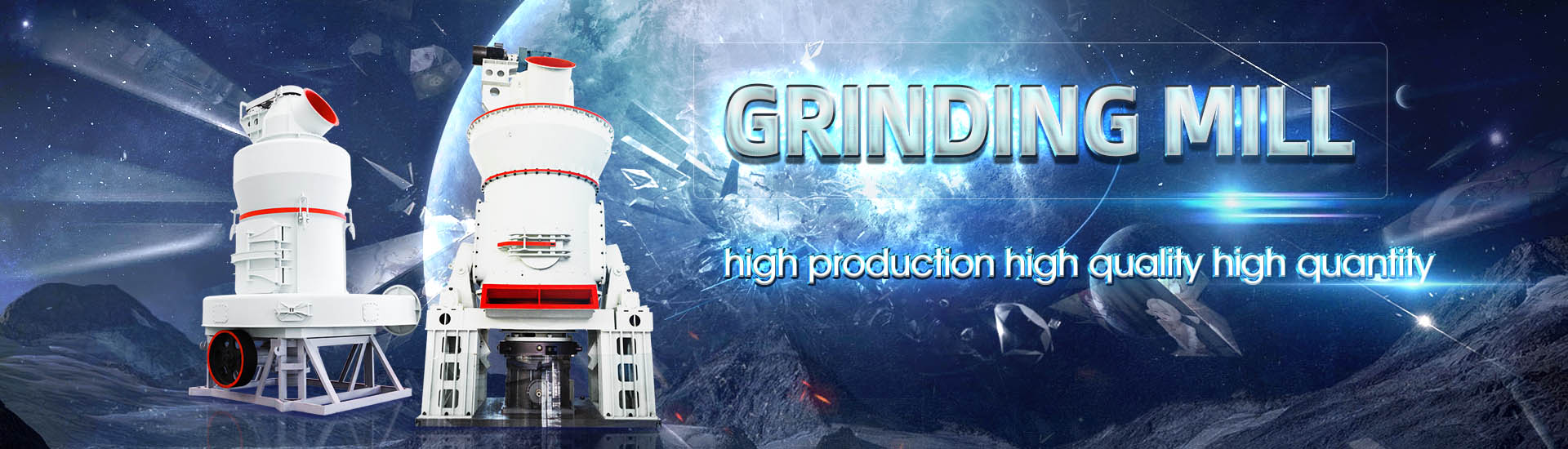
Powder mechanical ball mill
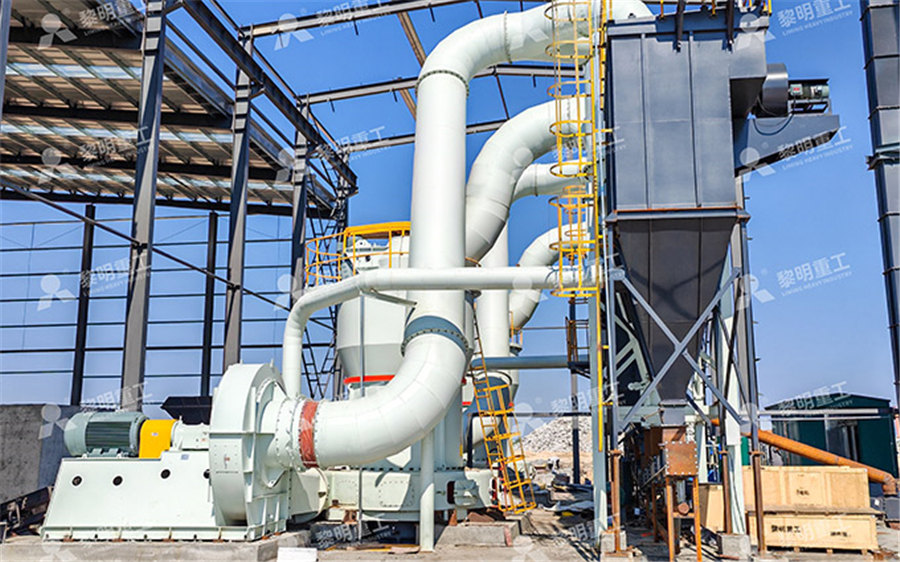
Ball Milling an overview ScienceDirect Topics
Ball milling is a grinding method that grinds nanotubes into extremely fine powders During the ball milling process, the collision between the tiny rigid balls in a concealed container will generate Mechanical alloying is a solidstate powder processing technique that involves repeated cold welding, fracturing, and rewelding of powder particles in a highenergy ball mill Originally developed Mechanical Alloying: A Novel Technique to Synthesize 2023年6月27日 This review found that ball milling is the best tool for reducing the particle size of recycled metal chips and creating new metal powders to enhance mechanical properties and novelty for(PDF) Producing Metal Powder from Machining Chips Mechanical alloying is a ball milling process where a powder mixture placed in the ball mill is subjected to high energy collision from the balls The process is usually carried out in an inert Introduction to Mechanical Alloying SpringerLink
.jpg)
Materials Development Using HighEnergy Ball Milling:
2022年6月17日 Highenergy ball milling (HEBM) of powders is a complex process involving mixing, morphology changes, generation and evolution of defects of the crystalline lattice, and formation of new phases2021年9月24日 Ball milling has evolved over the last five decades from a standard technique in mineral dressing and powder metallurgy, where it was primarily used for particle size reduction and powder blending, to its current Mechanical Milling: A Superior Nanotechnological Tool 2019年6月12日 Mechanical alloying (MA) is a simple, dry powder processing technique, which involves repeated welding, fracturing, and rewelding of powder particles by highly energetic Effect of HighEnergy Ball Milling on Structure and Properties of 2017年8月24日 Alloying of elemental blends achieved through highenergy ball milling (HEBM) is referred to as mechanical alloying (MA), which is a solidstate powder processing technique HighEnergy Ball Milling Parameters in Production of
.jpg)
Powder Milling an overview ScienceDirect Topics
2010年4月1日 Ball milling is the simplest, costeffective, fast, and ecofriendly method that is used to convert largesized particles to fine size particles through grinding This method can 2024年11月5日 This review comprehensively examines recent advancements in the synthesis and environmental applications of ironbased materials (IBMs), with a particular focus on the enhancements achieved through mechanical ball milling IBMs, including zerovalent iron (ZVI) and its composites, have garnered significant attention for their