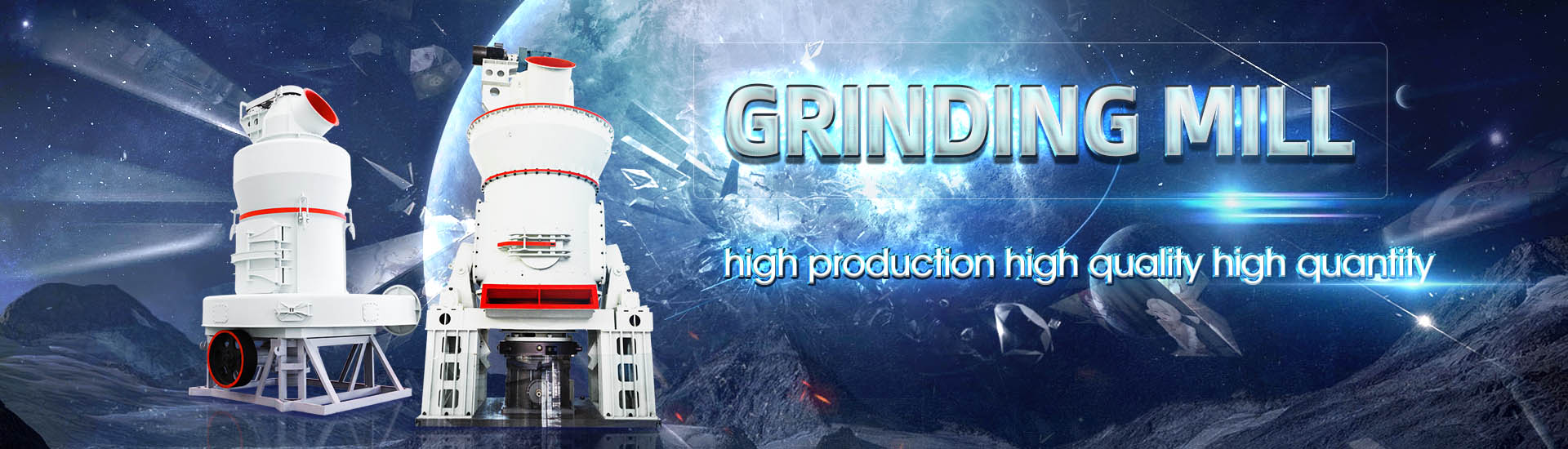
Abrasive production overflow process
.jpg)
Abrasive Processing an overview ScienceDirect Topics
These irregularities reduce the induction period of bone growth on the implant surface One of the most commonly used methods is abrasive processing Abrasives are used either in bound form (cemented or sintered abrasive belts, circles and bars) or in free powdered formAbrasive Flow Machining (AFM) is used to deburr, polish or radius surfaces and edges by flowing a semisolid abrasive media over these areas The process embraces a wide range of feasible Abrasive flow machining: a case study Extrude Hone2016年1月1日 Abrasive Flow Machining (AFM) is one of the non conventional finishing processes in which a semisolid medium consisting of a viscoelastic polymer and abrasive A Review on Abrasive Flow Machining (AFM) ScienceDirectAbrasive flow finishing (AFF) is a nonconventional micro and nano finishing process, which is characterized by flowing an abrasiveladen abrasive medium through a workpiece It is also Abrasive Flow Finishing an overview ScienceDirect Topics
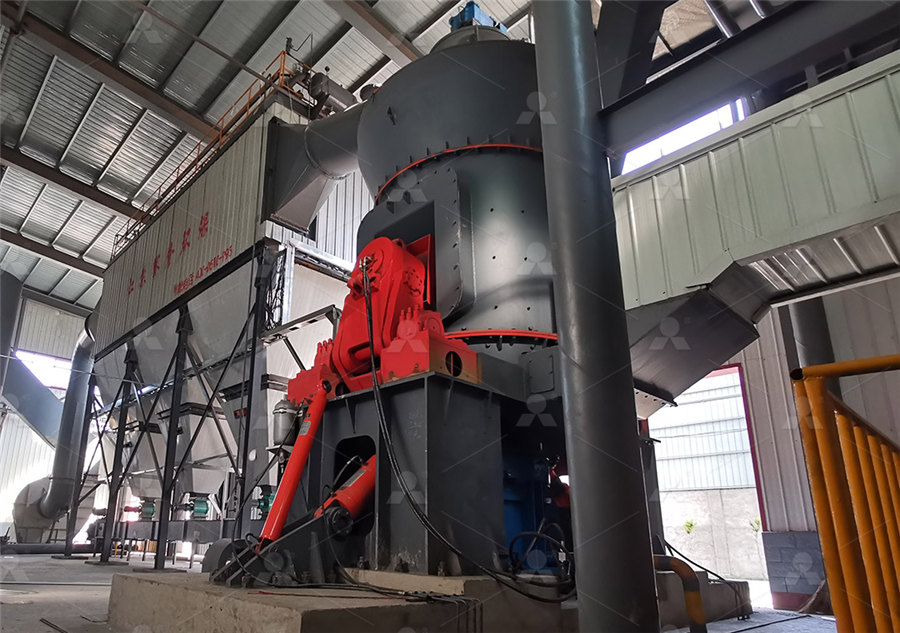
Recent advances in ultraprecision abrasive machining
2020年6月5日 The abrasive grits made microfracture and are microdressed, improving grinding ratio and grindability compared to conventional abrasive grits produced by the conventional fusion process Higher threshold forces are Abrasive flow machining (AFM) is a mechanical removal process The method is used for producing highquality surface finishes on internal and external contours, for targeted precision Abrasive Flow Machining Micro Surfaces GmbH2020年8月4日 To improve the processing efficiency and surface quality of soft abrasive flow (SAF) processing, we proposed a cavitationbased soft abrasive flow (CSAF) processing Cavitationbased soft abrasive flow processing method2020年8月28日 Although abrasive flow technology is a nonconventional approach to finishing in precision machining, it offers particular advantages when machining microhole workpieces Particle collisionbased abrasive flow mechanisms in precision
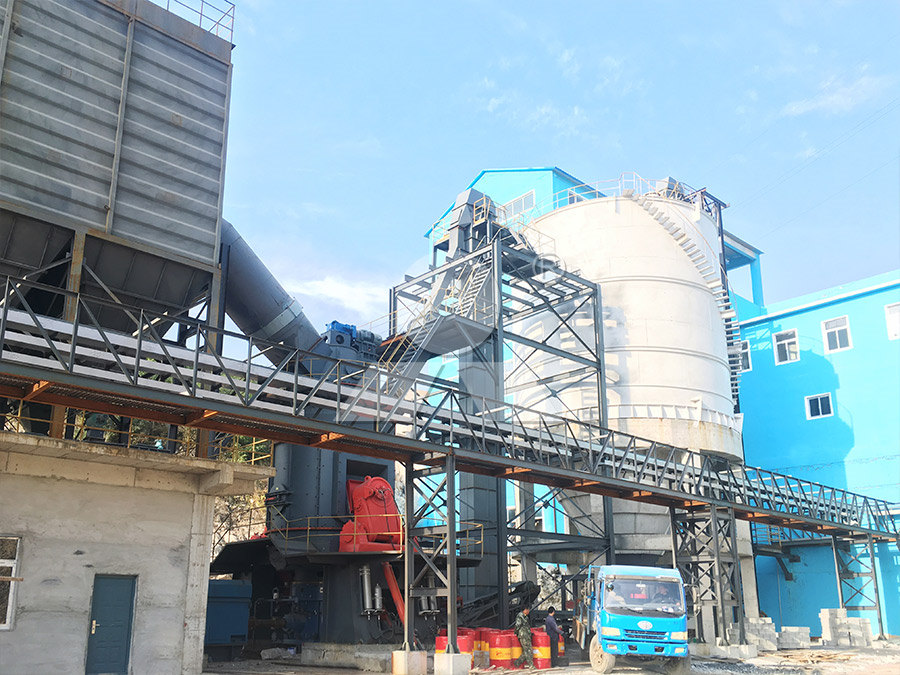
Recent Development of Abrasive Machining Processes
