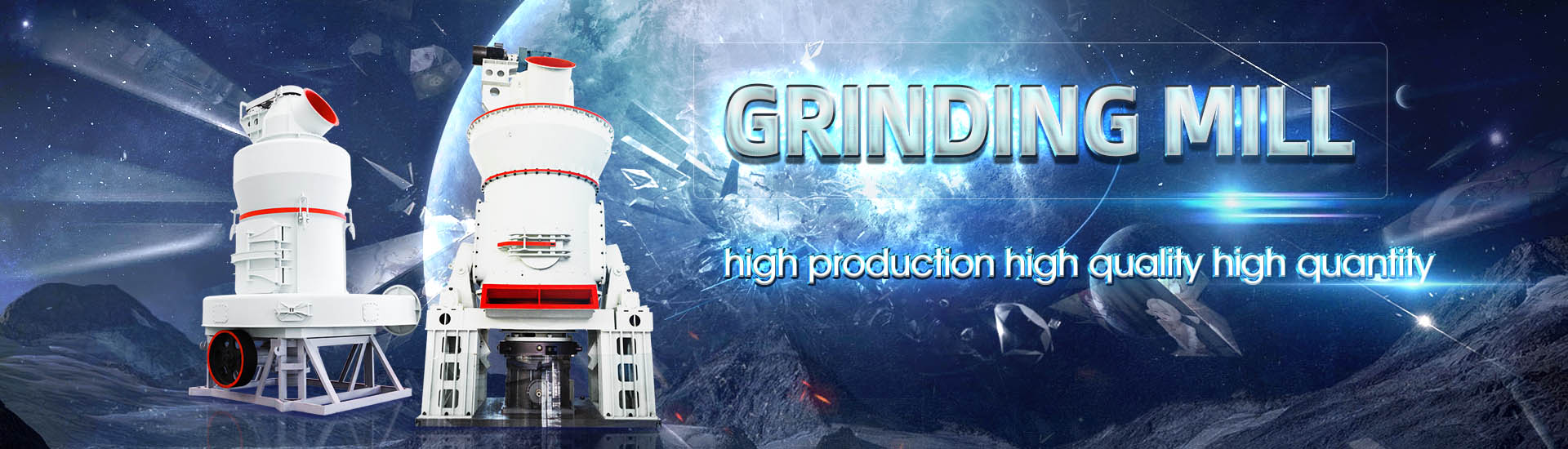
Iron oxide cost process
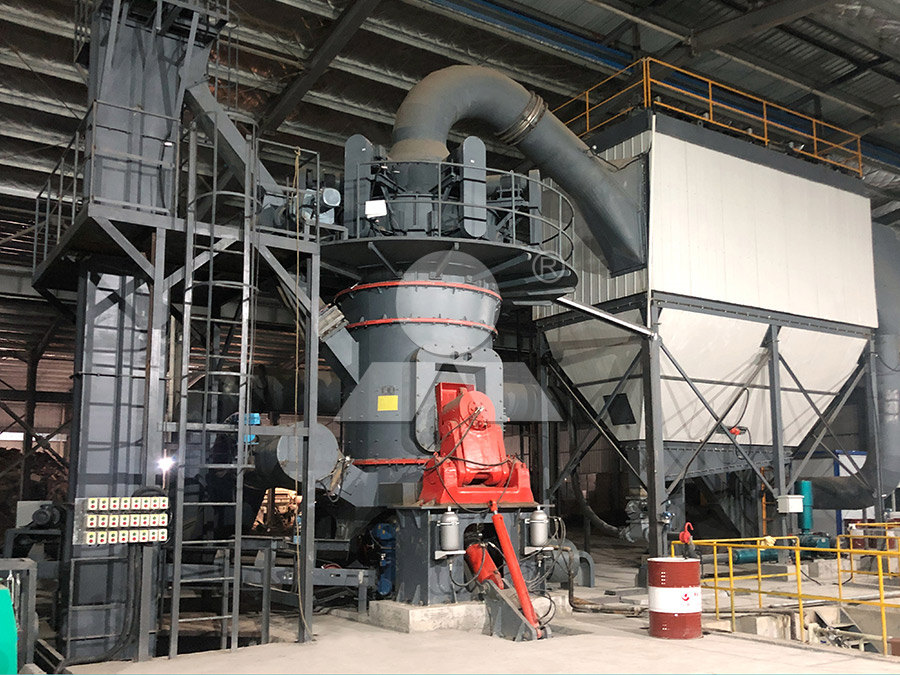
(PDF) An Overview of the ReductionSmelting Process
2022年8月23日 This study gave an overview of the reductionsmelting process as a third generational alternative for the modernday iron and steelmaking process whose hallmark is to mitigate theCosteffectiveness of iron NP preparation technique (depends on the final product and its application), relatively higher cost of production is tolerable, eg, for high end use such as in Synthesis, characterization, applications, and challenges of iron 2023年3月30日 Here, we introduce a sustainable ironmaking process by directly deploying ammonia in iron ore reduction (Figure 1b) An important advantage of this approach is that the green ammonia does not need to be Reducing Iron Oxide with Ammonia: A Sustainable 2021年5月18日 Thereby, in this chapter, we will cover the main characteristics of iron oxides with a focus on preparation processes, physicochemical properties, and their relationship with Synthesis, Properties, and Applications of Iron Oxides: Versatility
.jpg)
Producing iron from salt water and iron oxide
2024年2月8日 “This is a scalable and costeffective way to make iron without creating CO 2 emissions” The socalled chloriron process combines two known electrochemical methods One reduces iron oxide into iron in a sodium 2024年10月1日 Promising lowcarbon routes include use of alternative reductants for ore processing (hydrogen direct reduction, hydrogen plasmasmelting, hydrogen smelting, and Chemical and electrochemical pathways to lowcarbon iron and 2023年3月14日 Compared with MOE process, FFC process is a semicontinuous production process, which has the advantages of simple process, short production cycle, and low Research progress in the preparation of iron by electrochemical 2017年10月17日 Ironmaking is a critical step in producing high performance steel because highquality raw materials reduce the time and energy to purify the iron to steel On the other hand, newer smelting and direct iron reduction From Ore to Iron with Smelting and Direct Iron
.jpg)
Green steel: design and cost analysis of hydrogen
2023年4月4日 In this study, breakeven levelized cost of hydrogen (LCOH) targets for decarbonizing the steel industry with H 2DRI are established by comparing H 2DRI to the commercial natural gasbased direct reduced iron 2022年5月1日 Iron oxide nanoparticles are becoming progressively significant for the improvement of innovative biomedical and nanotechnology requests The keywords iron oxide nanoparticles, Fe 3 O 4 nanoparticles and magnetite nanoparticles have been utilized as a research object in the gross database of