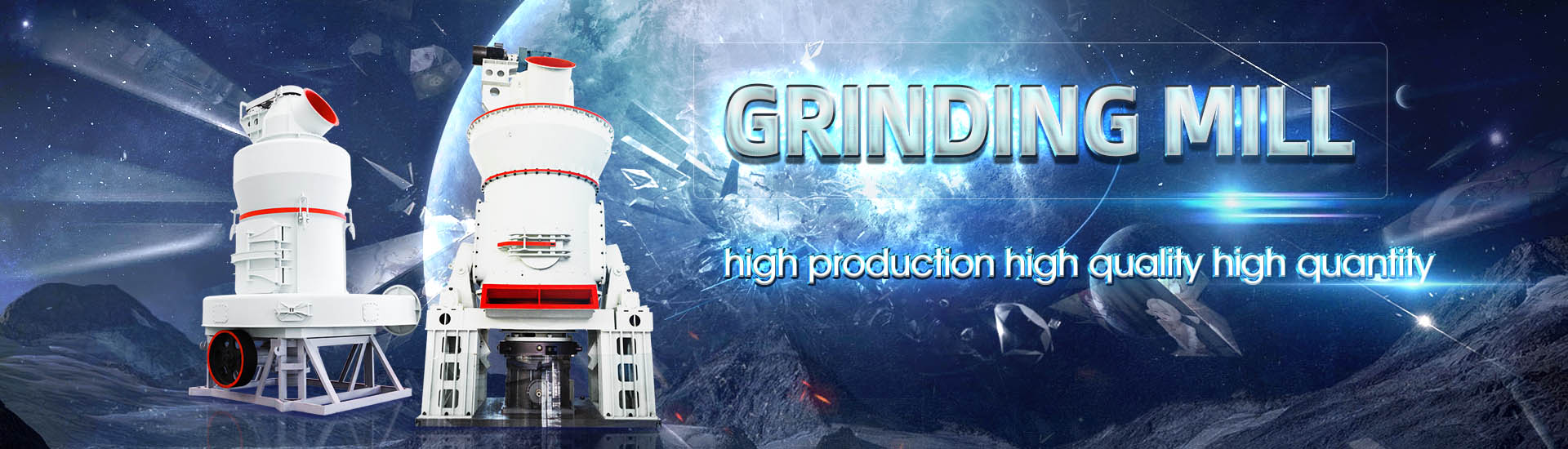
What is the pressure of the hydraulic pipeline of 165 grinding mill
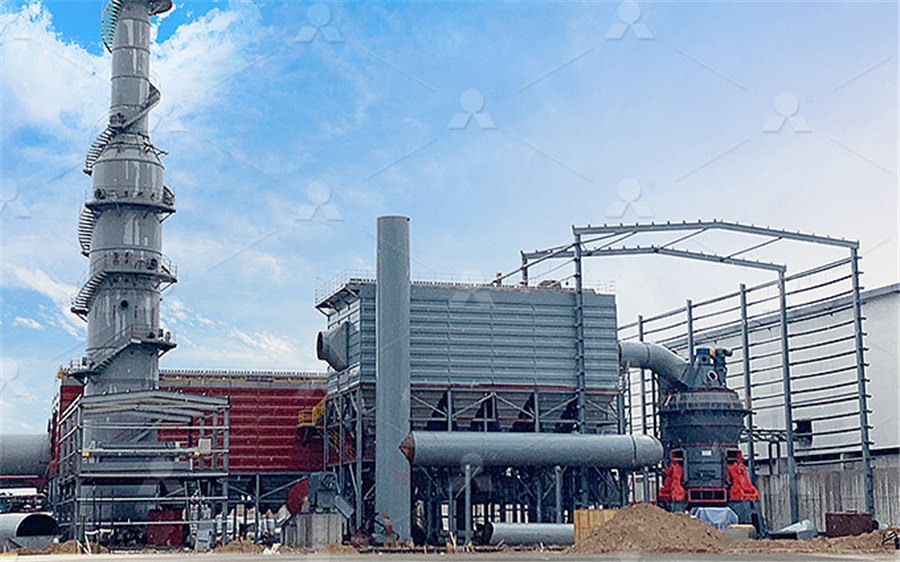
HYDRAULIC PIPING STANDARD HANDBOOK
Hydraulic Piping Standard Handbook is intended for professionals working within industries where hydraulic piping is used This Handbook offers relevant information in one package for anyone Pressure = 2,000 psi Example: How much torque does a motor develop at 1,200 psi, 1500 rpm, with 10 gpm input? Example: How much torque is developed by a motor at 12 horsepower and Hydraulic CalculationsWhat are the necessary requirements to move from a piping or pipeline system idea to its completion? The basic premise of this book is that at the heart of those requirements are a Piping and Pipeline Calculations Manual: Construction, Design Barlow’s Formula is a calculation used to show the relationship between internal pressure, allowable stress (also known as hoop stress), nominal thickness, and diameter It is helpful in Barlow's Formula Calculator Internal Pipe Pressure Capacity
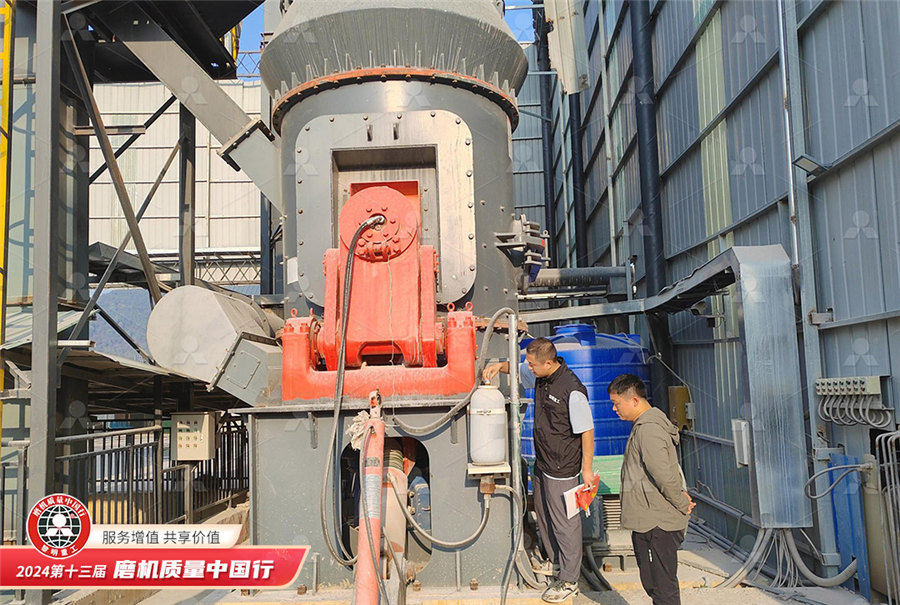
Pipeline Hydraulics and Design Optimized Technical Solutions
As a standard for comparison, 20inch pipe will be assumed with a source pressure of 800 psi, and a delivery pressure of 150 psi The product to be transported is 60°F natural gas with a Pipe pressure design for the separation station and steam lines is 15 MPa, and for brine line ranges from 15 to 4 MPa Pipe diameters are generally 250 to 1219 mm nominal pipe size Piping Hydraulics Fluid Flow Line Sizing and Material Selection In this article, we will consider the key concepts of pressure and flow and how they apply to hydraulic systems – as it is the pressure and flow which enable work and motion to be An Introduction to Hydraulic Pressure and Flow2023年9月1日 When a force is applied to the hydraulic fluid at one end of the system, it generates pressure that propagates throughout the entire piping network This pressure is Hydraulic Piping: Fundamentals, Types, and Significance
