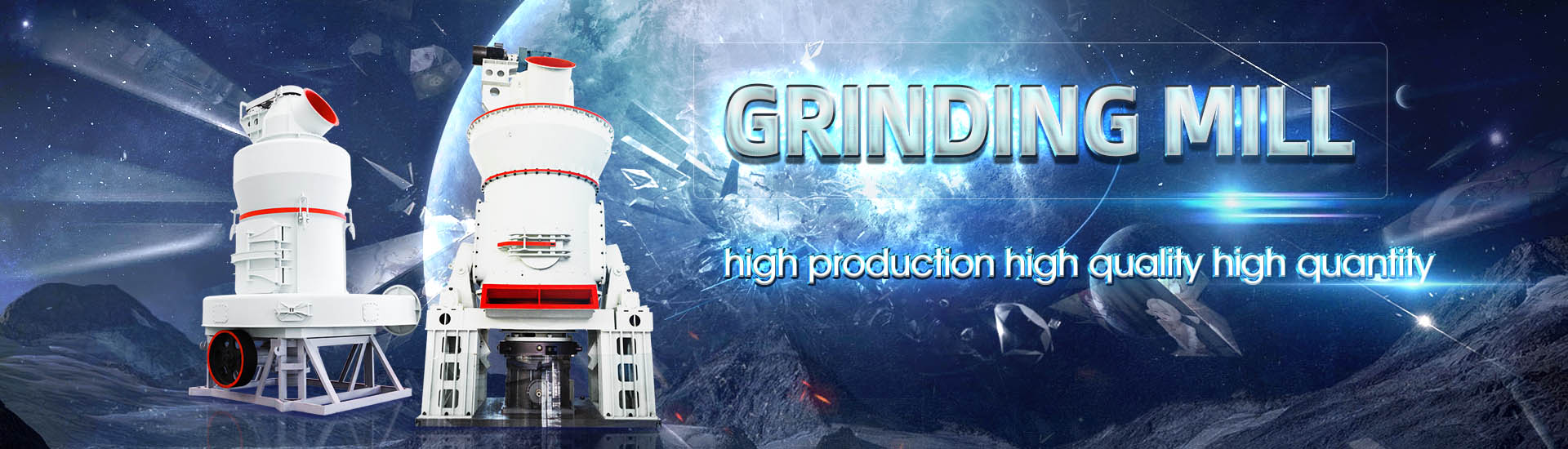
Desulfurization lime process
.jpg)
Dry Flue Gas Desulfurisation Technology ScienceDirect
2000年7月31日 The primary dry FGD technologies employ either a spray drying process or a circulating fluid bed (CFB) process The spray drying process typically uses slaked lime Limestone and lime are predominantly utilized in the desulfurization process within circulating fluidized bed boilers at the forefront of furnaces Under hightemperature conditions, limestone Recent advances in process and materials for dry desulfurization of In dry scrubbing, lime is injected directly into flue gas to remove SO 2 and HCl There are two major dry processes: “dry injection” systems inject dry hydrated lime into the flue gas duct and Flue Gas Desulfurization Lime2024年5月6日 This alternative desulfurization process involves an introduction of a lime powder desulfurization agent into 25ton molten cast iron by employing inert nitrogen gas as transport Industrial Ecotechnological Assessment of Lime as a Sustainable
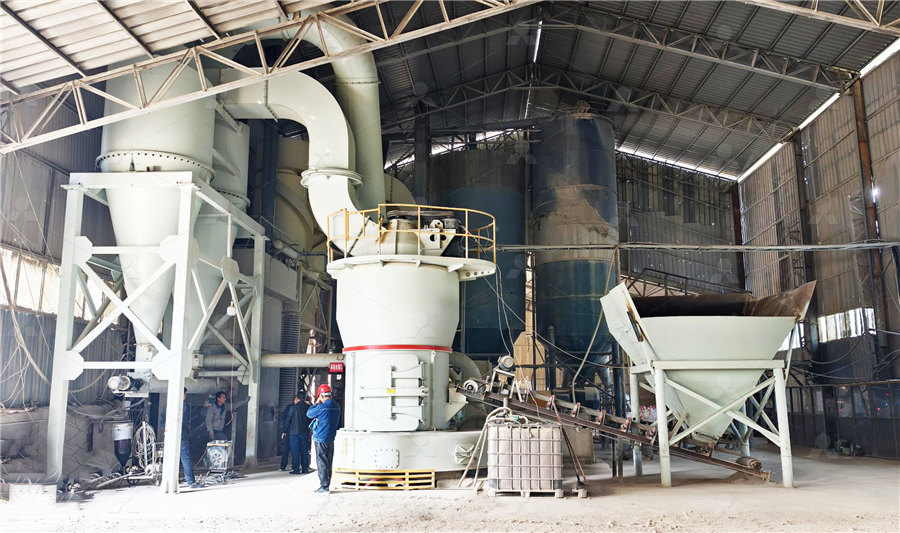
Wet flue gas desulphurisation procedures and relevant
2014年7月1日 Wet procedure with the most widespread industrial application, lime/limestone process, has been described in detail In addition, the procedures with chemical and physical absorption and2001年5月19日 A detailed process model of the wet limestone flue gas desulfurization system has been presented This model can be used to calculate indispensable parameters for Model of the Wet Limestone Flue Gas Desulfurization Process for 2002年1月1日 Data reflect that most wet limestone and LSD installations appear to be capable of ∼90% SO2 removal Advanced, stateoftheart wet can provide SO2 removal in excess of 95% Generating capacity (MWFlue Gas Desulfurization: The State of the Art [J]2019年7月10日 of the mediumtemperature desulfurization process Kinetics are an important consideration in the design of the desulfurization unit of a power plant and henceforth will be the subject of the present study Kinetic parameters like SO2 breakthrough time, total lime conversion, sulfur yield and sulfur selectivity are chosen as performance indicatorsKinetic Evaluation of Lime for MediumTemperature Desulfurization