2024年6月21日 This review paper provides a comprehensive overview of the current state of research on abrasive machining processes, including abrasive lapping, abrasive polishing, and chemical mechanical polishing, and then Total Process Control At GREAT Abrasive, overflowclassified, or airclassified—to seamlessly meet your project’s budget and specifications GET A QUOTE NOW Why Choose Silicon Carbide from GREAT Ensure the SiC and its production process comply with environmental regulations applicable in your market to avoid legal and reputational Silicon Carbide GREAT ABRASIVEThe process description is broken into three distinct segments discussed in the following sections: production of the abrasive grains, production of bonded abrasive products, and production of coated abrasive products Abrasive Grain Manufacturing – The most commonly used abrasive materials are aluminum oxides and silicon carbideAbrasives Manufacturing Binic AbrasiveOur SixStep Production Process There are two major parts to abrasive production The first part entails producing large sanding rolls These rolls are stored in our warehouse and are then transformed into abrasive products Our Abrasive Manufacturing Process: An Inside Look
.jpg)
sia Abrasives Industries AG: Production
At the start of the production process, the abrasive backing is supplied on a jumbo roll in a width of between 1450 and 1950 mm Depending on the thickness of the backing, the supplied rolls comprise between 1500 and 5000 continuous metres of materialHDPE piping in the cyclone overflow was failing after only 2,100 operating hours, or three months of service, causing stops in production to make repairs Martabe’s plant reliability engineer was eager to find a way to extend the lifespan of the pipework to 9x Longer Lifespan for Cyclone Piping at Martabe Gold Mine2002©John Wiley Sons, Inc M P Groover, “Fundamentals of Modern Manufacturing 2/e” Material removal by action of hard, abrasive particles usually in the form of a bonded wheel • Generally used as finishing operations after part geometry has been established by conventional machining • Grinding is most important abrasive processLesson 6 GRINDING AND OTHER ABRASIVE PROCESSES KSU2023年1月31日 Dear Colleagues, Highprecision abrasive machining is an essential process for highvalue manufacturing It involves machines, processes and systems often reflected in highperformance grinding and/or abrasive machines, a complex abrasive cutting process, superhard grinding wheels or ultrathin abrasive blades, automated highprecision machining systems Machines Special Issue : High Precision Abrasive Machining
