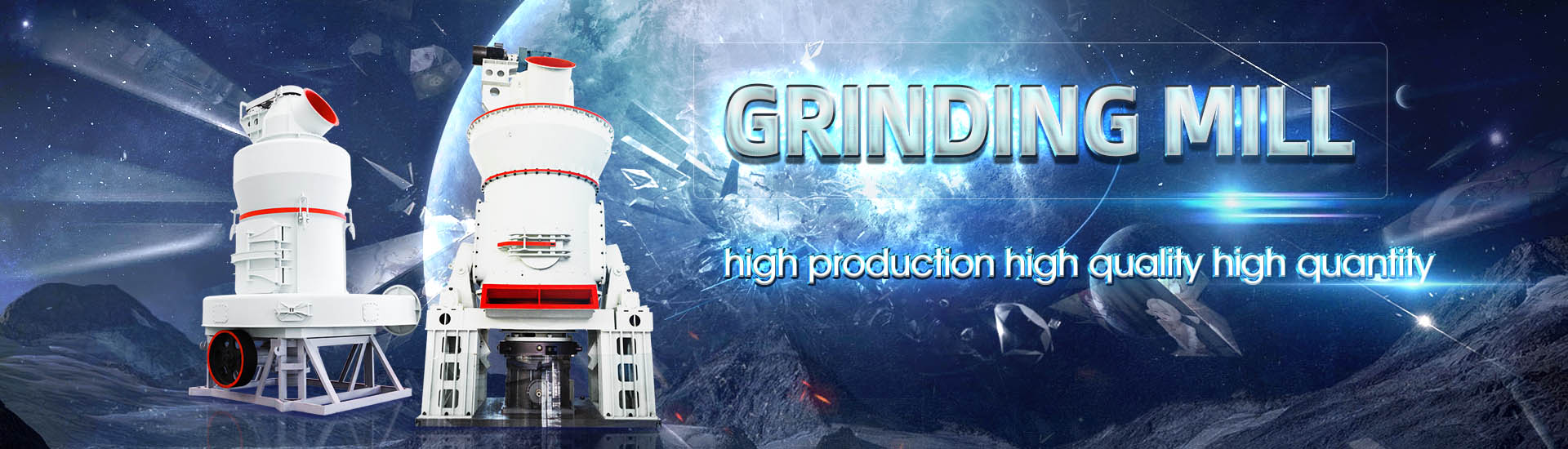
Cement raw material homogenization warehouse process
.jpg)
HOMOGENIZATION STRATEGY IN THE CEMENT INDUSTRY PEC
• Establish the regulated proportioning of the raw material components (A/B/C ratio) based on the target chemistry for the pile • Provide a metering arrangement for the materials A, B and C from hoppers or stockpilesHomogenization is achieved by two procedures, by ‘blending’ or ‘mixing’ Blending means that two or more material streams or layers are combined whereas mixing signifies theAspects of Raw Material Homogenization Archive“Holderbank” Cement Seminar 2000 Process Technology Raw Material Homogenization and Storage Page 188 © Holderbank Management Consulting, 2000Holderbank Cement engineering book2024年6月18日 This study helps to understand the homogenization process of raw materials by equipment in cement production and provides certain reference and data support for Evaluation and Analysis of Cement Raw Meal Homogenization
.jpg)
Homogenisation Cement manufacturing process
Raw meal homogenization is achieved in our Controlled Flow Inverted (CFI) cone silo, also designed by FL Smidth The blending silo has a capacity of 12,000 MT Raw meal is fed from the top of the silo through a splitter box2011年12月20日 The introduction of the homogenization process into the technological chain of manufacture of cement and mixture calculation, in accordance with the quality standards, Homogenization and Management of Cement Quality from Raw Establish the regulated proportioning of the raw material components (A/B/C ratio) based on the target chemistry for the pile Provide a metering arrangement for the materials A, B, and C from hoppers or stockpiles Ideally, an online Homogenization Strategy in the Cement Industry2024年4月26日 This study helps to understand the homogenization process of raw materials by equipment in cement production and provides certain reference and data support for equipment selection, operation optimization, and quality Evaluation and Analysis of Cement Raw Meal
.jpg)
From raw materials to cement
The desired raw mix of crushed raw material and the additional components required for the type of cement, eg silica sand and iron ore, is prepared using metering devicesThen, workers crush the extracted materials, often in multiple stages, to achieve the desired size This crushing is crucial as it increases the surface area of the raw materials, facilitating their chemical reaction during the cement StepbyStep Guide to the Manufacturing of Cement24 Turning waste into a source of raw material and fuel 8 25 Feeding points for waste materials into the cement manufacturing process 9 3 Selection of fuels and raw materials 10 31 Considerations for cement manufacturers 10 311 Kiln operation 10 312 Emissions 10 313 Clinker, cement and final product quality 11Guidelines for CoProcessing Fuels and Raw Materials in Cement together in a raw mill to a particle size of 90 micrometres, producing “kiln feed” Cement Plant: The Manufacturing Process worldcementassociation 1 Limestone (CaCO3) is taken from a quarry 2 4 3 warehouse Raw material silos Limestone storage and preblending unit Rotary Kiln Additives Silos Cement millCement Plant: The Manufacturing Process 4 5 World Cement

1000tpd cement production lineChina Cement Machinery
