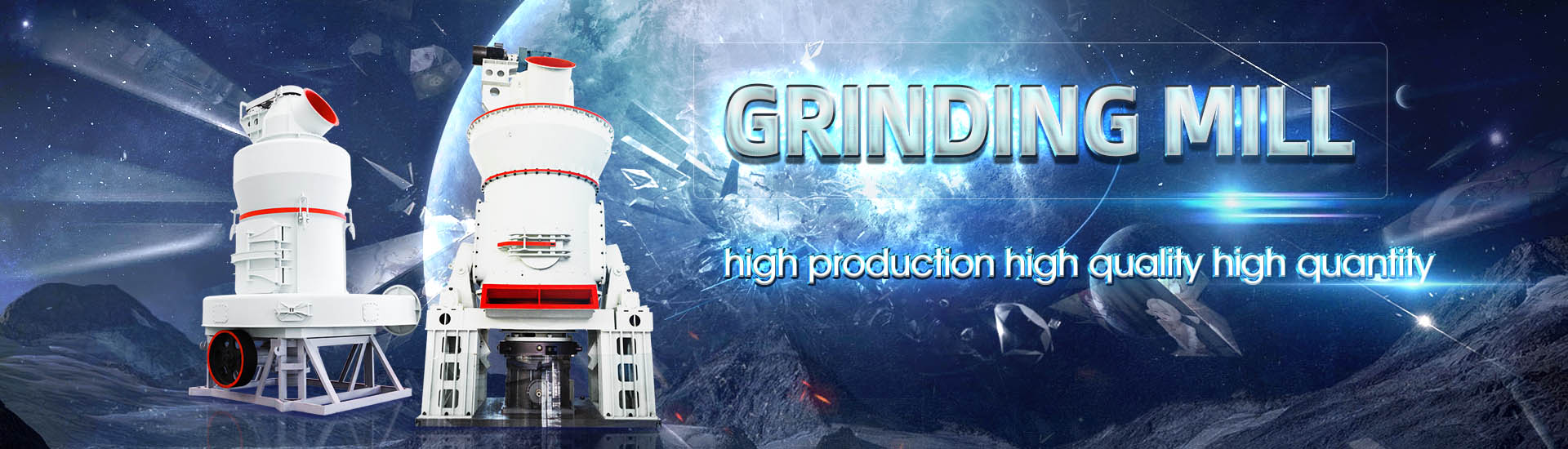
mill tooth surface contact requirements
.jpg)
Analytical Calculation of the Tooth Surface Contact Stress of
2020年8月6日 The present work establishes analytical solutions to research the effect of different parameters for the contact stress of VHCATT cylindrical gear incorporating elastic deformation on the tooth surface, and which have shown that the different module, 2019年2月1日 A new more accurate analytical model for calculating the tooth surface contact stress of tiprelieved gears is established based on the accurate tooth profile equations An analytical method for calculating the tooth surface contact 2020年1月4日 To avoid tooth edge contact of high contact ratio spiral bevel gear under misalignment or heavy load, a tooth surface modification method based on cutter blade profile Tooth surface modification method of facemilling spiral bevel 2024年1月3日 The actual tooth contact patterns of the spiral bevel gear pair become continuous when meshing tooth surfaces are elastically deformed This paper presents an ultimate motion MultiPoint Control for FaceMilled Spiral Bevel Gears with a
.jpg)
The optimal calculation and machining of the spiral bevel gear
milling and bevel gear face hobbing NISHINO et al, (2009) described the generation of tooth surface mathematically based on the movement of machine tool in end hobbing, and carried 2024年2月27日 In this paper, a new type of pointcontact gear formed by doublearc milling cutter on fouraxes machine is proposed Firstly, the meshing equation is proposed to obtain a Meshing equation, tooth contact analysis, stress analysis and 2006年4月6日 Modeling of tooth surface generation and simulation of contact is an important part of computerized design and manufacturing of spiral bevel and hypoid gears This paper Enhanced Algorithms of Contact Simulation for Hypoid Gear 2022年11月24日 To effectively improve the design and machining efficiency of face gears, a method of tooth surface design and side milling of ruled line face gears is proposed in this paperResearch on tooth surface design and side milling machining
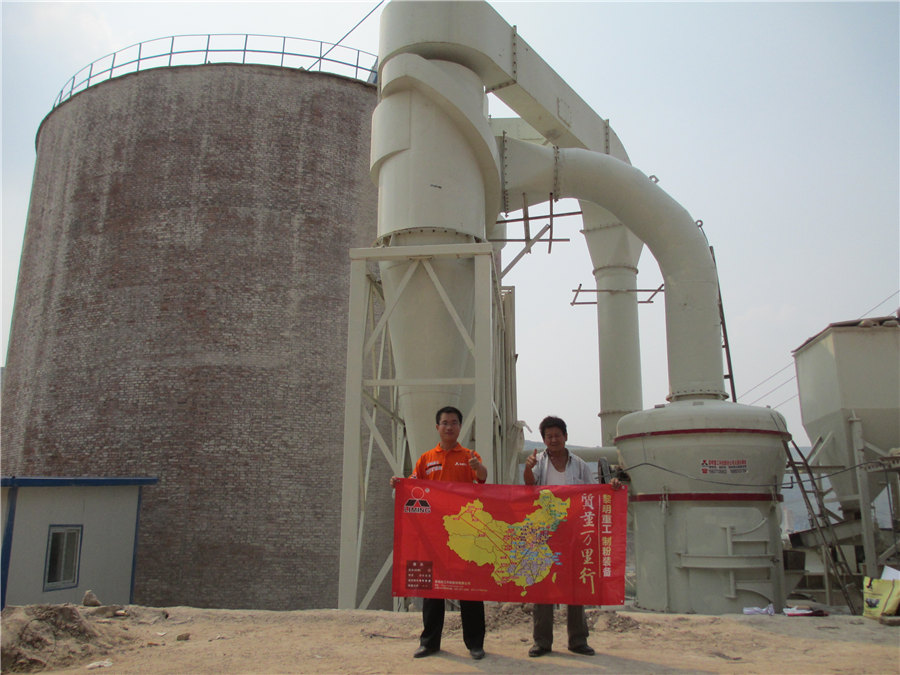
Tooth flank machining and modelling of line contact spiral bevel
2023年1月31日 Milling spiral bevel gears using the cutterhead to form the line contact conjugate flank with tapered teeth depth is challenging With this milling process, only local contact 2011年1月12日 The same surface feet per minute can be used for thread mills as for end mills of the same size The feed rate must be slower, however, since thread milling often involves unfavorable lengthtodiameter ratios Also, keep Thread Milling Techniques NEXT GENERATION ditions on the mill as on the gear cutter Tooth attribute inspections, such as profile and pitch, as