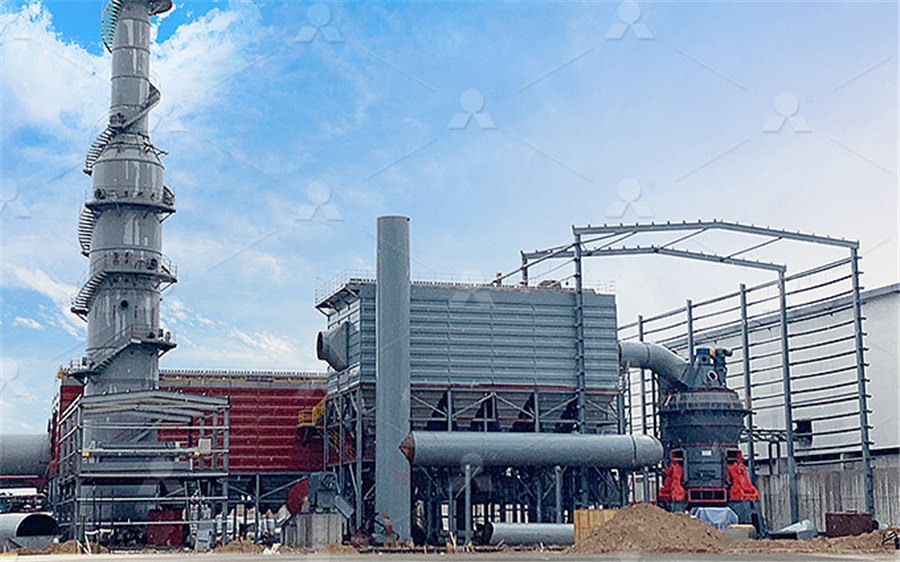
Comparison of flue Gas Desulfurization
2018年10月15日 lime, the desulfurization efficiency is h igher than that of lime method Its tower of lime process, and has the advantage of high absorption efficiency of sodium alkali method2019年12月1日 According to the US Energy Information Administration's statistics, in the 2006–2016 period, approximately 42% of the electricity consumed in the USA was produced by coal combustion (US Energy Information Administration, 2018)The coal combustion process generates various types of residues such as fly ash, bottom ash, boiler slag, flue bed Recent advances in flue gas desulfurization gypsum processes 2013年4月1日 The HIsarna ironmaking process is a break through process for the production of liquid hot metal The process produces liquid iron directly from iron ore and coal fines, without the need for ore Desulfurization strategies in oxygen steelmaking ResearchGate2024年5月6日 This study comprehensively assesses the ecotechnological consideration and perspective of implementing a limebased desulfurization process in the cast iron industry to replace the utilization of magnesium partially By adopting an injection process to introduce the lime powder into molten cast iron, this research elucidated that the new alternative concept Industrial Ecotechnological Assessment of Lime as a Sustainable
.jpg)
Wet Flue Gas Desulfurization (FGD) ARCOR Epoxy
The LSFO process with throwaway byproduct is the standard process against which other FGD processes are compared Wet FGD Performance Wet scrubbers are usually designed for efficiency of 80 to 95 percent SO 2 removal Additives (eg, magnesiumenhanced lime or adipic acid) improve the process efficiencyWet