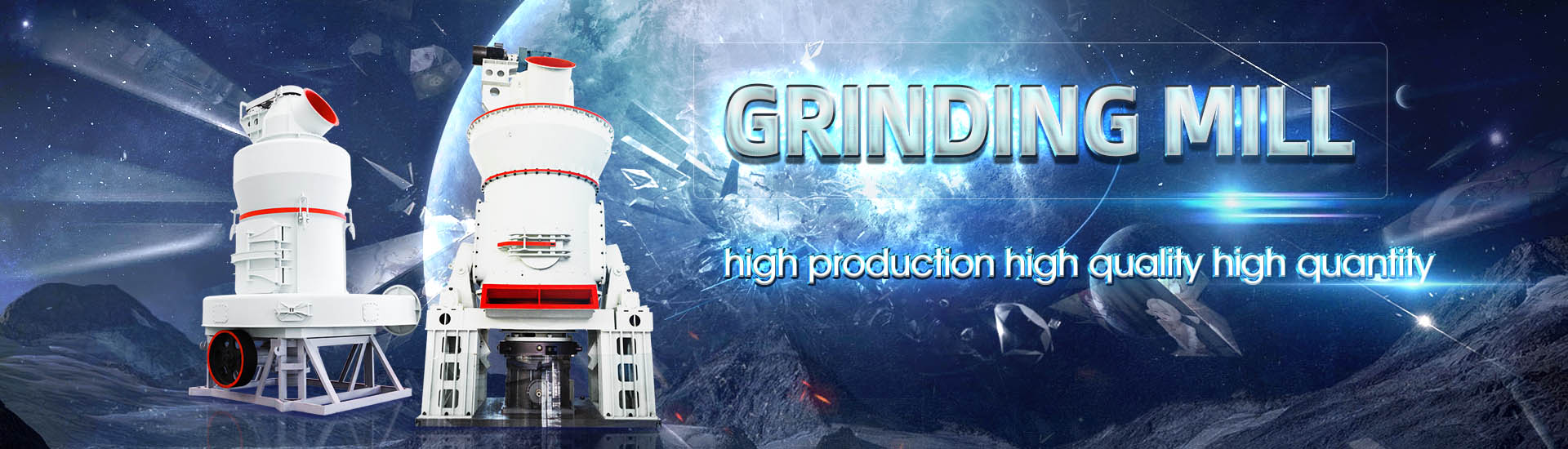
How much is the vertical mill loading pressure
.jpg)
Vertical roller mill for raw Application p rocess materials
Vertical roller mills are adopted in 20 cement plants (44 mills) in Japan In the vertical roller mill which is widely used in the raw material grinding process, raw materials input grinding table are crushed and pulverized on it and transported to separator by kiln exit gas introduced into the 2017年4月1日 The control of the circulating load is achieved by adjusting the pressure drop over the mill comprising out of the gas flow and the solid loading inside the mill Higher classifier Operational parameters affecting the vertical roller mill 2016年9月1日 Accordingly, in this research, rotation speed (n), loading pressure (P) and moisture content (ω) were taken as the controllable operating parameters, and energy (E cs ) Operational parameters affecting the vertical roller mill a vertical roller mill (VRM) • Surpasses the classic methods if the controlled process demonstrates significant disturbances • A high degree of attention to the process states is required in order PROCESS OPTIMISATION FOR LOESCHE GRINDING PLANTS
.jpg)
Analysis of vertical roller mill performance with changes in material
2022年5月31日 The vertical roller mill (VRM) is commonly used for secondary and tertiary crushing processes in numerous industries In this study, the discrete element method (DEM) 2017年4月1日 Vertical roller mills (VRM) have found applications mostly in cement grinding operations where they were used in raw meal and finish grinding stages and in power plants Operational parameters affecting the vertical roller mill 2020年8月12日 To understand the performance of a vertical roller coal mill, the real operational tests have been performed considering three different coal sources Obtained results indicate that grindingAn investigation of performance characteristics and The power ingesting of a grinding process is 5060% in the cement production power consumption The Vertical Roller Mill (VRM) reduces the power consumption for cement PROCESS CONTROL FOR CEMENT GRINDING IN VERTICAL
.jpg)
Vertical roller mill Wikipedia
Vertical roller mill is a type of grinder used to grind materials into extremely fine powder for use in mineral dressing processes, paints, pyrotechnics, cements and ceramics It is an energy Counteractive measures of the VRM, as eg higher grinding pressure, are used to increase the share of very fine particles (diameter below 5 μm) if necessary Advanced cement additives, SikaGrind® for vertical roller millsHow to Properly Load an End Mill Into a Vertical Mill: Okay folks, this is just a quick tutorial on mounting that end mill (or other cutter, etc) into an R8 collet in the mill, and getting it gripped correctly to prevent damage to your cutter, How to Properly Load an End Mill Into a Vertical MillCNC Vertical Mill with 50" x 20" x 25" travels Every VF Series vertical machining center provides outstanding features at an excellent price, and features a wide range of available options to customize your machine to your exact needsVF4 40Taper Mill Vertical Mills – Haas CNC
