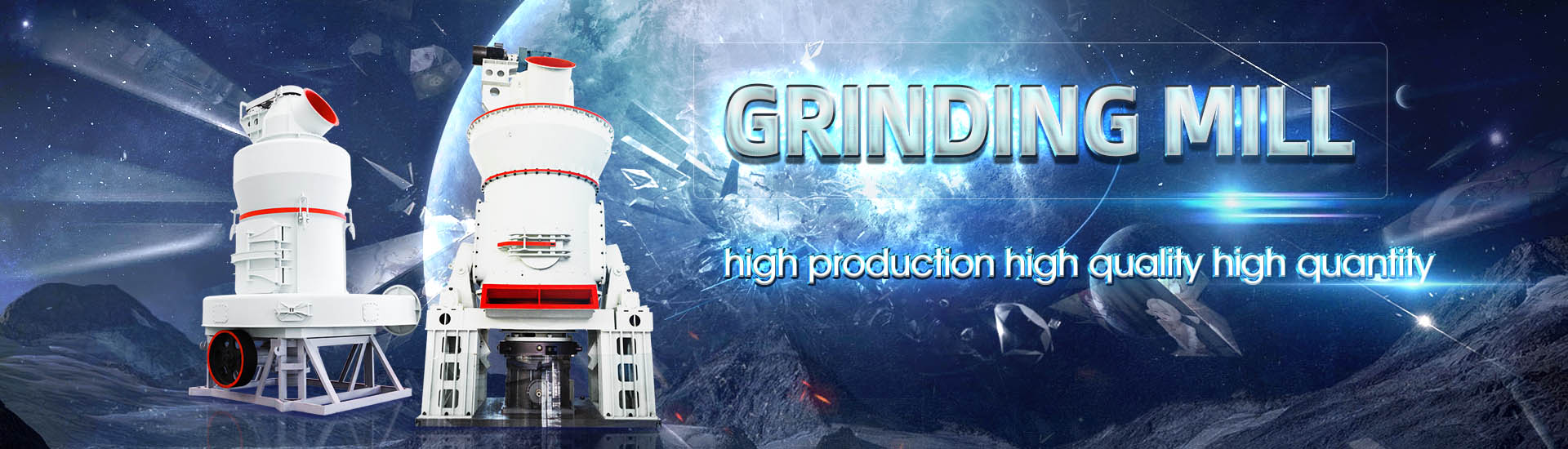
Cement grinding station powder making process
.jpg)
Cement Grinding Unit Process High Quality Cement
Explore Amrit Cement's stateoftheart cement grinding unit Learn about our cement grinding process and plant stages for high quality cementGrinding plays a pivotal role in the cement manufacturing process, transforming raw materials Grinding in Cement Manufacturing: Key Process, Types of Mills, The production process adopts efficient extrusion combined grinding system, DCS distributing automatic control system, large bag dust collector and other advanced equipment The host equipment is advanced, the quantity is stable Cement Grinding Plant CHAENGGrinding operation is monitored for following parameters to ensure objectivity and economy of Cement Grinding Cement Plant Optimization
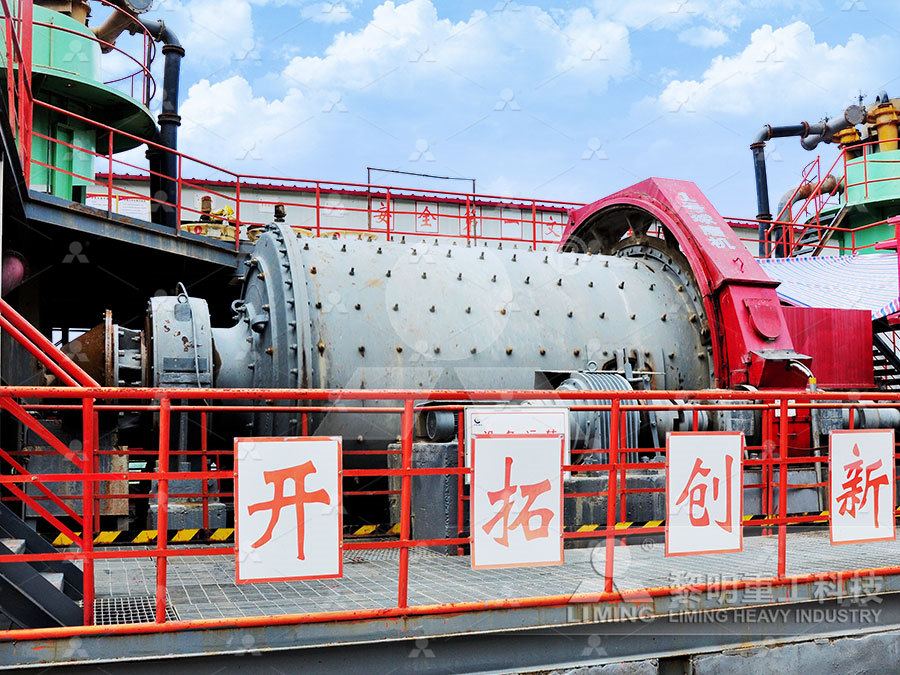
Cement grinding and packing process Al badia cement
Cement grinding and packing process The clinker is ground with an amount of gypsum to a 2017年5月19日 PDF Grinding is an essential operation in cement production given that it permits to obtain fine powder which reacts quickly with water, sets in few Find, read and cite all the researchOverview of cement grinding: fundamentals, additives, Optimization addresses the grinding process, maintenance and product quality The objective OPTIMIZATION OF CEMENT GRINDING OPERATION IN BALL MILLSEverything you need to know about clinker/cement Grinding if You read and understand this article , you will be ready to be a cement grinding area manager FEED AND FEED SYSTEM Feed Temperature Plants with satellite coolers Everything you need to know about clinker/cement
.jpg)
6 Cement Equipment For Dryprocess Cement
2023年12月26日 As we all know, the dryprocess cement production line is commonly used in the cement industry The new type of dryprocess cement production process includes four main sections: Prehomogenization of raw 2014年6月10日 Cement manufacturing process Download as a PDF or view online for free It then describes the industrial process for manufacturing cement, involving grinding raw materials like limestone and clay at high Cement manufacturing process PPT Free DownloadModular Mobile Grinding Plant To meet the small and mediumsized clinker grinding demand of cement producers, AGICO CEMENT develops a modular mobile grinding plant (MMGP in short) to achieve goals of quick return with minimal capital investment The modular mobile grinding plant developed by AGICO CEMENT is a highly flexible system capable of producing any Modular Mobile Grinding Plant, Portable Grinding Plant Cement Cement grinding process The whole workflow of the cement grinding plant is as follows: the cement clinker, gypsum, and mixture in the cement silo are mixed by the belt conveyor in a certain proportion and transported to the cement roller press, cement mill or group of them for grindingCement Grinding Plant Overview Cement Grinding Unit AGICO Cement
