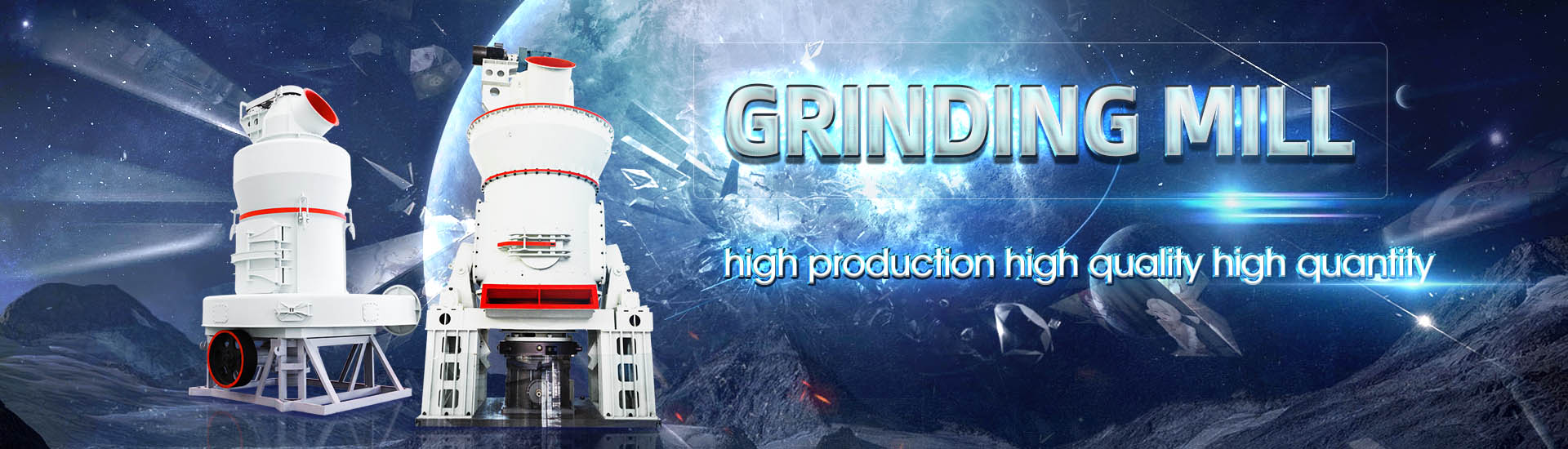
Deep processing of reduced iron oxide
.jpg)
Deep reduction behavior of iron oxide and its effect on direct CO
2012年1月15日 To investigate the reduction behaviors of iron oxide prepared by supporting Fe 2 O 3 on γAl 2 O 3 and its effect on CO oxidation, fluidizedbed combustion experiments, 2024年10月1日 Clearly, innovative deep processing techniques for iron ores with an iron grade below 67% are required Regridding followed by the beneficiation of ironore concentrates can Development of Direct Reduced Iron in China: Challenges and 2022年8月23日 This study gave an overview of the reductionsmelting process as a third generational alternative for the modernday iron and steelmaking process whose hallmark is to mitigate the(PDF) An Overview of the ReductionSmelting Process 2022年8月22日 Hydrogenbased direct reduction (HyDR) is an attractive processing technology, given that direct reduction (DR) furnaces are routinely operated in the steel industry but with Hydrogenbased direct reduction of iron oxide at 700°C Springer
.jpg)
Reduction behavior and microstructure evolution of iron oxides
2023年8月26日 In this study, two types of iron oxides with main phase compositions of hematite and magnetite are reduced by pure H 2 through a temperatureprogrammed reduction method 2023年1月12日 In the direct reduction process, the reducing agent converts the iron ore to elemental iron directly The final product is directly reduced iron (DRI) including matrix elements from the ore Typical feed gases for direct reduction Hydrogen‐Based Direct Reduction of Iron Oxides 2023年8月30日 Due to the large environmental impacts of BF technology, alternative ironmaking technologies have been explored; two widely used processes are direct reduction (DR) and smelting reduction (SR) The DR HydrogenBased Direct Reduction of Iron Oxides: A 2024年5月17日 Using biomass as a renewable carbon source for iron ore reduction in blast furnaces significantly cuts CO 2 emissions compared to conventional coal and cokeAn Overview Analysis of Current Research Status in
.jpg)
Hydrogenbased direct reduction of iron oxide at 700°C
2022年8月22日 Steel production causes a third of all industrial CO2 emissions due to the use of carbonbased substances as reductants for iron ores, making it a key driver of global warming Therefore, research efforts aim to replace these reductants with sustainably produced hydrogen Hydrogenbased direct reduction (HyDR) is an attractive processing technology, given that Download scientific diagram Gasphase equilibrium composition of H2reduced iron oxide from publication: Hydrogen Reduction of Hematite Ore Fines to Magnetite Ore Fines at Low Temperatures Gasphase equilibrium composition of H2reduced 2023年8月30日 Greenhouse gas emissions are the primary root cause of anthropogenic