The Pengfei EPC cement production line project includes services such as process design, equipment supply (including mechanical and electrical parts), civil engineering, installation and commissioning, trial operation, reaching production standards, and final delivery Mechanical equipments include limestone crushing and conveying, clay crushing, and auxiliary raw Take a look at our interactive animation of the cement production process to learn how cement is made by us at CEMEX Raw meal homogenization This process takes place in silos equipped for obtaining a homogenous mix of the Inside, at 1400 degrees C, the raw material is transformed into clinker: small, dark gray nodules 34 centimetres Cement Production: How Cement Is Manufactured CEMEX UKThe Pengfei EPC cement production line project includes services such as process design, equipment supply (including mechanical and electrical parts), civil engineering, installation and commissioning, trial operation, reaching production standards, and final delivery Mechanical equipments include limestone crushing and conveying, clay crushing, and auxiliary raw 3000tpd cement production lineChina Cement Machinery Mining the raw material Raw meal homogenization This process takes place in silos equipped for obtaining a homogenous mix of the material 8 Calcination Calcination is the core portion of the process, in which huge rotary kilns come into play How Cement is Made (Video) Cemex USA CEMEX
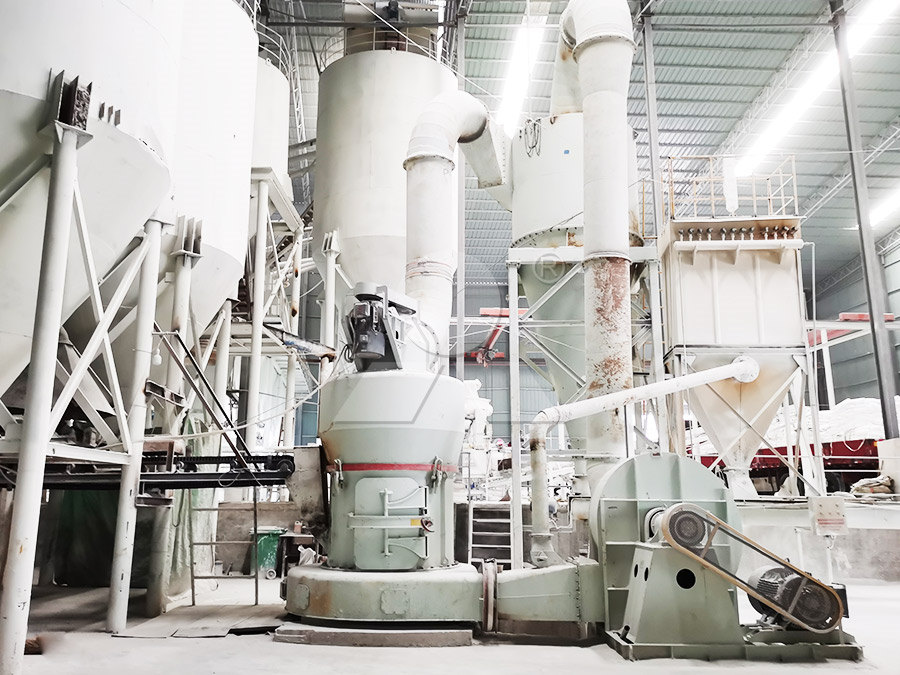
Cement Manufacturing Process INFINITY FOR CEMENT EQUIPMENT
The principal raw materials for cement manufacturing are: Limestone; Silica and alumina from basalt , shale or sand; Iron from iron ore or steel mill scale Sand stone; Pumice (volcanic ash for Portland Pozzolana cement ) Gypsum General Properties of Raw Material Sources Limestone; The basic raw material of the cement production is limestone50 Raw Material Homogenization and Storage As the daily practice demonstrates, chemical fluctuations in the raw mix have a considerable influence on kiln operation eg coating and ring formation as well as encrustation and clogging problems process in Cement IndustryRaw Material Homogenization and Storage INFINITY FOR CEMENT 2024年3月20日 This cement production line adopts a new dry cement preparation process, which is mainly composed of crushing and prehomogenization, raw material preparation homogenization, preheating decomposition, cement clinker clacination, cement grinding, packaging and other processes If you have any need, FREE quotation today!2500tpd Cement Plant Project In Kyrgyzstan AGICO CEMENTProcess and Energy Audit; Online Calculations; Knowledge Base; Contact Us; Homogenization (BLENDING) In preparing raw meal, raw materials like limestone, clay and iron ore are proportioned and fed to raw mill, where these Homogenization (BLENDING) Cement Plant
.jpg)
6 Cement Equipment For Dryprocess Cement
