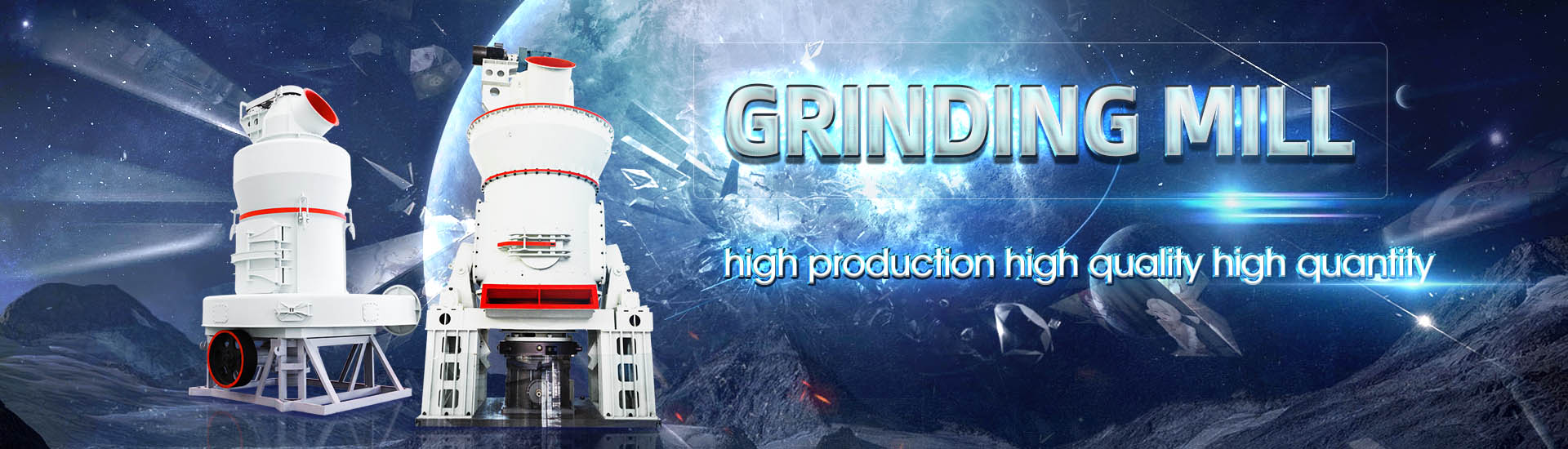
Raw coal drying process

(PDF) 43 Drying of Coal ResearchGate
2006年11月8日 Coal must also be dried for the following processes: (1) briquetting, (2) coking, (3) gasication, (4) lowtemperature carbonization, (5) liquid fuel synthesis, and others The nal moistureSteam drying process heats coal to temperatures more than 200°C for some of the carboxyl groups in the coal decompose and release carbon dioxide The carbon dioxide in turn expels Upgrading of Low Rank Coal by Steam Drying Method, a Process 2023年12月15日 Lowrank coal drying is essential for clean and efficient coal utilization In this study, a novel method, steam transient flash evaporation, is proposed for moisture removal A novel method for lowrank coal drying using steam transient Two dry processing technologies have been evaluated and implemented in South Africa, namely the FGX dry coal separator and Xray sorting The FGX unit is suited to processing of 80 mm raw coal while the Xray sorter is well suited to Processing lowgrade coal to produce highgrade
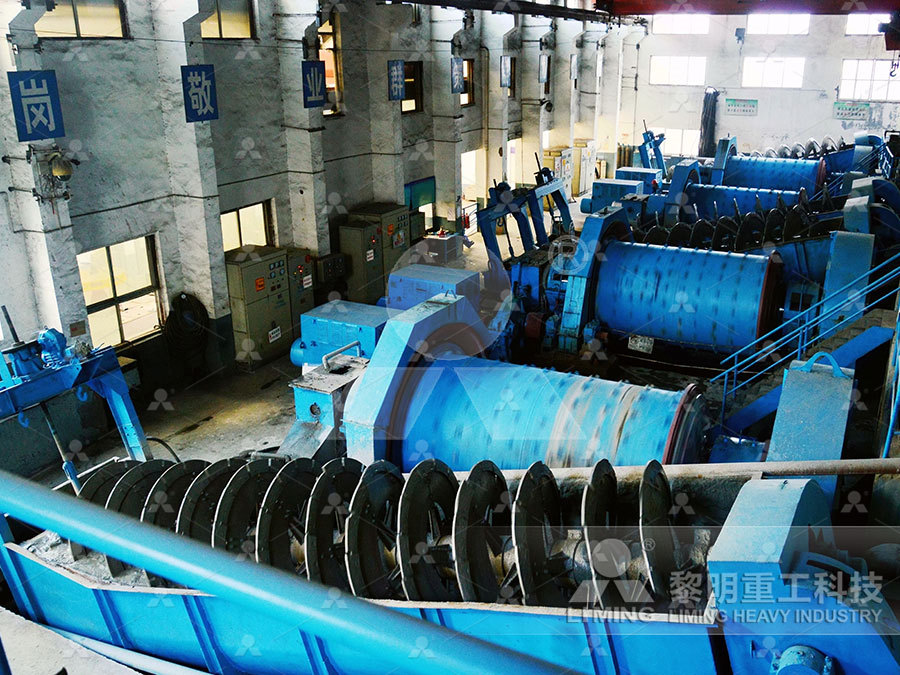
A novel method for lowrank coal drying using steam transient
2023年12月15日 Lowrank coal drying is essential for clean and efficient coal utilization In this study, a novel method, steam transient flash evaporation, is proposed for moisture removal raw coals is lower than expected and control of product quality is not always easy with dry processes In the case of easytoclean coals, dry processing gives good results and becomes Dry Processing Versus Dense Medium Processing For Preparing Dry coal processing benefits downstream utilizations through possible cost and energy savings along with a reduction in water pollution As a result, dry processing has inspired interest in the Dry processing for coal preparation: a review2019年9月5日 A modular and efficient dry coal preparation system was established for raw coal preparation, drying, separation, medium purification and recovery, density steadystate control, Research Progress in Dry Beneficiation University of Pittsburgh
.jpg)
Numerical simulation of lowrank coal drying based on non