climate change The heterogeneity of industrial operations and the use of carbonaceous fossil fuels as raw materials makes it challenging to find HydrogenBased Direct Reduction of Iron Oxides: A 2023年6月15日 At present, a large quantity of iron resource could not be utilized effectively, such as iron oxides (eg, oolitic hematite, limonite and cyanide residue) and smelting slags in the form of fayalite (eg, iron slag, copper slag and nickel slag) This kind of iron resources, containing 30%–40% iron, is still very difficult to be recycled or utilizedReview on nucleation and growth behavior of iron grain during deep
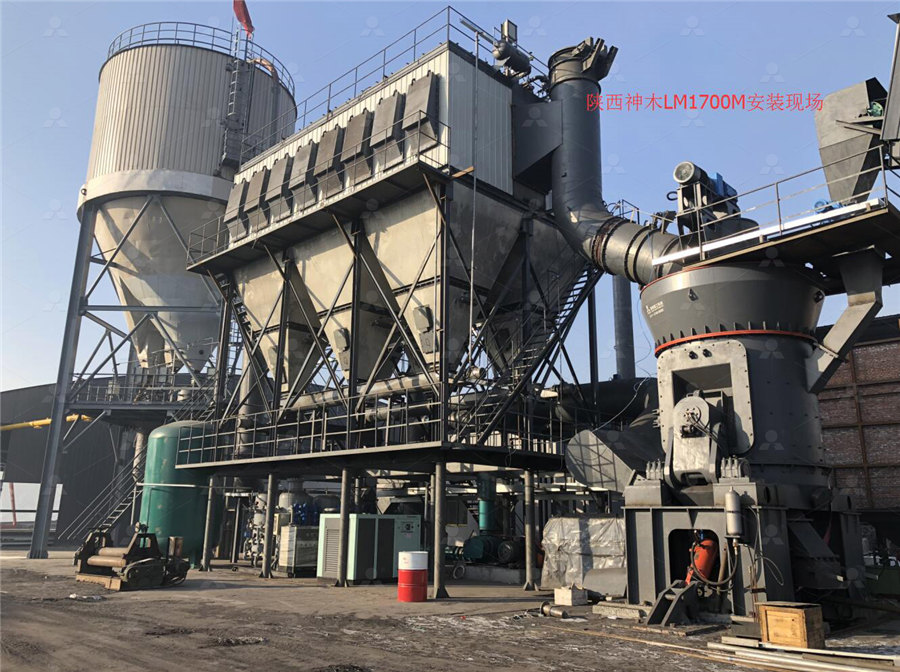
Energy and exergy analyses of hydrogen direct reduction iron by
2024年8月28日 It tells that, under the hydrogen atmosphere, the reduction of iron oxide to iron occurs through a stepbystep reduction process, which is closely influenced by the reaction temperature Below 570°C, the primary reaction sequence involves Fe 2 O 3 → Fe 3 O 4 → Fe2019年7月19日 The employed fuels are natural gas and/or coal The energy consumption is in the order of 104 GJ/tDRI that is equivalent to 300 m 3 of natural gas per ton of reduced iron The CO 2 emissions are quantified in the range 077–092 t of CO 2 per ton of steel As a function of the employed reducing reactors, the systems are of four main types:Direct Reduced Iron: Most Efficient Technologies for Greenhouse 2023年11月10日 The iron ore was successfully reduced to predominantly metallic iron phase when up to 30% by weight of biomass was introduced into the mixture Reduction commenced at approximately 670°C and was A REVIEW OF IRONMAKING BY DIRECT REDUCTION PROCESSES: 2022年8月23日 Preliminary studies have revealed that there are tendencies to achieve more than a 90 % metallization degree from the direct reduction of iron ore/oxides using noncoking coal or charcoal as a (PDF) An Overview of the ReductionSmelting Process of Iron Oxides
.jpg)
Graphene oxide: Fe2O3 nanocomposite: synthesis, properties, and
2023年1月28日 Graphene oxide/Iron III oxide (GO: Fe2O3) nanocomposites (NCs) have been topical in recent times owing to the enhanced properties they exhibit GO acting as a graphene derivative has demonstrated superior features as obtainable in a graphene sheet Furthermore, the attachment of oxygen functional groups at its basal and edge planes of graphene has 2023年8月5日 Iron oxide (αFe2O3) was synthesized from red mud extract followed by hydrothermal reaction at 150 °C/6–24 h in the presence of NH4OH The crystallinity of αFe2O3 increased with reaction time as confirmed by Xray Diffraction, while Fourier transform infrared spectroscopy and Raman illustrate the symmetric stretching vibration of the Fe–O bond in α Low Temperature Processing of Iron Oxide Nanoflakes from Red iron oxide structure classication