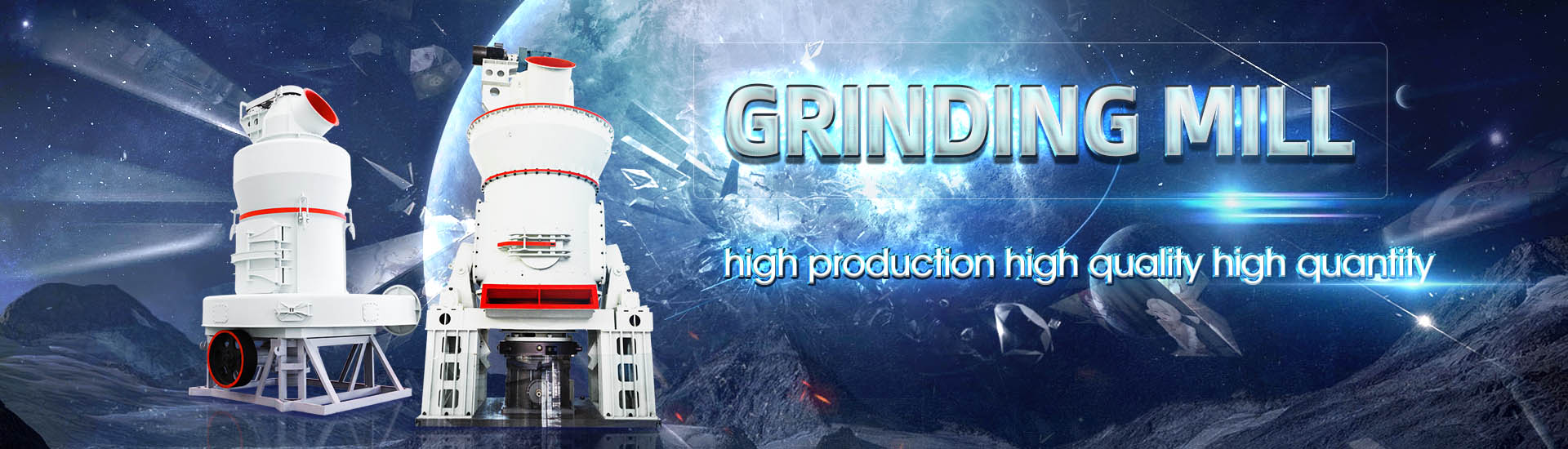
Ube grinding roller fracture reason

Operational Failure of Vertical Roller Attached to a Grinding Mill
2023年11月21日 Several reasons have been described in studies for the failure of vertical roller in grinding mill Unnatural vibration, short comings in maintenance, deviation in operating parameters and inferior grade of raw materials play a significant role in such failures [1]inspired UBE’s decision to develop a new VRM with smaller rollers but larger capacity than ever before By adopting smaller grinding rollers, theoretical mill capacity is decreased, but by 50 40 30 UBEマシナリー株式会社Several reasons have been described in studies for the failure of vertical roller in grinding mill Unnatural vibration, short comings in maintenance, deviation in operating parameters and Operational Failure of Vertical Roller Attached to a Grinding Mill 2024年3月1日 The main fracture mechanism of the bearing was a brittle fracture characterized with intergranular cracks • According to the failure reasons of the bearing, some reasonable Failure analysis for outer ring cracking of GCr15 rolling bearing
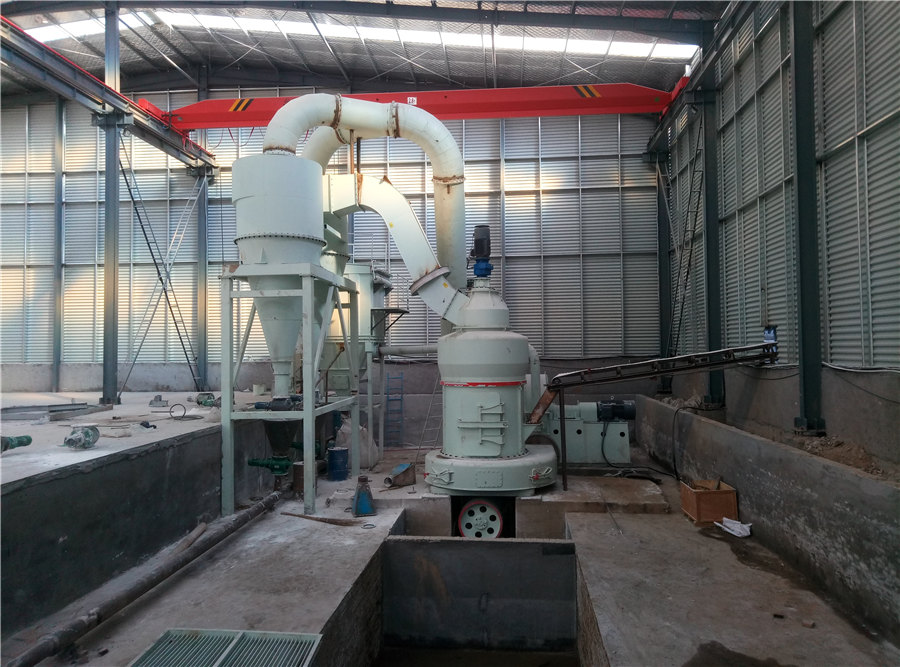
Rolling element bearing failure analysis: A case study
2013年1月1日 This paper addresses Rolling Contact Fatigue (RCF) occurs due to the result of cyclic stress developed during operation and mechanism that involve in fretting failure of When grinding fine products and slippery materials, vibration will occur by the roller slipping We have unique technology to use as a countermeasure for that vibration Vibration is avoided by UBE Vertical Mill UBE Machinery Corporation, Ltd2009年1月5日 Fourrow cylindrical roller bearings having pintype steel cage and pronged machined solid brass cage are commonly used in the backup roll assembly of cold rolling Root Cause Failure Analysis of Outer Ring Fracture of FourRow Download scientific diagram Failure modes of grinding roller: (a) roller fracture in the mill; (b) hardfacing layers peeling off from publication: Numerical simulation of hardfacing Failure modes of grinding roller: (a) roller fracture in the mill; (b
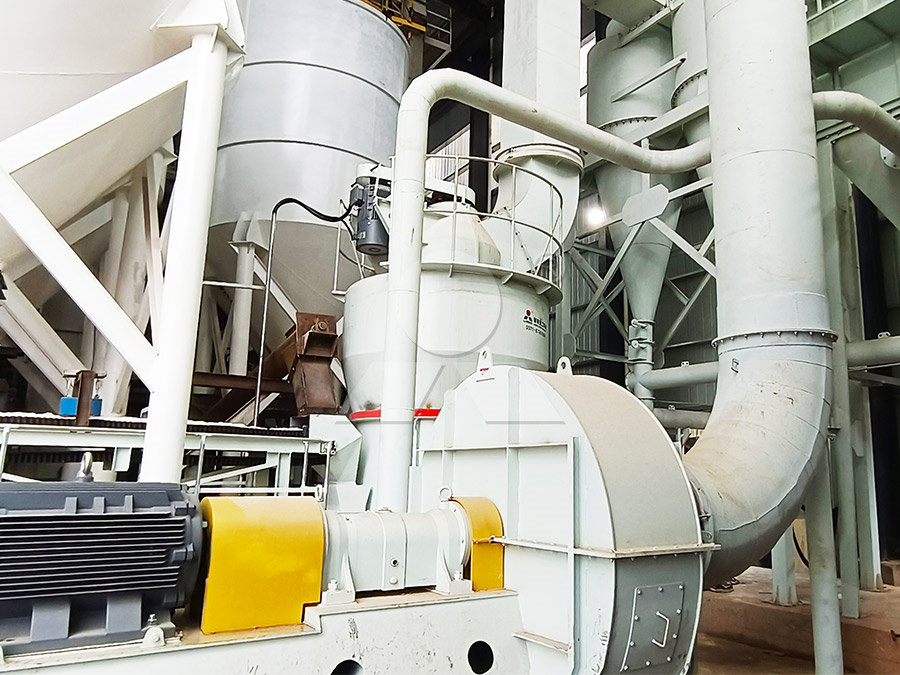
Failure analysis of tapered roller bearing inner rings used in heavy