5 天之前 The results revealed that the drying temperature had the greatest effect on the drying process, while the airflow velocity had a minor effect The optimum drying conditions for lignite 2009年2月25日 Drying coal is a highenergy and timeconsuming process, so reducing the required energy and drying time is crucial for drying technology Coal drying increases the thermal value of coal and makes (PDF) LowRank Coal Drying Technologies—Current Status and 2024年1月11日 The 5step process to pulverize coal efficiently The coal pulverization process involves a precise sequence of steps Each is systematically designed to convert raw coal into a fine, efficient powder But How to Process Coal into Pulverized Coal in 5 Steps?Drying Technologies for Mineral Raw Materials • Productoptimized drying • Wide variety of process options • Easy access for quick replacement of spare parts • Variable design for different products For every requirement coal, waste materials, wood, domesticDrying Technologies for Mineral Raw Materials
.jpg)
Research Progress in Dry Beneficiation University of Pittsburgh
2019年9月5日 The raw coal selection rate has reached 718% The dry coal preparation process system is composed of four modules as below (I) Raw coal preparation A modular and efficient dry coal preparation system was established for raw coal preparation, drying, separation, medium purification and recovery, density steadystate 2018年7月27日 For the necessary direct fine grinding of the runofmine lignite coal, RWE has developed a special process with two grinding stages connected in series for the reduction of the grain size of the raw lignite coal from around less than 80 mm to the desired value of less than 2 mm Fig 3b shows the overall process of finegrain WTA process WTA technology for drying of lignite coal – IspatGuru2020年1月20日 The priority feature of coal drying which accounts for its industrial use is moisture removal Though much improvement is made in thermaldrying process, volatilization of harmful elements during coal slime drying is mostly ignored which has manifold environmental implications In view of this, the present study attempted to investigate the moisture and Volatilization characteristics of selenium during conventional and In the first drying zone, most of the moisture is removed at 400°C under high humidity conditions, ensuring that the chemical composition of coal remains unchanged and is less prone to combustion The second drying zone operates at room temperature of 300°C, using mediumtemperature strong airflow to efficiently remove moisture, preventing the coal from cokingCoal Dryer Machine and Coal Drying Plant for Sale