well as tooth thickness, are recorded to confirm that the gear matches the design requirements of the engineer A roll contact check, or fixed center contact check is also completed to confirm that the helix (lead) of the gear matches the Girth Gear Inspection Pre and Post Manufacture Gear TechnologyProbst Class Colloid mill Type O Colloid mill Type O Probst Class Motor/Drive Type O colloid mills are powered by special threephase motors The motors are surfacecooled, have moisture guard insulation (IP55) and are suitable for use with inverters They can be supplied for all voltages, frequencies and protection classesColloid mill Type O
.jpg)
Analysis of the Tooth Surface Contact Area of a CircularArcTooth
DOI: 1021278/TOF Corpus ID: ; Analysis of the Tooth Surface Contact Area of a CircularArcToothTrace Cylindrical Gear under Load @article{Ma2021AnalysisOT, title={Analysis of the Tooth Surface Contact Area of a CircularArcToothTrace Cylindrical Gear under Load}, author={Dengqiu Ma and Yongping Liu and Zhenhuan Ye and Yongqiao Wei Surface roughness is a critical parameter for gears operating under a variety of conditions It directly influences friction and contact temperature, and therefore has an impact on various failure modes such as macropitting, micropitting and scuffing Typically, gear tooth surface roughness is measured using aA Comparison of Surface Roughness Measurement Methods for Gear Tooth transmission error, and achieved the whole gear surface control of the gear surface contact performance Tang et al, (2009)studied the design of point engagement tooth surface of spiral bevel gear based on predetermined engagement characteristics, strictly limiting the contact trace and the parameters below the third order and the tooth surfaceThe optimal calculation and machining of the spiral bevel gear December 2015; ARCHIVE Proceedings of the Institution of Mechanical Engineers Part C Journal of Mechanical Engineering Science 19891996 (vols 203210) 230(7)Tooth modification for optimizing gear contact of a wind
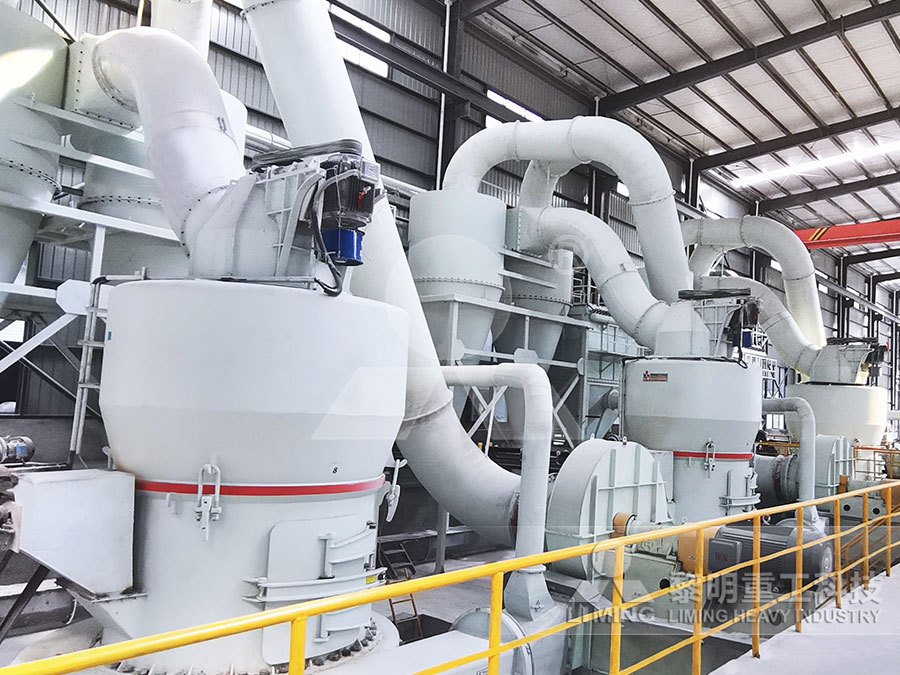
Face Milling 101: Everything You Need To Know BOYI
2024年7月10日 Different face milling operations entail vastly different requirements for cutting tools and shifting the surface contact point to the more robust primary cutting edges of the insert High Feed Milling face milling can be performed at extremely high pertooth feed rates (up to 4mm/z) Figure 3 – high feed milling cutting This guide offers you quality information about surface finish and provides a handy surface roughness chart for better understanding Noncontact methods; milling, drilling, and more Therefore, they are for clearance surfaces with stress requirements and design permits 32 125: The roughest kind of surface