potential in environmental IronBased Materials Synthesized by Mechanical Ball Milling for A ball mill is a type of grinder containing various metal balls of different sizes that work on the principle of impact and attrition 44 Mechanical activation The ball milling process is carried out for approximately 100–150 h to obtain uniformsized fine powder In Ball Mill an overview ScienceDirect TopicsMechanical alloying (MA) is a powder process that consists of repeated cold welding, fracturing, and rewelding of powder particles in a highenergy ball mill This process is capable of synthesizing different types of nonequilibrium Mechanical alloying: a critical review Taylor Francis
.jpg)
Technical specifications and selection guide for ball mills
Motor Power: The motor power of a ball mill is an important factor in determining its grinding capacity Ball mills can be equipped with motors ranging from 10 kW to 500 kW or more, depending on the size and desired output of the mill Speed: Ball mills are usually operated at speeds between 60% and 70% of the critical speedHighEnergy Mechanical Ball Mill Machine (04L, 1L, 2L, 4L, 8L, 10L, 12L, 16L) quantity Add to cart SKU: PBM Categories: Ball Mill Machines, Ball Mill Tag: custom made available Too much powder – there will not be enough mediamedia contact to cause any milling Filling Too much powder – the media will not tumble effectivelyHighEnergy Ball Mill Machine Primet Lab2022年8月1日 AlSi10Mg2 wt%TiB 2 powder mixture and Al 2 O 3 grinding balls with the diameter of 6 mm and 10 mm (the total mass ratio of the two grinding balls is 1:1) was loaded in a 500 ml ceramic vial, where the balltopowder mass ratio was set as 2:1, and placed into QM series Planetary Mill to achieve a homogeneous powder mixture under an argon Powder preparation during ball milling and laser additive 2020年10月1日 Request PDF Silicon Powder Properties Produced in a Planetary Ball Mill as a Function of Grinding Time, Grinding Bead Size and Rotational Speed Mechanical milling is a promising route for Silicon Powder Properties Produced in a Planetary Ball Mill as a
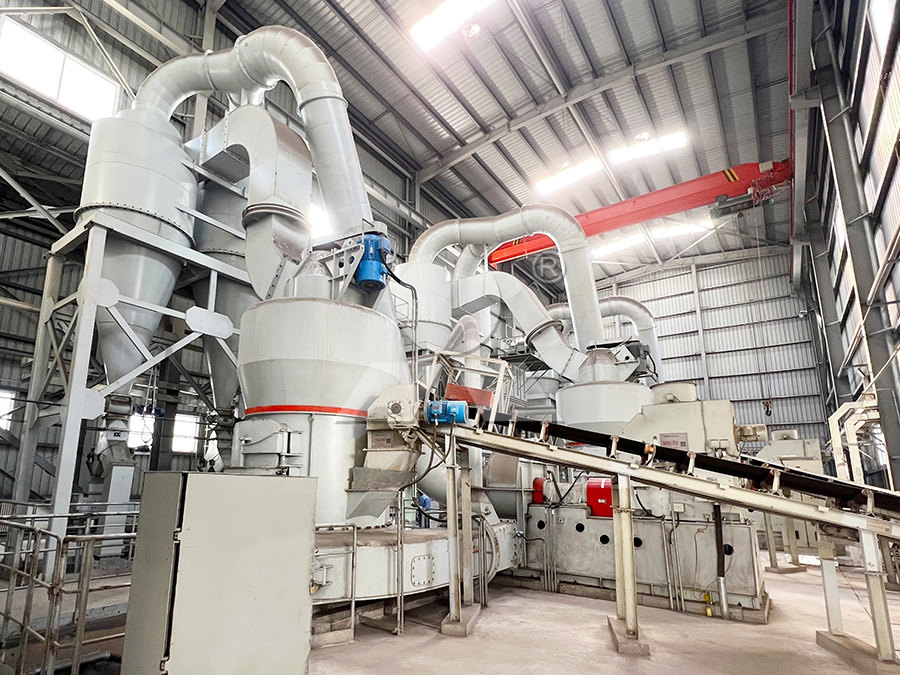
Ball milling: a green technology for the preparation and
The ball mill allows applying mechanical forces in the presence of chemical agents, therefore it represents an ideal method to combine chemical and mechanical actions to obtain CNCs Influence of reaction parameters on the depolymerization of H 2 SO 4impregnated cellulose in planetary ball mills, Powder Technol, The process consists of repeated weldingfracturingwelding of a mixture of powder particles in a highenergy ball mill The powder particles are trapped between the colliding balls