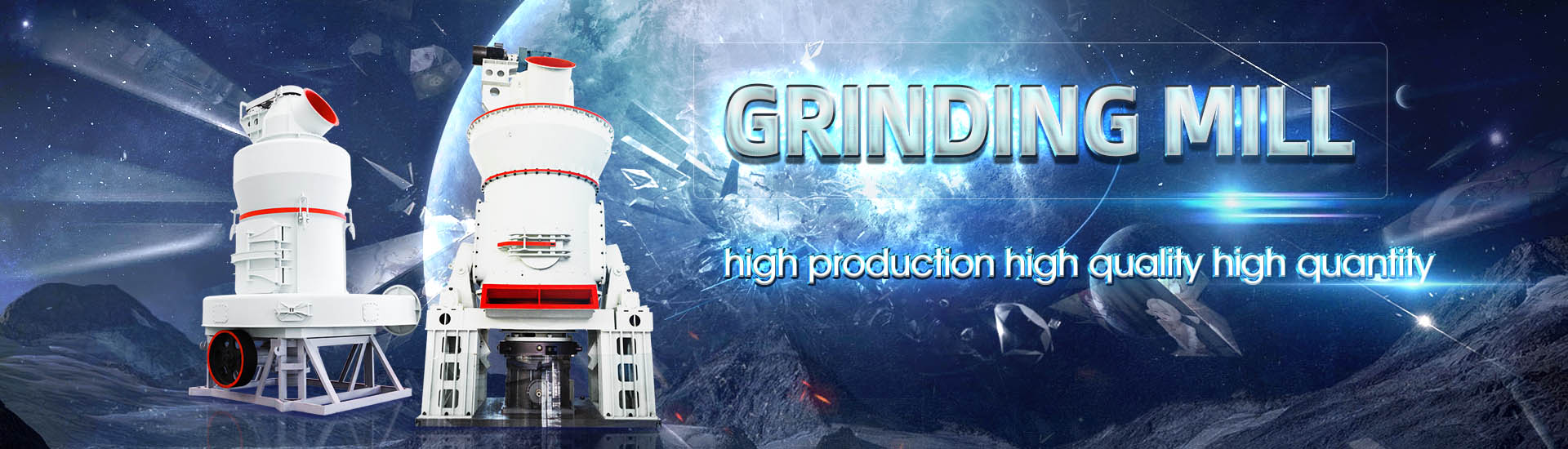
Daily output of 1200 cubic meters ore grinding mill
.jpg)
A Review of the Grinding Media in Ball Mills for Mineral Processing
2023年10月27日 Grinding media play an important role in the comminution of mineral ores in these mills This work reviews the application of balls in mineral processing as a function of the materials used to manufacture them and the mass loss, as influenced by three basic wear STM Minerals introduced the VPMTM (Vertical Power Mill), which is a further development of the industry leading VRMTM technology The VPMTM has a wider grinding chamber with RECENT DEVELOPMENTS IN COARSE GRINDING USING VERTICAL 2020年6月1日 Stirred media mills are used by the mining industry for ultrafine grinding to enhance liberation, and to decrease particle sizes of industrial minerals to tailor functional Stirred media mills in the mining industry: Material grindability 2023年7月20日 Moist grinding, a special grinding method, is used to prepare pellets for smelting According to the grinding medium features, ore grinding is mainly classified into ball grinding Ore Grinding SpringerLink
.jpg)
Measurement and Control for Ore Grinding and Classification
2023年6月1日 The main parameters of grinding and classification process include measurement of millfeeding quantity, mill load measurement, measurement of ore slurry density, Online 2023年11月1日 According to the ore feeding amount of a single grinding unit in the first stage grinding of Gongchangling Concentrator of 275 t/h, the overall unit consumption of ball mill Energy conservation and consumption reduction in grinding 2013年12月18日 Fine grinding, to P80 sizes as low as 7 μ m, is becoming increasingly important as mines treat ores with smaller liberation sizes This grinding is typically done using stirred Energy Use of Fine Grinding in Mineral ProcessingThe dry milling of ore in LOESCHE vertical roller mills has shown significant process advantages, as well as economic and ecological benefits To demonstrate these a mobile oregrinding plant Mills for minerals and ores Loesche
.jpg)
Codelco El Teniente SRP
2019年4月25日 El Teniente’s daily production volume can top 170,000 tonnes of ore, with around 150,000 tonnes processed in the Colón plant and another 20,000 tonnes processed in 2015年4月9日 The mill is normally used for grinding of ores and typical drum diameter ranges from 2 to 10 meters This type of mill is often used as a single stage process, Output from such a mill is low and the mill in used only for Grinding Mills and Their Types – IspatGuruA crushing plant delivered ore to a wet grinding mill for further