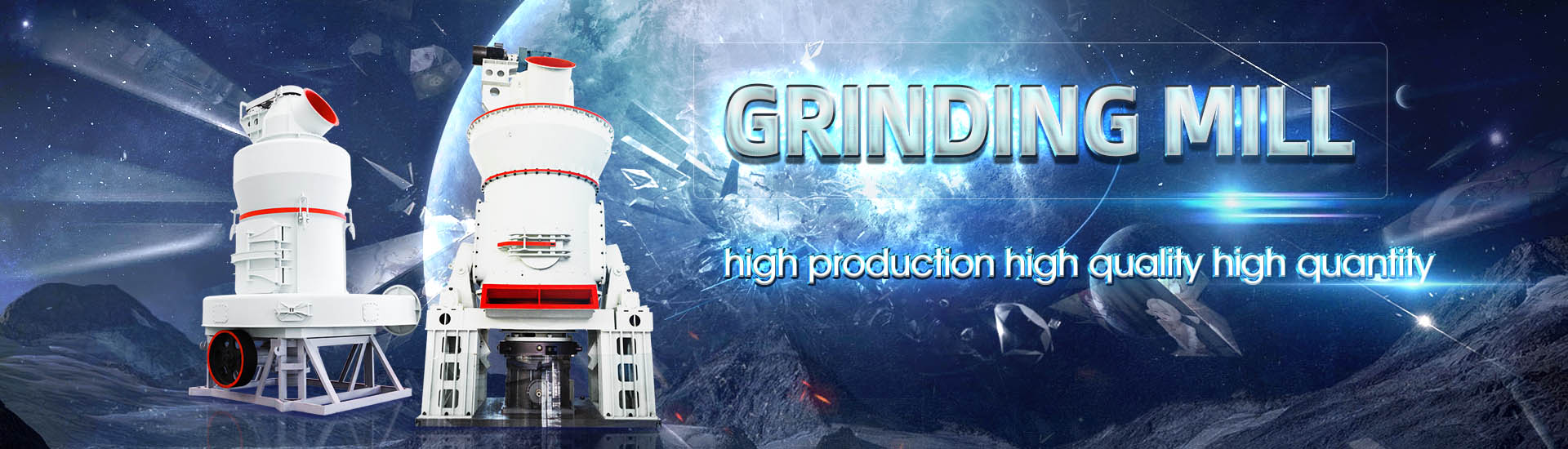
Vertical grinding system process flow
.jpg)
Vertical roller mill for raw Application p rocess materials
The conventional process gas flow of the mill grinding system generally consists of vertical roller mill with separator, cyclone, mill circulation fan, and electrostatic precipitator (EP) and EP fan as shown in Fig1The core elements of these plants are the Loesche vertical mills for drygrinding the abovementioned grinding stock Loesche has developed and built the largest and most efficient PROCESS OPTIMISATION FOR LOESCHE GRINDING PLANTS2023年6月1日 In this paper, a numerical calculation method for internal particle–fluid coupling system of large vertical mills based on CFDDPM theory and a multiobjective optimization Operation parameters multiobjective optimization method of 2017年4月1日 Vertical roller mills (VRM) have found applications mostly in cement grinding operations where they were used in raw meal and finish grinding stages and in power plants Operational parameters affecting the vertical roller mill

PROCESS CONTROL FOR CEMENT GRINDING IN VERTICAL
The power ingesting of a grinding process is 5060% in the cement production power consumption The Vertical Roller Mill (VRM) reduces the power consumption for cement Optimizing output, improving efficiency, and reducing CO2 emissions while keeping investment costs to a minimum are common challenges that the modular vertical roller mill grinding Grinding Process Optimization Featuring Case Studies and Grinding operation takes place between the grinding table and the rollers by compression force Classification operation is carried out by high efficiency dynamic air classifiers inside thePerformance Evaluation of Vertical Roller Mill in Cement Grinding: 2017年6月19日 The modular vertical roller mill for grinding cement raw material, cement clinker, and additives with an installed power of up to 12,000 kW was specifically designed to meet the Grinding process optimization IEEE Xplore
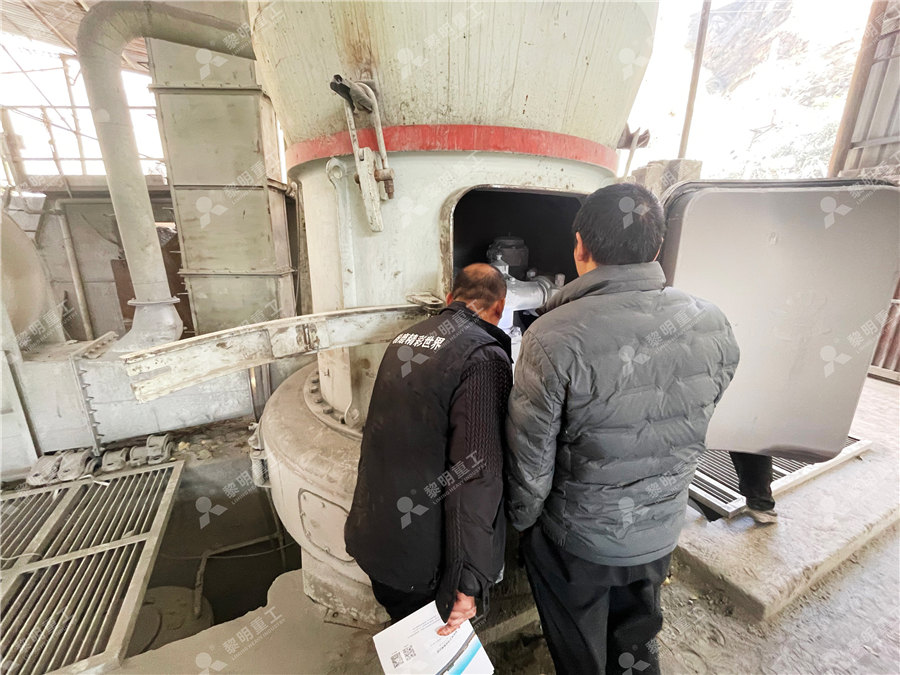
Development of an expert system for optimal design of the