during the milling and undergo deformation, welding, or fracture, depending on the mechanical behavior of the powder componentsMechanical Alloying an overview ScienceDirect TopicsMechanical alloying is a solidstate powder processing technique that involves repeated cold welding, fracturing, and rewelding of powder particles in a highenergy ball mill Originally developed about 50 years ago to produce oxidedispersionMechanical Alloying: A Novel Technique to Synthesize Research2021年12月1日 The effects of the balltopowder diameter ratio (BPDR) and the shape of the powder particles on EDEM simulation results and time in the planetary ball mill was investigated(PDF) Effects of balltopowder diameter ratio and
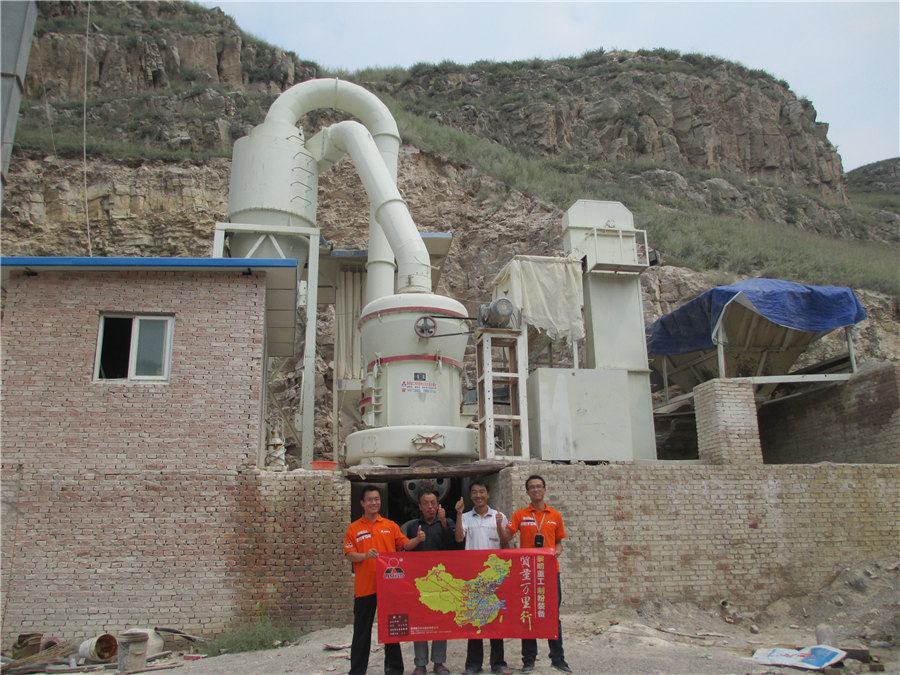
Mechanical alloying Wikipedia
Mechanical alloying is akin to metal powder processing, where metals may be mixed to produce superalloysMechanical alloying occurs in three steps First, the alloy materials are combined in a ball mill and ground to a fine powder A hot isostatic pressing (HIP) process is then applied to simultaneously compress and sinter the powder A final heat treatment stage helps remove The Planetary Ball Mill PM 100 is a powerful benchtop model with a single grinding station and an easytouse counterweight which mechanosynthesis, mechanical alloying and mechanocatalysis), or ultrafine colloidal grinding on a Planetary Ball Mill PM 100 RETSCH highest finenessHighEnergy Mechanical Ball Mill Machine (04L, 1L, 2L, 4L, 8L, 10L, 12L, 16L) quantity Add to cart SKU: PBM Categories: Ball Mill Machines, Ball Mill Guaranteed Safe Checkout Too much powder – there will not be enough mediamedia contact to cause any milling Filling Too much powder – the media will not tumble effectivelyHighEnergy Ball Mill Machine Landt InstrumentsA roller ball mill, also called a jar mill or rotary ball mill, is designed for fine grinding or mixing powder materials both for laboratory and 6L, 8L, 10L, 12L, 20L, 40L, 60L, 100L) HighEnergy Mechanical Ball Mill Machine (04L, 1L, 2L, 4L, 8L, 10L, 12L, 16L) Shop by Category Accessory for Battery Testers 5 5 products; Ball Mill 11 11 Roller Ball Mill Primet Lab
.jpg)
Introduction to Mechanical Alloying SpringerLink
Mechanical alloying is a ball milling process where a powder mixture placed in the ball mill is subjected to high energy collision from the balls The process is usually carried out in an inert atmosphere It is an alternative technique for producing metallic andBall Mill, Working Principle, Types, Parts, Applications and Advantages Ball Mill Grinding Machines: Exploring the Working Principle, Types, Parts, Applications, Advantages, and Recent Developments Ball mill grinding