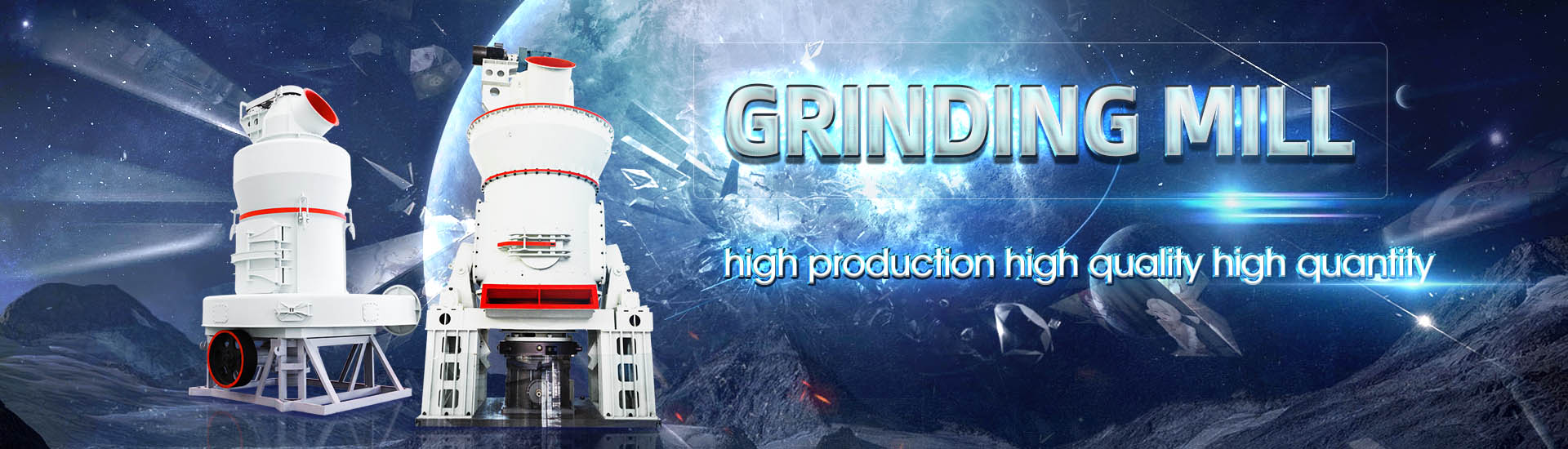
Annual summary of raw material processing in cement plant raw material workshopbureau control
.jpg)
Raw Mill in Cement Plant Cement Manufacturing Raw
A raw mill with a superior fineness and wellcontrolled chemical composition using as advanced control system can improve the cement quality and define critical cement craft parameters Amrit Cement uses the best of raw materials and raw materials, burning, grinding and quality control are supported by a range of chapters addressing critial topics such as maintenance and plant reporting, alongside a detailed The Cement Plant Operations Handbook International Cement 2019年4月1日 We present here the results of the calculations required to generate an internally consistent database for Great Britain and for Thailand that enables an informed materials flow analysis to beDatasets and calculations to evaluate raw material 2023年10月13日 Our approach not only consolidates data from established sources like development banks and governments but innovatively integrates the age of plants and the Global database of cement production assets and upstream
.jpg)
GCCA Sustainability Guidelines for coprocessing fuels and raw
The coprocessing of alternative fuels and raw materials in cement manufacturing to replace fossil fuels and primary raw materials is a longstanding contribution of the sector towards a circular Cement production requires the pyroprocessing of large quantities of raw materials in large kilns at high and sustained temperatures to produce clinker An average of almost 5 million Btus is Cement Production an overview ScienceDirect TopicsProducing cement consumes both large quantities of raw materials and fuel, and produces substantial CO2 emissions The use of alternative fuels and raw materials in cement Guidelines for CoProcessing Fuels and Raw Materials in Cement Objective of the study: to position the use of Alternative Raw Materials (ARM) in the clinker, cement and concrete production as a key element for the circular economy and the Status and prospects of Alternative Raw Materials in the European
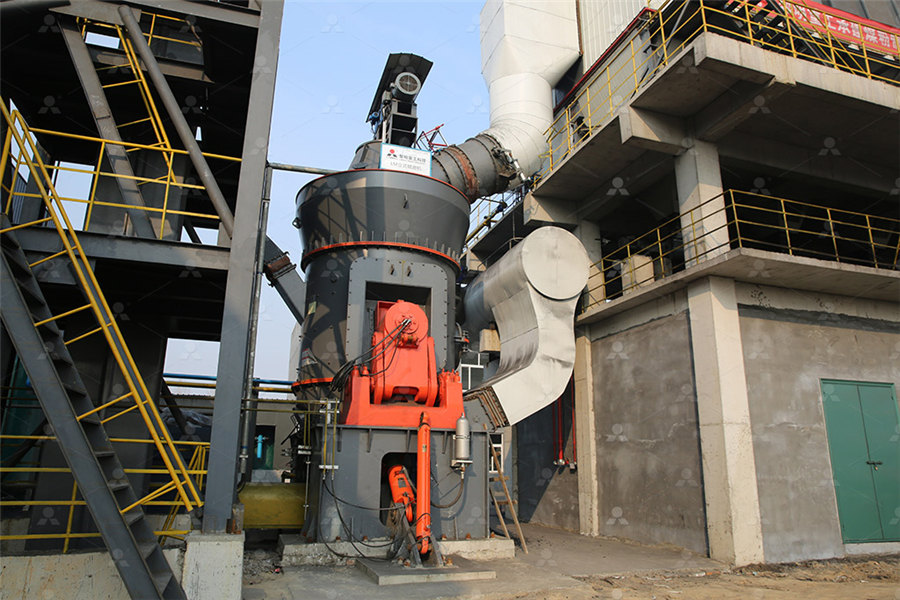
From raw materials to cement
The desired raw mix of crushed raw material and the additional components required for the type of cement, eg silica sand and iron ore, is prepared using metering devices2018年8月20日 Controlling the chemical composition of the raw meal in a cement plant is a critical process, impacting many of the key performance indices of cement production In addition to affecting several aspects of the final Analysing raw mix control International Cement ReviewCorrect blending and concentrating on the