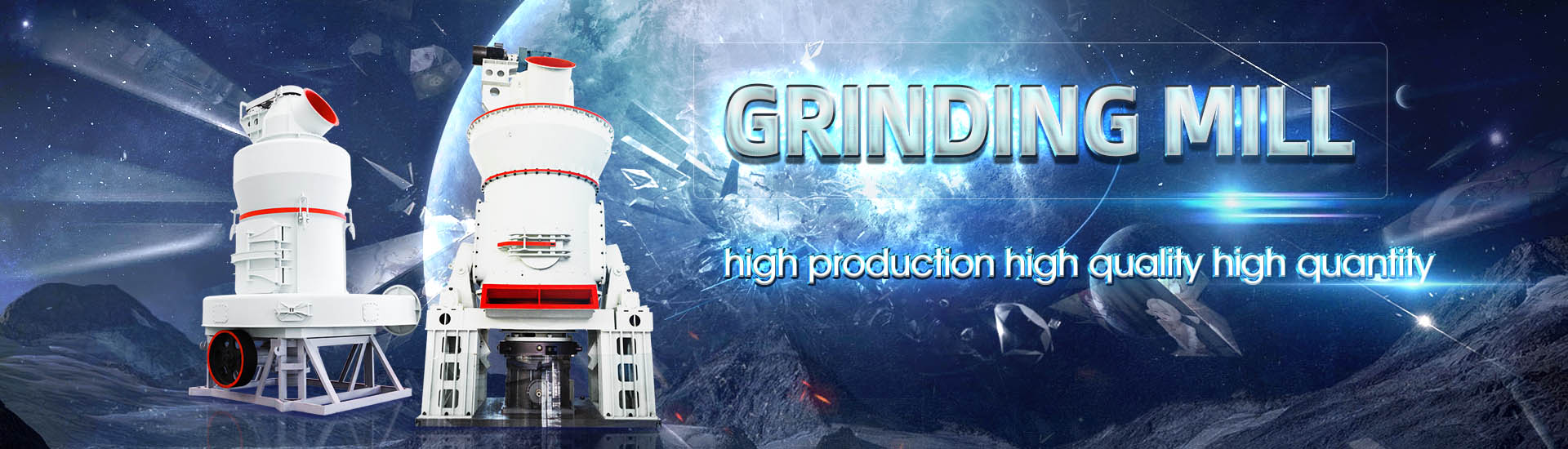
Cement plant raw material workshop
.jpg)
Cement plant operations workshops – Pertecnica Engineering
The Cement Plant Operations Workshops are designed to provide handson training and practical insights into the various aspects of cement plant operations These workshops cover the entire Cement Manufacturing and Production Training: Training programs cover the entire cement production process, from raw material extraction and grinding to clinker production and cement Cement Industry Courses, Cement production training, Cement Generally, cement plants are located on limestone deposits and shale or clay is sufficiently abundant for most plants to mine this locally Additives are usually brought in small quantities Raw materials for cement manufacturing Cement Plant The Cement Plant Operations Handbook is a concise, practical guide to cement manufacturing and is the standard reference used by plant operations personnel worldwide Providing a The Cement Plant Operations Handbook International Cement
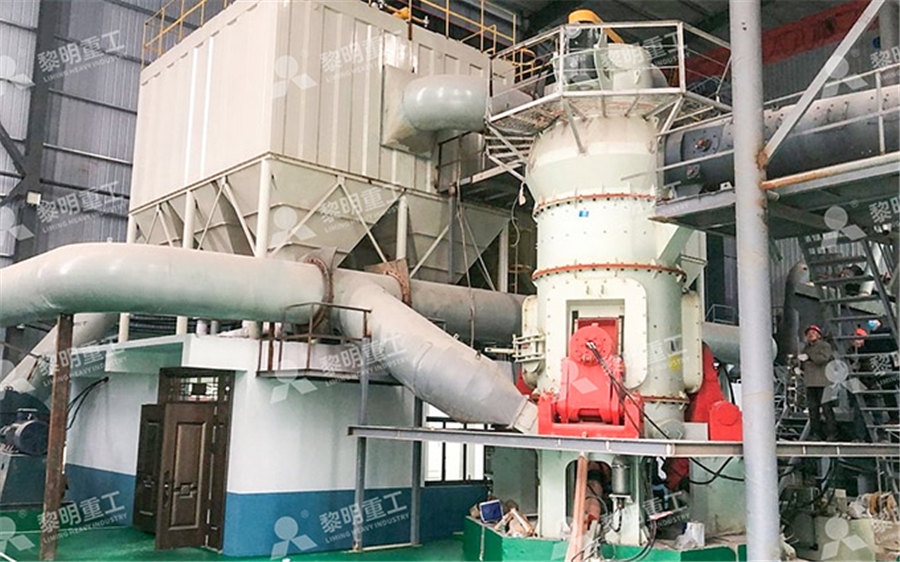
TRAINING FOR CEMENT PLANT OPERATIONS STAFF
workshop will aim to explain how that can be achieved Outline course programme Monday, 17 June Raw materials and their conversion into cement clinker, fuels and combustion n The In this threeday technical training workshop the progressive levels of cement manufacturing process optimisation will be explored, beginning with the raw materials and their preparation, TECHNICAL WORKSHOP International Cement Reviewtraining provided with respect to the use of alternative fuels and alternative raw materials within the Indian cement sector It covers the various aspects of coprocessing, includingALTERNATIVE FUELS AND ALTERNATIVE RAW MATERIALS UNIDOThe European Cement Research Academy (ECRA) conducts and supports research activities on the production of cement and its application in concrete and provides a comprehensive range of seminars and workshops covering the ECRA – European Cement Research Academy
.jpg)
CEMENT GRINDING COURSE The Cement Institute
Gas flow, advantage and disadvantage in the Raw mill and Cement mill installations – Grindability concept and the effects of intergrinding materials of different grindability – Ball mill grinding equations and dimensioning – raw materials are unavoidable at the start of the manufacturing process However, if undetected or left uncorrected, stable kiln operation becomes difficult That is why ABB has developed Raw Mix Preparation ABBStage of Cement Manufacture There are six main stages of the cement manufacturing process Stage 1: Raw Material Extraction/Quarry The raw cement ingredients needed for cement production are limestone (calcium), sand and clay (silicon, aluminum, iron), shale, fly ash, mill scale, and bauxite The ore rocks are quarried and crushed into smaller pieces of about 6 inchesHow Cement is Made Cement Manufacturing ProcessBall mill is a cylinder rotating at about 7080% of critical speed on two trunnions in white metal bearings or slide shoe bearings for large capacity mills Closed circuit ball mill with two compartments for coarse and fine grinding and a drying compartment with lifters are generally found in cement plants for raw material grindingRaw Material DryingGrinding Cement Plant Optimization
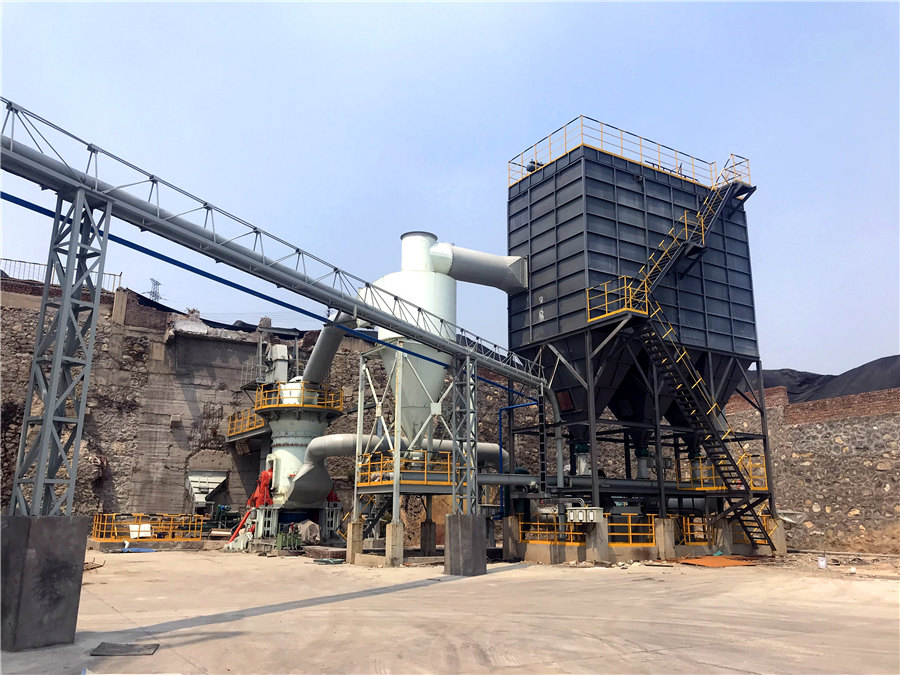
Alternative fuels and raw materials INFINITY FOR
Some of the cement plants have also set up integrated preprocessing plants in order to adopt the AFR strategy more effectively The interface of the waste management and recycling industry with cement plants along with the facilities workshop will aim to explain how that can be achieved Outline course programme Monday, 17 June Raw materials and their conversion into cement clinker, fuels and combustion n The fundamental objectives of clinker and cement manufacture n Best available technology n Raw materials for cement manufacture n Raw mix designTRAINING FOR CEMENT PLANT OPERATIONS STAFF International Cement Raw materials Home About this site About cement About clinker List of plants Map of plants About Kilns Other technical advances Trends in innovation Sources Historical Texts Reference Essays Contact Site Map Descriptions of material types: Chalk: general Chalk: Thames Estuary Chalk: the Medway Swale Chalk: Cam Valley Middle Jurassic Cement Plants: Raw MaterialsAs a cement plant manufacturer, it has a workshop of 30,000 square meters, 230 employees, and 42 professional and technical personnel with middle and senior titles Raw Material Production Cement crusher Jaw crusher; Cone Crusher; Hammer Crusher; Impact Crusher; Gyratory crusher; Mobile Crusher;Cement Plant Manufacturer Cement Equipment Manufacturers
.jpg)
Raw material handling and storage Indian Cement Review
2014年12月31日 Raw materials used in cement plants have a great influence on the investment for a cement plant as the design and selection of the handling equipment is based on their physical and chemical properties Effluent Treatment Plant (ETP) installed for mine’s workshop Treated water is reused in washing activityCement is typically made from limestone and clay or shale These raw materials are extracted from the quarry crushed to a very fine powder and then blended in the correct proportions This blended raw material is called the 'raw feed' or 'kiln feed' and is heated in a rotary kiln where it reaches a temperature of about 1400 C to 1500 