scrubbing primarily uses magnesiumenhanced lime (containing 38% magnesium oxide) because it provides high alkalinity to increase SO 2 removal capacity and reduce scaling potential Comparing Lime and Limestone SO 2 Wet Scrubbing Processes More than ninety percent of US flue gas desulfurization (FGD) system capacity uses lime or limestoneFlue Gas Desulfurization LimeControl and Treatment of Air Emissions Shahryar Jafarinejad, in Petroleum Waste Treatment and Pollution Control, 2017 515 FlueGas Desulfurization Fluegas desulfurization (FGD) is a scrubbing technique that uses an alkaline reagent (typically a sodium or calciumbased alkaline regent) to remove SO 2 from flue gas (TriState Synfuels Company, 1982; Tilly, 1983; FlueGas Desulphurization an overview ScienceDirect TopicsThe semidry desulfurization process consists of injecting a pulverized suspension of slaked lime into the flue gas flowing through the reactor, where calcium hydroxide reacts with SO 2 in flue gas The temperature of the process is 15–20°C higher Desulphurisation an overview ScienceDirect Topics
.jpg)
Desulphurization of Hot Metal IspatGuru
2013年10月16日 Cost of reagent – Magnesium is a costly reagent than the lime Further, the KR process uses lime of lower quality while the lime needed for the coinjection process is of higher quality It is estimated that for the MMI process and the coinjection process an amount of 05 kg/tHM (kilogram per ton of hot metal) magnesium is injectedEPACICA Fact Sheet Flue Gas Desulfurization1 Name of Technology: Flue Gas Desulfurization (FGD) Wet, Spray Dry, and Dry Scrubbers Type of Technology: Control Device absorption and reaction using an alkaline reagent to produce a solid Air Pollution Control Technology Fact Sheet US EPA2002年1月1日 This paper presents a comprehensive review of the state of the art in flue gas desulfurization (FGD) technologies for coalfired boilers The MEL process is a variation of the lime process inFlue Gas Desulfurization: The State of the Art [J]2022年1月3日 About the author: Cristina Tuser is associate editor of WWD Tuser can be reached at [ protected] What is the Flue Gas Desulfurization Process? Flue gas desulfurization is the process of removing sulphur What is Flue Gas Desulfurization? Wastewater Digest
