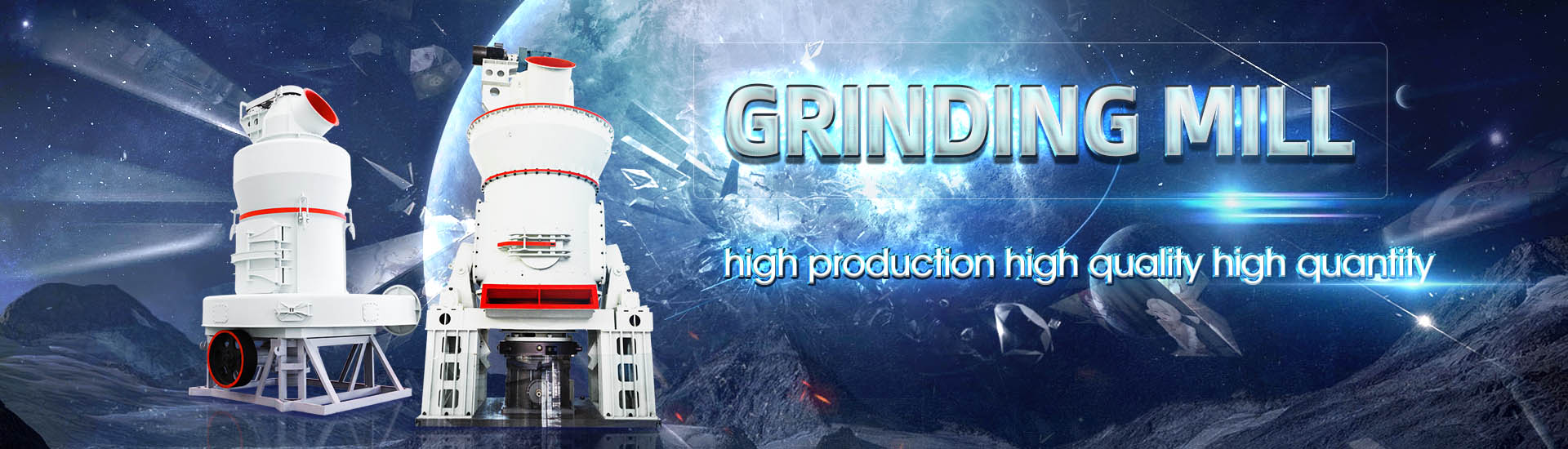
And will it be between the impeller and the casing
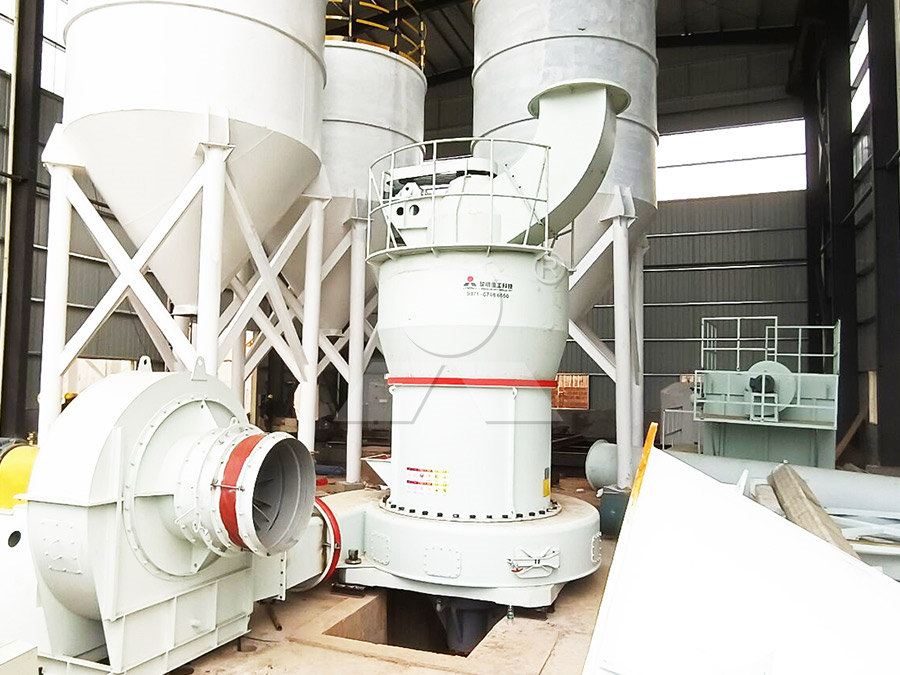
Casing vs Impeller Pumps Systems
The typical volute consists of a spiral collector and a vaneless diffuser (throat) Look at a small (OH1) ANSI B731 or ISO 5199 pump casing to visualize Many people in the pump world will answer the question by stating that the volute is the device that converts the high velocity of the liquid (imparted by the impeller) to 展开2014年6月16日 In addition to an optimized casing depth, the position of the impeller in the casing also influences the performance Using the results of several CFD simulations, we show that by creating a(PDF) Influence of the Casing Width and the Impeller 2021年4月21日 Setting the correct impeller clearance is essential to maintaining the energy efficiency of centrifugal pump systems Impeller clearance refers to the distance between the Optimizing Centrifugal Pump Impeller Performance: Guide forA centrifugal pump is a mechanical device designed to move a fluid by means of the transfer of rotational energy from one or more driven rotors, called impellers Fluid enters the rapidly rotating impeller along its axis and is cast out by Centrifugal pumps Useful Information Michael
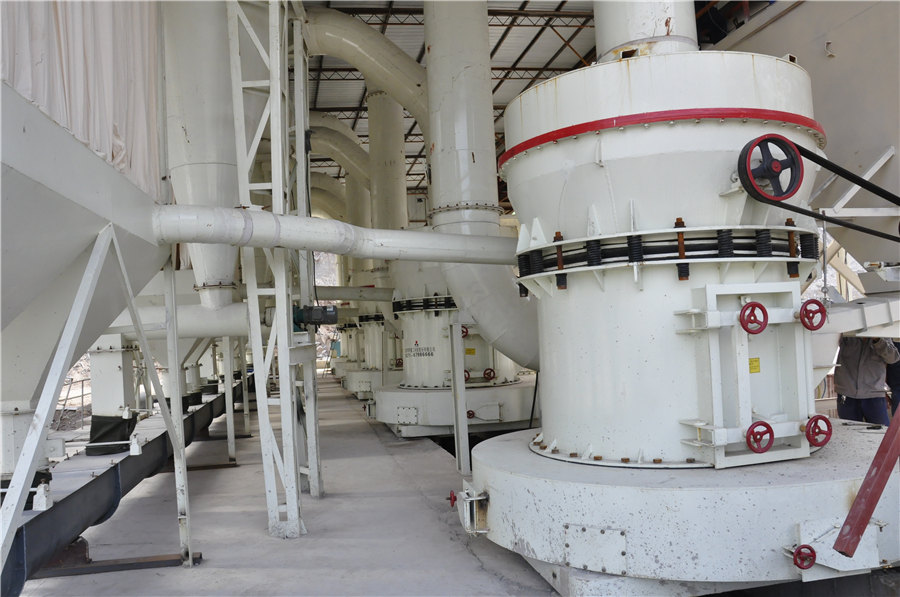
Understanding the Components of a Centrifugal Pump: A Guide
2021年4月15日 1 Impeller: The impeller is the rotating component of the pump that is responsible for transferring the energy from the motor to the fluid It is a series of curved With an enclosed composite impeller, the clearances are permanently set between the impeller wear ring and the pump casing ring or the pump housing Since the structural composite will Practice Operations Open Versus2023年11月22日 The casing, or volute as it is sometimes called, captures the fluid energy generated by the impeller and directs it out of the pump through the discharge nozzle As with impeller designs, manufacturers each have their Diving into Pump Casing Designs: Exploring Common 2022年2月4日 For an expanding volute pump where the impeller centerline is offset from the casing centerline (ie, noncongruent), the clearance between the outer diameter (OD) of the impeller (D 2 dimension) and the cutwater is a The Effect of Cutwater on Pump Performance, Part 1