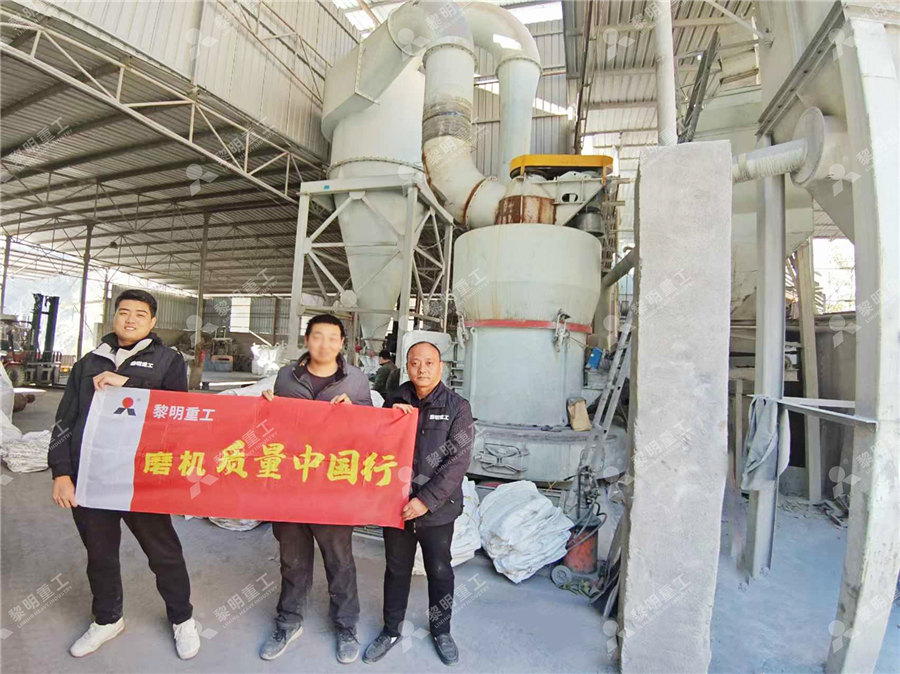
Pressure Transient Model of WaterHydraulic
2018年3月7日 Transient pressure investigation of waterhydraulic pipelines is a challenge in the fluid transmission field, since the flow continuity equation and momentum equation are partial differential, and 2022年9月21日 Hydraulic piping is used to convey fluids under high pressure in various industrial applications place to get it is from Global Steel Tubes +86 t is Hydraulic Piping? global steeltube2016年1月10日 On a 11’6” x 22’0” Ball Mill, the trunnion bearing lubrication system provides continuous low pressure flood oil for cooling and lubrication of the bearings, and high pressure oil for hydrostatic lift of the feed and Ball Mill Trunnion Bearing Lube SystemThe hydraulic integrity of a water distribution system is defined as its ability to provide a reliable water supply at an acceptable level of service—that is, meeting all demands placed upon the system with provisions for adequate pressure, fire protection, and reliability of uninterrupted supply (Cesario, 1995; AWWA, 2005)5 Hydraulic Integrity The National Academies Press
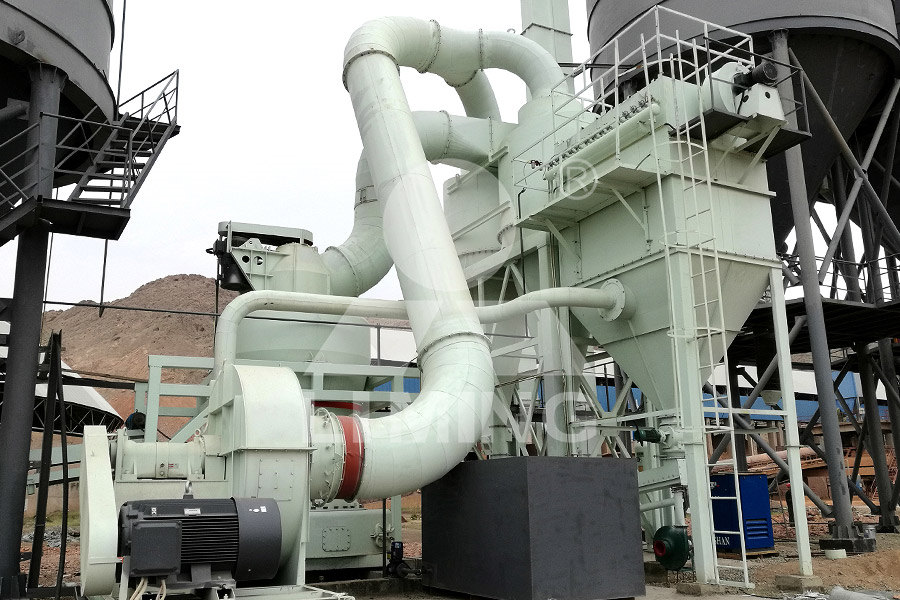
Pipeline Hydraulics and Design Optimized Technical Solutions
For the sake of illustration, a simplified hydraulic analysis will be performed where gas is transported from a source location to a delivery point located 200 miles away As a standard Pipeline Capacity Vs Source Pressure 200 Miles, 150 psi delivery, 20" pipe 050 060 070 080 090 100 110 120 130 140 150Generally accepted methods for calculating pressure losses within flat pipelines as presented in literature and used in praxis, are based on the Reynolds number, which considers the viscosity and density of fluid, internal pipe friction coefficient, pipe geometry, and oil circulation velocity Such an approach contains serious inconsequentiality Namely, the only nominal values for Determination of Pressure Losses in Hydraulic Pipeline Systems The Hydraulic Piping Standard Handbook assists in the above mentioned