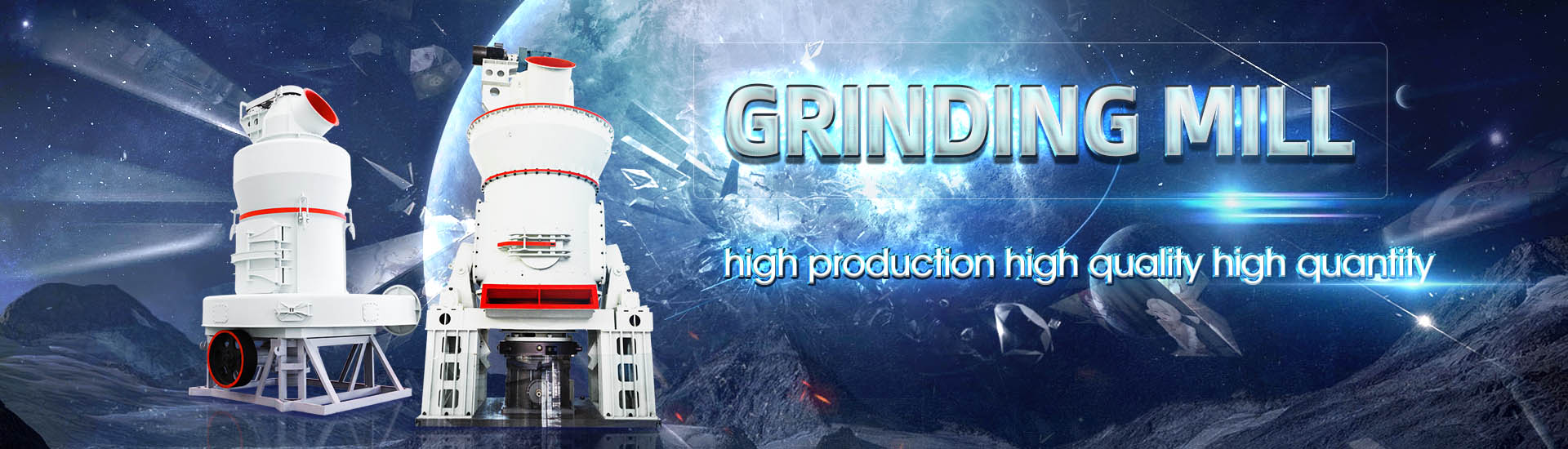
Safety technical measures for coal powder preparationVertical mill
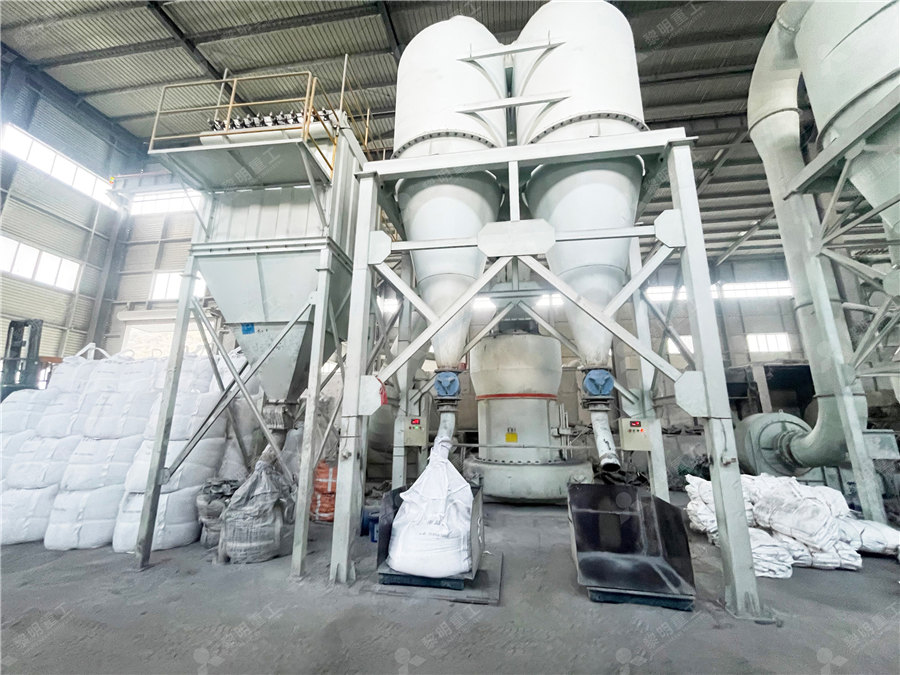
Ensuring Safety in Coal Mills – Best Practices and Precautions
By adhering to these best practices and implementing robust safety measures, the risks associated with coal mills can be significantly reduced Regular maintenance, effective dust To ensure the safety of coal mills, a combination of technical and procedural measures should be implemented: Dust Control: Effective dust control is crucial in preventing coal dust from Coal Mill Safety: A Critical Aspect of Power Plant Operations Coal Coal preparation activities (eg, use of dryers), coal gasification (eg, feeding and ash removal), and coal liquefaction processes may generate pointsource emissions of dust and heavy oils Environmental, Health and Safety Guidelines for Coal ProcessingCoal grinding is a critical process in various industries, particularly in power generation and cement production However, the process involves significant safety risks due to the Aspects of Coal Mill Safety Coal Mill Safety, Explosion and Fire
.jpg)
COAL HANDLING SAFETY Land Instruments International
Safe coal handling practices are designed to ensure that the fuel remains intact throughout its journey from the mine until the point at which it is ignited in the boiler It takes as little as 14 kg While appropriate precautions differ at the various stages of the process, this article concentrates on appropriate detection methods for coal mills Each generating unit at Merom has three COAL MILL Land Instruments InternationalThe safety record and availability history of coal pulverizing systems in the electric utility industry is com mendable The potential for fires and explosions inherent in air and pulverized coal Fire and Explosion Prevention in Coal Pulverizing SystemsThe raw coal is pulverized in the vertical cylindrical mill, and the pulverized coal is lifted to a powder separator by another bucket elevator The powder separator consists of a centrifugal Coal Pulverization System: Explosion Prevention and Process Control
.jpg)