is often Surface Roughness Chart: Understanding Surface Finishes2019年7月19日 The end mill and worm tooth surface contact at point Q and the coordinates of point Q in Oxyz is expressed as a position vector X r (Analysis of requirements and specifications) Int J Autom Technol 1:78–86 Article Google Scholar Moriwaki T (2008) Multifunctional machine tool CIRP Ann 57:736–749 Article Machining method of largesized cylindrical worm gears with 2013年1月29日 Straight bevel gears are widely used in the plant of largesized power generation when the gears have large size The purpose of this study is to manufacture the largesized straight bevel gears with equidepth teeth on a multitasking machine The manufacturing method has the advantages of arbitrary modification of the tooth surface and machining of the part Tooth Contact Analysis and Manufacture on Multitasking Machine
.jpg)
Hypoid Gear Tooth Surface Finish Requirements
This article will delve into the various aspects of hypoid gear tooth surface finish requirements, discussing their significance and the necessary considerations in achieving the desired finish Surface Finish Considerations 1 Contact Pattern Optimization Achieving the optimal contact pattern is a fundamental aspect of hypoid gear design2024年5月30日 Choose a thread mill geometry that aligns with your machining requirements 4 Assess Cutting Parameters : Once you’ve selected a thread mill, it’s crucial to optimize cutting parameters such as spindle speed, feed rate, Choosing The Right Thread Mill: A Machinist's Guide2024年7月22日 Operational Requirements: Align the mill’s operational needs for efficient They make highquality road construction project specific superior performing mill tooth among Wear plates ensure that there is no direct contact between the machine and the surface being milled which protects it further thereby prolonging Ultimate Guide to HighQuality Road Milling Teeth forApplications of Mill Tooth Tricone Bits Mill tooth tricone bits find applications in a wide range of drilling scenarios, making them incredibly versatile tools Some common applications include: Oil and Gas Drilling: Mill tooth tricone bits are often used in oil and gas exploration and extractionUnveiling the Mill Tooth Tricone Bit: A Guide to Efficient Drilling
.jpg)
Digital tooth contact analysis of face gear drives with an accurate
2022年1月1日 Zhou et al presented an accurate measurement model of the face gear tooth surface, wherein the digital tooth contact analysis is implemented with a robust algorithm [7], and they further applied 2023年10月3日 The mill tooth and insert bits use the same classification for cone and teeth row terminology The cone surface develops a hardness of 60 R, (Rockwell hardness test) hut gets progressively softer with