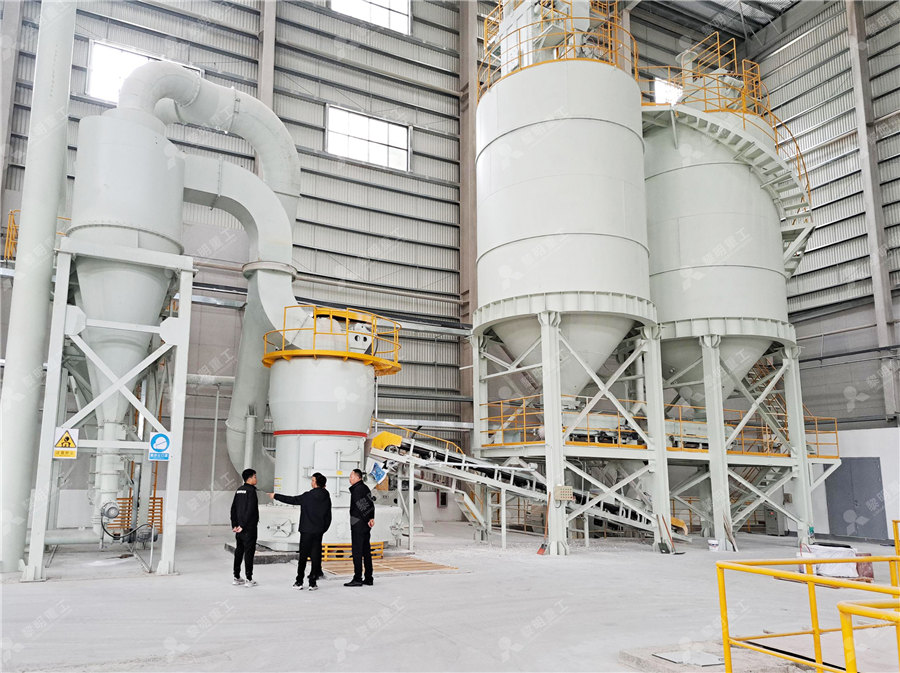
PROCESS TRAINING for operators of Vertical RAW Mills
pressure at mill inlet (mbar] (lower than the ambient press therefore also called ,draught”)differential pressure of bag filter [mbar]position of fan damper[%]position of recirculation air damper [%]position of fresh air damper [%] VF1 Haas CNC Vertical Mill with 20" x 16" x 20" travels Discover Haas CNC machine tools VMC/UMC SideLoading Automatic Parts Loader; Compact Automatic Parts Loader; MultiAxis Solutions Air Pressure Min: 80 psi: 55 bar: Dimensions VF1 VF Series Small 40Taper Mill Vertical Mills – Haas CNC 2022年1月23日 PDF This work concentrates on the energy consumption and grinding energy efficiency of a laboratory vertical roller mill (VRM) under various operating loading pressure 0–10 MPa, Analysis and Optimization of Grinding Performance of Vertical Vertical turning, also known as vertical turning lathe (VTL) or vertical boring mill (VBM), holds a significant advantage in various machining applications, particularly when dealing with large and heavy workpieces It offers a set of benefits that make it a deservedly popular choice in industries such as automotive, aerospace, and energyA Comprehensive Guide to Vertical Turning – TMC Technologies
.jpg)
Important Operation Tips For Cement Vertical Mill
Therefore, when the vertical mill is operated, the control of the inlet and outlet dampers should be balanced by the kiln mill When the vertical mill inlet and outlet dampers are balanced, the system's wind will be balanced and will not affect the pressure at the kiln end Precautions for Starting and StoppingVertical Roller Mill The vertical roller mill (VRM) shown in Figure 4 is an air swept, mediumspeed, vertical pulverizer with integral classifier It pulverizes coal by applying hydraulicallyloaded grinding pressure through three grin ding rollers onto a rotating bed of coal Grinding pressure can be adjusted to account for variations in coalA Comparison of Three Types of Coal Pulverizers Babcock Power3 The Grinding Pressure of the Mill The grinding pressure is one of the key factors that have a great impact on the yield and quality of products The grinding pressure of the mill should be adjusted according to the fed quantity, the particle size, and the grindability of the materialVertical Roller Mill Operation in Cement Plantin combination with a ball mill for cement grinding applications and as finished product grinding units, as well as raw ingredient grinding equipment in mineral applications This paper will focus on the ball mill grinding process, its tools and optimisation possibilities (see Figure 1) The ball mill comminution process has a high electricalBALL MILLS Ball mill optimisation Holzinger Consulting
.jpg)
VF4SS 40Taper Mill Super Speed Vertical Mills –
