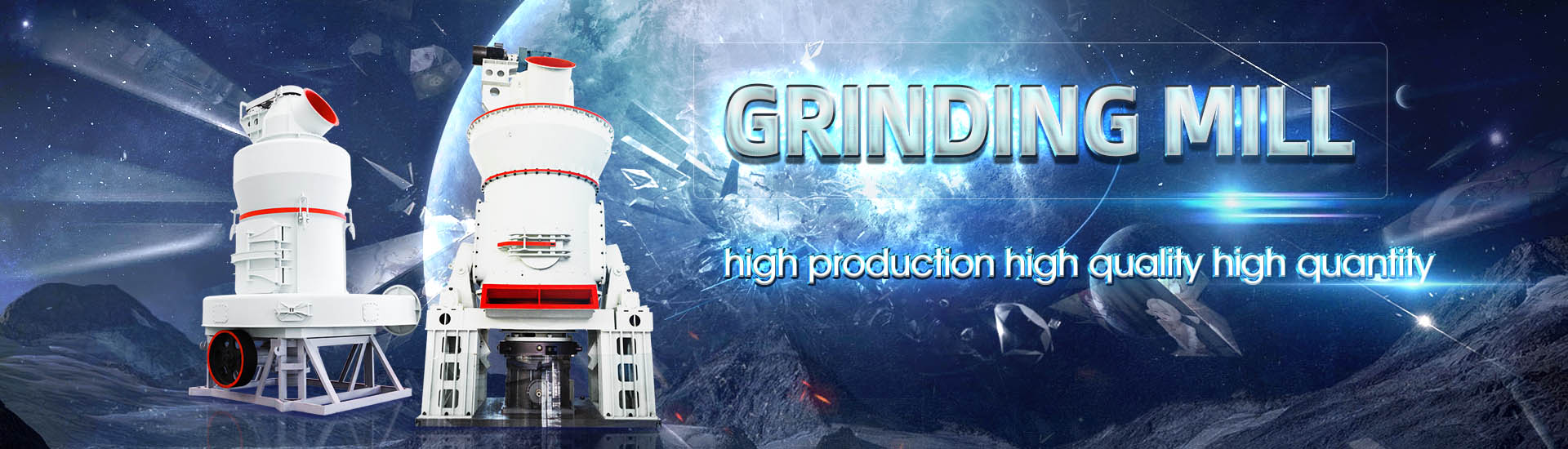
Ore grinding mill production cost
.jpg)
Mine operating costs and the potential impacts of energy and
2014年2月1日 Energy costs typically comprise one of the largest ongoing costs of mining operations, of which 70% is devoted to the comminution of the ore (Norgate and Jahanshahi, 1 Total Cash Cost (TCC) is a metric which includes all costs incurred at the mine site, such as open pit and underground mining, ore processing, (crushing, grinding, leaching etc) and onsite Methodology: Production costs data set World Gold CouncilThe Bond indices for ball mill grinding are often used to quantie throughput and grind product size, and Bond abrasion indices can be used for calculating grinding circuit metal costs Some mines use “modified” grinding index relationships to Process Operating Costs with Applications in Mine Please download the datafile to stresstest mining crushinggrinding costs, across capex, opex, maintenance, labor, electricity prices, CO2 prices, uptime utilization and ore grades Our 5 conclusions on the crushinggrinding industry Mining crushing grinding costs Thunder Said Energy
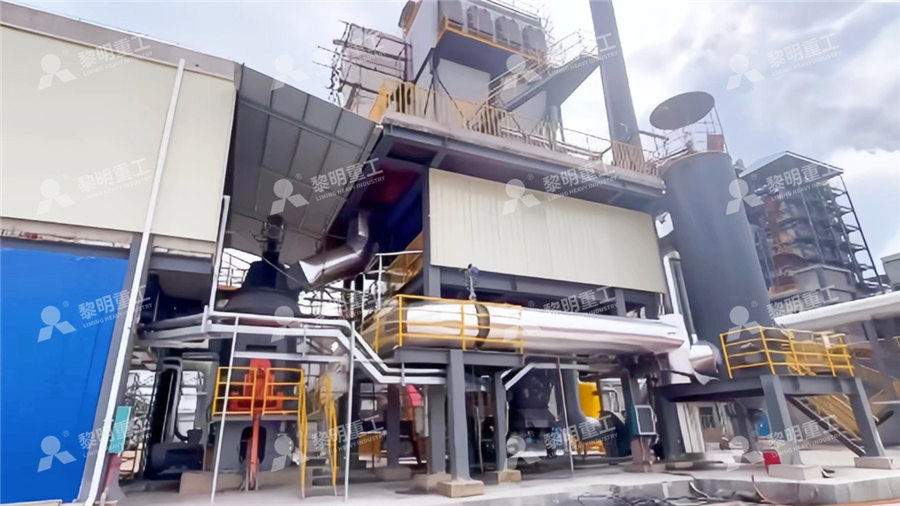
Mine operating costs and the potential impacts of energy and
2014年2月1日 This paper provides a breakdown of operating costs in 63 mines by dividing them into three main categories: mining, milling, and general and administrative (G A) costs The 2018年7月19日 This lecture overviews estimating methods for Mineral Processing capital and operating costs along with common aspects of financial analysis Content may be subject to copyright 1 EngineeringMineral Processing Short Course Cost AnalysisUnless capital data are available from a recent ore processing plant of the type and capacity envisaged, preliminary capital estimates will usually require some engineering and vendor Guidelines for mineral process plant development studies AusIMM2014年10月15日 In many specific metal industries (eg the refractory metals), milling can account for as much as 60% of the total energy cost to produce value added metals (Gupta, Development of ore sorting and its impact on mineral processing
.jpg)
Mine operating costs and the potential impacts of energy and
This paper provides a breakdown of operating costs in 63 mines by dividing them into three main categories: mining, milling, and general and administrative (G A) costs The study looks at 2021年11月8日 Illite ore industrial grinding mill machine can grind illite into powder up to 3000 mesh, including ultrafine mill, vertical mill, Raymond mill, wet mill, etc The stable lubrication system and the excellent sealing system Illite Ore Industrial Grinding Mill Machine SBM Rod Mill The rod mill is loaded with steel bars