quality of raw materials are the two key factors that decide the superiority of the cement Raw material blending is in fact one of the most important processes in cement manufacturing since it has a Raw Mill in Cement Plant Cement Manufacturing the most important building materials Whether for houses, bridges or tunnels, we cannot imagine our modern world without it Join us for a short tour to experience how cement is made: starting with the extraction of raw materials and ending with the finished product From raw materials to cement Extracting raw materials Crushing and transportationFrom raw materials to cement
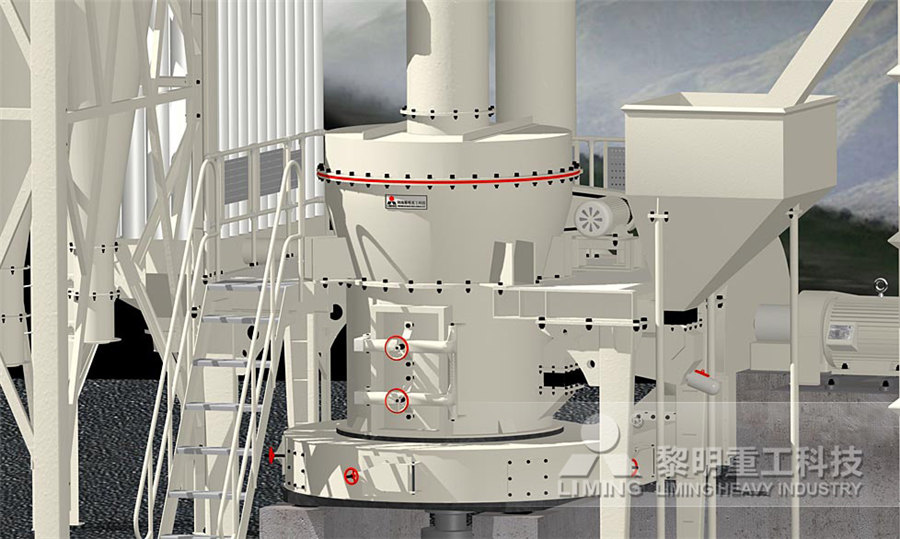
Understanding the Raw Materials for Manufacturing
2024年8月20日 Step 4: Cement grinding and storageThe cooled clinker with gypsum is finely ground in a cement mill to form the hard cement The other raw materials are added during the grinding process The raw material added In 2006 about 5% of the raw materials used in the production of clinker consisted of alternative raw materials, totalling about 145Mt/ year Alternative raw materials can be used to replace the traditional raw materials extracted from quarries, such as clay, shale and limestone, which are used in the kilnSustainable cement production COPROCESSING OF 2022年1月15日 Cement industry uses a number of wastes and byproducts as supplementary raw materials in cement raw mix which are referred to as alternative raw materials Industrial and mineral wastes from mineral processing industries, such as metallurgy, petrochemicals, chemicals, paper and pulp account for nearly 275 million tonnes per annumUtilisation of Alternative Fuels and Raw Materials in Indian Cement Sustainability Charter relating to Circular Economy and specifically the coprocessing of fuels and raw materials in cement manufacturing It is partially based on and supersedes the WBCSDCSI document Guidelines for Coprocessing Fuels and Raw Materials in Cement Manufacturing, version 2, July 2014 These guidelines areGCCA Sustainability Guidelines for coprocessing fuels and raw
.jpg)
Using Solid Waste Alternate Fuel Raw (AFR) Material as a Fuel
(E) Preprocessing: Transforming waste to AFR requires certain standards AFR does not always consist of a specific waste stream (such as tires or solvents) but must be prepared from different waste sources before being used as fuel or raw material in the cement plantLime Component Limestone: Common forms of calcium carbonate used as raw material for cement manufacturing are limestone and chalkLimestone is of predominantly fine grained crystalline structure, its hardness is between 18 to 30 of the Mohs scale of hardness and specific gravity 