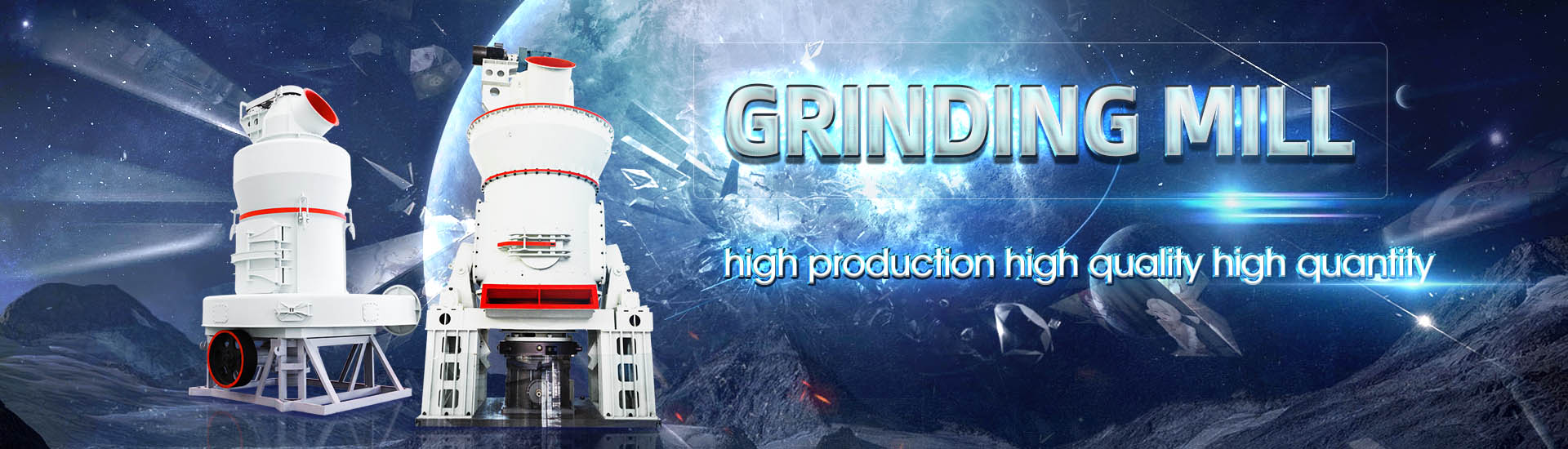
Output 1200th coal What are the raw coal mills
.jpg)
Modeling and Control of Coal Mill NTNU
2013年11月20日 Coal mill is an important component of the thermal power plant It is used to grind and dry the moisturized raw coal and transport the pulverized coal – air mixture to the boiler Poor dynamic performance of coal mill will lead to decrease in the overall efficiency of the In pulverised coalfired power plants, a pulveriser coal mill grinds the raw coal into a combustible dust Here, the coal particles are dried by flue gas or hot air and milled to fine size, so that Coal Mill an overview ScienceDirect Topics2012年5月1日 The paper presents development and validation of a coal mill model to be used for improved mill control, which may lead to a better load following capability of power plants Derivation and validation of a coal mill model for controlCharacteristics 1 High efficiency and large output GRMC series coal vertical grinding mill has higher working efficiency Compared with the same type of old vertical mill, the output COAL VERTICAL MILL Xinxiang Great Wall Machinery Co,
.jpg)
(PDF) Modeling and Parameter Identification of
2009年9月20日 The ball tube mill requires less mass flow rate of primary air and raw coal per MW of power produced than the bowl mill It contains larger mass of raw and pulverized coal but less2024年1月18日 The coal mills grind and dry the moisturized raw coal and transport the pulverized coal to the boiler burner Their poor dynamic performance causes a slow load take Modeling and Parameter Identification of Coal Mill2015年11月1日 Coal mills are one of the critical power plant components that influence the efficiency and reliability of a coal fired power plant The coal mill grinds the raw coal into fine A unified thermomechanical model for coal mill operation2020年8月12日 Coal mills are used to pulverize the raw coal and conveyor the fine coal particles to primary zone of boiler for an efficient combustion Performance of the pulverizing systemAn investigation of performance characteristics