2020年4月1日 In this case, the fracture incident occurred on several tapered roller bearing inner rings during the assembling before service Inner ring was mounted on to a shaft through a By replacing the conventional type separator with the newest type separator (UNKS type), it is possible to improve the grinding capacity, reduce the vibration value, and reduce the power UBE Vertical Mill|SERVICES|UBE Machinery Corporation, LtdThe schematic of grinding mill along with the position of three rollers is given in Fig 1a An isolated assembly of a vertical roller has been also presented (Fig 1b) As depicted in Fig 1a, the central roller was failed during service The defective component was removed from the assembly for investigation The examination of the failedOperational Failure of Vertical Roller Attached to a Grinding Mill For making a stable grinding bed between the roller tire and table liner, UBE Slag Grinding Mill adopts a '2Way System' By adopting this '2Way System', our mills are operated under less vibration achieving better performance Overview of UBE Vertical Mill UBE Machinery Corporation, Ltd
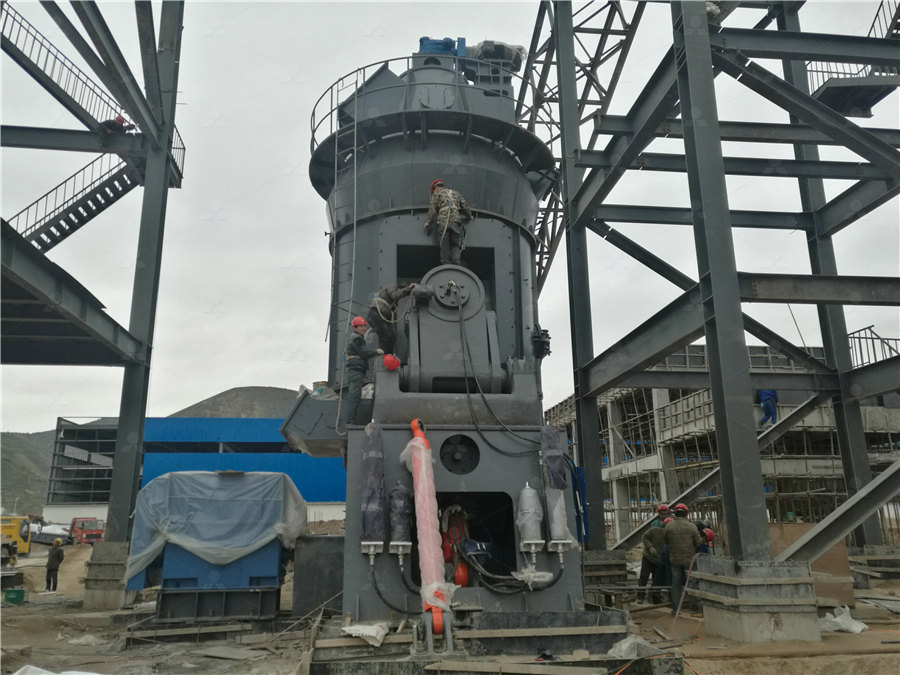
ENERGY EFFICIENT VRM TECHNOLOGY FOR CEMENT AND SLAG GRINDING
coefficient Due to this effect, the grinding rollers can suitably bite the material without slippage, allowing operation with minimized vibration Over the years UBE has the wellestablished 2+2 and 3+3 system of Main Roller and Sub Roller for Cement and Slag grinding Moreover, one of the features of UBE’s subrollers is their positioning5roller raw mill, a 10% downsizing was achieved, and by changing the conventional 4roller cement mill to the new 6roller mill, a 20% downsizing was achieved while maintaining the same grinding capacity in both cases As just described, by changing to smaller, modular roller mill design, the same grinding roller modules are Same50 40 30 UBEマシナリー株式会社2019年7月24日 Ube Machinery Corporation, Ltdhomepage HOME > News Releases2019 > 2019/07/24 AMCL has mainly been engaged in the production of Vertical Roller preGrinding Mills for cement plants across India and the Middle East, and Rubber and Tire Building Machines for the Indian tire industry2019/07/24 News Ube Machinery Corporation, Ltd2013年1月1日 The G20Cr2Ni4A steel bearing roller, quenched and tempered after carburizing, fractured after test running about 2 hours The fracture of G20Cr2Ni4A steel bearing roller was analyzed by Fracture failure analysis of G20Cr2Ni4A steel bearing roller