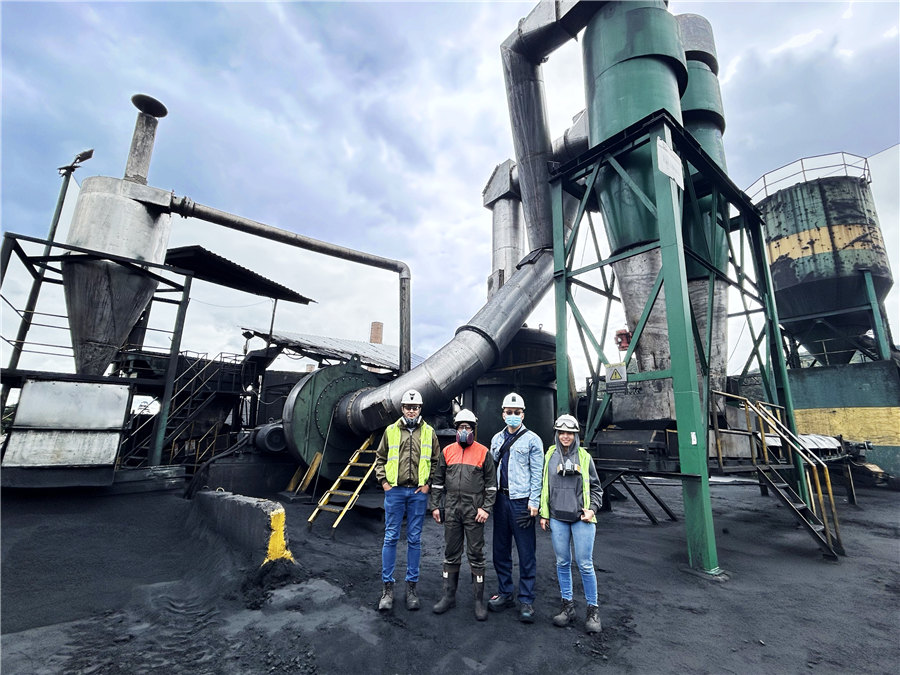
Diving into Pump Casing Designs: Exploring Common
2023年11月22日 Recessed impeller casing, as the name denotes, has the impeller recessed back into the casing With the impeller in this position, it allows the casing to pass very large particles and or “stringy” slurries The max To allow the impeller to rotate freely within the pump casing, a small clearance is designed to be maintained between the impeller and the pump casing To maximize the efficiency of a centrifugal pump, it is necessary to minimize the Pumps Engineering Library2009年11月14日 In mixed flow type impeller pump, what should be the clearance between the impeller and casing I am not asking the clearance between impeller wear ring and case wear ring Rather when the impeller is going to rotate in side the casing body, what should be this radial clearance My pump is aClearance between impeller and casing body EngTips2024年5月31日 Advantages of Open Impellers Easier to clean and maintain: The exposed vanes allow quick and thorough cleaning, reducing contamination risk and ensuring optimal performance; Better for handling solids and viscous fluids: The open design allows larger passages between the vanes, reducing clogging and enabling more efficient pumping; Wide What Is the Difference between Open, Semiopen, and Closed Impellers
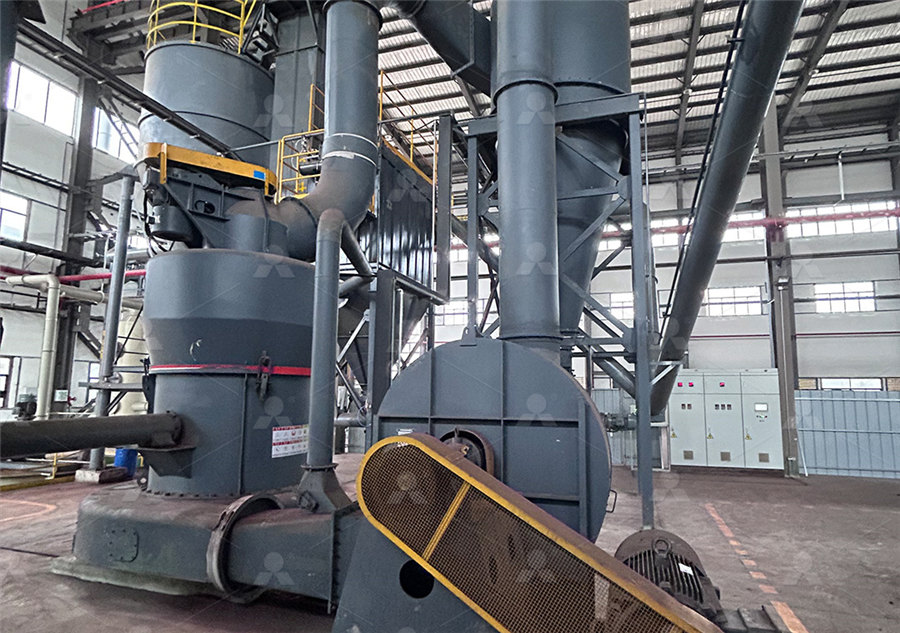
Centrifugal Pump Impeller Casing Clearance CR4 Discussion
2008年12月9日 On the other hand, Exteremely narrow clearance will occur excessive eddy current between impeller and casing and it will cause erosion (This is the reason why we have to have replaceable impeller and casing wear ring If it is eroded, you can change and it 1979年1月1日 Extreme values for the pressure are es timated INTRODUCTIOJ The lifetime of