inner cone depth, as shown in Fig 720 Table This reduces the amount of contact between the drill bit and the formation, Bit Cones Drilling Engineering Rig Worker2019年4月1日 Results show that a high surface integrity state with surface hardness of 6865 HV, maximum compressive residual stress of 1162 MPa, and surface roughness Sa of 036 μm, exhibits the highest Tribological behavior of coated spur gear pairs with tooth surface China leading provider of Tricone Drill Bits and Mill Tooth Drill Bit, Hejian Ruida Petroleum etc to the vicinity of the working point for later use ③According to the requirements of hole position design, ensure the reliable positioning of the ⑧When there is water on the working surface, use a largediameter drill bit to Quality Tricone Drill Bits Mill Tooth Drill Bit factory from China
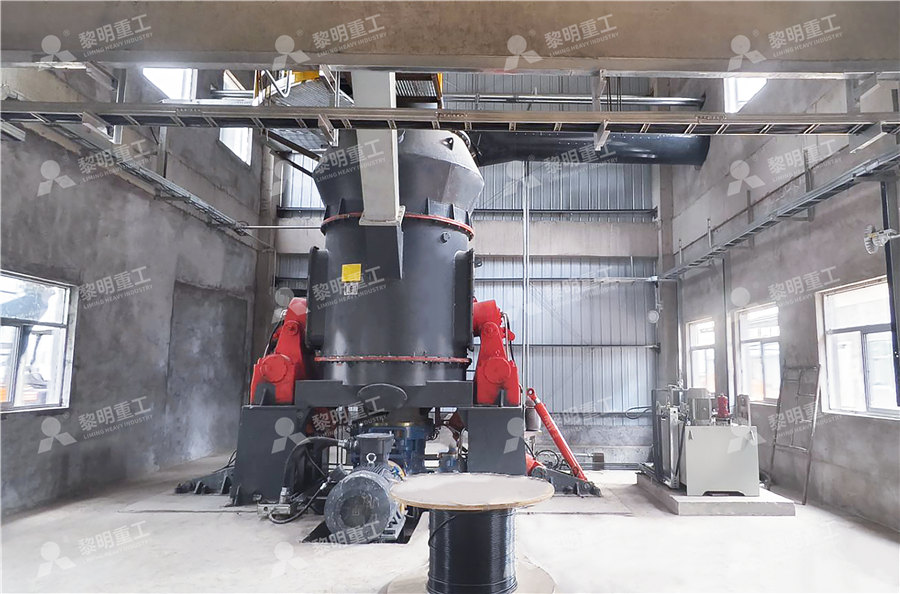
Ball mill pinion prmdrive
2019年9月22日 Mainly is the pinion material and blank weight, followed by the specific requirements and the tedious degree of gear processingThe pinion gears of ball mill manufactured by our factory are all processed by hobbing teeth or grinding teeth, the accuarcy of teeth can up to ISO6, and the tooth surface is quenched with high frequency2020年1月4日 To avoid tooth edge contact of high contact ratio spiral bevel gear under misalignment or heavy load, a tooth surface modification method based on cutter blade profile correction is proposed Generally, an arc blade is used to substitute the straight blade of cutterhead to get the ideal tooth surface Firstly of all, the mathematical model of the cutter blade Tooth surface modification method of facemilling spiral bevel 2011年5月12日 The three diamensional (3D) scanning measurement method of tooth flank form of generated face mill gear pair is proposed, which is based on the conjugate mating tooth flank form In this method, deviation sensor is placed at the position which has certain offset from the gear axis and synchronized to the gear rotation This method realizes the 3D tooth flank form [PDF] Development of scanning measurement of tooth flankform 2024年1月28日 Importance of tooth geometry in achieving optimal chip removal The tooth geometry of an end mill is another crucial factor influencing chip removal efficiency It primarily includes two aspects: rake angle and relief Roughing End Mill: Everything You Need to Know

Clinical guide Dentsply Sirona