.jpg)
cement grinding station
CHAENG can provide the complete solutions of 15100t/h cement grinding station for you Please send to for the quotation HOME; Powder separation system sets of processing equipment Rich experience in exporting more than 3000 large grinding equipment Providing professional cement grinding process for clientsProcess Description Cement clinker grinding unit, or called cement grinding plant, cement grinding station, is an individual grinding plant in the finished cement production Cement grinding plants are primarily used to produce finished cement products by grinding cement clinkers and moderate mixed materialsCement Grinding Plant CHAENGNowadays, the dry process is the most popular cement making process which is widely adopted by cement plants all over the world for its great advantages in energy saving and environmental protection Cement Making Process The cement making dry process includes six phases: Raw material extraction/ Quarry; Proportioning, Blending, and GrindingHow Is Cement Produced in Cement Plants Cement Making ProcessThe final step in cement manufacturing is the grinding of clinker into cement powder, followed by the finalization process that ensures the product meets all required specifications and standards This stage is crucial as it defines the physical and chemical properties of the cement, making it suitable for various construction purposesCement Making Guide: Steps, Impact Green Alternatives
CFB石灰石脱硫剂制备——磨机公众号12.8 推送案例(8)51.jpg)
Cement Making Process: Equipment Manufacturing
Cement manufacturing equipment needs to withstand the heat and the abrasive material from which cement is made Making cement involves combining raw materials including limestone, clay, and shale, which are milled into a very fine powder after being mined These materials are then mixed with other ingredients according to their enduse This mixture is then fired in a kiln With this crude method, Joseph Aspdin of Leeds laid the foundation for an industry that annually processes literally mountains of limestone, clay, cement rock, and other materials into a powder so fine, it will pass through a sieve How Cement is Made Portland Cement Association2017年8月15日 To produce powdered cement, the nodules of clinker are ground to the consistency of powder Grinding of clinker, together with