articles from the Web of Science The results of these Iron oxide nanoparticles: Preparation methods, functions, Electrochemical ChlorIron Process for Iron Production from Iron Oxide and Seawater Berkley B Noble,12 Louka J Moutarlier,12 Paul A Kempler12* 1Department of Chemistry and Biochemistry, The process can lead to levelized costs Electrochemical ChlorIron Process for Iron Production from Iron Oxide 2021年10月26日 Iron sponge process is the oldest and still the most widely used batch process for sweetening of natural gas and natural gas liquids Overall, iron sponge process has the following characteristics which make it still Gas Sweetening using Iron Sponge Process
.jpg)
MIDREX® Process Midrex Technologies, Inc
Iron oxide, in pellet or lump form, is introduced through a proportioning hopper at the top of the shaft furnace As the iron ore descends through the furnace by gravity flow, it is heated, and the oxygen is removed from the iron ore (reduction) by counterflowing gases that have a Natural Gas Sweetening Alireza Bahadori PhD, in Natural Gas Processing, 2014 10111 Iron oxide (sponge) process The iron sponge process selectively removes H 2 S from gas or liquid streams The process is limited to treating streams containing low concentrations of H 2 S at pressures ranging from 170 to 8300 kPa (ga) The process employs hydrated iron oxide, Iron Sponge Process an overview ScienceDirect Topics2024年3月20日 The iron and steel industry accounts for ∼8% of global greenhouse gas emissions Electrochemical reduction of iron ore to metal for electric arc furnaces can enable sustainable steel production, but existing electrochemical processes require expensive capital or electrolytes We report a lowtemperature, electrochemical cell that consumes lowcost and Electrochemical chloriron process for iron production from iron oxide 2023年2月22日 Process parameters and sensitivities of the batch chloriron cell (A) Relationship between ηFe and J for Fe plated in a batch cell divided by Nafion 115 ηFe >85 % was sustained for current Electrochemical ChlorIron Process for Iron Production from Iron Oxide
.jpg)
(PDF) An Overview of the ReductionSmelting Process of Iron Oxides
2022年8月23日 An Overview of the ReductionSmelting Process of Iron Oxides in ModernDay Ironmaking Technology August 2022; August 2022; 17(4) also can reduce metallic iron production costs by 65% compared 2022年5月30日 Abstract Inorganic pigments have been very important substances for human life for thousands of years They have contributed and continue to contribute to the beautification of our daily life and habitat and to the accentuation and differentiation of objects, and influence thoughts, moods, and feelings