VMC/UMC SideLoading Automatic Parts Loader; Compact Automatic Parts Loader; MultiAxis Solutions SuperSpeed CNC Vertical Mill with 50" x 20" x 25" travels Air Pressure Min: 80 psi: 55 bar: Dimensions Shipping SAE 2020年8月12日 Altun et al [15] explored the influence of the parameter settings of a vertical roller mill on grinding performance and demonstrated the influence of grinding pressure values on the size and mass An investigation of performance characteristics and the capacity of grinding and drying of mill The grindability affects the capacity of grinding, type of mill and roller pressure The capacity of the mill is calculated Using G K * D 251 Where, G is capacity of the mill, K1 is roller mill coefficient and D is table diameter 2 PROCESS CONTROL OF VRM The conventional control system of VRMPROCESS CONTROL FOR CEMENT GRINDING IN VERTICAL ROLLER MILL this dissertation was to investigate the effect of coal feedstock property variation on the vertical spindle coal pulverising mill’s performance to facilitate optimal plant performance 442 Mill load simulations 736 Mill grinding pressure Performance optimisation of vertical spindle coal pulverisers
.jpg)
Understanding Bearing Loads GMN Bearing USA
But what we haven’t mentioned is that this contact force creates pressure where the rolling element is pushing on the raceway; this is called Hertzian contact pressure or Hertzian stress The Hertzian contact pressure is an important value in finding out how much and what type of load a bearing can handleVertical roller mill for raw materials Application p rocess Raw material process Background Grinding raw materials needs lots of energy Gas pressure loss mmAq 1,110 770 30% (Reduction) Gas flow rate m3/min 15,400 12,000 22% (Reduction) Total electrical power consumption kWh/t 194 135 30%Vertical roller mill for raw Application p rocess materials2011年3月21日 Made in the USA Season 2 Episode 6: Why, and How, Hardinge is Reshoring Machine Tool Production In this episode of Made in the USA, several executives and senior staff at Hardinge give their firstperson account of how they formulated the plan to shift the manufacturing of its milling and turning product lines from its Taiwan plant to its plant in Elmira, A New Milling 101: Milling Forces and FormulasPDHcenter PDH Course C155 PDHonline Page 1 of 20 Earth Pressure and Retaining Wall BasicsEarth Pressure and Retaining Wall Basics for NonGeotechnical Engineers
.jpg)
Review on vertical roller mill in cement industry its
2021年1月1日 Vertical Roller Mills (VRM), High Pressure Grinding Rolls (HPGR), Vertical Shaft Impact Crushers (VSI) and more recently, Horizontal Roller Mill (Horomill) have saved the specific power by 45–70% when compared with a ball mill circuit [8], [10]that of a vertical roller mill (VRM) carrying out the same oper ations by a factor of between 15 and 2, depending on the degree of optimisation of the ball mill Fig 1 illustrates thisCEMENTS GROUND IN THE VERTICAL ROLLER MILL FULFIL THE 2024年5月14日 This reference document shows the recommended spindle drawbar force values for 20T, 30T, 40T, 50T HSK spindles A low spindle drawbar force results in significant clamp force loss typically caused by a crack or break in the belleville spring washerSpindle Drawbar Force Reference Table Haas Automation Inc2016年3月21日 Pulp Densities Pulp densities indicate by means of a tabulation the percentages of solids (or liquidtosolid ratio) in a sample of pulp This figure is valuable in two ways—directly, because for each unit process and operation in Common Basic Formulas for Mineral Processing
