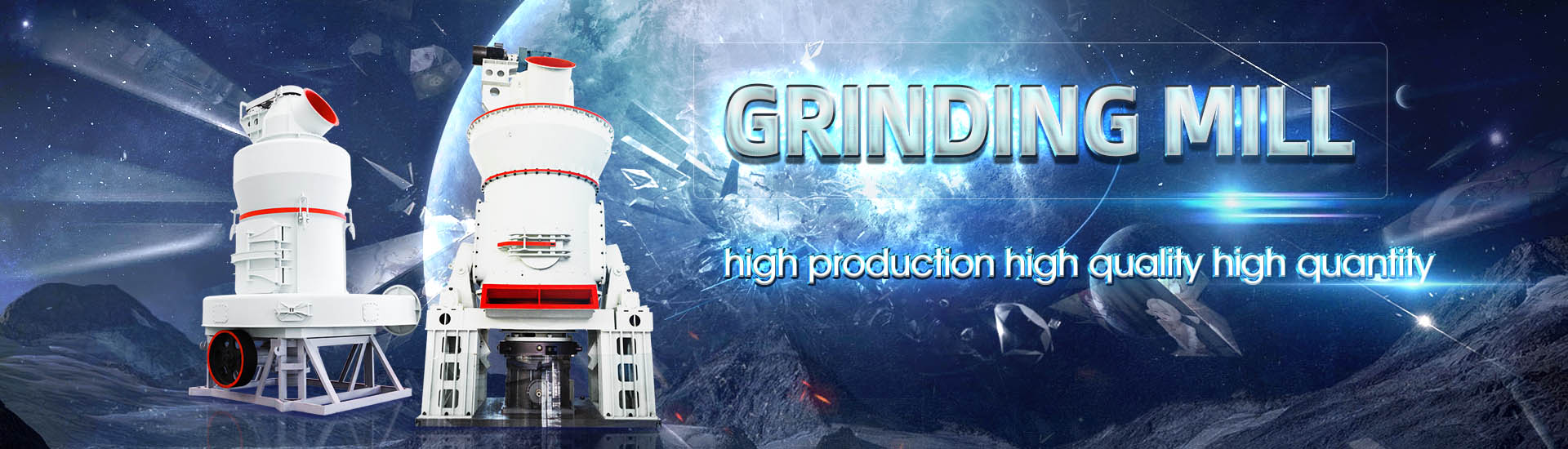
High pressure oil function of steel ball mill
.jpg)
Ball Mill Trunnion Bearing Lube System 911Metallurgist
2016年1月10日 On a 11’6” x 22’0” Ball Mill, the trunnion bearing lubrication system provides continuous low pressure flood oil for cooling and lubrication of the bearings, and high pressure oil for hydrostatic lift of the feed and 2015年4月30日 This paper describes the function and operation of lubrication systems for Ball Mill and SAG Mill Drives Provided within this paper are hydraulic schematics, functional Ball mill/SAG mill drive lubrication system IEEE Conference High Pressure Low Flow is required to be supplied to the bottom of the Trunnion before the Ball Mill is set in motion This High Pressure lubricant lifts the Mill to enable it to roll and avoid Oil Circulating Systems for Ball Mills Bijur DelimonCompared to conventional lubrication used in steel mill applications, oil/air lubrication reduces environmental pollution, increases lubricating and sealing performance, improves the high Oil/Air Lubrication Systems for Steel Production Facilities
.jpg)
Oil/Air Lubrication for Steelmaking Equipment Bearings
・ High viscous oil (VG680) can be used ・ Extremepressure oil Synthetic oil can be used ・Limited to mist oil ・VG220 to 460 of the rolling mill, such as the conveyance table In the case Ball mill optimisation As grinding accounts for a sizeable share in a cement plant’s power consumption, optimisation of grinding equipment such as ball mills can provide significant cost BALL MILLS Ball mill optimisation Holzinger ConsultingThe ball milling process is carried out for approximately 100–150 h to obtain uniformsized fine powder In highenergy ball milling, vacuum or a specific gaseous atmosphere is maintained Ball Mill an overview ScienceDirect TopicsHot Rolling Oil A is useful in improving productivity of the mill and life of rolls Regular use of Hot Rolling Oil A at the six finishing stand of Hot Strip Mill has demonstrated achievement of Hot Rolling Oil for Steel Plants A Case Study Society of
.jpg)
Grinding in Ball Mills: Modeling and Process Control ResearchGate