.jpg)
Operational Failure of Vertical Roller Attached to a Grinding Mill
2023年11月21日 In the present incident, one of the rollers of grinding mill in cement plant failed during operation, exhibiting longitudinal cracking over inner surface Deposition welding was carried out just before the incident to match the wornout profile of the roller Investigation revealed that the subsurface of the cracked region contained discontinuities like blow holes grinding conditions associated with fine grinding of cement clinker and related products, enabling a high grinding efficiency and stable operation Figure 3: H However, despite a generally good performance of vertical roller mills used for grinding of cement and related products the vertical roller mill is still inferior to the ballCement grinding Vertical roller mills versus ball millsTechnical factors affecting core recovery The following list presents a summary of some of the factors that could contribute to either low recovery orTechnical note Core recovery and quality: important factors in The sidegusset plate is connector of the combinedroller, which is the key component of the Highpressure Grinding Roller equipment that is applied in crushing raw iron ore, Fracture occurred at the bottom of the sidegusset plate while the roller’s operation For exploring the reason of fracture, the stress distribution and corresponding critical location of the sidegusset Fracture Analysis of SideGusset Plate of CombinedRoller Based
.jpg)
The mechanism investigation of ultrasonic roller dressing vitrified
2022年9月1日 Most of the previous studies were focused on the roller dressing mechanism Malkin et al [1] found that the interference angle controlled the rotary dressing process, there was a greater tendency for the grits to fracture rather than to deform plastically with a larger interference angle, thereby providing a sharper wheel and reducing the specific dressing energy2009年12月1日 Request PDF Application of ductile fracture criteria in spinforming and tubebending processes As one of the principal failures that occur in metal spinforming and tubebending processes Application of ductile fracture criteria in spinforming and tube years, UBE has the wellestablished 2+2 and 3+3 system of Main Roller and Sub Roller for