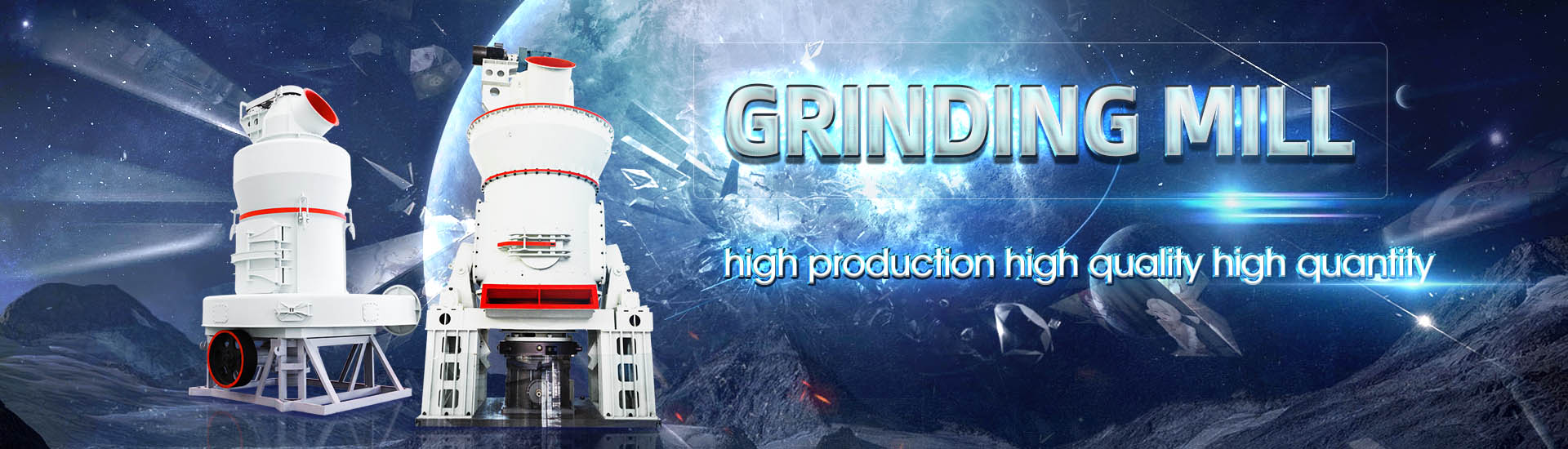
Formula and ratio of cement without clinker
.jpg)
CLINKER SUBSTITUTION IN THE CEMENT INDUSTRY CEMBUREAU
From a technical perspective, how does one lower the clinker content of cement? Lowering the clinkertocement ratio requires the use of Supplementary Cementitious Materials (SCMs) 2023年9月1日 We demonstrate that this reduces the carbon footprint by up to 50% for concrete and mortar with similar mechanical properties A theory is proposed, linking materials' strength Toward net zero carbon for concrete and mortar: Clinker Previous research indicated that Portland cement clinker is replaced by secondary cementitious materials such as steel slag and fly ash could potentially reduce CO 2 equivalent emissions by Steering the early strength of clinkerfree cementitious mortar by 2021年12月28日 Currently, the production of one ton of ordinary Portland cement (OPC) releases considerable amounts of CO2 into the atmosphere As the need and demand for this Alternative Clinker Technologies for Reducing Carbon Emissions in
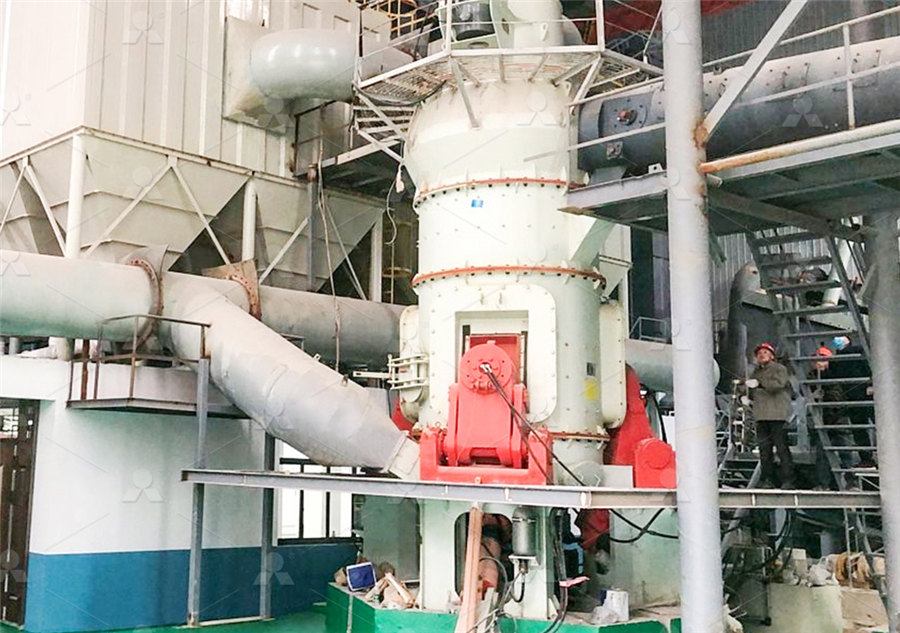
Cement substitution with secondary materials can reduce annual
2022年9月30日 Our data (Fig 2) show that such secondary CM mixtures can theoretically achieve an average clinkertocement mass ratio of ~014 globally, ie, a reduction of ~61 12 formulations and production processes These often go beyond the limitations of the Bogue 13 equations and more flexible approaches are required Modern thermodynamic calculations 15 Thermodynamic data for cement clinkering White Rose Maximal substitution of Portland cement clinker with these materials could have avoided up to 13 Gt CO2eq emissions (~44% of cement production and ~28% of anthropogenic CO2eq Cement substitution with secondary materials can reduce annual This ratio indicates the quantity of initial liquid phase present during burning It is generally accepted that an AIF ratio between 1416 is a desirable optimum level and most beneficial to U1e burning of U1c clinker The higher this ratio, the EVERYTHING YOU NEED TO KNOW ABOUT THE
.jpg)
Portland cement clinker: the Bogue calculation Understanding Cement
The standard Bogue calculation refers to cement clinker, rather than cement, but it can be adjusted for use with cement Although the result is only approximate, the calculation is an extremely useful and widelyused calculation in the cement industry The calculation assumes that the four main clinker minerals are pure minerals with compositions:Chemical compositional parameters used to describe Potland cement clinker (LSF, SR, AR, SR) Understanding Cement Interpreting Cement Science Since 2005 Menu Home; The LSF controls the ratio of alite to belite in the Chemicl parameters defining clinker compositionTechnological developments in over a century of production of Portland cement clinker have greatly improved the homogeneity of the feed and clinker leading to much more favourable conditions for alite formation which remains the key chemical reaction in the process This development is described along with the thermodynamic processes which either enhance the The chemistry of Portland cement clinker Advances in Cement 2018年12月31日 Energy recovery and exergy recovery in a clinker cooler was a major factor in optimizing clinker production and cement grinding process, the running clinker cooler has an energy recovery was 4831 Energy and Exergy Analysis of Clinker Cooler in the Cement