2012年6月1日 The paper presents an overview of the current methodology and practice in modeling and control of the grinding process in industrial ball mills Basic kinetic and energy 2017年7月5日 The simulation reveals that the ball milling velocity, ball volume fraction inside the canister, ball size, and impeller shaft design are all important parameters for energyefficient Modeling and Analysis of HighEnergy Ball Milling Through AttritorsBased on the MPT TITAN™ design, the Mills are girth gear dual pinion driven with selfaligned flanged motors, running on hydrodynamic oil lubricated bearings The TITAN design enables you to run full process load 40% Ball charge at Ball Mills – MechProTech MPTBall Mill is set in motion This High Pressure lubricant lifts the Mill to enable it to roll and avoid damaging metal to metal surfaces Once lifted and rolling the lubrication (low pressure high flow) can be started LUBRICATION SYSTEMS Low Pressure /High Flow oil is circulated from a reservoir to the top of the Trunnion bearing TheOil Circulating Systems for Ball Mills Bijur Delimon
.jpg)
2020 Technology and Operation of a Hot Rolling
2020年1月3日 The new products developed by using No 3 hot strip mill are as follows: (1) Ultra high rvalue coldrolled sheet steel: Newly developed continuous and warm rolling technique combined with BALL MILLS 1 FEBRUARY 2021 INTERNATIONAL CEMENT REVIEW T here are currently several energyefficient grinding systems available for the cement and mineral industry, including vertical roller mills (VRM), highpressure grinding units (HPGR) or simple roller presses, as well as the most traditional type of installation: ball mills, combined inBALL MILLS Ball mill optimisation Holzinger Consultingoutput is a function of temperatureand mechanical deformationduring rolling Shaping and Treating of Steel: 101 Mill Configuration REHEAT FURNACES SOAK = even heating through the crosssection of a slab Pusher High pressure descale water on entry side of mill removes remnant furnace scale and reoxidation 25 26Principles of Hot Rolling AIST2019年11月26日 The ball mill adopts a discharge screen similar to the ball mill, and the function of blocking the internal medium of the overflow ball mill is accomplished inside the rotary part of the ball mill The discharge screen is only responsible for forcing out a small amount of the medium that overflows into the discharge screen through the internal welding reverse spiral, to What’s the Difference Between SAG Mill and Ball Mill
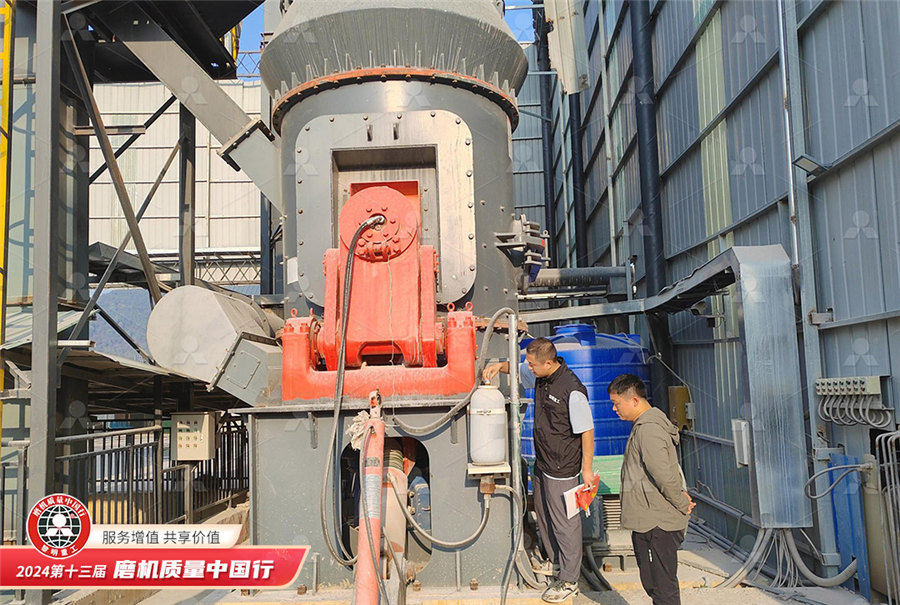
Evaluating the performance of an industrialscale high pressure