machines are widely used in various industries for the comminution of materials into fine powdersBall Mill Grinding Machines: Working Principle, Types, Parts 2017年8月24日 Alloying of elemental blends achieved through highenergy ball milling (HEBM) is referred to as mechanical alloying (MA), which is a solidstate powder processing technique involving the repeated deformation, fracture and welding of powder particles [1,2,3,4]This technique was originally developed to produce oxidedispersion strengthened (ODS) nickel HighEnergy Ball Milling Parameters in Production of However, some pyrotechnic applications such as flash powder do not use ballmill due to their sensitivity to impact Particle size can be reduced to as low as 5nm in high energy mills, In mechanical alloying, planetary ball mill is commonly employed because it involves very small quantities of precursor powdersBallmilling – Nanoscience and Nanotechnology I INFLIBNET
.jpg)
Mixing of Powder an overview ScienceDirect Topics
Ball mill diameter, media size and mill revolutions per minute (rpm) control the process of powder mixing and particle size reduction (Upadhyaya, 1998) For given mill size and media, too low an rpm extends the process time, whereas too high an rpm leads to poor cascading of media, leading to inefficient particle size reduction1995年2月24日 Note that the models proposed earlier for mechanical alloying in planetary mill [23, 24] ignored rolling ball motion as affecting the refinement or phase changes in the powder being processedPhysics of Mechanical Alloying in Planetary Ball Mill 2007年1月1日 welding, fracturing, and rewelding of powder particles in a highenergy ball mill Originally developed to produce oxidedispersion strengthened (ODS) nickel and ironbase(PDF) Mechanical alloying and milling / C 2019年5月20日 The manufacture and preparation of charge powders are the first and one of the most important stages of producing composite materials by powder metallurgy []Processing in planetary ball mills is often used to synthesize composite powders []The main parameters that characterize the efficiency of planetary mill processing are the input energy (fraction of the Simulation of the Energy–Force Parameters of Planetary Ball Mill
.jpg)
Mechanical Alloying an overview ScienceDirect Topics
