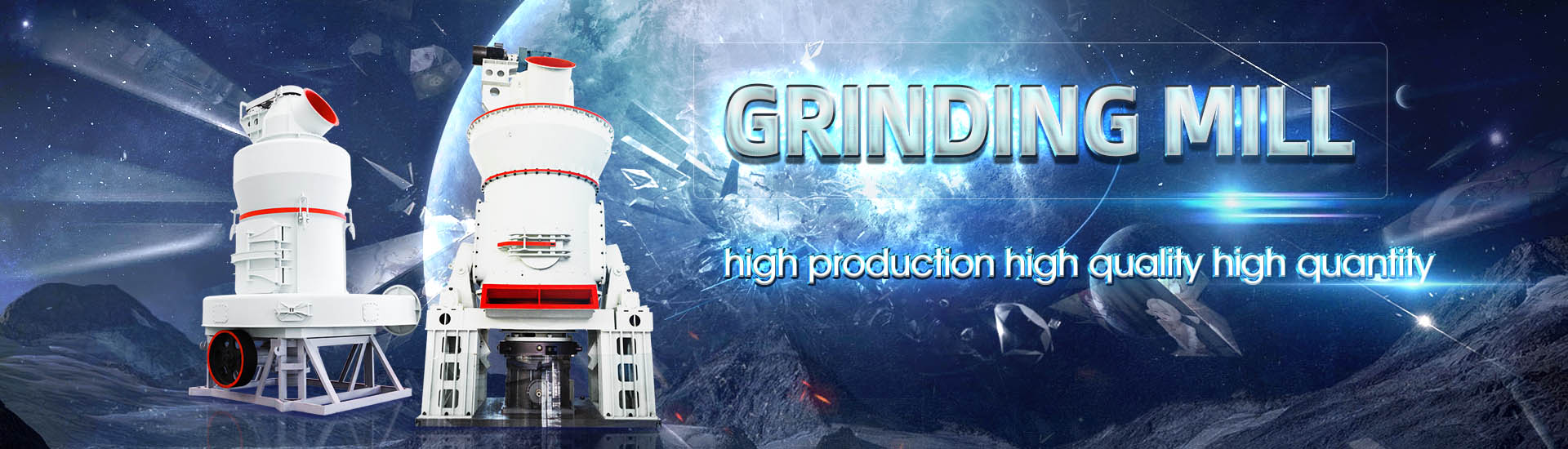
Design of tensioning device for coal mine ring roller mill
.jpg)
(PDF) Design and Fabrication of Rolling Mill Academia
This paper is to discuss to design and fabrication of a manual spring rolling machine by a simple mechanism arrangement for the production of closed and open coil helical springs This 2007年7月1日 The control law is based on tension estimation by using mill motor torque and rolling force etc and manipulates the speed of an upstream main motor The major Looper and tension control in hot rolling mills: A survey2024年1月19日 Tension control in coldrolling pilot mills (CRPMs) with hydraulic tension is subject to extraneous forces resulting from positional disturbances, strong coupling, and timevarying characteristics, making it challenging to Study on HighPrecision Tension Control Technology 2018年12月18日 In this paper, a tension control method is proposed by applying tension to the carbon fiber with three different driven rollers (the torque of unwind roll, the torque of magnetic Design and Analysis of a Novel Tension Control Method for
.jpg)
Breakage of coals in ringroller mills Part I The breakage
1996年3月1日 The objectives of the present study are to clarify breakage properties of coals in ringroller mills and to develop a mathematical mill model capable of predicting steadystate 2006年7月3日 A model machine with extensive flexibility has been designed to explore innovation in ring rolling, with the intention of developing ring rolling machines which can The design of a flexible model ring rolling machine2012年12月31日 The newly developed MVR roller mill from Gebr Pfeiffer AG for grinding cement raw material, cement clinker, and additives with an installed power of up to 12 000 kW does in fact Design and Realization Of Roller Mill Control SystemRoller mill is a type of grinding equipment for crushing materials by pressure between two or more rolling surfaces or between rolling grinding bodies (balls, rollers) and a track (plane, ring, and Roller Mill Springer
.jpg)
Designing of Hot Strip Rolling Mill Control System Semantic
Aimed at the complex demand of hot strip rolling mill in practicing, the configuration of the coiler and the technological process is analyzed The arithmetic of coiling tension and the control 2020年8月12日 This study shows the performance of a currently running vertical roller coal mill (VRM) in an existing coalfired power plant In a power plant, the coal mill is the critical An investigation of performance characteristics and energetic 2020年8月12日 To understand the performance of a vertical roller coal mill, the real operational tests have been performed considering three different coal sources Obtained results indicate that grinding pressure, primary air (PA) temperature and mill motor current have a tendency to rise by increasing coal feeding mass flow rates for all used coalAn investigation of performance characteristics and energetic 2012年12月31日 Report system used to show our main work pa ram eters roller mill, limestone, pul verized coal and accumulativ e total parameters, the time of history and can be used for roller mill work Design and Realization Of Roller Mill Control