2023年1月1日 A twostage HPGR–horizontal stirred mill circuit has been proposed and its specific energy requirement was determined by a series of stirred mill tests adopting a pilotscale HPGR and JKSimMet® model, it was shown that this circuit consumed 13 %–31 % less energy than SAB/AGBC/SABC circuits for Cu porphyry ore (Wang, 2013) and consumed 92 % and Many of these needs to be lubricated in order to function in the production The lubrication system lubricate gearboxes for roller cleaning of the application with high pressure cleaners lead to very high water content in the gear oil Gear Oil Steel Mill Screw Down Gear System ASIN5037UK Steel / Aluminium 24032009 CJC™ Application Steel Mills/Works Oil MaintenanceThe E max is an entirely new type of ball mill for high energy milling GrindControl to measure temperature and pressure inside the jar Available grinding jar sizes are 50 ml, 80 ml and 125 ml, materials include stainless steel, tungsten carbide and zirconium oxide, ensuring contaminationfree sample preparationEmax High Energy Ball Mill Retsch2024年5月27日 The General Function of Ball Mills A ball mill is a grinder used for grinding and blending materials for mineral dressing processes, paints, pyrotechnics, ceramics, and selective laser sintering Appearance Ball mills have various designs and functions, ranging from laboratoryscale versions to large industrial models The ball mill consists Ball Mills in the Mineral Processing Industry MechProTech

Grinding in Ball Mills: Modeling and Process Control
2012年6月1日 is lined with mill liners protecting the steel body of the mill and incorporating mill lifters which help to raise the content of the mill to greater heights before it drops and cascades down [36]2021年7月29日 The basic working principle of the colloid mill is that the fluid or semifluid materials undergo strong cutting force, friction force, and highspeed vibration through the relatively highspeed movement between the rotor and stator, which causes the materials to be crushed, emulsified, homogenised, and temperature, to obtain satisfactory results It has a The Function Of a Colloid Mill Machine and How To Use It2024年9月12日 Friction and wear test equipment, scanning electron microscope, abrasion balls made of CGr15 high carbon chromium bearing steel, and liners made of NM500 steel were used for wear simulation and friction–wear experiments The variation trends of friction coefficient, wear amount, and