size reduction The size of crushed ore (F 80) was 40 mm and the SG 28 t/m 3 The work index of the ore was determined as 122 kWh/t A wet ball mill 1 m × 1 m was chosen to grind the ore down to 200 micronsGrinding Mill an overview ScienceDirect Topics2018年10月17日 This plant’s ball mills are really huge The plant’s enrichment scheme includes two types of grinding mills – a SAG mill (semiselfgrinding) and a BALL mill (ball grinding) The semiselfgrinding mill (SAG) is 12192 m in GRINDING MILLS CHAMPIONS World's biggest
.jpg)
SAG Mill Grinding Circuit Design 911Metallurgist
2016年6月6日 Integral with the grinding circuit is a 1500 cubic meter capacity agitated surge tank equipped with level sensors and variable speed pumps This acts as a buffer between the grinding circuit and the flow rate sensitive cycloning and 2013年4月1日 This paper presents the design and application of a multipleinput–multipleoutput fractional order proportionalintegral (MIMO FOPI) controller to a grinding mill circuitAnalysis and validation of a runofmine ore grinding mill circuit 2018年3月27日 Dry grinding and classification circuit: (a) Idea of the circuit: 1feed stream, 2mill working chamber, 3working area with ferromagnetic rods, 4main transport air stream, 5mills output stream Comparison of Wet and Dry Grinding in Electromagnetic Mill2019年6月21日 Besides, newly proven reserves of platinum and biogas are also abundant Platinum reserves are second in the world Biogas reserves are estimated about 500 million cubic meters, ranking first in East Africa Ball mill for grinding gold ore Gold is a rare mineral resource extracted from ordinary ore and has high industrial valueBall Mill Of 510t/h For The Gold Ore In Zimbabwe
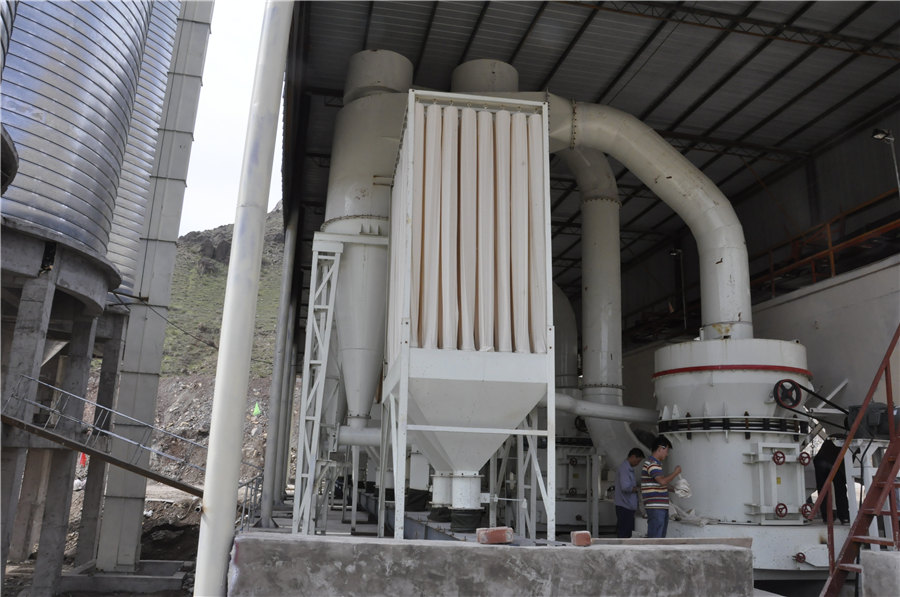
(PDF) Grinding Media in Ball MillsA Review ResearchGate
2023年4月23日 grinding media in a grinding mill with about 2630 wt% chrome by Chen et al [37] using a phosphate ore in a modified ball laboratory ball mill whose electrochemical potential could be controlled2017年2月20日 All Grinding Mill Ball Mill Manufacturers understand the object of the grinding process is a mechanical reduction in size of crushable material 911 Metallurgist is a trusted resource for practical insights, solutions, and support in mineral processing engineering, helping industry professionals succeed with proven expertise Grinding Mill Design Ball Mill Grinding Mill Design Ball Mill Manufacturer 911Metallurgist2017年9月11日 In this study, an extensive sampling study was carried out at vertical roller mill of ESCH Cement Plant in Luxemburg Samples were collected from mill inside and around the circuit to evaluate the (PDF) Performance Evaluation of Vertical Roller Mill in Cement Grinding 2016年7月8日 UNTIL THE THIRD THEORY OF COMMINUTION of "Work Index" method of determining crushing and grinding mill size was introduced, there was no way of accurately 911 Metallurgist is a trusted resource for Equipment Sizing: Crusher or Grinding Mill