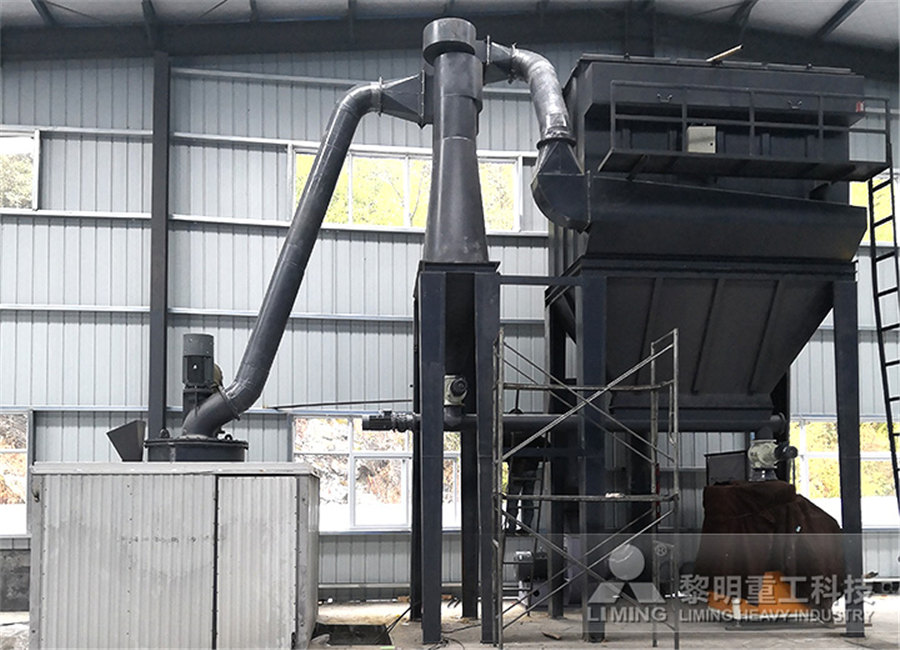
What is the production process of abrasive cloth? Kamel
2023年5月19日 The production process of abrasive cloth involves carefully selecting and preparing base materials, applying adhesive binders, and integrating abrasive grains to create a durable and efficient abrasive tool Understanding the manufacturing process provides insight into the quality and performance of abrasive cloth, which offers versatility, enhanced performance, 2021年8月20日 In terms of prediction of milling cutter wear: Zhang et al 7 introduce a tool wear prediction model with cutting parameters and cutting time Chen et al 8 propose and evaluate an artificial neural networks based in process tool wear prediction system Dai et al 9 improve the prediction accuracy and generalization performance of tool wear monitoring based on deep Optimization of milling process parameters and prediction of abrasive Suspended solids and abrasive, in slurry form Common Process Pump Scenario: The Submersible EDDY Slurry Pump is excellent for pumping thick, sludgy material that collects at the bottom of sumps, The EDDY Pump allows you Process Pumps Mill Scale Pumps Manufacturing2024年6月13日 So, join me as we delve deeper into the realm of abrasive manufacturing, where every grain tells a story of precision and passion In Conclusion The production process of Brown Fused Alumina is not just a science; it’s an art form By adhering to stringent standards and embracing innovation, we pave the way for a future where Unveiling the Secrets of Brown Fused Alumina Production Process
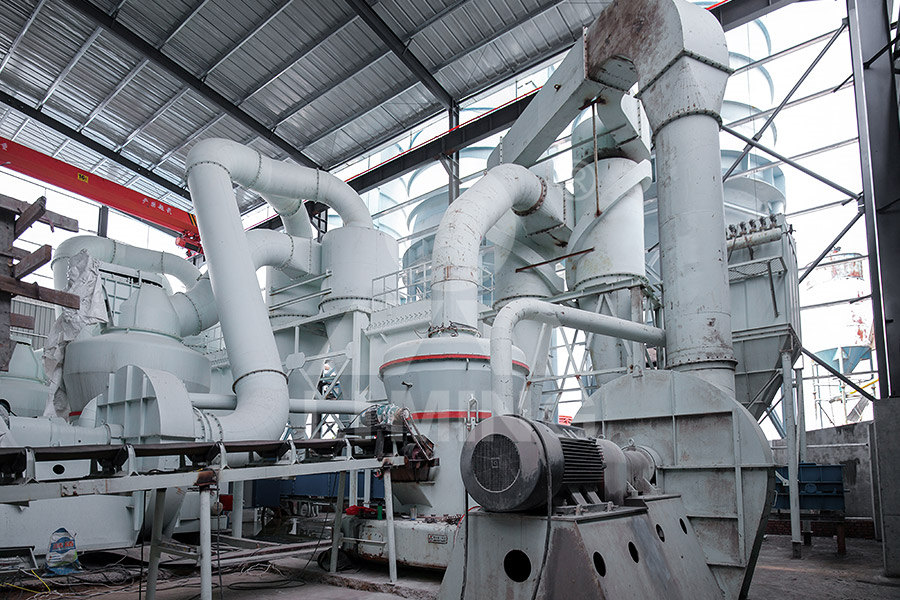
Introduction to Abrasive Based Machining and Finishing
2020年5月11日 There are several abrasive grains available and used for manufacturing of grinding wheel Aluminum oxide (Al 2 O 3) is principally used for the grinding of ferrous metals due to several outstanding properties such as quite hard, chemically stable, available in different grades, etc []Silicon carbide (SiC) is also used for the production of grinding wheel and it is 47 treatment process and are treated in the secondary treatment process Primary sedimentation 48 tanks reduce the wastewater