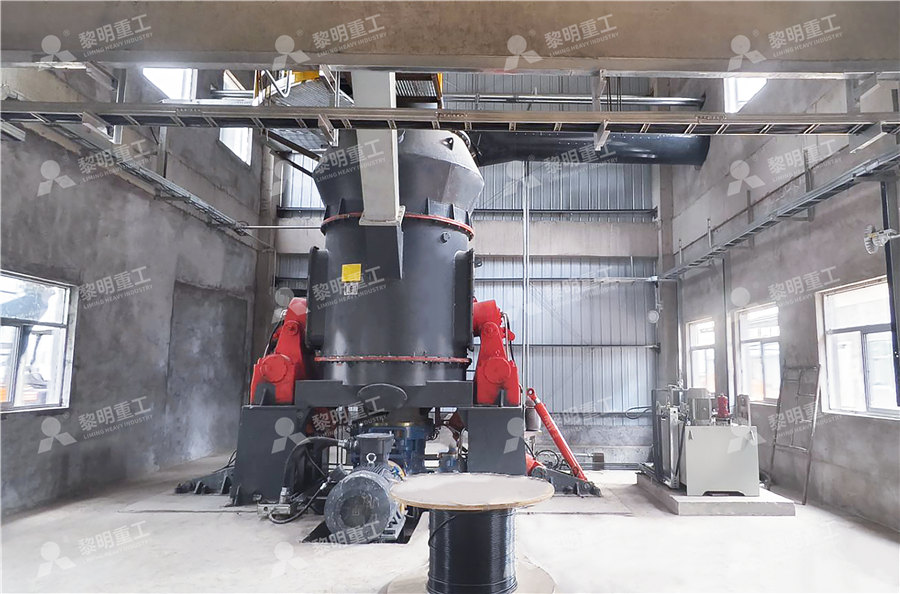
Analysis of high clinker ratio of Portland Composite Cement (PCC)
2020年10月1日 One way to increase efficiency and reduce costs, as well as CO 2 at a cement plant is to utilizing a third material to produce Portland Composite Cement (PCC) According to Indonesian National Standards of Portland Composite Cement (PCC)SNI 1570642004 [6], which adheres to ASTM C 59503 [7] and European Standards EN 1971:2000 [8], PCC is without need for adjustments The unusual clinker and cement regenerated from CRC rubble is investigated within this study Because the cement minerals within this regenerated clinker and cement are not necessarily the classic cement minerals, the influence on the formation and hydration of these minerals needs to be assessedThe Assessment of Clinker and Cement Regenerated from Alkali sulfur ratio is the ratio of alkali oxides (sodium oxide and potassium oxide) to sulfur trioxide in clinker It is expressed as a percentage and is an essential parameter in determining the quality of clinker The ideal alkali sulfur ratio for producing highquality cement is between 08 and 12 The Importance of Alkali Sulfur RatioAlkali Sulfur Ratio In Clinker: Understanding The Importance2020年10月15日 This research focused the role to study the effects and ways to control the chemical composition of clinker for better cement production Cement is a substance produced by grinding a mixture of a Effects and Control of Chemical Composition of Clinker for Cement
.jpg)
Process characteristics of clinker and cement production SINTEF
Continuous high temperature process in the cement industry: Calcination and cement clinker burning Calcination of raw material CaCO 3 => CaO + CO 2 Process emissions of raw material: = 054 t CO 2 /t clinker Endotherm reaction at 950 °C ca 1700 MJ/t clinker ≈ 50% of energy Cement clinker burning at 1450 °C formation of hydraulic2018年4月19日 The found average difference in Heat required for clinker formation between temperature 1338 °C and 1450 °C is 8226 kJ/kgclinker representing 223% of Total heat input are 3686 kJ/kgclinkerCalculation of the formation process of clinker 2020年7月1日 According to Indonesian Standard SNI 1570642004, Portland Composite Cement (PCC) or blended cement is defined as a hydraulic binder which consists of clinker, gypsum and one or more inorganic Analysis of high clinker ratio of Portland Composite In some countries, it is already today more than 90% This makes the European cement industry the global frontrunner in the use of alternative fuels and materials Clinker substitution and novel clinkers The effort in reducing the Clinker Cembureau
.jpg)
Quality Calculations Cement Plant Optimization