as grinding media and comprises five parts: cylinder shell, feeding system, discharge system, main bearing, and transmission system It is suitable for both dry and wet grinding to meet customer needs Materials with a Moh's Hardness of 5512 can all be handled by our millOre Grinding Mill2021年10月15日 Wollastonite industrial grinding mills can grind nonmetallic ores such as wollastonite into a fine powder and ultrafine powder The industrial grinding mills independently developed and produced by SBM mainly include highpressure suspension roller mills, HGM ultrafine grinding mills, and CLUM vertical roller mills, which can meet the production of Wollastonite Industrial Grinding Mill Equipment SBM
.jpg)
Control of ball mill operation depending on ball load and ore
the ore and the volume of the ready product The granularity of the ore is continuously reduced due to energy transfer by the grinding condition, which reduces their bond strength Ore size reduction is the result of the following three main fragmentation mechanisms 1 Abrasion 2 Cleavage 3 Fracture Figure 1 Grinding of ores inside a ball mill2017年7月26日 The power drawn and reduction achieved to the grinding mill feed will be maximized The grinding mill output will vary considerably with the Work Index If the feed size was 13,000 micrometers for the same grind production size, theoretical output from Fig (21) would change from about 90,000 tons per day on the 13 Work Index down to 65,000 How Ball Mill Ore Feed Size Affects Tonnage CapacityReducing Grinding Energy and Cost Magnetite Iron Ore Design Case Study A Jankovic and W Valery Metso Process Technology Innovation, PO Box 1028, Eagle Farm Qld, 4009, Australia ABSTRACT:Efficiency of the comminution operations is traditionally assessed based on operating cost and energy consumption(PDF) Reducing Grinding Energy and Cost Magnetite Iron Ore 2023年7月20日 Therefore, the rod mill is mostly used for coarse grinding of the previous period of ball mill, or grinding of brittle materials and materials against overcrushing, such as tungsten and tin ore before gravity separation; and (3) autogenous mill – it refers to the materials which themselves are collided and ground mutually to be crushed when the grinding mill rotates, and Ore Grinding SpringerLink
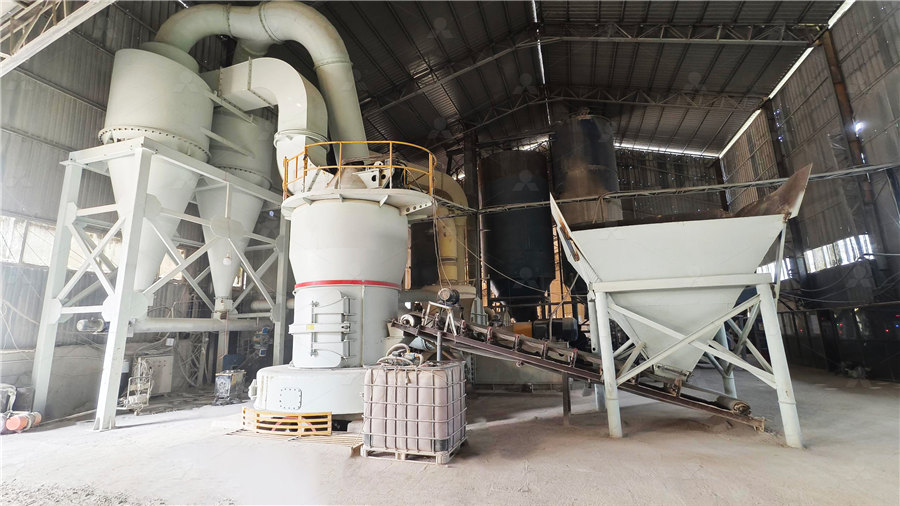
About Us SBM Ultrafine Powder Technology
