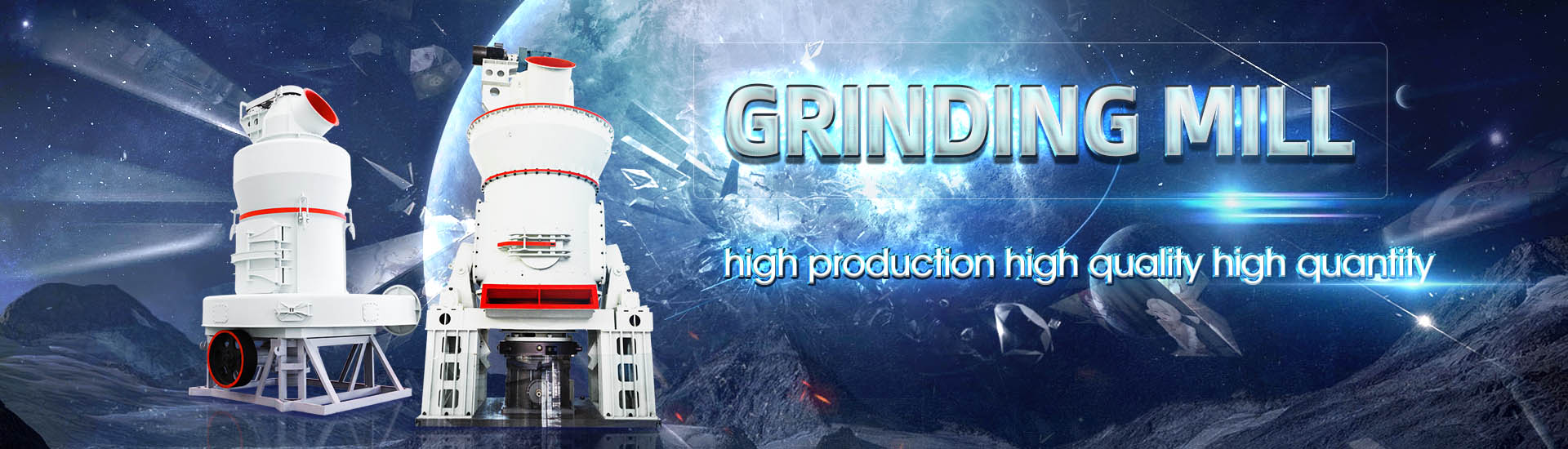
Cement grinding station equipment management method
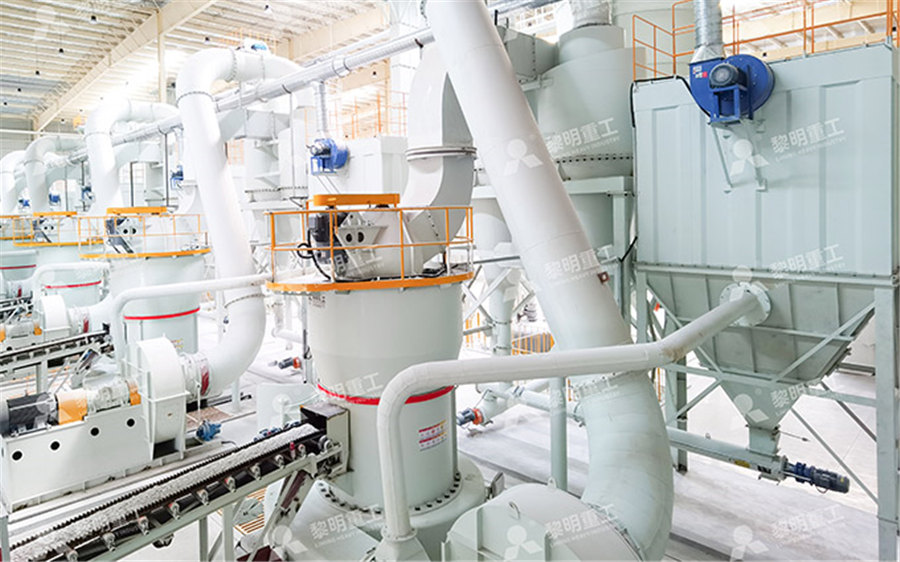
OPTIMIZATION OF CEMENT GRINDING OPERATION IN BALL MILLS
An evaluation of the grinding system and operation includes meaningful and critical inspection of all equipment, components and the process parameters by experts PEC Consulting can help carry out detailed evaluation of existing grinding systems and their operation and recommend As grinding accounts for a sizeable share in a cement plant’s power consumption, optimisation of grinding equipment such as ball mills can provide significant cost and CO 2BALL MILLS Ball mill optimisation Holzinger ConsultingThe cement industry uses a wide range of different systems in raw material, coal, and cement grinding While new plants mainly focus on highly energy‑efficient systems, using roller Thomas Holzinger, Holzinger Consulting, grinding system Cement production in cement grinding plants is performed by cogrinding clinker and gypsum in dedicated mills (eg ball mills, vertical roller mills), and by possibly using further cementitious Concrete Sustainability Council
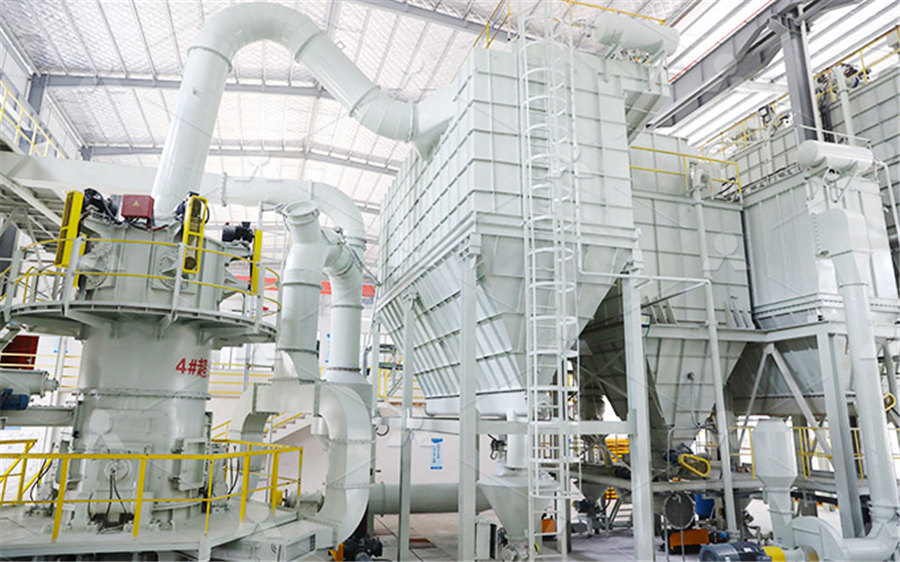
Monitoring Control Systems for Cement Plants Fuji Electric Global
Enabling stable operations by using optimal electrical equipment and monitoring and control systems to optimally control raw material processes, fi ring processes, and fi nishing 2004年11月1日 This paper describes the tools available for the analysis and optimisation of cement grinding circuits The application of the Bond based methodology as well as Cement grinding optimisation ScienceDirect2016年10月5日 In this chapter an introduction of widely applied energyefficient grinding technologies in cement grinding and description of the operating principles of the related equipments and comparisons over each other in EnergyEfficient Technologies in Cement GrindingThe implementation of intelligent optimization control system for cement grinding enables the system to operate under the most economical and optimal parameters The startup time of Application of Intelligent Optimal Control System for Cement
.jpg)
Energy and exergy analyses for a cement ball mill of a new
2020年5月1日 Nowadays, ball mills are used widely in cement plants to grind clinker and gypsum to produce cement In this work, the energy and exergy analyses of a cement ball mill 2018年7月1日 This study aimed at improving both the energy efficiency and product quality of the end product for a given cement grinding circuit by applying an accurate sampling Energy and cement quality optimization of a cement grinding circuitCondition in one of the grinding chambers of the mill Results of Optimization The graphical analysis presented in Figure 2 represents