.jpg)
4C3 Briquette Production Technology
Raw Coal Drying Crushing Coalite Cyclone Desulfurizer Binder Water Mixing Kneading Briquetting Drying Briquette Carbonizing Part 2 CCT Overview process The raw materials, coal and biomass, are pulverized to a size of approximately 2022年12月14日 The influence of the drying process on the coal was analyzed by comparing activation energy, functional group of immersed coal with different drying degrees and raw coalStudy the effect of drying on the oxidation thermogravimetric and 2020年7月8日 111 History The art of pottery is one of the oldest in the world due mainly to the abundance of clay and the ease of extraction and fabrication There is evidence of activity of this art in almost all peoples of antiquity and to improve their quality of life, man has always been seeking to perfect the various uses of ceramic materialsClay Ceramic Materials: From Fundamentals and Manufacturing to Drying Steam drying process of the Low Rank Coals (LRCs) has been conducted to produce coal which is comparable with the High Rank Coal (HRC) Characterization of the raw and dried coals was carried out through proximate, ultimate, calorific value, Fourier Transform Infrared (FTIR) spectroscopy and Thermo GravimetryDifferential Thermal Analysis (TGDTA) to study the The influence of steam drying process on combustion behavior of

Coal Slurry Drying Process Research
2018年8月1日 This process is more costeffective, but it is not integrated with the grinding process [14]; in addition, since condensation occurs along the entire length of the pipes or panels, both raw coal some Chinese coals are relatively easy to process As an example, the washability of a Chinese raw coal is shown in Table 2 Table 2: Washability data for a Chinese raw coal Fractional Cumulative Relative Density Yield Ash Yield Ash % % % % F @ 1400 7136 60 7136 60 F @ 1500 384 167 7520 65Dry Processing Versus Dense Medium Processing For Preparing Thermal CoalThe process of coal drying The Coldry process has the following six steps The process flow sheet is shown in Fig 2 Screening and feed control – The low rank raw coal having moisture content in the range of 30 % to 70 % is ground to a size which is less than 8 mmColdry technology for low rank coal drying – IspatGuru2006年11月8日 Drying of lowrank coal (LRC) is carried out to increase its caloric value and facilitate its transport Wet coal is difcult to load or unload from railway cars owing to freezing, which is a (PDF) 43 Drying of Coal ResearchGate