Alkali / Sulphur ratio Liquid Phase LP% 3CALC %Ash absorption in clinker Raw Mix to Clinker ratio (R/C) Go To Online Calculators Clinker C3S, C2S, C3A, C4AF Cement C3S, C2S, C3A, C4AF Burnability index (for clinker) Burnability factor (for clinker) Burning temperature (minimum) Go To Online Calculators10 alternative raw materials for cement manufacture [3, 4] Environmental concerns are also 11 promoting the development of lowercalcium clinker formulations, such as calcium 12 sulfoaluminate cement clinker which contain volatile species and involve gassolid reactions 13 not normally encountered in Portland cement (PC) clinkering [5]Thermodynamic data for cement clinkering White Rose 2021年12月28日 Reduction of the cementtoclinker ratio, by replacing clinker with supplementary cementitious materials (SCM’s); ii of cement without the need for a superplasticizer [19]Alternative Clinker Technologies for Reducing Carbon Emissions 2019年5月8日 This paper aims to evaluate the influence of three kinds of sulfates from the green production of cement on its sintering and hydration The properties of clinker and hydration were monitored by thermogravimetric and differential thermal analysis (TG–DTA), Xray diffraction, Xray fluorescence and isothermal conduction calorimeter Results indicate that gypsum lowers Sinterization and hydration of synthesized cement clinker doped with
.jpg)
Essential Cement Manufacturing Formulas and Their Applications
C4AF influences the color and clinker properties and plays a role in the liquid phase of cement during kiln heating Formula: C4AF=304Fe2O3C4AF = 304Fe₂O₃ C 4 A F = 304 F e 2 O 3 Application: The amount of C4AF determines the color and contributes to the formation of the liquid phase, which affects kiln operation and clinker cooling2024年3月1日 Commercially produced cement clinkers can either be aliteenriched (Type I or III Portland cement (PC)) and beliteenriched (Type II or IV PC) [11, 12]Type I or III PC, where C 3 S (where: C = CaO; S = SiO 2; A = Al 2 O 3, and F = Fe 2 O 3) is the dominant phase, is the most prevalent type used in constructionIn contrast, beliteenriched cement, where C 2 S is the Toward smart and sustainable cement manufacturing process: 2021年1月1日 In general, the quality targets for a clinker are expressed in terms of lime saturation, silica ratio and alumina ratio, which are determined in the following explications as [4], [5]: The silica ratio (SR) describes the ratio between solid (silicates) and liquid (aluminates) phases at sintering temperature and is calculated by the following formula: SR = SiO 2 / (Al 2 Influence of raw meal composition on clinker reactivity and cement At the highest temperatures reached by the clinker, perhaps only about 25% of the clinker is a liquid and the solid phases are then mainly alite, belite and free lime The liquid is vital in that it acts a flux, promoting reactions by ion transfer; without the liquid phase, combinability would be poor and it would be very difficult to make cementClinker: combinability of mixes Understanding Cement
.jpg)
Lime Saturation Factor Cement Plant Optimization