As an excellent manufacturer of ore grinding equipment in China, (ultrafine grinding mills, vertical mills, superfine wet mills, coarse powder mills, etc), milling production line accessories (lifters, balers, silencers, dust bags, etc SBM's ore grinding equipment sells well all over the world with high quality and high cost 2021年9月23日 It can grind 100+ kinds of ores into a fine powder Barite industrial ultrafine grinding mill is a highly efficient stone powder making machine It can grind 100+ kinds of ores into a fine powder +17 which reduces labor intensity and saves production costs 5Barite Industrial Ultrafine Grinding Mill SBM Ultrafine Powder CLUM series of ultrafine gypsum powder vertical grinding mills are a new type of ultrafine industrial ore grinding equipment that integrates grinding, grading, powder collection and conveying +17CLUM Ultrafine Vertical Grinding MillFigure 1 : Grinding Power to produce various product sizes in a Ball Mill (9mm balls) and an Isa Mill (2 mm sand) (for KCGM pyrite concentrate) Chemistry Impacts The use of inert grinding media gives a crucial advantage to stirred milling in fine flotation and leaching applications Even if it were economic to grind to 10 microns in a steel Fine Grinding as Enabling Technology – The IsaMill
.jpg)
A guide to SAG Mill management
2024年5月17日 In the heart of any mineral processing plant lies the SAG mill, a workhorse responsible for reducing large rocks into finer particles Optimising its performance is crucial for efficient and costeffective production This article delves into the world of SAG mill management, exploring its importance and the various techniques employed to achieve peak grinding media directly affects energy consumption, product size and consequently the grinding costs [11] Proper selection of the grinding media reduces energy and material consumption in a ball millGrinding Media in Ball MillsA Review ResearchGate2016年9月1日 DIRECT CYANIDATION COST The following typical examples of cost distribution in Canada may be of interest FLOTATION AND CYANIDATION COST A typical example of cost distribution is to be found in the following 1936 figures for a 1000tonperday flotation and cyanidation plant in Ontario, Canada FLOTATION, ROASTING, AND Mineral Processing Operating Cost Estimate of Ore Treatment2024年8月15日 Grinding equipment: Applicable materials: Advantages: Energy Consumption: Ball mill: Various ores, from hard to soft Widely used for fine grinding; can operate in dry or wet modes based on process requirements High Rod mill: Largersized ores Ideal for coarse ore grinding, preventing overgrinding Low Autogenous millMineral Processing Plants: What You Need to Know
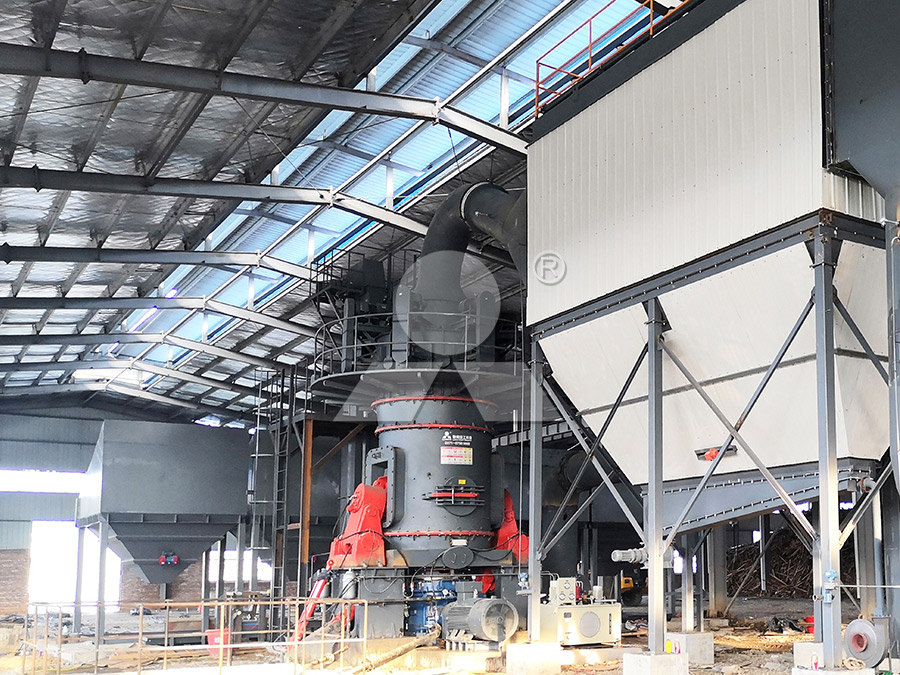
Phosphate Mineral Powder Grinding Mill SBM Ultrafine