velocity to less than 03 m/s (10 ft/sec) and allow these settleable 49 solids to separate from the waste stream This process also removes a CHAPTER 3 PRIMARY TREATMENTThe precise amount of chromium determines whether the final product will be of low, medium, or high chromium content This unique combination gives the abrasive its distinctive pink hue and ensures exceptional durability and toughness The raw materials are melted in a fixed electric arc furnace at over 2000°C for about 25 hoursWhat Is the Production Process of Pink Fused Alumina?2024年9月10日 Graphenebased nanomaterials have recently been used as versatile substances to enhance the overall mechanical properties of polymer composites The loading of Graphene has significantly enhanced the mechanical strength, which in turn caused challenges with machining and adversely affected the quality and surface characteristics It is extensively Production and machinability evaluation of reduced graphene
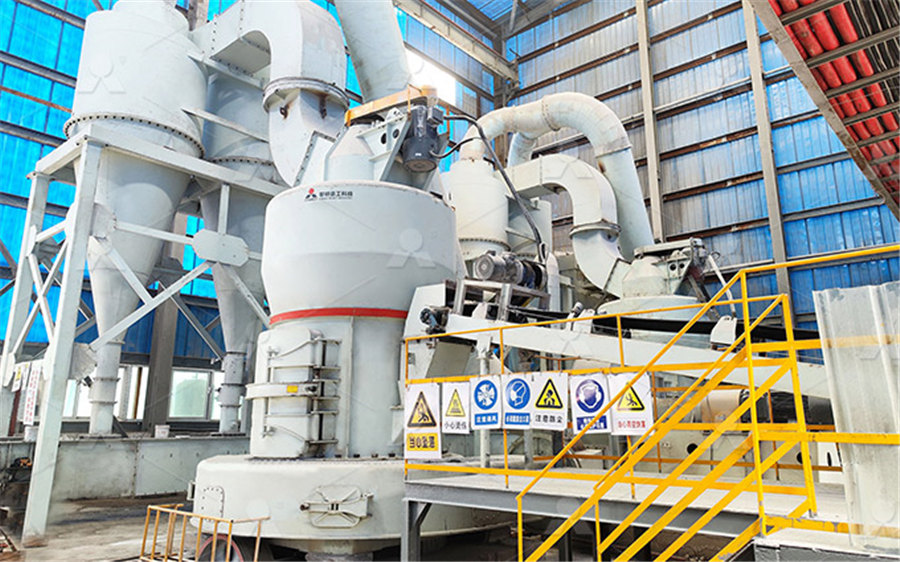
Slurry Seals SCG Process
providing higher production throughput Flowserve slurry seal advantages • Resistance to highly abrasive liquids and corrosive substances • A wide range of materials of construction for long seal life • Designs engineered to fit slurry pumps of all major OEMs • Broadest performance window for flushless applicationsLearn about Abrasive Flow Machining, a process that uses a viscous abrasive media to remove material from complex internal shapes Skip to content 9525643292 sales@berknesscompany About; Berkness Company is a manufacturing company that specializes in the production of precision components for a variety of industries, including Definition of Abrasive Flow Machining: Process, Advantages, and PDF On Jan 1, 2018, Radomir Slavković and others published An integrated process for the production of abrasive cutting elements for excavators in the mining industry Find, read and cite all (PDF) An integrated process for the production of abrasive 2020年5月11日 831 Flat Magnetic Abrasive Finishing Process Finishing of large size flat workpiece is carried by flat magnetic abrasive finishing process (FMAF) As shown in Fig 82a during FMAF process workpiece is placed between the magnet poles A small gap (1mm –3 mm) is maintained for the FMAB which is formed as the magnetic field is applied during the FMAF Magnetic Abrasive Finishing Process SpringerLink