engineering process by providing relevant information and standards for this project input phase This is when the piping requirements are defined such as desired working pressure, maximum pressure, maximum flow rate, acceptable pressure drops and classification requirementsHYDRAULIC PIPING STANDARD HANDBOOKGiven that the hydraulic gradient is computed by subtracting the head, h 1, at the origin from the head, h 2, at a distance ΔL from the origin in the direction of flow, and then dividing by the distance ΔL, the negative sign in Equation 21 provides a positive value of volumetric flow rate from high to low hydraulic headIn the vertical column shown in Figure 19, the value of head h 43 Hydraulic Gradient – Hydrogeologic Properties of Earth
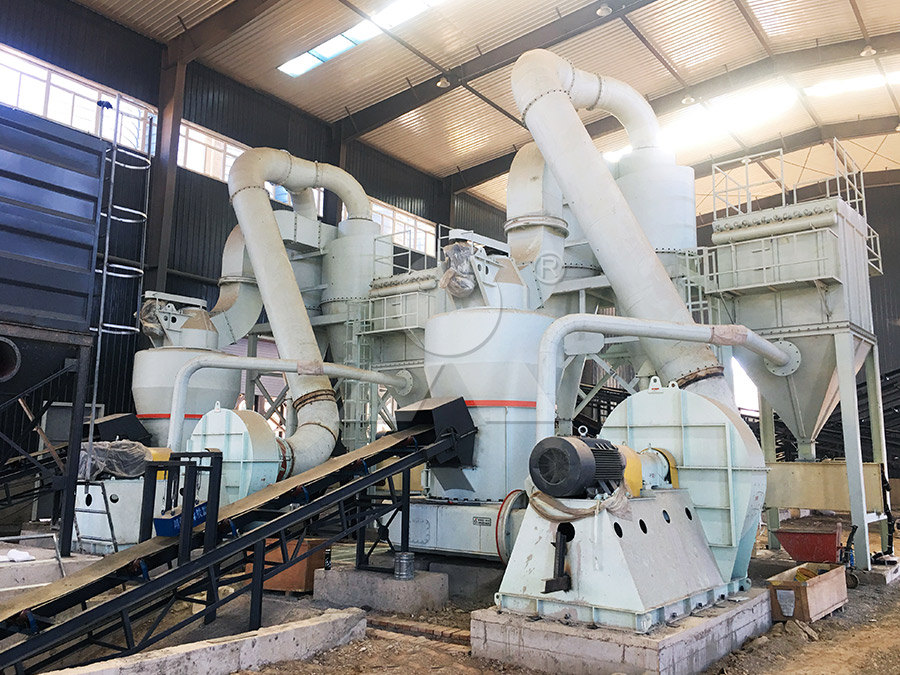
Dynamic response analysis of aero hydraulic pipeline system under pump
2018年2月14日 The pressure fluctuation excited by the hydraulic pump can cause serious vibration in aero hydraulic pipeline system, which poses a serious threat to the safety of the aircraft J Fluids Eng 1987; 109: 161–165 Crossref Web of Science Google Scholar 2 Lesmez MW, Wiggert DC, Hatfield FJ2022年12月15日 A multibranch pipeline is a typical structure, which is widely used in aerospace, marine and other hydraulic systems The multibranch pipeline suffers serious vibration from fluid–structure Vibration Analysis of MultiBranch Hydraulic Pipeline System For a given pipe size, fluid properties and flow rate, the hydraulic analysis should provide the pressure and temperature profiles along the pipeline for steady state and transient conditions Full account shall be taken of possible changes in Pipeline Design – The Piping Engineering World2024年8月22日 The fluidstructure interaction (FSI) in aircraft hydraulic pipeline systems is of great concern because of the damage it causes To accurately predict the vibration characteristic of long hydraulic pipelines with curved segments, we studied the frequencydomain modeling and solution method for FSI in these pipeline systems Fourteen partial differential equations Frequencydomain analysis of fluidstructure interaction in aircraft