The industrial manufacture of inorganic pigments based on The world of inorganic pigments ChemTexts Springer2024年8月21日 Moreira et al developed an iron oxide/graphenic carbon hybrid photocatalyst for the decomposition of PFAS contaminants, under UV light Their method offers a cheap and efficient alternative that Hybrid graphenic and iron oxide photocatalysts for the NatureElectrochemical chloriron process for iron production from iron oxide and salt water Berkley B Noble, 1,2Anastasiia Konovalova, Louka J Moutarlier, 1,2 Valerie Brogden, 3 and Paul A Kempler1 ,2 4 * SUMMARY The iron and steel industry accounts for 8% of global greenhouse gas emissions Electrochemical reduction of iron ore to metal forElectrochemical chloriron process for iron production from iron oxide
.jpg)
Producing iron from salt water and iron oxide
2024年2月8日 A new lowtemperature electrochemical process that produces metallic iron from iron oxide and saltwater could help clean up steelmaking’s act (Joule 2024, DOI: 101016/jjoule202401001)2016年3月30日 In book: Encyclopedia of Iron, Steel, and Their Alloys (pppp 10821108) Chapter: i) Direct Reduced Iron: Production; Publisher: CRC Press, Taylor and Francis Group, New York(PDF) i) Direct Reduced Iron: ProductionL F Verdeja (2017) Iron Ore Sintering: Process, Mineral Processing and Extractive Metallurgy Review, 38:4, 215227, Iron oxide can simultaneously be reduced by carbon mon(PDF) Iron Ore Sintering: Process ResearchGate2019年7月19日 During the process, the iron oxides are reduced at the solid state The porosity leads to high reactivity through oxidation; for this reason hot briquetted iron has been developed to overcome this limit The process costs are in the range $3444 and $1831 per ton of steelDirect Reduced Iron: Most Efficient Technologies for Greenhouse
.jpg)
Research progress in the preparation of iron by electrochemical
2023年3月14日 For decades, the steel production industry has been one of the largest sources of CO2 emissions, accounting for 7% of global CO2 emissions, of which 70% is emitted in the ironmaking process Currently, the main lowcarbon iron production route is hydrogen metallurgy, which uses renewable energy to generate electricity, electrolyze water to produce hydrogen, 2020年6月10日 224 Direct Reduction of Iron Oxide by Solid Carbon The direct reduction process of iron oxide by solid carbon is highly endothermic in nature and occurs when the molten slag flows over incandescent coke in the bosh region at a temperature above 1000 °C Therefore, the corresponding reaction can be written as follows:Iron and SteelMaking Process SpringerLinkWe’ve developed an electrolysis process that eliminates the need for coal in