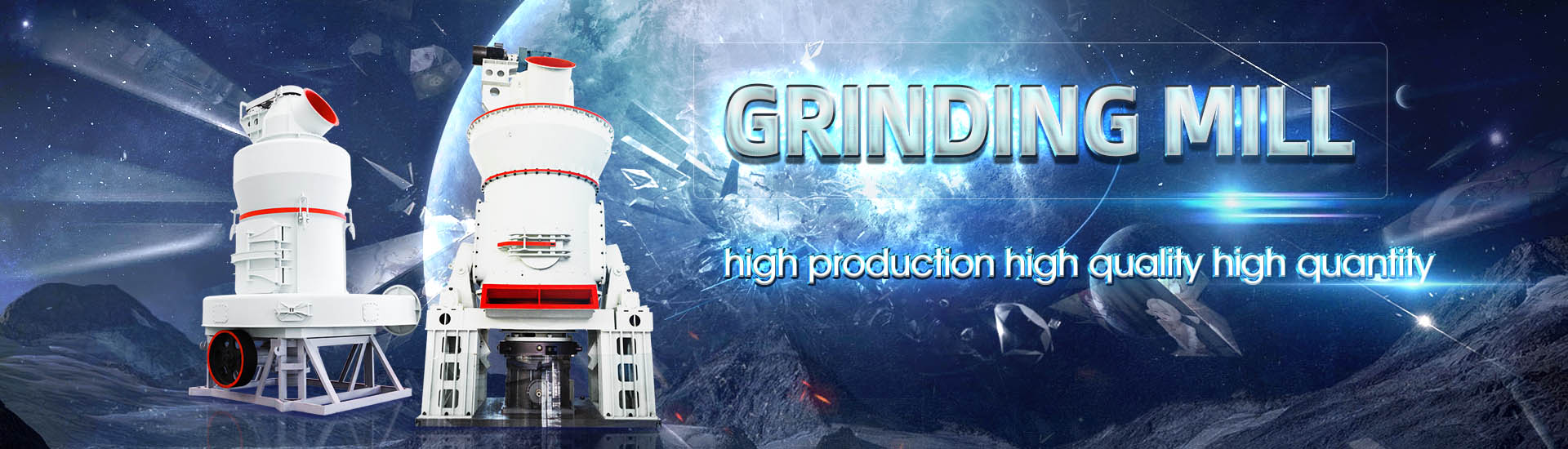
Combined grinding system ball mill inlet material fineness
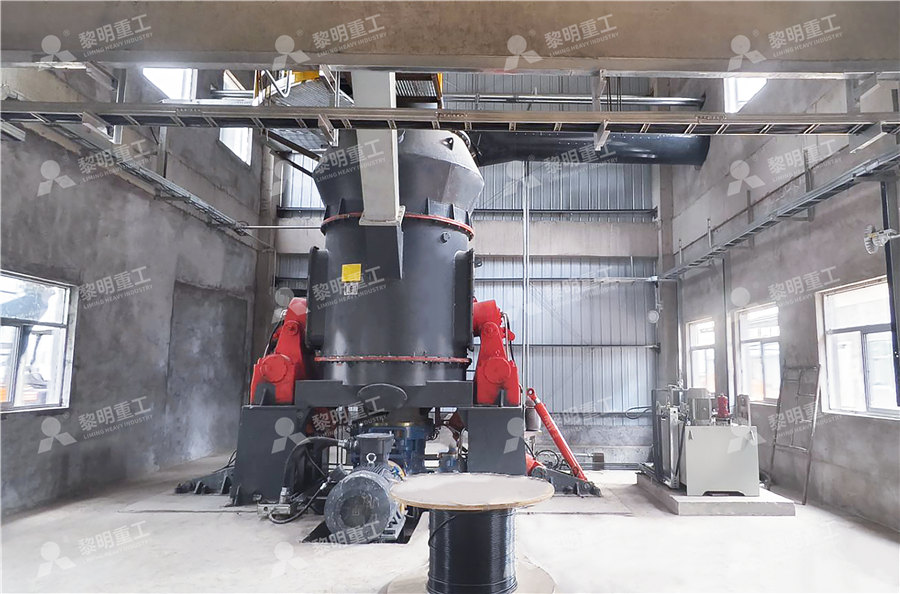
BALL MILLS Ball mill optimisation Holzinger Consulting
common solution to grind raw materials and cement Roller presses are used mainly in combination with a ball mill for cement grinding applications and as finished product grinding The present work aims to design and analysis of Ball mill inlet chute along with the truck assembly for Roller press circuit UMS (Unidan Mill S) type FLS Ball mill which are used in the Cement DESIGN AND ANALYSIS OF BALL MILL INLET CHUTE FORThis features a roller press together with a ball mill in a combi‑grinding mode, where both systems already produce a finished product, but still have two classifiers Another option in such a Thomas Holzinger, Holzinger Consulting, grinding system 2012年6月1日 The paper presents an overview of the current methodology and practice in modeling and control of the grinding process in industrial ball mills Basic kinetic and energy Grinding in Ball Mills: Modeling and Process Control ResearchGate
.jpg)
Optimization of a fully airswept dry grinding cement raw meal
2015年4月1日 Production capacity of a fully airswept industrial scale twocompartment KHD Humboldt Wedag® cement ball mill was optimized with the aid of simulation It was proposed at ceramic plants for grinding the clay The developed system provides continuous monitoring of the grinding, ventilating and drying productivities and it optimizes the mill performance in order MATERIAL GRINDING BY MEANS OF BALL MILLS DAAAMThere are three types of grinding media that are commonly used in ball mills: • steel and other metal balls; • metal cylindrical bodies called cylpebs; • ceramic balls with regular or high Grinding in Ball Mills: Modeling and Process Control Sciendo2002年1月1日 Extensive operational trials on industrial combined grinding plants have shown that the specific energy consumption of the ball mill can be lowered by about 20% by reducing Optimization of ball mills in combined grinding systems with
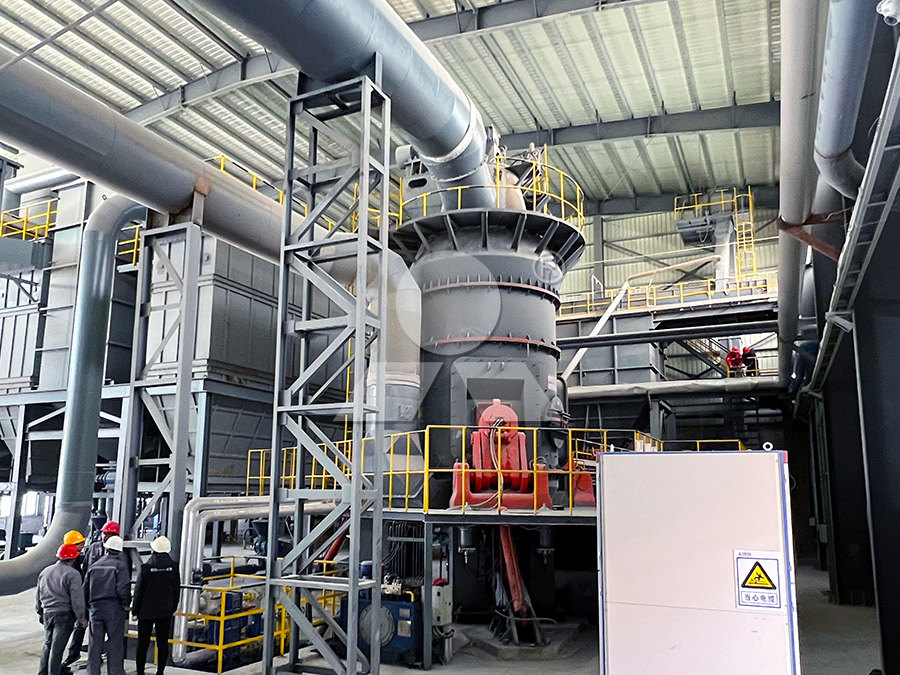
Simulation of the grinding of coarse/fine (heterogeneous) systems