CCement manufacturing components of a cement plant Understanding Cement2024年5月23日 Examples of Bucket Elevator Usage in Cement Plants Raw Material Transport: Bucket elevators are used to transport raw materials such as limestone and clay from groundlevel storage to higher processing areas, ensuring a continuous supply to the crushers and millsOptimizing Material Flow with Belt Conveyor in Cement PlantVertical raw material grinding has been widely used in dry process cement plants The raw material preparation system of the 2 500 t/d cement production line can adopt the vertical mill with the disc diameter of 3 400 mm as the main grinding Raw Material Preparation in Cement Manufacturing

Raw material stacking and reclaiming Indian
2016年11月30日 Stacking raw materials/fuels and reclaiming them is an essential part of cement industry Stacking of raw material is done in order to have sufficient raw material to feed the plant during any unforeseen Effluent The cement making machine frequently used in cement plants includes cement rotary kiln, shaft kiln, cement vertical mill, cement ball mill, such as the selection of raw materials, the use of production It occupies little space in Cement Manufacturing Machine Cement Making Production scheme of a cement plant (typical) Raw Mill Fan ID Fan Kiln Exhaust Fan Clinker Cooler Fan Raw Material Clinker Cooler Rotary Kiln with 4 Stage Heat Exchanger Ball Mill with Triager and Cyclone Separator Gypsum, Other Materials Clinker Silo Cement Silo and Dispatch Raw Mill Silos Fuel Silo Storage and Homogenisation Storage and Fans in Cement Plants BrownleeMorrow CompanyThe most important raw materials for making cement are limestone, clay and marl These are extracted from quarries by blasting or by The crushed material is transported into the raw material storage of the cement plant by conveyorbelts, cableways or railways and also in exceptional cases with trucksFrom raw materials to cement
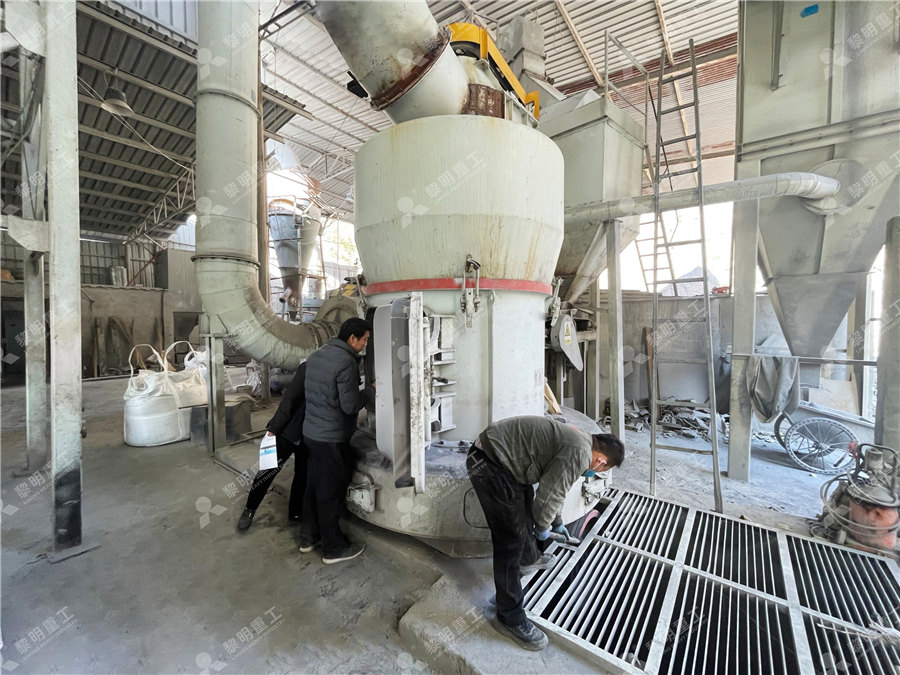
Cement Conveyor Belt Conveyor In Cement Plant AGICO
Cement conveyor refers to a belt conveyor in cement plant, which is necessary accessory equipment in the cement production line A belt conveyor is a kind of material handling equipment with strong adaptability, applied for conveying bulk density less than 167t / m³, it is mostly used for powder, granular, small lump materials, and bagged materials, such as sand, ore, coal, Alternative fuels – a first step to sustainability Embarking on an alternative fuels project is a great step towards reducing your environmental impact and your fuel costs – but it can also introduce new risks to your process You need an experienced partner to help you select the best solution for your facility