Cement and Slag grinding As a feature of UBE’s sub rollers, they are designed to generate sufficient amount of load and are positioned near the dam ring on the circumference of the table Flat Table Liner And Conical Type Roller TiresVERTICAL ROLLER MILLS AMCLOver the years UBE has wellestablished 2+2 and 3+3 system of Main Roller and Sub Roller for Cement and Slag grinding As a feature of UBE’s sub rollers, they are designed to generate sufficient amount of load and are positioned near the dam ring on the circumference of the tableVRM – AMCL Machinery Limited
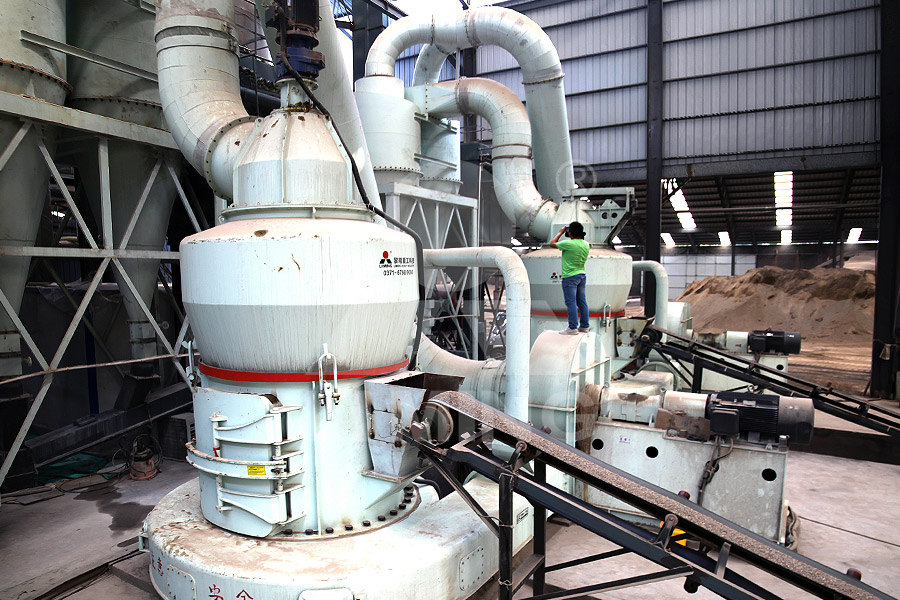
Enduron High Pressure Grinding Rolls Weir Group
4 Enduron® High Pressure Grinding Rolls 5 Traditional Crushing HPGR Grinding F F F F 4 5 4 Compacted cakes 5 Grinding pressure 2 Feed material 3 Fixed roller 1 Floating roller 1 2 3 HPGR in operation HPGR in operation Comminution principles: high pressure comminution and breakage process between rollers Azone Czone Ezone D d a0 y u 2024年3月4日 In order to comprehend the abrasive wear mechanism of CBN grinding wheels with varying structural characteristic parameters, the influence of these parameters on abrasive wear was transformed into the impact of undeformed chip thickness on abrasive wear Subsequently, a twodimensional finite element simulation model of single CBN abrasive Research on the Wear of Groove Structured Grinding Wheel In the production operation of the vibrating screen, due to various reasons, the screen box is cracked, the beam breaks and other failures, which have serious impact on production, and even cannot be produced normally, causing huge losses to the production enterprises 1 If the production load is too large, the equipment will be overloaded, and the screen box will be Fracture Reason and Improvement Method of Vibrating Screen 2017年1月1日 Schnatz, R et all: Operational experience from India's first MVR vertical roller mill for cement grinding Cement International, 5/2013, pp 4653 COPE drive system for VRM(PDF) Drives for large vertical roller mills ResearchGate
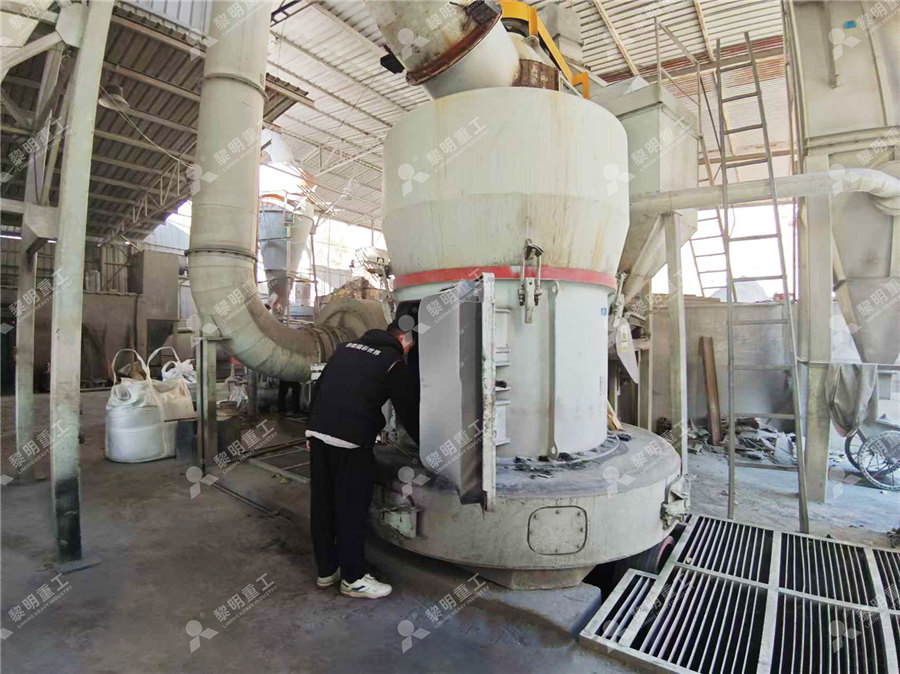
Grinding process within vertical roller mills ResearchGate