2011年5月8日 This study shows that the three material systems, ground in a ball mill, behave similarly, ie, the breakage distribution functions are independent of the mill environment, the 2013年7月4日 Operation aim of ball mill grinding process is to control grinding particle size and circulation load to ball mill into their objective limits respectively, while guaranteeing producing Intelligent optimal control system for ball mill grinding processBall Mill Ball mills with high efficiency separators have been used for raw material and cement grinding in cement plants all these years Ball mill is a cylinder rotating at about 7080% of critical speed on two trunnions in white metal bearings or slide shoe bearings for large capacity millsRaw Material DryingGrinding Cement Plant Optimization2023年4月23日 A comparison of the grinding media is given together with the knowledge gaps that still need to be bridged to improve the quality and performance of grinding media used in ball mills(PDF) Grinding Media in Ball MillsA Review
.jpg)
Cement grinding Vertical roller mills VS ball mills
Vertical roller mills and ball mills represent two clearly distinct technologies However, with proper adjustments to the operational parameters of the vertical roller mill almost identical cement properties can be achieved by the two mills Download Citation On Jun 1, 2019, Hangke Cui and others published MultiModel Control of Cement Combined Grinding Ball Mill System Based on Adaptive Dynamic Programming Find, read and cite all MultiModel Control of Cement Combined Grinding Ball Mill System 2017年10月25日 Ball mill circuit classification system performance is considered here first because it provides the basis for subsequent characterization of ball mill breakage efficiency Major design and operating variables in closed circuit ball milling of a specified feed to a desired product size are summarized in Table 1How to Improve Ball Mill Performance 911Metallurgist09 khd ball mill Free download as PDF File (pdf), Text File (txt) or view presentation slides online Separator 1520 Closed circuit mills with separator 1520 Double compartment mills 3040 Ball mills are commonly used for final grinding of materials like cement The key factors in ball mill design include the mill's speed, media charge, internal dimensions, and material properties09 KHD Ball Mill PDF Mill (Grinding) Bearing (Mechanical)
.jpg)
Industrial Vertical Grinding Mill