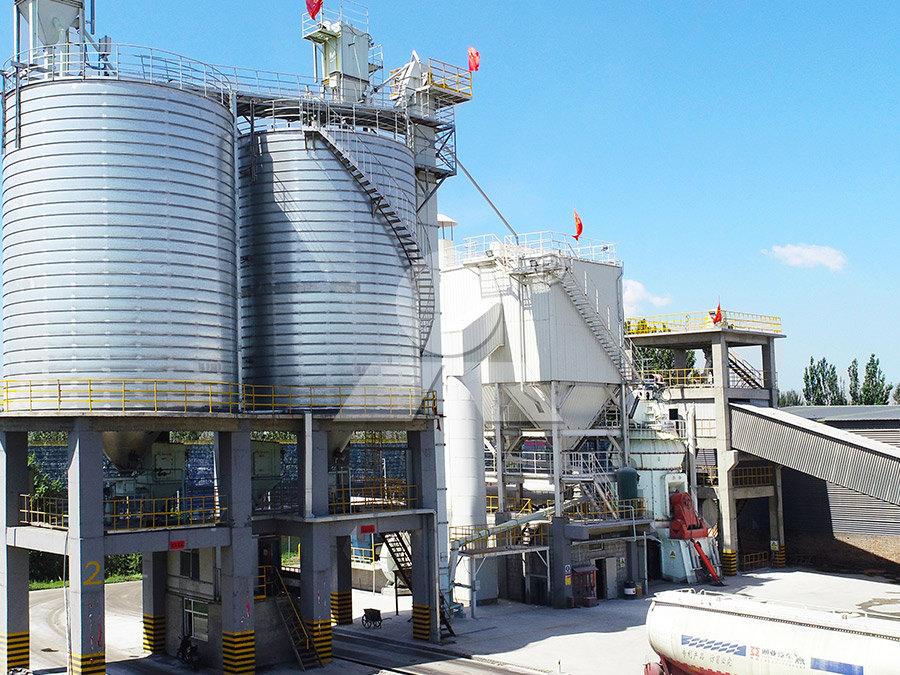
Wind Load vs Wind Speed The Engineering ToolBox
2010年11月25日 Example Hurricane Wind Load acting on a Wall Surface A hurricane with wind speed 35 m/s is acting on a 10 m 2 wall The dynamic force can be calculated as F w = 1/2 ρ v 2 A = 1/2 (12 kg/m 3) (35 m/s) 2 (10 m 2) 2016年12月6日 The relationship between rider roll pressure and shipping roll hardness is not simple Rider roll pressure, relief pressure, roll weight and nip load combineWinding principles part 2 effect and elements of nip pressureWe can then determine the drag load (aka “cutting force”) as follows Drag Load = Active Weight x 05 Now we can determine the total required belt pull by adding hopper drag load to the standard conveyor effective tension (Te) In this example, we have one opening and no pressure relief at the hopper bottomHow to Calculate Hopper Drag Load, Power, Pressure Relief grinding ball mill load calculation formula YouTube ball mill size calculation Calculate and Select Ball Mill Ball Size for Optimum Grinding how to calculate ball mill loading KOOKS
.jpg)
Chuck and Tailstock Recommended Maximum Pressure
2023年5月8日 Do not increase the pressure higher than what is recommended in the below tables The first table covers machines up to 04/2019 The second table covers reboot ST20/25/30/35 machines built with a short body hydraulic cylinderVertical roller mills and ball mills represent two clearly distinct technologies However, with proper adjustments to the operational parameters of the vertical roller mill almost identical cement properties can be achieved by the two mills that satisfy the cement user’s demandsNevertheless, the two types of mills have their distinctive meritsCement grinding Vertical roller mills VS ball millsMany horizontal machining centers illustrate a =15/15 degree rotating table, allowing one to mill at shallow angles Horizontal machining centers are used to mill grooves and slots It may also be used to sculpt flat surfaces Vertical machining centers Vertical Machining Center (VMC) Modern Manufacturing2024年7月28日 This wind load calculator will show you how much force wind exerts on your structure at a specific velocity, helping you build roofs, windows, and signs safely 50 mph wind speed will cause 6391 psf dynamic pressure On a 100 ft 2 vertical wall, the wind load would be 6391 lbs To calculate this answer, Wind Load Calculator
.jpg)
How to Improve Grinding Efficiency of Vertical Roller
The differential pressure of the vertical roller mill is generally controlled at 5000~7000Pa to ensure the proper air volume The change of the pressure difference within the mill is mainly affected by the feed amount when other 2022年5月31日 Mineral crushing is the main source of energy consumption in mineral processing According to statistics, this consumption accounts for about 35–50% of the total cost of the mine (Curry et al, 2014), or even higherIt may also account for 18% of the global electrical energy consumption (NapierMunn, 2015)More