Lime Saturation Factor (LSF) is the ratio of the actual amount of lime in raw meal/clinker to the theoretical lime required by the major oxides (SiO 2, Al 2 O 3 and Fe 2 O 3) in the raw mix or clinkerIt is practically impossible to complete the reaction to 100%, in a reactor like rotary kiln, therefore there will always be some unreacted lime (CaO f) known as free limeThe thermal efficiency of rotary kiln clinker coolers of all types of design is within the range of 40 to more than 80% b)Another criterion for judging the cooler efficiency is the temperature difference between the hot clinker entering the Clinker cooling INFINITY FOR CEMENT EQUIPMENTPortland cement clinker thermochemistry Clinker Thermochemistry Home; About this site from the cement manufacturing point of view, the effective formula is: Si 2 Al 2 O 5 (OH) 2 → 2 SiO 2 The rate at which melting takes place also varies If the mix has the "eutectic composition" with an Al 2 O 3 /Fe 2 O 3 ratio of 1415 Cement Kilns: Clinker Thermochemistry2021年12月1日 Portland cement production is responsible for about 5–8% of manmade CO 2 emissions [1]One of the most effective solutions to substantially reduce its environmental footprint is clinker replacement with supplementary cementitious materials (SCMs) [2]Much research has been conducted on identifying new sources of SCMs [3], on combining several types of SCMs Formulation of low clinker blended cements and concrete with enhanced
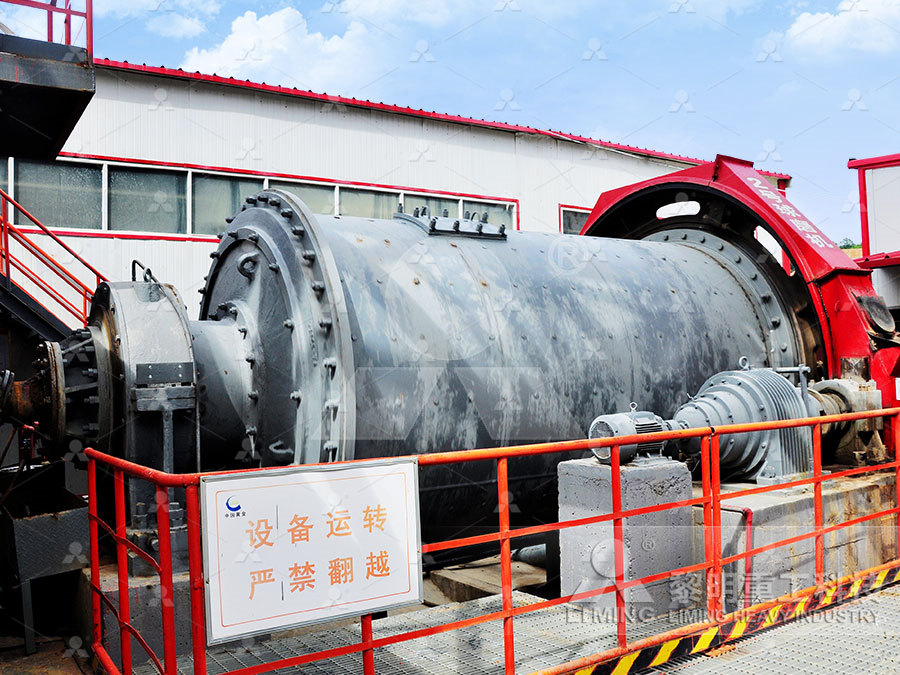
Quality Control Formula INFINITY FOR CEMENT EQUIPMENT
Previous Post Next Post Contents1 Quality Control Formula11 Loss on ignition (LOI) (CO2 from Calcination)12 Silica Modulus/Ratio (SM)13 Alumina Modulus/Alumina iron ratio (AM)14 Lime saturation factor (LSF)15 % Liquid16 Bogue’s Formula for Cement Constituents17 Degree of Calcination18 Sulphur to Alkali Ratio19 Free Lime110 Blending ratio111 Raw meal to 2024年7月21日 With the increasing depletion of highquality raw materials, siliceous limestone, sandstone and other hardtoburn raw materials containing crystalline SiO2 are gradually being used to produce clinker This study investigates the influence of the quartz content and particle size in siliceous limestone on the calcination process and the resultant quality of cement clinkerEffects of Fineness and Morphology of Quartz in Siliceous 2013年1月1日 Studies on cement production optimisation have been carried out on clinker simulation using AspenTech [36], cement raw materials blending using a general nonlinear timevarying model [37], cement Modelling the cement process and cement clinker quality2019年2月21日 Clinker (in cement industry) is It calculated from the ratio of the difference in total CaO content without the sum of Al 2 0 3 + Fe 2 0 3 and S0 3 to the Si0 2 concentration with the corresponding coefficients — the molar ratios of each oxide to CaO For calculation of factor of saturation used Kind VA formula (1) Value KS CLINKER GRINDING IN CEMENT PRODUCTION Energosteel
.jpg)
Modelling of clinker cooler and evaluation of its performance in