the expensive casing of a large pump, pumping a mixture of sand and water, is very much prolonged by installing wearing rings between the impeller shroud and pump casing These rings can be replaced when worn out at a much lower price than the casingON THE FLOW IN THE CLEARANCE BETWEEN THE IMPELLER AND CASING 2022年5月19日 However, some of the liquid will recirculate back between the impeller and the casing running clearance, resulting in erosion, excessive clearances, and decreased efficiency If not addressed, the growing clearances will produce a cascading effect that results in even higher flows and more erosion, which can significantly affect performance and pump lifeWear Rings 101: Location, Fit More Nickerson Company2021年1月6日 Figure 183 Tight tolerance casing serves as front of open style impeller Close clearance between impeller and casing wall for recirculation control, typically 010"030" gap Figure 183 Tight tolerance casing serves as front of open style impeller Figure 184 Casing volute and cutwater areas discharge flangeCasing Drilling Fluids Rig Worker
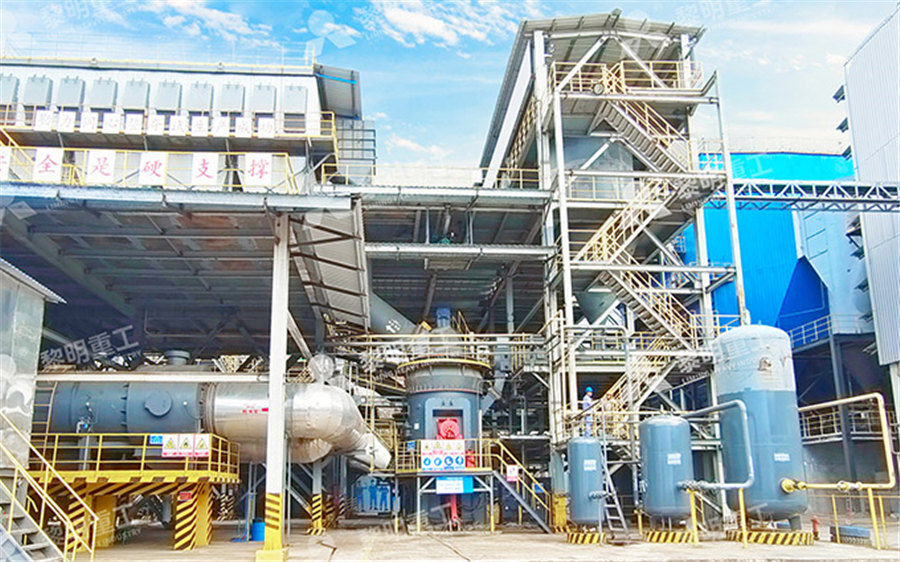
Proceedings of ResearchGate
study, the casing width of a centrifugal fan will be varied by 30 % and 60 %, but without changing the geometry of impeller In this situation, the impeller’s exit width is 0092 m and the2024年6月5日 Wear rings work by creating a close clearance between the rotating impeller and the stationary pump casing As the impeller rotates, the highpressure fluid on the discharge side of the pump tries to leak back to the lowpressure suction side through the clearance between the impeller and the casingWhat Is Wear Ring in Centrifugal Pump Mechanical seals & PumpsDownload scientific diagram Gap between the impeller blades and the discharge casing from publication: Design and Fluid Dynamics Features of a LowFlow HighHead Pump with BarskeType Impeller Gap between the impeller blades and the discharge 2019年10月5日 Beginning from the cutwater, as we move around the impeller, the distance between the volute and impeller gradually increases until we reach the discharge point This steady expansion of the area around the impeller Centrifugal Pump Casings AMARINE