2 To 28 Limestone usually contains admixtures of clay substance or iron compounds, Raw materials for cement manufacturing Cement Plant 2020年9月29日 This study proposes a raw meal proportioning methodology for optimising coprocessing of natural feedstocks with alternative raw materials in clinker production, intending to reduce the content of An overview of alternative raw materials used in cement and 2024年11月23日 Cement Extraction, Processing, Manufacturing: Raw materials employed in the manufacture of cement are extracted by quarrying in the case of hard rocks such as limestones, slates, and some shales, with the aid of blasting when necessary Some deposits are mined by underground methods Softer rocks such as chalk and clay can be dug directly by Cement Extraction, Processing, Manufacturing Britannica
.jpg)
Raw mill Cement Plant
Raw mill is generally called cement raw mill, raw mill in cement plant, it refers to a common type of cement equipment in the cement plantIn the cement manufacturing process, raw mill in cement plant grind cement raw materials Bulk material handling is a major activity and bins for raw materials, intermediate products and finished cement must reliably provide controlled flows of materials upon demand The tonnages of material to be stored at various process Cement Plant Raw materials INFINITY FOR Sustainability Charter relating to Circular Economy and specifically the coprocessing of fuels and raw materials in cement manufacturing It is partially based on and supersedes the WBCSDCSI document Guidelines for Coprocessing Fuels and Raw Materials in Cement Manufacturing, version 2, July 2014 These guidelines areGCCA Sustainability Guidelines for coprocessing fuels and raw A: Online analyzers continuously measure the elemental composition of the entire raw material stream, in real time, being carried on a conveyor belt The system provides an elemental analysis of the raw materials each minute, without touching the materials, and without errors and costs associated with material sampling for offline laboratory analysisOnline Material Analysis for Cement Production FAQs
.jpg)
(PDF) Incorporation of Alternative Fuels and Raw Materials
2018年11月30日 Currently, the use of alternative fuels and raw materials (AFR) in the cement industry is very attractive This is driven by demands for environmental sustainability and the efficiency of fuel and 1983年1月1日 Statistical approach to computer control of cement rotary kilns IFAC J Automatica, Vol8,pp3548 Phillips, RA ( )Automation of a portland cement plant using a digital control computer Riegel, RW ( ) Improved process control of raw material blending and kiln/cooler operation