The power consumption of the grinding system is 20% to 30% lower than that of the ball mill, and the energy saving effect is more obvious as the moisture of the raw material increases Compared with the ball mill system, the energy consumption of Ball mill Combi grinding system Finish grinding Ball mill with cage rotor separator Roller press in semifinish mode and ball mill VRM Roller press Specel Energy consumption mill motors kWh/t 30 25 17 17 % at mill motor (ball mill 100%) % 100 83 57 57 Specel Energy consumption mill system kWh/t 39 32 27 26 % department (ball mill 100%) % 100 Thomas Holzinger, Holzinger Consulting, grinding system Problems Existingnumberin the Ball Mill Design of Feed Inlet The hourly output of the ball mill is greatly affected by the feed rate According to a large of reference data, the mainreason that the feed rate and ventilation of the ball mill is whether the grinding mill feed inlet design is reasonable The feed inlet in the design of the old Ball Mill DesignOptimization Of Feeding Devicetor, also reduces the construction volume of the grinding plant to a minimum Drying by means of the connection of a separate hot gas generator is possible sepol® QM as an integral part of the quadropol® mill housing Layout of a combigrinding system for cement, with polycom®, ball mill and sepol® PC sepol® highefficiency separator 5brochure sepol separator myPolysiusService
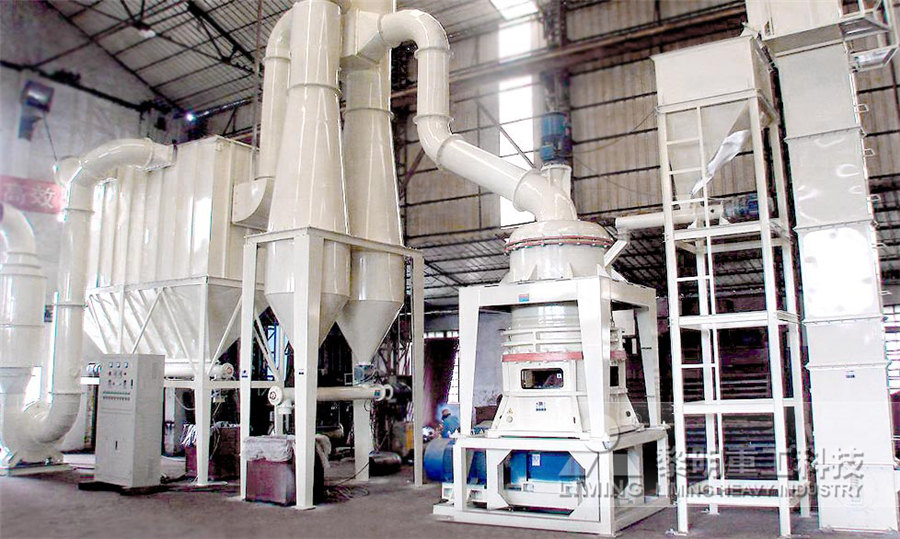
Changing the Fineness of Calcined Petroleum Coke with Ball Race Mills
2019年2月16日 The mill shown in Fig 1 is a modern ball race mill with a dynamic classifier The material to be ground is fed to the ball race mill centrally from the top where the material falls down onto the rotating grinding yoke The yoke and the lower grinding ring are driven by the mill gear The upper fixed grinding ring, pressed down by the hydraulic 2020年3月26日 As combined grinding systems are installed to increase the production capacity of a standalone ball mill as well as to save electrical energy, they are challenging in optimisation and to run them Optimising Combined Grinding Systems2024年5月27日 The General Function of Ball Mills A ball mill is a grinder used for grinding and blending materials for mineral dressing processes, paints, pyrotechnics, ceramics, and selective laser sintering Appearance Ball mills Ball Mills in the Mineral Processing Industry2022年7月7日 Effectively controlling the grinding fineness of the ball mill is an important factor to directly reduce costs and improve economic benefits In production, ball mill operators must supervise the crushing system If the particle size of raw 9 factors that affect the grinding fineness of ball mill