progress of grinding along the length of the mill after optimizing the grinding process rogress of grinding is clearly visible in Desired p the graphs Figure 2: Analysis of longitudinal samplesOPTIMIZATION OF CEMENT GRINDING OPERATION IN BALL MILLSPrevious Post Next Post Contents1 KILN ALIGNMENT ROLLER GRINDING2 1 Hot kiln alignment using electronic devices21 11 Advantages of this Technique22 12 Tools and Instruments Used23 13 Measurement Procedures Using Total Station24 14 General Notes3 2 Grinding of rollers tyres31 21 Grinding Method32 22 Grinding Machine33 23 KILN ALIGNMENT ROLLER GRINDING INFINITY FOR CEMENT EQUIPMENT
.jpg)
Grinding: Smarter Solutions Indian Cement Review
2022年8月10日 Cement grinding station can greatly digest the slag, fly ash, slag, coal gangue and other industrial waste residues near the city, is a green industry Evolution of cement grinding technology A cement mill is the The cement ball mill in this clinker grinding unit adopts the open circuit grinding method The open circuit grinding system has the advantages of a simple process, less equipment required, a small plant area, easy operation, convenient management, and a high operation rateClinker Grinding Unit for Sale, Buy Cement Grinding Station at 2019年1月3日 Clinker grinding technology is the most energyintensive process in cement manufacturing Traditionally, it was treated as "low on technology" and "high on energy" as grinding circuits use more than 60 per cent of total energy consumed and account for most of the manufacturing cost Since the increasing energy cost started burning the benefits significantly, Clinker grinding technology in cement manufacturinggrinding rollcement 3200 cm2/g ace to Blaine con ventionallyproduced cements from ballmill systems 2900 cm2/g, 3600 cm2/g, and 5100 cm2/g The grinding rollcement has by far the steepest par ticle size distribution line and therefore the narrow est particle size distribution, which very positively affects its strength developmentGrinding methods in the state of development INFINITY FOR CEMENT
.jpg)
New Features of Cement Grinding Station Design
2024年6月14日 If the cement grinding station and clinker production line are set near the limestone mine, unnecessary transportation expenses of cement mixture will be incurred Therefore, the cement grinding station is built near the sales area, which can save about 40% of the freight Improved cement grinding technology Cement grinding hasProduction of CKD and Kiln Pyroprocess Types Some past CKD reports and articles provide estimates of the amount of CKD that is produced and/or disposed by each kiln pyroprocessing type, ie, wet kilns, long dry kilns, preheater kilns and preheater/precalciner kilnsEverything you need to know about Cement Kiln Dust Generation