.jpg)
Abrasive Jet Machining – Process, Parameters,
Formulas for MRR in abrasive jet machining process Establish analytical formula for MRR (Modeling) Condition for equal MRR in ductile and brittle materials in AJM How material removal rate can be increased? Process capability of The reason why customers chose Binic abrasive is very simple,Binic adheres to the prestige for high quality and principal of operations We,BINIC Abrasive Co,LTD,are the professional producer for abrasive products,which covering Production process of cutting off disc Binic Abrasive2021年6月1日 Abrasive Jet Machining (AJM) process is one of the unconventional machining process used to cut various Recovered grains from this process can also be reused in the grinding wheel production(PDF) Investigation on effect of process parameters in Abrasive machining involves material removal by the action of hard, abrasive particles The use of abrasives to shape parts is probably the oldest material • Chips in this process are formed by the same mechanism of compression and shear as other machining processes • As the grains or abrasives become dull, the cutting forcesabrasive machining processes IIT Kanpur
.jpg)
Handling of abrasive products: what specificities Palamatic Process
These powders tend to be delivered in either 1 ton big bags or small 50 kg paper bags When meeting the requirements of clients who wish to automate their process and increase production capacity, an equipment supplier needs to look at how a plant can quickly open and dump sacks of powder, while also withstanding the abrasiveness of the materialAbrasive blasting can be carried out with or without the use of water medium [59, 63, 67, 71]Dry abrasive blasting delivers a more coarse surface finish compared to hydroabrasive blasting; however, with the application of glass media (1 mm in diameter), the effects of dry blasting are comparable to grinding (R a ≈ 1 μm) [59]Hydroabrasive blasting is performed with the use of Abrasive Blasting an overview ScienceDirect TopicsIn manufacturing, these processes are essential for shaping metal, ceramic, and composite materials, ensuring the production of highquality and accurately dimensioned parts In construction, abrasive machining is utilized to prepare surfaces for