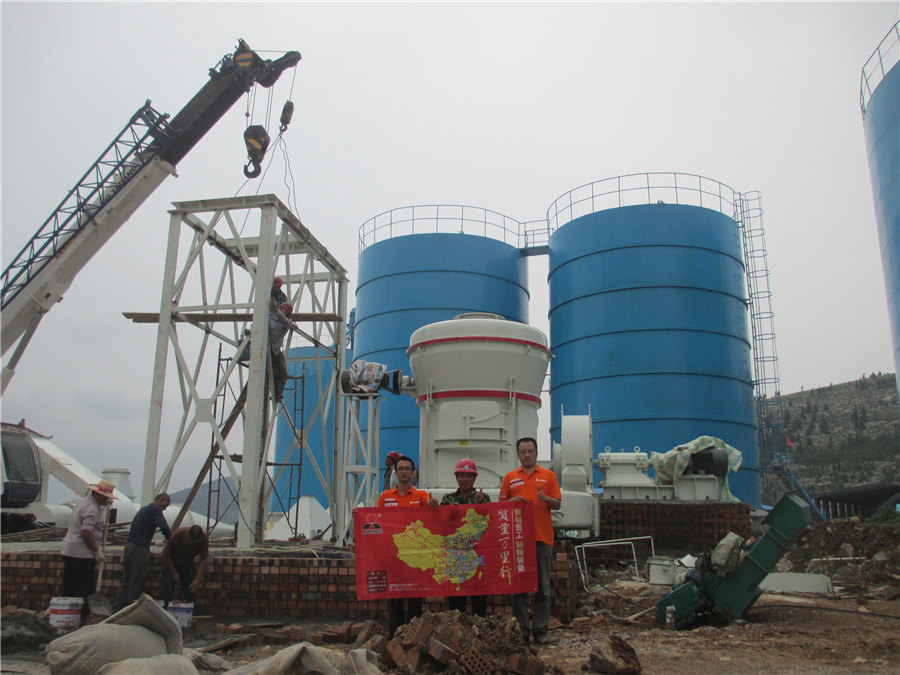
The Evaluation of Spontaneous Combustion Characteristics and
The upgrading process for Indonesian low rank coal by a combined process of vacuum drying and tar coating has been developed to 3005 upgraded coal are lower than for the raw coal, 2016年9月23日 Lignite is a lowquality energy source which accounts for 13 % of China’s coal reserves It is imperative to improve the quality of lignite for largescale utilization To further explore and analyze the influence of various key processes on the environment and economic costs, a lignite drying and compression technology is evaluated using an integrated approach Future of lignite resources: a life cycle analysis2014年8月1日 Raw coal was fed into the center of the disc dryer and then was transferred from the center of the heating plate to the outside of the plate by the rotary blades during the drying processOptimization of drying of lowgrade coal with high moisture content Energy 2012;45(1):203e12 [93] Aziz M, Kansha Y, Tsutsumi A Selfheat recuperative fluidized bed drying of brown coal Chem Eng Process 2011;50(9):944e51 [94] Aziz M, Kansha Y, Kishimoto A, Kotani Y, Liu Y, Tsutsumi A Advanced energy saving in low rank coal drying based on selfheat recuperation technology Fuel Process Technol 2012;104:16e22Recent developments in drying and dewatering for low rank coals

Construction of a New Type of Coal Moisture Control Device
2020年8月12日 coal predrying technology Keywords: moisture; coal predrying; heat; mass; drying kinetics 1 Introduction Research data from 2017 “BP World Energy Outlook” showed that coal still accounted for a massive 30% of the world’s primary energy structure, second only to oil which accounted for about 32% China is2020年7月24日 The results show that, the proposed pyrolysis–gasification integration process for Victorian brown coal possesses an exergy efficiency 45% higher than the drying–gasification process, and 15 Low Rank Coal Drying technology for Decreasing 2020年11月1日 Another visual angle for studying thermal fragmentation is the development of cracks in coal