steel production and then it’s electrified When the cell heats to 1600°C, the electrons split the bonds in the iron oxide in the ore, producing pure liquid metal No carbon dioxide or other harmful byproducts are generated, Cost Effective An efficient, Green Steel Solution Boston Metal2018年1月5日 Abstract Direct iron production at molten metal state from iron oxides by the sole application of electrical energy represents a possible route to decarbonize steel industry Although chemically simple, this reaction is difficult to implement due to the problem of the multiple valence states of iron and to an operating temperature above 1811 K Thermal, chemical, and Electrolysis of iron in a molten oxide electrolyte
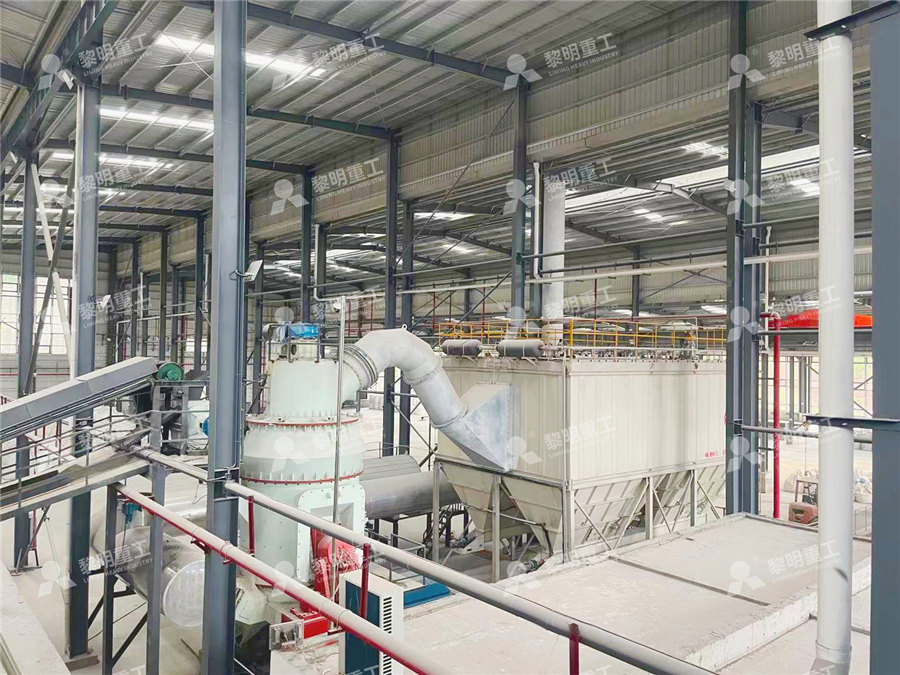
Green Synthesis: An Ecofriendly Route for the Synthesis of Iron Oxide
2021年6月14日 Biosynthesis Of iron Oxide Nanoparticles Using Plants Plants are generally considered as freely available, easy to handle, harmless and cheap material for synthesis of various types of nanoparticles (Noruzi, 2015)The biosynthesis process utilized distinct parts like roots, leaves, seeds, flowers, fruits, peels, petals, whole plant and seed husk as these are rich 2018年5月1日 Microalgae continue to gain in importance as a bioresource, while their harvesting remains a major challenge at the moment This study presents findings on microalgae separation using lowcost, easytoprocess bare iron Bare Iron Oxide Nanoparticles for Magnetic 2024年5月15日 In this system, in the negative electrode halfcell, the iron oxidation from elementary through Fe(II) to Fe(III) occurs, while in the positive electrode halfcell, the reduction of oxygen occurs yielding iron oxides and resulting in a voltage of about 128 V 95 The iron–air batteries are considered advanced secondary batteries due to the low solubility of the Back to the future with emerging iron technologiesFor instance, Fe 3 O 4 is a mixed iron oxide with Fe in different oxidation states as Fe 2 + and Fe 3 +Due to the flexible oxidation state of Fe, iron oxides can assume different phases and singlecrystalline structures with very different chemical and physical properties (cf Table 1 for an overview) This flexibility of their oxidation state makes iron oxides very interesting to be used Iron Oxide an overview ScienceDirect Topics
.jpg)
Iron Ore Pelletizing Process: An Overview IntechOpen