COAL GRINDING SYSTEMS SAFETY CONSIDERATIONS PEC
Scrap metal in a coal mill is particularly dangerous during mill shut down or start up Fires or explosions most likely occur during startup and shutdown of a coal mill system If a small This document discusses safety aspects of coal mill operations It outlines the general safety rules, ignition process, oxygen concentration limits, protection measures, and safety control Coal Mill Safety PDF Coke (Fuel) Coal Scribd2 After the break, particle size suitable materials are transferred to the European version of the Tshaped device or mediumspeed Tshaped grinding mill, LM milling machines and other coal milling equipment; 3 Coal particles in the coal grinding mill, coal pulverizer machine, coal ObserverBased and Regression ModelBased Detection of Emerging Faults in Coal Mills Peter Fogh Odgaard, Sten Bay Jørgensen, in Fault Detection, Supervision and Safety of Technical Processes 2006, 2007 2 THE COAL MILL The work presented in this paper, is based on a Babcock MPS 212 coal mill used at Elsam’s Nordjyllandsværktet Unit 3 However, the Coal Mill an overview ScienceDirect Topics
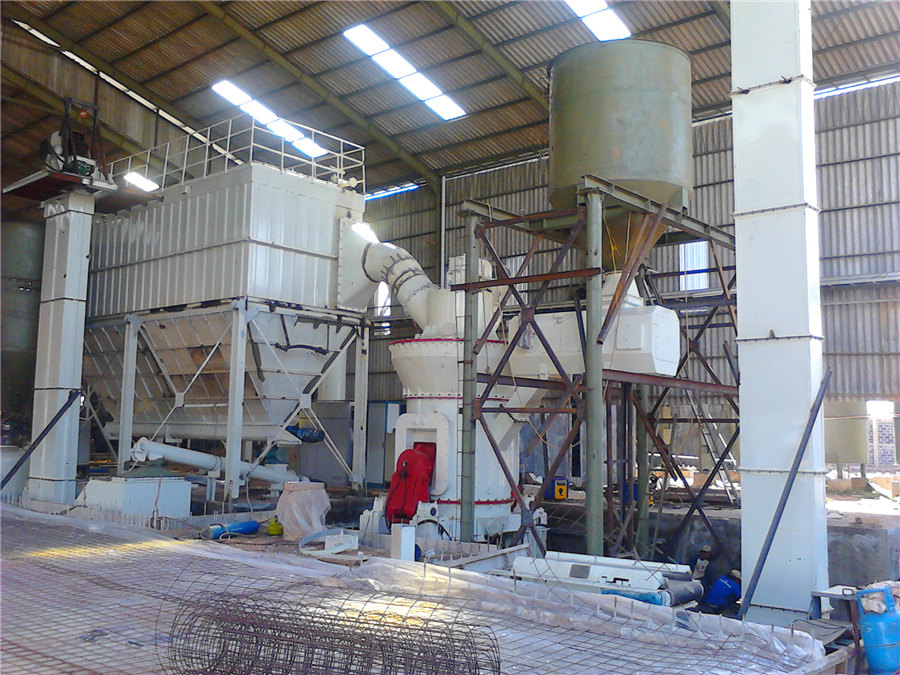
Coal Dust Explosion Protection: Ensuring Safety in industries using
Coal dust explosions are among the severe hazards in industries using coal, posing significant risks to personnel and infrastructure These explosions occur when fine coal particles become airborne and come into contact with a heat source in an enclosed environment, leading to a rapid combustion event Given the catastrophic potential of such incidents, robust measures for coal 2020年8月12日 In a power plant, the coal mill is the critical equipment, whose effectiveness impacts the overall power plant efficiency Uniform coal feeding mass flow rate and required particle size and temperature at the outlet channel throughout with better classifier performance are crucial indicators that characterize the coal mill performanceAn investigation of performance characteristics and energetic also find an application in grinding a wide variety of coal types in cement and power plants Gebr Pfeiffer SE (GPSE) describes its vertical roller mills for coal grinding and provides a case study of an MPS225BK installed at CBR’s Lixhe cement works in Belgium COAL GRINDING Figure 1: MPS coal grinding mill with SLS highefficiency classifierCOAL GRINDING IMPS: more than meets the eye Gebr PfeifferThis document discusses safety aspects of coal mill operations It outlines the general safety rules, ignition process, oxygen concentration limits, protection measures, and safety control systems for coal grinding The key points are: combustible dust or gas must not exceed explosive concentrations; oxygen must be controlled below critical levels; and ignition sources must be Coal Mill Safety PDF Coke (Fuel) Scribd
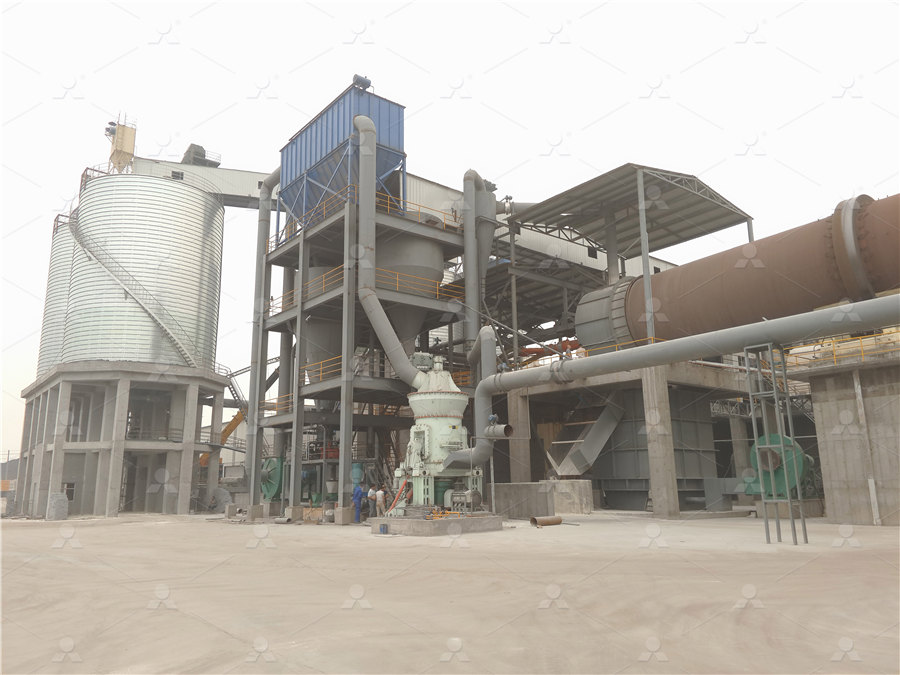
coal grinding machine CHAENG
Process introduction Vertical coal mill, also known as vertical roller coal mill or vertical coal grinding mill, is a mechanical equipment for crushing and grinding coal into coal powerMainly used for grinding raw coal, bituminous coal, and other fuels into coal powder, which is supplied to rotary kiln and other kilns in the cement plant and thermal power plant2009年1月1日 Wider coal lines and larger power plant units necessitate measures for increasing the capacity of the mills without driving up power consumption and installation costsCFD Modeling of MPS Coal Mill for Improved Performance and SafetyProcess introduction GRMC coal vertical mill produced by CHAENG adopts a special structure design and production technology, and the quality is up to the leading level in China It is the first choice equipment for grinding raw coal and bituminous coal 1 The raw coal is screened from the raw coal storage yard and then dropped onto the belt conveyor through the grid screenCOAL VERTICAL MILL Xinxiang Great Wall Machinery Co, LtdDesign measures preventing pulverized coal deposits: 6: Rollers can be lifted off: 7: Technical data; Throughput rate: up to 110 t/h: Mill drive: up to 2,000 kW: Number of grinding rollers: 3: MPS 200 BK coal mill, Krimzement Bakhchisarayski, Ukraine MPS 3070 BK coal mill, Jaypee Cement Balaji, Coal mill, gypsum mill, clay mill, etc Pfeiffer MPS mills