2023年12月26日 As we all know, the dryprocess cement production line is commonly used in the cement industry The new type of dryprocess cement production process includes four main sections: Prehomogenization of raw The cement quality control of cement plant is mainly based on specific technological process, which includes the quality control of various raw materials, semifinished products used in the production process, the sampling analysis How to improve cement plant process for better this journey through cement production emphasizes each stage’s contribution to the final product’s quality From raw material extraction to cement grinding and storage, this process showcases the pivotal role cement plays in contemporary construction Join us as we explore the durability and reliability of structures shaping our modern worldHow is Cement Produced? SRMPR Cements2012年8月30日 Raw mix is stored in a prehomogenization pile after grinding raw mix to fine powder Cement Manufacturing Process Phase III: Preheating Raw Material After final grinding, the material is ready to face the preheating chamber Preheater chamber consists of series of vertical cyclone from where the raw material passes before facing the kilnCement Manufacturing Process Engineering Intro
.jpg)
Prehomogenization INFINITY FOR CEMENT EQUIPMENT
Prehomogenization In past cases, where the main component of the cement raw material (usually limestone), showed con siderable fluctuations in the CaC03content, and as long as relatively low quantities of raw materials were processed in cement plants, selective quarrying was applied, to reduce to some extent fluctuations in the limestone’s chemistryThe cement production equipment adopts the dry process cement production process After the raw materials are dried and ground into raw meal powder, After the fine powder is selected by highefficiency powder concentrator, part of the fine powder is sent to raw material homogenization warehouse by air conveying chute and bucket elevator2500TPD new type dry process cement clinker production lineWhile each cement plant may differ in layout, equipment, and appearance, the general process of manufacturing portland cement is the same: crushed limestone and sand are mixed with ground clay, shale, iron ore, fly ash and alternative raw materials Some manufacturers grind the raw materials dry, while others use a wetgrinding process How Cement is Made Portland Cement AssociationGrinding and homogenization The grinding process takes place in a raw mill to reduce the particle size of the components to a typical value of 1015 % residue on a 90 um sieve The output of the grinding process – called ‘raw meal’ – is transferred to a homogenization silo before the clinker manufacturing processGrinding and homogenization Al badia cement
.jpg)
Cement Production Process Cement Manufacturing Process AGICO CEMENT
2020年8月25日 Cement raw material preparation: Limestone is main raw materials for cement manufacturing, and most cement plants are located next to the quarry to reduce the transportation cost; Using explosion or getter loader to mine raw materials; sending raw materials to the cement crusher to crush or hammer; crushed raw materials are stored to prevent from environment Stage of Cement Manufacture There are six main stages of the cement manufacturing process Stage 1: Raw Material Extraction/Quarry The raw cement ingredients needed for cement production are limestone (calcium), sand and clay (silicon, aluminum, iron), shale, fly ash, mill scale, and bauxite The ore rocks are quarried and crushed into smaller pieces of about 6 inchesHow Cement is Made Cement Manufacturing Process2024年6月18日 