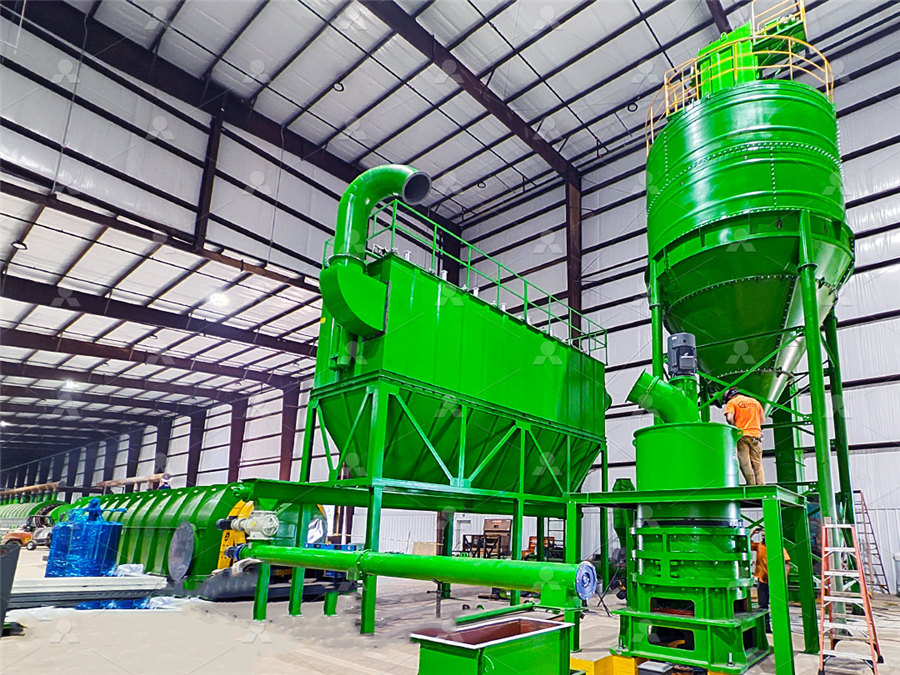
China United Coalbed says daily gas output tops 14m cubic meters
2024年11月14日 China United Coalbed says daily gas output tops 14m cubic meters By Zheng Xin Updated: 21:02 China United Coalbed Methane Corp said on Monday the company's daily gas production exceeded for the first time 14 million cubic meters, up 40 percent yearonyear, ranking it as the leading coalbed methane company in the countryRequest PDF On Mar 15, 2015, Mathis Reichert and others published Research of iron ore grinding in a verticalrollermill Find, read and cite all the research you need on ResearchGateResearch of iron ore grinding in a verticalrollermillSBM ultrafine powder technology co,ltd Is China's excellent ore mill supplier Our main products include ultrafine vertical roller mill, ultrafine grinding mill, HGM Series Ultrafine Grinding Mill; Feeding size: 200325 Mesh, D97; Output size: 800 mesh, D90; Capacity: 4000 kg/hourSBM Ultrafine Powder Technology Industrial Grinding Mill, 2016年2月2日 Our EXAMPLE Grinding and Classification Circuit is designed to grind 500 tonnes of ore per day, operating 24 hours per day, with an availability of 95% This circuit will grind 5/8″ material from the Crushing Plant, classify the slurry in one of two cyclones, and pass 70% of the minus 200 mesh material to the mill feed Thickener Circuit at a rate of 22 mtphGrinding and Classification Circuit 911Metallurgist
.jpg)
Effect of Water Density on Grinding Mill 911Metallurgist
2015年7月29日 As you add ore to the mill you are also adding WATER and changing density which affects the slurry rheology and workings of the grinding action inside that 911 Metallurgist is a trusted resource for practical insights, solutions, and support in mineral processing engineering, helping industry professionals succeed with proven expertise Effect of Water Density on 2023年12月12日 Ore can have various properties, such as hardness, density, moisture content, etc, which can affect the ore’s productivity and grinding efficiency Discover the world's research 25+ million members(PDF) Control of ball mill operation depending on ball load and ore 2017年7月26日 The power drawn and reduction achieved to the grinding mill feed will be maximized The grinding mill output will vary considerably with the Work