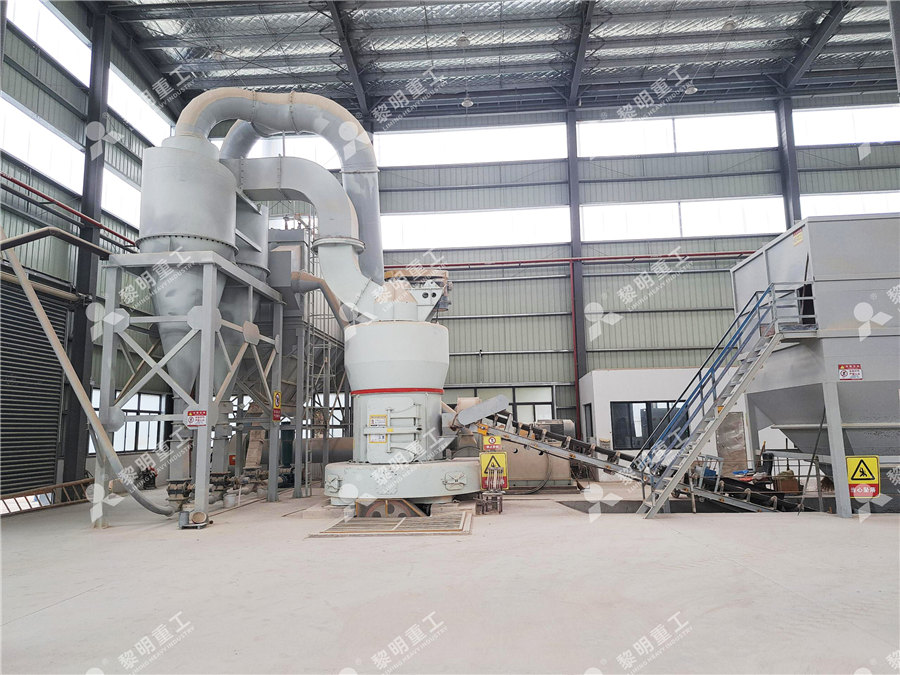
An investigation of performance characteristics and
2020年8月12日 In a power plant, the coal mill is the critical equipment, whose effectiveness impacts the overall power plant efficiency Uniform coal feeding mass flow rate and required 2024年10月31日 The results show that by implementing the revised control strategy, the absolute pulverized coal output deviation was reduced by up to 216 kg, 126kg, and 116kg, Optimization of the pulverized system of the coalfired 2023年10月23日 6 Du et al Applied Mathematics and Nonlinear Sciences (aop)1–8 Fig 7 Pressure ratio in coal mill 1 It can be seen from Figure 4 that the output of the ball grinder first increases and then Applied Mathematics and Nonlinear Sciences2018年9月24日 As in fig2 the raw coal (normally 25 mm) is fed into a rotating bowl through a centre feed pipe Fig2 HP Pulveriser Coal Air Flow Firm output t/h 8964 Minimum output t/h 249 coal mill inlet drying medium temperature °C 274 Coal mill outlet temperature °C 65 70 Pulveriser Mill Performance Analysis Optimisation in
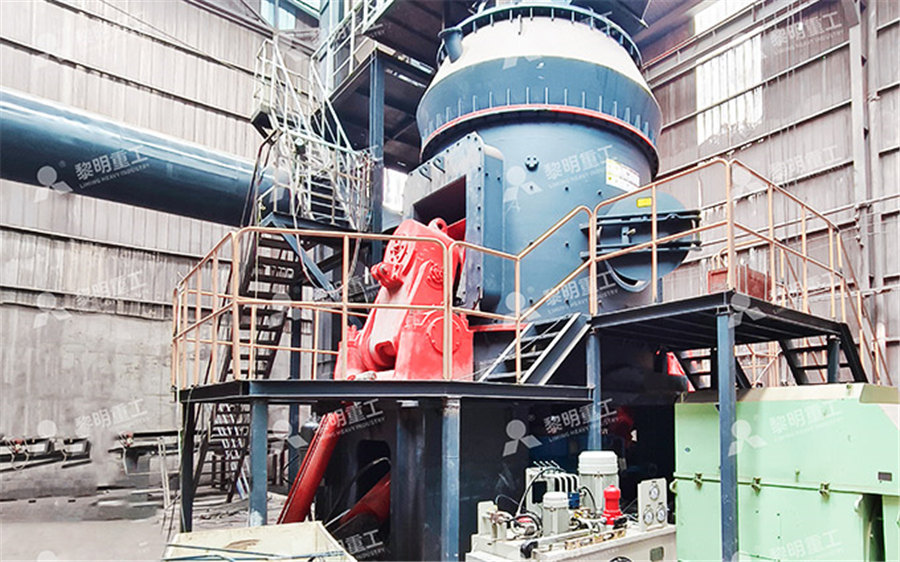
What is a Coal Grinding Mill ballmillssupplier
Coal grinding mills are essential components of power plants, responsible for converting raw coal into fine coal powder that is essential for efficient combustion in power plant boilers Coal grinding mills can also be used to grind biomass and other alternative fuels, providing a more sustainable and renewable energy source for power generation2023年10月20日 As shown in Fig 1, the raw coal falls into the coal feeder, enters the coal mill through the inlet pipe, and finally falls onto a constant speed rotating grinding tableA novel multimode Bayesian method for the process2024年11月26日 Coal grinding mills LOESCHE coal grinding mills are distinguished by characteristics that improve efficiency, safety and environmental protection, from