additions of approximately 5 percent gypsum to control the setting properties of the cement can be done in ball mills, ball mills in combination with roller presses, roller mills, or roller pressesThe Cement Manufacturing ProcessA 10 MW cement mill, output 270 tonnes per hour A cement mill (or finish mill in North American usage [1]) is the equipment used to grind the hard, nodular clinker from the cement kiln into the fine grey powder that is cementMost cement is currently ground in ball mills and also vertical roller mills which are more effective than ball millsCement mill Wikipedia
.jpg)
CuttingEdge Grinding Solutions Indian Cement Review
2023年8月21日 ICR looks at the inner workings of grinding mills in the cement industry to understand the technological advancements that are reshaping the landscape against the foreground of sustainability Innovations to enhance the grinding processes are aimed at minimising their environmental footprint while increasing efficiency and performance In The cement grinding process is a dynamic system with multiple variables and constraints, and the decisionmaking process is challenging due to the existence of multiple equivalent optimal solutions and the difficulty in finding the global optimal DOUDCGAN: Optimization of cement grinding operational 2023年10月19日 Therefore, efficient grinding techniques and technologies are employed to minimize energy use and reduce production costs, contributing to the sustainability of the cement industry Types of Clinker Grinding Techniques used in cement manufacturing process Clinker grinders are an important part of the cement manufacturing processClinker Grinding Techniques in Cement Manufacturing JM Grinding aids also serve to reduce coating problems in cement storage and enhances cement strengths GRINDING MILLS Mills will be selected according to type most suitable for required capacity and duty and for overall power consumption Cement grinding operation may be performed in one of the following mill setups Ball and tube millsCement Grinding Cement Plant Optimization
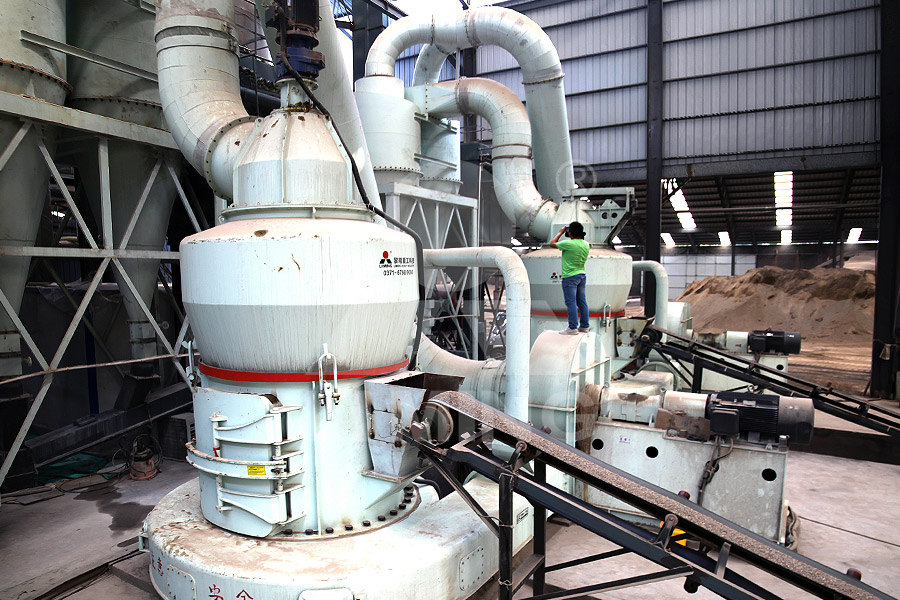
Cement Manufacturing Process: Know Extraction, Processing
2024年9月10日 Steps of Cement Manufacturing The steps involved in cement manufacturing are as follows: Quarrying: Raw materials such as limestone and clay are extracted from quarries or mines; Crushing and Grinding: The extracted raw materials are crushed and ground into a fine powder; Blending: The crushed and ground raw materials are blended in specific proportions 2024年1月17日 According to statistics, the dry cement production line grinding operation consumes Power accounts for more