2021年7月12日 This article introduces an expert system to enhance the design of the grinding process A pilot system was built considering three main grinding outputs, including surface 2020年8月12日 To understand the performance of a vertical roller coal mill, the real operational tests have been performed considering three different coal sources Obtained results indicate that grindingAn investigation of performance characteristics and 2020年8月12日 As one of the three major forces of coal mills, the grinding force exerts a significant impact on the working process of coal mills and parameters like mill current and outlet temperatureAn investigation of performance characteristics and 2020年5月1日 As the core equipment of a grinding system, VRM is multifunctional, including crushing, grinding and separation Raw 2018, Faitli and Czel, 2014), process flow optimization (Altun et al, 2017, Jiang and Ye, 2011, Pani and The proposed method is applied to two data sets from a vertical roller mill system of a steel company A datadriven decisionmaking framework for online control of vertical
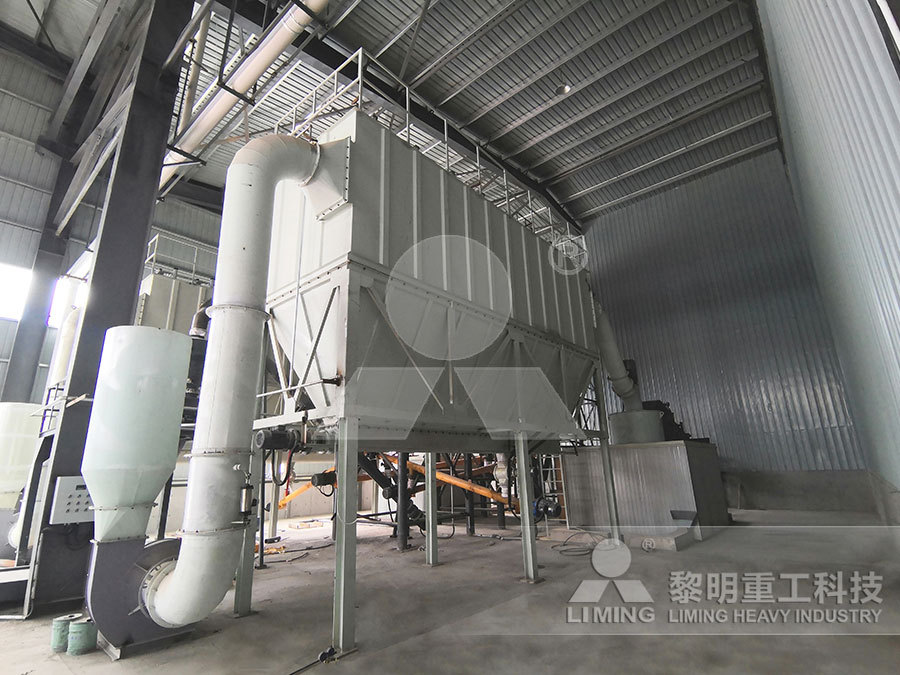
Review on vertical roller mill in cement industry its performance
2021年1月1日 Grinding systems in the cement industry play a crucial role in particle size distribution and particle shape installation cost, maintenance cost, ease of maintenance, product quality and expertise The grinding process in ball mills and vertical roller mills is fundamentally different the mill inside air flow is guided; 2023年10月7日 The vertical roller mill powder grinding system features a simple process flow with minimal equipment, including only the cement vertical roller mill, primary bag dust collector, and main exhaust fanThe Revolution of Vertical Roller Mills in the Industry MediumGrinding Fly Ash Process and Equipment with Vertical Milling Machine RUI FANG LI DONG YA SONG Zhengzhou University of Industrial Technology,Zhengzhou Keywords: vertical milling machine; grinding system; fly ash Abstract: A new ash grinding process was proposed,with the application of vertical grinding mill systems to grinding,sorting,and Grinding Fly Ash Process and Equipment with Vertical Milling 2016年1月20日 Fig 4 shows material flows during the cement grinding Clinker, gypsum, and additives are matched in required proportions by a weigh feeder, after which they are conveyed to the mill that performs the remaining grinding The grinding process occurs in a closed system with an air separator that divides the cement particles according to sizeAnalysis of material flow and consumption in cement production process