The iron ore production has significantly expanded in recent years, owing to increasing steel demands in developing countries However, the content of iron in ore deposits has deteriorated and lowgrade iron ore has been processed The fines resulting from the concentration process must be agglomerated for use in iron and steelmaking This chapter shows the status of the 2015年7月1日 Aggregation behaviour was observed within pH 3–45 for synthetic iron oxide NPs with a maximum particle size reading of 1398 ± 1173 dnm, while for natural iron oxide nano colloids, the Synthesis, Characterization and Applications of Iron Oxide 2008年10月2日 Surface functionalized magnetic iron oxide nanoparticles (NPs) are a kind of novel functional materials, which have been widely used in the biotechnology and catalysis This review focuses on the recent development and various strategies in preparation, structure, and magnetic properties of naked and surface functionalized iron oxide NPs and their Magnetic Iron Oxide Nanoparticles: Synthesis and Surface 2018年7月11日 Iron Ores and Iron Oxide Materials 50 Bentonite, an inorganic binder, has been the main binder used in the iron ore pelletizing process since the beginning of pellet production in the 1950sIron Ore Pelletizing Process: An Overview ResearchGate
.jpg)
Production of Iron Oxide Nanoparticles by CoPrecipitation
2020年2月1日 Production of Iron Oxide Nanoparticles by CoPrecipitation method with Optimization Studies of Processing Temperature, pH and Stirring Rate, Beh Hui Hui, Optimization processing condition that produce smallest crystallite size of 73657 nm was 50 °C, pH 1140 and 550 rpm by using Design of Expert software (DOE)2023年11月7日 Midtemperature black oxide process The blackening process can also be carried out at temperatures below the boiling point of water When it is carried out between 90 °C and 120 °C (194 °F – 248 °F), it is known as the midtemperature black oxide coating processBlack Oxide Coating – How It Works, Benefits Types2017年1月1日 Effective technology for a complex wasteless processing of the iron ores has been designed and includes three main components (plats): comminution plant, briquette plant, pigment plant(PDF) Effective Processing of the Iron Ores ResearchGate2022年5月1日 Iron oxide nanoparticles are becoming progressively significant for the improvement of innovative biomedical and nanotechnology requests The keywords iron oxide nanoparticles, Fe 3 O 4 nanoparticles and magnetite nanoparticles have been utilized as a research object in the gross database of articles from the Web of Science The results of these Iron oxide nanoparticles: Preparation methods, functions,
.jpg)
Electrochemical ChlorIron Process for Iron Production from Iron Oxide