the standard version to topoftherange installations Special versions are available with characteristics that meet special safety regulation or output control requirementsCoal Mills for Cement Plants Loesche2021年2月15日 The ball tube mill requires less mass flow rate of primary air and raw coal per MW of power produced than the bowl mill It contains larger mass of raw and pulverized coal but less grinding heat (PDF) System dynamics model of output of ball mill
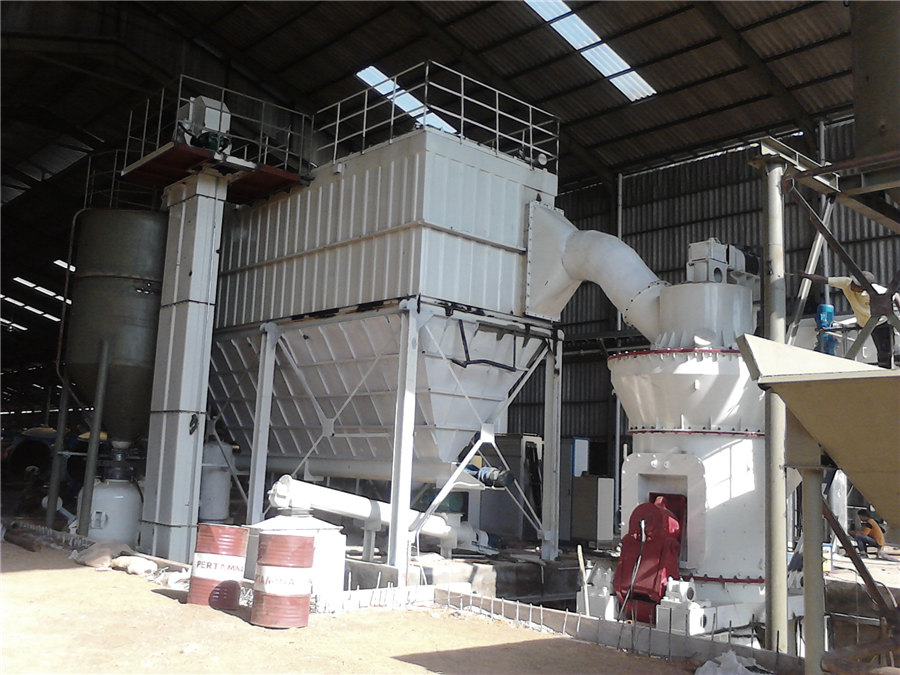
Coal Ball Mill Grinding for Different Kinds of Pulverized Coal
Raw coal enters the coal ball mill through the feeding device At this time, hot air with a temperature up to 300℃ enters the coal mill barrel from the intake pipe The raw coal falls on the lifting plate of the drying chamber and is continuously raised In the process of heat exchange between raw coal and hot air, water is continuously Section of coal bowl mill Table 1 Guaranteed coal conditions for mill performance evaluation Coal Moisture % 20 Coal HGI 55 Mill Outlet Temperarure °C 80 Mill Air Flow T/hr 102 Coal Fineness (% passing trough 200 mesh) 70% passing through 200 mesh and 90% passing through 50 mesh Differental Pressure 300 mmwc Coal Output from Mill 609 t/hrA Study on 500 MW Coal Fired Boiler Unit’s Bowl Mill 2020年8月1日 These coals include semisoft coking coals, pulverised coal injection (PCI) coal, and steam coal, which form a smaller proportion of the metallurgical coal market(PDF) COKING COAL THE STRATEGIC RAW MATERIAL2009年9月20日 The ball tube mill requires less mass flow rate of primary air and raw coal per MW of power produced than the bowl mill It contains larger mass of raw and pulverized coal but less grinding heat (PDF) Modeling and Parameter Identification of Coal Mill
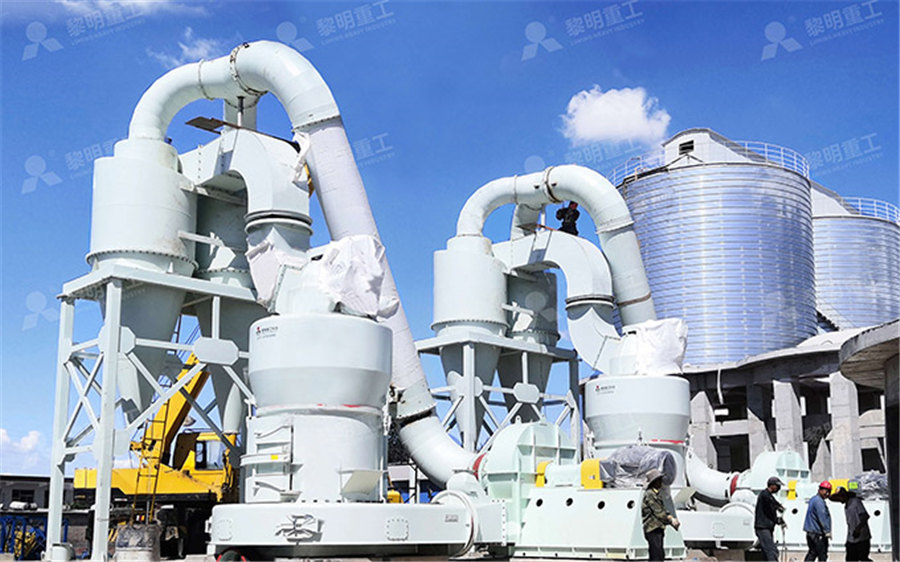
Early Warning of Critical Blockage in Coal Mills