Process data management and insights Process design basis, operational principles, control and regulation, process troubleshooting, calculation methods, and cement plants Work sessions are scheduled to allow for an interactive study of the design, function, and evaluation of grinding systems in a cement plant Cement Cement Production Seminar: Grinding2016年10月5日 In this chapter an introduction of widely applied energyefficient grinding technologies in cement grinding and description of the operating principles of the related equipments and comparisons over each other in terms of grinding efficiency, specific energy consumption, production capacity and cement quality are given A case study performed on a EnergyEfficient Technologies in Cement Grinding IntechOpen

CEMENGAL Engineering, equipment and assembly for
25 years in the cement industry supplying engineering and equipment for assembly and commissioning of clinker and slag Grinding Station, cement plants, metallic and concrete silos, vertical mills, horizontal mills, PLUGGRIND CEMENGAL has been awarded with a new contract for the supply of 2 nd Cement grinding station to ACICO Cement consisting of a complete cement mill workshop; Main equipment to be included within this new contract is related to a 5,200 Kws ball mill fully engineered by CEMENGAL with all the peripheral equipment and a 4 th generation classifier from Magotteaux XP4i130 for high Cemengal is a EPC contractor specialized in the Cement Industry As a leading cement plant builder, AGICO offers an expert cement grinding plant EPC service Cement Grinding Unit EPC Solution With a strong RD team, experienced engineers, and firstclass technical services, we aim to provide Cement Grinding Plant Expert Cement Grinding 2023年12月26日 As we all know, the dryprocess cement production line is commonly used in the cement industry The new type of dryprocess cement production process includes four main sections: Prehomogenization of raw materials, homogenization of raw materials, clinker firing, cement grinding, etc Raw material conveying system The raw material, including limestone, 6 Cement Equipment For Dryprocess Cement Production Line
.jpg)
Leading Supplier of Cement Plant Equipments Rotary
At present, it has completed over 60 new dryprocess cement clinker production lines of various sizes (3008000 tons/d), more than 10 pure low temperature waste heat power generation projects for cement clinker production lines and over High grinding efficiency For the structure, of the cement mill, we adopt the advanced obstructing equipment for internal powder, add the activated device to the fine grinding chamber, and there is the special grate plate at the end of the cement mill, which can reduce the size of the grinding medium, greatly improve