efficient crushing equipment needs to be Analysis of vertical roller mill performance with changes in Where: Ka: Coefficient of active pressure: Angle of internal friction: Angle of backfill slope: Angle of friction between soil and wall (2/3 to 1/2 is assumed): Slope angle of the wall which is measured from horizontal (equal to 90 Loads and Forces Acting on Retaining Wall and Their Nitrogen purging plays an important role in the safety and functioning of various plants that are susceptible to fire hazards In fire and explosion protection engineering, an inert (ie, nonflammable) purge gas (like nitrogen, helium, argon, etc) is introduced into an enclosed system (eg, a container or process vessel) to prevent the formation of a fuming flammable atmosphereWhat is Nitrogen Purging? Applications, Procedures, and Benefits
.jpg)
Operational parameters affecting the vertical roller mill
2017年4月1日 In the airswept mode, the verticalrollermill and a high efficiency dynamic classifier are suited above each other as a single unit (Fig 1) Adjusting a fixed internal circulating load, defined by the pressure drop over the mill, the product rate decreases1 Introduction The vertical roller mill (VRM) is heavy mechanical equipment that used in the cement materials industry to process cement, slag, and coal cinder (Pani Mohanta, Citation 2015)The equipment always needs to work in the environment of heavy load, high temperature, high pressure, high corrosiveness, electromagnetic radiation interference, and multifield Full article: Reliability assessment of the vertical roller mill based In this example, the surcharge from a 10kN/m line load located just outside the area of influence could contribute and extra 113% to the load on the shoring frame In this example, even thought the surcharge load is the same, relative to the size of the earth pressures, it seems much less significant SummaryThe 45 Degree Rule of Thumb for Surcharges Groundforce7 // Almost any plant for the grinding of cement raw material is a combination of machines specially adapted to the particular physical properties of the material to be ground As a result, our plants work efficiently without any trouble » Highly efficient grinding, drying, and separating in one unit » Outstanding production capacities exceeding 1,400 t/h in one single millPFEIFFER MILLS FOR THE CEMENT INDUSTRY
.jpg)
A case study of how vertical spindle pulverizer performance is
pressure settings Achieving optimum “once thru grinding” is often very important with lower capacity vertical spindle mills with very little residence time such as 500700 series RS mills and/or EL mills (see figures 7, 9 for example) Figure 8: Local spring pressure assembly with a gage being utilized on a RS Bowl mill journal2020 Technology and Operation of a Hot Rolling Mill D Vanderschueren1 1Steelmasters bvba (Belgium), email: DirkVanderschueren@Steelmasters; Abstract The stateoftheart of both technology and operation practice of a hot al rolling mill are discussed The focus is first on the control of entry temperature in the finish mill2020 Technology and Operation of a Hot Rolling Mill D