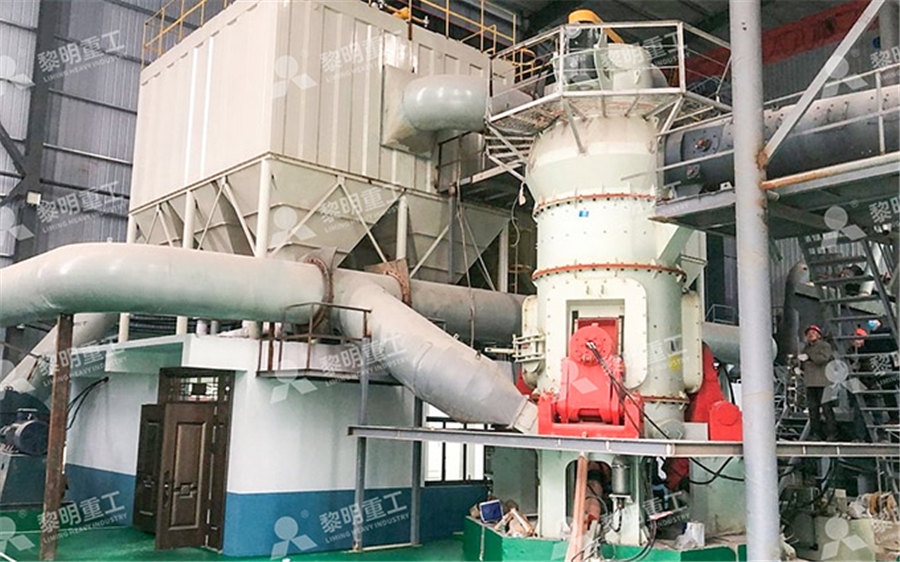
What is a Coal Grinding Mill
To convert raw coal into fine coal powder, coal grinding mills are essential Coal grinding mills are specialized equipment designed to break down coal into fine particles suitable for combustion The coal grinding process involves crushing and grinding coal into small particles, which are then heated to high temperatures in a furnace, producing steam that drives a turbine to generate 2022年5月31日 Mineral crushing is the main source of energy consumption in mineral processing According to statistics, this consumption accounts for about 35–50% of the total cost of the mine (Curry et al, 2014), or even higherIt may also account for 18% of the global electrical energy consumption (NapierMunn, 2015)More efficient crushing equipment needs to be Analysis of vertical roller mill performance with changes in Safe operation of coal grinding systems: Raw coal silo protection against fire and explosions Safe operation of coal grinding systems: Raw coal yard management The purchasing process for coal grinding systems needs changes Talk at a Coal Mill Safety, Explosion and Fire Protection Coal is sent into vertical mill through central entrance by coal feeder, and falls down on the grinding table Under the action of centrifugal force, coal is pushed to the edge of table Under the force of spring loaded roller, coal is compressed and sheared During grinding process, pulverized coal is blown upwards by hot air from primary air fanVertical mill for coal pulverizing in power plant Geckointech
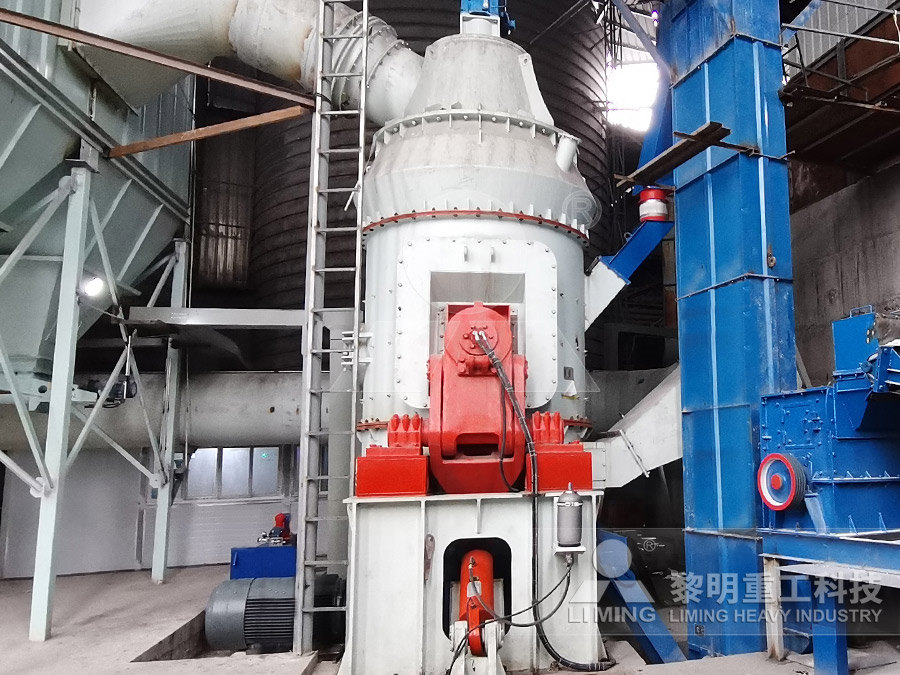
Experimental investigation on the preparation of macroscopic 0–1
2024年8月1日 In order to figure out the influence of the table revolution rate on the product size distribution, the table revolution rate was adjusted at the coal feeding rate of about 460 kg/h and the loading force of 06 MPa: 640 rpm for the basictype mill, 717 rpm for the Ⅰtype mill, 802 rpm for the Ⅱtype mill, and 861 rpm for the Ⅲtype millName: Coal Preparation Vertical Coal Mill For Coal Chemical Industry Type: Coal Grinding Capacity: 10~90 T/h Motor Power: 