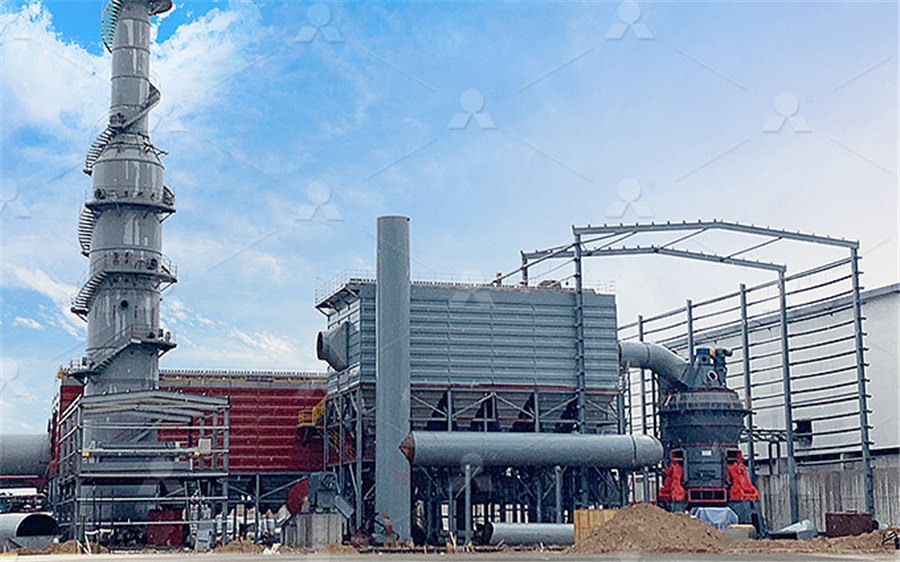
Lime / Limestone Wet Scrubbing System for Flue Gas Desulfurization
containing a sorbent The most common sorbents are lime (Ca[OH] 2) and limestone (CaCO 3) Rosemount Analytical pH equipment is used to control the feed rate of these chemicals PROCESS After fly ash removal, the flue gas (seen in Figure 1) is bubbled through the scrubber, and the slurry is added from aboveThe lime or limestone reacts with the 2021年3月17日 The desulphurization process in a lime spray dryer is a complex process, involving a series of subprocesses, as shown in Eqs 23–30 The ionic reactions are considered instantaneous, with the ratecontrolling step being either the gas diffusion or solid dissolution rate (Hill and Zank 2000)Spray drying absorption for desulphurization: a review of 2021年11月1日 Flue gas desulfurized gypsum mainly comes from thermal power plants, smelters, and largeenterprise boilers, and contains industrial byproducts produced through a wet desulfurization combustion process, where SO 2 gas and lime slurry react under strong oxidation conditions The main component of this gypsum is calcium sulfate dihydrate, which also Production and resource utilization of flue gas desulfurized In the presented work, desulfurization process parameters and the lime utilization ratio were correlated by datadriven technique, and a convolutional neural network was applied to predict the lime utilization ratio in the Kambara Reactor (KR) desulfurization processA convolutional neural networkbased model for predicting lime
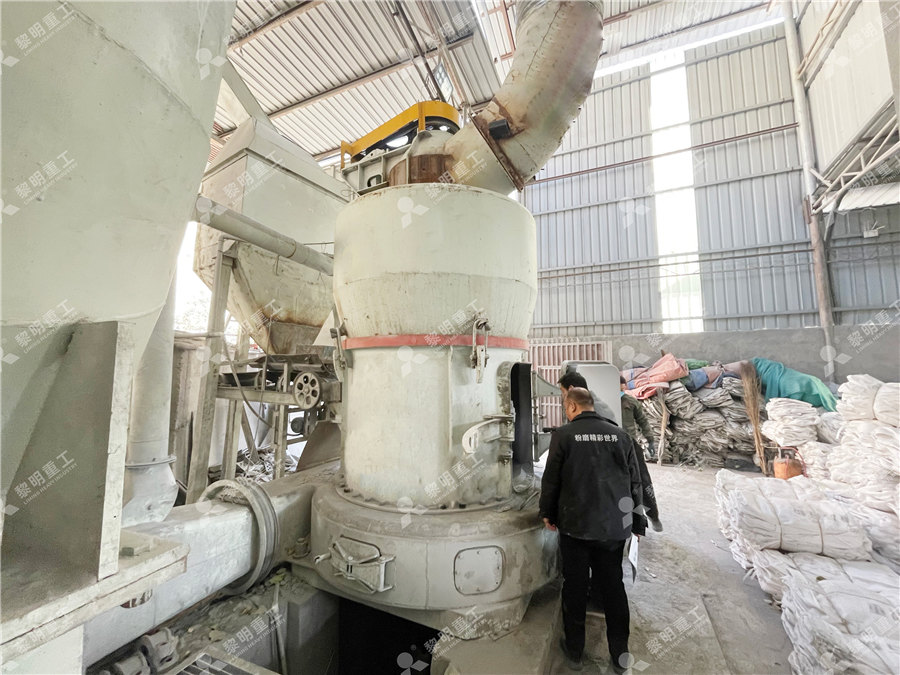
Insight into the magnetic lime coagulationmembrane distillation
