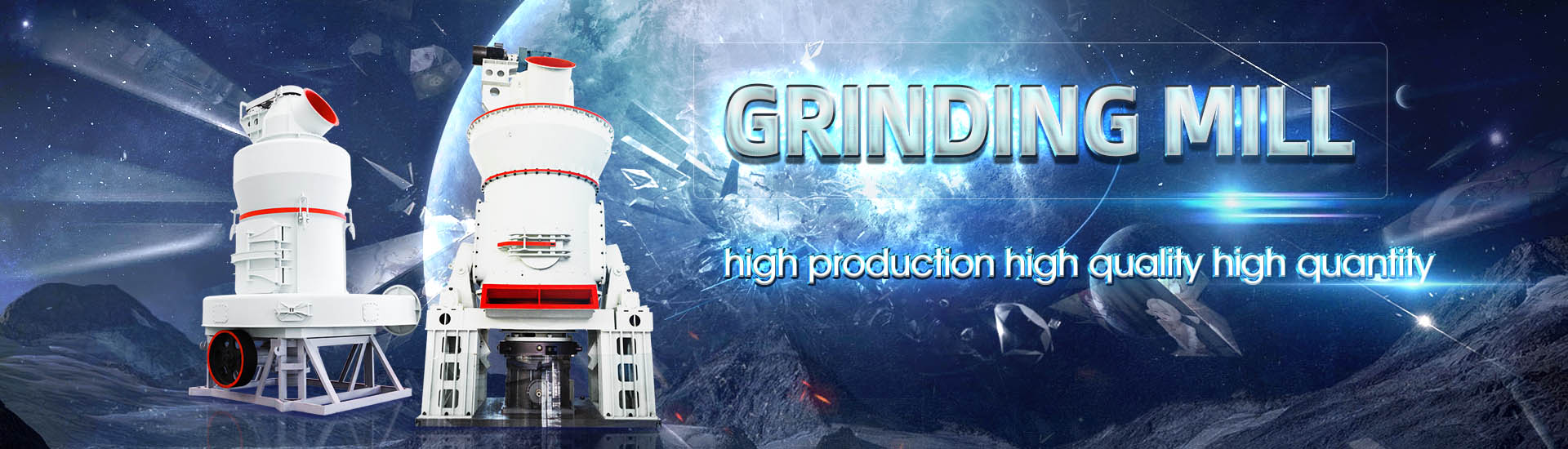
Drum coal mill model
.jpg)
DrumBoiler system model in Dymola Download
Coal mills play an important role in the overall dynamic response of coal fired power plants and there is significant potential to improve the load ramp rates of coal fired power plants2013年3月1日 In this paper a three state coal mill model based on heat and mass balances as well as a single step coarse to fine particle grinding relationship is presented with the purpose Nonlinear coal mill modeling and its application to model Our model is designed after one of the early tables, so it can be used in any mill after the late 1890's scale: HO M7 $4999 USD S M7 $5999 USD O M7 $6999 USDDetail Parts Mining Wild West Scale Model Builders2022年2月24日 Curves of mill productivity, power consumed, specific surface of coal dust in terms of the relative rotational speed of the ball drum mill Composition of the balls loading the mill with a standard Improving the efficiency of the coal grinding process in ball drum
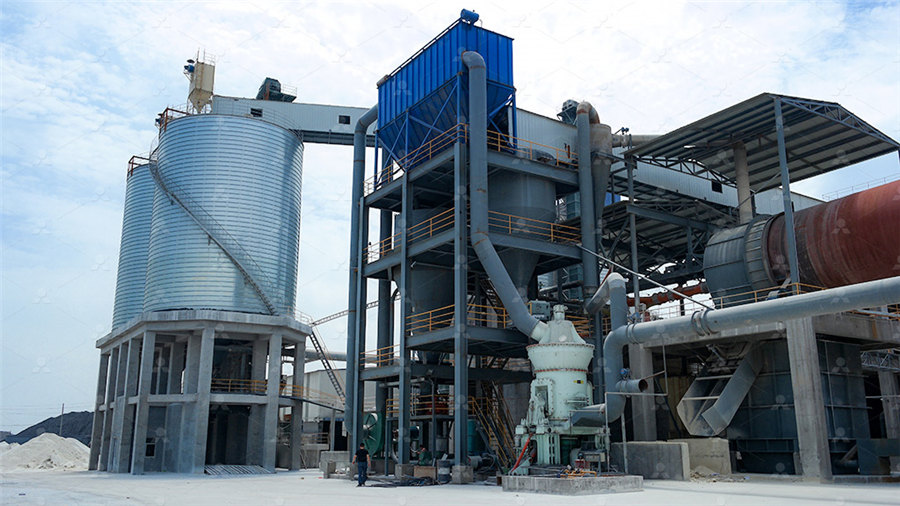
Determining Optimum Productivity of a Ball Drum Mill When
2021年2月8日 Abstract Ball drum mills (BDM) are one of the main types of coalgrinding equipment in Russia A significant drawback of BDM is high power consumption (a significant part of the TPP’s own needs) With a huge scale of production, reducing these costs even by a few percent gives a significant economic effect The problem of minimizing the specific energy A simple energy balance model of the coal mill is derived in (Odgaard and Mataji 2006), this model is based on a more detailed model found in (Rees and Fan 2003)In this model the coal mill is seen as one body with the mass m mThe following variables are defined: T(t) is the temperature in the coal dust flow in the mill, ṁ PA (t) is the primary air mass flow, T PA (t) is Coal Mill an overview ScienceDirect Topics2015年6月1日 Developed a dynamic model of a Wemco dense medium drum separator • Model parameters obtained from industrial Wemco dense medium drum data • Realistic steadystate partition factor model derived from the dynamic model • Coal washability and drum partitioning behaviour are used to estimate the grade • Dynamic drum model is considered Dynamic model for a dense medium drum separator in coal beneficiation While this boiler subflowsheet does not contain a specific coal mill model, the partial vaporization of the moisture in the raw coal is modeled in the fireside boiler model The drum level is controlled by a 3element controller as shown in Figure 2Subcritical CoalFired Power Plant Flowsheet (steady state and