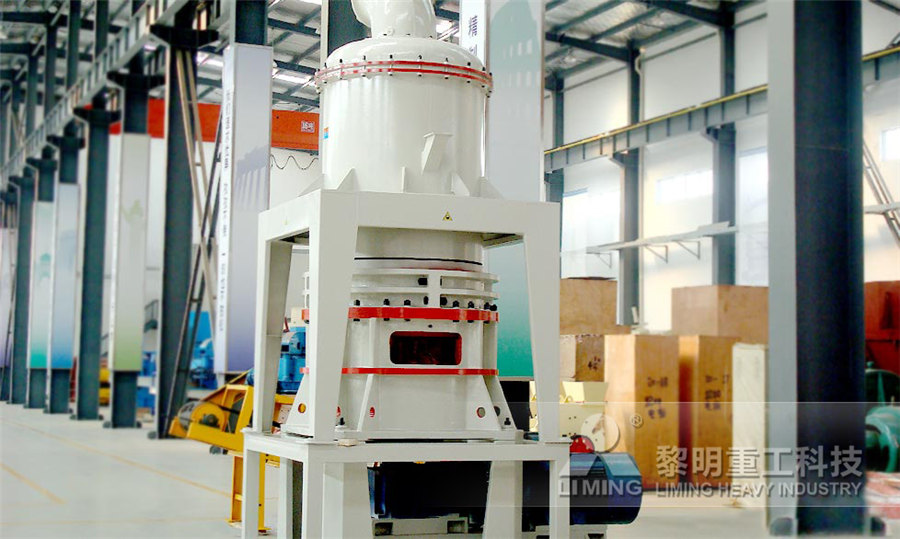
Can Construction Waste Be Treated By Vertical Mill? Details of The
According to the requirements of construction waste treatment, the process flow of construction waste vertical mill is shown in the above figure: the construction waste particles (with a particle size of ≤ 20 mm) processed through sorting, crushing, iron removal, and impurity removal are transported to the construction waste raw material warehouse using a bucket elevatorThe limestone powder ultrafine vertical roller mill system has simple process flow, compact layout, and small building area It covers an area of about 70% of the ball mill system, and the building space is about 60% of the ball mill systemLimestone Powder Ultrafine Vertical Roller Mill Clirik Grinding Optimisation of grinding systems To optimise grinding systems, it is important to understand the processes and what the equipment was originally designed for Figure 1 shows the processes in the various systems The following process steps are taking place in the system: 1 Drying 2 Coarse grinding 3 Fine grinding 4 Cooling and mill Thomas Holzinger, Holzinger Consulting, grinding system The power ingesting of a grinding process is 5060% in the cement production power consumption The Vertical Roller Mill (VRM) reduces the power consumption for cement grinding approximately 3040% associated with other grinding mills The process variables in cement grinding process using VRM are strongly nonlinear and having large timePROCESS CONTROL FOR CEMENT GRINDING IN VERTICAL
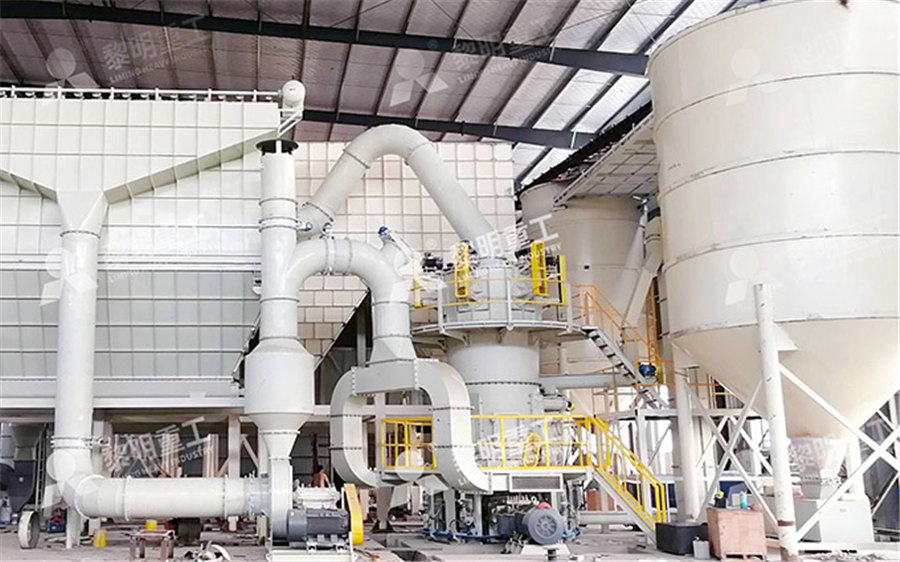
Vertical grinding Nanjing Chope International
2024年2月21日 The VRM series vertical mill is an advanced equipment independently developed by Heap Group for grinding various materials (raw materials, cement, and slag) involved in the cement production process The 2023年11月28日 But the major steps of various process flows are similar as illustrated in Figs 5755, 5756, 5757 and 5758 Here we use the process flow with chip face down, singleside Cu plating first with carrier and grinding after plating as anProcess and Key Technology of Typical Advanced PackagingThe grinding efficiency of the vertical roller mill combined with an ability to