than 60% of the power of the whole plant, of which raw material grinding accounts for more than 30%, coal grinding accounts for about 3%, and cement grinding station account for about 40%What Do You Know About Wet Process Of Cement ProductionThis article is focusing on the manufacturing process of cement, are also responsible for up to 60% of the total of emissions of the cement production process [PCA] In addition, grinding and milling operations, used upstream (limestone crushing and grounding) and downstream (milling of clinker into cement powder) Cement Production Demystified: StepbyStep Process and The new cement grinding process includes mixed material crushing, cement batching station, pregrinding, high fine grinding, fine powder separation, dust treatment, automatic control and other technologies, so that cement high yield, Cement Grinding Station Solution Ball Mill and
.jpg)
Cement Grinding Station FTM Machinery
Advantages : It can make 1,000 tons to 6,000 tons of cement per day It can finish the jobs of grinding and packaging cement Case Description: Cement grinding station is one production unit of cement finished products, which doesn't cements, such as super sulfatecement, very lowheat cement and calcium aluminate cement Cement manufacture The cementmaking process can be divided into two basic steps: • Clinker (the main constituent of cement) is first made in a kiln with gas up to 2000°C, whichTHE STORY OF CEMENT MANUFACTURE CEMBUREAU2012年8月30日 Cement Manufacturing Process Phase IV: Kiln Phase Kiln is a huge rotating furnace also called as the heart of cement making process Here, raw material is heated up to 1450 ⁰C This temperature begins a chemical reaction so called decarbonation In this reaction material (like limestone) releases the carbon dioxideCement Manufacturing Process Engineering Intro2022年8月10日 The process of cement manufacturing involves grinding clinker granules along with blending materials or additives and gypsum to produce a fine powder called cement Depending on the quality of clinker and type of cement, blending material/gypsum are added in controlled proportion to produce a quality product to meet the prescribed quality as per given Efficient grinding unit selection impacts profitability Indian Cement
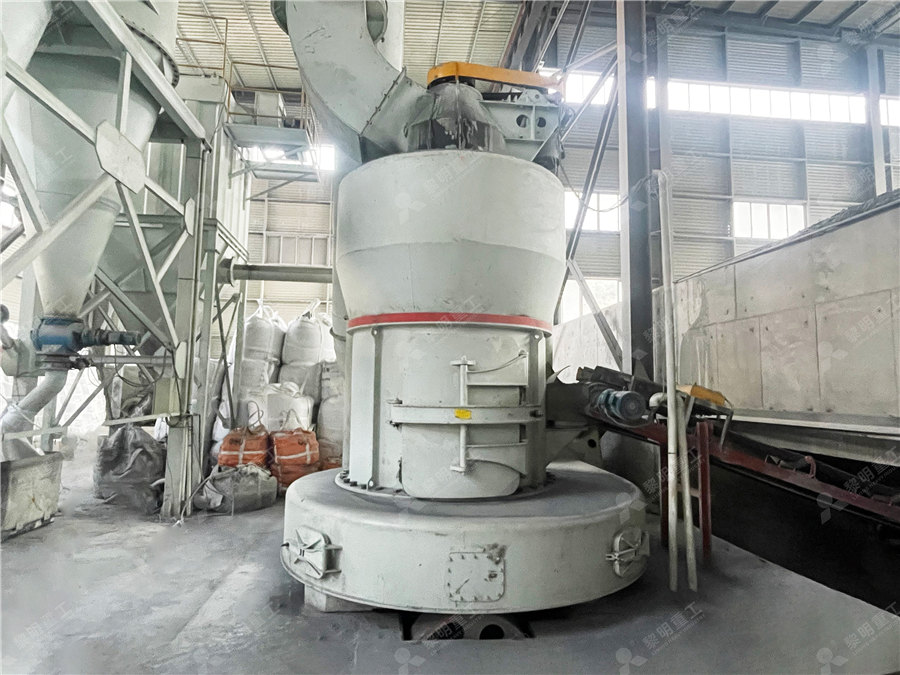
Gypsum Powder Manufacturing Gypsum Powder Making Machine Cement