drying process Feng and Zhao (2015) As shown in Fig 8, there are a large number of pores with the diameters of 44 and 83 nm in raw coal, and the numbers of the pore larger than 180 nm are roughly the same However, Lowrank coal drying behaviors under negative pressure: Thermal 2023年11月24日 Abstract The results of an analysis of the state of developments in the field of gasification of coal and biomass mixtures are presented It is shown that this is a promising direction for diversifying the areas of coal application and a new area for using biomass as a renewable natural resource The specific features of the process of gasification of coal and Gasification of Coal and Biomass Mixtures Solid Fuel Chemistry
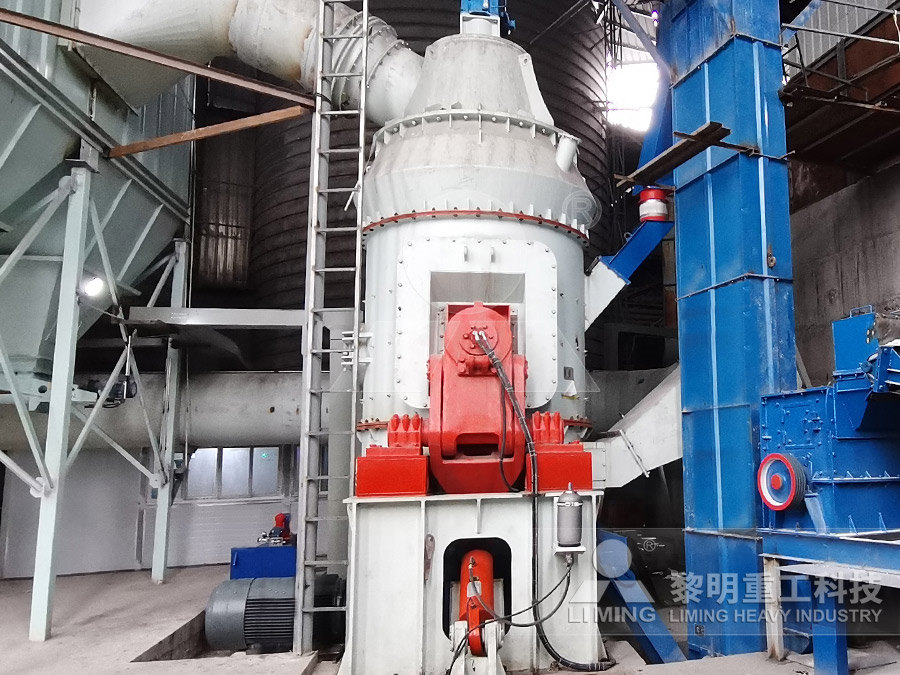
Dewatering and Drying in Mineral Processing Industry: Potential for
2010年6月30日 operations are generally carried out at the raw materials dewatering = drying process employed in the mineral proces ventional hot ai r used in coal drying b ecause it elimin ates fire 2018年7月18日 Heavy stocks of highmoisture coal slurries being kept on the territory of Russia should be dried prior to recycling combustion in a TTP’s pulverized coalfired boilers The expediency and applicability of coal slurry drying in panel steam dryers (PSD), currently manufactured by JSC Tyazhmash, is shown The results of laboratory and bench studies of Coal Slurry Drying Process Research Thermal Engineering2008年7月1日 Test results have shown that in contract to raw coal, the coal dried by the process at temperatures of 300 – 350°C has a decreased inherent moisture, an increased calorific value and lower Minimization of Moisture Readsorption in Dried Coal Samples2018年8月9日 Process advantages – These include (i) low processing time which is between 5 minutes to 10 minutes, (ii) adjustable product specifications, (iii) variety of feed coals can be processed since there is process control and optimization through knowledge based programmable logic controllers (PLC), (iv) suitable for feed coal size of 0 mm to 50 mm, (v) PristineM process technology for drying of low rank coals
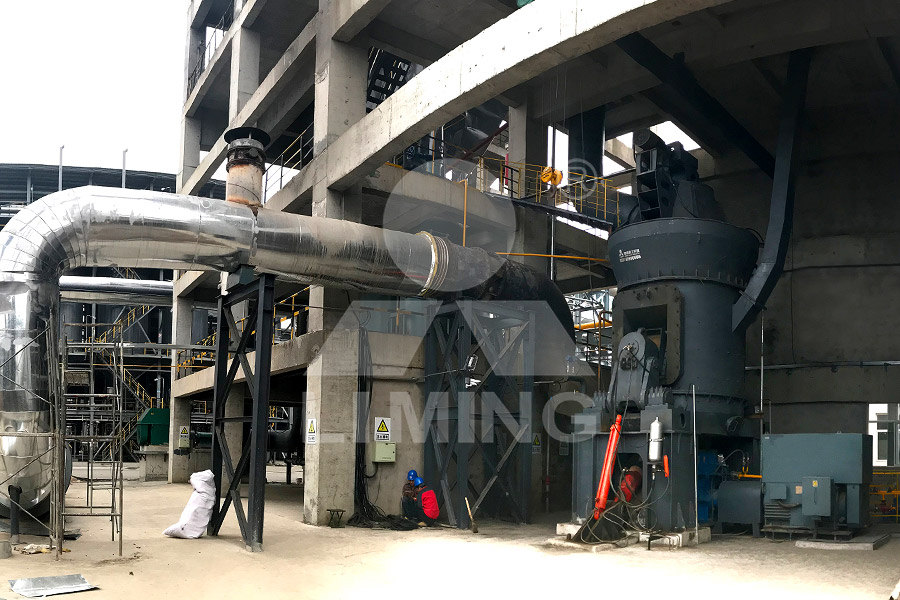
4D2 Lowrank Coal Upgrading Technology (UBC Process)