subsurface characteristics under dry friction and slurry conditions were studied Friction and wear characteristics and simulation study of NM500 2022年3月30日 All industries are facing increasing pressure to ensure that carbon emissions are reduced to help achieve the socalled 15 °C future This has led to most of the major mining companies committing to significant reductions in their operational carbon footprint – in many cases by up to 30–40% in the next 10–15 years and to place themselves in a netzero scope Helping to reduce mining industry carbon emissions: A stepby
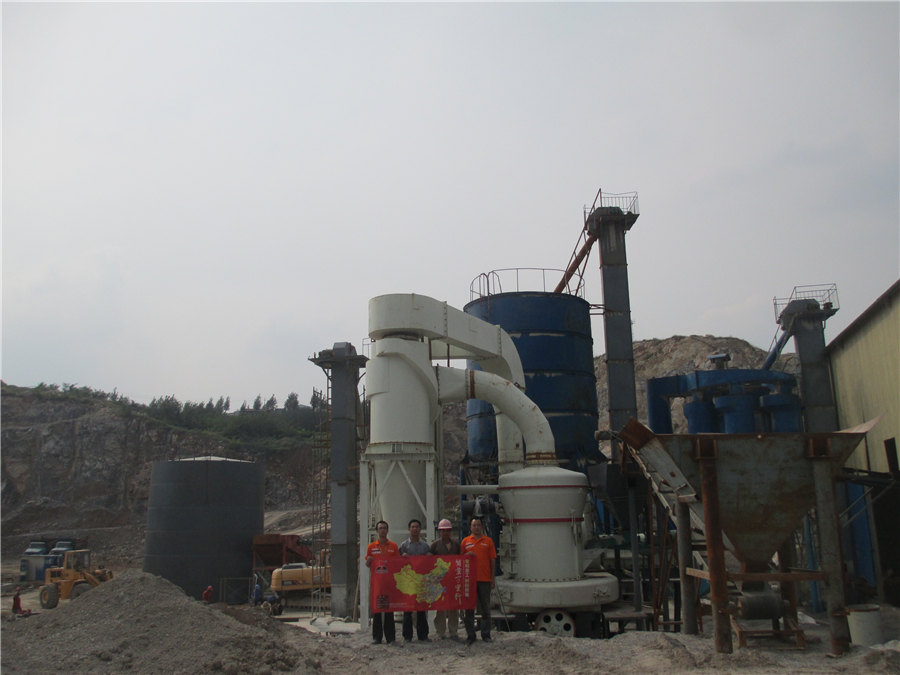
The operating principle of the ball mill Energosteel Grinding
2017年2月8日 Energy consumption for ball mills is a function of many factors: the physical properties of the ground material – its specific gravity and hardness; the degree of drum filling by grinding balls; the number of drum rotations, etc Ball mills have low efficiency – no more than 15% Energy is mainly consumed on the wear of grinding balls and admixture of oil, so this effect must be incorporated into the quantity of coolant being utilized 5% of oil in the may sound negligiblewater but the heat transfer is, compromised Water/oil emulsions are, however still about four times more effective in terms of cooling than rolling oilGENERAL ASPECTS OF ROLL COOLING FOR HOT COLD ROLLING MILLS RHP RHP high pressure roll mill The smart way of fine milling Autocomminution principle In a traditional tubular mill, grinding is due to the compression and attrition of the mineral to be milled between the balls (or pebbles) and the drum RHP high pressure roll mills upsets this principle: the material is forced to pass through two rolls and High Pressure Roll Mill / RHP 16Lab Minerali Engineering2016年10月20日 Ball Mill Sole Plate This crown should be between 002″ and 003″, per foot of length of sole plate For example, if the sole plate is about 8′ long, the crown should be between 016″ and 024″ Ball Mill Sole Plate After all shimming is completed, the sole plate and bases should be grouted in positionBall Mill Maintenance Installation Procedure 911Metallurgist
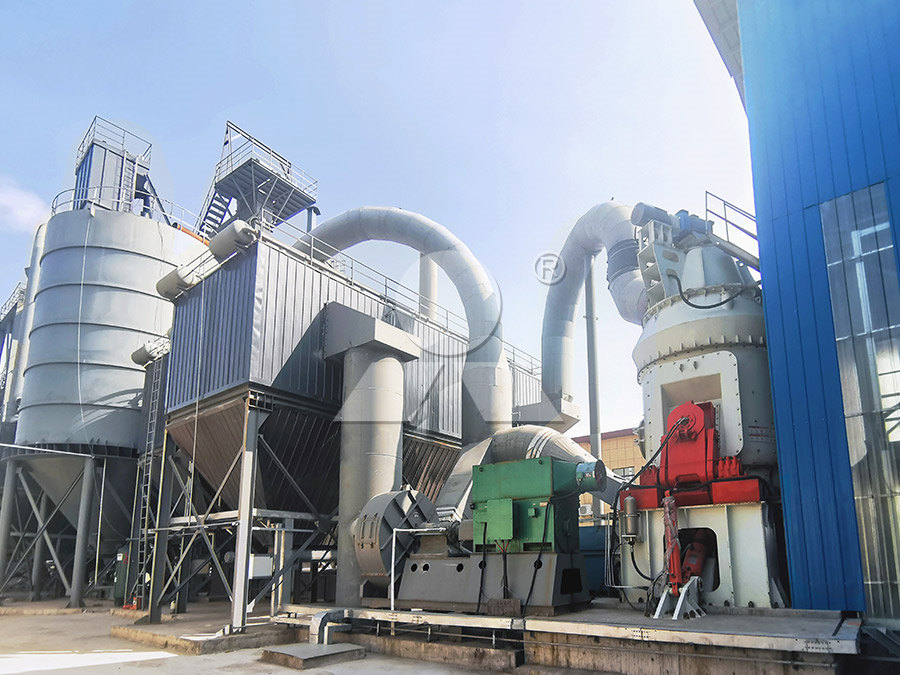
Modelling of the HighEnergy Ball Milling Process ResearchGate
