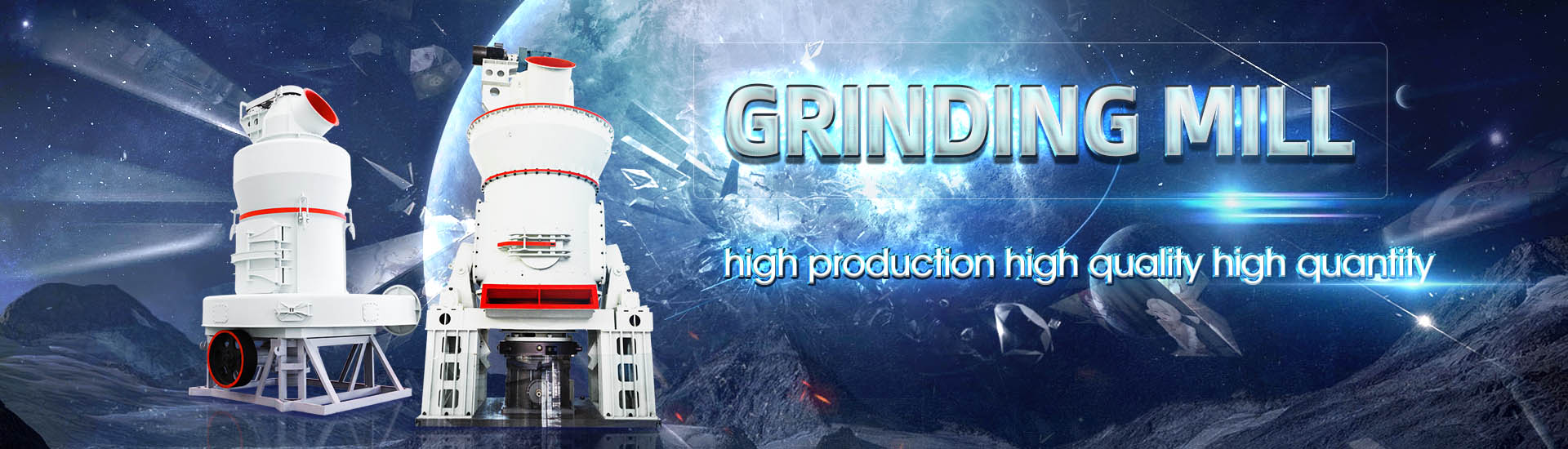
2.2 million tons of cement grinding station process

Carbon and air pollutant emissions from China’s cement industry
In this study, we investigated the decadal changes in carbon dioxide and air pollutant emissions for the period of 1990–2015 based on intensive unitbased information on activity rates, pro Process costs for the estimated annual production of 2 million tons of cement at the Lehigh Cement plant were considered in the technoeconomic assessment It evaluates the leading Continuous Assessment of the Environmental Impact and 2015年8月1日 The results show that approximately 248t, 469t, and 341t of materials are required to produce a ton of the product in raw material preparation, clinker production, and Analysis of material flow and consumption in cement production 2023年10月13日 The cement grinding process accounts for approximately 10% of the total emissions associated with the cement industry, primarily stemming from energy requirements 19Global database of cement production assets and upstream
.jpg)
Review on energy conservation and emission reduction
2022年12月1日 Raw meal preparation, clinker manufacturing, and cement grinding recorded the highest thermal energy savings of 430 GJ/t, 24 GJ/t, and 029 GJ/t, respectively Gravitytype Association of Portland Cement (ABCP), the International Energy Agency (IEA), the Cement Sustainability Initiative (CSI) of the World Business Council for Sustainable Development IMPROVING THERMAL AND ELECTRIC ENERGY EFFICIENCY AT 2022年4月5日 Global technology company ABB has installed ABB Ability™ System 800xA®, the marketleading distributed control system (DCS) automation platform, to upgrade three ABB upgrades process control systems and cement grinding units 2024年5月1日 Cement manufacturing consists of three basic stages: raw material preparation, clinker calcination, and cement grinding The clinker calcination process in the kiln is the only Carbon and air pollutant emissions forecast of China's cement
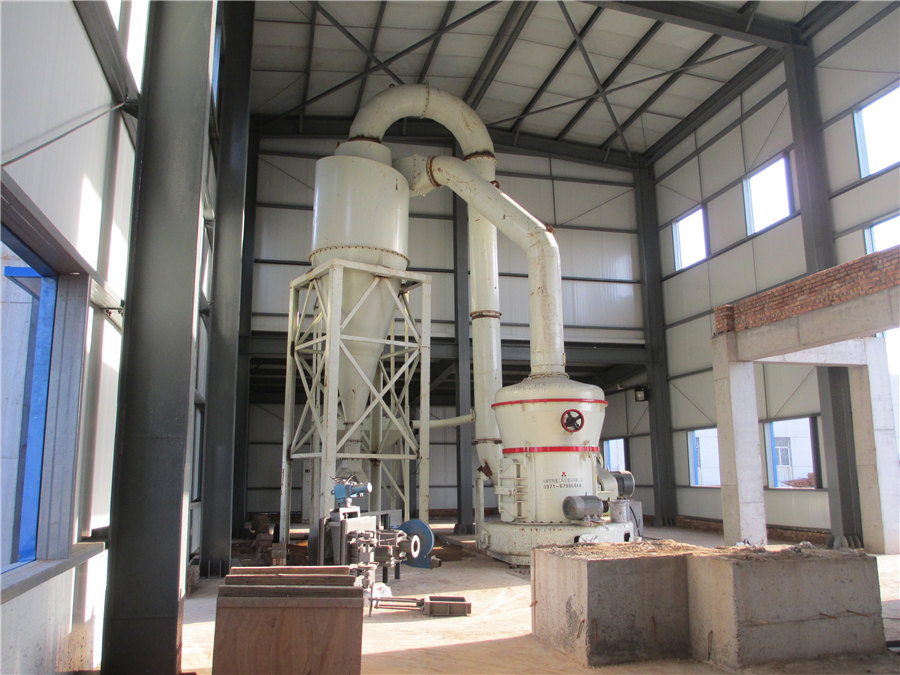
Carbon and air pollutant emissions from China's cement industry
In this study, we investigated the decadal changes of carbon dioxide and air pollutant emissions and control technologies, which improved the accuracy of the cement emissions in China We cement plants and an installed capacity of 234 million ton per annum (94% of which is from large cement plants) During 20062007 cement production grew at a rate of 91% compared to the same period theA Review Article on Manufacturing Process of Cement, 2022年9月21日 Global cement production has reached 39 billion tons However, the clinkerization process, which is the basis of cement production, is