We offer full flowsheet solutions and guaranteed resultsAlternative fuels FLSmidth CementThe principal raw materials for cement manufacturing are: Limestone; Silica and alumina from basalt , shale or sand; Iron from iron ore or steel mill scale Sand stone; Pumice (volcanic ash for Portland Pozzolana cement ) Gypsum General Properties of Raw Material Sources Limestone; The basic raw material of the cement production is limestoneCement Manufacturing Process INFINITY FOR CEMENT EQUIPMENTLearn about the raw mill in cement plants and the basic raw materials used in cement manufacturing Discover our efficient cement manufacturing process Contact us for more info! Amrit Support About Amrit Support; Services; Activities; Corporate Raw Mill in Cement Plant Cement Manufacturing Raw Materials
.jpg)
ALTERNATIVE FUELS AND ALTERNATIVE RAW MATERIALS
Objectives of the workshop 12 af/arm coprocessing 15 21 52 bringing solutions to waste producers in cement plants 37 53 Define procedure for sampling and analysis 38 training provided with respect to the use of alternative fuels and alternative raw materials within the Indian cement sector It covers the various aspects of co The whole process of cement manufacturing in Messebo Cement plant which consists of two separate Cement Production lines can be summarized into the following processes ;as can be seen in the process and Quality flow diagram below; 1 Quarrying and Crushing 2 Raw material Storage and Transportation 3 Proportioning 4 Raw material Grinding and CEMENT PRODUCTION AND QUALITY CONTROL2022年10月3日 The halfday workshop aims at sharing international experiences in coprocessing of wastes in the cement industry, informing the industry of the results of the recent demonstration using nonrecyclable plastic WORKSHOP: “Coprocessing of alternative fuels and 1 Mixing of raw material The major raw materials used in the manufacture of cement are Calcium, Silicon, Iron and Aluminum These minerals are used in different form as per the availability of the minerals Table shows the raw Manufacture of Cement Materials and Manufacturing
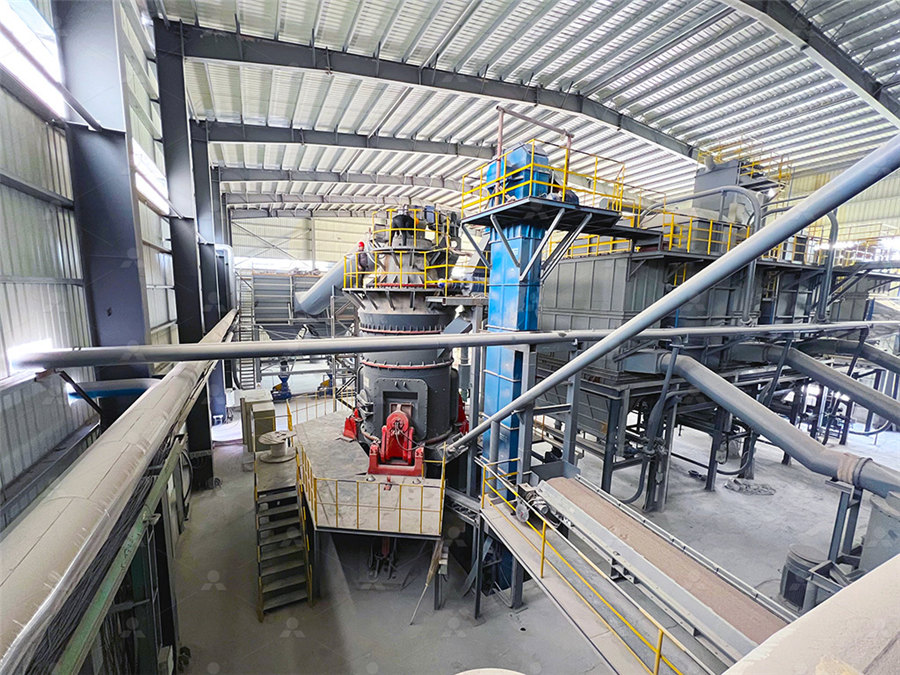
Everything about Cement Production Thermo Fisher Scientific
2024年3月1日 Extending Quarry Life through Raw Material Analysis in Cement Production While the life of a cement plant quarry is by its very nature finite, it can be extended by means of a quarry plan that takes into account the mix of raw materials required and mines them according to a mining plan How is the Crystalline Structure of Your Cement?2024年11月23日 Raw materials employed in the manufacture of cement are extracted by quarrying in the case of hard rocks such as limestones, slates, and some shales, with the aid of blasting