2021年11月3日 HGM superfine powder mill The newly designed grinding roller grinding ring grinding curve improves the grinding efficiency The production capacity is 40% higher than that of jet mills and stirring mills, and the energy consumption is only 30% of that of jet mills Equipped with multihead cage type powder concentrator2009年1月1日 Also, equipment like ball mill is used at the final stages of grinding Among the comminution and grinding equipment, HPGR is increasingly utilized as tertiary crusher or primary mill because of Processing of Magnetite Iron Ores–Comparing Grinding OptionsThe cost of rubber lining is lower by 2030 % with the same putting into production, joint tests of lining with the customer are carried out Warranty is provided Generic Lining Products Overall wearresistant plates Used for cladding These are protruding parts of lining of the ore grinding mill In addition to protecting the Rubber Lining for Ore Grinding Mills and Mining and Processing 2019年12月15日 However, the demand for finer grinding has set new challenges for grinding technology; new technological advancements in mineral processing, including stirred milling, have opened the door for many new opportunities Lowergrade ore and finely distributed ore require finer grinding than the traditional mill circuit product size (P80) of 75 μmBeneficiation of Gold and Silver Ores SpringerLink
.jpg)
(PDF) The Effects of Blasting on Crushing and Grinding
2003年1月1日 grinding production and cost associ ated with changes in blasting For reasons made clear in this paper it will be important to clarify the survivab ility and role of microf ractures in future study2021年10月26日 HGM superfine powder grinding mill The newly designed grinding roller grinding ring grinding curve improves the grinding efficiency The production capacity is 40% higher than that of jet mills and stirring mills, and Graphite Grinding Machine Powder Mill Equipmentproduction costs on a quarterly basis since 2012, as well as providing an industry cost curve for the latest available quarter 12 Why is this data important? mining, ore processing, (crushing, grinding, leaching etc) and onsite general administrative costs incurred in producing anMethodology: Production costs data set World Gold Council2023年4月24日 Grinding is the final stage of comminution, which reduces particle size to micron size level The size reduction is achieved by attrition, abrasion, and impact between the ore itself and between the ore particles and grinding media []According to Swart et al [], ball mills are mostly used because of their very high size reduction ratio, although they have a very low Grinding Media in Ball MillsA Review [v1] Preprints
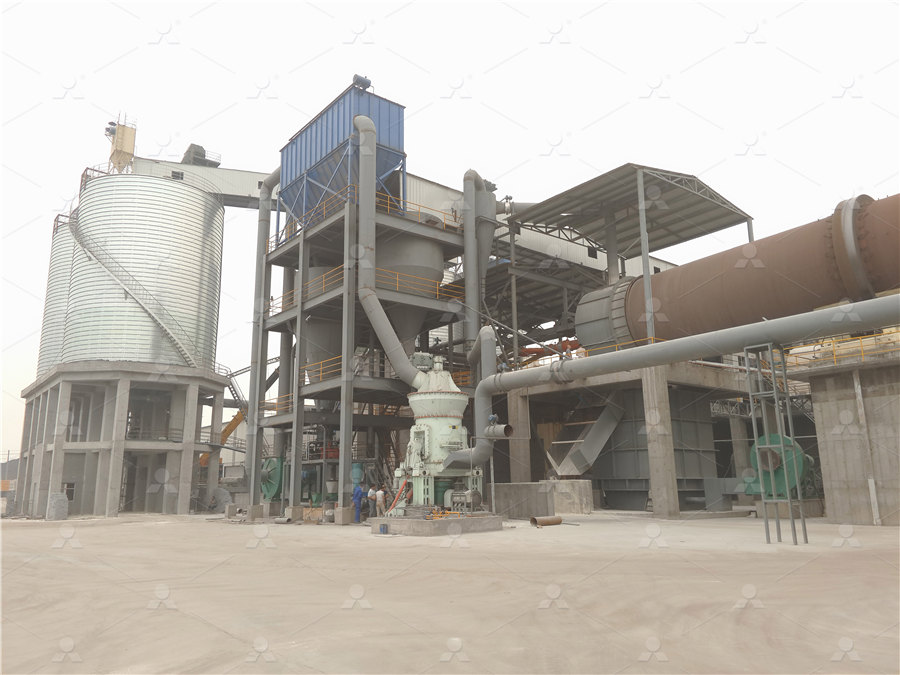
screens dramatically increase production, lower cost in ball mill