1101120kwQuality Vertical Coal Mill, Limestone Vertical Mill factory, Vertical vertical roller mill with separator, cyclone, mill circulation fan, and electrostatic precipitator (EP) and EP fan as shown in Fig1 Pulverized final products, which is called kiln feed raw meal, are collected at the cyclone and EP Because of large pressure loss at the cyclone and in order to control mill gas flow, mill circulation fanVertical roller mill for raw Application p rocess materialsTechnical Data Capacity: 1TPH4TPH Application: The coal powder prepareation system is designed with safety measures, like antiexplosion value, inert gas fire extinguishing system 1The raw coal from storage and conveying system come into air swept coal mill for grinding The coal powder mass and heat transfer with 200℃~350℃ hot airPulverized Coal Preparation Production LineZK Ball MillCement Mill
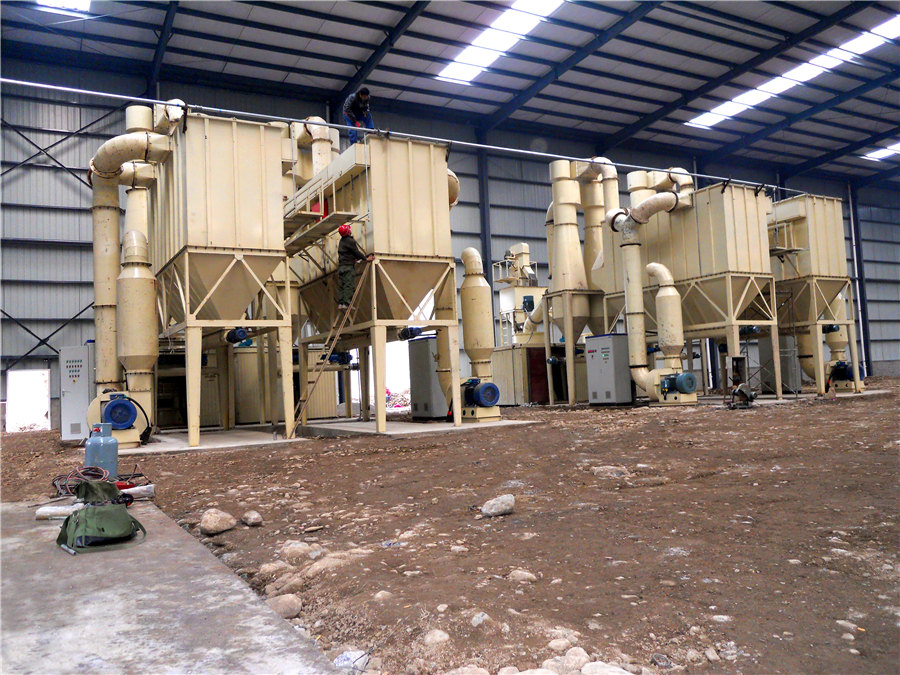
Fire and Explosion Prevention in Coal Pulverizing Systems
The safety record and availability history of coal pulverizing systems in the electric utility industry is com mendable The potential for fires and explosions inherent in air and pulverized coal mixtures has been studied for over 60 years Design and operating practices have evolved to a state that allows the safe, practicableIntroduction Hot Sale: Drying and grinding are two in one, and can dry while grinding Domestic largescale highend vertical coal mill LM vertical coal mill, also known as mediumspeed coal mill, is lunched by the company for the domestic market demand, the introduction of German advantages of integrated technology, combined with 30 years of advanced milling machine LM vertical coal millCompared with the vertical roller mill, the advantages of airswept ball mill are strong adaptability to raw coal quality, simple operation and low investment cost; the disadvantages are high power consumption and high noise Vertical Roller Coal Mill in Cement Plant Vertical Roller Mill Air 2012年11月17日 20 131Fineness Fineness is an indicator of the quality of the pulverizer action Specifically, fineness is a measurement of the percentage of a coal sample that passes through a set of test sieves usually designated at 50, Coal mill pulverizer in thermal power plants PPT