.jpg)
Coal fragment size model in cutting process Semantic Scholar
2015年3月1日 Semantic Scholar extracted view of "Coal fragment size model in cutting process" by Xiaohui Liu the mechanised mining of thin coal seam mainly relies on a drum shearer Investigation of breakage characteristics of low rank coals in a laboratory swing hammer mill Jihoe Kwon Heechan Cho Daeyang Lee R Kim Engineering mill model parameters and dynamics estimating the quality of deposit coal in the mill, which is essential for predicting potential mill fires The thesis reports the work completed and the main contributions of the thesis are summarized as follows: The pulverized coal mill mathematical model for EType vertical spindle millsDevelopment of a tube ball mill mathematical model for mill For the [O] and [OH] groups, the partial equilibrium method is used Fuel type NO is mainly generated by the pyrolysis and oxidation reaction of nitrogen in fuel, which is theCombined operation mode of subcritical Wflame boiler and coal mill 2014年4月1日 Multisegment pulverised coal mill model and online implementation for condition monitoring Int J Model Ident Control 2006;1:206–13 [17] Niemczyk P, Bendtsen JD, Ravn AD(PDF) A new modelbased approach for power plant Tubeball mill
.jpg)
Derivation and validation of a coal mill model for control
2012年5月1日 Neal, Waddington, and Wilson (1980) perform a frequency analysis of mill and boiler complex, and analyze its effects on the steam pressure This leads to simple transfer function plant models Similarly, Bollinger and Snowden (1983) perform an experimental study of a mill's transfer functions in order to devise feedforward controllers The identification process 2021年8月1日 Yukio et al [7] proposed a model consisting of blending, grinding and classifying processes for pulverizer control Agarawal et al [8] differentiated coal powder into ten size groups, divided the bowl mill into four zones, and developed a unified model Palizban et al [9] derived nonlinear differential mass equations of raw coal, recirculation coal and suspension coal in Coal mill model considering heat transfer effect on mass Key words: thin coal seam; shearer; cutting; drum; coalloading rate; model test Cite this article as: GAO Kuidong, XU Wenbo, JIANG Shoubo, DU Changlong Factors affecting thin coal seam shearer drum coalloading