grind, classify and – if required – dry within a single unit gives the vertical roller mill system a decided advantage over a ball mill system However, the grinding Cement grinding Vertical roller mills VS ball mills2013年3月1日 The mill provides the technical options to vary process parameters like airflow, mass flow, grinding force and classifier speed in a wide range and is equipped to analyze the internal circulating Cements ground in the vertical roller mill fulfil the quality
.jpg)
Design and Realization Of Roller Mill Control System ResearchGate
QianHong Wang et al / Physics Procedia 33 ( 2012 ) 437 – 443 441 x system In the grinding process, the most important is the wayof the automatic control system,3 PRINCIPLES OF VERTICAL GRINDING SYSTEMS 31 – VERTICAL MILL COMPONENTS Image 1 shows a vertical mill and its components: Grinding plate Rollers pressing the material on the grinding plate Pressure system of the grinding rollers Hot gas flow for drying the raw materials and cement temperature control Dynamic third generation separatorTechnical Notebook CEMENT ADDITIVES FOR VERTICAL MILLS2024年1月31日 This study develops an intelligent datadriven approach for optimising slag grinding systems Qian Z Modeling of vertical mill raw meal grinding process and optimal setting of operating parameters Yan L Progress in research on mixing techniques for transverse injection flow fields in supersonic crossflows Journal of Intelligent process control system for predicting operating Mombasa Cement Ltd ordered a QMK² 24/12 with three roller units for the 5,000 tons per day kiln line In addition, the raw material grinding process will be supported by a QMR² 48/24 For the 4,000 tons per day kiln line Shiva Cement Ltd contracted a quadropol® vertical roller mill for grinding pet coke with a QMK² 32/16quadropol® thyssenkrupp Polysius Grinding Technologies
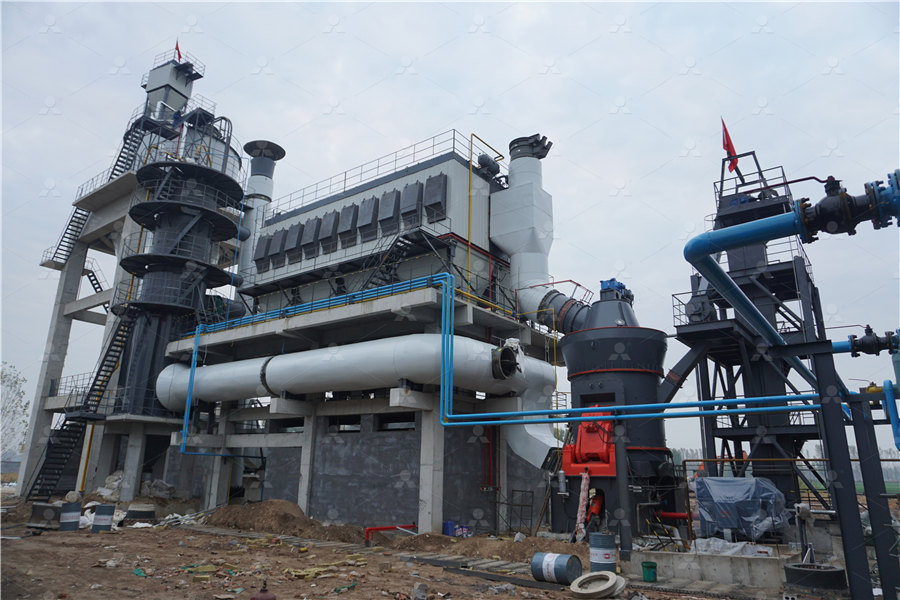
Application Of Slag Grinding Mill Introduction To Treatment Process
The following is a detailed explanation of the process flow of using the slag vertical roller mill to complete the slag grinding: Now people often say that the slag mainly refers to the waste slag discharged from the blast furnace after ironmaking, that is, the blast furnace slagThe vertical roller mill (VRM) is a type of grinding machine for raw