Index If the feed size was 13,000 micrometers for the same grind production size, theoretical output from Fig (21) would change from about 90,000 tons per day on the 13 Work Index down to 65,000 How Ball Mill Ore Feed Size Affects Tonnage Capacity2013年8月3日 In Grinding, selecting (calculate) the correct or optimum ball size that allows for the best and optimum/ideal or target grind size to be achieved by your ball mill is an important thing for a Mineral Processing Engineer AKA Metallurgist to do Often, the ball used in ball mills is oversize “just in case” Well, this safety factor can cost you much in recovery and/or mill liner Calculate and Select Ball Mill Ball Size for Optimum Grinding
.jpg)
Grinding Mill an overview ScienceDirect Topics
In the mill, the mixture of medium, ore, and water, known as the mill charge, is intimately mixed, the medium comminuting the particles by any of the above methods Apart from laboratory testing, grinding in mineral processing is a continuous process, material being fed at a controlled rate into one end of the mill and discharging at the other end after a suitable dwell (residence) time2021年1月5日 For example, the filling rate of ball mill (78 cubic meters) is 44% (according to the technical documentation for the mill) Knowing the bulk weight of grinding balls, we understand that for the efficient operation of the mill it is THE MILL FILLING RATE IS THE FOUNDATION OF Iron ore dry grinding dry magnetic process of iron ore dressing mill for dry fine grinding, grinding fine reading can guarantee200 above 80%, equivalent to the common process of ball mill and screw grading machine or ball mill and cyclone grinding closed process, at the same time, iron ore dressing mill processing capacity is much higher than the ball mill, low energy consumption, News Iron ore mineral processing with standing grinding or ball 2022年5月23日 Grinding experiments were conducted in a laboratoryscale stirred mill on a lowgrade PGE bearing chromite ore HighPressure Grinding Rolls (HPGR) product of −1 mm was used as feed material to Modeling and application of stirred mill for the coarse grinding
.jpg)
Understanding the operation of grinding mills in the mining and
1 Grindability: The grindability of the ore affects the efficiency of the grinding mill Harder ores require more energy and longer grinding times, which can impact the mill's performance and operational costs 2 Media andliner Wear: The condition of the grinding media and liners affects the mill's efficiency2013年5月30日 This research has developed a population balance equation (PBE) model simulation to predict the output