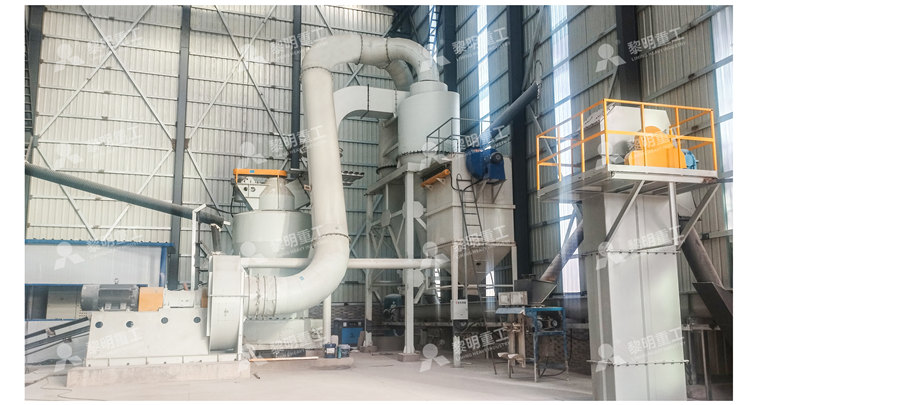
COAL GRINDING IMPS: more than meets the eye Gebr Pfeiffer
also find an application in grinding a wide variety of coal types in cement and power plants Gebr Pfeiffer SE (GPSE) describes its vertical roller mills for coal grinding and provides a case study of an MPS225BK installed at CBR’s Lixhe cement works in Belgium COAL GRINDING Figure 1: MPS coal grinding mill with SLS highefficiency classifier2012年9月27日 Mill design, which follows engineering rules, design concepts, and past design experiences, provides a fundamental blueprint of a mill The mill design innovation focuses on performance On the Optimization Procedure of Rolling Mill Design2023年6月9日 Conveyor belts are widely used in ore transportation in largescale mines for their long transportation range, high safety, and strong economic applicability Coal mine belt conveyors are not only traditional, simple mechanical conveying devices but also automatic control system operating devices that integrate safety, stability, and low power consumption In Research on and Design of an Electric Drive Automatic Control Coal Pulverizer Design Upgrades to Meet the Demands of Low NOx Burners by Qingsheng Lin Staff Engineer, vertical spindle, table/roller mill It contains an integral classifier, a grinding section, a windbox (plenum), and auxiliary components (Figure 1) Opera ion curve s ring mill 120 80 100 80 60 40 20 20 40 Non c 60Coal Pulverizer Design Upgrades to Meet the Demands of Low
.jpg)
Numerical Investigation of Vertical Roller Mill Operation Using
2023年12月4日 This study investigated the effect of table speed (mill speed), roller and table gap, dam ring height, and rolling resistance of material using the discrete element method in an industrialscale VRM Simulation results showed that the rolling point is moved near the outer diameter of the grinding table as the mill speed increased2024年1月15日 An industrialscale vertical roller mill (M600) was analysed for air flow in this study This led to proposed modifications, which were implemented in a new mill design (M350) The M600 mill can operate under continuous mode and is used for fine grinding of materials The design of this mill is depicted in Fig 1Optimisation of the performance of a new vertical roller mill by The document provides installation and operation instructions for the HRM1700M Vertical Roller Coal Mill It describes the mill's technical parameters, components, structure, working principles, and installation process Key aspects include grinding rollers that can be removed for maintenance, a hydraulic system that controls grinding pressure, and a separator that Operation Manual: HRM1700M Vertical Roller Coal Mill2021年2月1日 Design and Application of Intelligent Monitoring and Identification System in Coal Mine February 2021 IOP Conference Series Earth and Environmental Science 651(3):(PDF) Design and Application of Intelligent Monitoring and
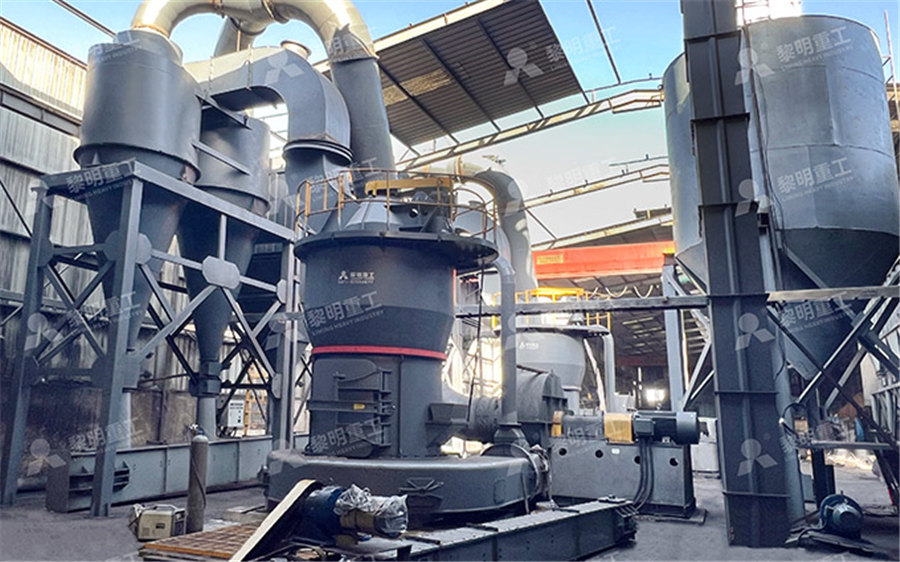