2009年1月31日 Download Citation Grinding process within vertical roller mills: Experiment and simulation Based on screening analysis, laser size analysis, grindability and rigidity tests of samples 2005年6月1日 Request PDF Particle weakening in highpressure roll grinding In the literature, comminution in the roller press and subsequent ball milling has been observed to produce significant energy Particle weakening in highpressure roll grinding Request PDF2011年9月2日 During operation, the grinding bed is drawn underneath the roller and compressed to a very hard and dense press cake (high pressure zone) Since the particles are fully interlocked in this compressed bed, not being able to rotate, a 2body anisotropic abrasion wear mechanism is expectedWear mechanism of abrasion resistant wear parts in raw 2018年1月1日 Tube spinning is an advanced forming process to produce thinwalled tubular workpieces with high precision and improved mechanical properties, widely used in aviation, chemistry, power industries, etc [1], [2]During tube spinning, a tubularshaped metal blank or workpiece placed over a mandrel is shaped via radial compressive forces applied by the rollersDamage evolution and ductile fracture prediction during tube
.jpg)
Fracture Failure Analysis of Gear Teeth ResearchGate
2022年2月1日 This content was downloaded from IP address 18524617268 on 10/02/2023 at 16:28Crack reason for spherical roller bearing and bearing carbide network defect analysis ( FIG 5) ; Outer ring rolling road running trajectory deviation occurs, a side grinding crack near one end chamfering, on the other side grinding crack about 30 mm, Crack reason for spherical roller bearing and bearing carbide 2012年11月8日 The fracture process zone can be accurately observed and measured using XRD FRACTURE TOUGHNESS Fracture toughness is a measure of a material’s resistance to fracture Griffith demonstrated that most fractures for brittle materials start at a flaw, or a plane of weakness in the material The ease ofBreakthrough in Clinker Grinding Massachusetts Institute of 2024年3月1日 Analysis of the changing law of residual stress and material micromechanisms under high efficiency deep grinding: (a) Residual stress with (a) strong grinding (Huang, 2009); (b) change in coarse grinding area angle (Yin et al, 2018), (b) Mechanism of efficient deep grinding removal of microscopic morphology (Zhang et al, 2021), (c) Relationship between grinding Residual stress generation in grinding: Mechanism and modeling
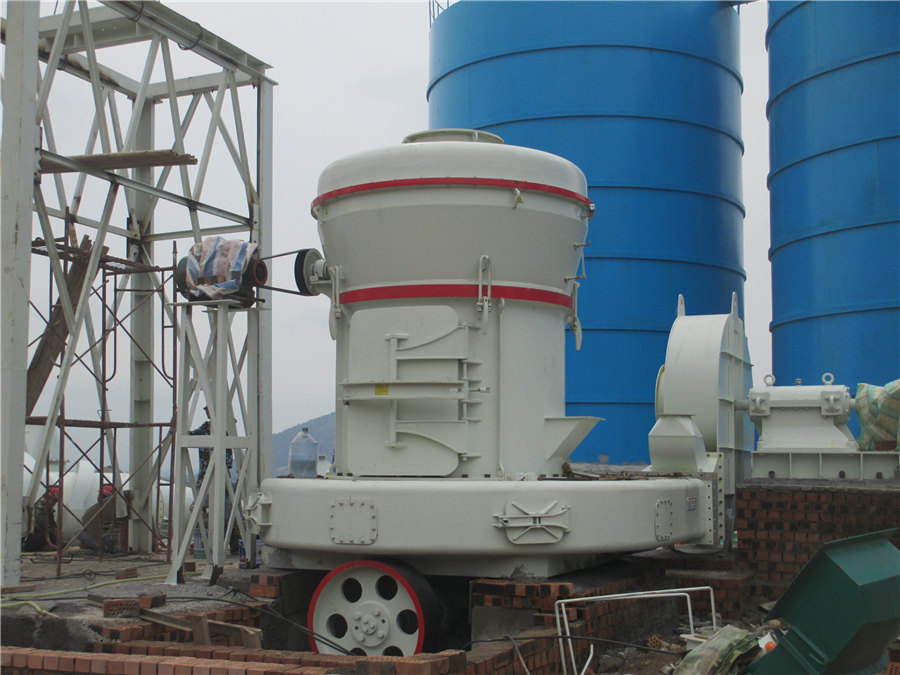