responsible for an approximate annual global CO2 emission of Cement and Clinker Production by Indirect 3 The global investment estimated at nearly MAD 24 billion, or EUR 216 million will be financed by the AfDB, Société Générale (SG), Banque Commerciale Populaire (BCP) and BMCE Bank 22 Location The cement factory site is located in Oulad Ghanem rural municipality in El Jadida Province, 45 km to the SouthWest of the town of El Jadida and 21 km to the NorthEast of AFRICAN DEVELOPMENT BANK GROUP
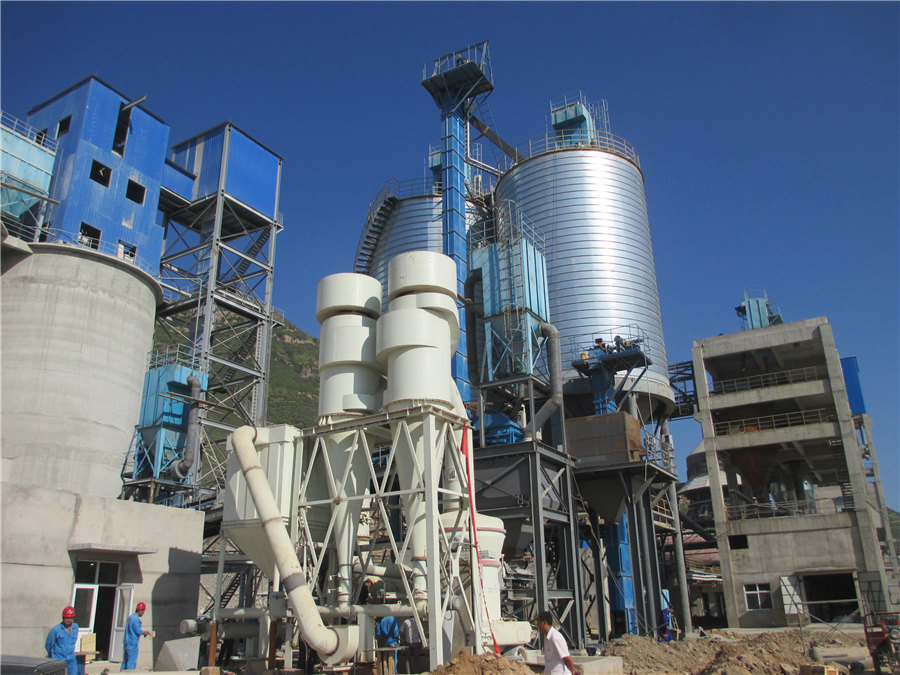
Review on energy conservation and emission reduction
2022年12月1日 In the cement industry, the total energy consumption accounts for 50–60% of the overall manufacturing cost, while thermal energy accounts for 20–25% (Wang et al, 2009; Singhi and Bhargava, 2010)The modern cement industry requires 110–120 kWh of electrical power to produce one ton of cement (Mejeoumov, 2007)Thermal energy is used mainly during One Million Tpy Cement Grinding Production Line / 3300 Tpd Clinker Roller Mill Plant Facility, Find Details and Price about Cement Grinding Station Clinker Grinding Plant from One Million Tpy like the construction of cement grinding plant with an annual output of 112 million tons, the building of cement grinding plant with 0506 One Million Tpy Cement Grinding Production Line / 3300 Tpd 2021年3月3日 Cement is produced by a hightemperature (about 1500 °C) reaction in a rotary kiln of carefully proportioned and blended ratios of lime (CaO), silica (SiO 2), alumina (Al 2 O 3), and iron oxide (Fe 2 O 3)The production of cement is a chemical process requiring an accurate blend of the previously cited four key organic oxides and the limitation of several undesirable Cement SpringerLinkThe final manufacturing stage at a cement plant is the grinding of cement clinker from the kiln, mixed with 45% gypsum and possible additives, into the final product, cement In a modern cement plant the total consumption of electrical energy is about 100 kWh/t The cement grinding process accounts for approx 40% if this energy consumptionCEMENT GRINDING SYSTEMS INFINITY FOR CEMENT EQUIPMENT
.jpg)
Cement Production an overview ScienceDirect Topics
China was the largest producer of groundnut, contributing to approximately 40% (∼18 million metric tons) of worldwide production (Fig 2) Shell compartments comprise around 21–29% of the ground nut by weight [24, 25] So, ground nut shell waste of around 11 million metric tons from the groundnut industry is generated per annum [26]In order to realise efficient comminution in limited size ranges with a minimum number of mills, ECRA has developed the concept of “multistage grinding” of cement 2 Multistage