M Mhadhbi DOI: 104236/ampc2021 33 Advances in Materials Physics and Chemistry Figure 1 Photograph of the highenergy planetary ball mill2018年11月7日 Ball mill is an important mineral processing equipmentDuring the use of the ball mill, problems such as wear, loose links, deterioration of the oil, and corrosion of the metal structure are inevitable in each link, which causes the technical, economic and safety performance of the ball mill to be reduced at different degrees3 Aspects of Ball Mill Maintenance MiningpediaFunction principle of HPGR Mill High Pressure Grinding Roller Mill, ie HPGR mill, the working principle of HPGR mill is using two horizontal arranged roller turning in opposite direction and press crushing material layer, refer to sketch High Pressure Grinding Roller Mill – belt conveyor, 2020年4月6日 nanopropolis coated with casein micelle using highpressure ball mill homogenizer for making nanosized particles Point of view from potential nanopropolis researchers, and that was research from Supardi (2011), the resulting product nanopropolis has a diameter of 3161 nm [9] Then the coating efficiency of theProduction of Nanopropolis Using High Pressure Ball Mill
.jpg)
Ball Mill Liner Design 911Metallurgist
2016年1月5日 Mill HEAD LINERS Head liners are of the segmental type constructed of Manganese Steel, Chrome molybdenum, or NiHard and are designed to pass easily through the manhole opening or discharge opening in 2016年6月6日 Used in conjunction with Grade 5 (highstrength) bolts, this assembly is generally applied to rod mills over 100′ in diameter and ball and autogenous mills greater than 135″ in diameter Metal tometal contact (nut washer retaining ring mill) compresses the seal ring and allows full proof load of liner bolt to be utilized, keeping liners tight, in large diameter, high SAG Mill Liner Design 911MetallurgistThe history and necessity of mechanical alloying M Sherif ElEskandarany, in Mechanical Alloying (Second Edition), 2015 2515 Planetary ball mills The Planetary ball mills are the most popular mills used in MM, MA, and MD scientific researches for synthesizing almost all of the materials presented in Figure 11 In this type of mill, the milling media have considerably high Ball Mill an overview ScienceDirect Topics5′ x 10′ ball mill = 15 m X 3 m Ball Mill A PULP level sufficiently high to interpose a bed of pulp, partly to cushion the impact of the balls, permits a maximum crushing effect with a minimum wear of steel05 TO 15 TPH SMALL SCALE MINER’S BALL MILL
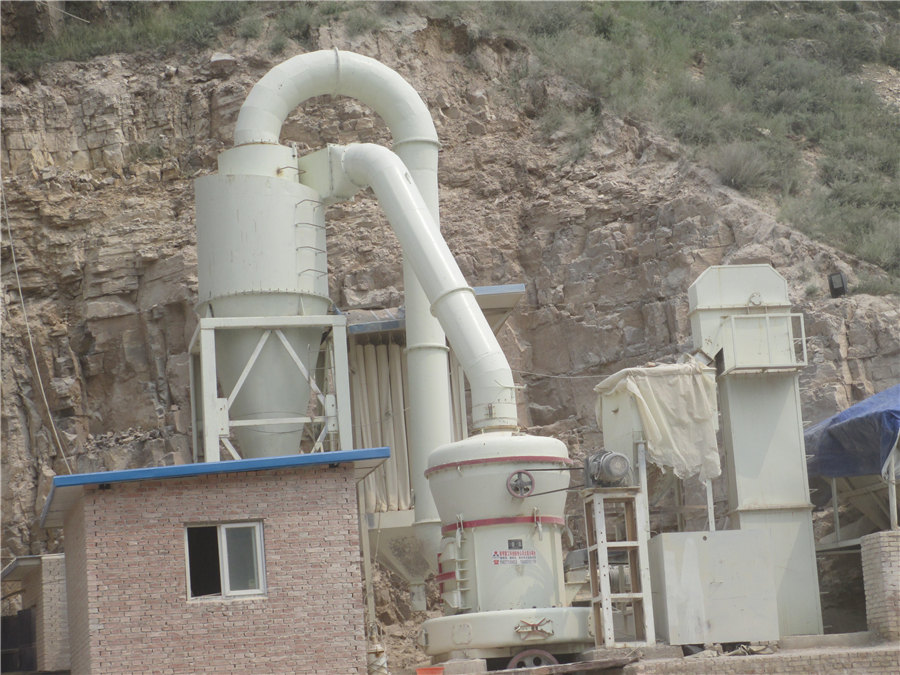