Fig 2 Fundamentals of lowrank coal upgrading Multipurpose Coal Utilization Technologies (Deashing and Reforming Technologies) 77 4D2 Lowrank Coal Upgrading Technology (UBC Process) Technology overview˜ ˜ 1 Background and process overview˜ Brown and subbituminous coal, accounting for about 50% of coal reserves, are referred to as "low 2015年6月28日 Following the successful demonstration, the lowtemperature coal drying technology was commercialized by GRE under the trade name DryFining TM fuel enhancement process and implemented at both (PDF) Four Years of Operating Experience with DryFiningTM Fuel 2016年6月5日 Great River Energy's Coal Creek Station has successfully commercialized a low temperature coal drying process Mercury Concentration Relative to Raw Coal Coal Stream Coal Creek Unit 2: March (PDF) Low Temperature Drying Process Improves Heat Rate 2024年10月15日 Pulverized coal drying: Raw coal is grinded in the vertical coal mill and dried by hot air (usually below 300°) into the vertical roller coal mill, which meets the drying standard of finished pulverized coal For the safety operation of the following parameter are controlled to avoid the explosion of the coal mill bag filterCashew Nutshell and Raw Coal Cogrinding for Sustainability
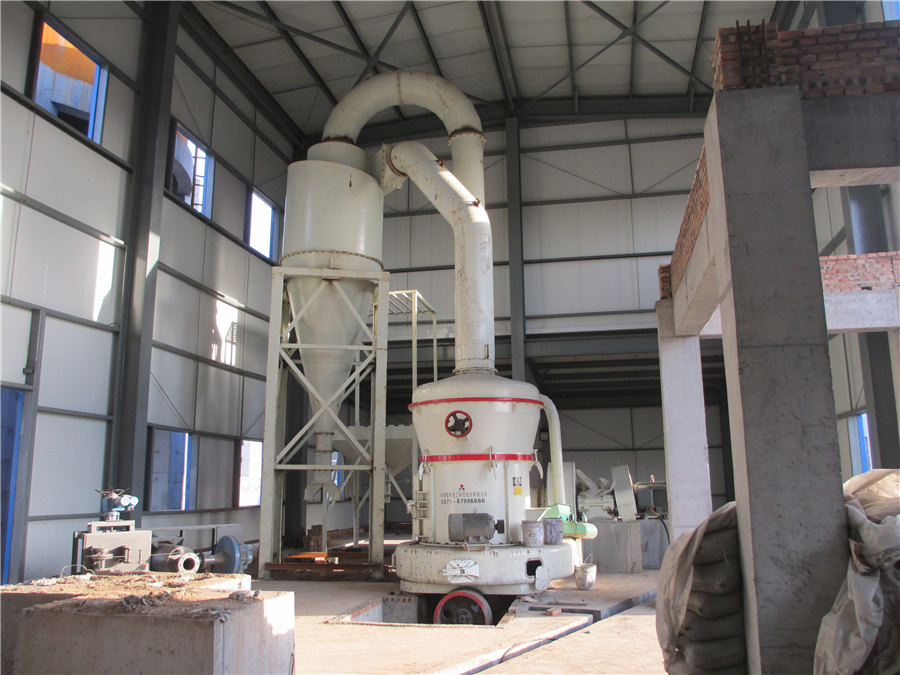
Laboratory experimental study on watersoaked–dried bituminous coal
2019年9月11日 In the process of multiseam mining, the measure of water exploration is usually employed for the upper coal seam to prevent and control water accumulation The residual coal immersed in water for a long time in the upper layer is dried under the action of air leakage, leading to the enhancement of the risk of coal spontaneous combustion Therefore, it is Coal Drying Technology and Plant Design Free download as PDF File (pdf), Text File (txt) or read online for free The document describes the process and design of a rotary drum coal drying system, including how wet coal is fed into and dried within a rotating metal drum using hot gas as the heating medium before being discharged, with the goal of improving the energy efficiency Coal Drying Technology and Plant DesignRemoval of the mineral matter (or “ash”), 3 which is largely noncombustible and may constitute up to 65 percent of the raw coal, increases the heating value of the coal on a mass basis 4 Although some combustible material is lost as part of the cleaning process, the removal of unwanted material reduces the mass and volume of coal for a given heating