when necessary Some deposits are mined by underground methods Softer rocks such as chalk and clay can be dug directly by excavators The excavated materials are transported Cement Extraction, Processing, Manufacturing BritannicaWhere, G is another constant The majority of the kiln feed is limestone, which does not have to be finer than 125 µm If an argillaceous limestone (cement rock) is used, it may be possible to obtain good burnability at particle sizes considerably coarser than this (since the effective calcite grain size is smaller than the particle size)Every Thing you need to know about Raw Mix Design cement manufacture – 3 Portland cement in today’s world 2 Raw materials management system – 22 Concrete problems 16 1 Raw materials – 2 Raw mix – 3 Reserves – 4 Crushing – 5 Drying – 6 Preblending – 7 Storage and handling 3 Raw milling and blending 3 Computerised Maintenance Management Systems 30 1 Raw milling The Cement Plant Operations Handbook International Cement
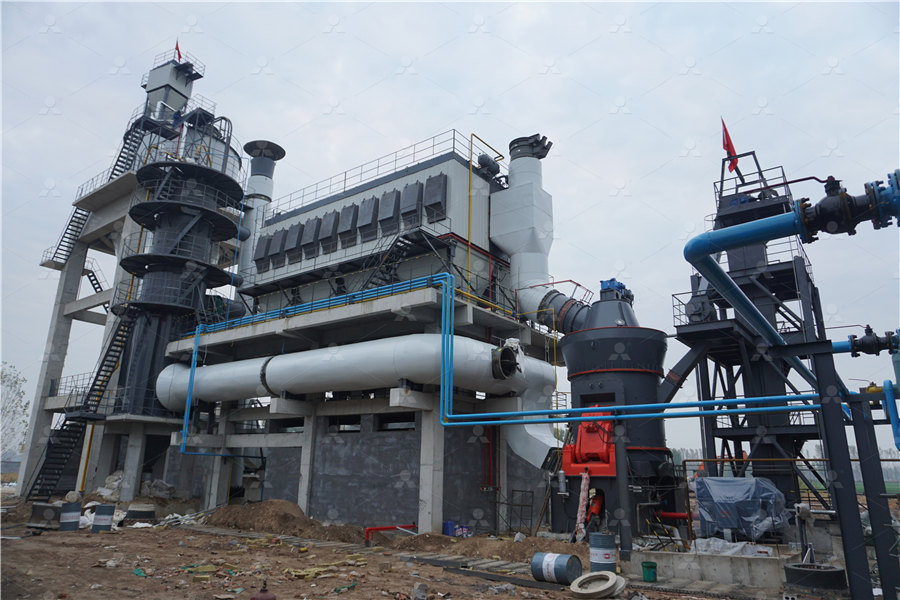
Alternative Fuels Raw Materials – Cement
These alternative fuels and raw materials are typically byproducts of other industrial processes or waste materials that would otherwise be disposed of Source: CIF Survey, Status and prospects of coprocessing of waste in EU cement plants (Ecofys 2017), Portland Cement Association, Global Cement and Concrete Association, CembureauCement Plant Schematic Process Flow The Calcination Process Raw Materials Use and Product Flexibility The Use of Steelmaking Slag in Cement Manufacturing, 2009 RCC Workshop Author: William Stanley Subject: 2009 RCC Workshop Keywords: William Stanley, Edward C Levy Co,The Use of Steelmaking Slag in Cement manufacturing P2 Vertical raw mill is one kind of raw mill, generally used to grind bulk, granular, and powder raw materials into required cement raw meal in the cement manufacturing plantVertical raw mill is an ideal grinding mill that crushing, drying, grinding, grading transfer set in one It can be widely used in cement, electric power, metallurgy, chemical industry, nonmetallic ore, and other industriesVertical raw mill Cement PlantIn cement raw materials the lime component is generally represented up to an amount of 7680 0/o Therefore, the chemical and physical properties of this component are of decisive influence, when it comes to selecting a method of Raw materials used for Cement Production
.jpg)
Crushing Technologies thyssenkrupp Polysius