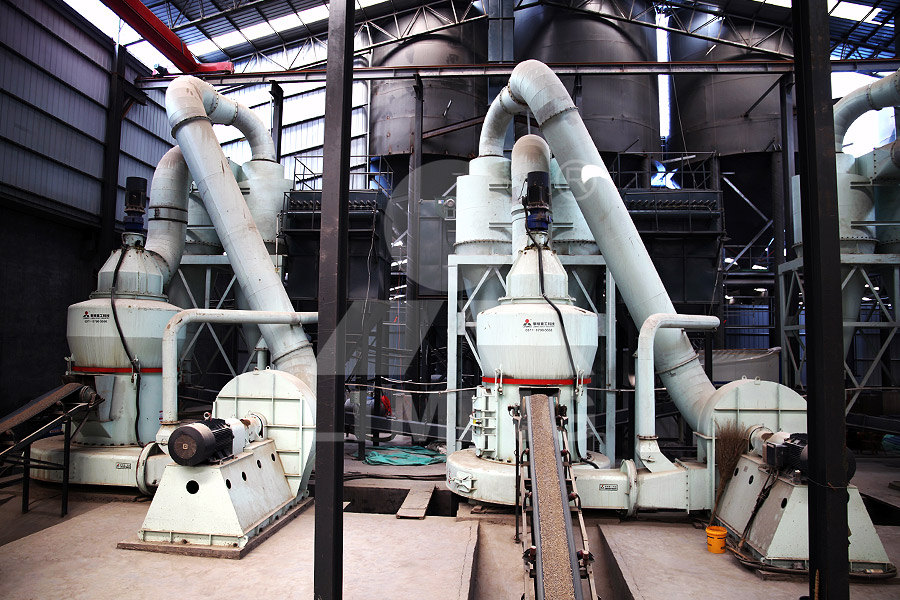
Radial waves of pipeline pressure at the hydraulic shock
2019年3月1日 Radial waves of pipeline pressure at the hydraulic shock To cite this article: I V Lopa et al 2019 J Phys: Conf Ser 1210 View the article online for updates and enhancementsthen "cascade" pressure testing will be required, (ie complete the pressure test on the higher pressure system prior to system closure welding and then repeat full Pressure Test Procedure for the test of the combined systems at the lowest pressure) 2 Heat exchangers, pressure vessels and fired heaters may be included in aHYDROSTATIC PRESSURE TESTING OF PIPING (PROJECT 2023年10月23日 Mechanical power is converted into hydraulic energy using the flow and pressure of a hydraulic pump Hydraulic pumps operate by creating a vacuum at a pump inlet, forcing liquid from a reservoir into an inlet line, and to the pump Mechanical action sends the liquid to the pump outlet, and as it does, forces it into the hydraulic systemWhat is a Hydraulic System How Does It Work? Vector Solutionssolution of the grinding model and the selection of relevant parameters needs further study It is obvious that the working process of a ball mill or a rod mill is different from the pipeline transportation In this study, the slurry pipeline transportation process is regarded as a special ball mill or rod mill grinding processPREDICTION OF COAL SLURRY PIPELINE TRANSPORTATION
.jpg)
Determination of Pressure Losses in Hydraulic Pipeline Systems
2009年4月1日 Large pipeline pressure loss can lead to a further change of viscosity on the basis of the viscosity increase caused by the ambient pressure when the hydraulic oil flows through the pipelineDescription: Pipeline hydraulics has all to do with understanding pressures and flow rates The key focus of this class is teaching students the five basic hydraulics tools with include the systems resistance curve, hydraulic gradient, systems profile, pump