Electrochemical ChlorIron Process for Iron Production from Iron Oxide and Seawater Berkley B Noble,12 Louka J Moutarlier,12 Paul A Kempler12* 1Department of Chemistry and Biochemistry, The process can lead to levelized costs 2021年10月26日 Iron sponge process is the oldest and still the most widely used batch process for sweetening of natural gas and natural gas liquids Overall, iron sponge process has the following characteristics which make it still Gas Sweetening using Iron Sponge ProcessIron oxide, in pellet or lump form, is introduced through a proportioning hopper at the top of the shaft furnace As the iron ore descends through the furnace by gravity flow, it is heated, and the oxygen is removed from the iron ore (reduction) by counterflowing gases that have a MIDREX® Process Midrex Technologies, IncNatural Gas Sweetening Alireza Bahadori PhD, in Natural Gas Processing, 2014 10111 Iron oxide (sponge) process The iron sponge process selectively removes H 2 S from gas or liquid streams The process is limited to treating streams containing low concentrations of H 2 S at pressures ranging from 170 to 8300 kPa (ga) The process employs hydrated iron oxide, Iron Sponge Process an overview ScienceDirect Topics
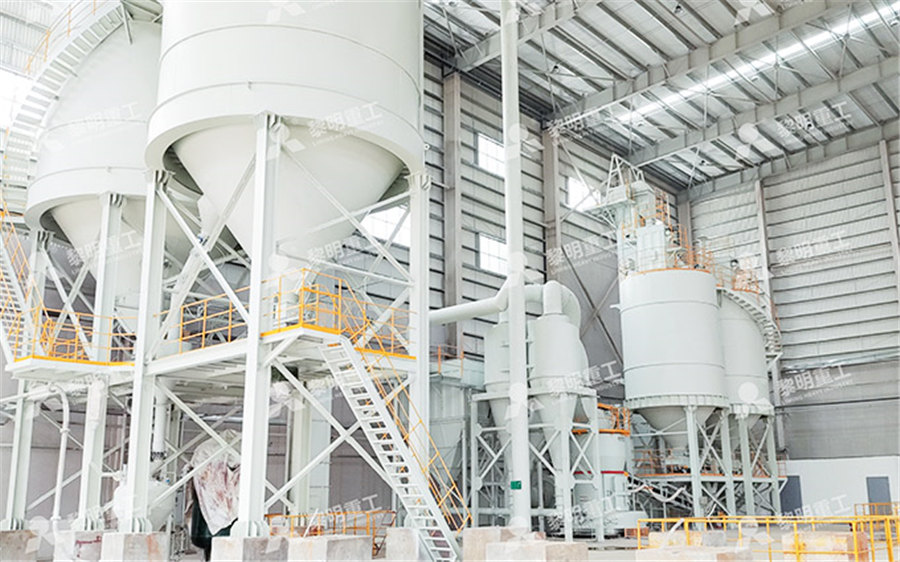
Electrochemical chloriron process for iron production from iron oxide
2024年3月20日 The iron and steel industry accounts for ∼8% of global greenhouse gas emissions Electrochemical reduction of iron ore to metal for electric arc furnaces can enable sustainable steel production, but existing electrochemical processes require expensive capital or electrolytes We report a lowtemperature, electrochemical cell that consumes lowcost and 2023年2月22日 Process parameters and sensitivities of the batch chloriron cell (A) Relationship between ηFe and J for Fe plated in a batch cell divided by Nafion 115 ηFe >85 % was sustained for current Electrochemical ChlorIron Process for Iron Production from Iron Oxide 2022年8月23日 An Overview of the ReductionSmelting Process of Iron Oxides in ModernDay Ironmaking Technology August 2022; August 2022; 17(4) also can reduce metallic iron production costs by 65% compared (PDF) An Overview of the ReductionSmelting Process of Iron Oxides 2022年5月30日 Abstract Inorganic pigments have been very important substances for human life for thousands of years They have contributed and continue to contribute to the beautification of our daily life and habitat and to the accentuation and differentiation of objects, and influence thoughts, moods, and feelings The industrial manufacture of inorganic pigments based on The world of inorganic pigments ChemTexts Springer
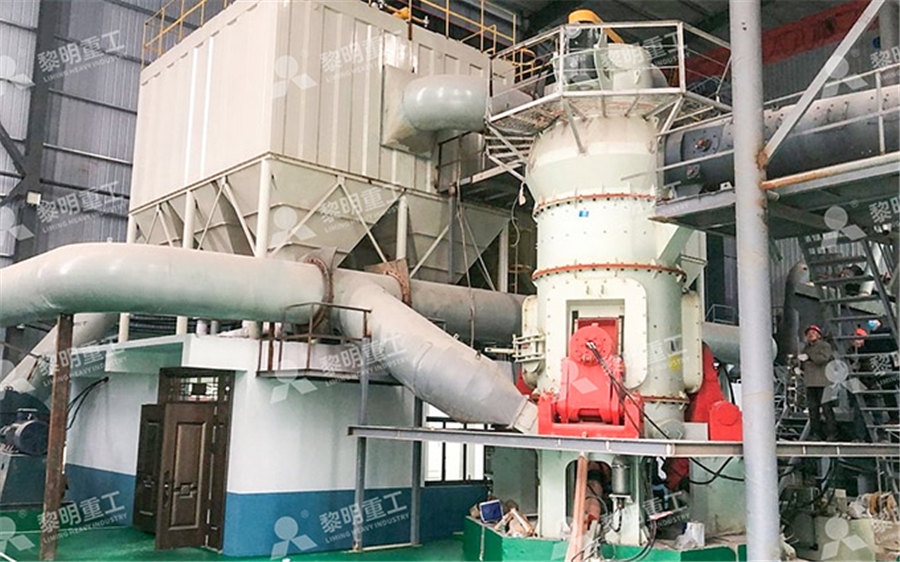
Hybrid graphenic and iron oxide photocatalysts for the Nature
2024年8月21日 Moreira et al developed an iron oxide/graphenic carbon hybrid photocatalyst for the decomposition of PFAS contaminants, under UV light Their method offers a cheap and efficient alternative that