Gypsum powdermaking process According to the process requirements, the construction gypsum production line is usually divided into five parts, including crushing system, storage conveying system, grinding system, calcining system, and electric control system STEP1 crushing system The size and specifications of gypsum ores are different after mining, and 2023年11月1日 We give some tips for cement plant design, including cement site selection, mineral selection, raw material prehomogenizing, grinding station design, calcination system design, waste gas generating system design, electrical automation system design, etc8 Tips For Cement Plant Design Cement Manufacturing Process2023年12月7日 After passing, the finished mixture is the final cement powder ready for packaging, storing and transporting Step 5: Packaging, Storing and Transporting Silos store large quantities of the final cement powder until it’s ready for processing At processing plants, machines package the cement powder in large paper bagsHow Is Cement Made? StepbyStep Guide BigRentz2024年5月31日 Cement grinding plant or cement grinding unit, grinding station is a necessary section of the cement manufacturing plantWhat does cement grinding plant do? In brief, cement grinding plant helps to grind clinker into finished cement For investors who are new to the cement industry, now is the perfect time to invest in cement grinding plantHow much dose it cost to start a cement grinding plant?
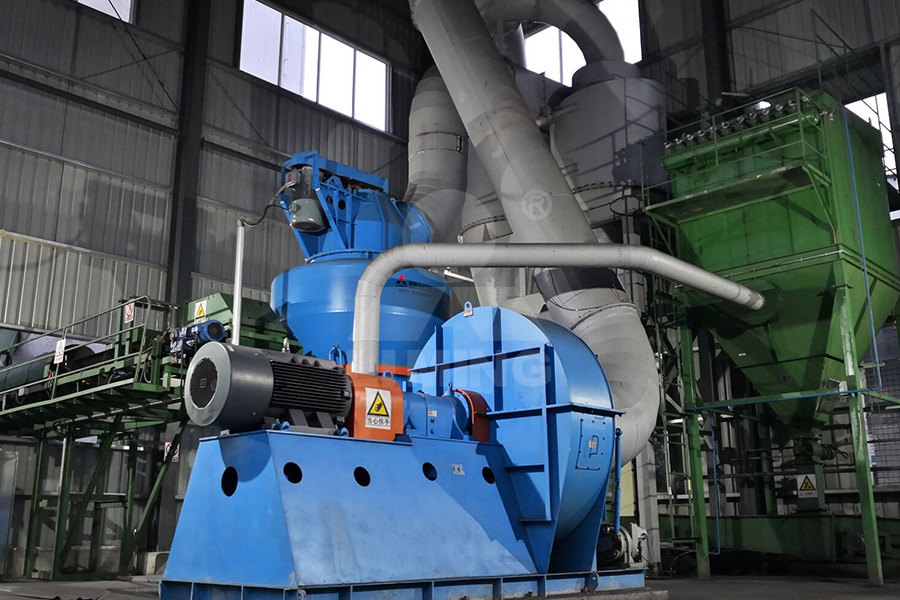
Cement Grinding StationHongji Mining Machinery
Closedcircuit grinding process: After the materials are milled, the products are selected through the powder concentrator system, and the coarse powder is returned to the mill for regrinding Reducing the phenomenon of overgrinding can increase output, reduce power consumption, and make product fineness easy to controlThe dry process cement production line is widely used in cement industry it is generally divided into the following processes: prehomogenization of raw materials, homogenization of raw materials, clinker firing, cement grinding, and so on Get A free quote!Dry Process Of Cement Production 3005000TPD AGICO CEMENT1971年8月17日 116 Portland Cement Manufacturing 1161 Process Description17 Portland cement is a fine powder, gray or white in color, that consists of a mixture of hydraulic cement materials comprising primarily calcium silicates, aluminates and aluminoferrites More than 30 raw materials are known to be used in the manufacture of portland cement, and these116 Portland Cement Manufacturing US EPA2023年7月10日 Cement manufacturing is a significant industrial activity that plays a vital role in the construction sector However, the process of cement production is associated with various environmental Cement Manufacturing Process and Its Environmental
.jpg)
2 Major Roles of Limestone in Cement Manufacturing