This study helps to understand the homogenization process of raw materials by equipment in cement production and provides certain reference and data support for equipment selection, operation Evaluation and Analysis of Cement Raw Meal Homogenization Homogenization Raw meal homogenization is achieved in our Controlled Flow Inverted (CFI) cone silo, also designed by FL Smidth The blending silo has a capacity of 12,000 MT Raw meal is fed from the top of the silo through a Homogenisation Cement manufacturing process

Cement manufacturing raw materials Understanding Cement
If you happen to be a geologist, the raw materials quarry is probably the most interesting part of a cement works, maybe unless you view the clinkering process as igneous rocks in the making The most common raw rock types used in cement production are: Limestone (supplies the bulk of Mixing: according to the requirement of clinker, compound desired raw material for cement production line Grinding: grinding all materials into required fineness by cement mill Cement ball mill and vertical cement mill are two common types Homogenizing: homogeneous kiln feed is the precondition of clinker production, so homogenization of raw Preparation Of Cement Raw Material Cement Mill, Cement However, it would be seen that the most significant process and types used for raw material grinding operations in modern cement industry are: Process: Dry Closed circuit drygrinding Type of mill: Ball and tube mills Vertical Roller Mills (VRM) Horizontal roller mill (Roll Press) Roller press with Ball millRaw Material DryingGrinding Cement Plant OptimizationExtraction and Preparation of Raw Materials The main raw materials (limestone, clay chalk or basalt) are quarried from natural rocks They are crushed and transferred to preblending storage where other substances (such as sand, iron ore, bauxite, shale, slag, fly ash) are added to get the desired chemical composition HomogenizationCement Clinker Manufacturing Process with Reactions
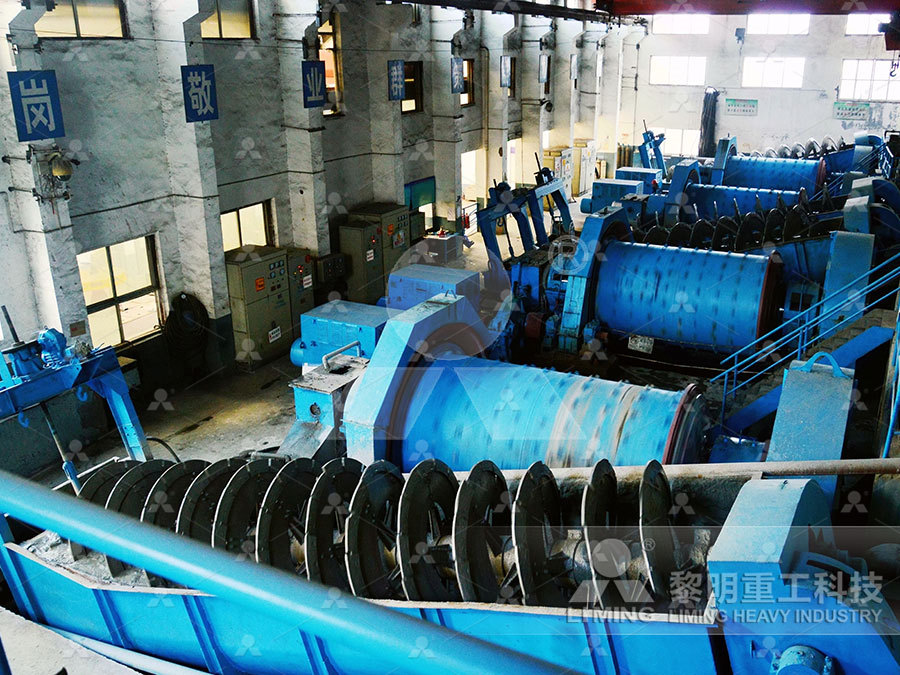
Raw material handling and storage Indian Cement Review
2014年12月31日 Raw materials used in cement plants have a great influence on the investment for a cement plant as the design and selection of the handling equipment is based on their physical and chemical The homogenization process is similar in both trapezoidal and circular piles However, In order to convert these raw materials into clinker and cement, it is necessary to produce a raw mix with a top size of about 02 mm The reduction ratio required for most raw materials is consequently 10002000:02 or 500010,000 It is obvious that such a degree of comminution cannot be achieved through a single machine or a onestage operationEverything you need to know about cement Materials Preparation and Raw 2023年7月10日 The cement manufacturing process involves the extraction and processing of raw materials, such as limestone, clay, and shale, which are then heated in a kiln at high temperatures to form clinkerCement Manufacturing Process and Its Environmental ImpactPortland Pozzolana Cement Manufacturing Process Portland pozzolana cement shall be manufactured by mixing and intergrinding Portland cement clinker, pozzolanic materials, and gypsum The manufacturing process is PPC Cement Manufacturing Process Portland