.jpg)
Cement Grinding Plant Solution Ball Mill Final Grinding Plant
Clinker grinding process with a ball mill (closed circuit) First Step: Raw material dosing The ingredient ratio is decided by the type of cement produced Normally, the main raw materials are clinker, gypsum, and additives Second Step: Grinding The grinding system adopts a closedcircuit ball mill grinding systempulverised to fineness such that 7080% passes through a 200 Mesh sieve Normally low speed ball mills or medium speed vertical spindle mills are employed in thermal power plant for this purpose The milling system is an important part of the auxiliary equipment of a coalfired power plant Pulveriser mill are one of the critical equipment of coalPulveriser Mill Performance Analysis Optimisation in SuperProblems Existingnumberin the Ball Mill Design of Feed Inlet The hourly output of the ball mill is greatly affected by the feed rate According to a large of reference data, the mainreason that the feed rate and ventilation of the ball mill is whether the grinding mill feed inlet design is reasonable The feed inlet in the design of the old Ball Mill DesignOptimization Of Feeding Device2021年2月3日 However, the grinding process is complex and unstable, with nonlinear characteristics caused by natural variation, mill load, and fluctuation of the raw material [36]Coarse Return Prediction in a Cement Industry’s Closed Grinding
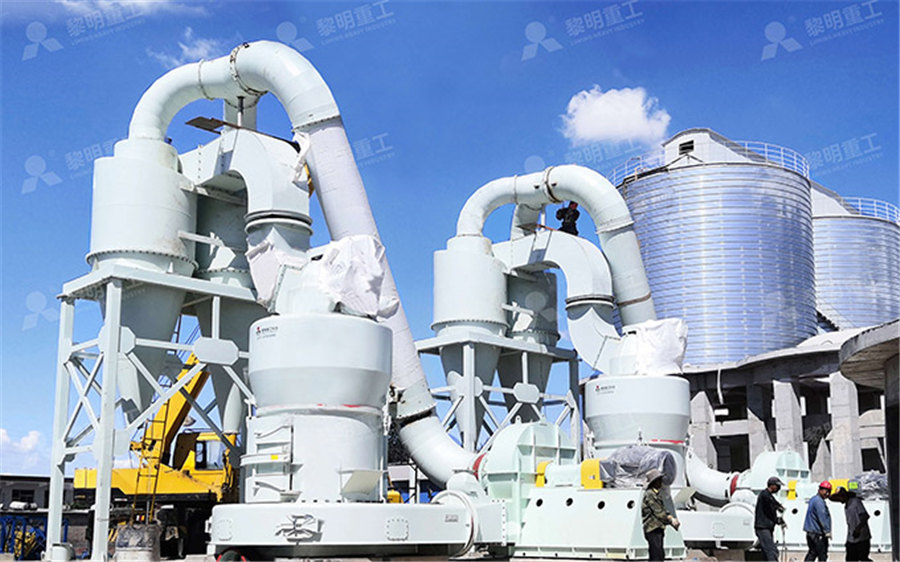
Audit Cement Ball Mill Systems PDF Mill (Grinding) Scribd
Audit Cement Ball Mill Systems Free download as PDF File (pdf), Text File (txt) or read online for free This document provides guidance on conducting a level B audit of a cement ball mill system A level B audit involves gathering detailed design and operational information on the mill system to identify short and mediumterm optimization opportunities and needs for further Mill feed inlet Gear box Grinding table Mill stand Hydraulic system Figure 4:The segment dam ring, easy to adjust in height Figure 