grinding: An approach for future comminution 21 The general idea of multistage grinding Separate grinding systems for raw meal and cement are state of the artStudy on the production of cements using a multistage grinding 2023年2月1日 about 268 million tons of cement in 360 installations, of which 268 produce both clinker and cement, 90 produce only cement and 2 produce only clinker [1] CEMENT RAW MATERIALS BLENDING PROCESS BY 2022年4月5日 which can be avoided by grinding the ash [27] in 2000 it amounted to 1600 million tons, The concentration of these compounds affects the hydration process of cement mortars doped with SSARecovery of Sewage Sludge in the Cement Industry
.jpg)
Deciphering the CO2 emissions and emission intensity of cement
2022年6月10日 Up to 8% of anthropogenic CO 2 emissions are released to the atmosphere during cement production, not only due to the amount of fuel burning but also because of its unique limestone decomposition Yet, the industry generally considers that no material is capable of replacing reinforced concrete at a low economic cost at present or even in the mid to long Our cement grinding plant has the features of simple technological process, easy operation, low like the construction of cement grinding plant with an annual output of 112 million tons, the building of cement grinding plant with 0506 Supplier Homepage Products cement grinding station Cement Roller Press and Ball Mill Cement Roller Press and Ball Mill Combined Grinding System in Cement 2020年1月2日 2 CEMENT MANUFACTURING PROCESS A cement production plant consists of three major processes such as quarry and raw material preparation, clinker production and cement grinding and distribution [2] During raw material preparation first, limestone and other raw materials are extracted using drilling and blasting techniquesCement Industry in Sri Lanka JRTE2015年10月23日 In this chapter an introduction of widely applied energyefficient grinding technologies in cement grinding and description of the operating principles of the related equipments and comparisons over each other in terms of grinding efficiency, specific energy consumption, production capacity and cement quality are given A case study performed on a EnergyEfficient Technologies in Cement Grinding IntechOpen
.jpg)
ABB upgrades process control systems and cement grinding