Mechanical alloying is a solid state powder processing technique involving repeated cold welding, fracturing, and rewelding of powder particles in a highenergy ball mill [25] Mechanical alloying has been reported to have the capability of synthesizing a variety of equilibrium and nonequilibrium alloys starting from blended elemental or pre Specification of high energy ball mill: • Principle: Milling to be done using friction and repeated impact of shots and balls • Applications: Mechanical alloying, homogenization, size reduction, colloidal grinding These application are the domain of chemistry, civil engineering, recycling of wastes, metallurgy, mining, chemicals, ceramics, and oxides etcCRF Ball Milling NITK2020年4月21日 Besides the mill geometries there exist several easy to control and reasonably wellunderstood parameters unique to mechanochemical reactions As mentioned above, the rotational speed (planetary ball mill) or milling frequency (vibrational ball mill) are an easy to adjust parameter to control the energy input in the milled powderDirect Mechanocatalysis: Using Milling Balls as Catalysts2018年4月19日 The highenergy ball milling method was adopted to explore the influence of ball milling parameters, such as milling speed and additive amounts of process control agent (PCA) on tungsten powder The morphology and microstructure of tungsten powder in the process of refinement were characterized by fieldemission scanning electron microscope (FESEM), field Effect of Ball Milling Parameters on the Refinement of Tungsten Powder
.jpg)
Particle morphology control of metal powder with various
2021年12月1日 Mechanical milling involves repeated collision between the balls and the wall and results in deformation, welding, and fracture Many parameters, such as the type of miller, grinding media, rotation speed, milling atmosphere, balltopowder ratio, and process control agent can influence the stages of milling [6, 7]Many researchers were carried out for the 2020年9月1日 There are a number of parameters that govern various aspects of the ball milling process For example, the type of mill (eg, planetary ball mills, tumbler ball mills, vibratory tube mills, and attrition mill) decides the intensity of the kinetic energy of the ball transferred to the carbonaceous powderBall milling as a mechanochemical technology for fabrication of 2019年5月28日 The powder mixtures were mechanical alloyed in a highenergy ball mill and then pressed into cylindrical [Show full abstract] performs with a diameter of 40 mm under 150 MPa pressure in order (PDF) Design and Performance of Ball Milling for Powder 2012年6月1日 Hybrid HighPressure Roll Mill/Ball Mill Grinding – Powder T echnology, V ol 105, 1999, generating mechanical energy that aids in breaking bonds, Ball mills can grind a wide range of Grinding in Ball Mills: Modeling and Process Control
.jpg)
Silicon Powder Properties Produced in a Planetary Ball Mill as a