2020年1月1日 Coal mills have a significant influence on the reliability, efficiency, and safe operation of a coalfired power plant Coal blockage is one of the main reasons for coal mill malfunction2018年12月12日 instant there will be certain amounts of raw coal (M c) and pulverised coal (M pf) in the mill The raw coal is fed into the mill by raw coal feeders for pulverizing at a mass flow rate of W c By grinding the raw coal M c in the mill, the pulverized coal M pf is produced and carried out by the warm air flow at the mill outletPulverised Coal Flow measurement in Thermal Power 2016年9月1日 In contrast, increasing the separator speed from 60 to 80 rpm at a constant grinding pressure results in a reduced raw material production rate from 240,000 kg/h to 230,000 kg/h and which Operational parameters affecting the vertical roller mill 2 天之前 2 Raw coal properties – Hardgrove index and moisture level 3 Pulverized coal fineness The raw coal is fed into a rotating bowl via a center feed pipe The rate of coal feed is normally determined automatically by a combustion control system, taking into account the MW demand on the unit, coal quality, and the number of coal pulverizers in Bowl Mill Coal Pulverizer COAL HANDLING PLANTS
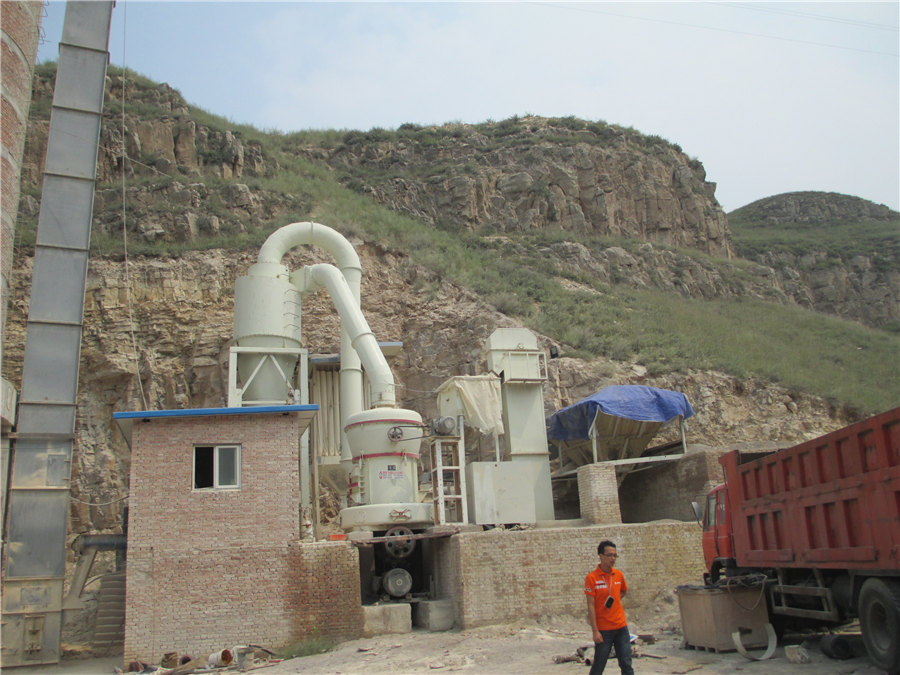
Pulverizer Capacity is not simply “tons throughput per
2016年5月3日 (HGI), at a given raw coal sizing entering the mill and at a given coal moisture content Throughput alone is NOT a definition of pulverizer capacity! Please read on for more explanation Predicting Pulverizer Performance Often power plant managers and engineers refer to pulverizer capacity as “throughput” Throughput is a2012年11月17日 15 10Bowl Mill Bowl mills are employed to pulverize the precrushed raw coal to the required fineness before it is admitted into the boiler furnace for combustion The mill output can be easily varied, as per the turndown ratio from its minimum to maximum load Crushed raw coal at a controlled rate is fed into the revolving bowl of the Bowl Mill Centrifugal force feeds Coal mill pulverizer in thermal power plants PPT SlideShareMPS 