performance by a model test method [J] Journal of Central South University, 2019, 26(6): 1619−1636Factors affecting thin coal seam shearer drum coalloading Air Swept Coal Mill Working Principle First, the raw coal is fed into the feed chute by the feeding device Then, the hot air with a temperature of about 300 ℃ enters through the air intake pipe and begins to dry the raw coal while they are fallingAir Swept Coal Mill Coal Mill In Cement Plant AGICO GROUP
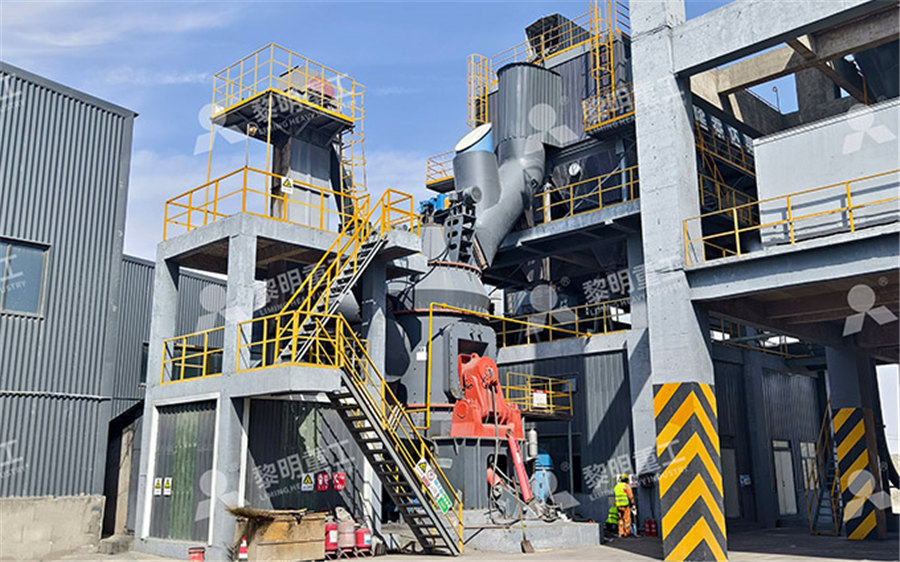
Factors affecting thin coal seam shearer drum coalloading
2019年7月10日 To solve the problem of a low coalloading rate being exhibited by the drum shearer on Chinese thin coal seams, systematic tests and research were performed to study the pivotal factors’ influences on drum coalloading rate using a model test method The effects of the drum hub diameter, cutting depth, vane helix angle, drum rotation speed and hauling speed on Dynamic model for a dense medium drum separator in coal beneficiation EJ Meyera,b, IK Craigb, aSnr Solution Architect, MES Plant Business Solution Provision, Exxaro Resources, PO Box 9229, Pretoria 0001, South Africa bDepartment of Electrical, Electronic and Computer Engineering, University of Pretoria, Pretoria 0002, South Africa Abstract Dynamic model for a dense medium drum separator in coal A control oriented model was then developed by Fan (1994) and Fan and Rees (1994) In 2009, coal flow and outlet temperature of mill were modelled using mass and heat balance equations for startup Sectional view of MBF coal mill Download Scientific Diagram2022年7月26日 diagnosis of the major faults in the coal mill system [4] Fan et al, designed a knowledgebased finegrained coal mill operator support/control system for coal plants The system is composed of mathematical coal mill model and expert knowledge database and has the ability of parameter estimation, coal mill performance monitoring, fault diagnosisFault Diagnosis of Coal Mill Based on Kernel Extreme Learning
.jpg)
System dynamics model of output of ball mill ResearchGate
2021年2月15日 The coal mill model was developed and the unknown model coefficients were obtained numerically by genetic algorithm (GA) The input variables of mass flow rates of raw coal and air and temperature 2012年11月17日 20 131Fineness Fineness is an indicator of the quality of the pulverizer action Specifically, fineness is a measurement of the percentage of a coal sample that passes through a set of test sieves usually