statistics, this paper proposes a deep learningbased automatic recognition method for iron oxide structure, and the main pro cess is shown in Fig 3 Firstly, an image recognition network combining SENet to enhance the aention mechanism is proposed based on the Unet structureDevelopment and application of automatic identification methods 2024年4月30日 Conversely, HPR starts violent and unstable with arc delocalization, but proceeds smoothly and efficiently when processing semireduced oxides, an effect which might be related to the material's (PDF) Investigation of the Use of Hydrogen in Direct Reduced Iron
.jpg)
Development and application of automatic identification methods
2023年11月29日 Iron oxide structure has an important impact on the surface quality of steel, and the experimental segmentation and identification of iron oxide structure can provide help for statistical and modeling studies of iron oxide In this paper, the images of the oxide scale structure were used to establishing a dataset, and a segmentation model was established, which was 2024年8月1日 Achieving the desired pellet activity is a complex task that requires a deep understanding of the underlying chemical and physical processes In fact, the composition of iron oxide pellets can vary considerably, and understanding how the different components affect their activity is a difficult task [4]The quality of iron oxide pellets depends on various factors, such Effect of composition and processing conditions on the direct 2021年12月1日 Lachén et al (2020) investigated the reduction of synthetic iron oxide (98 wt% hematite) and iron oxide ore (813 wt% hematite) with 25 vol% of an equimolar mixture of methane, carbon dioxide and nitrogen in argon at 873 K Mendiara et al (2019) investigated the reduction of hematite ore from Tierga (Zaragoza, Spain) in a gas feed of 5–60 Clean iron production through direct reduction of mineral iron 2023年4月5日 Recent Trends in the Technologies of the Direct Reduction and Smelting Process of Iron Ore/Iron Oxide in the Extraction of Iron and Steelmaking April 2023 DOI: 105772/intechopen(PDF) Recent Trends in the Technologies of the Direct
.jpg)
(PDF) Hydrogenbased direct reduction of iron oxide at 700°C
2022年2月17日 Overview of the microstructure, phase fractions, and porosity along the radius of a hematite pellet reduced at 700 °C for 30 minutes with pure hydrogen, probed by scanning electron microscopy 2004年11月1日 However, for iron, T melt = 1539 ºC, the decrease in the melting point of iron can be caused by two factors: (1) the carbothermal reduction of Fe 2 O 3 particles in the medium of reactive carbon Reduction of iron oxide in carbon monoxide atmosphereAmong heavy industrial sectors worldwide, the steel industry ranks first in carbon dioxide (CO 2) emissionsTechnologies that produce