the grinding efficiency, and achieve the purpose of high output and cement grinding Unitcemengal: engineering, equipment and assembly for the cement industry EXPERTS IN GRINDING STATION 25 years in the cement industry supplying engineering and equipment for assembly and commissioning of clinker and slag Grinding Station, cement plants, metallic and concrete silos, vertical mills, horizontal mills, PLUGGRIND modular and portable grinding modular and portable grinding station plug and grind verticalHighEfficiency Cement Separators and Classifiers has been supplied by AGICO for 15 years, this equipment is mainly used to improves cement grinding sCement Seperator Improves Cement Grinding System
.jpg)
Cemengal is a EPC contractor specialized in the Cement Industry
25 years in the cement industry supplying engineering and equipment for assembly and commissioning of clinker and slag Grinding Station, cement plants, metallic and concrete silos, and the client is extremely satisfied with the service received by Cemengal Project Management More information Grinding Station PLUGGRIND More information Expert solutions, from equipment supply to complete plant delivery Fives is renowned for its extensive experience in industrial plant project management and has installed more than 80 complete cement production lines around the world We bring our original equipment manufacturer (OEM) expertise and our engineering, procurement and construction (EPC) Fives Project management for cement and mineral grinding Grinding: the material is ground between rollers and grinding table while passing from the center of the table to the nozzle ring The commnation method belongs to the most efficient grinding processes applied in the cement manufacturing Cement Manufacturing Process INFINITY FOR 25 years in the cement industry supplying engineering and equipment for assembly and commissioning of clinker and slag Grinding Station, cement plants, metallic and concrete silos, vertical mills, horizontal mills, PLUGGRIND MODULAR AND PORTABLE GRINDING STATION
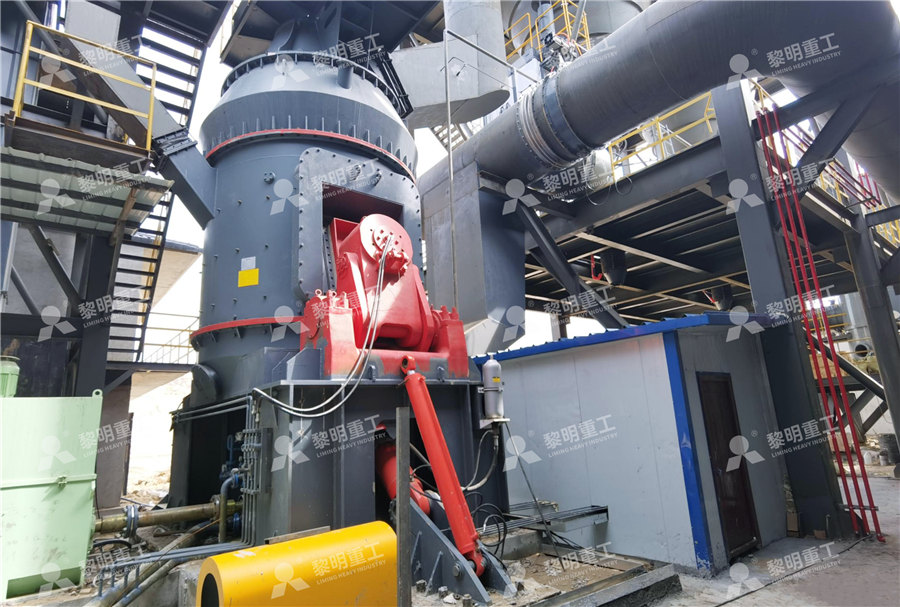
CEMENGAL Engineering, equipment and assembly for the cement
25 years in the cement industry supplying engineering and equipment for assembly and commissioning of clinker and slag Grinding Station, cement plants, metallic and concrete silos, vertical mills, horizontal mills, PLUGGRIND modular and portable grinding stations Previous Post Next Post Contents1 INSPECTION OF THE KILN SYSTEM11 GENERAL12 INSPECTION121 Supporting Roller and Bearing122 Livering123 Drive station124 Thrust Rollers125 Kiln Shell126 Seals at inlet – and outlet end127 Pneumatic system (if relevant)128 Description and mode of operation13 METHODS OF EXAMINATION131 INSPECTION OF THE KILN SYSTEM INFINITY FOR