HPGR vs Ball Mill, their differences MAXTON
2024年4月13日 HPGR and ball mill are both widely used ore crushing (grinding) equipment Within comminution circuits, High Pressure Grinding Rolls (HPGR) are increasingly replacing ball mills for hard rock reduction – owing to their substantially lower energy consumption and potential for significant total cost of ownership reduction but these two machines differ in working 2023年4月23日 One of the most used tumbling mills is the ball mill oilquenched alloysteel balls heattreated at lower High mill filling reduces the grinding rate because the collision zone (PDF) Grinding Media in Ball MillsA Review ResearchGate2021年6月29日 The aim of this work was to observe the impact of the milling technique employed by the DESI 11 disintegrator on the properties of fly ash This type of mill is a highspeed pin mill with two Effects of Mill Speed and Air Classifier Speed on Performance of Planetary ball mills are ideal for nanoscale grinding and mixing Vibratory Ball Mills: Utilizing vibrations, these mills are suitable for ultrafine grinding and mixing of materials Vibratory ball mills provide highenergy input to the grinding media, resulting in Ball Mill Grinding Machines: Working Principle, Types, Parts
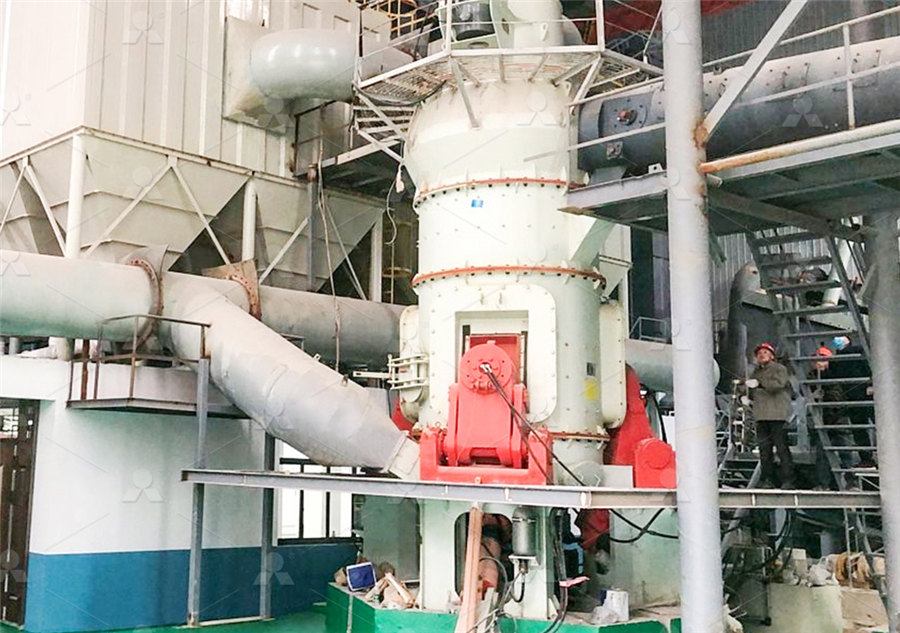
Ball Mills 911Metallurgist
2017年2月13日 Steel Head Ball Mills SteelHead Rod Mills Quotation on a Ball Mill Price or a Rod Mill Price When requesting a quotation on a Ball Rod Mill, it is requested that you include the following information: Type of mill: Type “A” 2019年9月15日 Highpressure ball valves are suitable for applications where the medium is flowing at a pressure greater than 3000 psiHighpressure 3way ball valves can even handle mediums flowing at a pressure greater than 15000 How Do HighPressure Ball Valves Work? SIOType “D” Ball and Pebble Mills One of the most popular designs, the Type D mill is available as a steel ball mill with or without steel plate wearliners, or as a lined ball or pebble mill utilizing Alumina, Buhrstone or rubber linings Type D ball Ball Mills, Pebble Mills, Material Processing Mills2021年1月1日 In this paper, the milling parameters of high energy ball mill (Fritsch Pulverisette 7) like vial geometry, number and size of balls and speed of the mill were modelled and discussedModelling of the HighEnergy Ball Milling Process
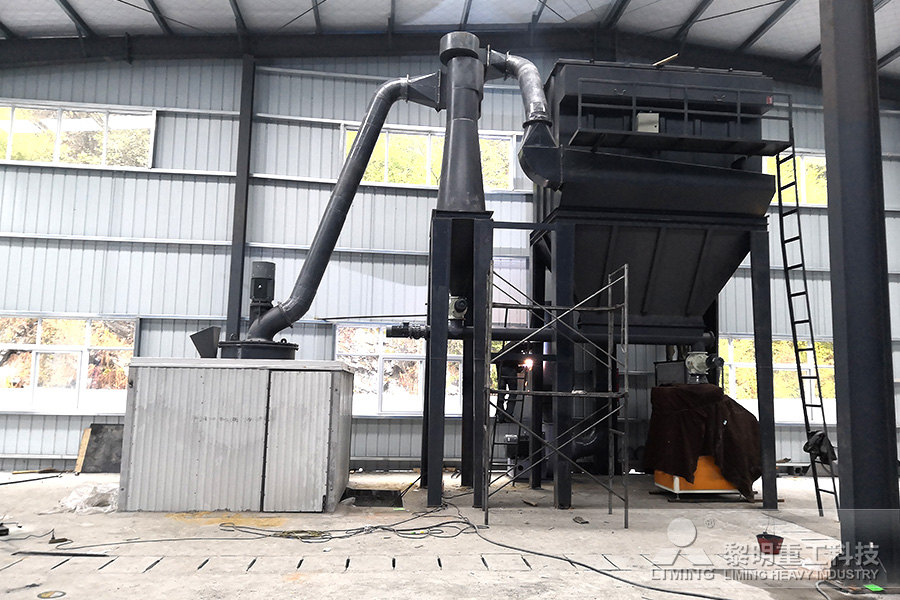