.jpg)
Pulverized Coal Preparation Pulverized Coal Grinding
Our Pulverized Coal Preparation Production Line is composed of Raw Coal Storage Transportation System, Grinding System, Dust Collecting System, Electrical Instrument Automation System By the consideration of safety 2022年1月27日 In view of the hidden dangers in the coal grinding system, cement production enterprises should improve the safety management system, take active preventive measures, grasp the key points of DISCUSSION ON SAFETY PRODUCTION OF COAL MILLING Coal grinding mills LOESCHE coal grinding mills are distinguished by characteristics that improve efficiency, safety and environmental protection, from the standard version to topoftherange installations Special versions are available with characteristics that meet special safety regulation or output control requirementsCoal Mills for Cement Plants LoescheSafe operation of coal grinding systems: Raw coal silo protection against fire and explosions Safe operation of coal grinding systems: Raw coal yard management The purchasing process for coal grinding systems needs changes Talk at a virtual seminar, November 2023 Accept the probability that the fire and explosion safety of your coal grinding system is nothing more than a mirageFire and explosion protection of coal grinding systems Where are
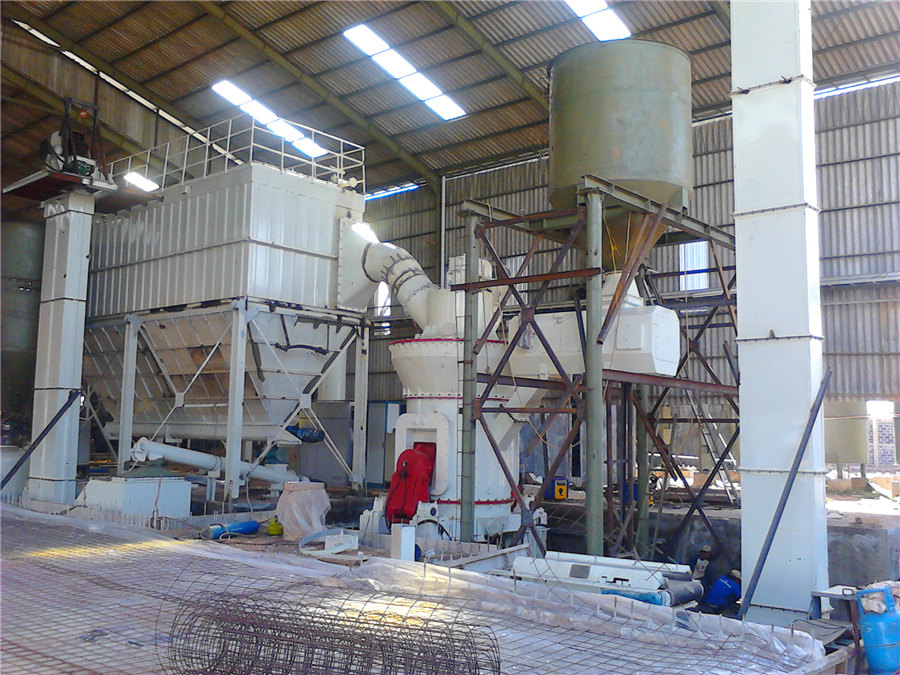
Live Webinar: Conventional kiln fuels preparation, storage, firing
This Cemtech Live Webinar considered vital developments in the field of conventional kiln fuels, including coal and petcoke sourcing, grinding and safety measures As such, presentations were delivered by Vincent Grosskopf, Coal Mill Safety Pty Ltd (Singapore), Dr Roland Aeckersberg, Loesche (Germany), and Virendra Rathore, JK White Cement (India)2015年11月1日 As presented by Andersen et al (2009) and Odgaard, Stoustrup, and Mataji (2007), coal moisture imposes limit on the maximum load at which a coal mill can be operated and the load gradient (how fast the mill may change its operating