The additional crusher ensures the supply of High Grade Limestone to the cement plant in the coming years As it will be necessary to move the crusher in the future, Semen Bima has opted for a semimobile design of the crushing Cement production starts in quarries where limestone and clay are mined and crushed Location of the crushers could be at the quarry or at the plant (largely is a function of haulage vs conveying costs) Already crushed raw materials are Raw Meal Suspension In Calciner INFINITY FOR China stacker and reclaimer manufacturer offers circular or rectangular stacker and reclaimer for bulk material handling system in cement plants customization design and competitive price Skip to content +86 s about blog contact EN ES Menu Menu Home; Cement Equipment Raw Material processing Stacker Stacker And Reclaimer Cement Plant PartsAGICO CEMENT supplier cement roller press, high pressure grinding roll for raw materials grinding, and clinker grinding plant As a leading cement grinding plant manufacturer in China, we offer roller press in cement plant, roller press cement mill, high pressure grinding roller, Get your free quote now!Cement Roller Press, Roller Press In Cement Plant HPGR Crusher
.jpg)
Understanding the Raw Materials for Manufacturing Cement
2024年8月20日 Step 4: Cement grinding and storageThe cooled clinker with gypsum is finely ground in a cement mill to form the hard cement The other raw materials are added during the grinding process The raw material added during the grinding process defines the quality of the cement Therefore, the raw materials determine the cement grade Let us discuss Raw material: raw gypsum powder, special paper, modified starch, foamingagent, our workshop Onestop solution service Design Equipment Supply AGICO CEMENT supplies EPC projects for both cement plant and single cement plant equipment CONTACT INFO +86 s 19F, Gypsum Board Manufacturing Plant Plasterboard Production Line2024年2月11日 Usually, limestone is 80 percent, and the remaining 20 percent is clay The raw mix is dried in the cement mining process or cement plant, and heavy wheel rollers and moving tables mix the raw material And then, the rotating roller crushes the material into a fine powder to be stored in silos fed to the kiln PreHeating Raw MaterialAll Stages of Cement Manufacturing from The Cement MiningRaw material blending is an important process affecting cement quality The aim of this process is to mix a variety of materials such as limestone, shale (clay), sandstone and iron to produce The cement raw material blending process and its control
.jpg)
Raw milling and blending INFINITY FOR CEMENT EQUIPMENT
Although about lSSt raw materials are required to produce 1t of clinker,kiln feedtoclinker ratio is typically 165175 as weighed, due to the loss of dust with exhaust gas, later collected and returned The ratio should be periodically reconciled with clinker and cement inventories and with measured dust loss in the preheater exhaust