increase in mill capacity! Ball Mill Four (4) 5Deck Derrick Stack Sizers Oversize 82% Solids 167 t/h (135% Circulating Load) Screen Feed 291 t/h Pump Undersize 34% Solids 124 t/h Flotation Froth New Feed Underflow (Crushed Ore) 124 t/h Figure 2: New AO Apatit flowsheet Ball Mill Hydrocyclones Overflow (44% solids) 95 t/h Cyclone Feed 504 t/h 5 天之前 Additionally, the ball mill’s versatility allows parameters such as speed, feed rate and material composition to be adjusted, making it adaptable to different types of lithium ore This flexibility is essential to optimize the grinding process for each specific ore type, thereby increasing cost efficiency and resource sustainabilityBall Mill Is The Key To Grinding Lithium Ore JXSC Machinery2017年2月20日 All Grinding Mill Ball Mill Manufacturers understand the object of the grinding process is When choosing primary autogenous grinding, run of mine ore up to 200300 mm in size The use of high speed cutting and drilling tools has stepped up production, thereby reducing costs and permitting us to add other refinements Grinding Mill Design Ball Mill Manufacturer 911MetallurgistA crushing plant delivered ore to a wet grinding mill for further size reduction The size of crushed ore (F 80) was 40 mm and the SG 28 t/m 3 The work index of the ore was determined as 122 kWh/t A wet ball mill 1 m × 1 m was chosen to grind the ore down to 200 micronsGrinding Mill an overview ScienceDirect Topics
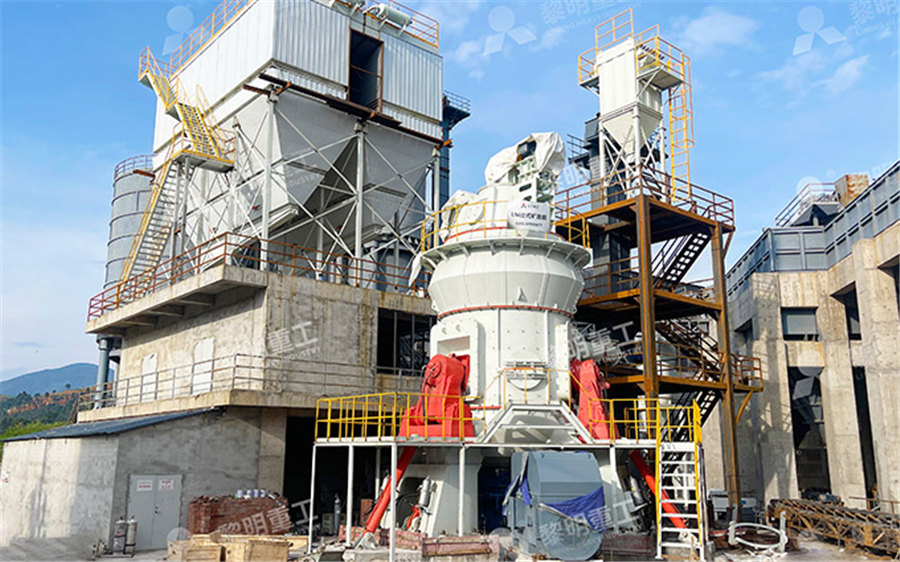
(PDF) Grinding Media in Ball MillsA Review ResearchGate
2023年4月23日 grinding media in a grinding mill with about 2630 wt% chrome by Chen et al [37] using a phosphate ore in a modified ball laboratory ball mill whose electrochemical potential could be controlled2022年8月3日 The iron ore processing and production process mainly includes three processes: crushing, grinding and beneficiation In the crushing process, the threestage closedcircuit crushing is more modern and suitable for highhardness iron ore crushing and can complete the work of ore crushing and partial dissociation, thereby improving the subsequent grinding Iron ore crushing and screening process SBM Ultrafine Powder 2024年2月26日 Oxidised pellets have become an indispensable highquality charge for blast furnaces Nevertheless, highquality pellet feeds are becoming scarcer and scarcer To broaden the range of sources of pellet feeds and Grinding of Australian and Brazilian Iron Ore Fines for SAG Mill ore hardness kWh/t: Energy required to grind an ore from F80 of 152 mm to T80 of 17 mm It is a resulting value from the SAGDesign test No other test accurately reports SAG hardness in kWh/t The required SAG energy is calculated using the Bond Wi to adjust the test T80 SAG energy to the design T80 energy Ball Mill ore hardness Design SAG mill production when you need it most: In day 1 and
.jpg)
Population balance model approach to ball mill optimization in iron ore