2022年4月5日 Star Cement and Star Super Cement are subsidiaries of Ultratech Cement, India and operate a 3 million tons per annum (tpa) clinkerization unit at Ras Al Khaimah, four cement grinding units of 22 million tpa unit at Jabel Ali, 14 million tpa unit at Abu Dhabi and 11 million tpa unit at Ajman in UAE as well as a 1 million tpa grinding unit in plete proposal and process equipment of 2,000,000 tons per year is supplied by Jiangsu Pengfei Group This project adopts Φ42×13m open circuit tube mill, 170140 rolling machine and 1200 Vtype separator, consist of the extruding and united grinding process flow, form one separate and complete cement grinding, bulk and packing cement production line, the process One to Two Million Tonnes Per Annum Clinker Grinding Station 2021年7月1日 The clinker quality assessment can best be done by Lab Ball Mill grinding of day average clinker with mineral gypsum (with SO3 of the lab ground cement targeted at 22 to 24 with fixed grinding time to achieve Blaine’s of around 300320 M2/kg with the residue on 45 microns of the cement in range of 18 per cent to 20 per cent, at this fineness, the clinker is Cement grinding capacity expansion Indian Cement Review2020年9月14日 Let material ground be 3000 tons in 20 hours Therefore Tons/hour = 3000/20 = 150 tph Average kWh/ton of material ground = 2608/150 = 174 kWh; Power consumption per ton of clinker with a conversion ratio for consumption 155 : 1 = 174 x 155 = 27 kWh/ton; Using 4% gypsum – 1 ton clinker = 104 tons of cementThe essentials of electrical systems in cement plants EEP
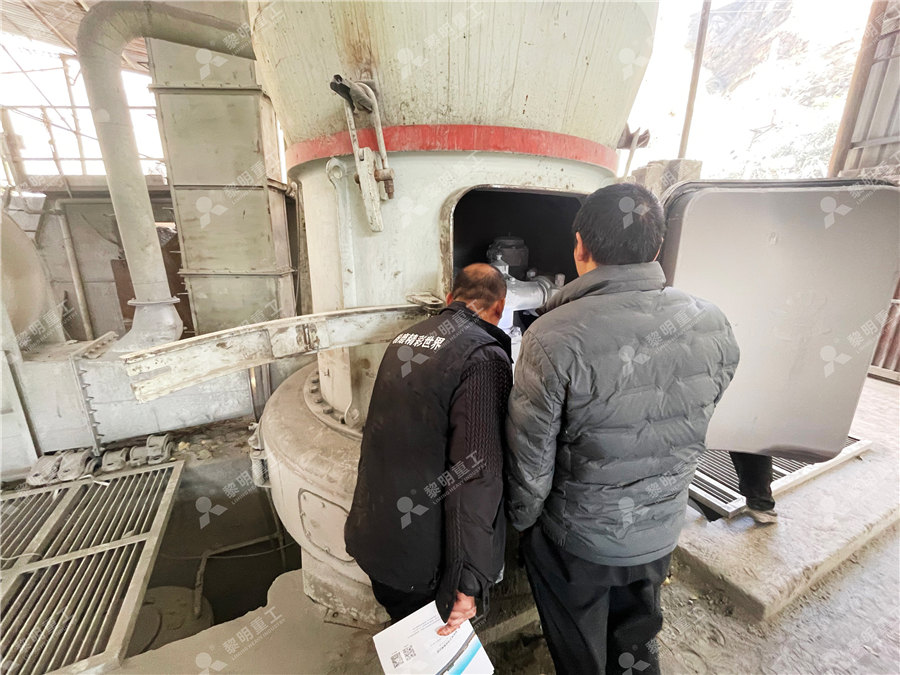
Simulation and Optimization of an Integrated Process Flow Sheet
2021年3月9日 In this study the process flow diagram for the cement production was simulated using Aspen HYSYS 88 software to achieve high energy optimization and optimum cement flow rate by varying the flow 2024年6月5日 A typical modern cement plant is estimated to consume up to 110 kWh of electricity for grinding a ton of cement About 95 million metric tons of cement was produced in the United States in 2022, using up more than 89 Towards Leveraging Artificial Intelligence for 2024年10月9日 [Sinoma Construction Signs Morocco Cement Grinding Station Project] Sinoma Construction Company and Moroccan Janoub Cimenterie Company signed a contract for EL OUATIA modular grinding station with an annual output of 400,000 tons Editor/He Yuting and plans to reduce 38 million tons of carbon dioxide emissions by 2025 In Sinoma Construction Signs Morocco Cement Grinding Station2021年2月8日 Abstract China is the largest cement producer and consumer in the world Cement manufacturing is highly energyintensive and is one of the major contributors to carbon dioxide (CO2) and air pollutant emissions, which threatens climate mitigation and air quality improvement In this study, we investigated the decadal changes in carbon dioxide and air ACP Carbon and air pollutant emissions from China's cement
.jpg)
List of companies and cities in Africa that manufacture cement