Coal Mill in Cement Plant Vertical Roller Mill Air
A coal mill is also called a coal pulverizer or coal grinder It is a mechanical device used to grind raw coal into pulverized coal powders The most used coal mills in cement plants are airswept ball mills and vertical roller mills At present, most Introduction This article concerns itself with vertical grinding mills used for coal pulverization only (coal pulverizers), although vertical grinding mills can and are used for other purposes The 3D model in the saVRee database represents a Vertical Grinding Mill (Coal Pulverizer) Explained2012年11月17日 20 131Fineness Fineness is an indicator of the quality of the pulverizer action Specifically, fineness is a measurement of the percentage of a coal sample that passes through a set of test sieves usually designated at 50, Coal mill pulverizer in thermal power plants PPT2014年2月28日 The calculation of two transport systems (conveyor length of nine kilometers) for start and stop modes with the CDI fiveelement composite model was performed using the finite element methodSimulation Method of Designing and Selecting Tensioning Systems
.jpg)
(PDF) Performance Evaluation of Vertical Roller Mill in
2017年9月11日 Due to the compact design and material transportation system of vertical roller mills (VRM), some important streams (total mill feed and discharge, dynamic separator feed and reject) remain in the 2016年12月1日 Worker safety in underground coal mines has always remained a challenging task Several fatal and nonfatal accidents take place worldwide resulting in casualties and injuries of coal minersDevelopment of a Wearable Safety Device for Coal Minersuses the testroller mill Atrol (throughput approx 240 kg/h) for grindability testing and quantitative prediction of wear in industrial mills Roller mill for granulated blast furnace slag grinding in China Roller mill for cement raw material grinding in China Roller mill for cement clinker grinding in Mexico Coal grinding plant in PolandPolysius Roller Mills For grinding2014年4月1日 Two mill systems are employed for most coal grinding applications in the cement industry These are, on the one hand, vertical roller mills (VRM) that have achieved a share of almost 90% and, on (PDF) The latest innovative technology for vertical roller mills
.jpg)
Roller Mill SpringerLink
2023年7月4日 The basic structure of the roller mill includes the grinding roller, the grinding body, the force generation and transmission mechanism, airflow, and the device for easy replacement It can be divided into vertical roller mill, horizontal cylinder roller mill, high pressure roller mill, Raymond mill, and column mill2023年6月9日 Coal mine belt conveyors are not only traditional, simple mechanical conveying devices but also automatic control system operating devices that integrate safety, stability, and low power consumptionResearch on and Design of an Electric Drive Automatic Control PDF On Jan 1, 2015, Wei Chen and others published Design of Control Device for Mine Endless Rope Winch Find, read and cite all the research you need on ResearchGateDesign of Control Device for Mine Endless Rope Run of Mine (ROM) Material from a mine that has not been crushed or screened Run of Quarry (ROQ) Material from a quarry that has not been crushed or screened Scalping Removing all sizes smaller than output top size from the crusher input material Side Liners / Cheek Plates Wear plates used to protect the crusher frame side platesConstruction, Working and Maintenance of Crushers for Crushing