result in major energy savings Ross, C W, TBay (]977)Control in Cement Production ScienceDirectTo evaluate the material flows associated with construction and demolition in different countries it is necessary to have a consistent set of data However, data collected by regulators and governments differ and this study used concrete as a case in point Concrete is a significant manmade material in construction whose use reflects socioeconomic variation between countries Evaluation of raw material extraction, processing, construction 2020年9月22日 The use of cement and concrete, among the most widely used manmade materials, is under scrutiny Owing to their largescale use, production of cement and concrete results in substantial emission Environmental impacts and decarbonization strategies in the cement
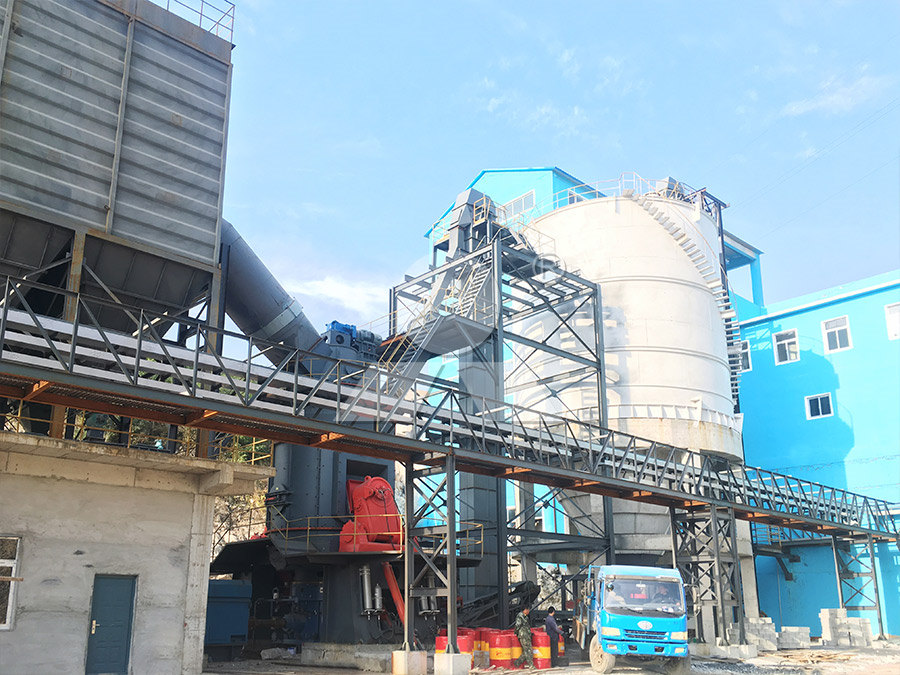
Raw material stacking and reclaiming Indian Cement Review
2016年11月30日 R Murthy and Santhosh Kumar M elaborate on the use of stackers and reclaimers used in cement industry for feeding raw materials Stacking raw materials/fuels and reclaiming them is an essential part of cement industry Stacking of raw material is done in order to have sufficient raw material to feed the plant during any unforeseen supply stoppageThis paper focuses on modelling and solving the ingredient ratio optimization problem in cement raw material blending process A general nonlinear timevarying (GNLTV) model is established for The cement raw material blending process and its control 2019年4月1日 Datasets and calculations to evaluate raw material extraction, processing, MPA Annual Cement Channel of Sale 20 032014; A Continuing Commitment: Summary Sustainable Development Report Datasets and calculations to evaluate raw material Alternative Raw Material” (AF/ARM), conducted on 79 June 2016 There is great potential for the development of alternative fuels and raw materials in India This usage of AF/ARM would improve the competitiveness of the sector and will also help the local industries and the communities to manage their waste in a more sustainable mannerALTERNATIVE FUELS AND ALTERNATIVE RAW MATERIALS UNIDO
.jpg)
Vertical raw mill Cement Plant
Vertical raw mill is one kind of raw mill, generally used to grind bulk, granular, and powder raw materials into required cement raw meal in the cement manufacturing plantVertical raw mill is an ideal grinding mill that crushing, drying, grinding, grading transfer set in one It can be widely used in cement, electric power, metallurgy, chemical industry, nonmetallic ore, and other industriesClinker – 11 Finish mill – 12 Cement – 13 Quality control – 14 Packing and distribution – 15 Emission