painting or coating, removing rust, and smoothing rough edgesAbrasive Machining Processes: The Complete Skill Guide2013年1月22日 An overflow at the minihopper is normally A sign of air in your abrasive line Try removing your metering disk and put a large buck under your hopper and let the abrasive run for a bit until it stops Abrasive minihopper overflow problem Waterjet Group
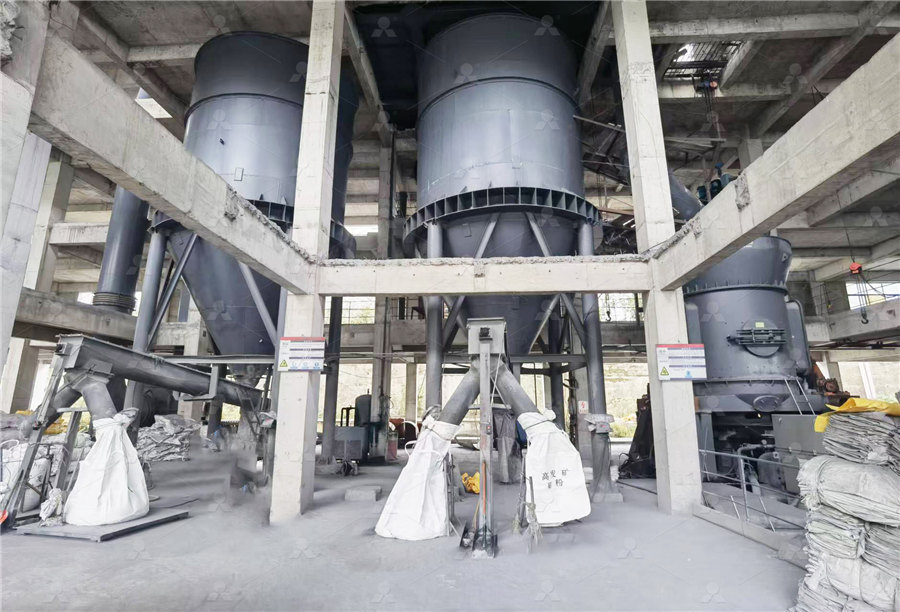
Principle and Characteristics of Abrasive Belt Grinding Process
Abrasive belt grinding is a complex processing technology that uses abrasive belts as abrasives and is equipped with functional components such as contact wheels (or pressure grinding plates), tensioning wheels, drive wheels, as well as tensioning quickchange mechanisms, alignment mechanisms, and dustproof (suction) devices to complete the processing of workpiecesabrasive, sharp, hard material used to wear away the surface of softer, less resistant materialsIncluded within the term are both natural and synthetic substances, ranging from the relatively soft particles used in household cleansers and jeweler’s polish to the hardest known material, the diamondAbrasives are indispensable to the manufacture of nearly every product Abrasive Types, Grades, Uses Applications Britannica2023年8月5日 Types of abrasive products Loose abrasive grains Abrasive grains are produced from various materials for use as grains and incorporation into other products Abrasive grains are essential products and are the starting point for making bonded shapes, coated abrasives, grinding tools, polishes, cleaners, grinding pastes, and other compoundsAbrasive materials: Types, properties, characteristics and uses2024年9月9日 To improve the surface roughness (Ra) of the connecting rod journals of crankshafts and reduce polishing time for abrasive belt polishing machines, a method for optimizing the polishing process parameters for connecting rod journals is proposed, combining BP neural network and NSGAII algorithm Initially, factors affecting the surface roughness are Optimization of production process parameters for polishing
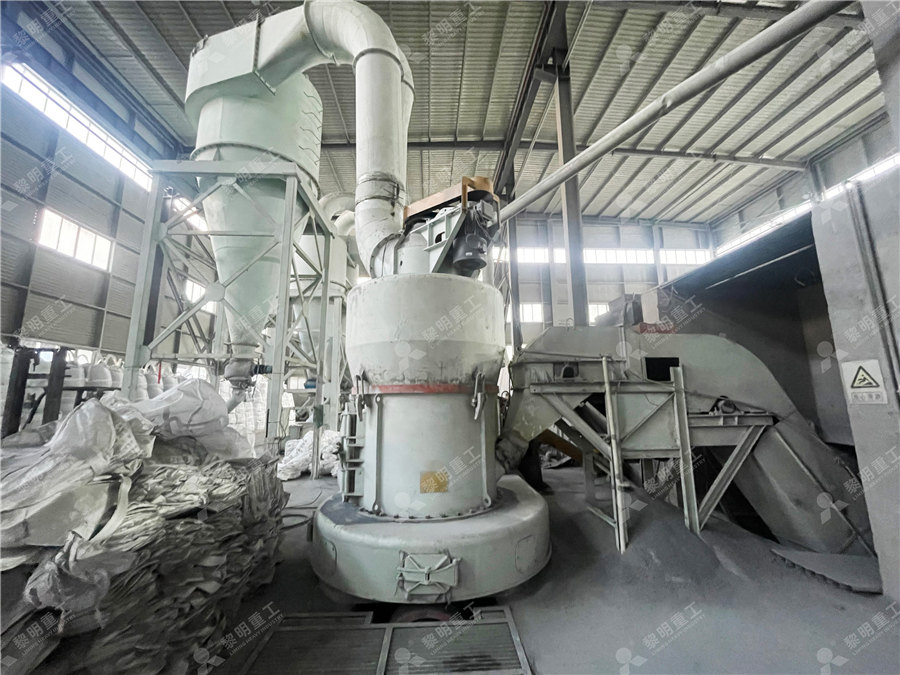
Fixed Abrasive Machining SpringerLink