CEMENT EQUIPMENTWhat AGICO Offers AGICO is specialized in design and supplies equipments for complete cement production lines of different scales, capacity from 300t/d to above 8000t/d;About AGICO Cement Production Line Solutions Providergrinding (see Figure 2) However, the combination of cement fineness and slag fineness in interground cement may not be the optimum to provide the maximum strength for a given Blaine Separate grinding offers the option whereby the fineness ratio of the components can be optimised, eg through kriging (Stein, 1999) Therefore, blended cements fromSEPARATE OR INTERGRINDING? Loesche
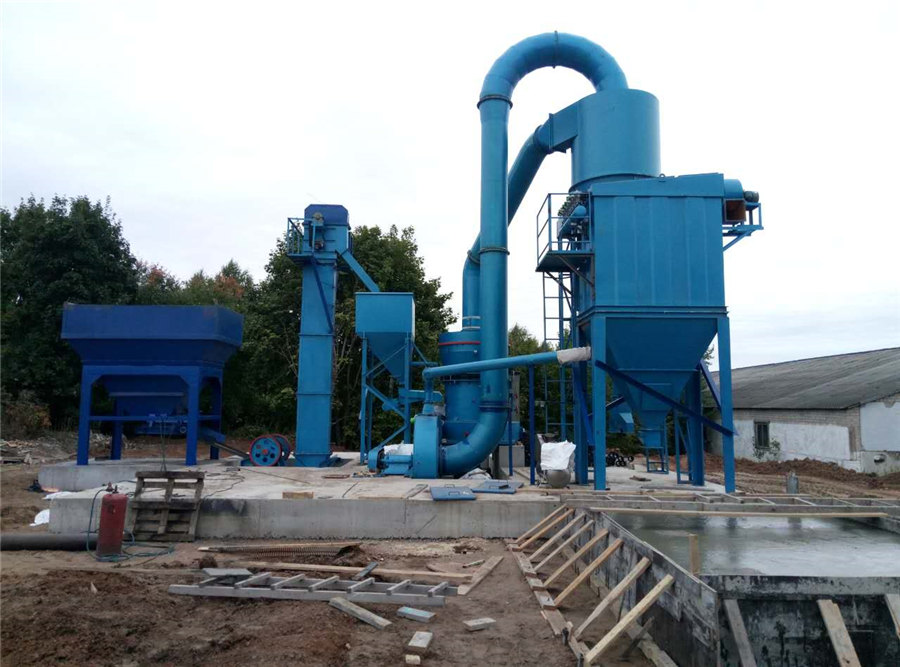
Energy and exergy analyses for a cement ball mill of a new
2020年2月1日 They showed that the polymerbased grinding aid increases the specific surface, prevents agglomeration and ball coatings, and improves the roundness, fineness and fluidity of the ground cementBrundick, H, “Drying and grinding of extremely moist cement raw materials in the Loesche mill,” ZKG International, No2, 1998, pages 6471Brundick, Horst, and Schäfer, HeinzUllrich, “Loesche mills for clinker grinding,” Asian Cement and Construction Everything you need to know about cement Materials Preparation The amount of feed in the mill can be tested by 3 methods: Grinding roller limit device clearance; The power of the mill Cement Grinding Station; Cement Silo; Raw Mill Grinding Solution; Spare Part Girth Gear; Ball Mill Liner; The second is the calcination equipment and calcination method according to limestone conditions How to Improve Grinding Efficiency of Vertical Roller MillBased on customer needs and years of experience in cement equipment manufacturing, AGICO Cement develops a lowcost and highly efficient EPC solution for cement grinding unit – modular mobile (MMG) cement grinding plant Compared to the traditional grinding station available on the market, the MMG cement grinding plant is more suitable for the small and mediumsized Modular Mobile Cement Grinding Plant For Sale AGICO Cement

Modern Processing Techniques to minimize cost in Cement
Low investment costs due to reduced number of equipment 62 Separate Grinding In separate grinding, each component can be ground to the desired fineness and the concentration of one component in the finer fraction can be avoided • Features Separate weighing and proportioning of mill feed and intermediate productsMAINTENANCE METHODS Adequate maintenance program can be achieved by the use of three different methods: Unscheduled maintenance, preventive maintenance and predictive maintenance (Fig 1) Management and Cement Ball Mill Maintenance INFINITY FOR 2023年10月19日 Use of HighEfficiency Equipment: Invest in modern, energyefficient grinding equipment, such as vertical roller mills (VRM), which can significantly reduce energy consumption Waste Heat Recovery: Implement Clinker Grinding Techniques in Cement This method is advantageous due to its lower fuel consumption and reduced time of processing, making it a costeffective and efficient method in cement production Wet Process Conversely, the wet process involves mixing the crushed raw materials with water in a StepbyStep Guide to the Manufacturing of Cement PRACTICAL
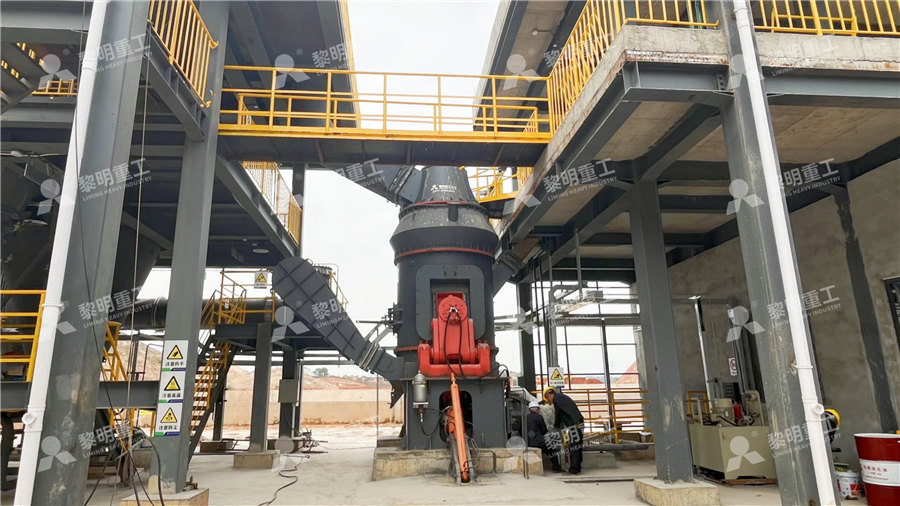
Grinding in Cement Manufacturing: Key Process, Types of Mills,
The choice of grinding mills, operational settings, and energy management all contribute to the overall efficiency and quality of the cement produced By optimizing these factors, manufacturers can produce highquality cement that meets the demands of modern construction while also minimizing energy consumption and production costsThere are two types of mills commonly used in the modular mobile grinding station: ball mill and vertical roller mill (VRM) We will select the appropriate mill module according to the specific needs of customers The mill is the core component of a grinding plant All other equipment in the grinding station serves the purpose of grindingModular Grinding Plant AGICO Cement Machineryprocess of the modular grinding station Need To Know: we can provide all equipment of modular mobile grinding plant AGICO CEMENT supplies EPC projects for both cement plant and single cement plant equipment CONTACT INFO +86 s 19F, Suite B, Global Trade Mansion, Wenfeng Avenue, Anyang, Henan, ChinaModular Mobile Grinding Plant, Portable Grinding Plant Cement Previous Post Next Post Contents1 Ball charge optimization2 1 How to use the BP21 2 Description of the main indicators used in this BP2101 The residue on 2mm/4mm before partition wall2102 Material filling level and ball charge expansion211 Cement mill specific power 1st compartment 212 Raw mill specific power 1st compartment Ball charge Ball charge optimization INFINITY FOR CEMENT EQUIPMENT
.jpg)
Everything you need to know about Automation and Optimization
The quality aspects of analytics and how they provide data for cement plant management and control have been covered in another chapter the sampling method, and the type and sophistication of the laboratory equipment installed The configuration of lab equipment (grinding mills, presses, fusion machines, Xray analyzers, 3 2019 Cement Concrete Road made at Solapur grinding unit as per Consent to operate condition 19,983,025 AAQMS maintenance and Calibration, Environment Monitoring report Opacity meter upgradation, DG report, Water tanker for tree plantation etc 1,081,984 21,065,009 4 2020 Cement Concrete Road made at Solapur grinding unitZuari Cement Limited Energy Management 2021 (Solapur Grinding