direct reduced iron (DRI) enable the industry to reduce emissions or even approach netzero CO 2 emissions for steel production Herein, comprehensive cradletogate (CTG) life cycle analysis (LCA) and technoeconomic analysis (TEA) are used Cost and Life Cycle Analysis for Deep CO Wiley Online Library2013年3月16日 One is in metallic form which is known as metallic iron, Fe (M), and the second form of iron which is present in residual iron oxides, Fe (O) The total iron, Fe (T), in DRI is the sum of these two iron components Metallic iron is the aggregate quantity of iron, either free or combined with carbon (as cementite) present in DRIDirect Reduced Iron and its Production Processes – IspatGuru

Hydrogen Plasma Processing of Iron Ore
2017年6月21日 Iron is currently produced by carbothermic reduction of oxide ores This is a multiplestage process that requires largescale equipment and high capital investment, and produces large amounts of CO212 Generation and Processing of Direct Reduced Iron Fines There are two principal sources of fines generation during the direct reduction process, as illustrated in the graphic below, Iron Oxide Fines 62 68 0 0 2 5 2 5 Gangue = SiO 2 + Al 2 O 3 + CaO + MgO Direct Reduced Iron Fines: Guide for Shipping, Handling and 2020年6月3日 A new route for making steel from iron ore based on the use of hydrogen to reduce iron oxides is presented, detailed and analyzed The main advantage of this steelmaking route is the dramatic reduction (90% off) in CO2 Hydrogen Ironmaking: How It Works MDPI2021年5月18日 21 Iron (III) Oxides Iron (III) oxide is, of course, a compound that exhibits four different crystalline polymorphs: αFe 2 O 3, βFe 2 O 3, γFe 2 O 3, and εFe 2 O 3Hematite and maghemite usually appear in nature, while beta and epsilon structures are generally synthetic oxides [10, 11]In general, the iron (III) oxides anions arrange in closepacked structures, Synthesis, Properties, and Applications of Iron Oxides: Versatility
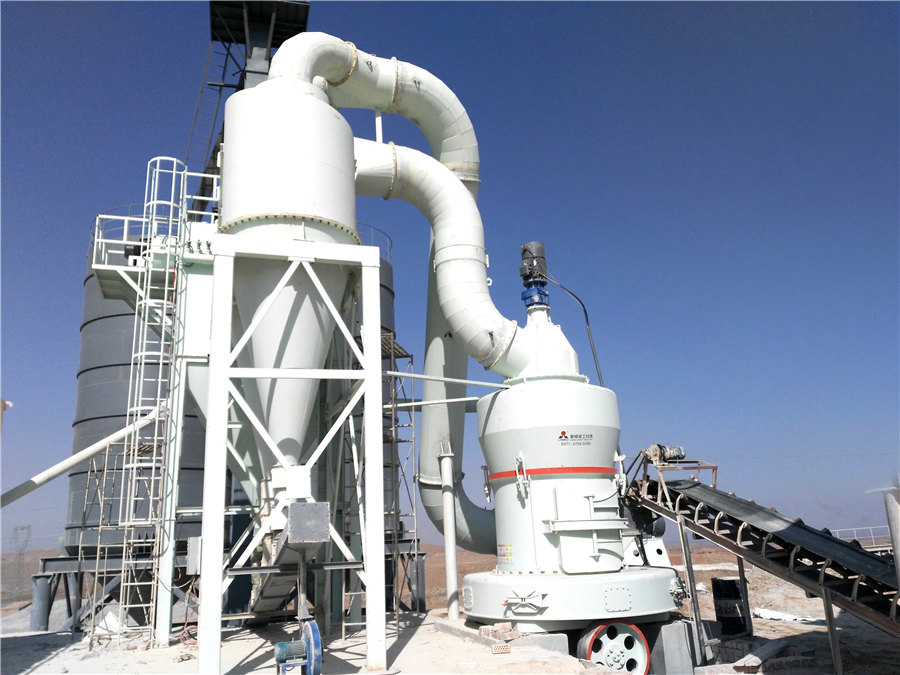
An Overview Analysis of Current Research Status in Iron Oxides
2024年5月17日 Moreover, arc plasma operates much more stably when processing semireduced oxides (for example, pellets reduced by 38%) compared to using hematitebased materials as the starting input 25 Critical Analysis of Reduction in Iron Oxides with Hydrogen, Advantages and Disadvantages of Reduction of Iron Oxides with Hydrogen2024年10月15日 It is known that the reactions in the hydrogenbased direct reduction of iron oxide can proceed in two or three stages, depending on the furnace temperature [] When the temperature is below 570 °C, direct reduction of Fe 2 O 3 → Fe 3 O 4 → metallic iron (Fe) takes place, regardless of the type of reducing gas At temperatures above 570 °C, Fe 3 O 4 → FeO Optimization of Hydrogen Utilization and Process