Now perform this anterior tooth scan on the contralateral side, also from the 2nd premolar to the midline Attention: as you scan, continuously ensure the preparation is dry The longer the scan time, the greater the risk of saliva running onto the tooth surface Stop the scanning process at any time and dry the surface to obtain an optimal result2020年10月14日 Based on the threedimensional (3D) finite element method (FEM) and Taguchi method (TM), this paper analyzes the tooth surface contact stress (TSCS) of spur gears with three different influence (PDF) Analysis and Optimization of Tooth Surface Contact Stress 2024年9月23日 Technical requirements for rolling mill assembly 利玛集团 September 23, 2024; 10:15 am; The contact surface of the balancing block is spherical, The thread is a trapezoidal tooth with a sixthgrade precisionTechnical requirements for Rolling mill roll assembly2024年3月28日 The end mill is a cutting tool that has teeth on both sides This tool is versatile and can be used for a variety of drilling operations The term “end mill” is commonly used for flatbottomed tools Unlike a drill bit, which only cuts in the axial direction, the end mill is capable of cutting in all directions10 Types of Milling Cutters: Uses and Selection Principles
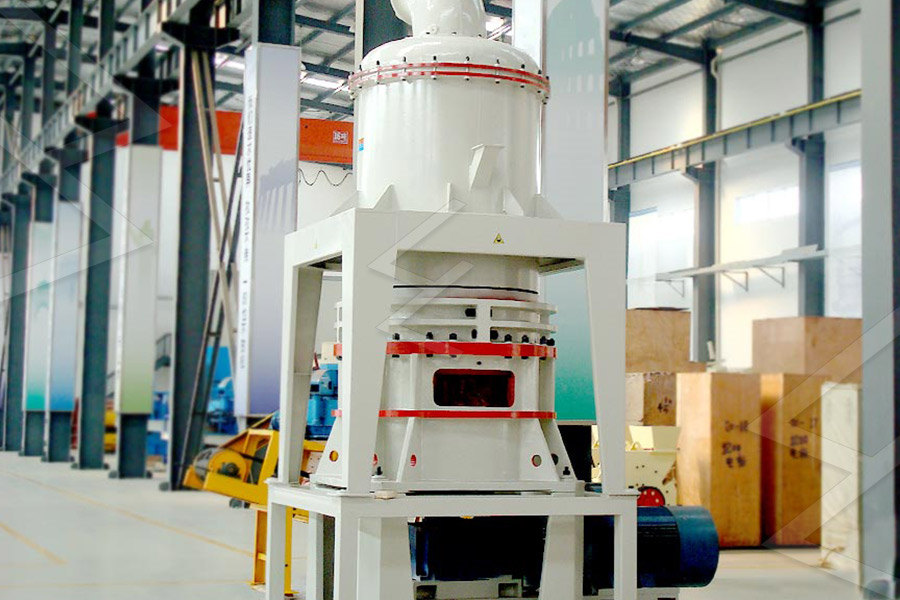
A Comprehensive Optimization Model of Tooth Surface
2022年8月29日 A Comprehensive Optimization Model of Tooth Surface Parameters for the Minimization of Contact Stress of Helical Face Gears by Considering the Avoidance of Edge Contact2024年8月15日 Furthermore, the tooth pitch must allow for proper chip formation and evacuation Insufficient chip space can lead to chip packing, potentially damaging both the cutting edges and the workpiece surface Conversely, excessively sparse tooth arrangements may result in increased cutting forces per tooth and reduced surface quality 3How to Choose the Right Face Milling Cutter: A Guide2024年5月1日 Considering that the tooth surfaces of gear and pinion are regular surfaces, this study assumes that the tooth surface contact satisfies the assumption of modified Hertz point contact, and a complete theoretical solution can be obtained both in the tooth surface and at the edge of the tooth surfaceEfficient semianalytic method for single tooth contact analysis of 2015年1月1日 Computerized simulation and modeling of hypoid gears, including modeling of tooth surface generation, simulation of meshing, tooth contact analysis, stress analysis, and tooth contact analysis under load, have been the subjects of EaseOff and Application in Tooth Contact Analysis for Face
.jpg)
Effect of machining inclination angle of ballnose end mill on surface
2013年10月1日 Ballend milling cutter has a strong adaptability and widely used in machining complex surface of parts However, the geometry of ballend milling cutter tooth is complex, and contact points 2020年2月1日 Download Citation Tooth surface modification method of facemilling spiral bevel gears with high contact ratio based on cutter blade profile correction To avoid tooth edge contact of high Tooth surface modification method of facemilling At present, most straight