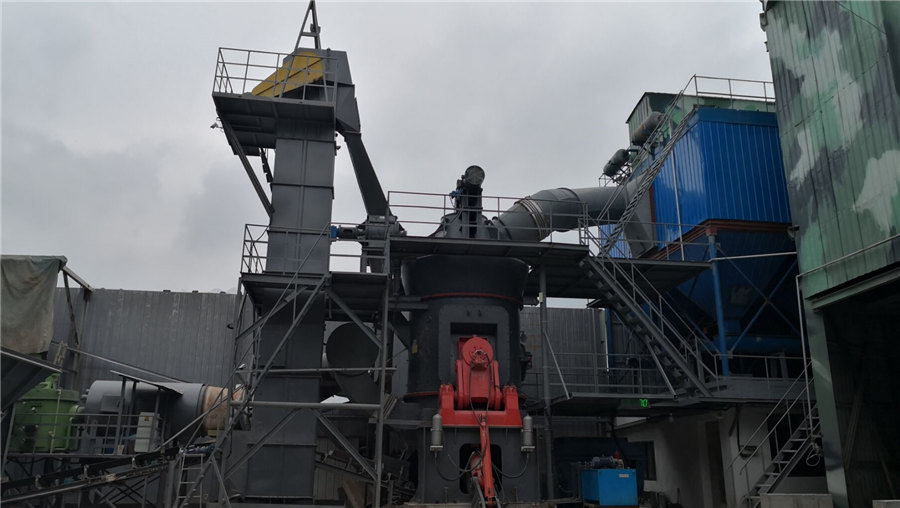
Understanding the Components of a Centrifugal Pump: A Guide
2021年4月15日 1 Impeller: The impeller is the rotating component of the pump that is responsible for transferring the energy from the motor to the fluid It is a series of curved blades that spin rapidly to create a centrifugal force, pushing the fluid through the pump 2 Casing: The casing is the stationary component of the pump that surrounds the impellerWear rings installed on the impeller are called ‘impeller wear rings’, whilst wear rings installed on the casing are referred to as ‘casing wear rings’ Impeller Wear Ring If no wear rings were installed, the process liquid would be able to flow from the discharge to suction side of the pump in relatively large quantities and this leads to a drop in pump efficiency (as much as 4%)Centrifugal Pump Explained saVRee2020年11月11日 These pumps because you have a gap between the casing and the impeller you’re not going to get the same hydraulic efficiency and performance out of these pumps There’s an advantage when it comes to solids because if you do have a solid that gets stuck in the pump it will wear itself down until it gets passed throughCentrifugal Pump Basics: Types Of Impellers2017年9月2日 Impellers are sandwiched between the Pump Suction and Collar Impellers have rotating Impeller Wear Rings and stationary Casing Wear Rings that are expected to wear out before the much more expensive Impellers and Casings wear out Wear Rings are much easier to replace than Impellers and Casings Wear Rings also limit the amount internal pump EVERYTHING PROCESS OPERATORS NEED TO KNOW ABOUT IMPELLERS

Figure 623Impeller, impeller wearing ring, and casing tpub