2020年6月5日 The lime solution was applied for absorption of contaminants such as SO 2, NO x, HCl, particulates, heavy metals, organic matters (OMs) in the fluegas These contaminants accumulate and eventually reduces the efficiency of desulfurization process, accelerate corrosion, and reduce the quality of gypsum2024年9月1日 Circulating fluidized bed flue gas desulfurization (CFBFGD) process has been widely applied in recent years However, high cost caused by the use of highquality slaked lime and difficult operation due to the complex flow field Desulfurization characteristics of slaked lime and regulation 2024年9月1日 Circulating fluidized bed flue gas desulfurization (CFBFGD) process has been widely applied in recent years However, high cost caused by the use of highquality slaked lime and difficult operation due to the complex flow field Desulfurization characteristics of slaked lime and regulation 1 Introduction Hot metal desulfurization serves as the main unit process for removing sulfur in blastfurnacebased steelmaking Hot metal desulfurization is commonly conducted in a ladle or a torpedo car, 1 using a desulfurization A Review of Modeling Hot Metal Desulfurization
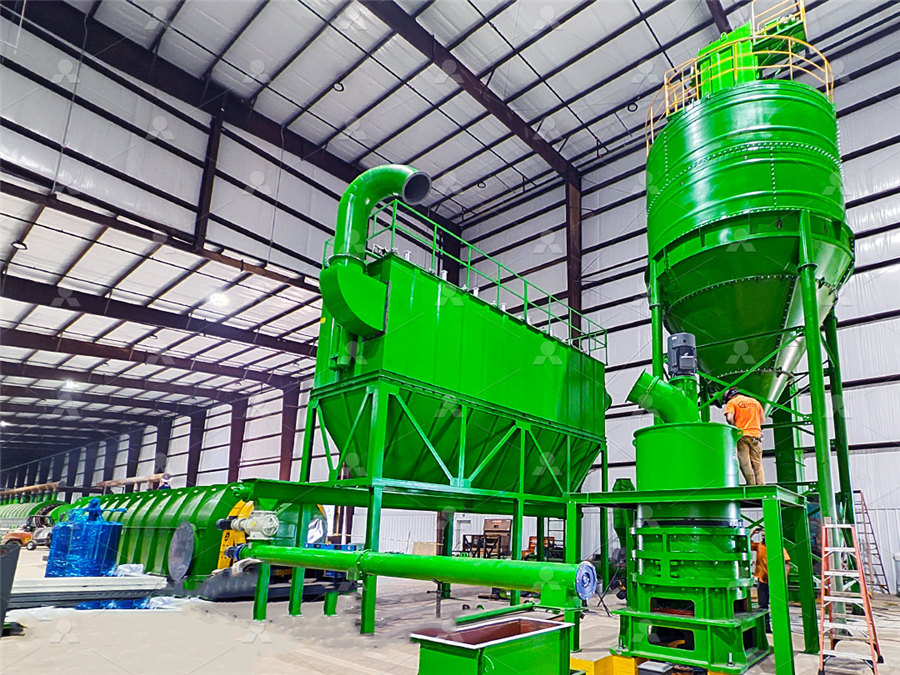
Recent advances in flue gas desulfurization gypsum processes
Flue gas desulfurization gypsum (FGDG) is an industrial byproduct generated during the flue gas desulfurization process in coalfired power plants Hydrated lime – CaSO 3: Semidry FGD process: Neathery (1996) Hybrid pollution abatement system (HYPAS) sorbent injection: Dry mixture of lime and recycled solids:2024年8月1日 Recently, slaked lime with increased specific surface area has been found to have significantly improved dry desulfurization performance [16], [32], and the specific surface area of the slaked lime product is always required to be larger than 38 m 2 /g for the technical application of dry desulfurization process in industryThe effect of magnesium content and roasting process on the Numerous methods have been applied