Ghana Cement 97% market share [15]; Diamond Cement Ghana 2001; [16] railway siding Diamond Cement Ghana at Aflao near Lomé Buipe proposed [17]; Ghacem, a subsidiary of Scancem and Heidelberg Cement, with operations in the port city of Tema [18] "Ghacem" is same as "Ghana Cement", and does not have 97% market share anymore because Buipe plant has 2015年4月1日 The typical electrical energy consumption of a modern cement plant is about 110–120 kW h per tonne of cement In the process thermal energy is used mainly during the burning, while maximum share of electrical energy is used for cement grinding approximately 107 million tons of waste oil is used by cement kilns as Recent development on the uses of alternative fuels in cement 2016年1月20日 In the surveyed cement plant, three balances are established between input and output material in the raw mill, clinker production, and cement grinding system 248 t, 469 t, and 341 t of materials are required to produce a ton of the product in raw material preparation, clinker production, and cement grinding stages; waste gases account for the largest proportion of the Analysis of material flow and consumption in cement production process 2015年4月15日 Li et al (2015) analyzed the addition of 002 to 010% of sugarcane molasses in proportion to cement, determining that the addition of 004% results in the optimization of properties of the Sustainable Resource Opportunity for Cane Molasses: Use of Cane
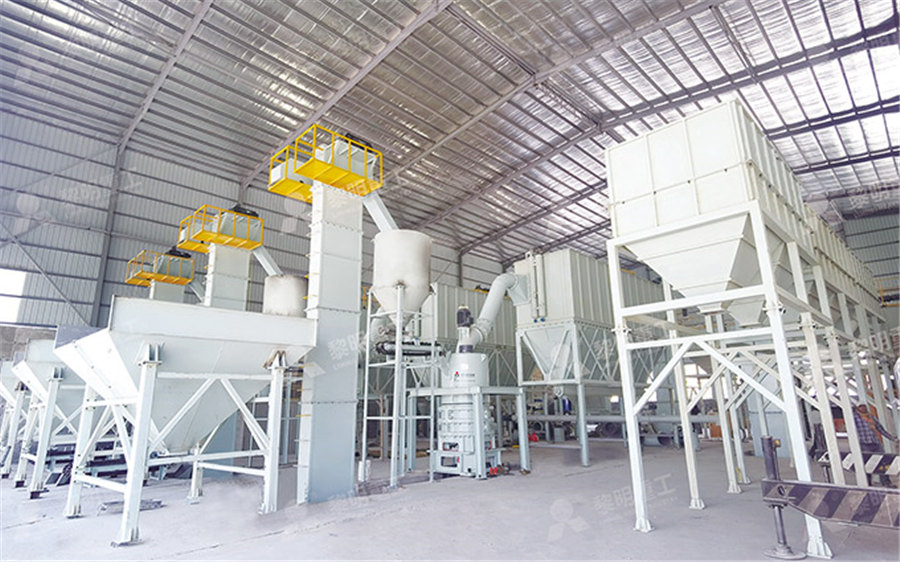
(PDF) Effect of Gypsum Amount in Cement on Fresh and Hard
2020年5月1日 160+ million publication pages; 13 billion tons of global cement production was pared by the process of crushing and grinding the quarried gypsum to the required size2009年5月15日 Grinding of clinker is the last and most energyconsuming stage of the cement manufacturing process, drawing on average 40% of the total energy required to produce one ton of cement During this stage, the clinker particles are substantially reduced in size to generate a certain level of fineness as it has a direct influence on such performance characteristics of the [PDF] Improved cement quality and grinding efficiency by 2016年12月31日 Waste management is a serious issue around the world It is most prominent in the developing countries Non–hazardous industrial waste is another aspect at 100 million tons/year with coal ash Coprocessing of Industrial Waste in Cement Kiln2022年12月23日 This review provides an indepth analysis of the complex chemistry of cement, offering valuable insights for researchers(PDF) An Insight into the Chemistry of Cement—A
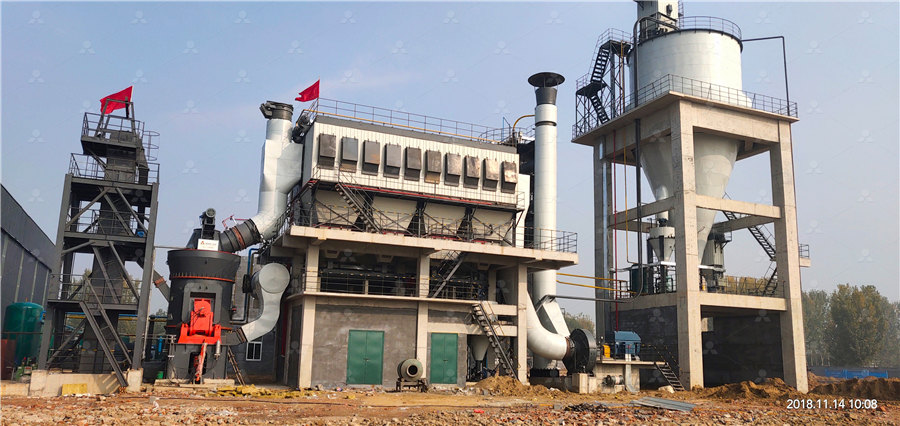
(PDF) EFFECTS OF VARIOUS GRINDING AIDS DOSAGE