The clearance between the impeller wearing ring and the casingwearing ring (fig 623) must be maintained, as shown in the manufacturer's plans When clearances exceed the specified figures, the wearing rings must be replaced This replacement requires the The enclosed impeller’s performance and effi ciency is simply a function of the design of the impeller and casing volute Performance tests with the same pump casing volute (Figure 1) show that an identical impeller to the open impeller but with a shroud on the suction side of the impeller increases the effi ciency of the pump by as much as 5 Open vs Enclosed Impellers2019年10月1日 As fluid passes through the impeller, it is expelled through the casing volute channel, passing the volute lip into the case discharge Properly selected, a centrifugal pump’s wear rings limit the recirculation flowrate between the sides of the impeller and the impeller eyeCentrifugal Pump Wear Ring Clearance PumpWorks2024年10月23日 Recessed Impeller: Recessed impellers, or “torque flow” impellers, generate centrifugal force uniquely Instead of directly accelerating the liquid down the vanes, these impellers use their vanes to create a hydraulic coupling This coupling spins the slurry within the pump casing, producing the necessary discharge pressureImpeller Design: Types, Applications, and Simulation
.jpg)
Casing and Impeller Wear Rings Plasmatron
Impeller and casing wear rings are subjected to two different forms of wear Even in the absence of any solid particles in the process fluid, the wear rings can be damaged by sliding wear (also called metaltometal wear) due to unintentional contact between the rotating (eg impeller wear ring) and stationary (eg casing wear ring) surfaces resulting in wear ring rubthe pump casing to allow a small running clearance between the impeller and the pump casing without causing wear of the actual impeller or pump casing material These wearing rings are designed to be replaced periodically during the life of a pump and prevent the more costly replacement of the impeller or the casing Centrifugal and Positive Centrifugal and Positive Displacement Pumps CED EngineeringCentrifugal Pumps Wearing Ring Review Pump Knowledge Menu Centrifugal Pumps Wearing Ring Review Centrifugal