Flowsheet of the Future: HighPressure Grinding Rolls, Vertical
A primary breakage unit (eg, AG, SAG, or rod mill) A ball mill working with a hydrocyclone to perform the final grind to product size The main feature of the typical flowsheet (Figure 1) is that an AG–SAG mill’s capacity is a function of the ore’s feed sizedistribution and hardnessMill Type Overview Three types of mill design are common The Overflow Discharge mill is best suited for fine grinding to 75 – 106 microns; The Diaphram or Grate Discharge mill keeps coarse particles within the mill for additional grinding and typically used for grinds to 150 – 250 microns; The CenterPeriphery Discharge mill has feed reporting from both ends and the product AMIT 135: Lesson 7 Ball Mills Circuits – Mining Mill Operator 2023年7月4日 The basic structure of the roller mill includes the grinding roller, the grinding body, the force generation and transmission mechanism, airflow, and the device for easy replacement It can be divided into vertical roller mill, horizontal cylinder roller mill, high pressure roller mill, Raymond mill, and column millRoller Mill SpringerLinkaccording to packing list, and if the ball mill, power pack and ball milling tank are damaged in transportation 72 Reading Read the User’s Manual carefully, carry out nonload test running of the ball mill as per the steps described in the Manual, and check if the operation of frequency converter and ball mill is normal 73 Loading TankSFM1 (QM 3SP2) High Speed Shimmy Ball Mill Operational
.jpg)
High Energy Planetary Ball Mill Kintek Solution
Experience fast and effective sample processing with the FP2000 highenergy planetary ball mill This versatile equipment offers precise control and excellent grinding capabilities Perfect for laboratories, it features multiple grinding bowls for simultaneous testing and high output Achieve optimal results with its ergonomic design, compact structure, and advanced featuresReason: This is a common problem mining ball mills face, resulting in low productivity and low ore processing efficiency One reason may be the improper design of the grinding chamber, which affects the flow of materials and reduces grinding efficiency Additionally, worn or damaged liners can hinder the grinding process by reducing the effective impact between the ball and the Inventory Of Common Faults And Solutions Of Mining Ball Mill