curve, and operating point These tools and how to use them are the focus of this moduleOil Pipeline Hydraulics and Hydraulic ToolsChapter 3: Selection and Use of Pipeline Materials 21 PART II CONSTRUCTION AND DESIGN FABRICATION Chapter 4: Piping and Pipeline Sizing, Friction Losses, and Flow Calculations 35 Chapter 5: Piping and Pipeline Pressure Thickness Integrity Calculations 57 Chapter 6: Straight Pipe, Curved Pipe, and Intersection Calculations 85Piping and Pipeline Calculations Manual: Construction, Design 2020年10月2日 The pneumatic capsule pipeline and hydraulic capsule pipeline are both moved and stopped by water under normal operating velocities Hydraulic capsule pipeline systems typically function at a velocity of 6–10 feet per second, whilst the functional velocity of pneumatic capsule pipeline is typically much greater—20 to 50 feet per secondThe Importance of Pipeline Transportation SpringerLink
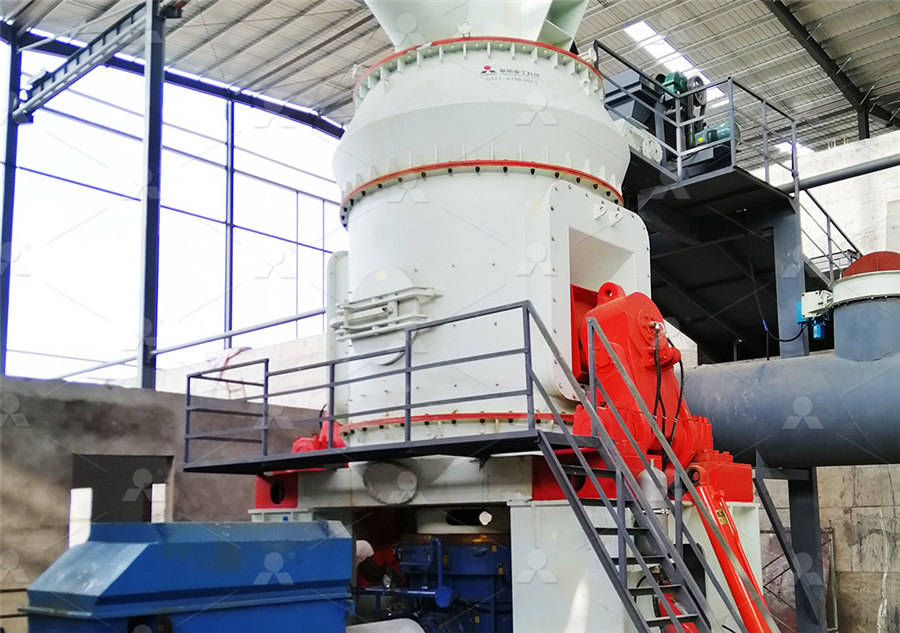
(PDF) Hot rolling mill hydraulic gap control (HGC)
2015年1月1日 Hot rolling mill hydraulic gap control (HGC) thickness control improvement January 2015; January 2015; 12(6):93106; According to the control principle of pressure AGC, 2024年6月21日 Herein, we discuss designs of single and multidisc grinding tools for formation of sealing surfaces (SSs) of valves of pipe fittings We study on the effect of microcutting on the parameters of “undulation” and “roughness,” following which the surface quality of the SS is evaluated While processing the measurement results, the programs Microsoft Excel and Optimal grinding modes for sealing surfaces of the valve Pressure hydraulic pipeline vibration is a type of solidliquid coupling in fluidconveying pipes, with obvious instability characteristics in its development Structural vibration caused by changes in oil flow velocity and pressure in the pressure transmission hydraulic pipeline have significant impact on the efficiency, noise, safety, and many other characteristics of the hydraulic system Experimental Study of Hydraulic Pipeline