abatement (dust, NO x, SO 2, etc) – 16 Maintenance – 17 Process – 18 Materials analysis –19 Plant capacity summary – 20 Storage capacity 15 Cement plant construction and valuation 244 1 New plant construction – 2The Cement Plant Operations Handbook International Cement Industrial waste Figure 3 Clinker microstructure analysed by optical microscopy (a and b) clinker obtained from cement plant that prepared with normal raw materials without alternative fuel nor alternative raw materials (c and d) clinker prepared by mixing 55% oilbased mud cutting wasteAn overview of alternative raw materials used in cement and AGICO Cement Vertical Mill AGICO Cement Ball Mill Cement Vertical Mill Grinding System Cement vertical mill, also called roller mill, is another raw mill commonly used in cement pared with the cement ball mill, it has a great difference in structure, grinding principle, process layout, automatic control, and energy consumption, which play an important role in the Raw Mill – Raw Mill In Cement Plant AGICO Cement Raw Mill

Summary Guidelines on Coprocessing Waste Materials in Cement
Baselines for traditional fuels and raw materials shall be defined: Y Control and monitor inputs, outputs, and emissions during the operation of the cement plant with virgin fuel and primary raw materials Y Evaluate the given environmental situation prior to starting waste coprocessing2021年3月3日 Cement is produced by a hightemperature (about 1500 °C) reaction in a rotary kiln of carefully proportioned and blended ratios of lime (CaO), silica (SiO 2), alumina (Al 2 O 3), and iron oxide (Fe 2 O 3)The production of cement is a chemical process requiring an accurate blend of the previously cited four key organic oxides and the limitation of several undesirable Cement SpringerLinkObjectives and contents Objective of the study: to position the use of Alternative Raw Materials (ARM) in the clinker, cement and concrete production as a key element for the circular economy and the decarbonization of the built environment Contents • The current use of Alternative Raw Materials including decarbonated raw materials • The future potential use of Alternative Raw Status and prospects of Alternative Raw Materials in the 2022年1月1日 This study uses linear programming to develop a methodology for selecting the best raw material mix in an ASCOM cement plant in Egypt In cement factories, this type adheres to Egyptian chemical LINEAR PROGRAMMING AS A TOOL TO DESIGN THE
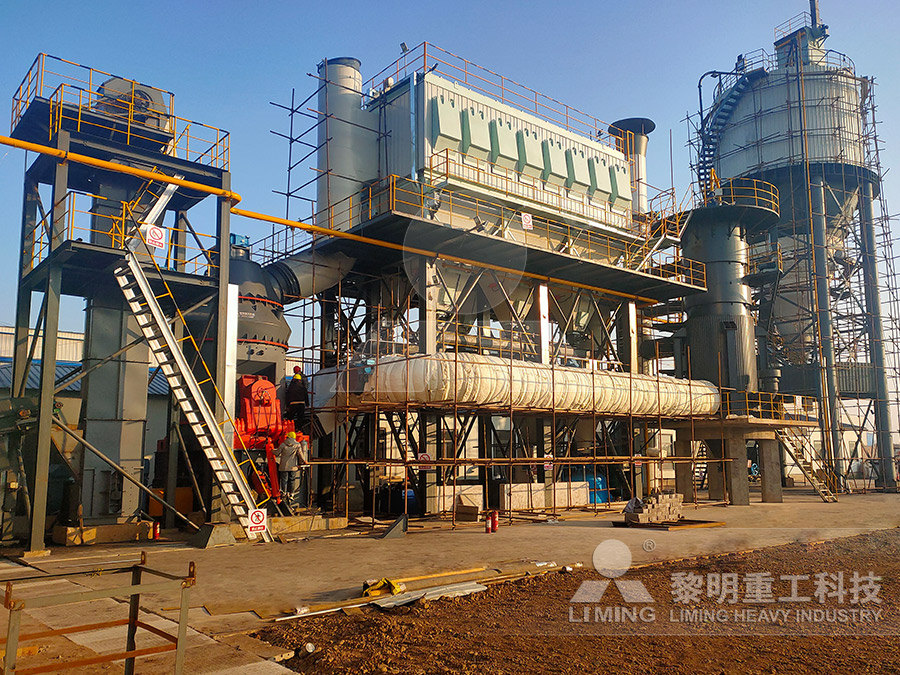
Coprocessing of Industrial Waste in Cement Kiln – A Robust