point), if it is desired that the pulverized coal entering the furnace has moisture content less than or equal to a certain value A unified thermomechanical model for coal mill operationHard coal is a sedimentary rock which was formed by deposition and carbonization of plant remains It is hard and resistant More than 50% of its weight is made up by carbon Therefore it is classified as highrank coal Other fossil fuels like subbituminous coals with high moisture contents as well as brown coal and lignite are lower rankedCoal mills for all requirements Gebr Pfeiffer• Coal • Cement raw material • Clinker / granulated slag • Industrial minerals, and • Ores The core elements of these plants are the Loesche vertical mills for drygrinding the abovementioned grinding stock Loesche has developed and built the largest and most efficient grinding plants for its customers Loesche plantsPROCESS OPTIMISATION FOR LOESCHE GRINDING PLANTS
.jpg)
Flow visualisation and velocity measurements in a vertical spindle coal
2003年10月1日 Request PDF Flow visualisation and velocity measurements in a vertical spindle coal mill static classifier☆ The aerodynamics within a reduced scale model of a vertical spindle coal mill Coal Mill Safety Free download as Powerpoint Presentation (ppt), PDF File (pdf), Text File (txt) or view presentation slides online This document discusses safety aspects of coal mill operations It describes the types of solid fuels used Coal Mill Safety PDF Combustion Coke (Fuel)DOI: 101016/jerd202406049 Corpus ID: ; Experimental Investigation on the Preparation of Macroscopic 01 mm Powdered Coal by a Vertical Spindle Mill @article{Shang2024ExperimentalIO, title={Experimental Investigation on the Preparation of Macroscopic 01 mm Powdered Coal by a Vertical Spindle Mill}, author={Ma Shang and Xiwei Experimental Investigation on the Preparation of Macroscopic 01 This article delves into the properties, benefits, and risks associated with pulverized coal, and outlines essential safety measures to mitigate these risks Properties and Uses of Pulverized Coal Pulverized coal is created by grinding coal into a fine powder, which increases its surface area and enhances its combustion efficiencyUnderstanding Pulverized Coal: Benefits, Risks, and Safety Measures