3070 BK coal mill, Jaypee Cement Balaji, India MPS 180 GC vertical roller mill for the grinding, drying and calcining of gypsum, Knauf Knin, Croatia of gypsum, Trevo, Brasil MPS 3350 B mill for limestone grinding, China Chongqing Foreign Trade Huaneng, China MPS 5000 B mill for raw material grinding, Turkey Tracim, Turkey MPS 5300 B Coal mill, gypsum mill, clay mill, etc Pfeiffer MPS mills2024年10月31日 Coal mills, essential components in power generation and various industrial processes, pose significant safety risks if not properly managed These mills, used to grind coal into a fine powder for combustion, present potential hazards such as fire, explosion, and mechanical failures This article outlines best practices and precautions to ensure thEnsuring Safety in Coal Mills Coal Mill Safety, Explosion and
.jpg)
Coal Mill in Cement Plant Vertical Roller Mill AirSwept Ball Mill
A coal mill is also called a coal pulverizer or coal grinder It is a mechanical device used to grind raw coal into pulverized coal powders The most used coal mills in cement plants are airswept ball mills and vertical roller mills At present, most cement plants use coal as the main fuel in the clinker production process2020年1月1日 The calorific value of coal is the basic technical basis for calculating parameters such as boiler heat balance, thermal efficiency, and boiler output The calorific value of coal has different Measurement and calculation of calorific value of raw coal 2020年9月1日 For modelbased fault diagnosis method, it first needs to establish a mathematical model of the coal mill Odgaard et al [2] used a simplified energy balance equation to monitor and diagnose abnormal energy flow in the coal mill Andersen et al [3] designed a Kalman filter to estimate the moisture entering and leaving the coal mill, thereby identifying whether the Research on fault diagnosis of coal mill system based on the The purpose of the coal drying system is drying and grinding the raw coal for stable