bevel gears use a root fillet transition surface with a radius of 03 modulus This tends to cause excessive root bending stress and reduces the service life of bevel gears In order to solve this problem, a root fillet transition surface controlled by a set of thirdorder Bezier curves is designed based on spherical involute tooth surface In the common cone apex Optimized design of straight bevel gear tooth root transition surface 2022年11月4日 According to the helical gear slicing model, one of the sections is taken as the tooth profile unit of the spur gear Along the tooth profile direction, with v as variable, the tooth profile is divided into n units of width ΔyChange the position of force F (point M in Figure 6) and calculate the stiffness value of this positionIn the Figure 6, S z and l y are the distances from Calculation of gear mesh stiffness and loaded tooth contact
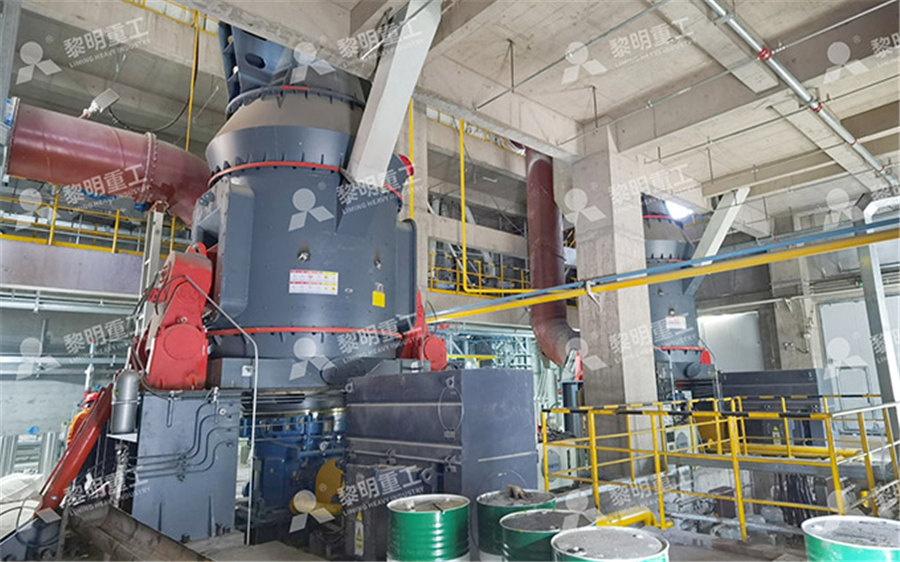
Effects of tooth surface modification on planar double
The planar doubleenveloping hourglass worm gear drives have the larger load capacity and higher transmission efficiency and extensively applied in power transmission However, there is a twicecontact zone on the tooth surface of the worm wheel In this zone, the contact lines crosses with each other so that the contact frequency of the two transmission elements is higher and 2023年11月24日 Face Mill vs Shell Mill vs End Mill, Which One To Choose? The choice between a face mill, shell mill, or end mill depends on the specific machining requirements and the type of operation you need to perform Here are some general guidelines to consider: Face Mill: Choose a face mill when you need to perform facing operations on large flat surfacesFace Mill vs Shell Mill vs End Mill Cutters: Differences JunyingDownload scientific diagram Surface appearance of face milling, single tooth from publication: Segmentation of workpiece surfaces with tool marks based on high definition metrology Tool marks Surface appearance of face milling, single tooth2023年11月23日 The workpiece to be processed is fixed on the lathe At this time, the milling cutter faces the lathe workpiece After calculating the feed per tooth, the multipoint cutting tool of the face mill cuts on the plane of the workpiece Face milling focuses on producing a flat and uniform workpiece surface perpendicular to the spindle axisFace Milling: Definition, Machining, Tools, Tech Tips Ruitai Mould
.jpg)
RESHARPENING INSPECTION The HobbyMachinist
The high point of the tooth rest must contact the tooth face at the high side of the wheel and be the same height as the wheel and work centers Watch the primary relief after trial grinding, to check that the reflectional light or primary relief surface is parallel to axis of the end mill