Vibration Under Pressure 2019年12月30日 If HGL is above the center of the pipeline, the pressure is positive and HGL is below the center of the pipeline, the pressure is negative Above are the various reasons that the hydraulic grade line is useful Read More: Euler’s and Bernoulli’ equation : Derivation, Assumptions, Limitations Total Energy Line (TEL)Explain hydraulic grade line and total energy line EnggStudy
[GYQ0R)ZQ]ESS4NJ.jpg)
Precommissioning Hydrotest of Pipelines all about pipelines
The value of change in pressure due to gravity head ( ∆P g) may appear small compared to the required hydrotest pressureHowever, it plays a vital role in sectionalizing the pipeline for hydrotest, mainly when the minimum hydrotest pressure is close to the pipe's minimum yield strength (SMYS) eg, 90% of SMYS After meeting the requirement of minimum pressure at 2022年6月1日 This content was downloaded from IP address 11912201132 on 24/11/2022 at 06:30Dynamic Simulation Analysis of Aircraft Hydraulic Pipeline 2017年8月1日 There is two type of flushing as below which are enough for pipelines flushing 1 Chemical flushing (pickling) 2 Oil flushing CHEMICAL FLUSHING (PICKLING) The purpose of chemical flushing is to remove any dirts, debris, oil, grease, rust, scale, ect form the pipelines During chemical flushing thin layer of surface of pipe wall will remove as well all thePipe Flushing (Full procedure, standards NAS, Filter selection 2024年11月17日 ASME B3610M: for wrought steel pipes ASME B3619M: for stainless steel pipes Note: Both standards will have the same value, so we can refer to any of them Referring to the below image from ASME B3610M, we can see that the outside diameter (D) for 6″ pipe is 1683 mm S: Allowable Stress value of the Pipe Material (ASTM A 106Gr B) at Design Pipe Thickness Calculation for Internal Pressure
.jpg)
Factors Affecting Line Sizing of Piping or Pipeline Systems