designated at 50, 100, and 200 mesh A 70% coal sample passing through a 200 mesh screen indicates optimum mill performance The mill wear and Coal mill pulverizer in thermal power plants PPT SlideShare2013年3月1日 Based on simulations with this model, a conventional coal mill control strategy from the same hard coal power plant is implemented and a new modelbased control strategy is developed The conventional control is utilized as a reference to compare the performance improvement on ramp rates of coal fired power plants using nonlinear model predictive control Nonlinear coal mill modeling and its application to model 2016年1月1日 The dynamic model of the drum separator focusses on throughput equations by making use of the of the drum coal product A model representation of the drum separator can be found in CJ, and Davis, JJ (1982) Dynamic modelling of dense medium cyclone washing circuits In Proceedings of the Mill Opera tions Conference Model predictive control of a coal dense medium drum separator
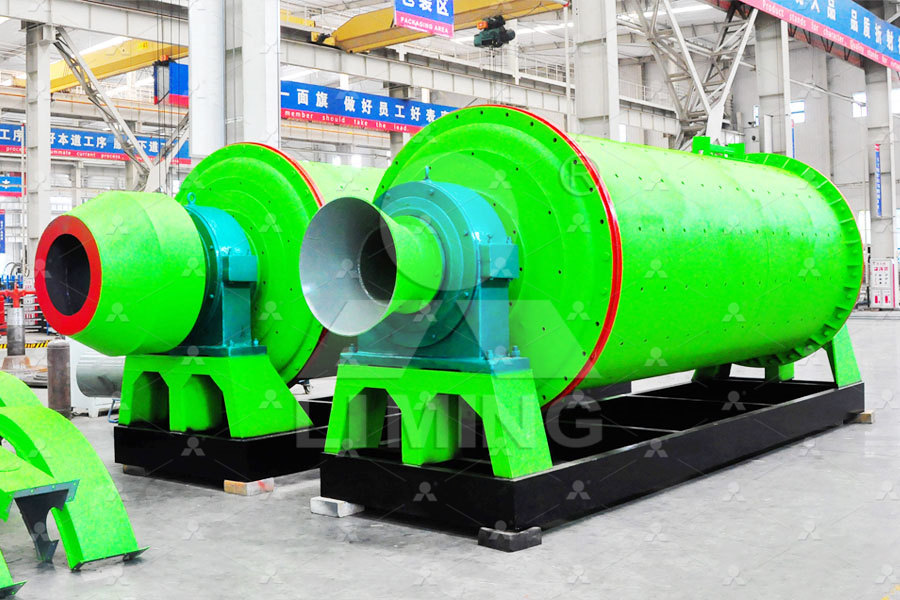
DRUM MILL TM 500 Analysis
DRUM MILL TM 500 The Drum Mill TM 500 is a laboratory ball mill designed to grind large sample volumes up to 35 l It accepts initial feed sizes of up to 20 mm and can achieve grind sizes down to 15 µm by friction and impact Hard, brittle or ibrous samples are pulverized in the 150 l drum illed with 80 kg grinding balls The variable speed of While this boiler subflowsheet does not contain a specific coal mill model, the partial vaporization of the moisture in the raw coal is modeled in the fireside boiler model The drum level is controlled by a 3element controller as shown in Figure 2Subcritical CoalFired Power Plant Flowsheet (steady state and Kuidong Gao, Qingliang Zeng, Changlong Du and Su Yang: Orthogonal model test on the drum coal loading performance of a thin seam shearer 336 conveyor Ayhan M and Eyyuboglu EM (2006) compared the coal loading performance and cutting performance of the globoid drum and the cylindrical drum, from which it is demonstrated that the coal loadingOrthogonal model test on the drum coal loading performance of 2019年1月3日 22 Unit Type and Material Parameters and Finite Element Mesh Division For the spiral drum and coal rock SOLID164 unit [], the material of the tooth body was 42CrMo, and the alloy head material was YG8The material of the square head, blade, end plate, and barrel body was 16Mn steel, and the material parameters of the spiral drum have been shown in A Study on the Dynamic Transmission Law of Spiral Drum Cutting Coal