2021年3月24日 Cement manufacturing requires cooling down of hot clinker at temperature of about 1350o C to temperature lower than 100 o C in a cooling system known as clinker cooler2021年11月17日 The 43grade cement concrete mortar made with cement, water, and sand in the ratio of 1:1:3,cured for 28 days under controlled conditions achieves a minimum compressive strength of 43 N/mm 2 A 43grade cement is used in general civil engineering construction work, RCC structures (M25 concrete), NonRCC structures, plastering works, etcFundamentals of Cement Chemistry, Operations, and Quality 1983年1月1日 Cement raw mix represents a polymineral and polydispersive mixture whose compositions can vary within a wide range due to the character of raw materials used In the clinkermaking process, 90% of the raw mix constituents is comprised of the four major oxides, viz C, A, S and F, and the remaining 10% is made up of minor constituentsBurnability and Clinkerization of Cement Raw MixesSulfate Resistant Clinker – The composition of this type of clinker is alite 76%, belite 5%, tricalcium aluminate 2%, tetra calcium aluminoferrite 16%, and free calcium oxide 1% In recent years the production of this type of clinker has What is Cement Clinker? Composition, Types Uses
.jpg)
Quality Control of Cement Clinker through Operating Condition
2024年1月29日 Recent advances in artificial intelligence (AI) technologies such as deep learning open up new opportunities for various industries, such as cement manufacturing, to transition from traditional humanaided manually controlled production processes to the modern era of “intelligentization” More and more practitioners have started to apply machine learning As an alternative replacement of clay, sewage sludge is also combined with other solid waste in cement production Lin and Lin (2004; 2005) used different types of waste sludge ash, including sewage sludge ash, water purification sludge ash and steel slag and limestone, as raw components for the production of ecocement clinkers by burning at 1400 °C for 6 hCement Clinker Production an overview ScienceDirect Topics2011年5月1日 In this paper, concrete mixtures were prepared with the substitution of CEM I 425R cement with an “untreated” raw bypass dust at the ratios of 10, 20, and 30% along with a control specimen Reactions of alkalis, chlorine and sulfur during clinker productionYou can produce highquality concrete by lowering the watercement ratio as much as possible without sacrificing the workability of fresh concrete, allowing it to be properly placed, consolidated, and cured The watercement ratio is the weight of the Applications of Cement Portland Cement Association
.jpg)
Cement Clinker an overview ScienceDirect Topics
Report of UNEP SBCI WORKING GROUP ON LOWCO2 ECOEFFICIENT CEMENTBASED MATERIALS Ellis Gartner, Tongbo Sui, in Cement and Concrete Research, 2018 1 Introduction The term “alternative cement clinker ” as used here refers to a manmade mineral material that, when ground to a fine powder, is capable of reacting sufficiently rapidly with water and/or CO 2 2011年6月14日 5 CONCLUSIONS Although the amount of liquid phase in the burning and transition zones of the kiln is important to clinker formation and brick performance, the rheological properties of the melt are even more important The rheological properties of the clinker melt control parameters such as clinker mineral formation, clinker coatability, clinker fineness, Clinker Liquid Phase PDF Free Download SlideShare