value thereby reducing Coal Mining and Processing The National Academies Press2021年9月1日 Process modeling and technoeconomic analysis of a solar thermal aided lowrank coal dryingpyrolysis process Author links open overlay panel Tara Hosseini a b, Lian Zhang a Show more The raw coal composition and the production yields of the conventional pyrolysis process at 800 °C for the bestcase scenario are presented in Process modeling and technoeconomic analysis of a solar
.jpg)
Using Copper Ore and Hematite Fine Particles as Raw Materials of
Using Copper Ore and Hematite Fine Particles as Raw Materials of an Oxygen Carrier for Chemical Looping Combustion of Coal: Spray Drying Granulation and Performance Evaluation @article{Su2020UsingCO Research progress of oxygen carriers for the chemical looping process of different feedstocks Xiaofeng Liu Huimin Liang +7 authors Chong HeCrushing Stacking Reclaiming of Coal The process of making cement clinker requires heat Coal is used as the fuel for providing heat Raw Coal received from the collieries is stored in a coal yard Raw Coal is dropped on a belt conveyor from a Businesses CementManufacturing Process Jaypee GroupEffect of DryFineTM Low Temperature Coal Drying Process on Emissions from a CoalFired Power Plant Paper #25 Charles W Bullinger Great River Energy, 1611 E Century Avenue Bismarck, ND 58503 Mark Ness Coal Creek, 2875 3rd St SW, Underwood, ND 58576 Katherine Dombrowski URS Corporation, 9400 Amberglen Boulevard, Austin, TX 78729 Nenad SarunacEffect of DryFineTM Low Temperature Coal Drying Process on 2014年8月21日 China’s energy supply heavily relies on coal and China’s coal resource and water resource has a reverse distribution The problem of water shortages restricts the applications of wet coal beneficiation technologies in drought regions The present situation highlights the significance and urgency of developing dry beneficiation technologies of coal Progress in developments of dry coal beneficiation
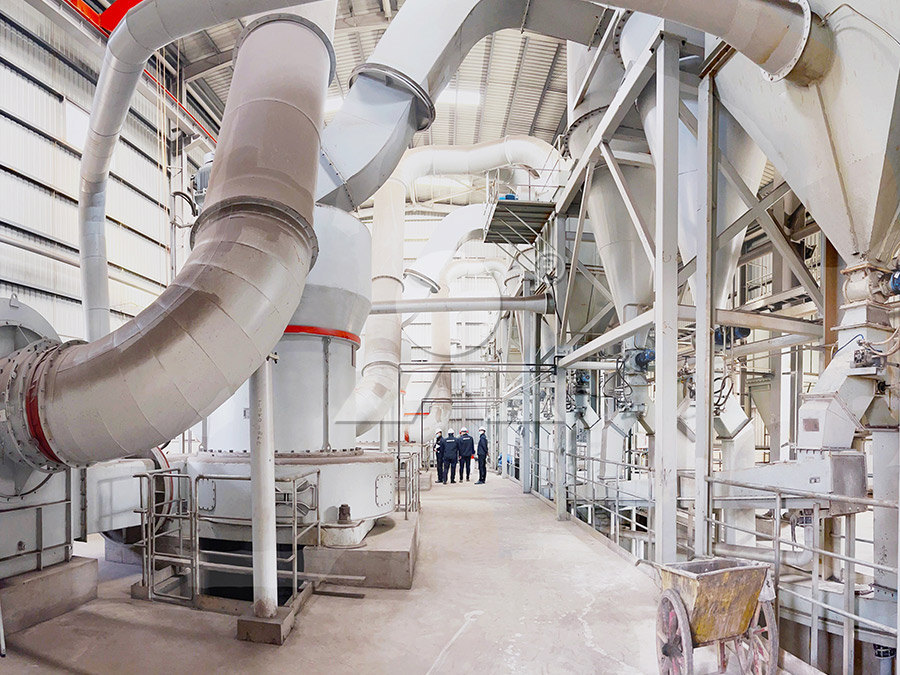
A novel method for lowrank coal drying using steam transient
2023年12月15日 The drying process of lowrank coal is essentially a mass transfer process from the porous media inside to the outside The vitrinite content in raw coal is only 4867%, it can be increased to 6185% and the yield of clean coal is only 2644% by flotation for raw coal