in the desulfurization process including wet scrubbing by means of slurry of alkaline sorbent, commonly lime or limestone, or seawater, spraydry scrubbing, SNO X desulfurization, etc Desulfurization efficiency and energy consumption during the process are two main factors when choosing the appropriate Desulfurization an overview ScienceDirect Topics2019年3月13日 PSO with a penalty function algorithm is applied to improve the economy of desulfurization process Aimed at the minimization of operating cost, the operating parameters, including lime slurry pH, temperature, lime slurry density, and number of circulating pumps in operation, are optimizedFull article: Modeling and optimization of wet flue gas desulfurization
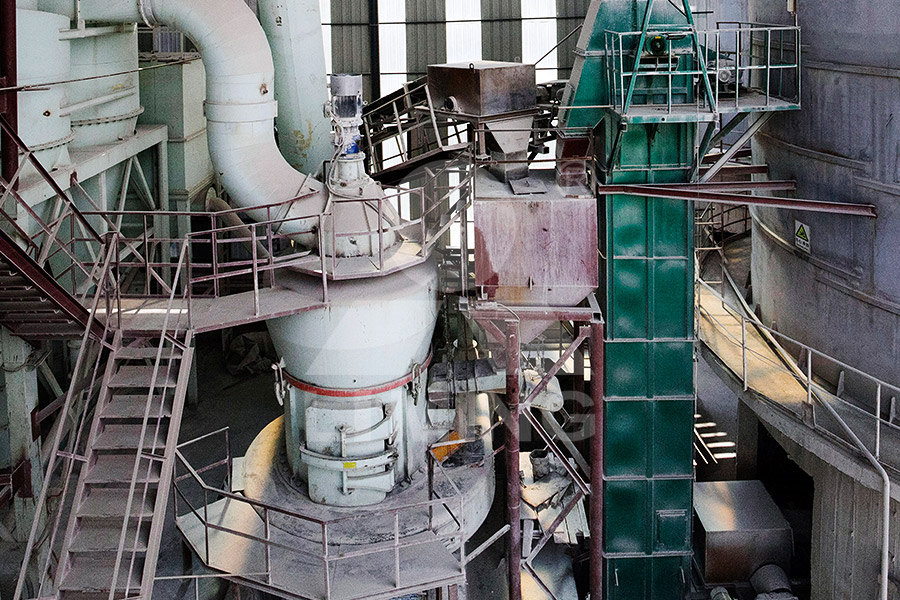
11 Flue Gas Desulfurization Air Quality and Stationary Source
Read chapter 11 Flue Gas Desulfurization: Air Quality and Stationary Source Emission Control Read chapter 11 Flue Gas Desulfurization: Limestone process Lime process $ $/kw $ $/kw Coalfired power units 90% SO 2 removal; onsite solids disposal 200 MW new, 35% sulfur 30 13,031,000 6522022年7月11日 Due to the most recent environmental requirements, wide desulfurization has become an increasingly important way to obtain ultraclean fuels for transportation of less than 15 ppmw of sulfur, such (PDF) Desulfurization techniques process and future challenges 2021年4月7日 2Lime addition The major S removal takes place with the help of lime Lime is generally added in batches The slag has to be killed or the potential of O has been to be reduced for effective S removal in the form of CaS The killing of slag is brought about by the addition of aluminium cubes owing to its higher surface areaDesulphurization of Steel Metal World InsightLime and Lime/Limestone FGD Systems Planned or Under Construction in US Utilities as of June 1980 Process, utility, and station3 FGD units Size(MW) No Gas volume treated11 (1,000stdft3/min) Fuel Type % S02 removal (design) Startup date Lime: Arizona Public Service: Four Corners 4 (R) 755 NA 1,510 Coal 075 NA 1982 Four Corners 5 (R) 755 NA 1,510 Coal Summary Report, Sulfur Oxides Control Technology Series: Flue