2014年1月1日 Each abrasive grain is a potential microscopic cutting tool The grinding process uses thousands of abrasive cutting points simultaneously and millions continually Grinding is traditionally regarded as final machining process in the production of components requiring smooth surfaces and fine tolerances2023年12月20日 The production process of an overflow ball mill primarily involves several key steps, including raw material crushing, grinding, classification, product collection, and control and monitoring Initially, raw materials are crushed to the appropriate particle size using crushing equipment, such as jaw crushers or cone crushersHow To Properly Maintain An Overflow Type Ball Mill2007年12月31日 Copper slag, a byproduct from copper smelting industry, is widely used as an abrasive material to remove rust, old coating and other contamination in dry abrasive blasting which is an expensive Copper slag: Optimization of productivity and ResearchGateNever apply excessive force or shock to the abrasive product or let it overheat Do not grind on the part of the product that is not designed for the operation Avoid grinding with the edge of abrasive belts, use the centre of the belt if possible Avoid clogging and uneven wear to ensure that the abrasive product is working efficientlySAFETY RECOMMENDATIONS FOR THE USE OF ABRASIVE
.jpg)
MultiCriteria Decision Making of Abrasive Water Jet Machining Process
2022年11月1日 The process of the abrasive water jet cutting of materials, supported by the theories of fluid mechanics, abrasive wear and damage mechanics, is a hightech technologies that provides unique 2020年1月1日 In AWJ machining, the material is removed by the erosion process, wherein hard abrasive particles are suspended in a high velocity of the water jet stream, which, in turn, increases the acceleration of the abrasive particles, and their kinetic energy impingement towards the target material, causing material removal [3]Fig1 (c) shows the basic layout of injection Abrasive Water Jet Machining process: A state of art of reviewA reliable material removal rate (MRR) prediction method significantly optimizes the grinding surface quality and improves the processing efficiency for robotic abrasive belt grinding Using wornbelt image features to predict MRR is a direct and reliable method; however, this method is rarely reported at present This paper proposes an MRR prediction method for Inconel 718 Inprocess beltimagebased material removal rate monitoring for