pumps contain rotating impellers within stationary pump casings To allow the impeller to rotate freely within the pump Centrifugal Pumps Wearing Ring Review Engineers cutoff clearance (impeller blade tongue clearance) of the casing which is closest to the rotating impeller This paper presents the design methodology for the casing of centrifugal blower with impeller having backward curved blades In this paper the casing design of centrifugal blower with different cutoff clearances of 6 to 125 % ofCasing Design of Centrifugal Blower IERJournal
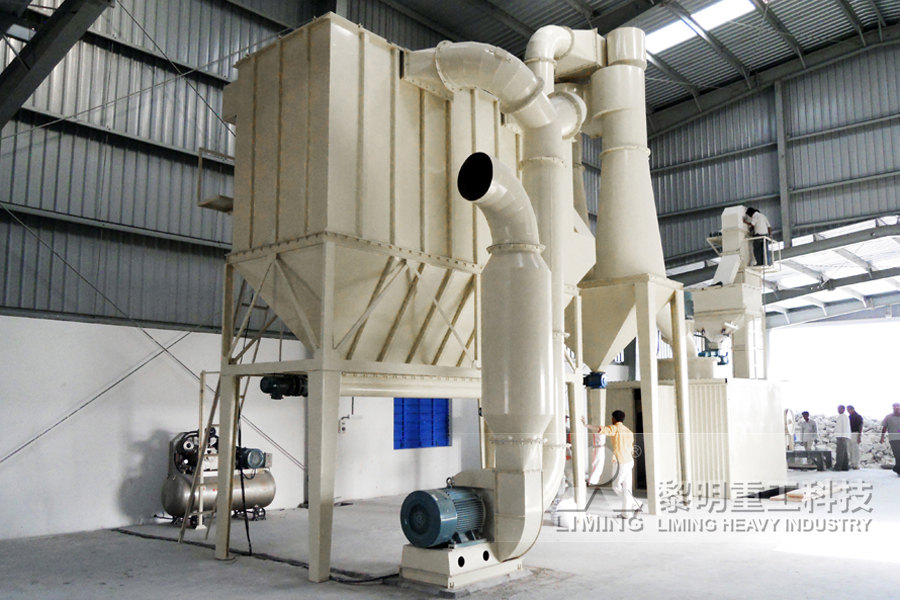
A few millimetres can cause huge problems: Why wear ring KSB
Enlarged wear ring clearances allow this foreign matter to become tangled between the impeller suction hub and casing wear ring which can increase your clogging headaches Internal stresses: As radial wear rings also act as a bushing, enlarged wear ring clearances expose the pump to additional radial loadings2024年5月28日 The vortex generated by rapid impeller rotation moves fluid and solids with minimal contact to the impeller Lack of contact between the pumped fluid and impeller is beneficial in applications with abrasives or large solids Cutters Choppers For applications prone to clogging, there are impeller styles designed to handle these troublesome The Basics of Centrifugal Pump Impellers Pumps Systemsclearance exists between the impeller vanes and the casing Closed impeller The vanes are located between the two discs, all in a single casting They are used in large pumps with high efficiencies and low required Net Positive Suction Head The centrifugal pumps with closed impeller are the most widely used pumps handling clear liquidsImpeller – Types of Impellers2018 European regulations set standards for energyefficiency of fans, with increasing requirements in the near future Many studies concerning centrifugal fans have investigated the impeller but to only a smaller extends the spiral casing, which may take up a substantial part of the fan#39;s hydraulic lossEffect of Clearance Gap in Spiral Casing Design of a Centrifugal