transportation of pulverized coal to gasifier and stable/highefficiency gasification at the gasifier [111] designed two independent single input–single output (SISO) systems for the mill, after reducing coupling between the outlet temperature and the Coal Pulverizers an overview ScienceDirect Topics
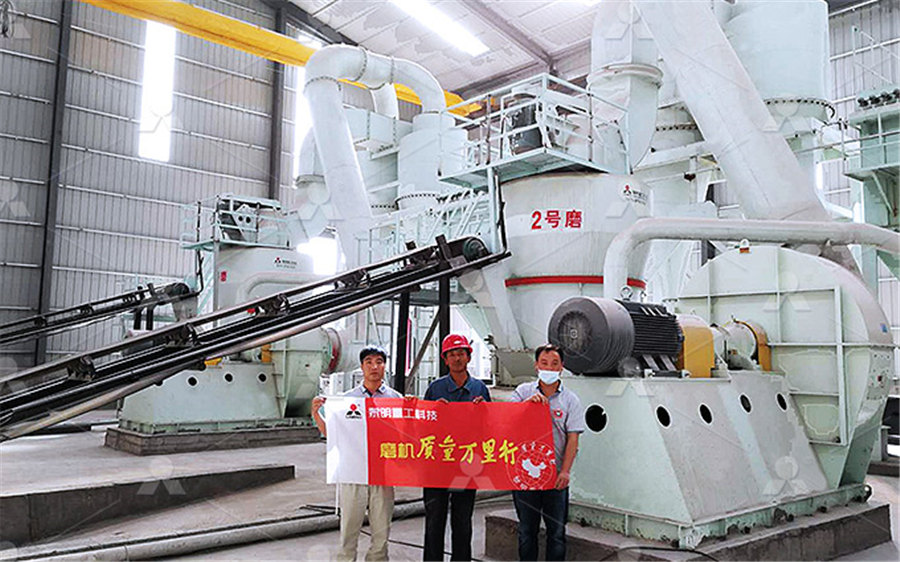
What is the role of a mill in a coalfired power plant? LinkedIn
2023年11月30日 Here are the main functions of a mill in a coalfired power plant: Coal Crushing: The mill crushes the raw coal into a fine powder, increasing its surface area This facilitates efficient Output: 5 t/h 70 t/h Coal vertical mills also called coal mills, which are specialized in superfine grinding of raw coal and bituminous coal Compare this product Remove from comparison tool See the other products Xinxiang Great Wall Machinery Co, Ltd Raymond mill HGM series Coal grinding mill, Coal grinding grinding mill All industrial There are two main types of coal mills: pulverizer and raw coal mills Pulverizer Coal Mill A pulverizer coal mill works by grinding coal into a fine powder and then drying it in a hot air fan The coal powder is then blown into a combustion chamber where it is burned to generate heat The hot gases and heat energy produced from burning the How does a Coal Mill Work? ball mills supplier2019年7月30日 instant there will be certain amounts of raw coal (M c) and pulverised coal (M pf) in the mill The raw coal is fed into the mill by raw coal feeders for pulverizing at a mass flow rate of W c By grinding the raw coal M c in the mill, the pulverized coal M pf is produced and carried out by the warm air flow at the mill outletPulverised Coal Flow measurement in Thermal Power Plant
.jpg)
The structure of MPS mediumspeed coal mill system