5: Dependenceof the in clination in the RRSBdiagramon the grind ing pressure,classifier speed, dam ring height and air flow 14 A ir f lo 13 w [%] 1 2 11 14 13 12 11 78 83 89 100 60 80 100 Grinding pressure Cement grinding a comparison between vertical roller mill and ball millPlanetary ball mill (best result) High energy ball mill Emax / 2,000 min1 Comparison of grinding time and fineness in the Emax and in a planetary ball mill Titanium dioxide: 5 x finer Graphite: 8 x faster 7 x finer grinding time [µm] 50 40 30 20 10 0 particle size 0 102030 40 50 60 70 80 8 x faster 13 µm [h] Planetary ball mill (best High Energy Ball Mill ATS Scientific2022年12月22日 5 Compared with the combined grinding system of traditional Raymond mill and ball mill, vertical lime grinding has the advantages of wide adaptability, simple operation, quick adjustment, low maintenance cost, energy saving, etc It is the preferred choice for deep processing of quick lime HGM Ring Roller Micro Powder MillType Selection of Quicklime Deep Processing EquipmentNewsultramill
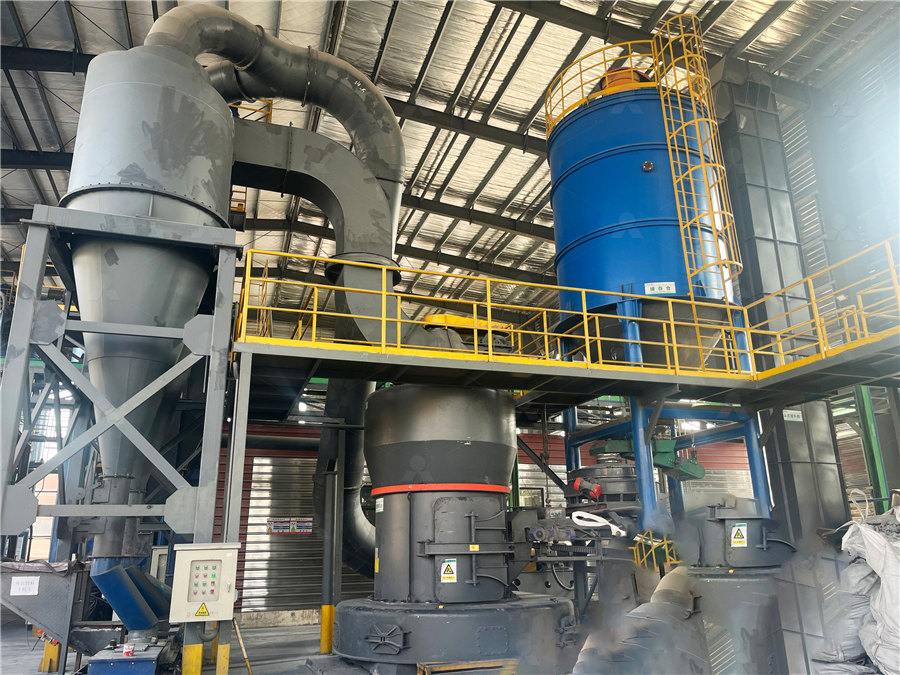
System dynamics model of output of ball mill
2021年2月15日 This study analyzes the dynamic characteristics of duplex inlet and outlet ball mill direct firing pulverizing system A mass and energy balancebased model is built by thermodynamic analysis2021年1月22日 To investigate the effects of grinding media shapes on the grinding kinetics of ball mill cement clinker, the grinding effects with ϕ20 mm balls and ϕ20 × 20 mm cylinders on six different size An innovative approach for determining the grinding media system Cement clinker grinding unit with ball mill, roll press or VRM 24×7 Consulting Support Skip to area, easy operation, convenient management, and a high operation rate In this clinker grinding unit, the roller press system’s air release and the ball mill’s ventilation share a dust vertical mill, ball mill, combined powder Cement Clinker Grinding Plant ball mills supplierThe more control you have over the mill, the better your grinding efficiency is likely to be Our ball mills include monitoring systems to continuously measure the material and air temperatures as well as the pressure at the mill exit The venting of the mill is adjusted by a damper in the inlet to the mill fan And the materialBALL MILL