Fracture analysis on cage rivets of a cylindrical roller bearing
2008年9月1日 Li et al [8] analyzed the rivet fracture failure of the aeroengine cylindrical roller bearing cage, found the reason for the fault, and put forward the improvement measures to prevent rivet Highquality tube and pipe rollers for efficient bending in metalworking projectsTube Roller Efficient Pipe Rollers for Bending Baileigh“The grinding wheel is one component in an engineered system consisting of wheel, machine tool, work material and operational factors Each factor affects all the others Accordingly, the shop that wants to optimize grinding performance will choose the grinding wheel best suited to all of these other components of the process” Original SourceGrinding Wheel Selection Made Easy: Insider Tips and Tricks2013年1月1日 Damage to the roller surfaces has often caused problems with the reliability of highpressure grinding rolls in the past One reason for these damages is the overloading of the roll surfaces by Determination of the nip zone angle in highpressure grinding rolls
.jpg)
Gear Grinding Cracks: Causes and Prevention Measures
2023年9月25日 In conclusion, not grinding the root of the gear groove can improve the gear’s loadbearing capacity, prevent damage during gear grinding, improve the quality of gear grinding, reduce the load on the grinding process, 2018年2月14日 31 Dressing normal force and radial grinding wheel wear To examine the relationships between the grinding wheel load in the dressing process and the grinding wheel wear behavior in the grinding process, Klocke et al carried out dressing and grinding tests with a vitrified corundum grinding wheel with white aluminium oxide grains (WAO) of size F80 and Influence of different grinding wheel and dressing roller on the Topography of Grinding Wheels during Roller Dressing Abstract Vitreousbonded grinding wheels are widely used for machining features on aerospace components achieving high material removal rates under high pressure coolant Dressing is a vital stage in the grinding process to ensure a consistent wheel topography and performanceAn experimental study of the effects of dressing parameters on the 2013年9月13日 The correct way to measure concentricity on a grinding machine is 180º from wheel (back side), if the roll is supported on grinding seats For example, if the grinding seat is out of round this form will be transferred to the roll shell by the grinding wheel Runout will not be seen on the wheel side but when aPractical Roll Techniques Grinding Balancing Valmet