The mediumspeed coal mill system is mainly composed of raw coal bunker, coal feeder, coal mill, primary fan, sealing fan, hot and cold air regulating valves View in fulltext Similar 2024年10月31日 Today, CMS shares experience with coal mill safety in cement production facilities and answers questions like the following: Evaluation of a coal grinding system’s fire and explosion protection, including the raw coal storage and the fine coal silo storage normally can be done in one day, mostly without having to stop coal grindingCoal Mill Safety In Cement Production Industries2012年5月1日 Coal fired power plants are heavily used due to large and long lasting coal resources compared with oil or natural gas An important bottleneck in the operation of this particular kind of plants, however, is the coal pulverization process, which gives rise to slow takeup rates and frequent plant shutdowns (Rees Fan, 2003)In typical coal fired power plants, Derivation and validation of a coal mill model for control2023年10月23日 6 Du et al Applied Mathematics and Nonlinear Sciences (aop)1–8 Fig 7 Pressure ratio in coal mill 1 It can be seen from Figure 4 that the output of the ball grinder first increases and then Applied Mathematics and Nonlinear Sciences
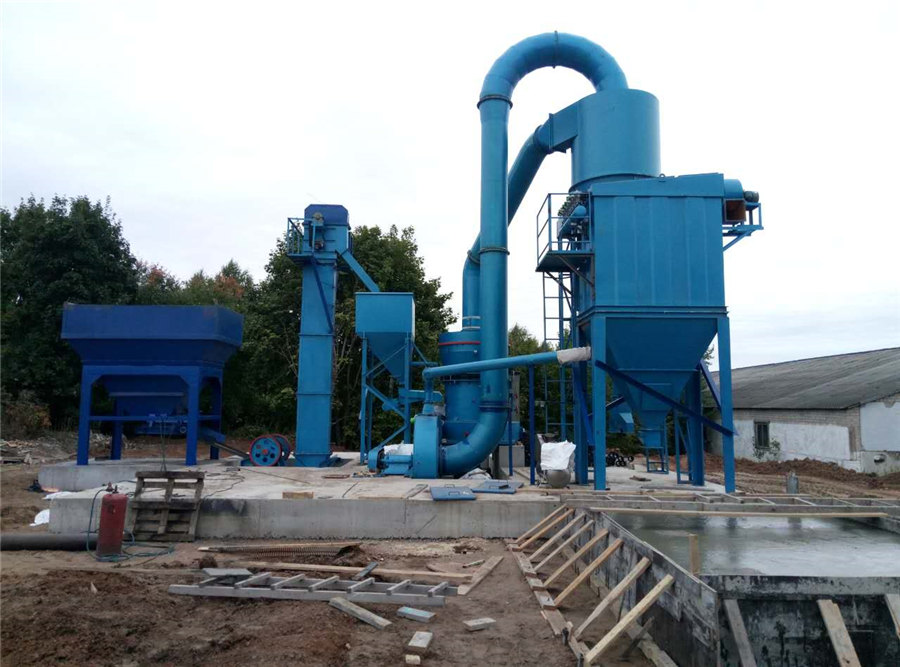
Pulveriser Mill Performance Analysis Optimisation in
2018年9月24日 As in fig2 the raw coal (normally 25 mm) is fed into a rotating bowl through a centre feed pipe Fig2 HP Pulveriser Coal Air Flow Firm output t/h 8964 Minimum output t/h 249 coal mill inlet drying medium temperature °C 274 Coal mill outlet temperature °C 65 70 Coal grinding mills are essential components of power plants, responsible for converting raw coal into fine coal powder that is essential for efficient combustion in power plant boilers Coal grinding mills can also be used to grind biomass and other alternative fuels, providing a more sustainable and renewable energy source for power generationWhat is a Coal Grinding Mill ballmillssupplier2023年10月20日 As shown in Fig 1, the raw coal falls into the coal feeder, enters the coal mill through the inlet pipe, and finally falls onto a constant speed rotating grinding tableA novel