The production of cement is material and energy intensive and coprocessing of waste derived materials represents a common strategy to reduce the cost and environmental impact 2, 3, 4 Coupled withIn cement raw materials the lime component is generally represented up to an amount of 7680 0/o Therefore, the chemical and physical properties of this component are of decisive influence, when it comes to selecting a method of Raw materials used for Cement Production2008年10月31日 According to the ΘpH diagram of metal sulfides, it is known that the properties of FeS 2 are quite stable and theoretically require a pH of less than −2 to achieve optimal leaching, while FeS (PDF) Potential use of pyrite cinders as raw material in cement 2019年1月30日 No trial runs would be necessary for grant of authorisation for coprocessing of wastes in cement kilns: No trial runs would be necessary for grant of authorisation for coprocessing of wastes in cement kilns since MoEFCC has notified the Emission Standards for coprocessing of wastes in cement kiln vide GSR No 497 (E) dated 1052016 under the Coprocessing of Alternative Fuels and Resources in Indian Cement
.jpg)
Everything you need to know about Cement Kiln Dust Generation
The generation of waste kiln dust that cannot be reused can be a significant financial loss to the cement plant in terms of the value of raw materials, processing (quarrying, grinding, and storage), and energy usage during pyroprocessing, dust collection, and disposal2018年12月18日 This research paper describes mineralogical analysis technique of primary raw materials, auxiliary components for cement production, byproduct clinker and final product, cementCharacterization of raw materials and final product in the cement of raw materials and fuel, and produces substantial CO2 emissions The use of alternative fuels and raw materials in cement manufacturing can reduce the amount of conventional fuels and virgin raw materials needed, and thus reduce the overall environmental impact of the operations These alternative materials can be either waste orGuidelines for CoProcessing Fuels and Raw Materials in Cement In the building and construction sector, Portland cement (PC) is the main binder in the production of concrete Its production uses 16 tonnes of raw materials, principally quartz and limestone Summary of the main cement types, composition, and raw materials
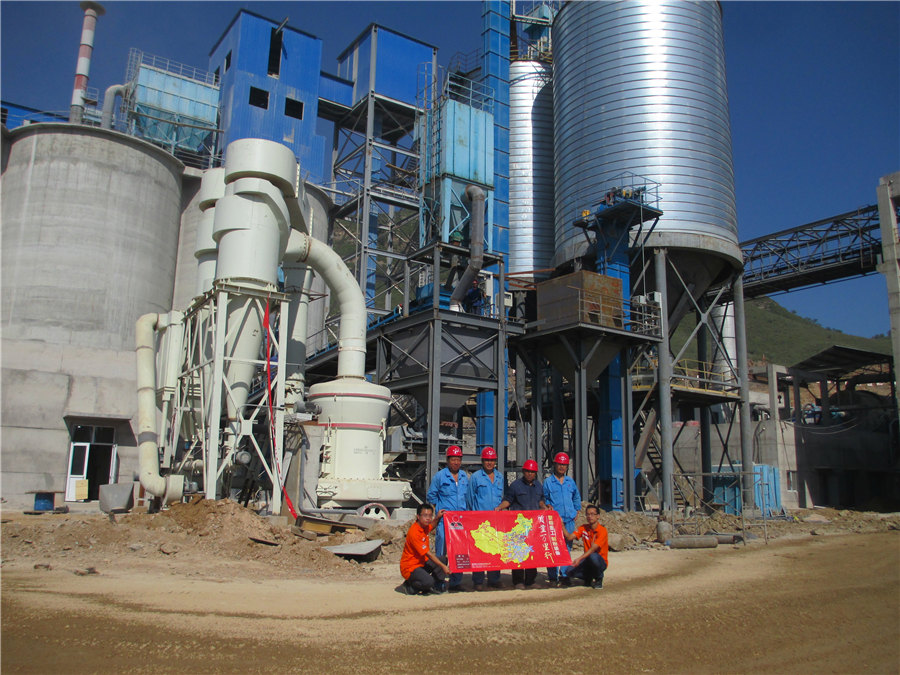
Portland Cement: Raw Materials, Manufacturing, Types and Quality Control
2023年1月15日 Quality Control of Portland Cement The stages in the manufacturing of Portland cement need to be closely monitored since they involve complex chemical reactionsPlant chemists are therefore, tasked with analyzing the raw materials fed into the kiln as well as the finished product