Efficiency in the 2024年3月16日 In the wake of the era of big data, the techniques of deep learning have become an essential research direction in the machine learning field and are beginning to be applied in the steel industry The sintering process is an extremely complex industrial scene As the main process of the blast furnace ironmaking industry, it has great economic value and Application of deep learning in iron ore sintering process: a review2017年1月1日 Effective technology for a complex wasteless processing of the iron ores has been designed and includes three main components (plats): comminution plant, briquette plant, pigment plant(PDF) Effective Processing of the Iron Ores ResearchGate
.jpg)
Threedimensional characterization of porosity in iron ore pellets:
2024年8月1日 In direct reduction, iron oxides are solidstate reduced to metallic iron without melting, resulting in increased porosity and fine generation (Pfeiffer et al, 2023) The removal of oxygen leaves a highly porous structure ( Meshram et al, 2022 , Man and Feng, 2016 ), and both raw materials and reduction temperature influence DRI porosity ( Cavaliere et al, 2023 , 2024年5月22日 The iron and steel industry is a major emitter of global CO 2 emissions, responsible for approximately 7 to 9% 1–3 Conventional blast furnacebasic oxygen furnace (BFBOF) steelmaking process (732% share) emits about two tonnes of CO 2 per tonne of steelmaking due to the use of 800 kg of coal/t steel 4,5 Direct reduced iron (DRI) followed by Process modelling for the production of hydrogenbased direct reduced 2023年8月1日 In the past decades, direct reduction (DR) represented an affordable innovative process in the ironmaking processing The most widespread technologies are the Midrex and HYL shaft furnaces accounting for almost 80% of the globally produced direct reduced iron [[2], [3], [4], [5]]A comprehensive understanding of the role of the reducing gas composition and Effect of reducing atmosphere on the direct reduction of iron oxides 2019年12月24日 Ionic liquids (ILs) and deep eutectic solvents (DESs) have proven to be suitable solvents and reactants for lowtemperature reactions To date, several attempts were made to apply this promising class of materials to Synthesis and Dissolution of Metal Oxides in Ionic
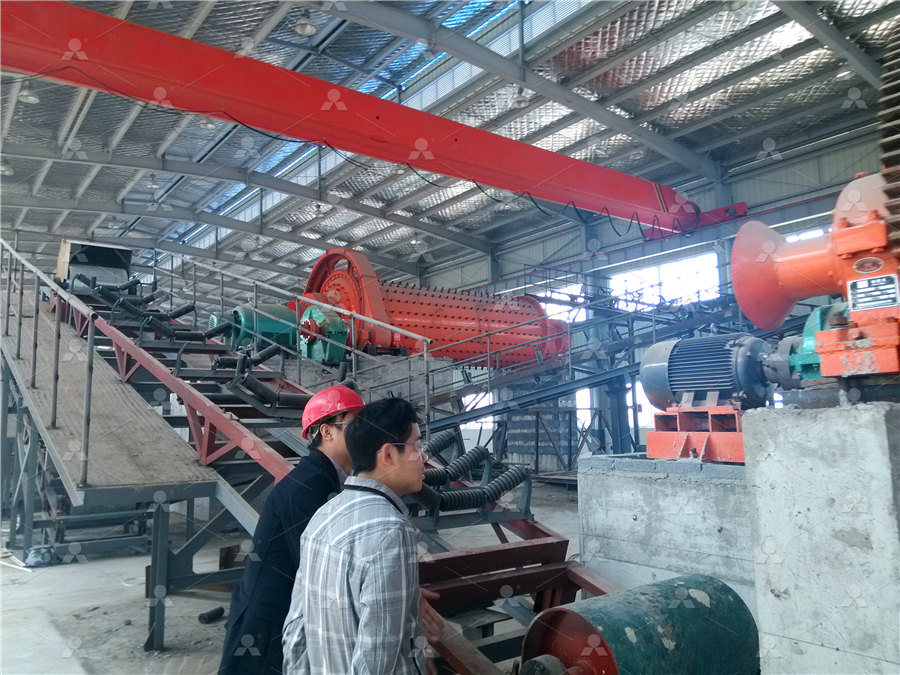
HydrogenBased Direct Reduction of Iron Oxides Pellets Modeling
HydrogenBased Direct Reduction of Iron Oxides Pellets Modeling Pasquale Cavaliere,* Angelo Perrone, Debora Marsano, and Vito process in the ironmaking processing widespread technologies are the Midrex and HYL shaft furnaces accounting for almost 80% of the globally produced direct reduced iron[2] Here, basically, syngas is employed 2019年3月1日 Graphene is an atomicallythin, 2dimensional (2D) sheet of sp 2 carbon atoms in a honeycomb