2023年5月27日 Step 5: Cement grinding After mixing with gypsum and admixtures, the clinker is sent to a cement mill for grinding Cement grinding can be carried out either in an integrated cement plant or in a standalone cement grinding station 3 What should limestone be mixed with to make cement? This needs to start with the cement composition2019年1月3日 Clinker grinding technology is the most energyintensive process in cement manufacturing Traditionally, it was treated as "low on technology" and "high on energy" as grinding circuits use more than 60 per cent of total energy consumed and account for most of the manufacturing cost Since the increasing energy cost started burning the benefits significantly, Clinker grinding technology in cement manufacturing2022年6月30日 It also prevents agglomeration and coating of cement powder at the surface of balls and mill walls Sometimes Triethanolamine is added to the mix to prevent powder agglomeration The grinding process can occur in an open circuit grinding or closedcircuit grinding In the open circuit grinding, the materials pass straight through the millThe Manufacturing Process of Cement in Factory2024年9月5日 The Manufacturing Process of Cement Now, let’s explore the steps involved in the cement production process in more detail: 1 Mining and Crushing The process of making cement begins with mining, where raw materials are extracted from quarries Huge machines called excavators dig the limestone out of the earthA Comprehensive Guide to the Cement Manufacturing Process
.jpg)
How Cement is Made? A Step by Step Process Cement Shop
2022年2月22日 Step 4: Cement Grinding, Storage and Packaging Clinker and gypsum are taken from their respective hoppers and fed to the mills for Ordinary Portland Cement (OPC), limestone for limestone cement, and slag for slag cement In the first and second chambers of the ball mill, the feed is ground to a fine powder2024年2月11日 The final grinding process is the last stage of the cement mining process and making procedure In the cement plant, there are circulating drums adjusted with steel balls Clinker, after being cooled, is moving to these circulating drums ground into such a powder that each pound has 150 billion grainsAll Stages of Cement Manufacturing from The Cement Mining Process 2021年4月19日 Grinding of finished cement is performed in a single stage, intergrinding materials with very different grindabilities This intergrinding process has many different interactions among the different components of the finished cement In a context of developing more sustainable and less energy intensive processes, it is important to understand the Resistance to Grinding and Cement Paste Performance of Blends