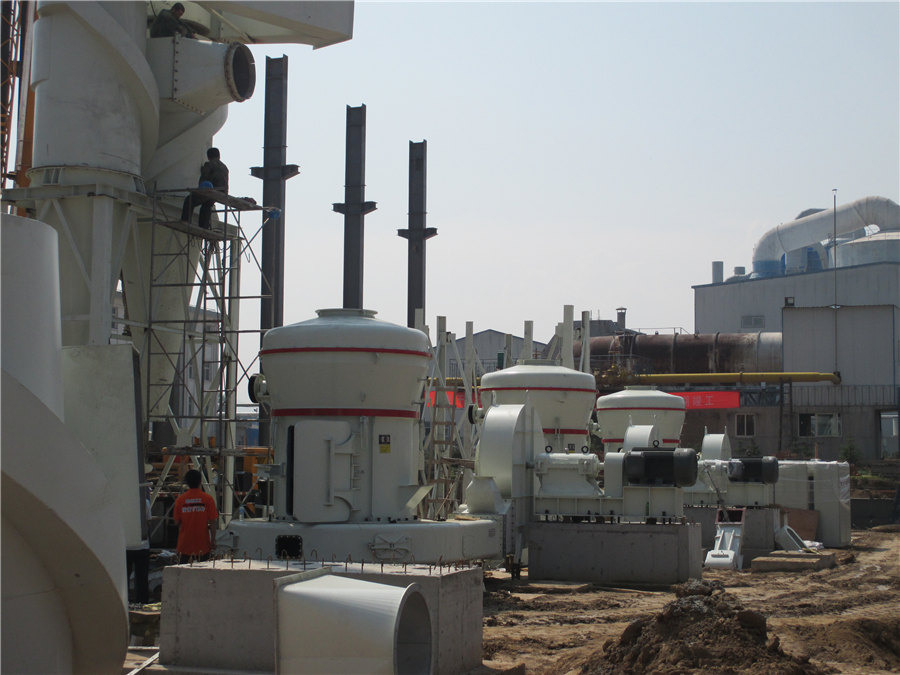
Water utility lime sludge reuse for flue gas desulfurization
We have recently evaluated the feasibility of utilizing lime sludge in the flue gas desulfurization process of coalfired power plants1,2 A supplydemand evaluation showed that the water treatment plants in the US generate approximately 32 million tons of lime sludge per year at an estimated disposal cost of approximately US$90 millionRehan Jamil, Li Ming, Irfan Jamil, and Rizwan Jamil ISSN : 20289324 Vol 4 No 2, Oct 2013 289 Fig 3 3rd Generation of wetProcess Limestone/LimeGypsum Flue Gas Desulfurization System SchematicApplication and Development Trend of Flue Gas Desulfurization Flue gas desulfurization (FGD) systems using lime or limestone as the chemical reagent are widely used throughout the world for SO 2 emissions Efficient Ammonia Desulfurization Process Schematic:AmmoniaBased Flue Gas Desulfurization Power EngineeringThe calciumbased desulfurization process, which has been transformed into a standard practice among European iron and steelmakers [15], could also be one promising sustainable alternative for the cast iron industry Extensive research has been carried out to optimize the application of the limebased desulfurization process due to its cost andIndustrial Ecotechnological Assessment of Lime as a Sustainable
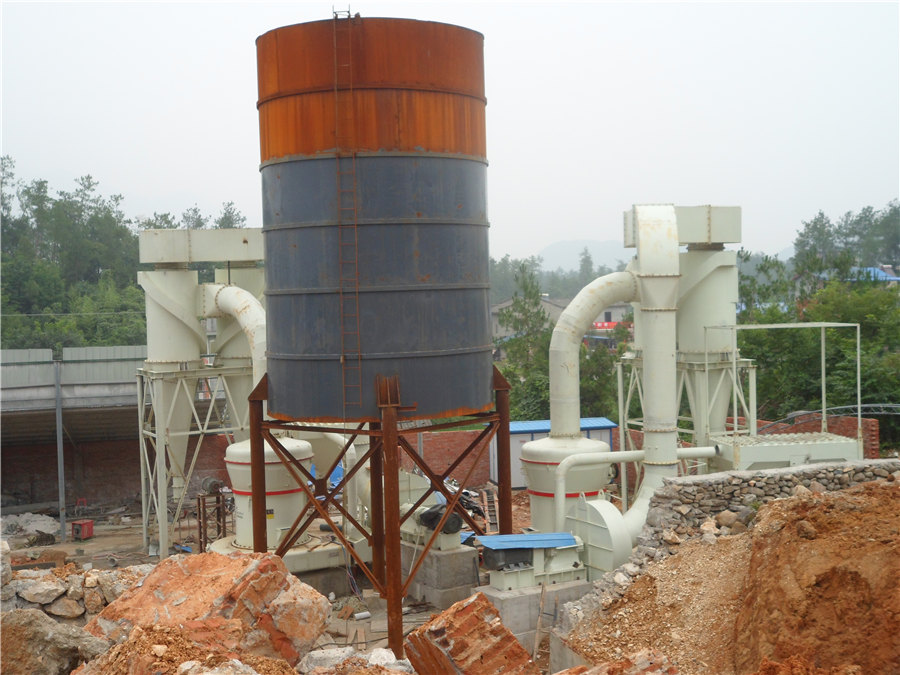
Integrated Assessment of the Environmental and Economic Effects
Request PDF On Apr 20, 2021, Xiao Xia and others published Integrated Assessment of the Environmental and Economic Effects of Resource Utilization Process for Lime/Gypsum Flue Gas 2023年10月31日 Kinetic characteristics of desulfurization reactions can be described by the twofilm theory In the kinetic process of desulfurizer desulfurization, the