2024年3月7日 3 Pressure Drop Effects for Line Sizing: The effect of pressure drop within a system is closely correlated to the economics of the system Smaller pipe sizes result in larger pressure drop requirements; economic considerations require a balance between pipe size and pumping/power requirements to overcome pressure losses through the system 4In SI units, pressure is stated as kilopascal (kPa), megapascal (MPa), bar or kg/cm2 When dealing with gases it is very important to distinguish between gauge pressure and absolute pressure The absolute pressure at any point within the gas is the actual pressure inclusive of the local atmospheric pressure (approximately 147 psi at sea level)Gas Pipeline Hydraulics CED EngineeringThe Hydraulic Piping Standard Handbook assists in the above mentioned engineering process by providing relevant information and standards for this project input phase This is when the piping requirements are defined such as desired working pressure, maximum pressure, maximum flow rate, acceptable pressure drops and classification requirementsHYDRAULIC PIPING STANDARD HANDBOOK2012年8月28日 Experimental Study on Pressure Pulsation and Acceleration Response of Fluid Conveying Pipeline Under MultiExcitation 17 July 2023 Journal of Pressure Vessel Technology, Vol 145, No 5 Evaluation of gravity effects on the vibration of fluidconveying pipesModal Analysis of the Aircraft HydraulicSystem Pipeline
.jpg)
(PDF) Pressure Wave Velocity in FluidFilled Pipes
2018年10月1日 Solid pipeline deposits can be mapped by analyzing reflections of hydraulic pressure pulse waves in the lowfrequency range To determine the amount and position of the deposits, an inverse 2023年7月13日 Two tanks and are connected by a pipe 100 ft long The first 70 ft has a diameter of 3 in and then the pipe is suddenly reduced to 2 in for the remaining 30 ft The difference of levels between the tanks is constant at 30 ft = 0005 and the coefficient of contraction at all sudden changes of area is 058 Find all the head losses including that at the The Hydraulic Gradient Pipes Fluid Mechanics CodeCogs2020年12月1日 Hydraulic calculation is a major path to the management of natural gas pipeline network However, the