structure It has been shown to have many desirable properties such as high mechanical strength [1], electrical conductivity [2], molecular barrier abilities [3] and other remarkable propertiesFor these reasons, it has been the goal of countless research efforts to Synthesis, properties, and applications of graphene oxide/reduced 2023年11月1日 Since then, successful iron oxide electroreduction in alkaline systems has been reported using various species of iron oxide (αFe 2 O 3, Fe 3 O 4, and αFeOOH) with different chemical reactivity responses [16] and different compounds, such as redmud of bauxite residue [1], hematitebased ceramics [31] and magnesium ferro spinel [32], as well as residual Comparative study of electroreduction of iron oxide using acidic 2024年3月22日 Particles outside the ore are reduced into iron but particles of iron oxide at the core do not undergo reduction In actual conditions, iron ore has some extra gangue minerals whose types and numbers are determined by iron ore itself and mineral processing technology Typical gangue oxides include SiO 2, CaO, MgO, and AI 2 O 3Direct Reduction of Iron Oxides with Hydrogen SpringerLink

Direct reduced iron Wikipedia
Hotbriquetted iron Direct reduced iron (DRI), also called sponge iron, [1] is produced from the direct reduction of iron ore (in the form of lumps, pellets, or fines) into iron by a reducing gas which contains elemental carbon (produced from natural gas or coal) and/or hydrogenWhen hydrogen is used as the reducing gas no carbon dioxide is produced2022年8月22日 Steel production causes a third of all industrial CO2 emissions due to the use of carbonbased substances as reductants for iron ores, making it a key driver of global warming Therefore, research efforts aim to replace these reductants with sustainably produced hydrogen Hydrogenbased direct reduction (HyDR) is an attractive processing technology, given that [PDF] Hydrogenbased direct reduction of iron oxide at 700°C 2024年10月15日 It is known that the reactions in the hydrogenbased direct reduction of iron oxide can proceed in two or three stages, depending on the furnace temperature [] When the temperature is below 570 °C, direct reduction of Fe 2 O 3 → Fe 3 O 4 → metallic iron (Fe) takes place, regardless of the type of reducing gas At temperatures above 570 °C, Fe 3 O 4 → FeO Optimization of Hydrogen Utilization and Process Efficiency in the 2019年3月21日 The research from Qu et al [Citation 10] uncovered the melting behaviour of the reduced iron oxides in the experiments A complete melting down of all particles was observed at 1700 K when the particle residence time was above 970 ms It comes to the third characteristic that reduction of iron oxides accompanies melting above 1650 KReview and data evaluation for hightemperature reduction of iron oxide