2020年1月15日 Mechanical milling is a promising route for production of submicron and nano sized silicon powders, but it is challenging to predict and control the product properties In this study a metallurgical grade silicon quality was milled in a planetary ball mill and the properties of the powder were investigated as a function of grinding time, grinding bead size (20 mm, 2 mm, by a fully loaded and an empty mill, respectively Based on this relationship, it is clearly seen that grinding time is one of the most important operation parameters for mechanical milling Em ¼ ðÞPnet=m †t ð1Þ In the work by Gotor et al [28], the power input to a planetary ball mill was reported to be strongly dependent onSilicon Powder Properties Produced in a Planetary Ball Mill as a 2021年8月26日 Industrial ball mills may be used to coarsely crush relatively large pieces of material, whereas labgrade ball mills are capable of finely milling glass to micron level and below Socalled “high energy” ball milling can even be used to reliably grind the material into nanoscale particles 4 Centrifugal MillGlass Milling Equipment and Techniques — MoSci Blog2015年9月21日 Flake silver powder with controllable particle size and specific surface area was prepared using planetary ball mill by varying milling parameters including milling time, revolution speed, and the weight ratio of balls to powder (BRP) Asprepared flake silver powder was characterized by laser particle analyzer, scanning electron microscope, Xray diffraction (XRD) Preparation of microsize flake silver powder by planetary ball mill
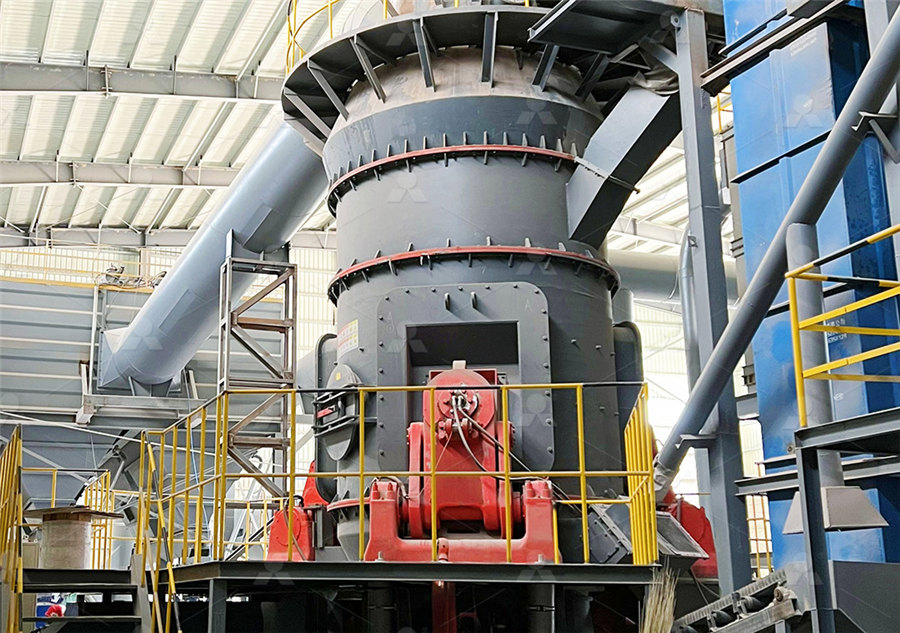
Particle morphology control of metal powder with various
2021年12月1日 Mechanical alloying (MA) is a solidstate powder processing technique that involves repeated cold welding, fracturing, and rewelding of powder particles in a highenergy ball mill [3], MA widely used technique in synthesizing nanocrystalline materials and alsoHigh energy ball milling can be applied anywhere from the laboratory scale of a few grams of powder to commercial setups WE’RE PIONEERING ADVANCED HIGHENERGY BALL MILLING PROCESSES MATSYS is a leader in high energy milling and has developed unique powder metallurgy capabilitiesLeaders in High Energy Ball Milling — Matsys2014年6月15日 The ball to powder ratio (BPR) is a processing parameter that is frequently used in both mechanical (ball) milling and mechanical alloying A number of recent studies provided the BPR as a Why the ball to powder ratio (BPR) is insufficient for describing 2021年9月24日 At the turn of the century, several ball mill manufacturers started to produce cryoball mills, which grind the desired materials under a flow of liquid nitrogen It is designed specifically for cryogenic grinding and crushing of tough or Mechanical Milling: A Superior Nanotechnological Tool for