of biomass pellet grinding for Lopulco E16 mill and a Retsch PM100 planetary ball mill; this Application of multi regressive linear model and neural network 2017年10月26日 The following are factors that have been investigated and applied in conventional ball milling in order to maximize grinding efficiency: a) Mill Geometry and Speed – Bond (1954) observed grinding efficiency to be a function of ball mill diameter, and established empirical relationships for recommended media size and mill speed that take this factor into Factors Affecting Ball Mill Grinding EfficiencySpeed also plays a role in ore grinding; too high of a speed can cause damage to the mill gears and other components, while too low of a speed can cause excessive wear on these same components It is important to find a balance between these two variables in order to achieve optimal grinding performanceFactors affecting ores grinding performance in ball mills

The effects of iron ore concentrate grinding methods (HPGR and
2020年10月18日 An iron ore concentrate sample was ground separately in a pilotscale HPGR mill in multiple passes and a dry opencircuit ball mill to increase the specific surface area of particles2018年3月29日 Comparison of dry and wet grinding process in an electromagnetic mill is presented in this paper The research was conducted in a batch copper ore grinding Batch mode allows for precise parametrization and constant repetitive conditions of the experiments The following key aspects were tested: processing time, feed size, size of the grinding media, Comparison of Wet and Dry Grinding in Electromagnetic Mill MDPICLUM series of ultrafine gypsum powder vertical grinding mills are a new type of ultrafine industrial ore grinding equipment that integrates grinding, grading, powder collection and conveying +17CLUM Ultrafine Vertical Grinding Mill2023年7月10日 The present literature review explores the energyefficient ultrafine grinding of particles using stirred mills The review provides an overview of the different techniques for size reduction and (PDF) EnergyEfficient Advanced Ultrafine Grinding of
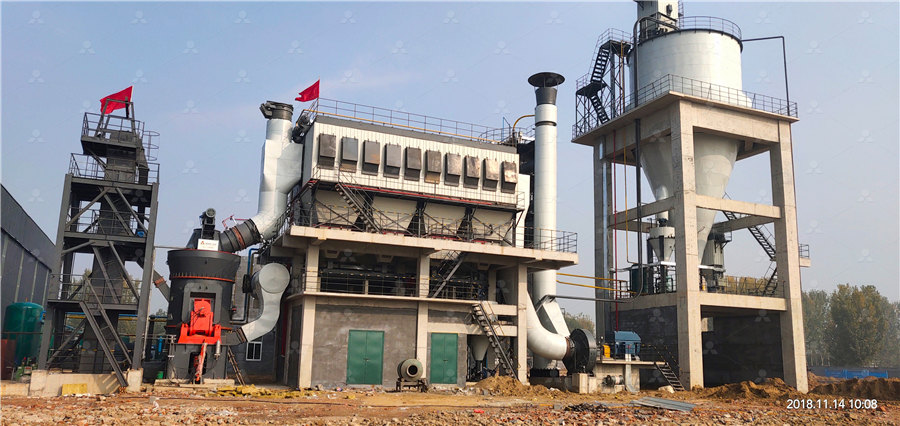
Large mill, Large grinding mill All industrial manufacturers
The Metso Outotec® Open Ended Discharge Grinding Mill (OED Mill) 15′ tub opening and a capacity of 20 cubic yards With horsepower ranging from 1,050 to 1,200, this machine can power through Compare this product Remove from comparison tool Output: 20 kg/h 1,200 kg/h2019年6月9日 There is ample evidence of the role of fragmentation on the overall minemill fragmentation system performance [3,4] The efficiency of the system