.jpg)
Development of a Multisegment Coal Mill Model Using an
2007年10月1日 Wei et al [11] proposed a multisegment coal mill model that covers six milling processes (startup, standard milling, shutdown, idle and transit periods) with parameters identified in each process2022年7月26日 Aiming at the typical faults in the coal mills operation process, the kernel extreme learning machine diagnosis model based on variational model feature extraction and kernel principal component (PDF) Fault Diagnosis of Coal Mill Based on Kernel Extreme mill model parameters and dynamics estimating the quality of deposit coal in the mill, which is essential for predicting potential mill fires The thesis reports the work completed and the main contributions of the thesis are summarized as follows: The pulverized coal mill mathematical model for EType vertical spindle millsDevelopment of a tube ball mill mathematical model for mill 2016年1月25日 I just finished designing an HO scale model railroad layout This layout is based on the steel mill and coal mine operations of the Union Railroad in Pittsburgh Pennsylvania The layout is 140" by 80" or about 115 ft by 65 feet Or if you prefer metric about 35 meters by 2 meters It's a very small table layoutModular HO Steel Mill Coal Mine layout Model Train Forum
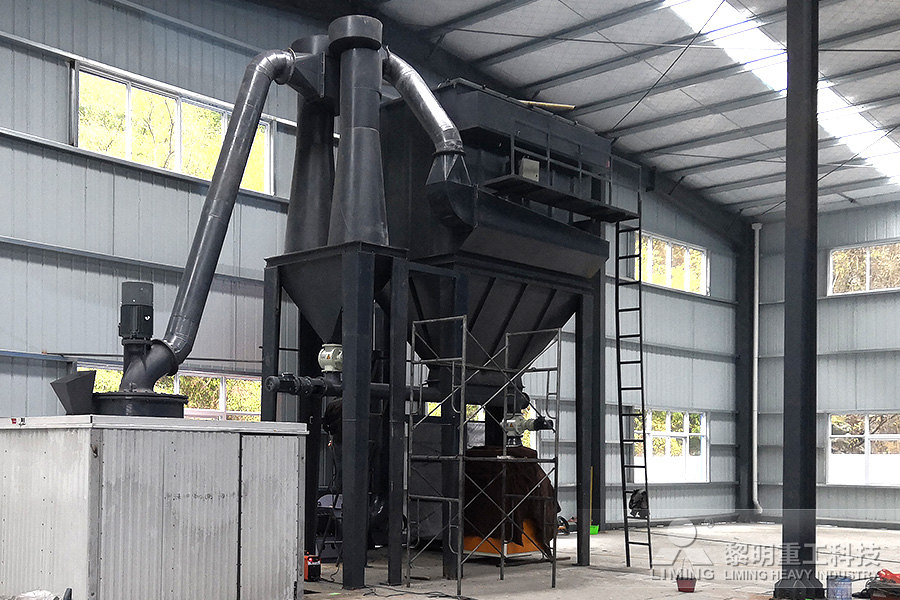
Coal Slime Rotary Drum Dryer Machine
Why Choose Quality Rotary Dryer Manufacturer AGICO As a rotary dryer manufacturer with over 30+ years of experience in designing and producing dryers, AGICO has been renowned for its innovative technology and strict 2020年10月21日 The Drum Mill TM 500 is a laboratory ball mill A TM 500 foodGrade model featuring a stainless steel 316L drum and the hopper is available for applications bones, carbon fibers, catalysts, cellulose, cement Drum Mill TM 500 BulkInsideRotary drum mill Rotary drum mills 49 companies 99 products My filters rotary drum Delete all High operational reliability, stable performance, simple structure and easy maintenance Model with speed controller available(Model Rotary drum mill, Rotary drum grinding mill All Dynamic model for a dense medium drum separator in coal beneficiation EJ Meyera,b, IK Craigb,⇑ a Snr Solution Architect, MES Plant – Business Solution Provision, Exxaro Resources, PO Box 9229, Pretoria 0001, South Africa bDepartment of Electrical, Electronic and Computer Engineering, University of Pretoria, Pretoria 0002, South Africa article infoDynamic model for a dense medium drum separator in coal