.jpg)
Impeller Types in Pumps Selections and Considerations
There are further design conflicts on certain applications where the gap between the semi open impeller and the casing of the pump is large enough that some fluid goes back into the start of the vanes recirculation and slipping This issue makes the 2022年8月3日 The advantages of forging Forging can eliminate the defects like porosity and optimize the microstructure during the manufacturing process Meanwhile, as the complete metal streamline is well preserved, the mechanical properties of forging parts are normally better than that of the casting parts made by the same materialsThe differences between forging and casting2023年9月28日 However, the unit is designed to have low shear, and its rotational speed is limited to less than 1400rpm because the impeller touches the casing The Advantages Of Open Design Centrifugal Pumps This design EXPLORING THE TYPES AND USES OF CENTRIFUGAL As the clearance between the impeller and pump casing wears and becomes greater, the complaint from an operator would be A the flow is low B there is air in the line C the pressure is too high D there is no flow There are 2 steps to solve this one Solution Step 1Solved As the clearance between the impeller and pump casing
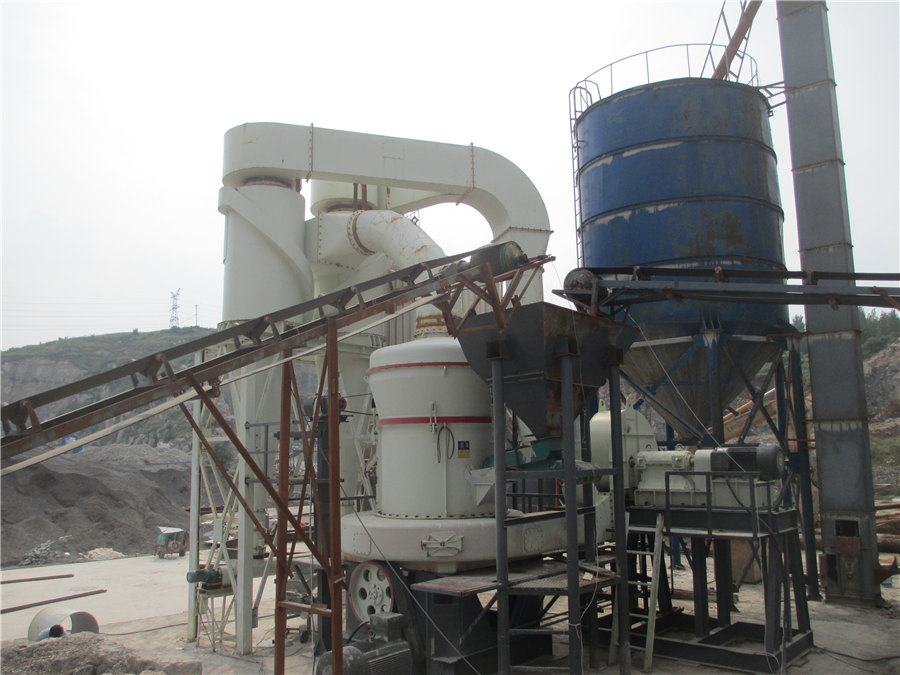
Impellers and Wearing Rings
split casing, the construction is more complex but often employed for both lower NPSHR and the advantage of a between bearings rotor Multistage pumps usually have singlesuction impellers to avoid the casing complexity associated with getting liquid to and from a series of doublesuction impellers The only exception is the first stageA bit of clearance space must be left between the impeller vanes and casing to minimize the liquid’s recirculation 2 – SemiOpen Impellers Semiopen impellers have a metallic back wall that strengthens their vanes more than open impellers However, the front side remains openPump Impellers: 3 Different Types and How to Choose the Right 2009年1月1日 