.jpg)
Homogenization and Management of Cement Quality from Raw Materials
2011年12月20日 In spite of the improvements of the exploitation methods, the problem of the raw materials’ quality and stability is not solved The old calculation method of a cement mixture is based on the principal of groping This procedure induced significant losses for the manufacturing unit at technical and economic level However, the purpose of recent studies is to consider a 2022年10月25日 Due to fast analysis speed, analyzing composition content of cement raw meal utilizing near infrared (NIR) spectroscopy, combined with partial least squares regression (PLS), is a reliable alternative method for the cement Rapid Analysis of Raw Meal Composition Content 2016年8月12日 Rawmaterial blending is an important process affecting cement quality The aim of this process is to mix a variety of materials such as limestone, shale, sandstone and iron to produce cement raw (PDF) Mathematical modeling of a cement rawmaterial blending process 2024年9月10日 Steps of Cement Manufacturing The steps involved in cement manufacturing are as follows: Quarrying: Raw materials such as limestone and clay are extracted from quarries or mines; Crushing and Grinding: The extracted raw materials are crushed and ground into a fine powder; Blending: The crushed and ground raw materials are blended in specific proportions Cement Manufacturing Process: Know Extraction, Processing
.jpg)
The Cement Manufacturing Process Thermo Fisher Scientific
2023年12月20日 Cement manufacturing is a complex process that begins with mining and then grinding raw materials that include limestone and clay, to a fine powder, called raw meal, which is then heated to a sintering temperature as high as 1450 °C in a cement kiln In this process, the chemical bonds of the raw materials are broken down and then they are Although modern technology and improved methodologies has greatly influenced to bring down inconsistency in raw materials through mine planning greatly facilitated by the introduction of Global Positioning System (GPS) However, the remaining material variations can be reduced more economically by preblending via staking and reclaimingPreHomogenization(Stacking and Reclaiming) Cement Plant 2021年7月5日 The exergy efficiency of the cement raw meal manufacturing process (Citation 2019) evaluated integrated multilevel multiwholesaler supply chains under the shortage and limited warehouse The chemistry of the raw materials and the raw meal is very closely regulated to ensure a high cement quality Material homogenization is Full article: Evaluation of optimization techniques for predicting PDF On Apr 7, 2022, Alick Sinoya published CEMENT PRODUCTION PROCESS REPORT A SINOYA 1 Find, read and cite all the research you need on ResearchGate(PDF) CEMENT PRODUCTION PROCESS REPORT A SINOYA 1
.jpg)
Evaluation and Analysis of Cement Raw Meal Homogenization
2024年4月26日 In recent years, the variability in the composition of cement raw materials has increasingly impacted the quality of cement products However, there has been relatively little research on the homogenization effects of equipment in the cement production process Existing studies mainly focus on the primary functions of equipment, such as the grinding efficiency of