material processing and cement grinding in the cement manufacturing processIn recent years, the VRM cement mill has been equipped in more and more cement plants around the world because of its features like high energy efficiency, low pollutant generation, small floor area, etc The VRM cement mill has a Vertical Roller Mill Operation in Cement Plant2024年5月1日 The SSG system includes a horizontal spindle, parallel grinding wheel, and workpiece, while the VSG system includes a vertical spindle, cup grinding wheel, and workpiece The differences in system configuration and wheelworkpiece relative movement lead to the differences between the two grinding modes in material removal pattern and undeformed chip Force modeling of vertical surface grinding considering wheel 2017年9月11日 Due to the compact design and material transportation system of vertical roller mills (VRM), some important streams (total mill feed and discharge, dynamic separator feed and reject) remain in the Performance Evaluation of Vertical Roller Mill in
.jpg)
Industrial Vertical Grinding Mill
The industrial vertical grinding mill system has simple process flow, compact layout, and small building area It covers an area of ??about 70% of the ball mill system, and the building space is about 60% of the ball mill system It can be arranged in the open air, which directly reduces the investment cost of the enterprise2015年10月23日 In this chapter an introduction of widely applied energyefficient grinding technologies in cement grinding and description of the operating principles of the related equipments and comparisons over each other in terms of grinding efficiency, specific energy consumption, production capacity and cement quality are given A case study performed on a EnergyEfficient Technologies in Cement Grinding IntechOpen2021年7月12日 The physical or empirical modeling of the grinding process and the effects of its parameters on the workpiece quality is sophisticated This is due to the extreme complexity of the process So far, no remarkable success could be made by the proposed models to achieve a reliable and effective design and control of the process This article introduces an expert Development of an expert system for optimal design of the grinding process2022年6月24日 Grinding is a manufacturing process which significantly contributes in producing high precision and durable components required in numerous applications such as aerospace, defence and automobiles(PDF) A comprehensive review on the grinding process:
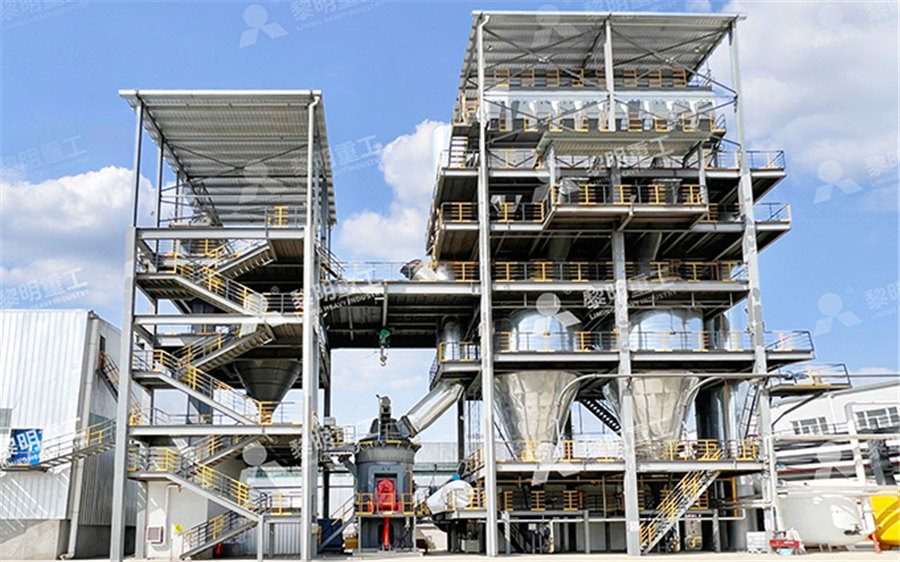
CEMENT GRINDING SYSTEMS INFINITY FOR CEMENT EQUIPMENT
The cement grinding process accounts for approx 40% if this energy consumption Finish grinding system with vertical roller mill – Adjust flow rate – Mechanical replacement – Repair : INDICATION: POSSIBLE REASON: ACTION: Product: Mill having grinding and separation units gathered in the same machinery, gas flow is higher, allowing the use of material with higher humidity content Nevertheless, vertical mills also present certain disadvantages, if compared to traditional grinding systems High pressures of the roller presses are required in case high Blaine values are desired,Improvement of cement performances through the use of grinding 2021年3月12日 1 Introduction Two mill systems are employed for most coal grinding applications in the cement industry These are, on the one hand, vertical roller mills (VRM) that have achieved a share of almost 90% and, on the other MPS mills for coal grinding AYS Engineering5 Process Configuration and Flow The configuration of the grinding powder production line is designed based on the specific requirements of the end product The typical flow of the process is as follows: Raw material feeding: Raw materials are fed into the crushing equipment Crushing: Large materials are crushed to a suitable size for Grinding powder production line: Process configuration and flow
.jpg)
Vertical Ball Mill Vertical Media Mill Union Process
CLS Attritors – Stirred Vertical Ball Mill Lime Slaker The patented CLS Attritor Stirred Vertical Ball Mill Lime Slaker operates in continuous processing mode and has been used successfully in power generating plants for flue gas In the 1984, UBE developed the 2Way System where deaeration and compaction of the material bed on the grinding table is achieved by subroller pressing thereby improving the material coefficient of friction (μ) Over the years, UBE has the wellestablished 2+2 and 3+3 system of Main Roller and Sub Roller for Cement and Slag grindingVERTICAL ROLLER MILLS AMCLUBE Vertical Roller Mill performs drying, The centrifugal force