1 Population balance model approach to ball mill optimization in iron ore grinding Patricia M C Faria1,2, Luís Marcelo Tavares2 and Raj K Rajamani3 1 Vale SA, Brazil 2 Department of 2024年2月26日 To broaden the range of sources of pellet feeds and reduce the production cost of pellets, more steel mills are predicted to use coarse iron ore fines with a relatively low iron grade and low (PDF) Grinding of Australian and Brazilian Iron Ore Fines for Low 1, Raymond Mill, HC series pendulum grinding mill: low investment costs, high capacity, low energy consumption, equipment stability, low noise; is the ideal equipment for wollastonite powder processing But the degree of largescale is relatively lower compared to vertical grinding mill 2, HLM vertical mill: largescale equipment, high capacity, to meet the largescale production Iron ore grinding mill Grinding plants for Iron Ore2015年4月9日 Grinding Mills and Their Types satyendra; April 9, 2015; 12 Comments ; autogenous grinding, ball mill, grinding mills, hammer mill, rod mill, roller mill, SAG,; Grinding Mills and Their Types In various fields of the process industry, reduction of size of different materials is a basic unit operationGrinding Mills and Their Types IspatGuru
.jpg)
Grinding Media in Ball MillsA Review Preprints
2023年4月24日 This review paper is mainly going to focus on the effect of grinding media on ball mill performance Grinding media directly affects energy consumption, product size and consequently the grinding costs [11] Proper selection of the grinding media reduces energy and material consumption in a ball mill Different performances are achieved whenKey Components of Ore Powder Production Equipment: 1 Crushers The initial step in ore powder production is the reduction of ore size, which is accomplished by crushers Jaw crushers, cone crushers, and impact crushers are commonly used to break down the ore into manageable pieces 2 Grinding Mills Grinding mills are central to the powder Advancements in ore powder production process equipment: 2022年9月1日 The purpose of ore blending is simply to provide uniform mill feed which aids in improving production efficiency and reducing production cost Metso Minerals (2022) introduced an integrated approach, which is similar to the mine to mill approach ( Ouchterlony, 2003 , McKee, 2013 ), in quarriesTowards waterless operations from mine to mill ScienceDirect2016年3月19日 In this concentrating mill, however, it has been found that the middling product is of so little value that it would not be economically profitable to regrind and retreat this product The cost data above referred to has been compiled from actual operating results and shows the cost of milling both for the old 50ton plant and the new 100 ton concentrator, as is now in useOperating Costs of Gold Processing Plant 911Metallurgist