Download Citation Analysis of the Flow Between the Impeller and Pump Casing Back Face for a Centrifugal Pump Previous experimental investigations of an open faced impeller, low specific speed Analysis of the Flow Between the Impeller and Pump Casing impeller range for that casing with an operating point in the high efficiency area (see Figure 48) It is also important not to go too far right or left from the BEP A guideline is to locate the operating point between 110% and 80% (see reference 16) of CENTRIFUGAL PUMP SELECTION, SIZING, AND INTERPRETATION OF PERFORMANCE
.jpg)
Pump cavitation and how to avoid it ScienceDirect
2018年2月1日 The formation of the first vapor bubbles are induced by local pressure drops caused by discontinuous surfaces or in the gaps between the impeller and the pump casing Methods to capture these effects are far more complicated than those used to evaluate NPSH3 and the effects on pump reliability are in most cases negligibleImpellers (also spelled impellors or impellars) are rotating devices designed to alter the flow and/or pressure of liquids, gases, and vaporsImpellers consist of various vanes — often bladeshaped — arranged around a short central shaft When the shaft and vanes rotate, they suck in fluids or gases and impel them out the other sideImpellers Selection Guide: Types, Features, ApplicationsThe casing is usually made of cast iron, stainless steel, or other materials that are resistant to corrosion and erosion The casing contains multiple impellers, each of which is designed to increase the pressure of the fluid passing through the pump Specification:Different Types of Centrifugal Pump Casing Grow MechanicalPump Casing (Volute) converts high velocity (energy) into a pressure head Impeller imparts kinetic energy to the liquid (accelerates the liquid) Shaft transmits rotational energy from driver (Used to spin the impeller) Wear rings reduce leakage between high and low pressure regions Seal prevents leakage where shaft exits casingCENTRIFUGAL PUMP SIZING, SELECTION AND DESIGN PRACTICES