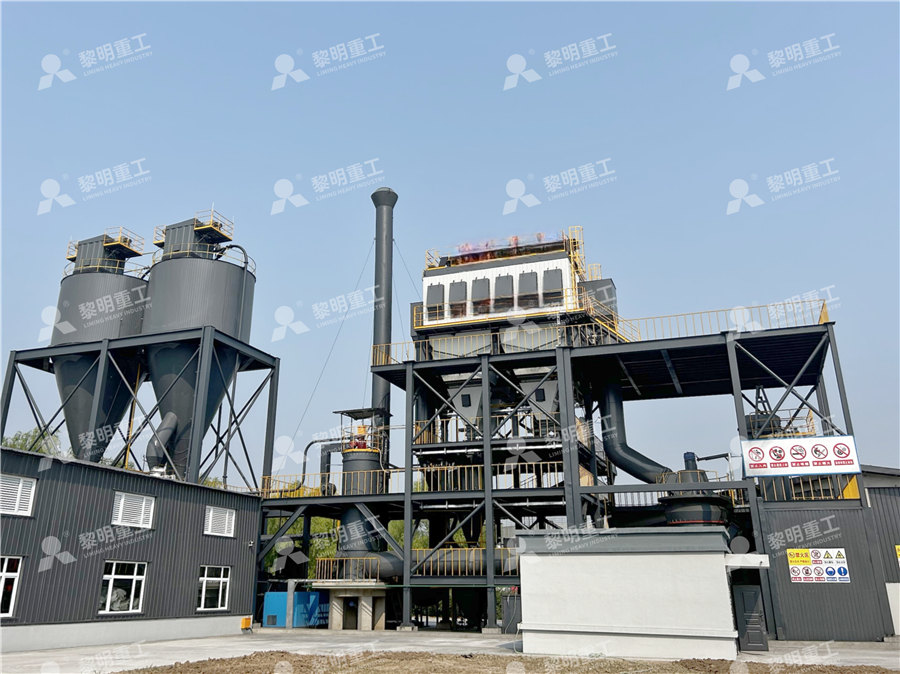
Failure analysis of oil refinery heater treater’s fractured fire tube
2023年12月1日 It is of utmost importance for any oil refinery to operate continuously for uninterrupted crude oil processing Some parts of refineries may be damaged and need to be evaluated to confirm the continuity of process safety [1]The initial design of fire tube, the method of manufacturing its main components, appropriate maintenance and operating conditions are 2011年7月1日 Fracture energy of roller compacted SFRC is higher than ordinary SFRC for the higher steel fiber volume ratio Discover the world's research 25+ million members; 160+ million publication pages;(PDF) Experimental Research on the Fracture Properties of Roller 2002©John Wiley Sons, Inc M P Groover, “Fundamentals of Modern Manufacturing 2/e” Material removal by action of hard, abrasive particles usually in the form of a bonded wheel • Generally used as finishing operations after part geometry has been established by conventional machining • Grinding is most important abrasive processLesson 6 GRINDING AND OTHER ABRASIVE PROCESSES KSU2007年7月1日 Request PDF Investigation of the effect of conditioning on the fracture of hard and soft wheat grain by the singlekernel characterization system: A comparison with roller milling A study has Investigation of the effect of conditioning on the fracture of hard
.jpg)
UBE Vertical Mill UBE Machinery Corporation, Ltd
We meet our customers' needs with our powder and grinding technology based on long tearm experienceAs for limestone, cement, metals, chemicals, biomass, ceramis, and fiber materials, various fields needs pulverization technology for materials into fine particlesWe will continue to contribute to our customers' productivity improvement and energy saving with our grinding Grinding uses a rotating wheel called a grinding wheel for this purpose, which has abrasive grains held by a binder (Figure 467) [54] These abrasive grains act like sharp tools that remove material from the workpiece When these abrasive grains wear Grinding Mill an overview ScienceDirect Topics