.jpg)
VERTICAL ROLLER MILLS A holistic VRM approach
The quadropol® vertical roller mill by thyssenkrupp Industrial Solutions takes a holistic approach to modern grinding systems in terms of its simple and compatible design Describing the key concepts behind the technology, materials such as rebars and tensioning devices, including civil engineering Therefore, a big base frame for the2019年2月21日 The paper analyzes the interrelation of: motion, particle size of ground rice grains, displacement, and grinding in a roller–plate mill The purpose of the study was to analyze and evaluate A study of operating parameters of a roller mill with a new designR Roller Mill Xiao Xiao1, Huang Lilong2 and Xu Kuangdi3 1Changsha Research Institute of Mining and Metallurgy, Changsha, China 2Changsha Research Institute of Mining and Metallurgy, Changsha, China 3Chinese Academy of Engineering, Beijing, China Roller mill is a type of grinding equipment for crushing materials by pressure between two orRoller Mill Springer2012年1月1日 A large conveyor belt with the capacity of 37,500 t/h and speed of 74 m/s has been applied in one open pit mine of Germany Compared with foreign countries, the belt conveyors used in coal mines of China have smaller capacity and lower speed Greater disparity exists in the aspects of dynamic design, computer monitoring and intelligent levelResearch on Control System of Belt Conveyor in Coal Mine
.jpg)
Analysis and Optimization of Grinding Performance of Vertical Roller
2022年1月23日 This work concentrates on the energy consumption and grinding energy efficiency of a laboratory vertical roller mill (VRM) under various operating parameters2009年1月1日 This book details advances in the production of steam and the utilization of all types of fuels Section 1 covers Steam Fundamentals including thermodynamics, fluid mechanics, heat transfer CFD Modeling of MPS Coal Mill for Improved Performance and Safetythe conveyor is coal, so some properties of the coal are given in Table 1 Table 1: Pulley Some mechanical properties of coal 2 width Pile mater Density of coal [t/m 3] Maximu m slope Pile angle Static Slope Resistance Coefficient Particle Size a [mm] Coal 0,9 15 40 1,85 80 Transportation capacity of the belt conveyor is 500 tons perCONSTRUCTIVE DESIGN OF A BELT CONVEYOR FOR A COAL MINE2020年5月21日 For hard rock drilling in coal mine, the drilling efficiency and service life of polycrystalline diamond compact bit are very low To overcome these shortcomings, the bionic technology is applied Bionic design and test of polycrystalline diamond compact bit for
.jpg)
Breakage and separation mechanism of ZGM coal mill based