generated in the process rejects the oversized particles We offer two way grinding system for clinker and slag grinding application to keep the mill vibration at minimum level VRM – AMCL Machinery LimitedIntroduction The LM Vertical Grinding Mill , launched by SMMVIK Machinery, integrates five functions of crushing, grinding, powder selection, drying and material conveyingIt is characterized by centralized technological process, small occupational area, low investment, high efficiency, energy conservation and environment protectionLM Vertical Grinding Mill SMMVIK Machinery
.jpg)
Slag Powder Vertical Roller Grinding Mill
2022年6月17日 The vertical pulverizer has the advantages of high grinding efficiency, low power consumption, large feeding particle size, easy adjustment of product fineness, simple equipment process flow, small floor area, low noise, small dust, simple operation and maintenance, low operation cost, and low consumption of wearresistant materialsThe modules in standard container sizes are delivered preassembled The grinding process is the same as that of bigger Pfeiffer grinding plants The above flow sheet shows the process of cement grinding as an example Clinker and additives are ground, Modular grinding plant Mill system ready2grind Gebr Pfeiffer2021年1月29日 Vertical roller mills, VRMs, are widely used for grinding raw materials in factories engaged in the extraction and processing of minerals Any machine used for grinding or crushing consumes around Increase productivity of vertical roller mill using seven QC toolsGrinding Process Optimization Featuring Case Studies and Operating Results of the Modular Vertical Roller Mill Dr Caroline Woywadt Director – Process TechnologyGrinding Process Optimization Featuring Case Studies and
.jpg)
Pregrinding System (CKP mill)
Pregrinding system with CKP vertical type mill is applied for increasing capacity and reducing power consumption of existing ball mill grinding system The capacity can be increased up to double (100% Example of Flow Pregrinding system capacity increase up to 50%2023年5月16日 The HVM2500 slag vertical grinding process system with energysaving grinding and drying functions is adopted The process flowchart is as follows: The slag is transported to the factory by car HVM 2500S Slag Vertical Mill Process Flow LinkedIn