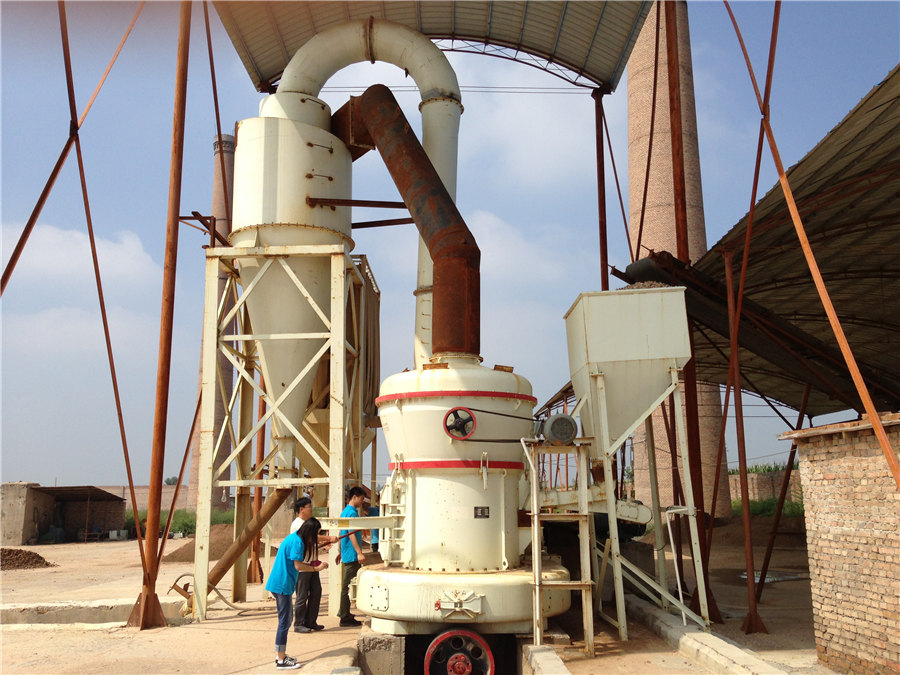
PLANETARY BALL MILL Laarmann
PLANETARY BALL MILL LM PM Laarmann Group BV Op het Schoor 6 6041 AV The Netherlands info@laarmann laarmann webshoplaarmann +31 6 23 40 00 33 • Quick and easy to clean • Rapid fine grinding • Easy exchange of grinding jars and balls • Grinding jars and balls made from a wide range of materials available2021年1月22日 In the whole process of cement production, the electricity consumption of a raw material mill accounts for about 24% of the total Based on the statistics of the electricity consumption of the raw A Survey and Analysis on Electricity Consumption of Raw Material Mill Ball mills are used primary for single stage fine grinding, regrinding, and as the second stage in two stage grinding circuits According to the need of customers, ball mill can be either wet or dry designs Ball mills have been designed in standard sizes of the final products between 0074 mm and 04 mm in diameter Applicationhow to change ball mill inlet trunnion liner Grinding Mill ChinaThe air swept ball mill is an ideal grinding machine that merges pulverizing and drying into a single It has the characteristics of high efficiency, energy saving, and environmental protection It is often used as the main equipment in the coal preparation system, which is capable to grind coal of various hardness (the fineness of pulverized coal can reach 85% and the moisture content Air Swept Coal Mill AGICO Ball Grinding Mill ball mill machines
.jpg)
Grinding Fineness Of Ball Mill Knowledge News CIC
2021年5月11日 For example, the grinding fineness of grinding machine is less than 0074 mm ( 200 mesh), accounting for 70% The fineness of grinding products is closely related to particle size, but the meaning is different Particle size refers to the size of material particle size How to control grinding fineness of ball mill The grinding fineness of 2015年10月23日 In this chapter an introduction of widely applied energyefficient grinding technologies in cement grinding and description of the operating principles of the related equipments and comparisons over each other in EnergyEfficient Technologies in Cement GrindingThe material level in a ball mill is normal if: 1 st Compartment: Approx 1/3 of the grinding ball surface lies bare and the grinding balls are lying next to each other with material