multimode Bayesian method for the process2024年11月26日 Coal grinding mills LOESCHE coal grinding mills are distinguished by characteristics that improve efficiency, safety and environmental protection, from the standard version to topoftherange installations Special versions are available with characteristics that meet special safety regulation or output control requirementsCoal Mills for Cement Plants Loesche
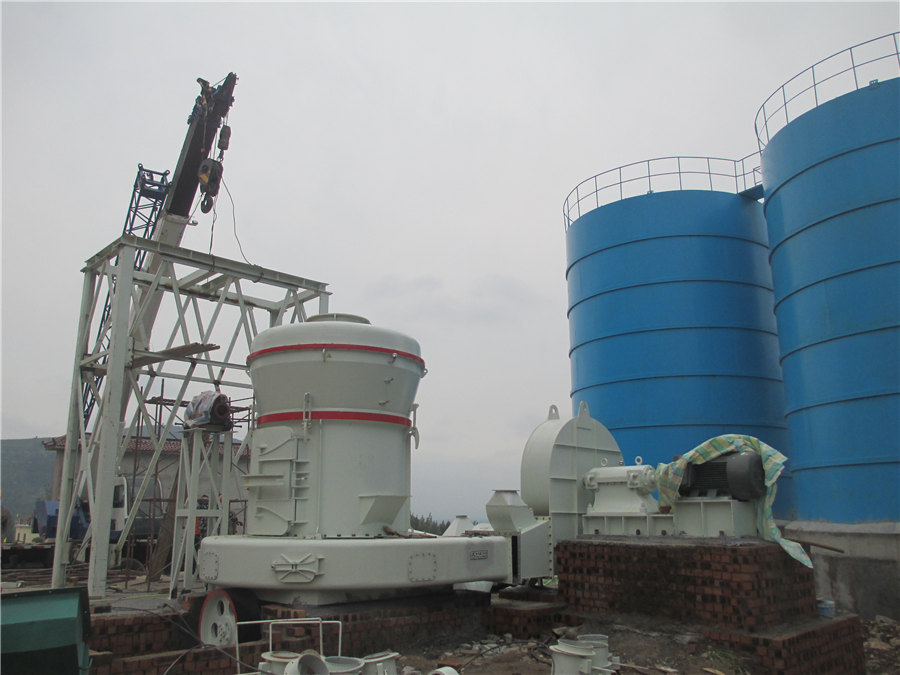
(PDF) System dynamics model of output of ball mill
2021年2月15日 The ball tube mill requires less mass flow rate of primary air and raw coal per MW of power produced than the bowl mill It contains larger mass of raw and pulverized coal but less grinding heat Raw coal enters the coal ball mill through the feeding device At this time, hot air with a temperature up to 300℃ enters the coal mill barrel from the intake pipe The raw coal falls on the lifting plate of the drying chamber and is continuously raised In the process of heat exchange between raw coal and hot air, water is continuously Coal Ball Mill Grinding for Different Kinds of Pulverized CoalSection of coal bowl mill Table 1 Guaranteed coal conditions for mill performance evaluation Coal Moisture % 20 Coal HGI 55 Mill Outlet Temperarure °C 80 Mill Air Flow T/hr 102 Coal Fineness (% passing trough 200 mesh) 70% passing through 200 mesh and 90% passing through 50 mesh Differental Pressure 300 mmwc Coal Output from Mill 609 t/hrA Study on 500 MW Coal Fired Boiler Unit’s Bowl Mill 2020年8月1日 These coals include semisoft coking coals, pulverised coal injection (PCI) coal, and steam coal, which form a smaller proportion of the metallurgical coal market(PDF) COKING COAL THE STRATEGIC RAW MATERIAL
.jpg)
(PDF) Modeling and Parameter Identification of Coal Mill
2009年9月20日 The ball tube mill requires less mass flow rate of primary air and raw coal per MW of power produced than the bowl mill It contains larger mass of raw and pulverized coal but less grinding heat