2023年1月1日 In this study, the effects of four grinding aids with three different levels on the three important characteristics of the cement, namely the specific surface area, the compressive strength of the 2020年8月15日 Throughout the studies, the data related to cement grinding process was collected from two different cement grinding circuits of Bursa Cement Plant/Turkey Turkish cement sector with 90 million tons of capacity is in the first place of European production, and third and fourth in export and production in the world rankings respectively ( Saka, 2019 )The impacts of dry stirred milling application on quality and 2020年4月6日 Evaluating the Effect of Calcination and Grinding of Corn Stalk Ash on Pozzolanic Potential for Sustainable CementBased Materials April 2020 Advances in Materials Science and Engineering 2020:113(PDF) Evaluating the Effect of Calcination and Grinding of Corn 2020年4月10日 212 Waste glass (powder) The WG used in this experiment was postconsumer window plate glass obtained from a waste recycling station in Guiyang, which was a typical soda lime glass and the WGPs were obtained by grinding the cleaned and crushed WG in different time of testing mill (SM∅500 × 500, 48 r/min) The chemical analysis of WGPs, shown Grinding kinetics of waste glass powder and its composite effect
.jpg)
Determination of correlation between specific energy consumption
2016年4月25日 This process typically requires approximately 3 to 6 million Btu (32 to 63 GJ) of energy and 17 tons of raw materials (chiefly limestone) per ton (t) of clinker produced and is accompanied by 2014年12月1日 The design value of generated power per ton clinker is 341 kW h/t, the design for power generation is 7600 h, annual power generation is 4864 million kW h, and the power generation station will supply about 4523 million kW h Exergetic life cycle assessment of cement production process 2000年3月1日 There are ∼6700 million tons of perlite reserves in the world and two thirds of this amount takes place in Turkey Although perlite possesses pozzolanic properties, it has not been so far used in producing blended cements This study focuses on the use of natural perlites in blended cement productionA study of intergrinding and separate grinding of blast furnace slag cement2022年8月16日 The grinding process can ensure that CFBA meets the Chinese standards for a cement admixture and realize the resource utilization of CFBA With the widespread application of circulating fluidized bed (CFB) combustion technology, the popularity of CFB ash (CFBA) has increased dramatically and its production and largescale utilization have become increasingly Feasibility Study of Grinding Circulating Fluidized Bed Ash as Cement