laying in the space between 2 nd Compartment: if the grinding Process Training Ball Mill INFINITY FOR CEMENT 2013年8月1日 Present work deals with design and fabrication of a ball mill for mixing and blending of metal powders The ball milling was done for AA7068 metal powders for three different speeds at 150, 200 Judgement of ball mill working condition in combined grinding system
.jpg)
Ultrafine Grinding with Laboratory Ball Mills ResearchGate
2015年10月11日 Grinding of alumina in water with 1 mm grinding balls (left) after 1 hour (blue) and after 4 hours (green) Fig 6: Grinding of alumina with a 1 mm grinding ball (1 hour) and then with 01 mm balls Ball mills can be used for dry or wet grinding of various ores and other grindable materials Ball Mill Discharge fineness: 007504 mm Feed size: 25 mm The working principle of ball mill The material enters the first chamber of the mill evenly and spirally from the feeding device through the feeding hollow shaftBall Mill SBM Ultrafine Powder TechnologyNormally, grinding aids are added in a 15% concentrated solution (1:7 grinding aid to water – helps the dispersal of grinding aid in mill), at approximately 225 Lb/Ton for medium fineness and 34 Lb/Ton for high fineness cementEverything you need to know about clinker/cement Grinding4 SUBSET SELECTION The material that leaves the ball mill and enters the separator depends on the characteristics of the material that enters the mill and also on the grinding mill performance, which means that the process variables of all parts of the cement grinding circuit are potential inputs for online estimation of the cement finenessSoft Sensor for Online Cement Fineness Predicting in Ball Mills
.jpg)
Soft Sensor for Online Cement Fineness Predicting in Ball Mills
PDF On Jan 1, 2020, Karina Andreatta and others published Soft Sensor for Online Cement Fineness Predicting in Ball Mills Find, read and cite all the research you need on ResearchGatematerial is fed into the mill at the inlet side of the drum by means of a feeder and the grinded material is taken away at the outlet side of the drum by means of the ventilation system This is how grinding in a ball mill takes place [2] The relation between grinding productivity and loading of a ball mill by the material is proportional TheMATERIAL GRINDING BY MEANS OF BALL MILLS DAAAM