kinetic process can be divided into (1) The movement of [S] from the molten steel through the boundary layer on the molten steel side to the slag–steel interface; (2) (O 2−) in the slag moves from the top slag through the Kinetic Model of Desulfurization During RH Refining Process2022年12月28日 In the absorption tower, the main component of hydrated lime is Ca(OH) 2, the desulfurization rate of sintering flue gas reaches 98% and the denitrification rate reaches 88%, A Realistic Approach to Modeling an InDuct Desulfurization Process Based on an Experimental Pilot Plant Study Chem Eng J 2008, 141, 141–150Effect of CO 2 on the Desulfurization of Sintering Flue Gas with2023年12月13日 Therefore ability of Basic Oxygen Process (BOP) to remove sulfur is low due to its highly oxidized slag Desulfurization may be effectively conducted in the reducing slag stage of the steel making process in Electricarc furnace At this stage the oxidizing slag is removed and then lime flux is added to form basic slag with high CaO contentDesulfurization of steel [SubsTech]
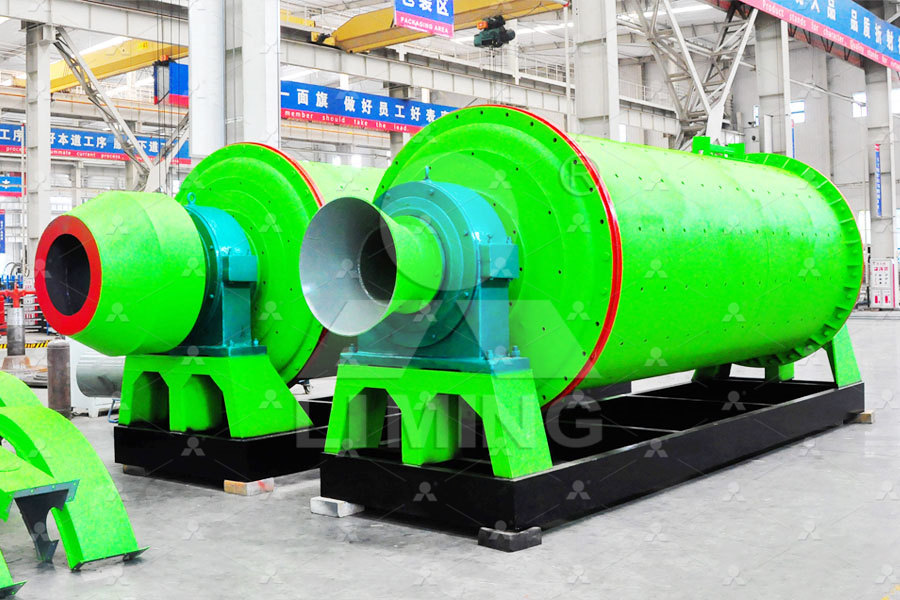
Effect of relative humidity on the desulfurization performance of
2024年4月1日 Increasing efforts have been made in the development and application of different desulfurization technologies in our country to control the excessive emission of sulfur dioxide (Wu et al, 2020; Su et al, 2005)The common flue gas desulfurization technologies currently can be divided into the dry method, semidry method, and wet method according to the process 2015年10月30日 A Review of Desulfurization Technology using Limestone in Circulating Fluidized Bed Boiler Type Power Plant(PDF) A Review of Desulfurization Technology using Limestone in 2020年1月29日 The high suspended solid (SS) and salts were main issues for flue gas desulfurization wastewater (FGDW) A magnetic lime coagulation (MLC)membrane distillation (MD) integrated process was firstly Insight into the magnetic lime coagulationmembrane distillation