.jpg)
Dynamic model for a dense medium drum separator in coal beneficiation
2015年6月30日 For DMD, Meyer and Craig (2015) proposed the dynamic model for dynamic control of the Wemco drum to estimate the grade of products using coal washability and drum partitioning behavior [119]2019年12月5日 The lime ball mill can superfinely grind lime or coal ash, consists of feeding part, the discharging part, turning part, Wet Drum Magnetic Separator; Three Disc Dry Magnetic Separator; The selected limestone wet ball mill model can be used more widely to ensure the smooth commissioning of the equipment at the initial stage; 3Lime Ball Mill JXSC Machine2 Coal mill model The coal mill model was derived from mass, power and heat balance equations of the mill containing converting factors known as model coefficients The coal classification is not considered in the model but it is classified as pulverized and unpulverized or raw coal The derivation of coal mill model is discussed in RefsMathematical validation and comparison of ball tube and bowl mill 2022年7月26日 Aiming at the typical faults in the coal mills operation process, the kernel extreme learning machine diagnosis model based on variational model feature extraction and kernel principal component analysis is offered Firstly, the collected signals of vibration and loading force, corresponding to typical faults of coal mill, are decomposed by variational model Fault Diagnosis of Coal Mill Based on Kernel Extreme Learning
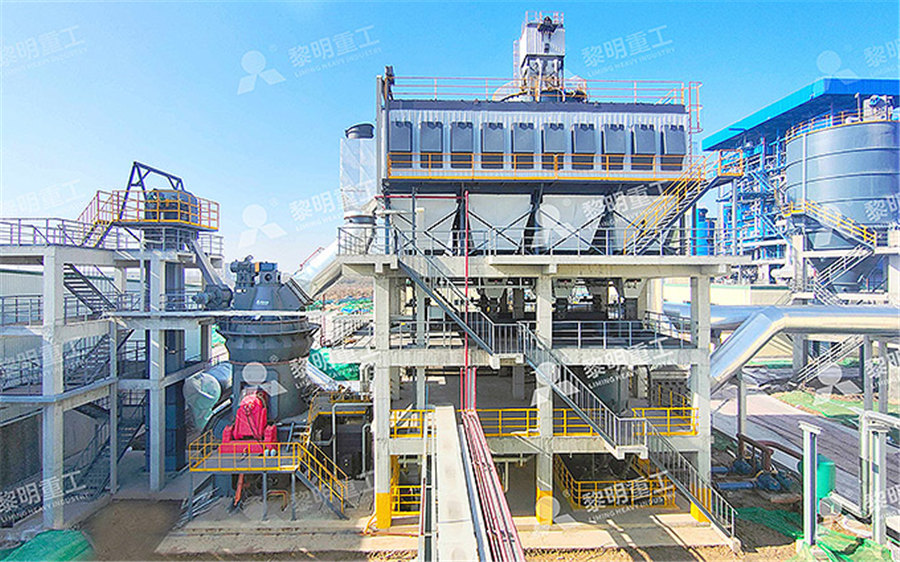
Factors affecting thin coal seam shearer drum coalloading
2019年6月1日 To solve the problem of a low coalloading rate being exhibited by the drum shearer on Chinese thin coal seams, systematic tests and research were performed to study the pivotal factors’ influences on drum coalloading rate using a model test method The effects of the drum hub diameter, cutting depth, vane helix angle, drum rotation speed and hauling speed on 2021年10月1日 China's mining of medium and thick coal seams has reached the leading technical level [1], but there are still difficulties in mining thin coal seamsThe main reasons are that the mining space of thin coal seams is relatively small, manual operations are difficult, the mining efficiency is low, and the economic income cannot make ends meet, resulting in Wear analysis and performance optimization of drum blade in mining coal