2014年3月1日 For the mill's classifier device, in the longwall 16101 face of the Fuping Coal Mine breakage properties of coals in ringroller mills and to develop a mathematical mill model 2002年2月14日 This paper presents a systematic design procedure for the design of a laboratory cold rolling mill In order to arrive at proper decisions at various stages of the design, the concepts of fuzzy sets and priority decision tables were employed The design process starts from deciding specifications and gradually reaches the detailed design phaseA systematic procedure for the design of a cold rolling mill2021年1月29日 Vertical roller mills, VRMs, are widely used for grinding raw materials in factories engaged in the extraction and processing of minerals Any machine used for grinding or crushing consumes around Increase productivity of vertical roller mill using seven Roller mills are now operated with throughput capacities of more than 500 tons per hour of cement raw mix (Loeschemill, Polysius double roller mill, Pfeif ferMPSmill, SKET/ZABroller mill) The working principle of roller mills is based on two to four grinding rollers with shafts carried on hinged arms and riding on a horizontal grinding table or grinding bowlRoller mills INFINITY FOR CEMENT EQUIPMENT
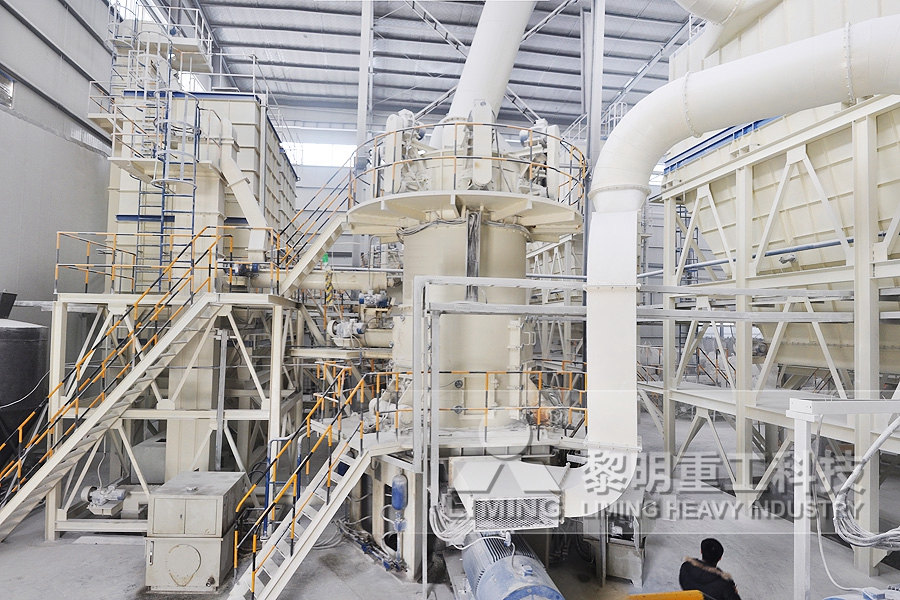
VRM – AMCL Machinery Limited
UBE Vertical Roller Mill UBE’s mill design and rich experience of more than 260 Mill installation allows us to handle coal which is combustible and volatile in nature by ensuring safety and efficient grinding efficiency UBE Mills are capable to grind and dries all the types of coal We offers the coal mill to suited for 2024年2月25日 Figure 1 is a structural diagram of the main devices of the belt conveyor In practical applications, the belt conveyor not only includes the conveyor belt, frame, drive drum, diversion drum, and tail drum as shown in Fig 1, but also includes components such as frame, loadbearing roller, return roller, tensioning device, retracting device, cleaning device, etcControl System Design for Belt Conveyor SpringerLinkof 80mm The raw materials are mixed in a certain proportion and fed into a vertical roller mill (LOESCHE mill) The vertical roller mill grinds the marital to D 85 of 90µm The ground product is calcined in a preheater to 850900℃ After calcination, the materials enter to a rotary kiln and heated to 1450℃ to become clinkerModeling and simulation of vertical roller mill using population 1990 Central coal grinding plant (LM 263 D) for gas and steam power station (coal gasification) 1992 Central coal grinding plant (LM 263 D) for the production of lignite (brown) coal dust 2002 Coal grinding plant (LM 232 D) for grinding wood pellets for power stations 2005 First 4roller pressure mill (LM 434 D) becomes availableLOESCHEMILLS
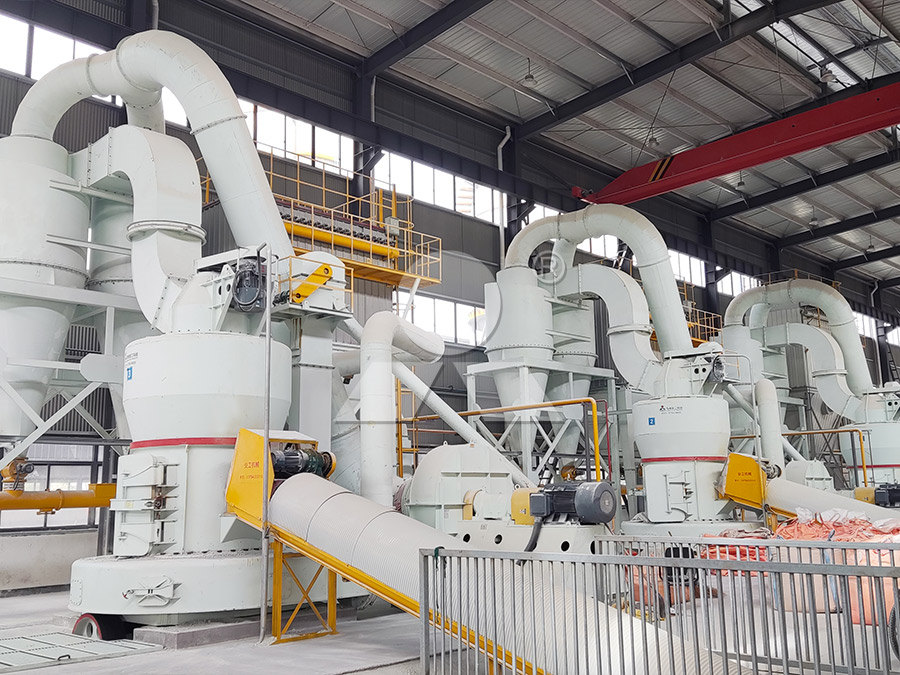
Operational parameters affecting the vertical roller mill
2016年9月1日 Furthermore, VRM separator speed (rpm) is one of the key operational parameters that determines product particle size Increasing the classi er rotor speed from 60 to 80 rpm decreases the particle