assumed physical parameters such as the length of the pipes are usually investigated from Datadriven computation of natural gas pipeline network hydraulicsTransient pressure investigation of waterhydraulic pipelines is a challenge in the fluid transmission field, since the flow continuity equation and momentum equation are partial differential, and the vaporous cavitation has high dynamics; the frictional force caused by fluid viscosity is especially uncertain In this study, due to the different transient pressure dynamics Pressure Transient Model of WaterHydraulic Pipelines with
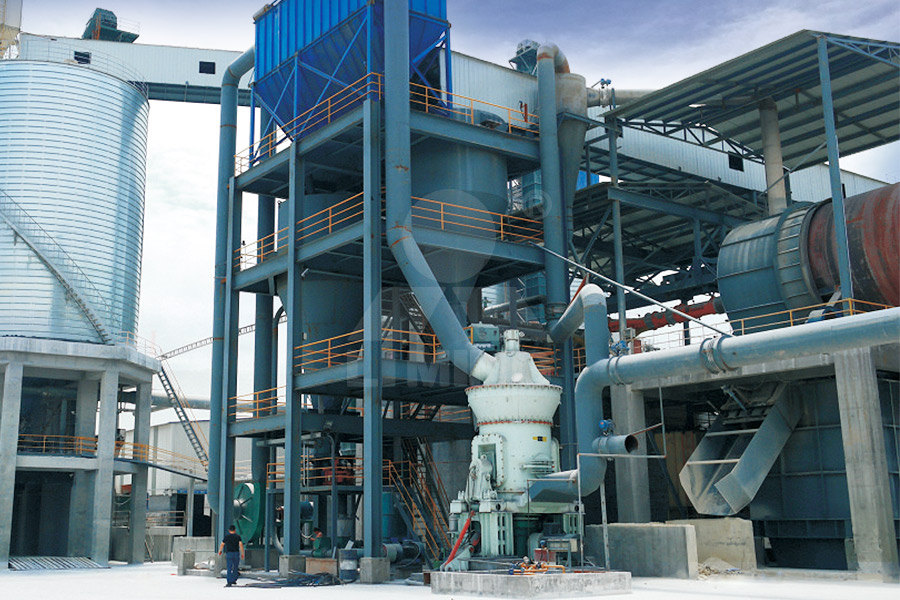
Optimal design of the positions of the hoops for a hydraulic pipelines
2011年12月1日 Fig 1 gives a hydraulic pipelines system (such pipelines systems are common in the engineering problems, such as aircraft hydraulic pipelines and feeder pipelines of nuclear power plants) The hydraulic pipelines system herein consists of 263 elements, namely 91 elastic straight pipes, 58 elastic curved pipes, 3 elastic pipe tees, 37 hoops, 8 valves, 4 flanges and 2022年2月17日 Over the past 20 years, most of the hydraulic systems I've worked on have been between 2500 psi and 3000 psi (165 to 207 bar) The ideal hydraulic system pressure range is between 2500 and 3000 psi (172 to 207 bar) because of safety, internal leakage, weight and sizeHow to Select The Best Hydraulic System Pressure2019年3月1日 Radial waves of pipeline pressure at the hydraulic shock I V Lopa 1, N E Proskuriakov 1 and A I Zhukaev 2 Published under licence by IOP Publishing Ltd Journal of Physics: Conference Series, Volume 1210, XII International scientific and technical conference "Applied Mechanics and Systems Dynamics" 13–15 November 2018, Omsk, Russian Radial waves of pipeline pressure at the hydraulic shock2011年12月31日 This chapter discusses the pipeline hydraulic analysis for both liquid and gas pipelines Based on the understanding of building on the liquid and gas properties and the pipe strength analysis, it Pipeline Hydraulic Analysis ResearchGate