through fragmentation optimization is documented Grinding mill process optimization algorithm ResearchGate2024年4月26日 These mills utilize the ore itself as the grinding media, reducing the need for additional grinding media AG/SAG mills are typically used for coarse grinding, where large pieces of ore are efficiently broken down The grinding process reduces the ore size, which enhances the efficiency of subsequent beneficiation processes by increasing the Iron Ore Processing: From Extraction to Manufacturing2012年6月1日 As the cylinder starts to rotate, the grinding balls inside the cylinder crush and grind the feed material, generating mechanical energy that aids in breaking bonds, activating the catalyst, and Grinding in Ball Mills: Modeling and Process Control
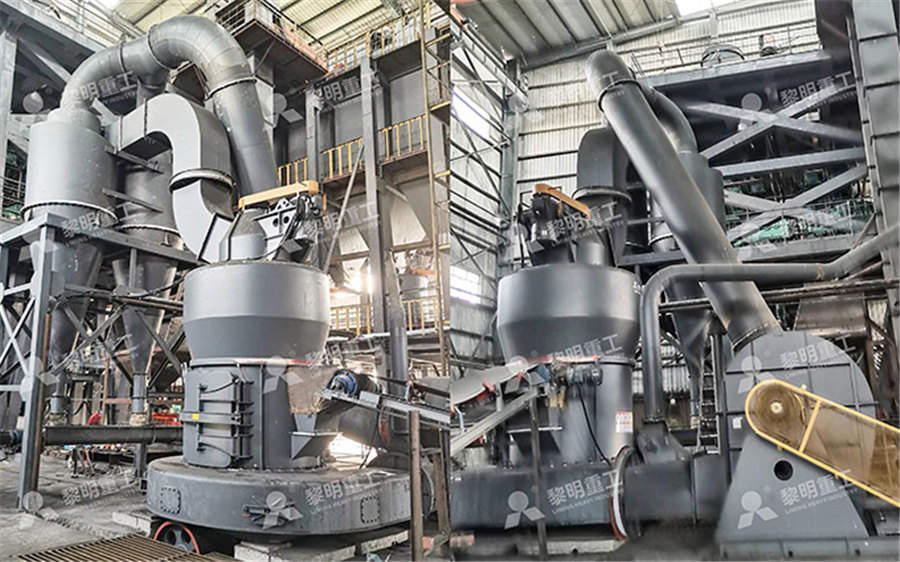
Monitoring the fill level of a ball mill using vibration sensing and
2019年10月19日 Ball mills are extensively used in the size reduction process of different ores and minerals The fill level inside a ball mill is a crucial parameter which needs to be monitored regularly for optimal operation of the ball mill In this paper, a vibration monitoringbased method is proposed and tested for estimating the fill level inside a laboratoryscale ball mill A vibration 2011年1月1日 A Panalytical (Epsilon1; 50 kV; Ag anode Xray tube) XRF spectrometer was used to analyze the elemental composition of pulverized rock samples at Sepro Mineral Systems (Langley, BC)Measurement of electrical energy consumption in a Bond ball mill2024年5月17日 A SAG (SemiAutogenous Grinding) mill is a giant rotating cylinder filled with grinding media and the ore being reduced As the mill rotates, the grinding media lifts and the impact crushes the feed material SAG mill control refers to the practice of managing the mill load, which is the amount of material inside the mill at any given timeA guide to SAG Mill management2021年6月17日 Due to its strong lifting capacity and excellent grinding performance, the trapezoidal liner is widely used in the SAG mill The structure of the trapezoidal liner is shown in Fig 1, the main dimensions are: dip angle \(\tau\), length of the top edge \(L\) and height \(h\)Dip angle \(\tau\) determines the trajectory of the mediums in the SAG mill, which directly affects PARAMETER OPTIMIZATION OF LARGE SAG MILL LINER BASED
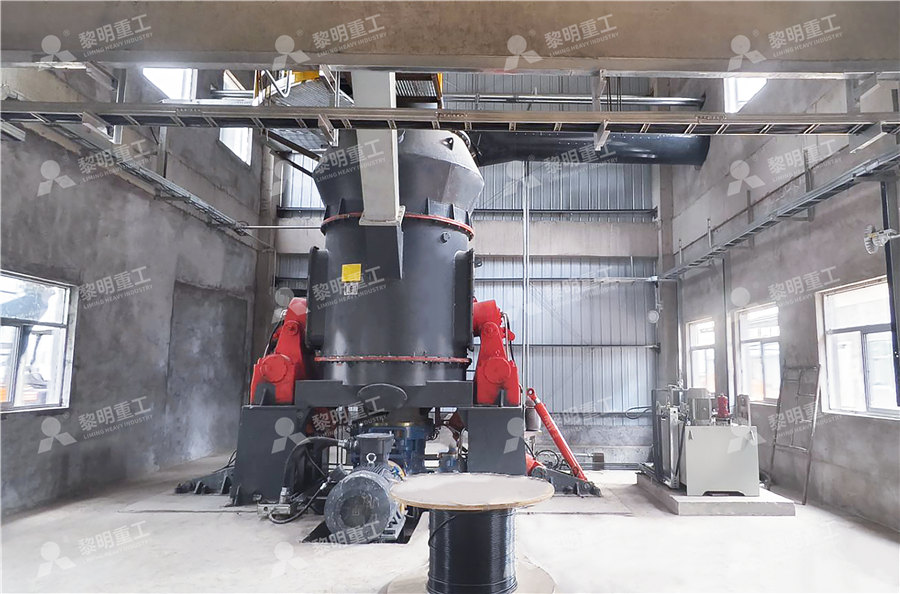
Hybrid nonlinear model predictive control of a runofmine ore
2018年7月1日 Request PDF Hybrid nonlinear model predictive control of a runofmine ore grinding mill circuit A hybrid nonlinear model predictive controller (HNMPC) is developed for a runofmine ore