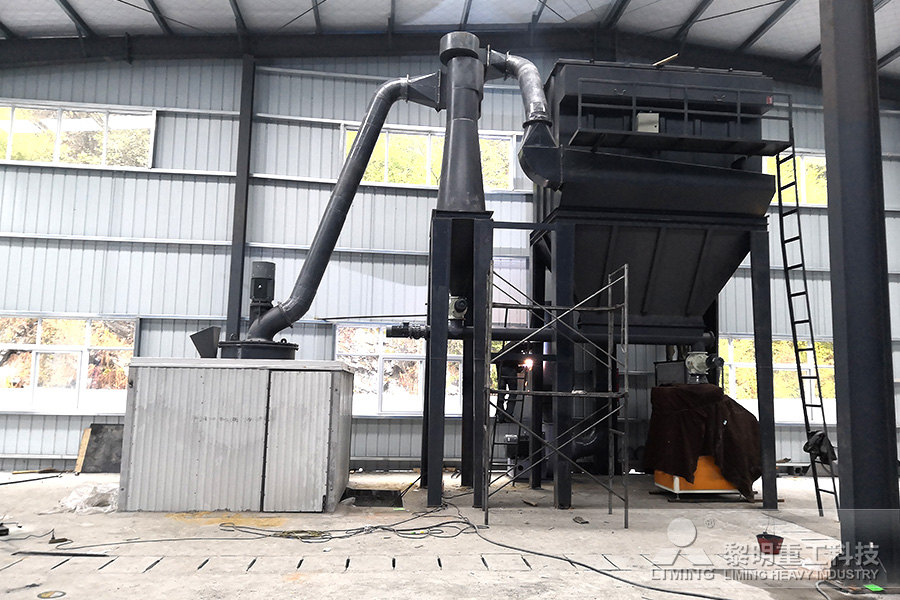
GRINDING AND SEPARATING TECHNOLOGY SYSTEMS
5 VERTICAL ROLLER MILL KTM Main data Type Min motor power Max motor power Min capacity Max capacity [kW] [kW] [t/h] [t/h] KTM 400 11 18,5 0,1 0,8 KTM 800 37 55 2 5 KTM 1000 55 90 4 8 KTM 1200 90 132 6 12 KTM 1400 132 200 9 18 KTM 1600 200 315 12 24 KTM 1800 315 400 20 38 KTM 2000 400 500 29 50 KTM 2200 500 630 39 64 KTM 2400 630 800 2014年1月1日 Two mill systems are employed for most coal grinding applications in the cement industry These are, on the one hand, vertical roller mills (VRM) that have achieved a share of almost 90% and, on (PDF) MPS mills for coal grinding ResearchGateCoal grinding is a critical process in the production of energy and industrial products like cement It comes with inherent risks Ensuring the safety of workers and equipment in coal grinding operations is paramount This article outlines key safety measures and best practices to mitigate the hazards associated with coal grindingEnsuring Safety in Coal Grinding Operations Coal Mill Safety 2017年9月11日 In this study, an extensive sampling study was carried out at vertical roller mill of ESCH Cement Plant in Luxemburg Samples were collected from mill inside and around the circuit to evaluate the (PDF) Performance Evaluation of Vertical Roller Mill in
.jpg)
COAL PREPARATION AND FIRING INFINITY FOR CEMENT EQUIPMENT
Previous Post Next Post Contents1 COAL PREPARATION AND FIRING11 INTRODUCTION12 2COAL RESERVES13 CHARACTERISATION OF COALS BY CHEMICAL131 31 Major components132 32 Minor Components14 4CHARACTERISATION BY PHYSICAL AND MECHANICAL PROPERTIES141 41 Coal Storage142 42 Variation of Physical and Here's an overview of the components that typically make up a coal powder preparation system: 1 Coal Handling System: Coal Storage: Facilities to store coal in a dry environment to prevent moisture absorption Coal Feeders: Devices that regulate the flow of coal from the storage to the processing plete set of coal powder preparation equipment